Additive manufacturing has affected many industries, but few stand to benefit as much as the medical fields, including dentistry.
3D printing technologies thrive in an environment where our unique bodies require custom solutions. As a result, the dental industry is going through a rapid digital transformation with digital workflows bringing increased efficiency, consistently high quality, and lower costs to dental labs and practices.
Read on to discover five ways in which the digital workflows are revolutionizing the dental industry.
Low-Cost Mass Customization
While dentistry has always required high levels of customization, the industry has traditionally relied mostly on manual methods to create custom appliances. Today, digital workflows enable mass customization in a consistent, automated way, requiring less labor and incurring lower costs.
Everyone has a dentition—the pattern of development and arrangement of teeth—unique to them. Dental indications must, therefore, be made to match each individual patient’s anatomy. With traditional manual workflows, the quality of the finished products is highly dependent on the skills of a given technician. Achieving consistent and high-quality dental products with so many potential sources of error is incredibly difficult and expensive.
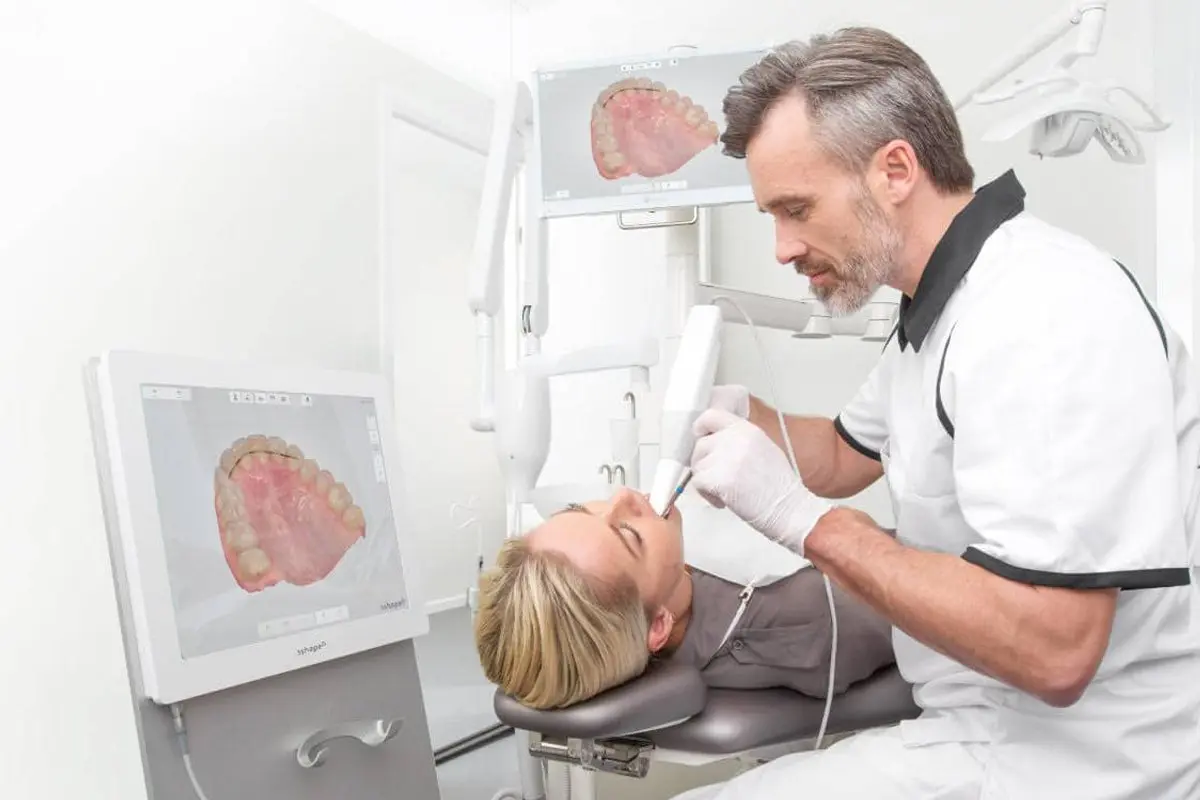
With digital workflows, each dental product is precisely detailed to the specifications dictated by the patient's anatomy. 3D printers are like Swiss-army knives—no other tool can produce such a wide variety of dental products with consistently high quality. Using dedicated materials, labs and practices can use 3D printers to produce orthodontic models, highly accurate crown and bridge models, surgical guides, castable or pressable restorations, aligners, retainers, long-term biocompatible dental products like splints or dentures and more.
