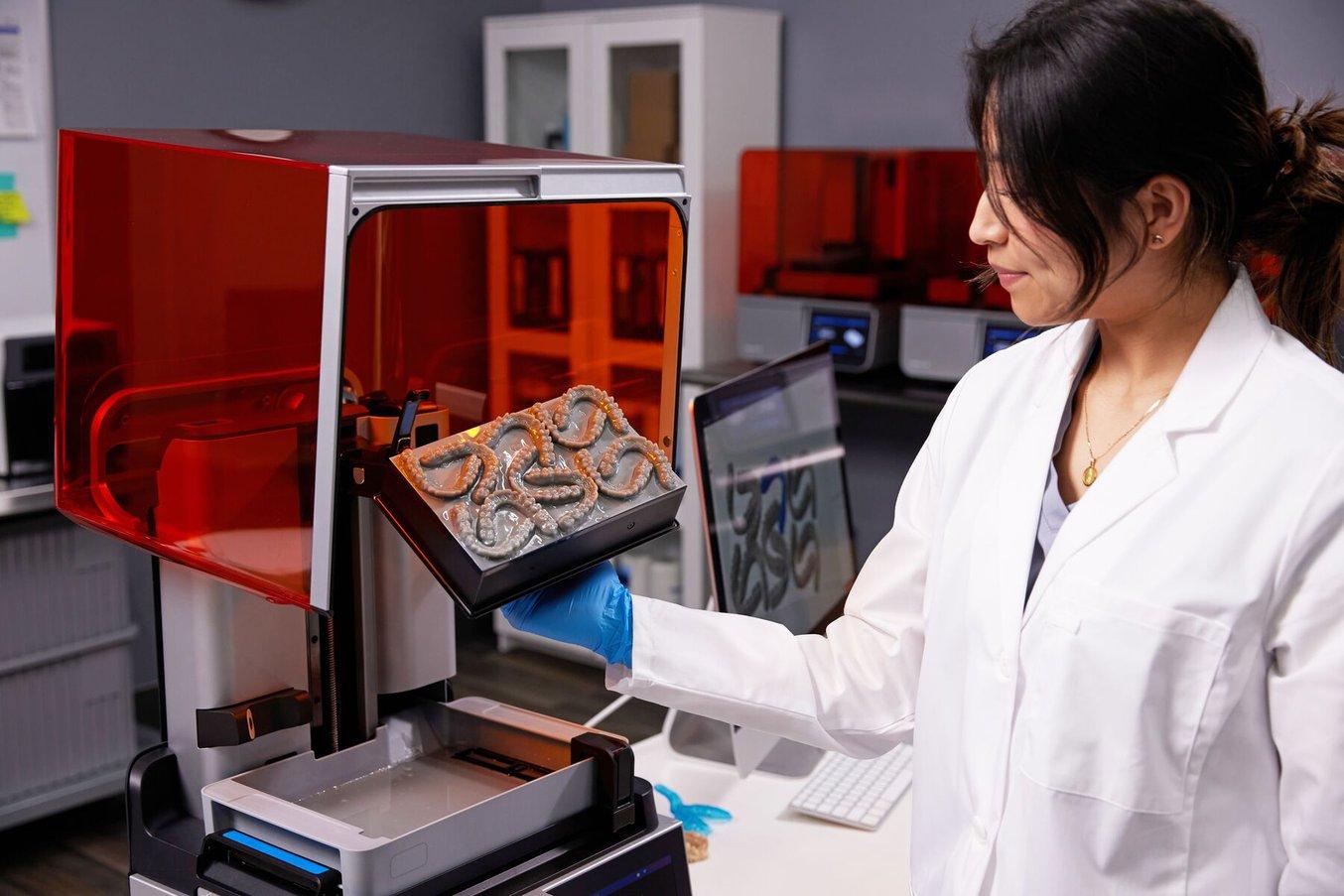
Additive manufacturing is the latest piece of the workflow in digital dentistry that has become a logical business choice for dental practices and labs, combining high quality with low costs and streamlined workflows. The market has been expanding rapidly, bringing this technology within reach for more businesses.
In this guide, we’ll examine the different 3D printing technologies for restorative dentistry and orthodontics, and the attributes to evaluate before investing in a dental 3D printer.
New to digital dentistry? Check out our guide to find out more about the difference between analog and digital workflows, and learn what’s involved in integrating 3D printing into your business.
Dental 3D Printing Technologies Overview
Today, three resin 3D printing technologies are common in dental and orthodontic practices and labs: traditional (laser-based) stereolithography (SLA), digital light processing (DLP), and masked stereolithography (MSLA).
In traditional SLA, a vat of liquid resin is selectively exposed to a laser across the print area, solidifying resin in specific areas. This exposure occurs layer by layer, building the print. Low Force Stereolithography (LFS)™ is an advanced form of laser SLA technology used by Formlabs’ Form 3B+ and 3BL 3D printers. LFS reduces the strain created on a part when peeling it from the resin tank between layers, producing parts with a smooth surface finish, clarity, and accuracy.
Digital light processing (DLP) operates with the same chemical process, but uses a digital projector as the light source and a micromirror device light-processing technique to selectively solidify the resin. With DLP, the entire layer gets cured at the same time.
Masked stereolithography (MSLA) uses the light from LEDs and an LCD as the light-processing solution to cure an entire layer rapidly and with high accuracy. Formlabs’ Low Force Display (LFD)™ is an advanced form of MSLA, developed for Form 4B and Form 4BL. LFD introduces a brand new technology stack including a backlight unit, light processing unit, release texture, and integrated camera, and significant improvements with updates to the flexible film tank, resin cartridge, automatic resin handling, and intelligent control systems to deliver the speed, reliability, and part quality that professionals need, all in a single printer.
