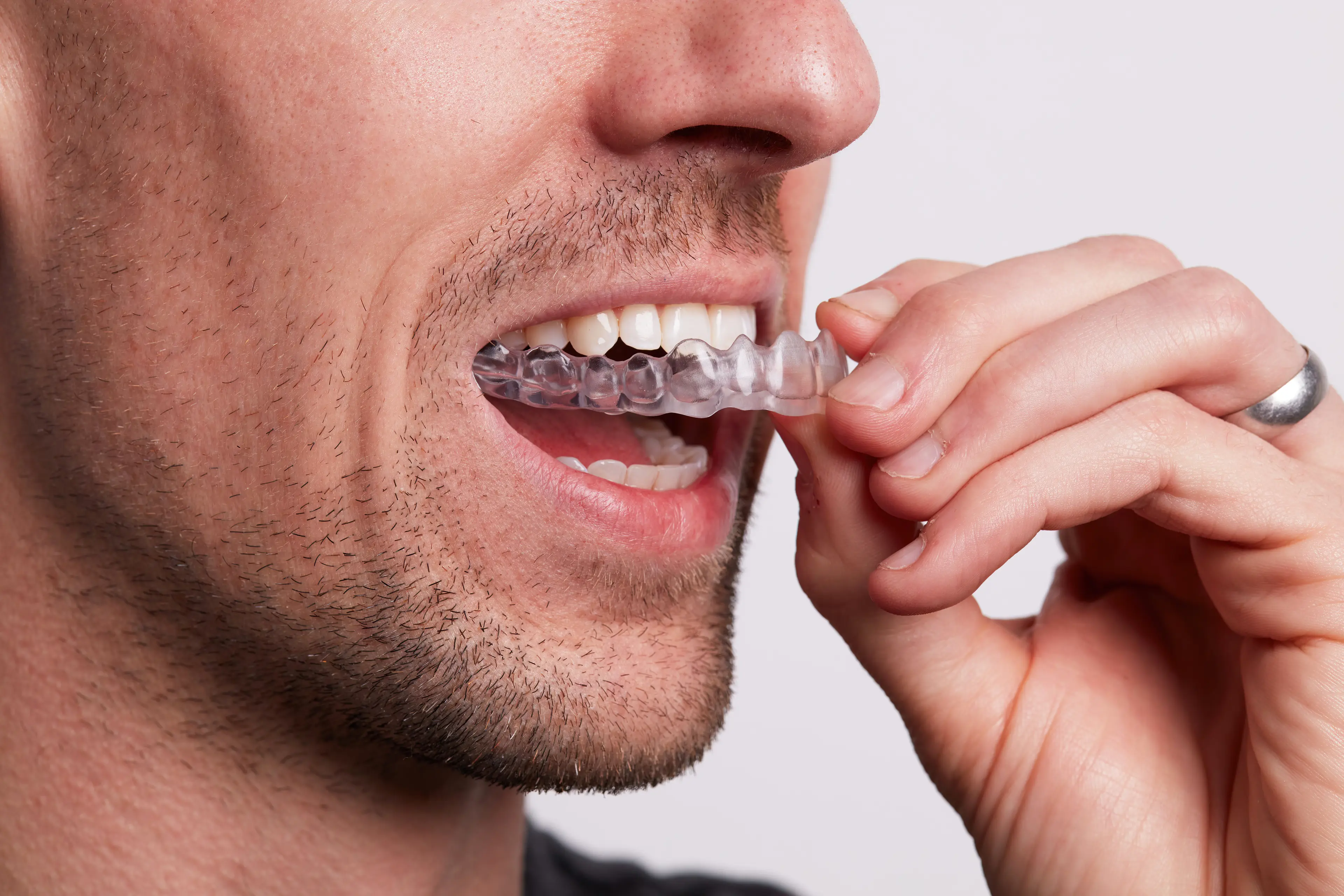
3D Printing Occlusal Splints and Night Guards With Formlabs SLA 3D Printers
Formlabs provides two distinct materials for splint fabrication:
-
Dental LT Clear Resin: A fracture-resistant option for rigid occlusal splints and guards.
-
Dental LT Comfort Resin: A durable material designed for comfortable, flexible occlusal splints, night guards, and bleaching trays.
These resins are biocompatible Class II/IIa materials approved for long-term intraoral use in both the U.S. and EU. Both materials can be easily polished to achieve high optical transparency and are formulated to resist discoloration over time.
This guide details the complete workflow for producing 3D printed occlusal splints using Formlabs SLA 3D printers, ensuring precise outcomes at every step.
3D Printing Occlusal Splints and Night Guards With Formlabs SLA 3D Printers
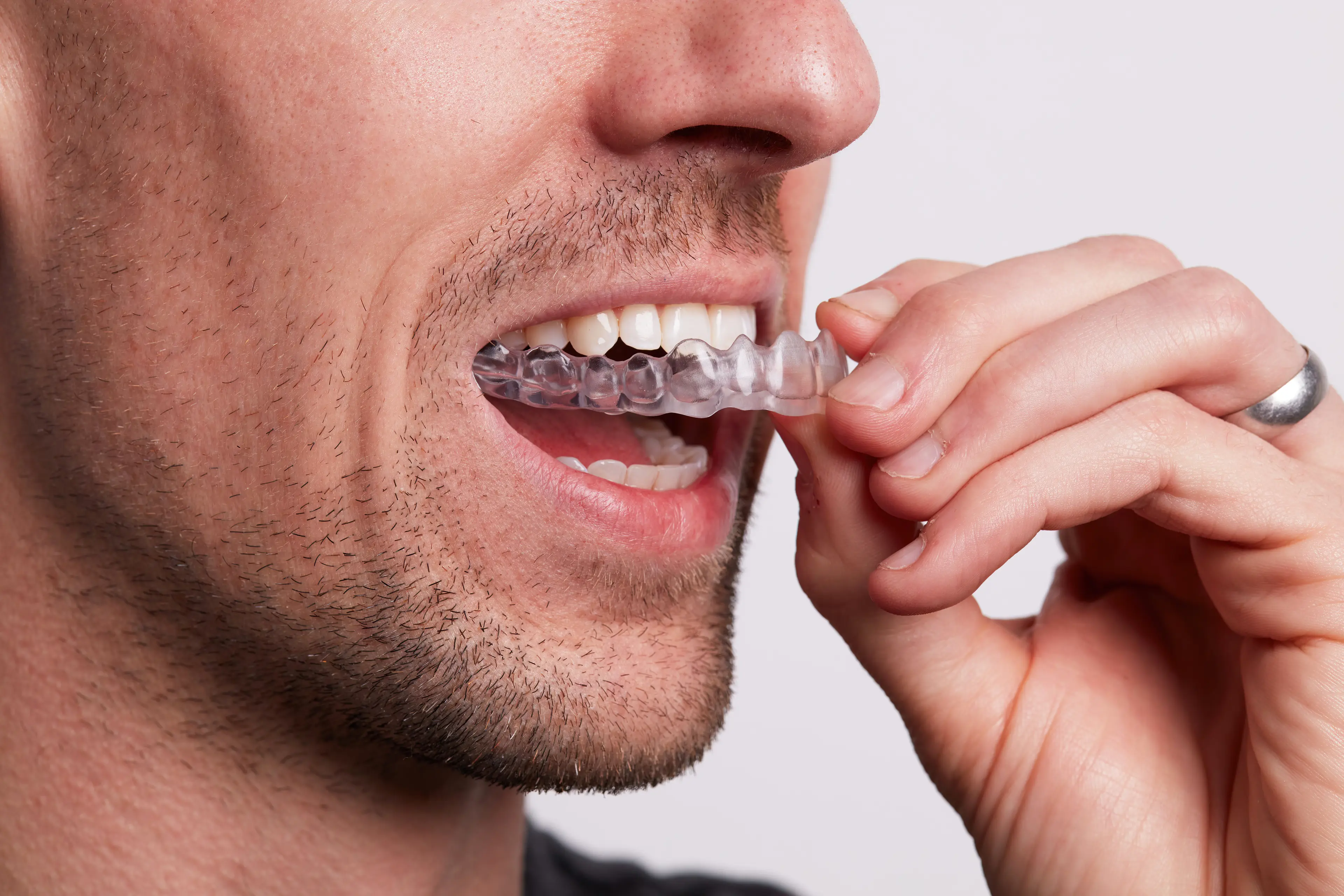
Formlabs provides two distinct materials for splint fabrication:
-
Dental LT Clear Resin: A fracture-resistant option for rigid occlusal splints and guards.
-
Dental LT Comfort Resin: A durable material designed for comfortable, flexible occlusal splints, night guards, and bleaching trays.
These resins are biocompatible Class II/IIa materials approved for long-term intraoral use in both the U.S. and EU. Both materials can be easily polished to achieve high optical transparency and are formulated to resist discoloration over time.
This guide details the complete workflow for producing 3D printed occlusal splints using Formlabs SLA 3D printers, ensuring precise outcomes at every step.
Essentials
Provided by the Dentist
-
A physical or digital impression of the patient’s dentition
-
A prescription with desired type of occlusal splint
Required Hardware and Materials
Made by Formlabs
-
Resin Tank for each resin
-
Form 4 Mixer for each resin
-
Form 4 Build Platform or Form 4 Flex Build Platform
-
Dental LT Clear V2 Resin or Dental LT Comfort Resin
-
Form Wash (2nd Generation) or Form 4 Finish Kit
-
Form Cure (2nd Generation) or Form Cure
Made by Third Parties
-
A dental handpiece and tools for acrylics
-
Isopropyl alcohol (IPA)
-
Optional:
-
Desktop scanner ( to digitize a physical impression )
-
A steam cleaner
-
An ultrasonic bath
-
Pumice and polishing compound
-
Required Software
Made by Formlabs
Latest PreForm Dental and Firmware versions
Made by Third Parties
Dental design software or outsourcing to a dental design provider
1. Scan
Dental design software requires a digital impression of the patient’s anatomy in order to design an occlusal splint or guard. To acquire this data, scan the patient directly with a 3D intraoral scanner or scan a physical impression or a poured model with a desktop 3D scanner.
