Comment le flux de travail numérique et l'impression 3D permettent des partenariats avec plus de 160 cabinets dentaires en Italie
En 2011, Mimmo Castellana a fondé SmileLine Allineatori Invisibili, un laboratoire spécialisé dans l'orthodontie invisible situé à Mola di Bari. Aujourd'hui, grâce au flux de travail numérique, SmileLine travaille en partenariat avec plus de 160 cabinets dentaires dans toute l'Italie et produit jusqu'à 100 modèles et plaques occlusales par jour grâce aux imprimantes Formlabs.
Lisez la suite pour savoir ce qui a motivé Mimmo à se tourner vers l'impression 3D pour produire les modèles en interne plutôt que de faire appel à des sous-traitants, comme c'était autrefois la norme dans ce secteur.
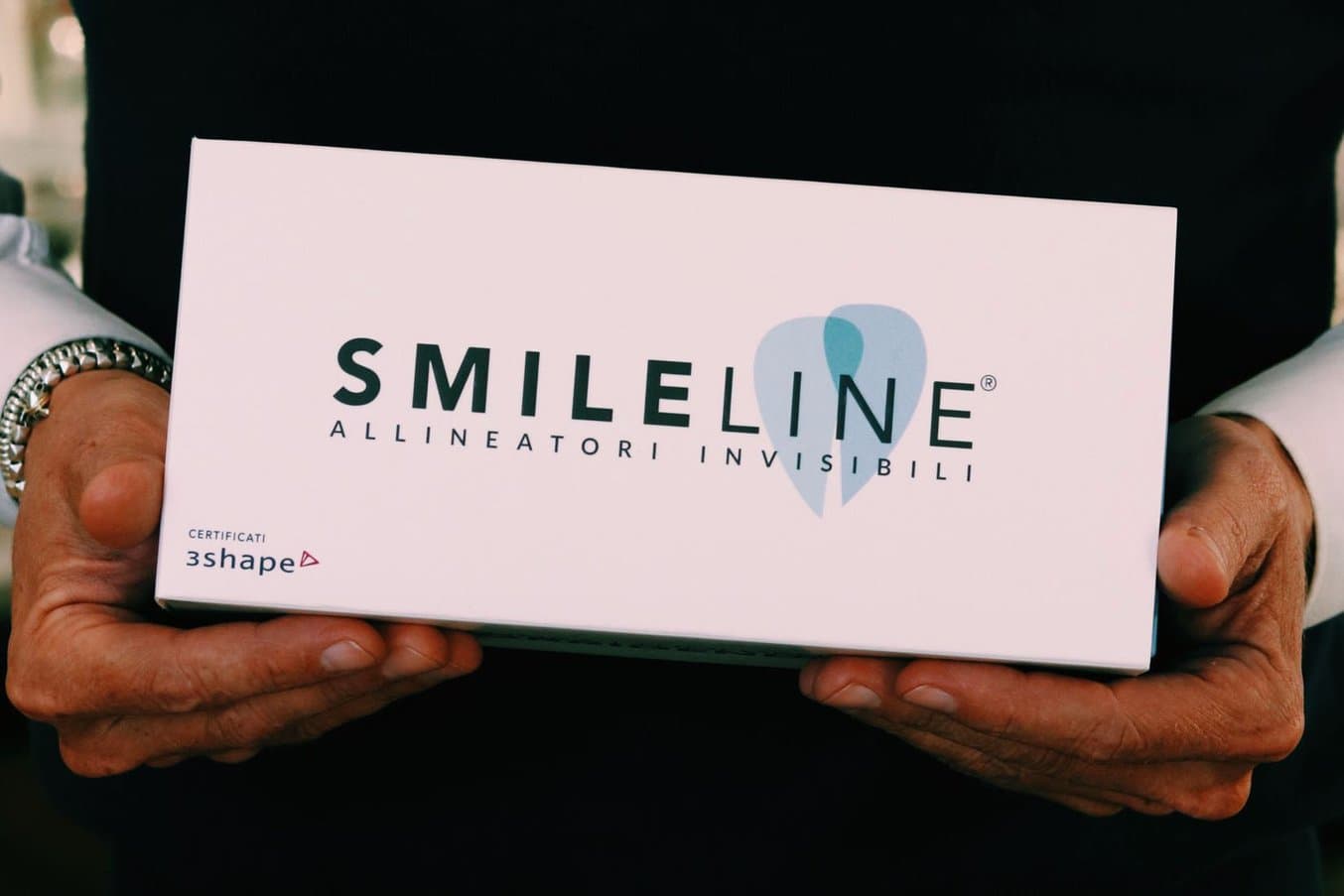
Vers un flux de travail numérique
Les modèles créés chez différents fabricants, tant en Italie qu'à l'étranger, ne présentaient pas une finition de surface satisfaisante. En effet, leur surface n'était pas polie et présentait des lignes de couches très marquées. Les plaques occlusales thermoformées sur ces modèles reproduisaient donc ces lignes de couches, ce qui les rendait opaques, peu transparentes et sensibles à l'accumulation de plaque. L'accumulation de plaque bactérienne entre les couches faisait passer la couleur de la plaque occlusale du blanc au jaune en quelques jours à peine. Si un patient choisit l'orthodontie invisible, c'est avant parce qu'il ne veut pas que l'on voie qu'il porte un appareil. Il est donc important que la plaque occlusale reste transparente et invisible tout au long du traitement. Lorsque la demande des cliniciens et des utilisateurs finaux a augmenté, Mimmo a réalisé que le moment était venu de trouver un produit qui pourrait servir d'alternative à celui utilisé jusqu'alors.
En 2015, il a rencontré l'équipe de Formlabs lors du salon international des soins dentaires (IDS) à Cologne. Après sa visite, il a décidé d'envoyer un dossier à Formlabs pour recevoir un échantillon gratuit. Après avoir envoyé le même fichier à un autre fabricant pour impression, il a comparé les résultats. Selon Mimmo, les deux modèles étaient complètement différents : l'un présentait des défauts de surface visibles, tandis que l'autre avait une surface lisse et était très détaillé. C'est alors qu'il a décidé d'acheter sa première imprimante 3D Formlabs. Actuellement, SmileLine en compte six.