Low Force Stereolithography (LFS)
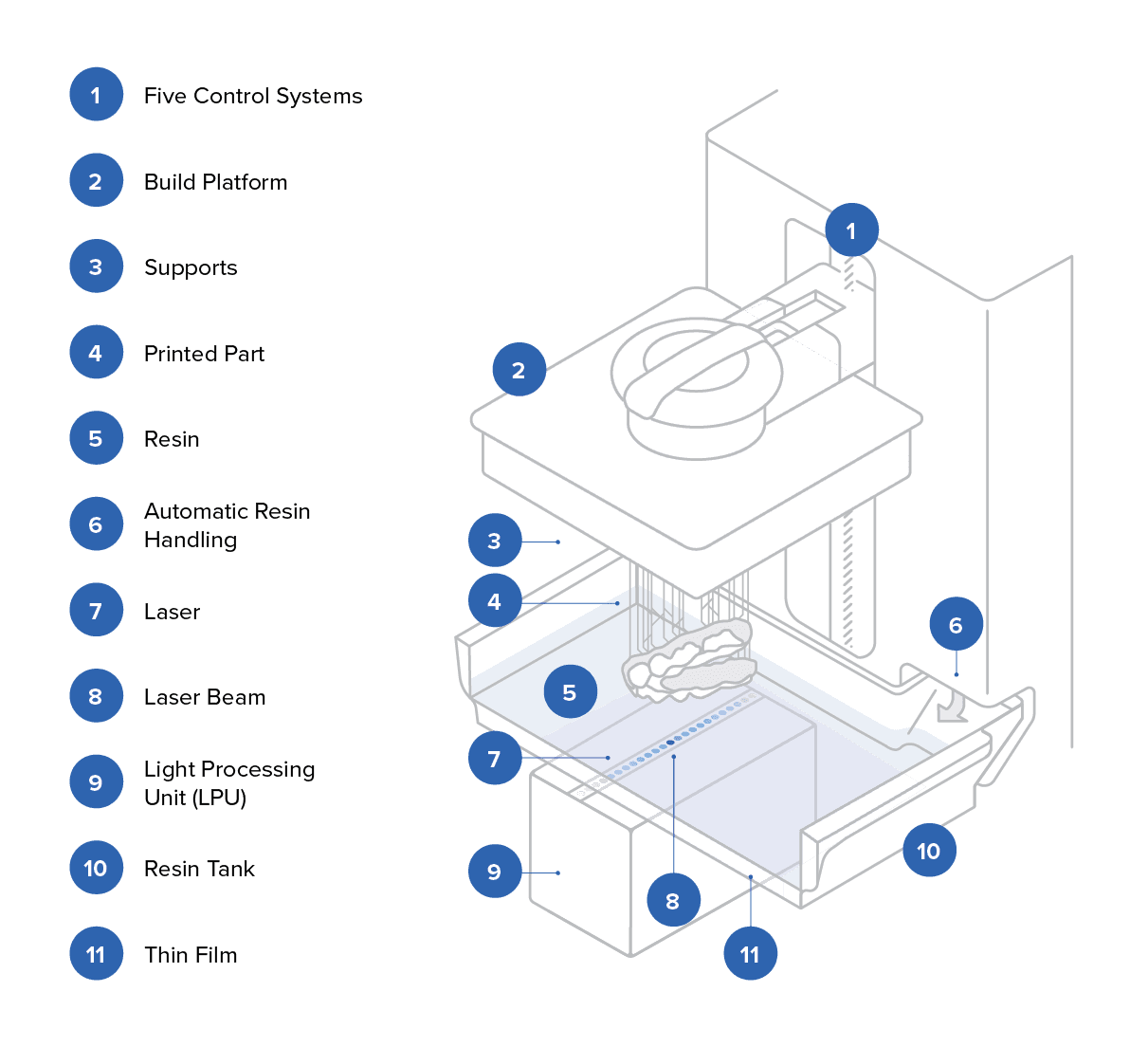
Digital Light Processing (DLP)
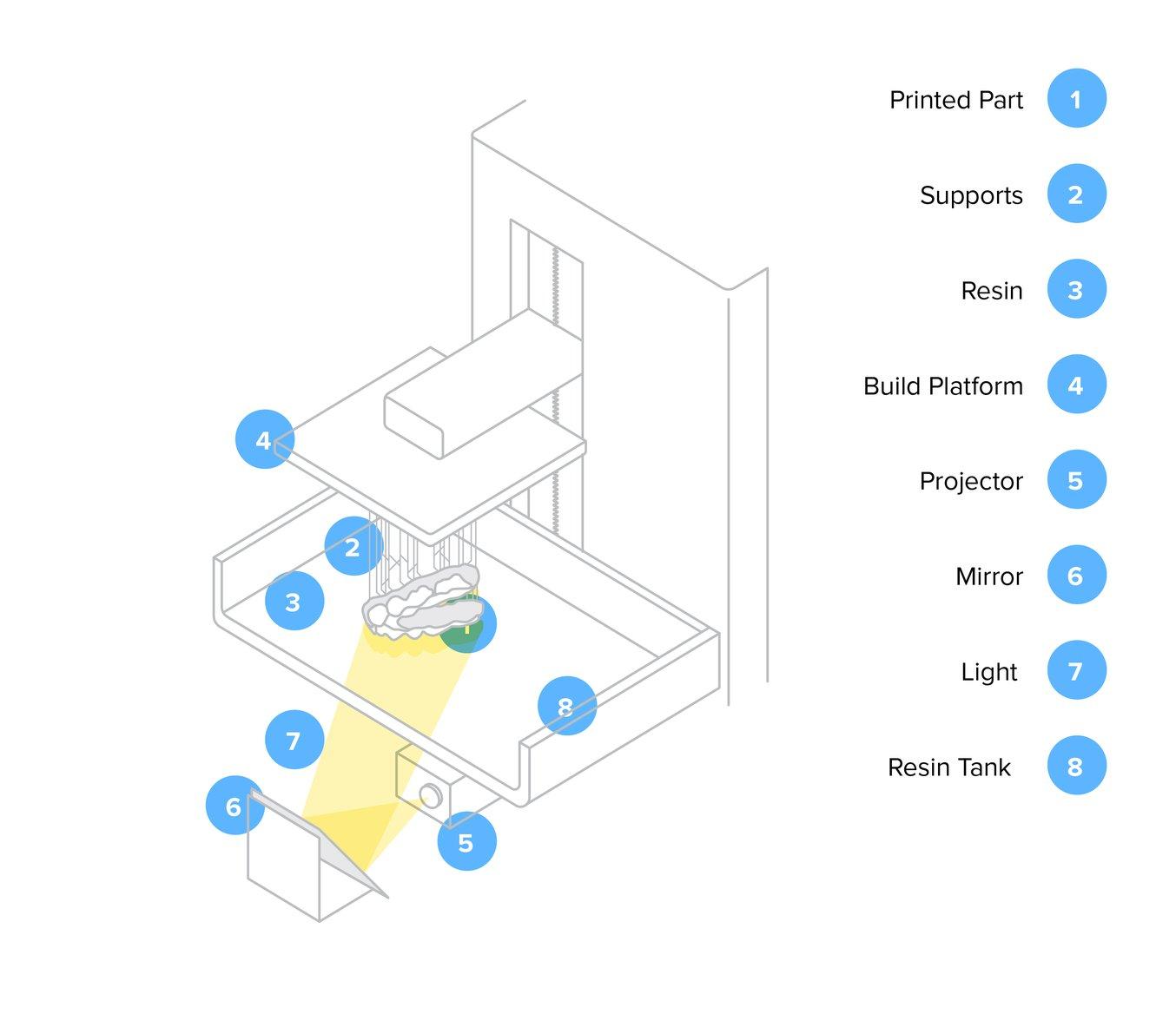
Low Force Display (LFD)
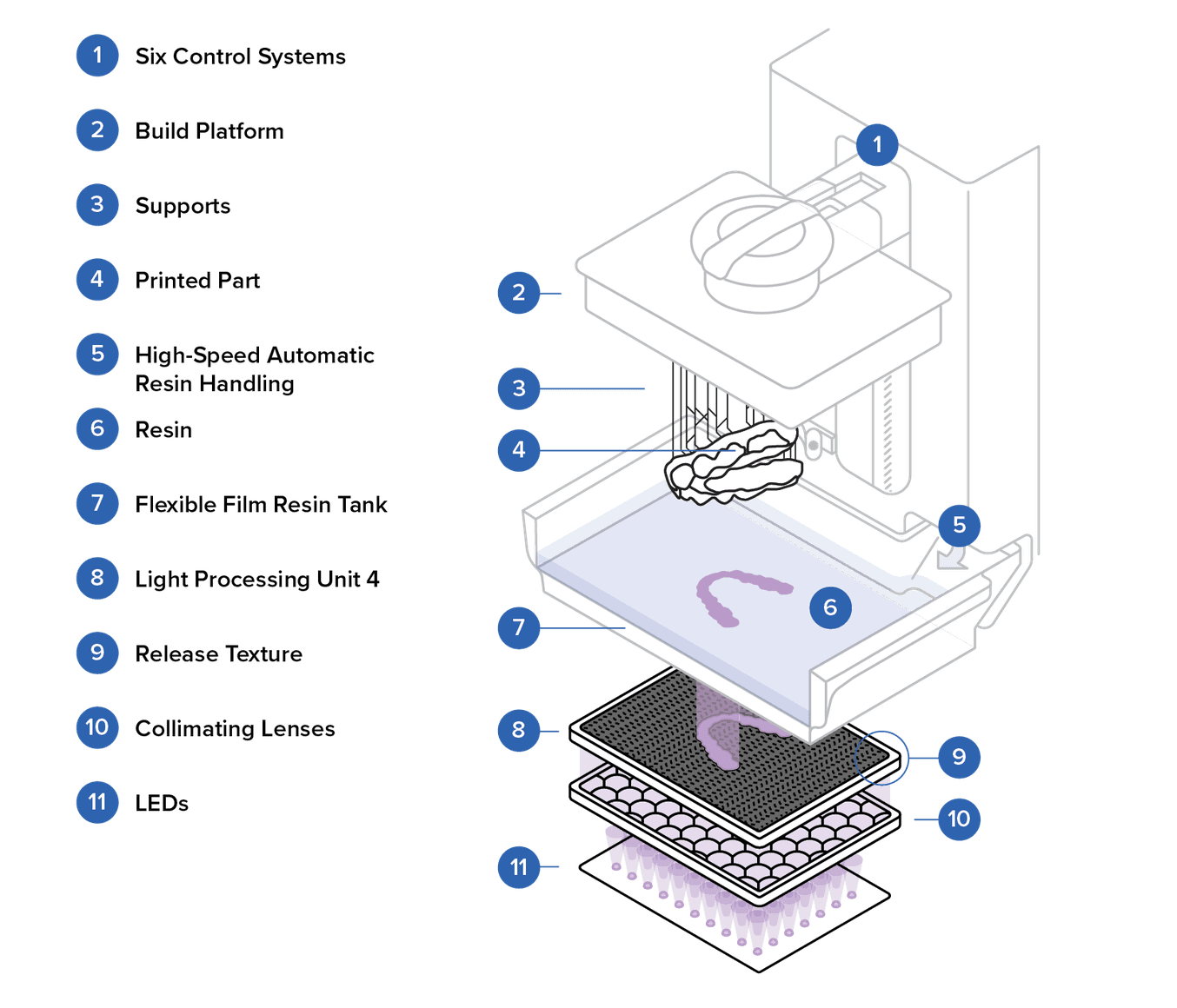
The most common dental 3D printers work by selectively exposing liquid resin to a light source filtered and projected by various light-processing techniques to form very thin layers of material that stack up to create a solid object.
The way resin 3D printers work is similar — the differences in print quality, workflow, available materials, costs, and other factors are bigger from machine to machine than technology to technology.