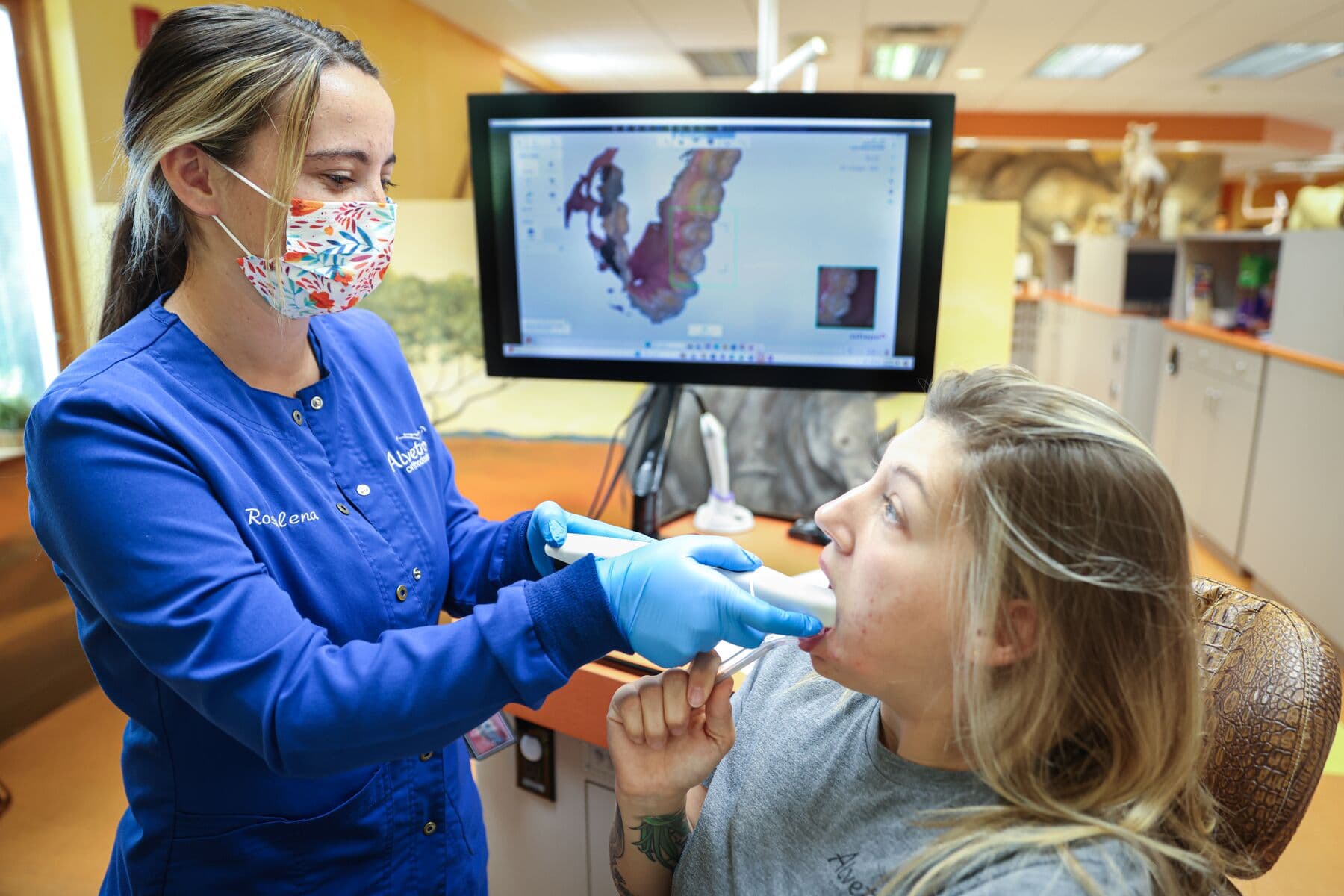
2. Design
2.1 Design the Appliance
There are several dental software options for digitally designing occlusal splints. In this application guide, we will be outlining parameters for 3Shape Dental System and ExoCAD. You can download Formlabs material libraries for 3Shape here or get Formlabs exocad material presets from exocad’s dentalshare platform.
There are also outsourced dental CAD providers where you can send a digitized impression for design creation.
General Construction Requirements
Please check the appropriate manufacturing guide for material-specific construction requirements such as minimum occlusal surface thickness and minimum wall thickness.
3Shape & exocad Settings
Dental LT Clear (V2): Offset from 0.05 to 0.10 mm (depending on the desired snugness and case design, the smaller the value the tighter the fit).
Dental LT Comfort: Offset from 0.01 to -0.03 mm (depending on the desired snugness and case design; the smaller the value, the tighter the fit).
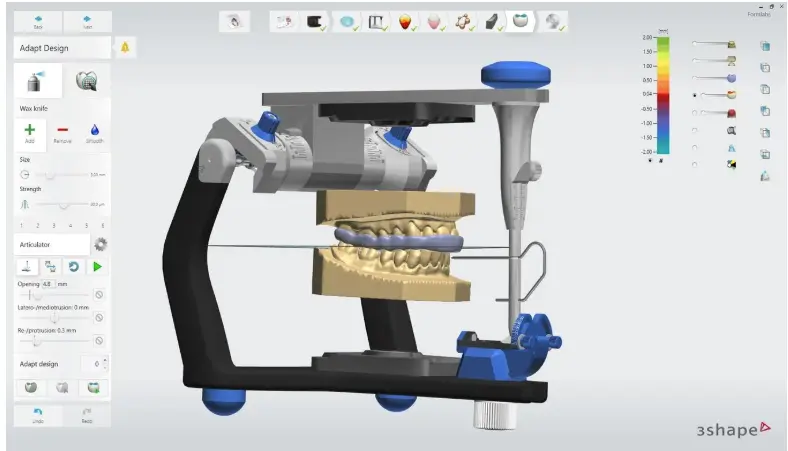
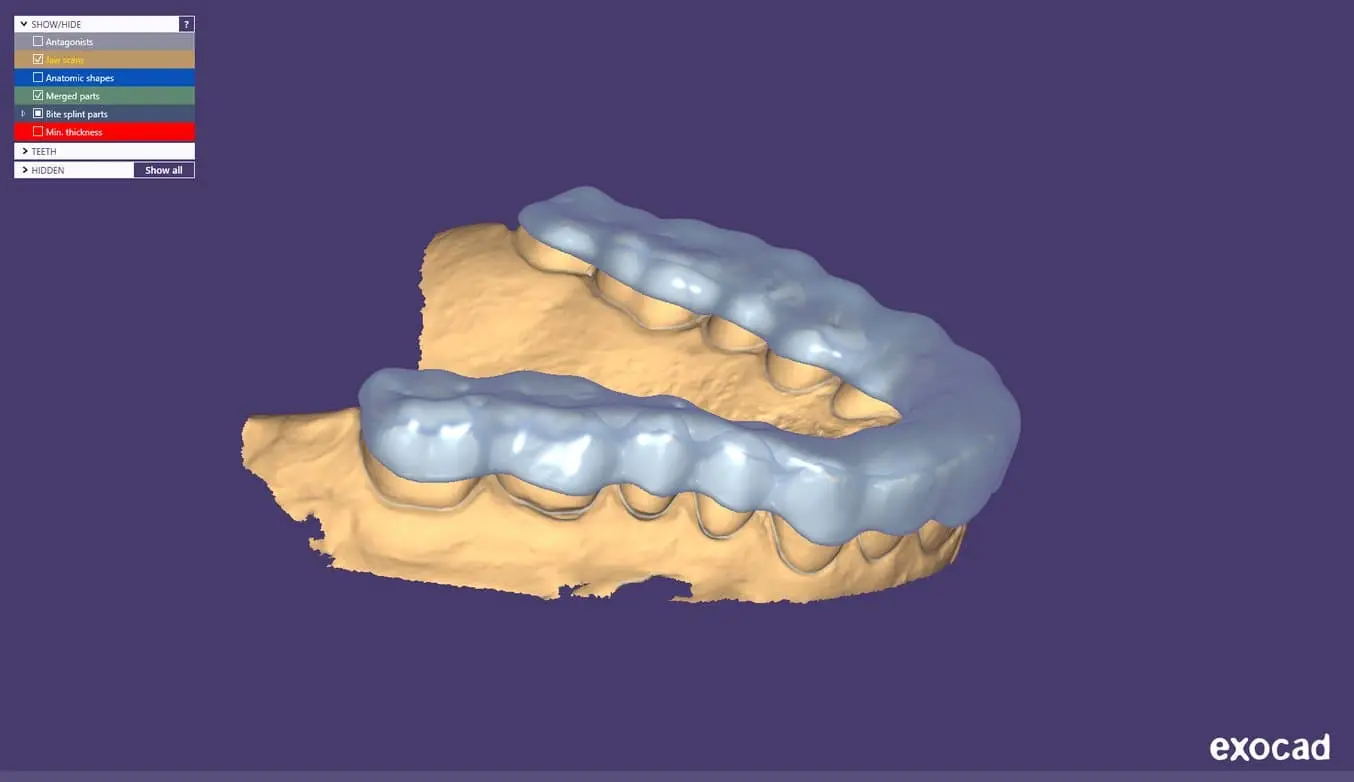
2.2 Export the STL File
Once the case has been designed to specification, manufacturing can begin. The majority of dental design software generates a manufacturing file in STL format. Locate the file and move it into the print preparation software, PreForm Dental.
3. Print
Note
Use latest PreForm and Firmware versions
3.1 Import File(s)
Follow the instructions to activate Dental Workspace for PreForm. Open PreForm and set up your splint print job using an adequate preset. You can find instructions here on:
-
How to activate and use Dental Workspace from PreForm
-
How to create a preset
PreForm Dental Workspace will take care of importing, orienting, and supporting your splint in an optimal way.