Digital technologies simplify workflows, reduce the room for error and the amount of labor required, resulting in time and cost savings on both the lab's and practice's side.
Disrupting Orthodontics With Clear Aligners
Orthodontics as a dental specialty has come a long way since traditional metal wired braces. While still necessary in some complex cases, removable clear aligners provide an appealing alternative today and have been used to treat millions of patients.
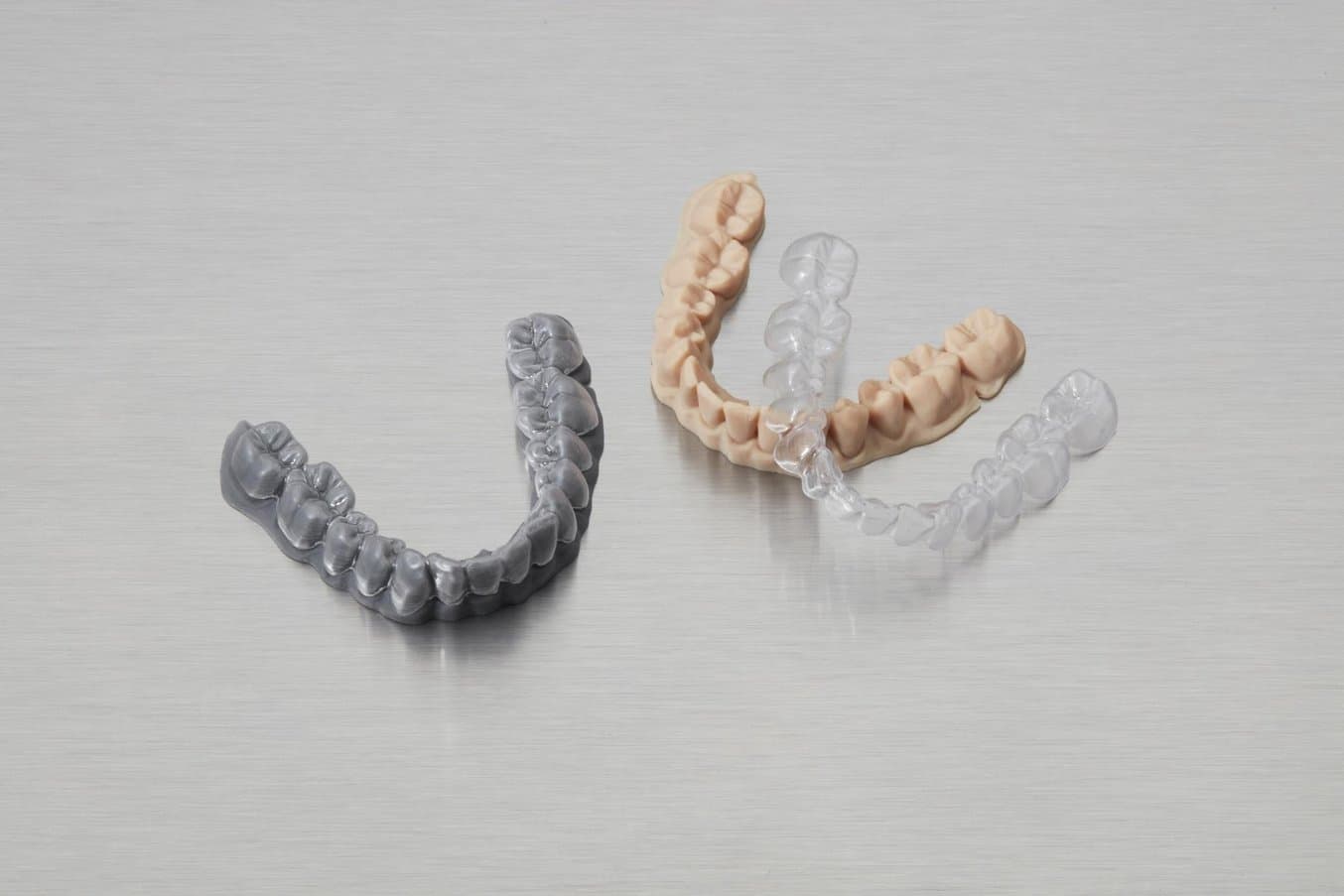
Clear aligners couldn't exist without digital technologies; their manufacturing process is a brilliant combination of multiple digital workflows. An orthodontist or dentist first captures an impression of a patient's dentition with a 3D intraoral scanner or takes a traditional impression for the lab to scan. The digital model provides a basis to plan the progressive stages between the current and desired teeth positions. Each stage is then 3D printed and the aligners are thermoformed over these 3D printed molds.