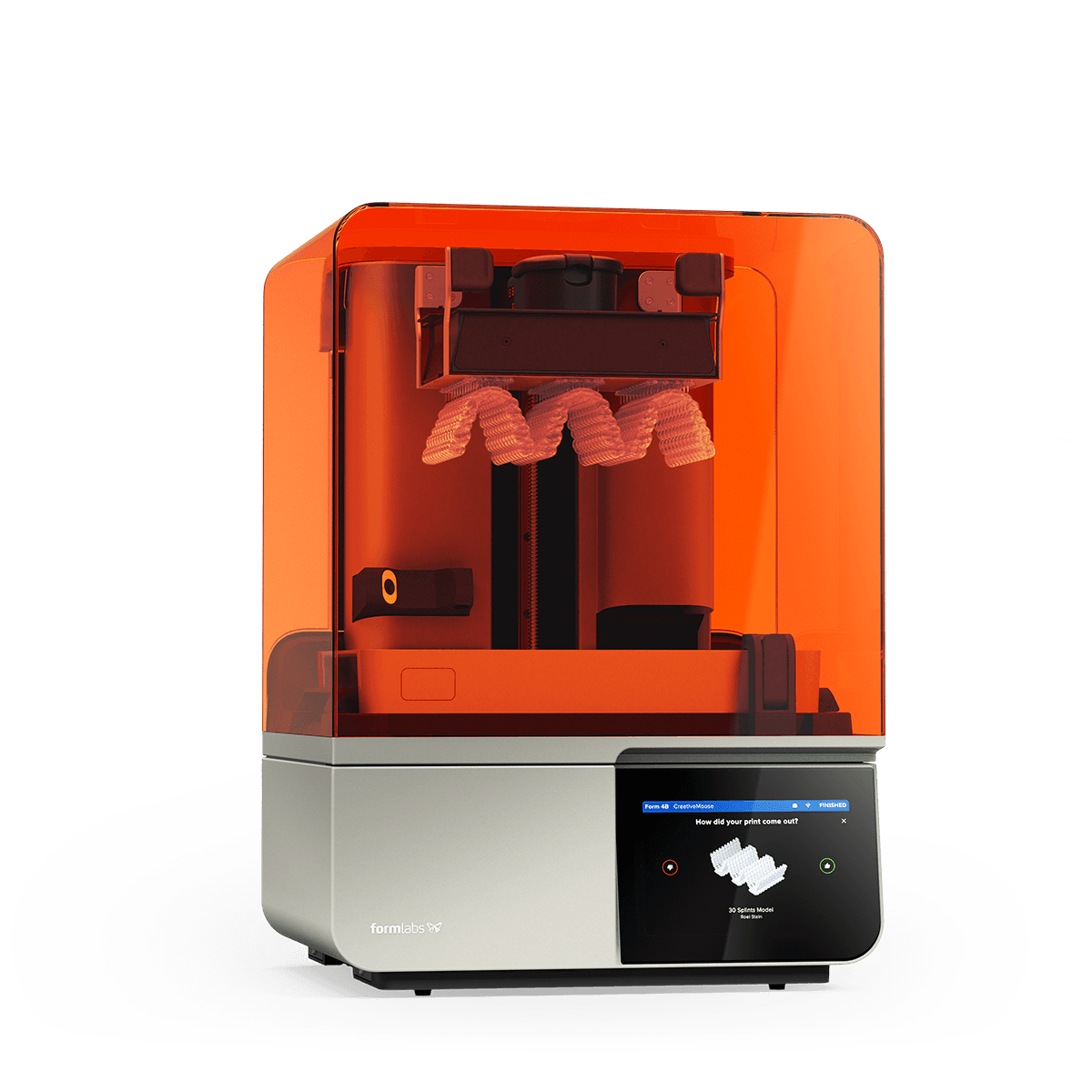
Product Demo: Form 4B Dental 3D Printer
Blazing speed meets unmatched accuracy in the next generation of dental 3D printing. Explore the latest innovations in our webinar.
How to Compare Dental 3D Printers
Speed and Throughput
For dental practices, print speed can be the difference between providing a solution during an appointment versus a day or more later. For labs, it’s important to consider both speed and throughput. While speed can equate to more prints in less time, variables including post-processing time and labor required will impact throughput.
Both DLP and MSLA 3D printers expose the entire layer at once. This means print speed is uniform regardless of how many parts are on the build platform and depends only on the height of the parts in the Z-axis. Laser SLA 3D printers utilize a single laser to draw out each part. Generally, this means they can be slower when printing a densely covered print platform.
However, there’s a trade-off between resolution and build volume for DLP printers. A small DLP 3D printer might be able to print fast, but you can only fit a few models on the build platform. A different machine with a larger build volume might be able to print more parts, but only at a lower resolution, which means that it might not be accurate enough for printing restorative models or surgical guides that require higher accuracy.
MSLA printers combine build volume and speed, allowing dental professionals to have the best of both worlds. LFD technology takes this one step further, combining speed and accuracy across the build platform in one machine. With the LFD Print Engine of Form 4 Generation printers, surface accuracy is over 95% of data points within 50 μm of the original CAD data consistent across the build platform – while being able to print 11 models in nine minutes on Form 4B, and 32 models in 14 minutes on Form 4BL.