« J'ai consulté d'autres offres avant de choisir Formlabs, mais ses produits correspondaient exactement à mes besoins. J'avais besoin d'imprimer en permanence, et les autres imprimantes du marché étaient malheureusement limitées à cet égard. D'autres modèles exigeaient par exemple que nous ajoutions de la résine manuellement, ce qui aurait causé pas mal de problèmes. Je voulais pouvoir lancer des impressions même la nuit pour que les plaques occlusales soient prêtes le matin. »
Mimmo Castellana, fondateur de SmileLine Allineatori Invisibili
Impression et usinage de modèles
Mimmo et son équipe font fonctionner les imprimantes en continu, jour et nuit, et obtiennent toujours d'excellents résultats. Toute son équipe travaille ainsi efficacement et sans temps mort. Les imprimantes disposent de flux de travail internes qui permettent à l'équipe SmileLine de travailler de manière ordonnée, proprement et sans erreur.
Après avoir effectué des tests d'impression verticale et horizontale, Mimm a constaté que lorsque le modèle était imprimé horizontalement, le modèle thermoformé s'adaptait comme un gant au modèle en plâtre. Une fois les modèles imprimés, ils sont placés dans la station de rinçage Form Wash puis dans la Form Cure pour achever la post-polymérisation. Les modèles post-polymérisés sont ensuite placés dans des machines de thermoformage de haute précision et reçoivent leur finition. Pour garantir systématiquement des résultats d'impression optimaux, les modèles imprimés sont pleins (et non creux). Si le modèle imprimé est creux, les pièces risquent de se déformer en raison de la forte pression des machines de thermoformage professionnelles (6 bars de puissance) qui permet un ajustement idéal des plaques occlusales. L'impression de modèles pleins permet d'éviter ces erreurs.