Traditionally, the 3D printers used in this process were large and complex to use and prohibitively expensive. Now, smaller format desktop 3D printers can create molds for thermoformed appliances, opening up the possibility for any lab or practice to produce aligners and retainers in-house and expand production without adding substantial overhead.
Ashford Orthodontics, the largest orthodontics laboratory in the UK produces thousands of clear retainers using 3D printed models.
Digital Implantology
Digital technologies can augment complex surgical procedures. CBCT, virtual placement planning, and surgical guides are becoming the new standards of care in implantology. With them, the accuracy of implant placement during surgery is all but guaranteed, the risk of surgical complications fall, and clinical results are improved overall. Let's look at the workflow-enhanced production of a surgical guide as an example.
To create a guide, implantologists combine intraoral scan data of a patient's dentition and anatomy of the patient osteotomy from a CBCT or cone beam scanner. Based on the anatomical data, practitioners use CAD software to plan treatment with high accuracy and then use a 3D printer to produce a guide that is ready to be used in surgery.
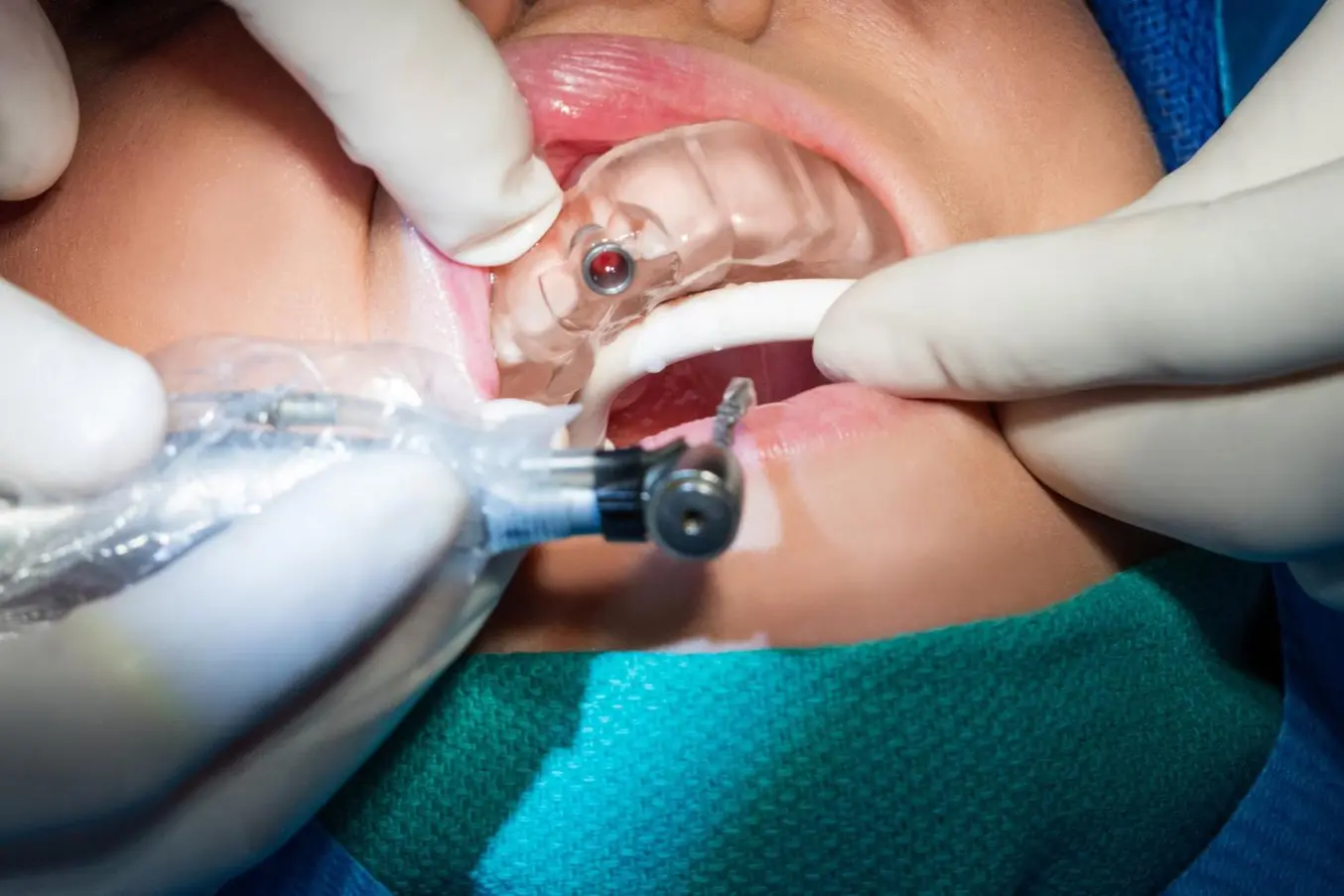
Formerly, the only ways of producing surgical guides was through milling or 3D printing on industrial 3D printers. But due to the complex and expensive machinery involved, these guides could easily cost hundreds of dollars, which made them cost-prohibitive in most cases. Now with desktop 3D printing, the costs are down by a factor of 10-100X, paving the way for guided surgeries to become the standard.
Digital Dentures
Traditional denture manufacturing is a time-consuming and labor-intensive analog workflow that involves multiple patient visits and production steps. It is a complex craft with a steep learning curve and dental labs increasingly struggle to find technicians with the advanced skills and expertise required to produce them.
Dentures are one of the latest innovations in digital dentistry. They offer an efficient and cost-effective manufacturing solution and a major step toward the overall simplification of the dental laboratory manufacturing process.
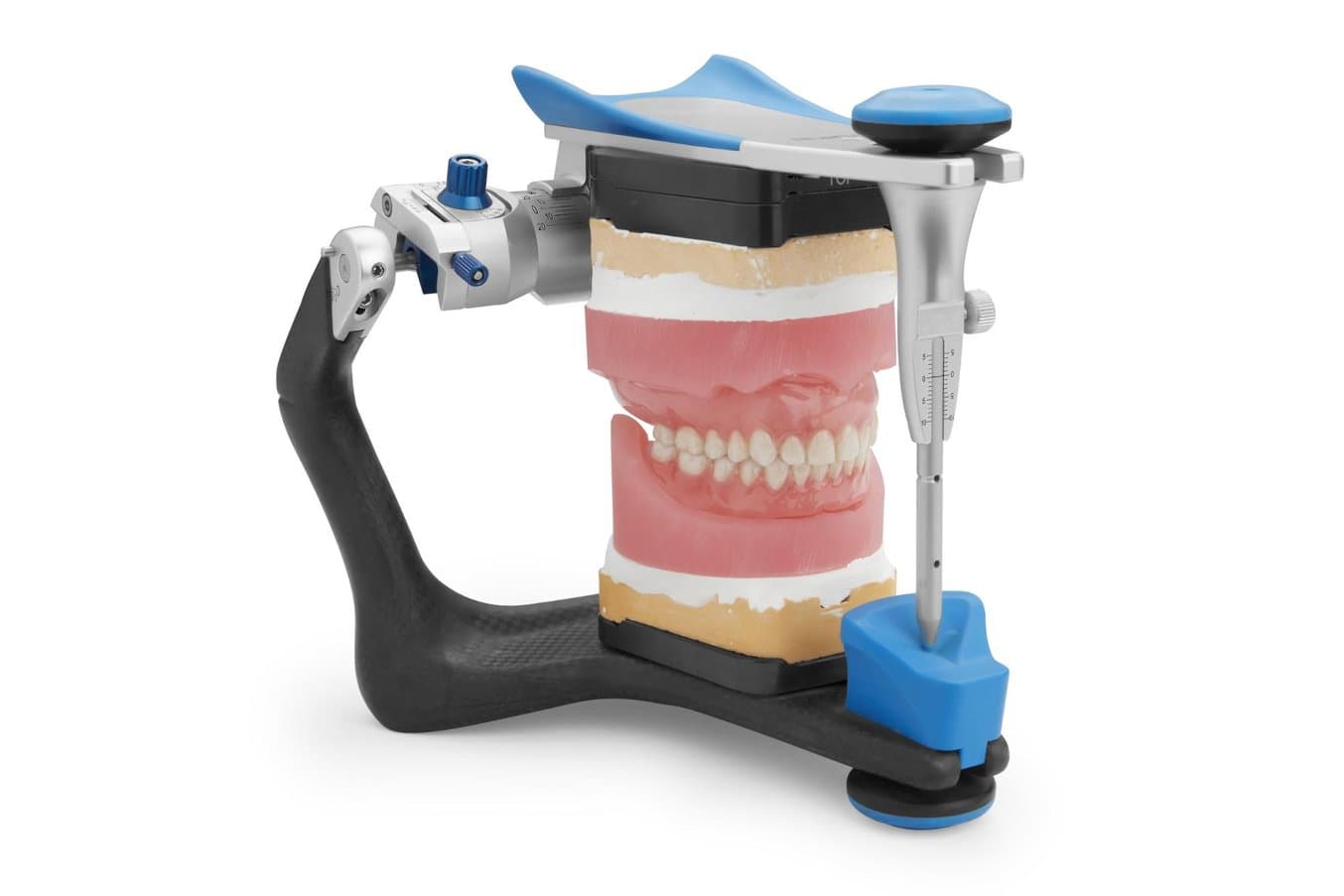
Denture production with the digital workflow includes fewer steps and less variability, resulting in a more consistent workflow for a high-quality end product every time. Digital denture designs are also reusable, shareable, modifiable, and easy to reproduce with 3D printing. The affordable hardware, lower material costs, and time savings (less labor) all contribute to a substantial cost advantage over their handcrafted counterparts.
Scanning solutions, software tools, and materials are developing rapidly to take digital dentures to their full potential. As they do, digital dentures are bound to replace or supplement the traditional workflow for an increasing share of the 50 million dentures produced a year globally and pave the way for more inclusive denture solutions for everyone who needs treatment.
Better Patient Experience
At the end of the day, it's the patients who stand to gain the most from the advances in digital dentistry.
Starting with the visit to the dentist or orthodontist, being able to visualize a dental procedure can be as reassuring for the patient as it is helpful for the practitioner. Virtual treatment planning, diagnostic wax-ups, and highly detailed replicas can help patients envision and understand the treatment they will be receiving in great detail, reducing anxiety and increasing patient acceptance.