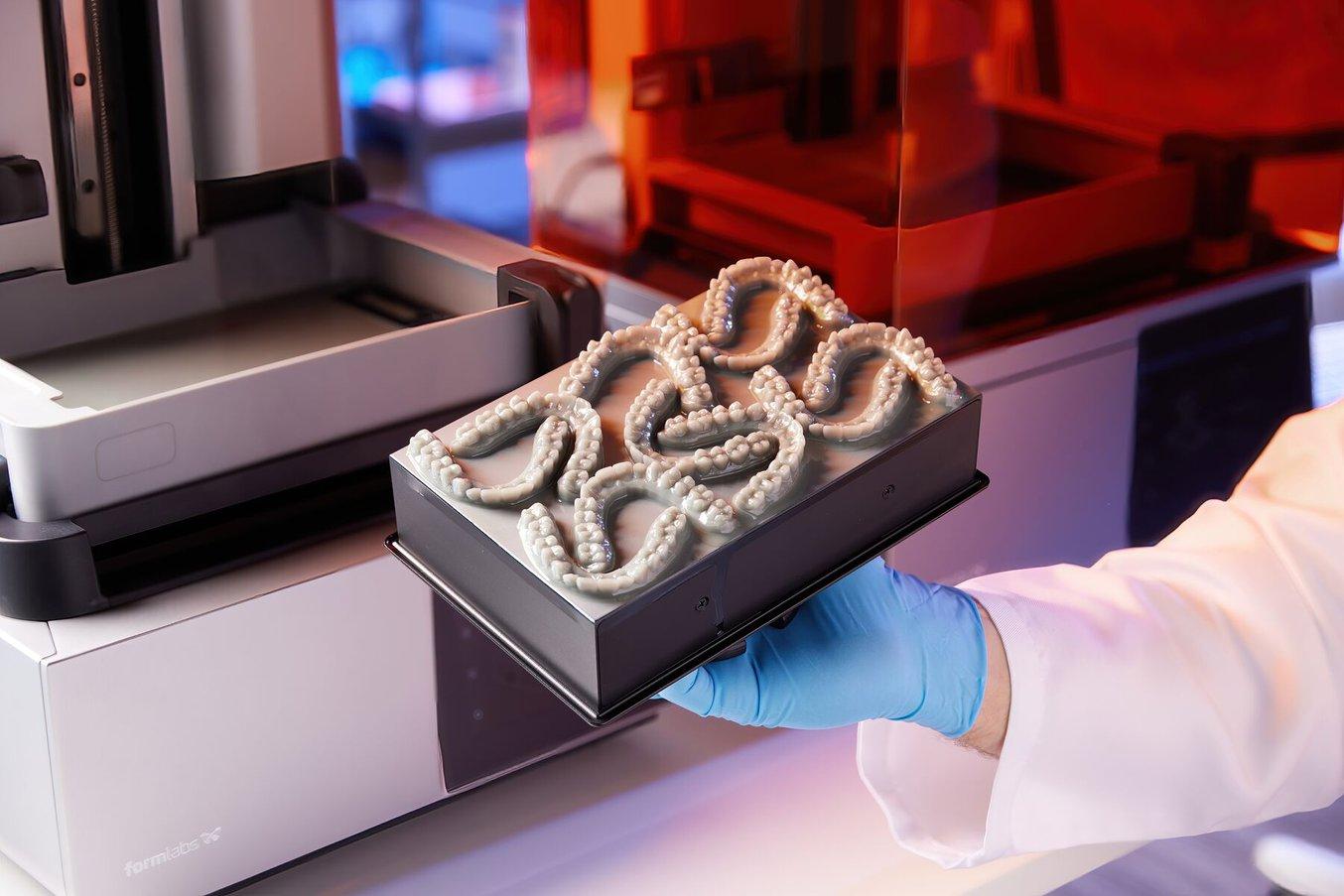
With the LFD Print Engine of Form 4 Series printers, surface accuracy is over 95% of data points within 50 μm of the original CAD data consistent across the build platform – while being able to print 11 models in nine minutes on Form 4B, and 32 models in 14 minutes on Form 4BL.
Print Speeds for Various Dental Appliances on Form 4B
Appliance | Quantity | Time |
---|---|---|
Surgical Guides | 12 | 48 min |
Orthodontic Models and Models for Thermoforming (Flat Orientation) | 11 | 9 min |
Splints | 8 | 54 min |
All-on-X | 9 | |
Denture Bases | 6 | 1 h 40 min |
Restorative Models | 10 | 25 min |
Crowns and Bridges | Up to 130 units | 25 min |
Print Speeds for Various Dental Appliances on Form 4BL
Appliance | Quantity | Time |
---|---|---|
Orthodontic Models and Models for Thermoforming (Flat Orientation) | 32 | 14 min |
Orthodontic Models and Models for Thermoforming (Vertical Orientation) | 75 | 1 h 46 min |
Restorative Models | 28 | 2 h 48 min |
Splints (15° Orientation) | 24 | 1 h 19 min |
Splints (Vertical Orientation) | 80 | 2 h 10 min |
Surgical Guides | 36 | 1 h 9 min |
Note: Time is consistent for the quantity range as print time is similar across the build platform.
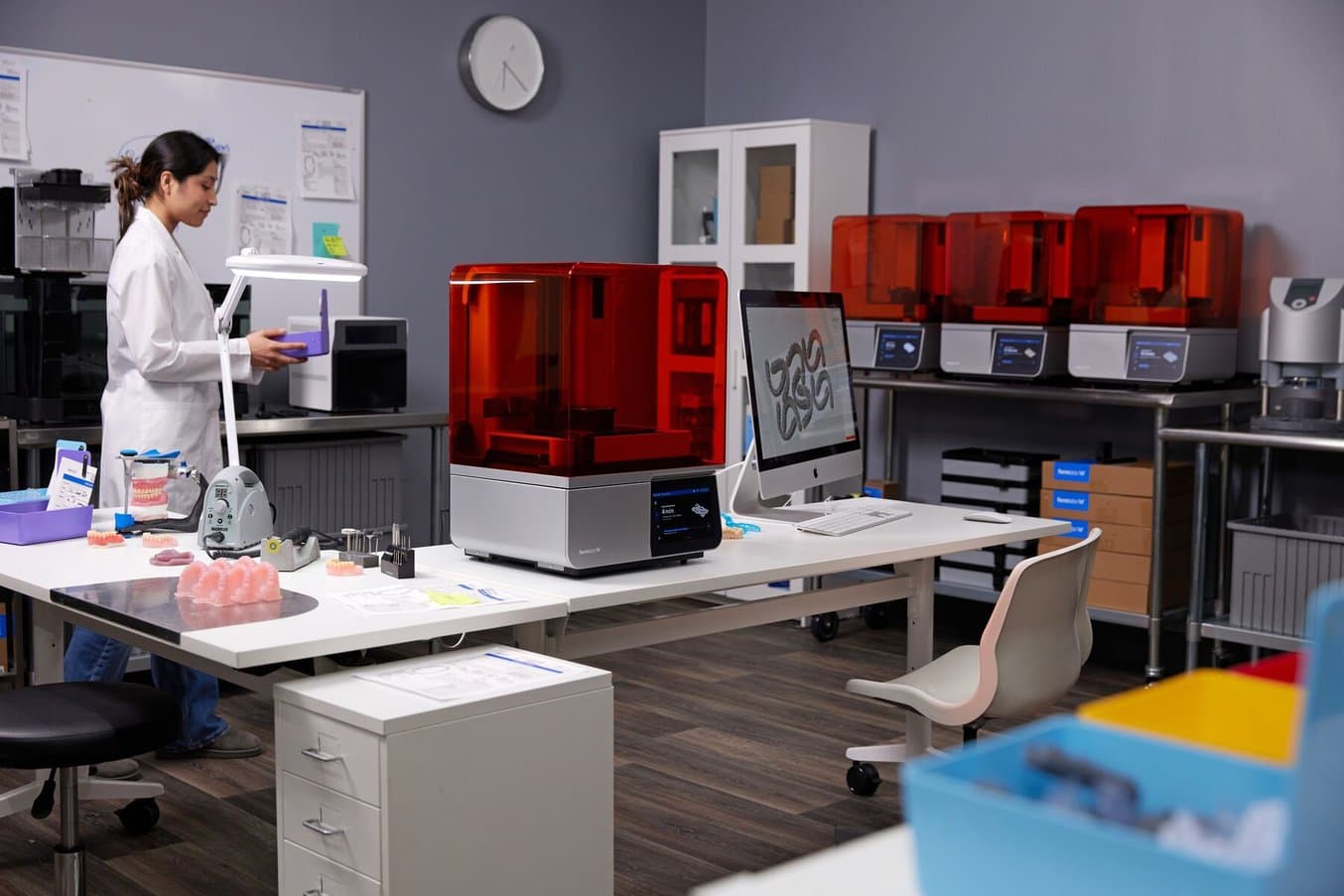
Accuracy Requirements of 3D Printed Models in Dentistry
This document aims to establish a comprehensive understanding of the dimensional accuracy requirements of models used in dentistry, assessing what researchers have determined to be clinically acceptable, and what constitutes an adapted gold standard in the context of our current 3D printing technology’s capabilities and limitations.