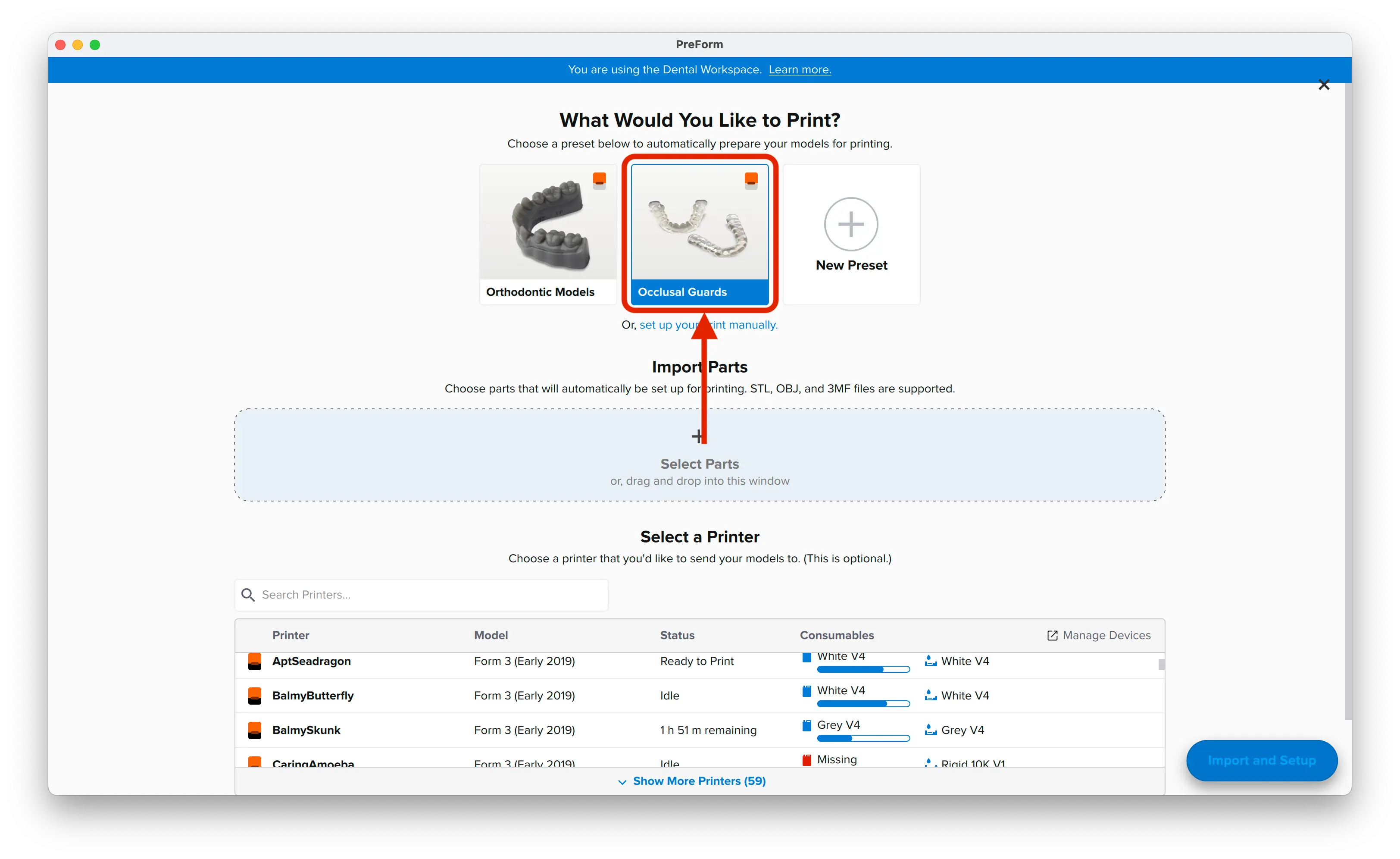
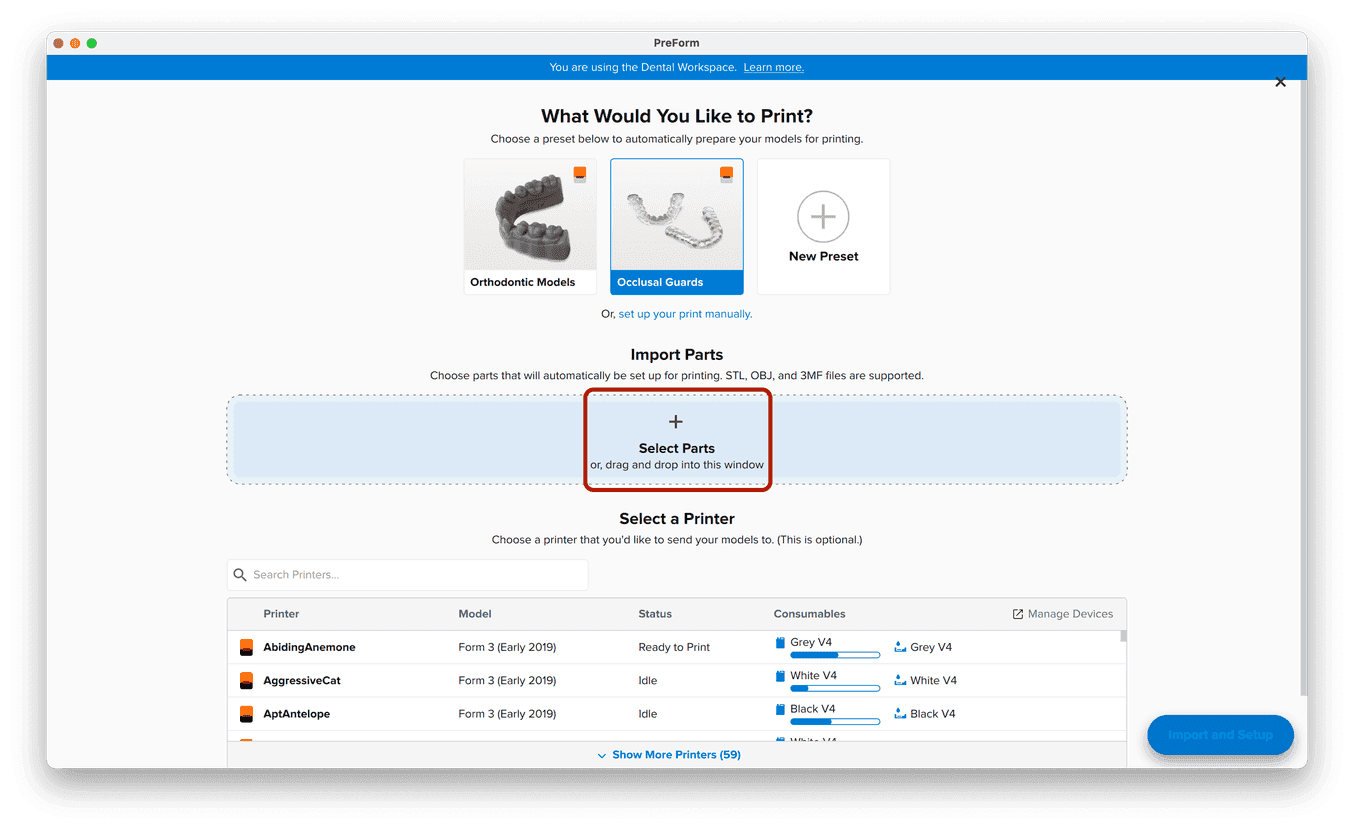
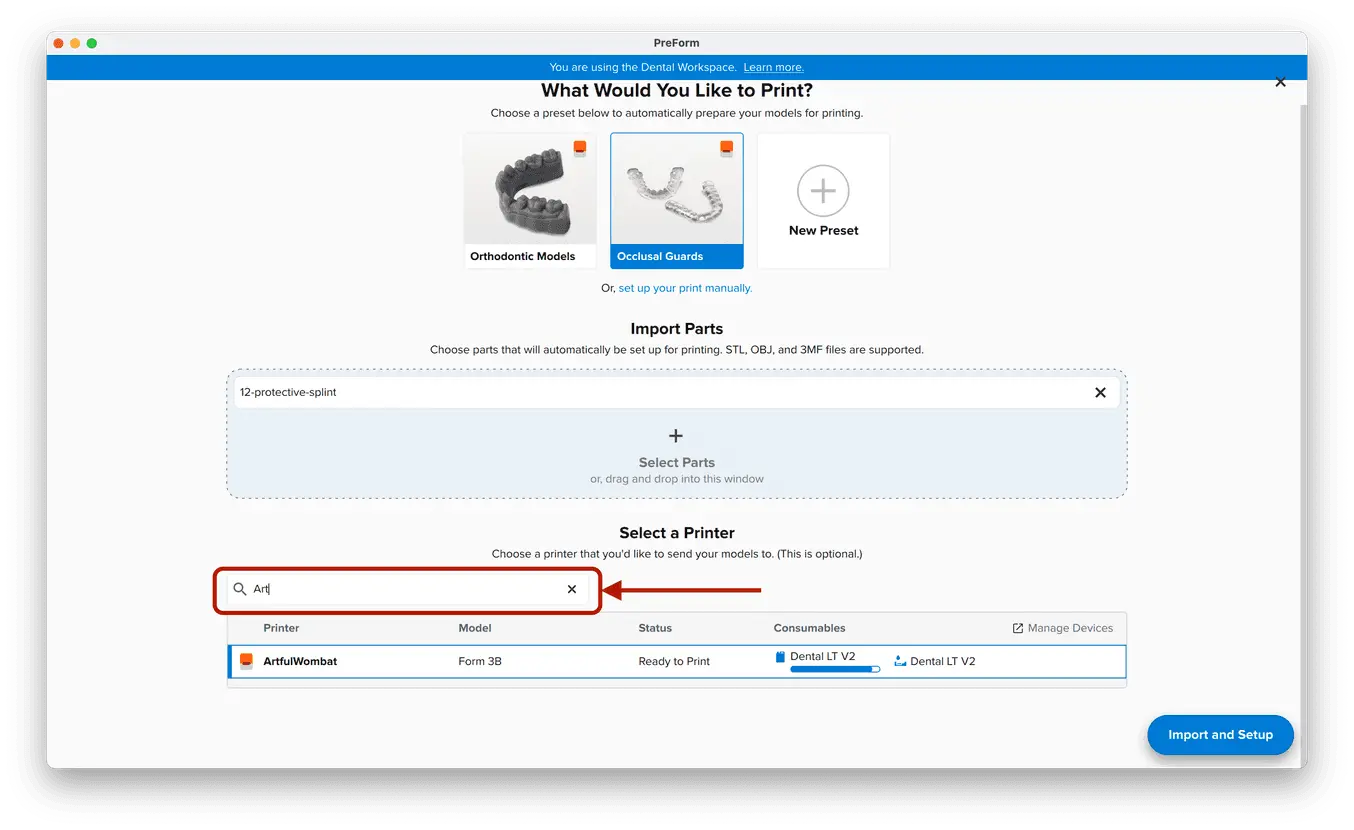
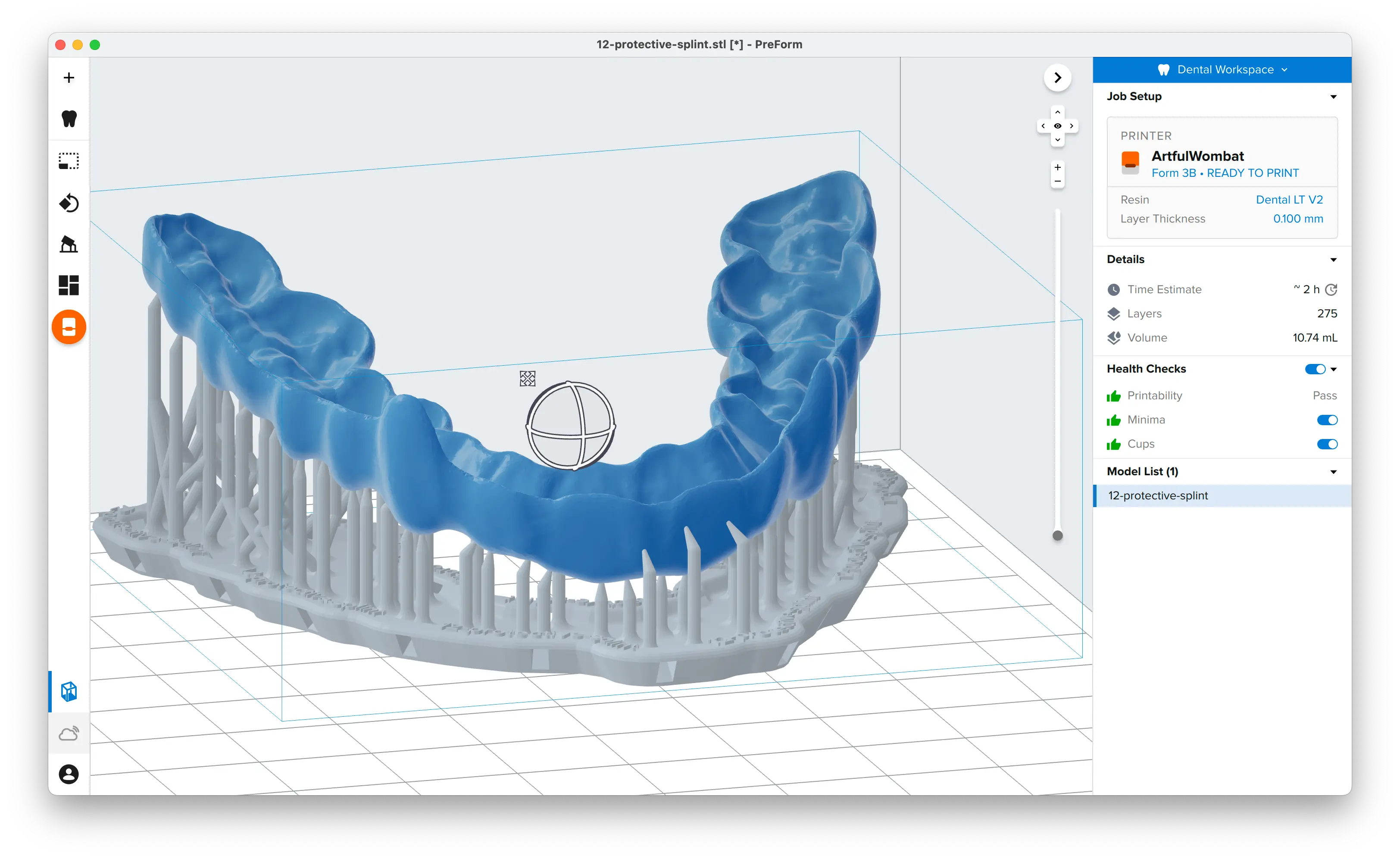
3.2 Adjust Touchpoints
The PreForm Dental Workspace auto-generates supports based on material properties. Your supports might be at unsuitable areas like antagonist contact impressions or dynamic occlusal contact surfaces. For optimal results, we recommend entering the Support menu and adjusting touchpoints as needed.