Après avoir testé plusieurs modèles avec différentes résines Formlabs, Mimmo et son équipe de SmileLine ont pu constater que Grey Resin était idéale pour les plaques occlusales et les appareils orthodontiques. Le laboratoire SmileLine utilise également White Resin et Model Resin pour réaliser des modèles d'étude, et Draft Resin pour réaliser rapidement des modèles de blanchiment et des appareils dentaires. Travaillant à pleine capacité du lundi au vendredi, SmileLine imprime jusqu'à 100 modèles par jour avec ses six imprimantes Formlabs, dont la Form 2, la Form 3 et la Form 3B. En outre, Mimmo a récemment commandé une Build Platform 2, qui sera selon lui un grand atout pour son équipe. L'impression étant horizontale, et donc sans supports, l'équipe SmileLine doit faire particulièrement attention lorsqu'elle retire les modèles de la plateforme de fabrication pour ne pas casser les modèles.
Expansion vers de nouvelles applications dentaires
SmileLine utilise les imprimantes Formlabs pour produire des plaques occlusales, mais aussi des modèles orthodontiques traditionnels. Il existe énormément d'applications : plaques de Schwarz, expanseurs rapides, barres transpalatines, appareils fonctionnels, dispositifs orthodontiques traditionnels, dispositifs entièrement numériques, etc.
Mimmo souhaiterait trouver un produit, similaire à ceux qu'il utilise aujourd'hui, qui permette de créer une plaque occlusale numérique performante. Pour l'instant, SmileLine continue de fabriquer ses plaques dans son atelier selon un protocole qui lui est propre. Il souhaiterait également trouver au plus vite des produits élastiques qui permettraient une expansion orthodontique (et non orthopédique) en déplaçant uniquement les dents et en créant ainsi de l'espace.
« Je pense que grâce à la recherche et au développement, la science et les entreprises essaient de trouver des produits biocompatibles plus tolérables que les métaux ou les alliages métalliques présents actuellement sur le marché qui puissent convenir à tous les patients, même ceux qui sont allergiques, et faciliter le processus. Ce serait vraiment une excellente nouvelle. »