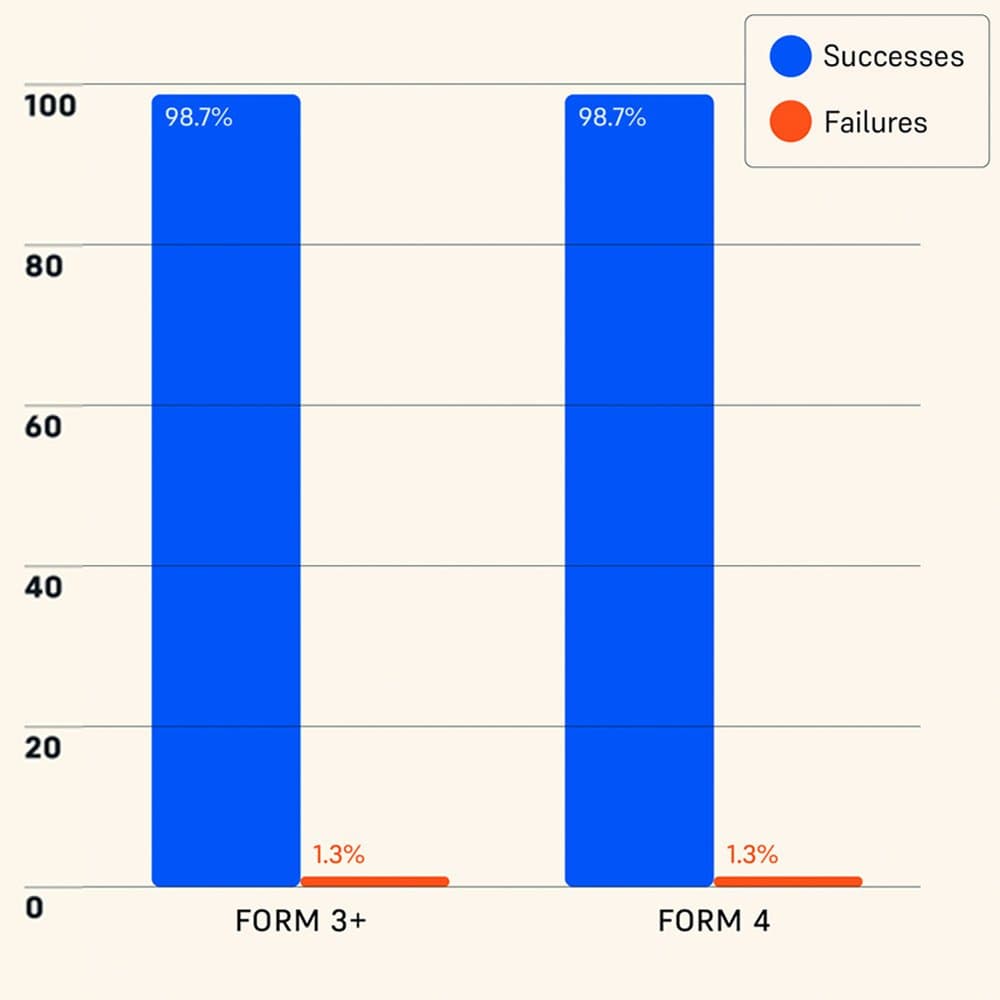
Independently Tested Reliability of Form 4 and Other Resin 3D Printers
Formlabs Form 4 was measured to have a 98.7% print success rate by an independent global leader in product testing. Read a complete description of the test methodology and see the results in our white paper.
The Power of Printer Fleets
Another important consideration, especially for dental labs, is whether to fulfill capacity with a single printer or multiple printers. Production with printer fleets often reduces upfront costs compared to larger-format machines. By buying one machine at first, labs can test out production methods before ultimately scaling up production with demand.
This provides the opportunity to pay for production only when it is needed, rather than making large, long-term investments in a rapidly evolving market. Printer fleets with multiple printers also empower the printing of multiple different indications, and different materials, at once, and reduce risk through redundancy. If one machine needs servicing, production can be balanced across the rest of the printer fleet.