Be sure not to reduce the number of supports and always properly support the parts of the splint closest to the build plate.
PreForm will indicate in red what areas might require additional support.
Confirm under the Job Info menu bar on the right side of the window that Printability has green thumbs-up.
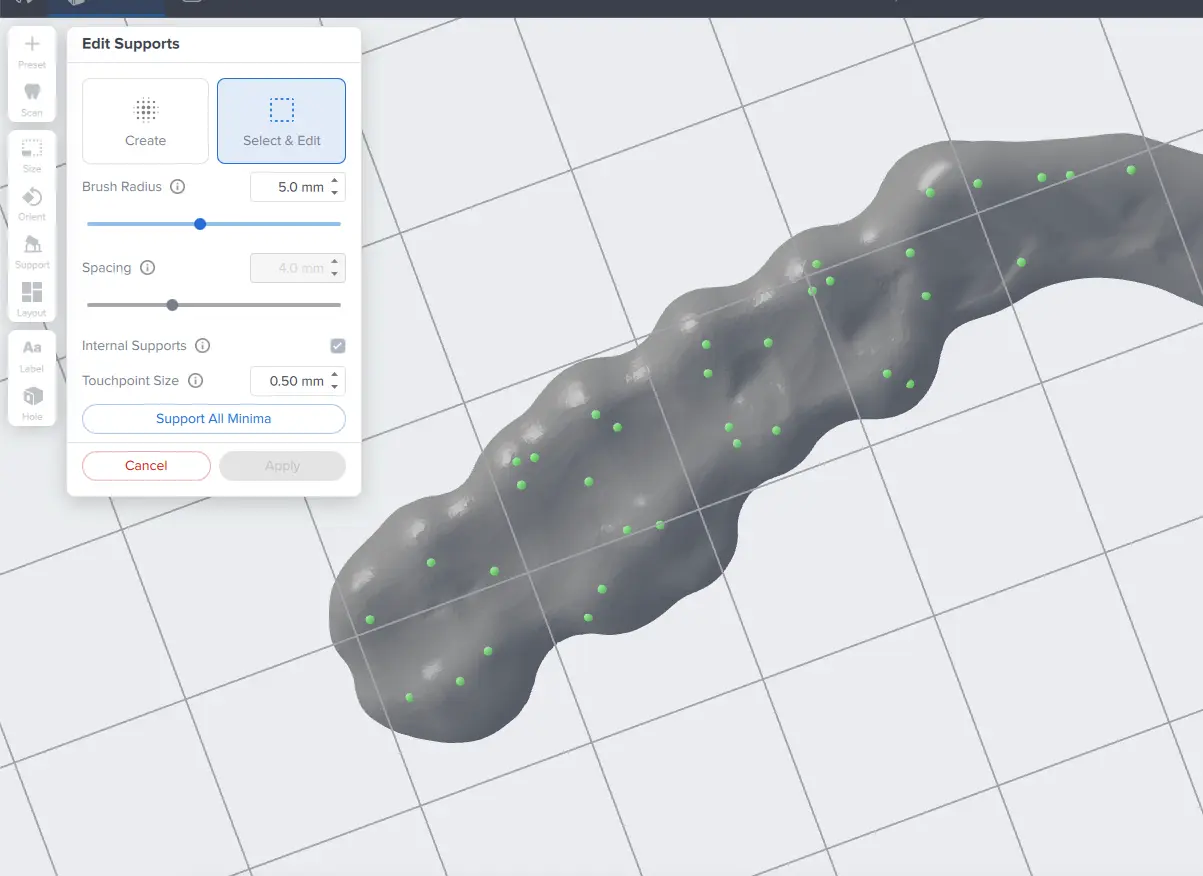
3.3 Layout
For normal printing, it is best to place parts toward the middle of the build plate.
When printing multiple cases, overlapping rafts can optimize the use of the build volume and save material.
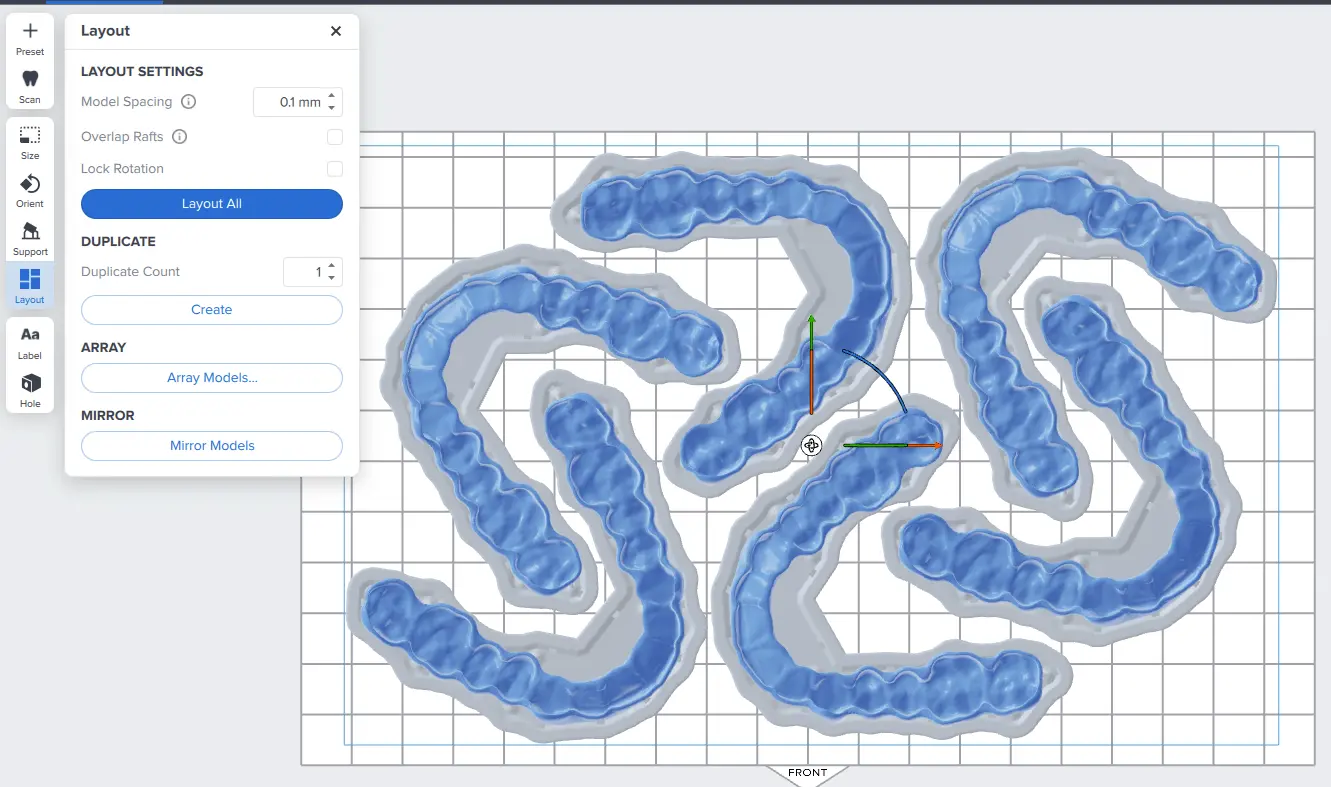
3.4 Sending the Job to the Printer
Send the job to the printer by clicking the orange printer icon on the left.
The Print dialog box will open. Click the orange Print Now or Upload Job button to send the job to the printer (whether you see one or the other button in this dialog depends on the current configuration of the selected printer).