Mimmo Castellana, fondateur de SmileLine Allineatori Invisibili
Comparaison des méthodes traditionnelles et numériques
SmileLine est un laboratoire certifié 3Shape car tout sont sysyème est fourni par cette compagnie, du scanner au logiciel de traitement. Par exemple, en plus de recevoir des fichiers de n'importe quel scanner intraoral, SmileLine a la capacité de communiquer avec les scans 3Shape d'un cabinet partenaire grâce à un logiciel appelé Communicate. L'empreinte numérique 3Shape détecte le scanner intraoral et, sans utiliser de courrier électronique, Dropbox ou d'autres outils de communication, communique immédiatement avec le laboratoire (en l’occurrence SmileLine) et envoie le fichier STL directement via le logiciel propriétaire.
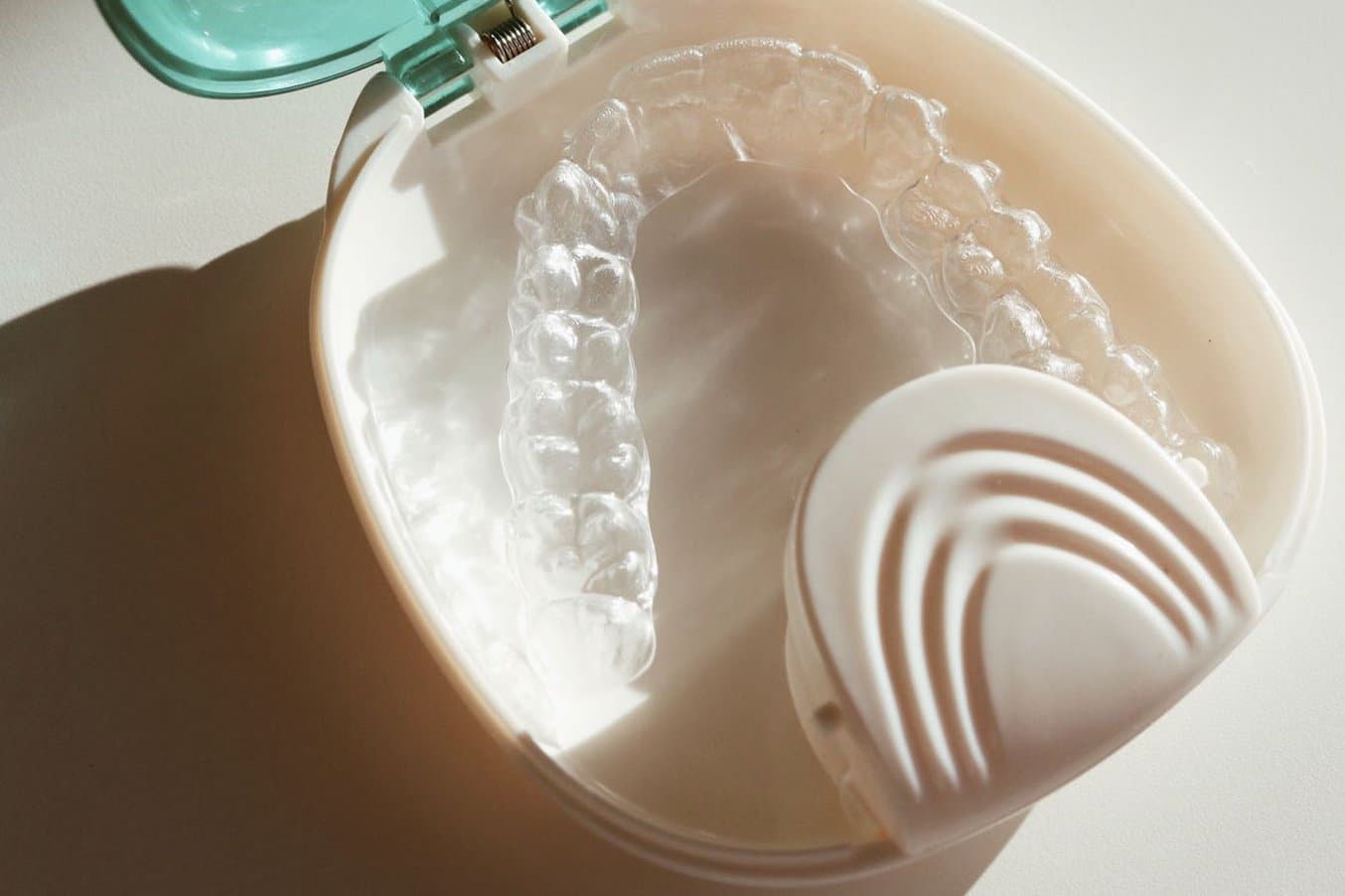
SmileLine effectue des tests périodiques pour vérifier que tout le processus entre la numérisation et l'envoi au laboratoire fonctionne parfaitement. Par exemple, il est possible de consulter le fichier de scan, le fichier traité en interne et le fichier destiné aux imprimantes Formlabs. Ils ont numérisé ce modèle et ont superposé les trois fichiers, c'est-à-dire le fichier numérisé, le fichier créé en interne et le fichier généré à la suite de l'impression 3D. Le résultat était stupéfiant.Les trois dossiers correspondaient parfaitement. Les imprimantes ont ensuite reproduit fidèlement le fichier créé à partir du scan... Le résultat obtenu était parfait : chaque cuspide de la dent et chaque point de l'arcade a pu être parfaitement superposé à partir du fichier initialement généré à partir des empreintes numériques. Le modèle fabriqué avec les imprimantes Formlabs correspond parfaitement au résultat obtenu à partir d'une empreinte intraorale ou d'une empreinte traditionnelle prise dans la cavité buccale.
Retour sur investissement et gain de temps
Auparavant, SmileLine devait payer chaque pièce imprimée par les centres de fabrication et couvrir les frais d'expédition. Grâce à Formlabs, Mimmo a pu réduire considérablement ses dépenses.