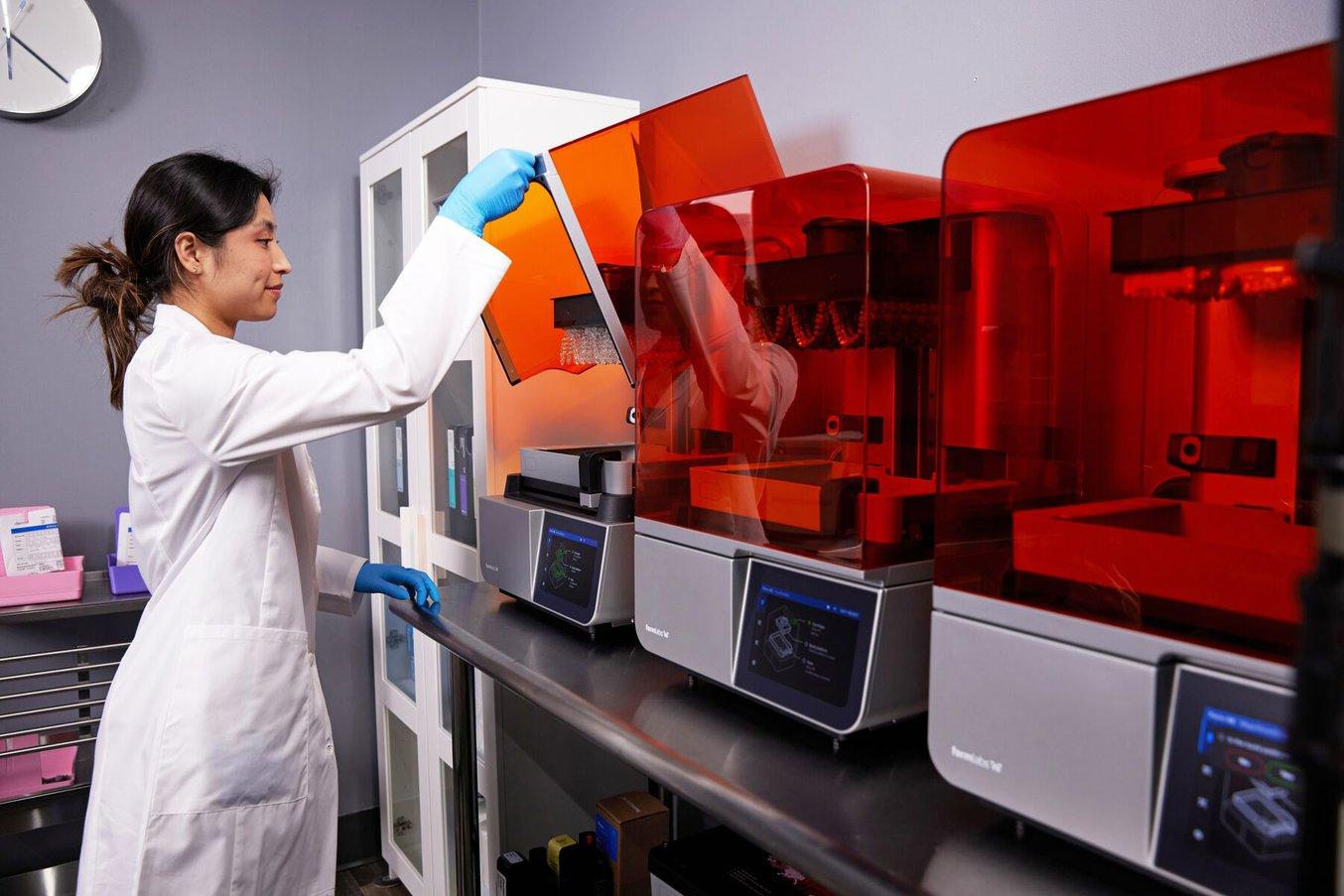
Printer fleets allow 3D printing for multiple different applications in parallel, balancing production needs and lowering risk through redundancy.
Printer fleet management can also be automated, minimizing touchpoints and freeing up workers for higher-value tasks. For example, Formlabs’ Dashboard enables automatic print-to-printer assignment, streamlined queueing, and optimized workflow management. In a lab setting, this allows multiple users to collaborate, adding, duplicating, and prioritizing prints across an entire fleet of printers.
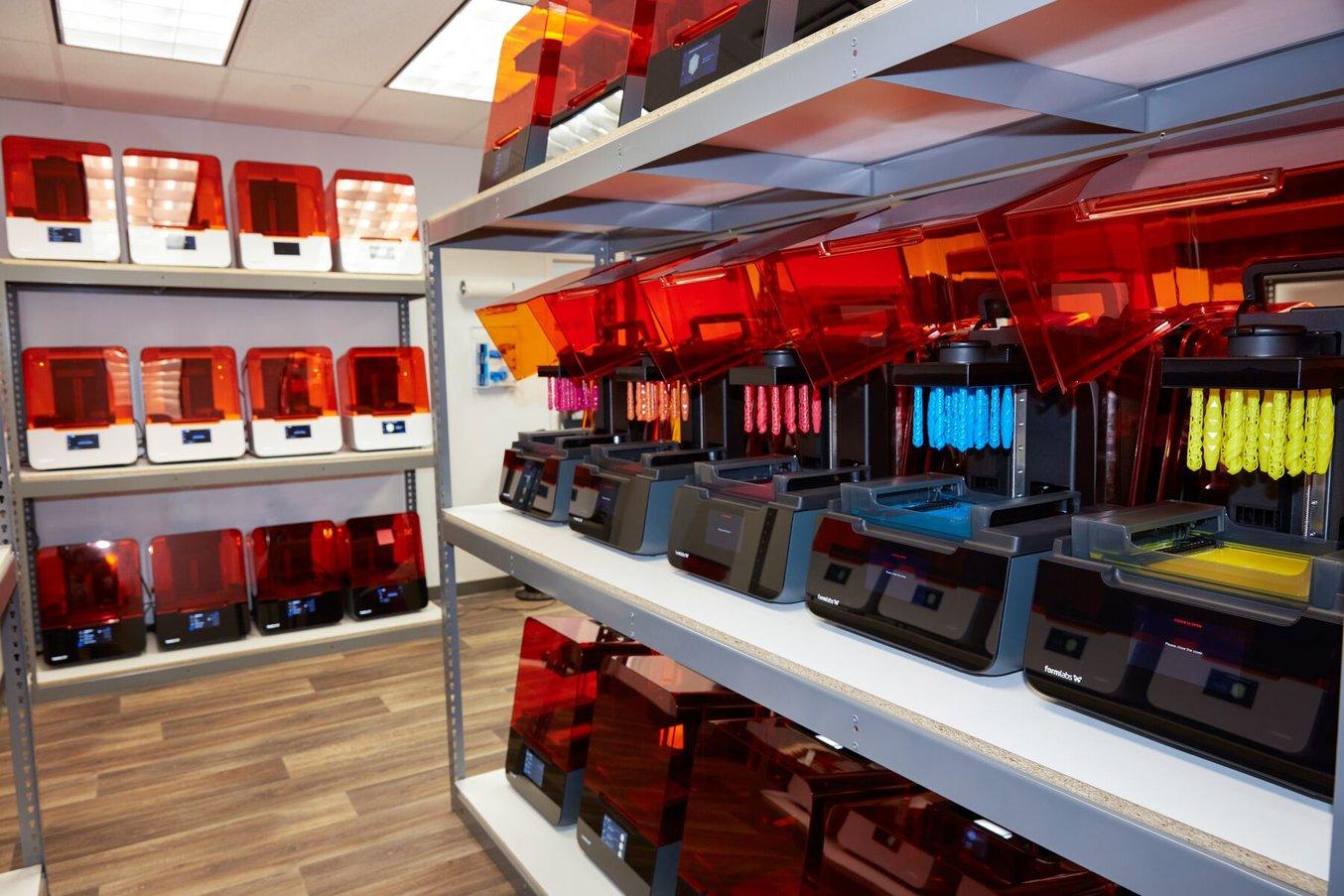
Managing 3D Printer Fleets
Managing multiple SLA and SLS printers doesn’t have to be complicated — with the right organizational system, any business can run a printer fleet in just a day or two.