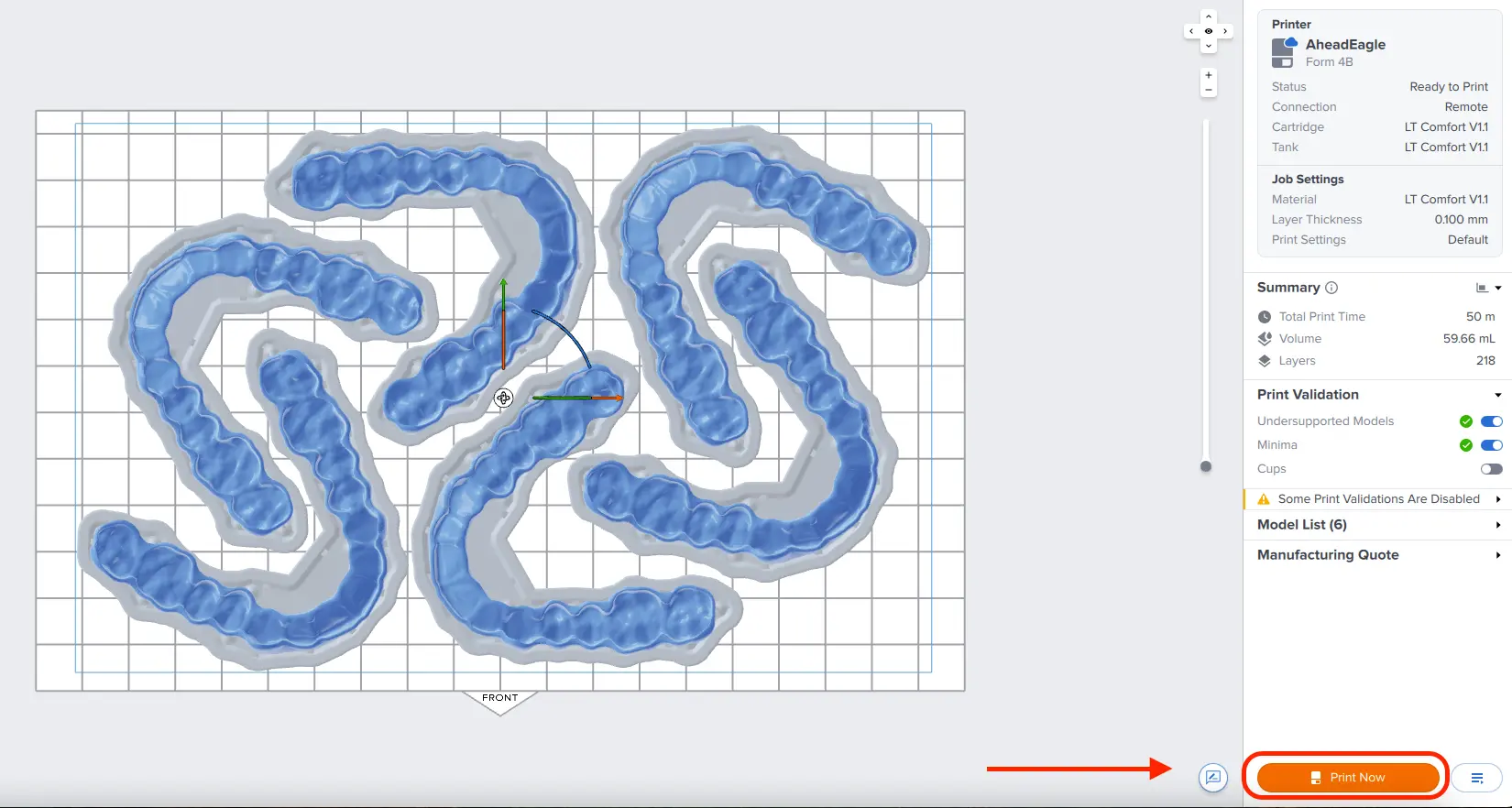
3.5 Set Up the Printer
Shake the splint material cartridge and then insert the cartridge, a build platform, and a compatible resin tank into the Form 4B 3D printer.
-
Begin printing by selecting the print job from the printer’s touch screen
-
Follow any prompts or dialogs shown on the printer screen
-
The printer will automatically complete the print
Attention
For full compliance and biocompatibility, splint materials require a dedicated Resin Tank and Build Platform. Only use the Form Wash with other Formlabs biocompatible resins, such as Surgical Guide Resin.
4. Post Processing
Caution
Always use gloves when handling uncured resin and parts.
Note
Post processing steps for Dental LT Clear Resin (V2) and Dental LT Comfort Resin are different. Please refer to your splint material’s manufacturing guide for the appropriate details.
4.1 Part Removal
Remove printed parts from Form 4 Flex Build Platform by pushing the quick release handles. Use a spatula if you printed on the Form 4 Build Platform.
Tip
Printed parts can also be washed directly on the build platform in the Form Wash.
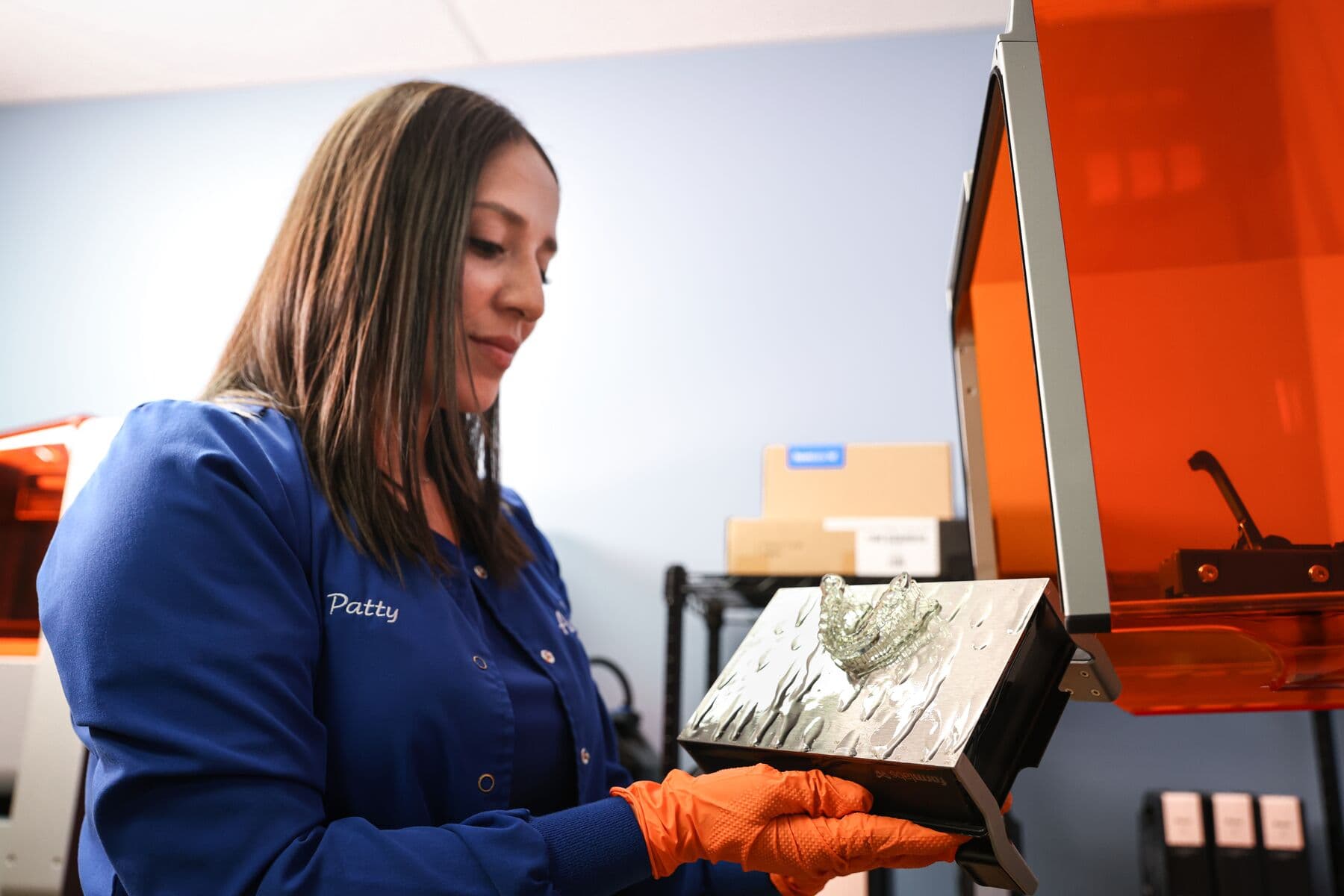
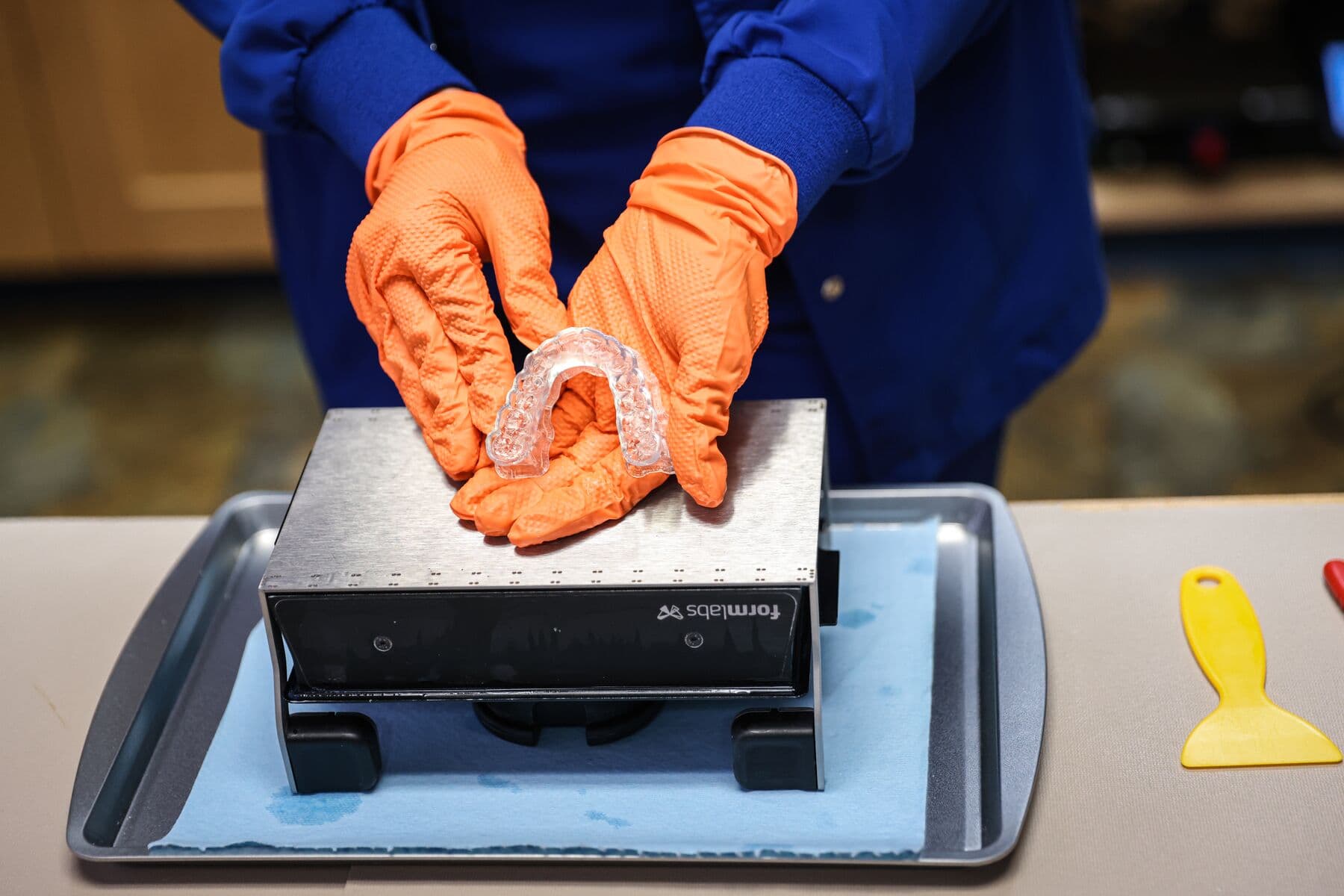
4.2 Washing
Precautions
-
When washing the printed part with solvent, it should be in a properly ventilated environment with proper protective masks and gloves.