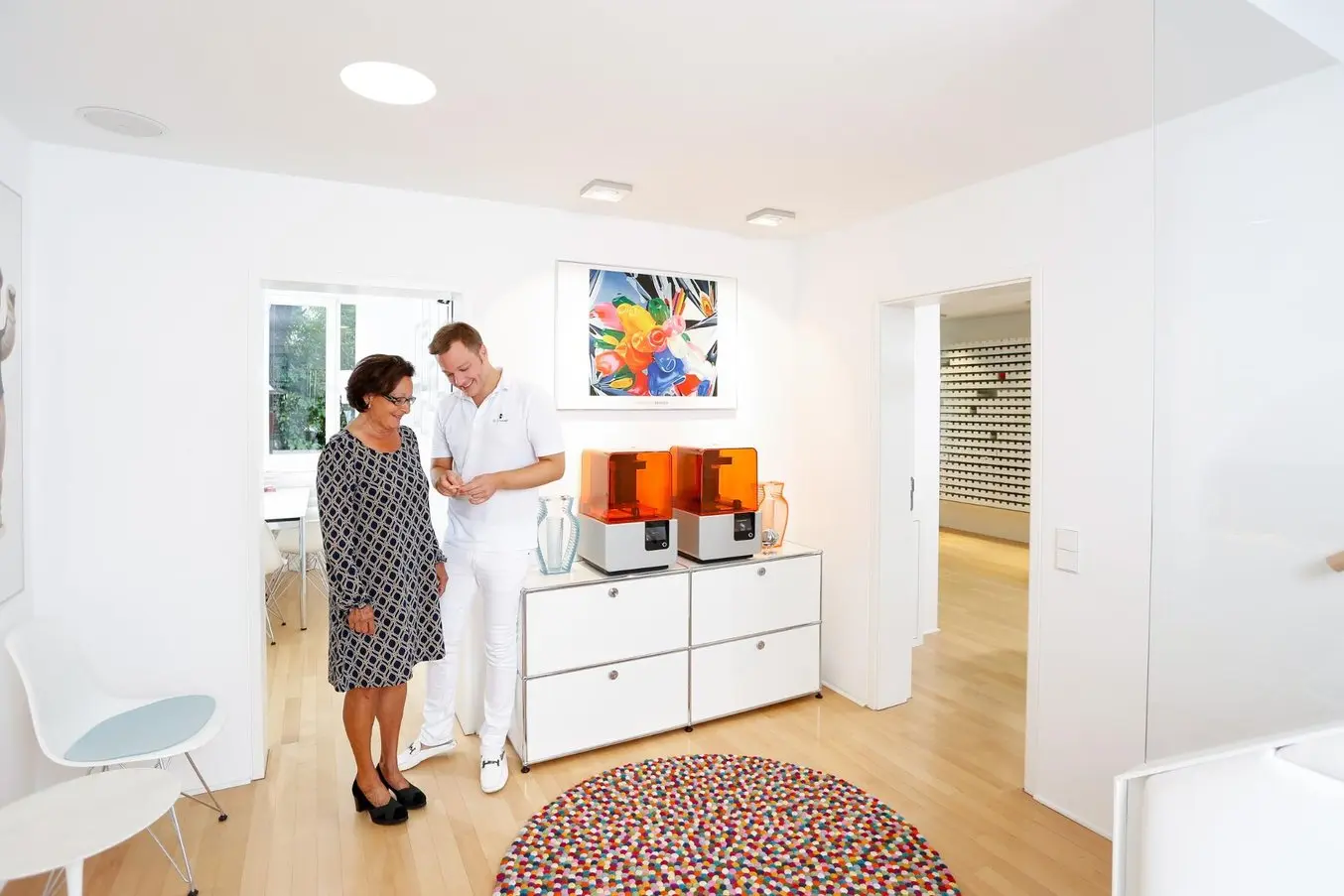
Considering workflow and treatment improvements, taking an impression of a patient's dentition with intraoral scanning is quicker and more comfortable than traditional alginate and PVS impressions. The products themselves can be more aesthetically pleasing (clear aligners) and treatments more accurate and less invasive (digital implantology and surgical guides). Processes are generally faster as digital elements remove superfluous steps, making the patient's visit quicker and easier.
Precise and consistent treatments mean that patients are vastly less likely to need to return for repeat work on the same problem, saving their time and money. But a satisfied patient is more likely to become a return customer and refer others, contributing to the long-term success of all dental businesses.
Get Started with Digital Dentistry
These are just some examples of the wider scope of changes that digital dentistry and 3D printing processes are bringing to the dental industry.
Despite the narrative of “traditional vs. digital workflows” used frequently to promote the latter, contemporary dental workflows can combine the best of both. The support of digital workflows translates to a plethora of new possibilities for the industry and a raft of improvements for the customer.
Find out more about how Formlabs is driving this change, learn about the range of dental indications, and request a free sample part for yourself to see the quality firsthand.
Request a Sample 3D Printed Part