« Ce qu'il y a de mieux avec les produits Formlabs, c'est qu'ils me permettent de ne pas perdre de temps. Grâce aux scans numériques, le dossier arrive immédiatement au laboratoire, et nous pouvons livrer les appareils de contention dès le lendemain. Il est crucial que ces appareils de contention soient livrés rapidement car le risque de récidive, et donc de déplacement des dents, est élevé. Si l'impression n'était pas aussi rapide, nous devrions traiter les modèles, les envoyer au centre de conception et attendre 2, 3, voire 4 jours. Nous sommes aujourd'hui en mesure de tout livrer au destinataire en un seul jour. C'est un gros gain de temps, et nos services n'en sont qu'améliorés. »
Mimmo Castellana, fondateur de SmileLine Allineatori Invisibili
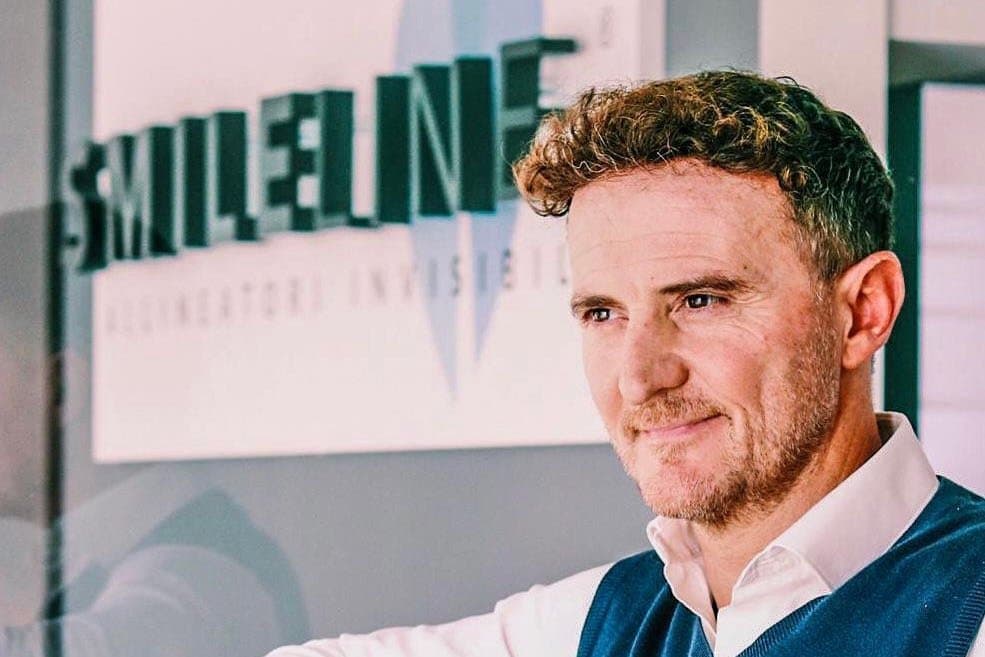
L'avenir de la dentisterie numérique
« Si je regarde en arrière, je me rends compte que nous sommes aujourd'hui capables de faire des choses qui étaient encore inimaginables il y a 2 ou 3 ans. », nous dit Mimmo.Mimmo est convaincu que l'on peut faire beaucoup plus avec l'impression 3D. Aujourd'hui, il passe la plupart de son temps devant son ordinateur, à travailler avec ses imprimantes et non plus à l'atelier. « L'avenir de l'impression 3D dépend toutefois des entreprises et du nombre de produits biocompatibles qui seront fabriqués (en ce qui concerne mon secteur). Je pense également que la qualité d'un produit additif est nettement supérieure à celle d'un produit soustractif. Les personnes travaillant avec des prothèses fixes espèrent qu'un matériau qui leur permettra d'utiliser l'impression 3D sortira dans les plus brefs délais. »
Conclusions
SmileLine utilise toutes les imprimantes Formlabs car les pièces produites sont les mêmes : entre la Form 2 et la Form 3, seuls les délais de fabrication sont différents. « Mes imprimantes fonctionnent constamment. Je les utilise tout le temps et elles sont toujours en marche », nous dit Mimmo. « Mon équipe enlève la plateforme de fabrication, retire les modèles, remet la plateforme, et une nouvelle impression commence. Il s'agit d'un cycle continu et constant. Dès qu'une de mes imprimantes décide de s'arrêter, je la laisse se reposer, car elle a rempli sa mission. Dès que la dernière de mes Form 2 sera hors service, je pourrai la remplacer par une Form 3B+. »