-
Expired or unused resin shall be disposed of in accordance with local regulations.
-
IPA shall be disposed of in accordance with local regulations.
-
Use a dedicated wash for biocompatible parts to avoid contamination
Place the printed parts in a Form Wash (2nd Generation) filled with isopropyl alcohol (IPA) and wash them using the recommended wash time as specified in the manufacturing guide for your splint material.
Alternatively, an ultrasonic wash unit may be used, see manufacturing guide for specific directions.
Make sure the parts are fully submerged in IPA when washing.
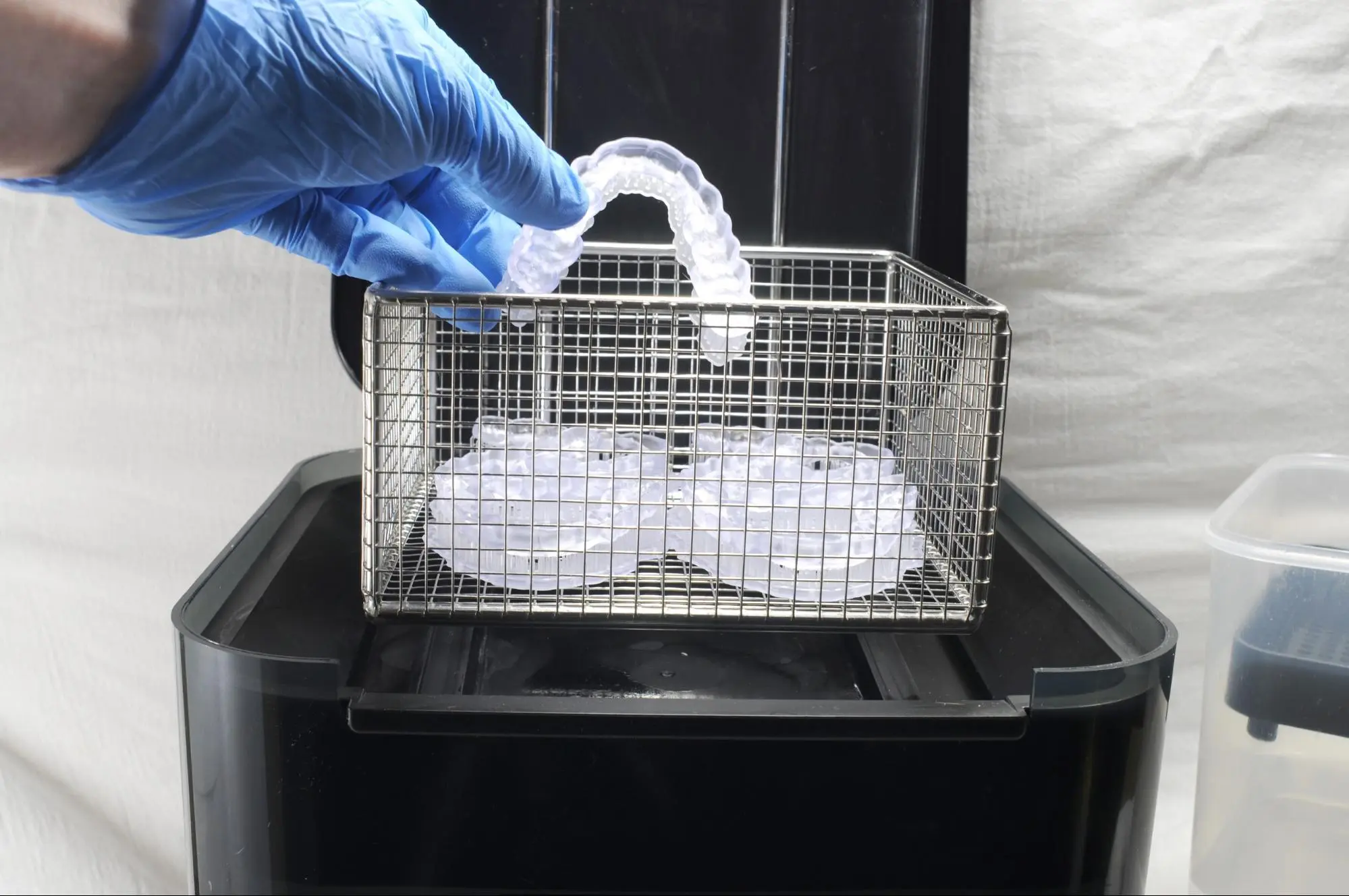
Notice
Exceeding wash duration may affect dimensional accuracy and performance of printed parts over time.
Tip
Using a squeeze bottle of fresh IPA and compressed air can help make parts clean, especially in deep parts of the intaglio anatomy. Use compressed air to blow dry.
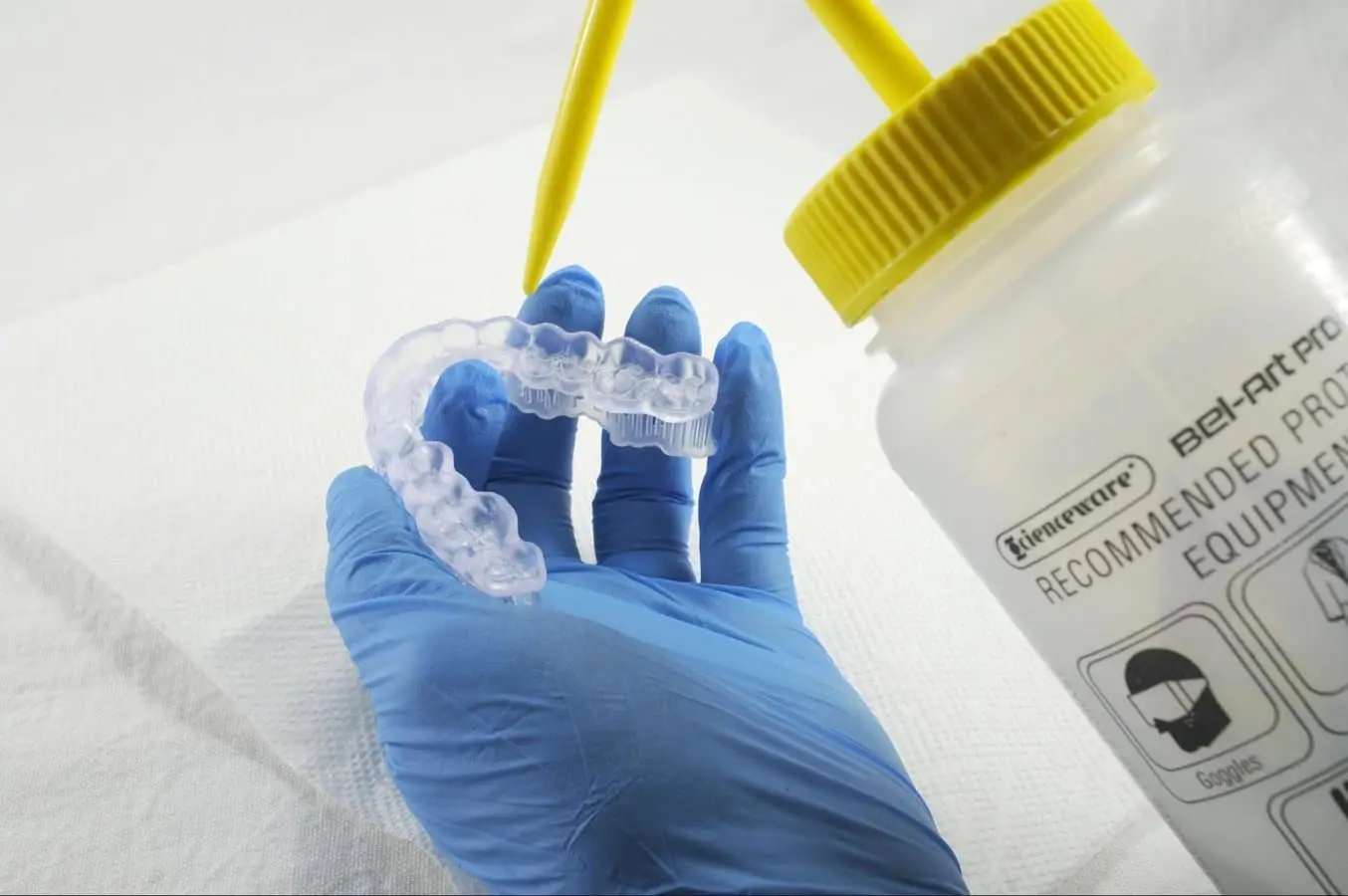
4.3 Drying
Notice
For optimal mechanical properties and biocompatibility, it is essential to observe the recommended drying times after washing the printed parts in alcohol, before placing them in the Form Cure.
Remove parts from the IPA and leave to air dry at room temperature. Refer to your resin’s manufacturing guide for the exact drying time.
Inspect printed parts to ensure that they are clean and dry.
No residual alcohol, excess liquid resin, or residue particles may remain on the surface before proceeding to subsequent steps.
4.4 Post-Curing
Place the dried printed parts in a Form Cure and post-cure using the recommended post-cure settings for your splint material. Please refer to the manufacturing guide.
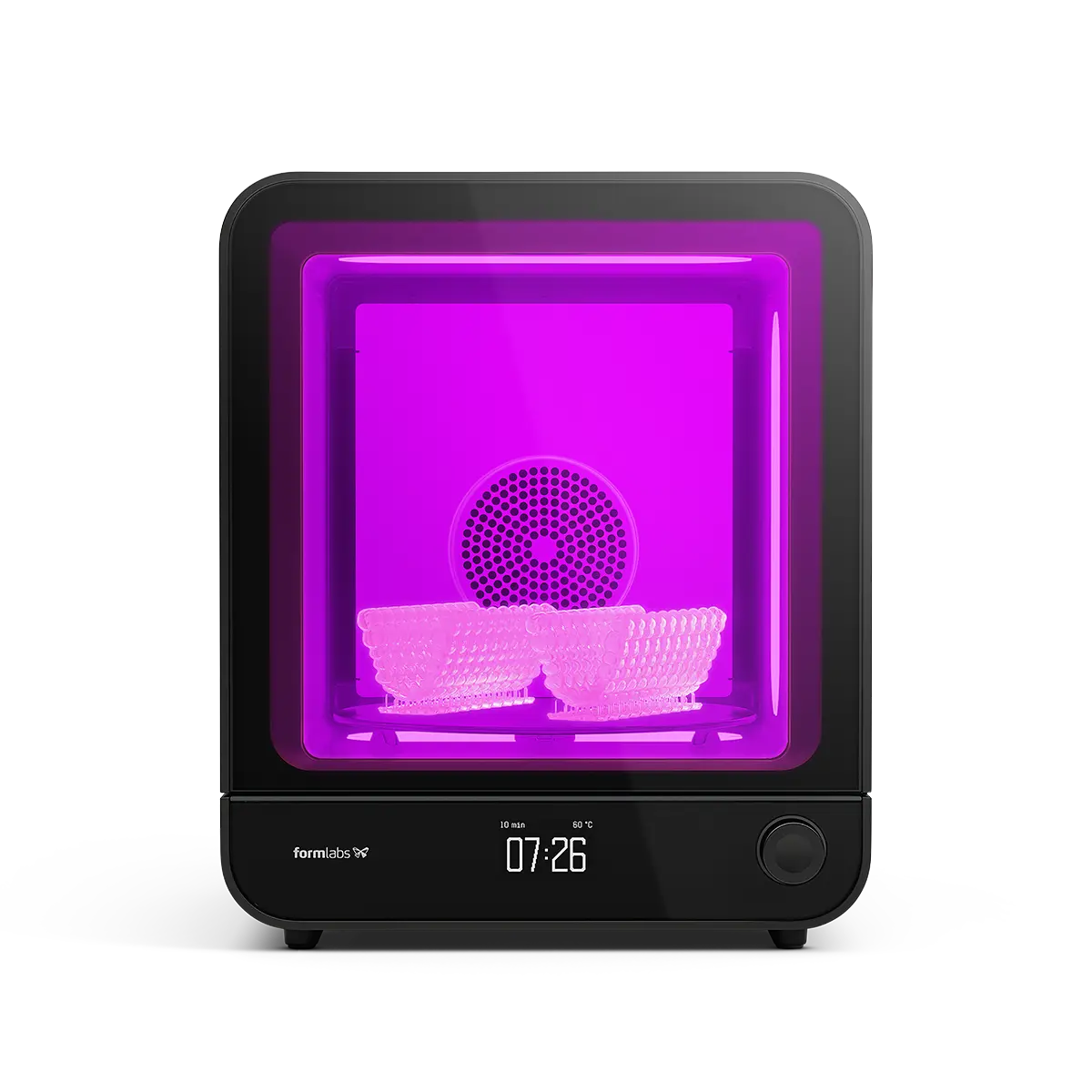
4.5 Support Removal
Supports can be removed using a cutting disk or sharp tweezers.
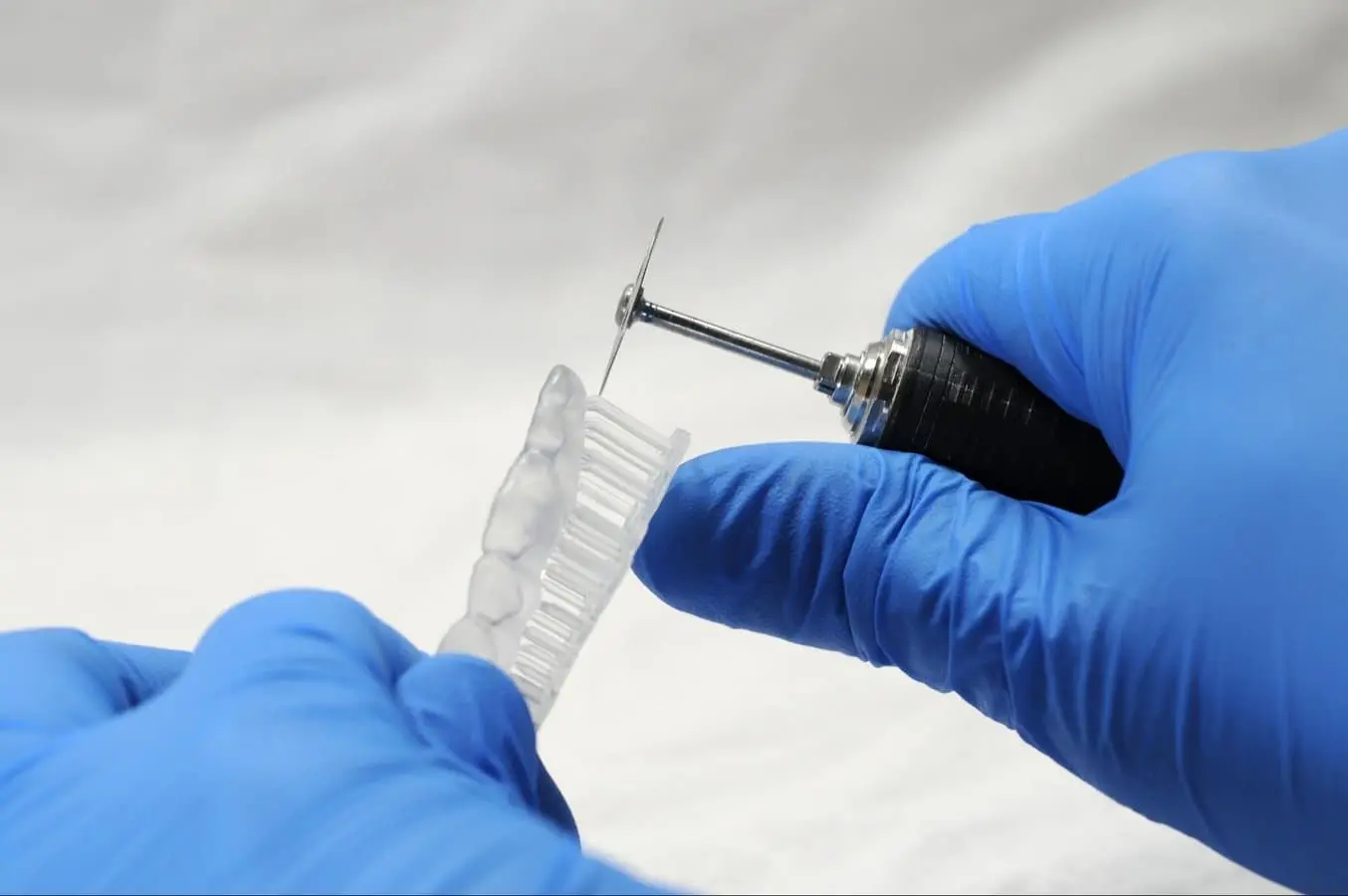
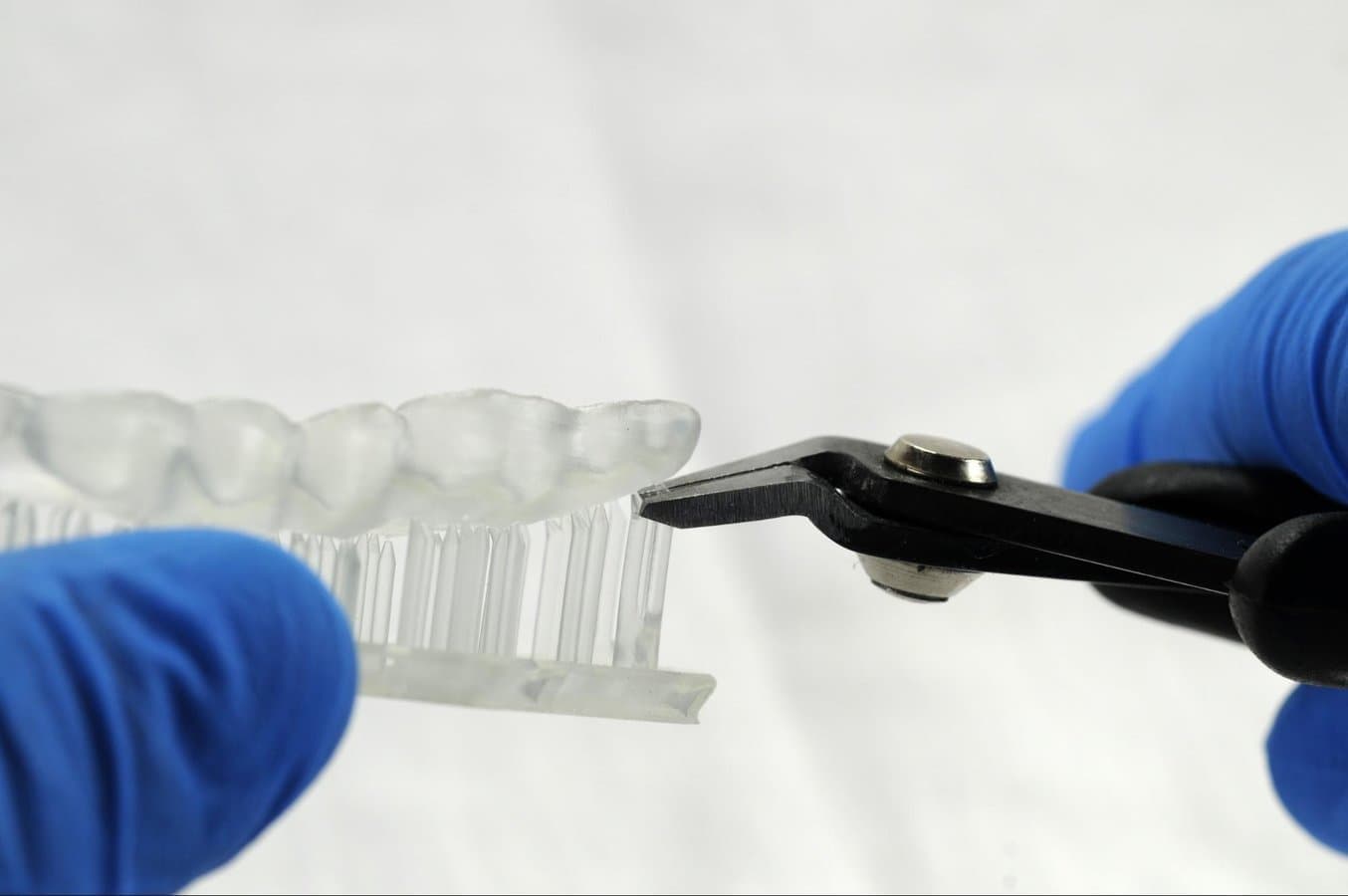
Tip
While ripping the supports from the part might be quicker, it can leave divots in the part. We recommend cutting the supports off individually.
Inspect the appliance. Discard and reprint the part if any cracks are detected.
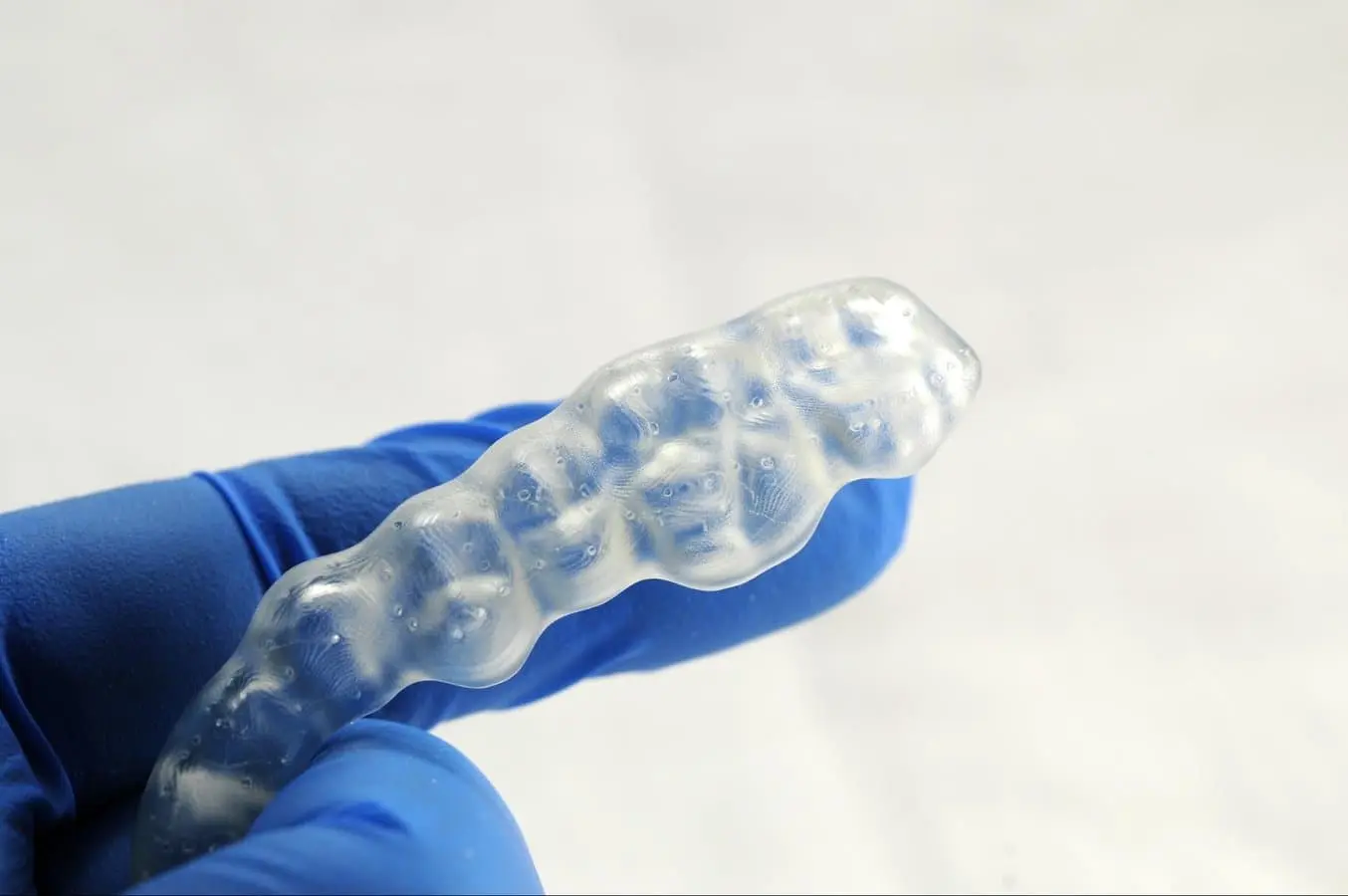
4.6 Finishing and Polishing
Using a handpiece and a carbide cutter or universal silicone wheel, smooth the support surfaces. The tools and polishing compounds employed for conventional acrylic appliances are suitable. For a high-gloss finish, the quickest and simplest method involves using a lathe with pumice and a high-gloss polishing compound designed for acrylics.
For dental practices without lathe access, the same outcome can be achieved as explained in this video.
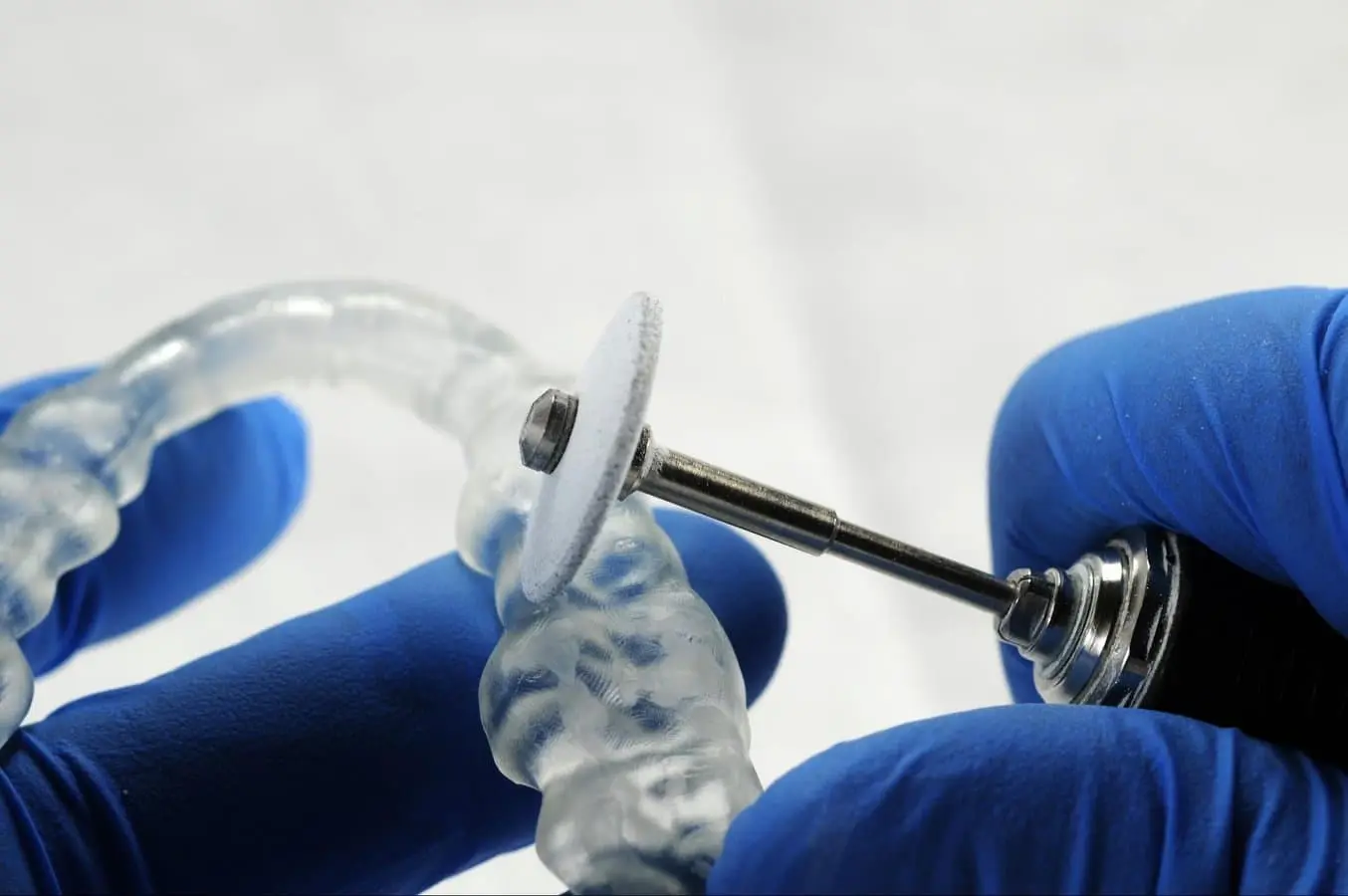
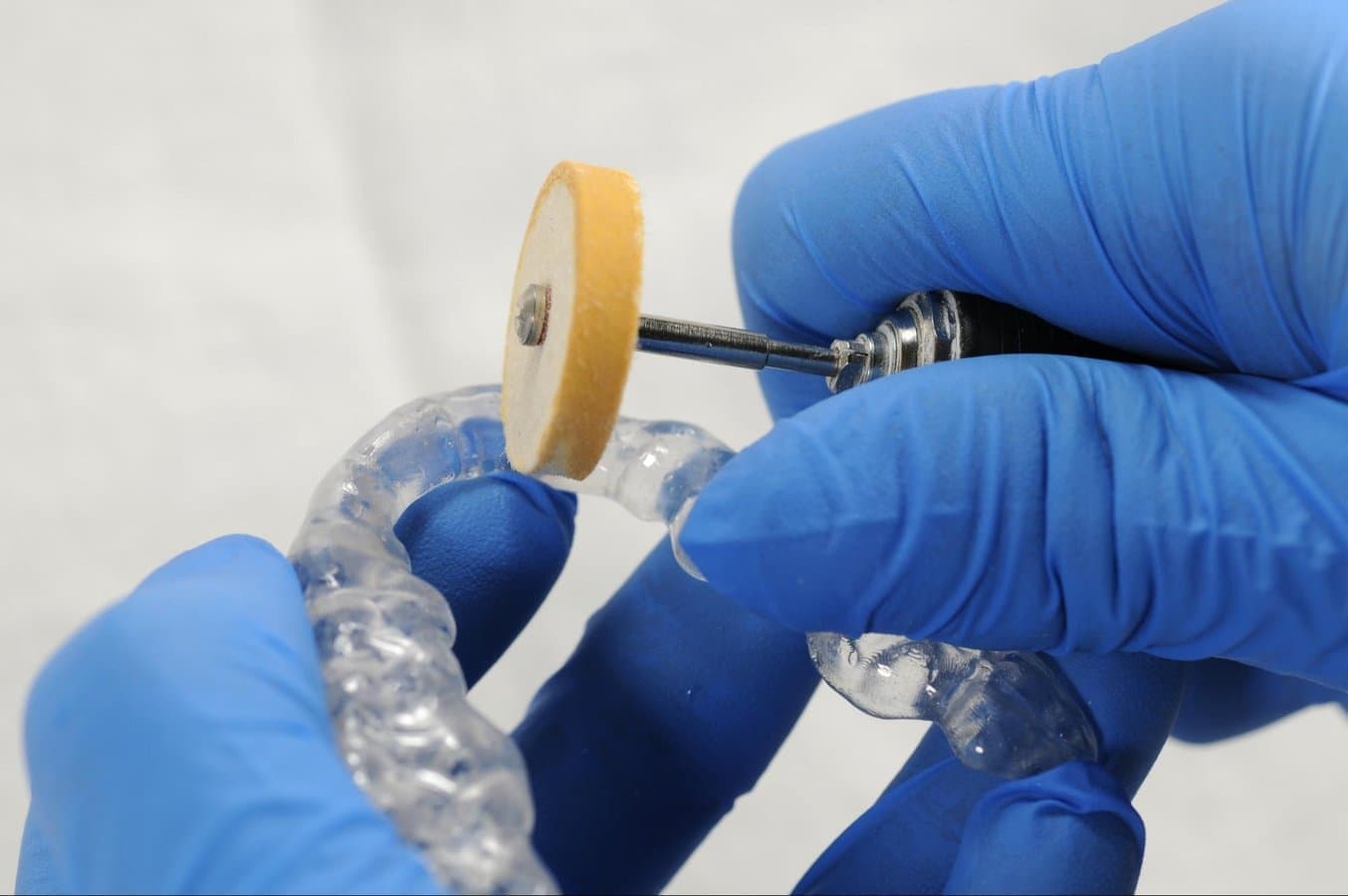
Optional
Verify the vertical dimension of the appliance and make adjustments as needed.
5. Care Instructions
Fully post-processed parts can be cleaned and disinfected. Please check the appropriate manufacturing guide for your splint material for detailed recommendations.