High-Throughput With Large-Format Dental 3D Printers
For dental and orthodontic labs with high-throughput needs, large-format dental 3D printers can print more models or appliances in each build, minimizing user interactions for efficient production. Batching prints also makes for less time spent post-processing.
For example, three batches of 11 models on Form 4B would require staff to remove the build platform and post-process three times, for a total of 33 models. In comparison, printing 32 models on Form 4BL would batch all the models together, requiring only one interaction with the printer to remove the build platform and post-process models.
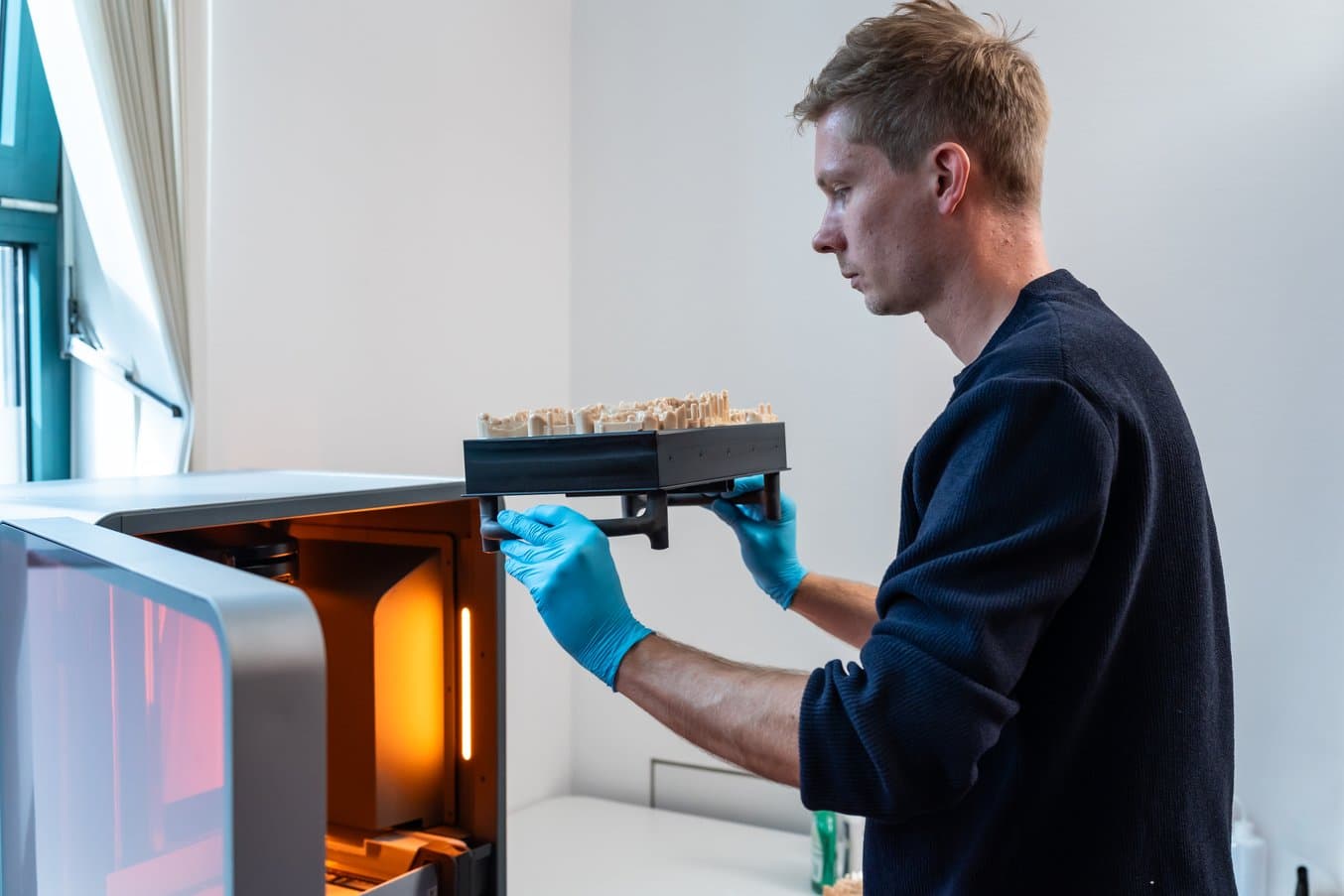
At Kreimer Dentallabor, Form 4BL is used to efficiently print highly accurate restorative models in Precision Model Resin.
Many labs find that one application is printed at higher volumes than others, often models. If this is the case, it’s worth considering the cost-savings and labor efficiency of purchasing a large-format 3D printer exclusively for printing this high-volume application.
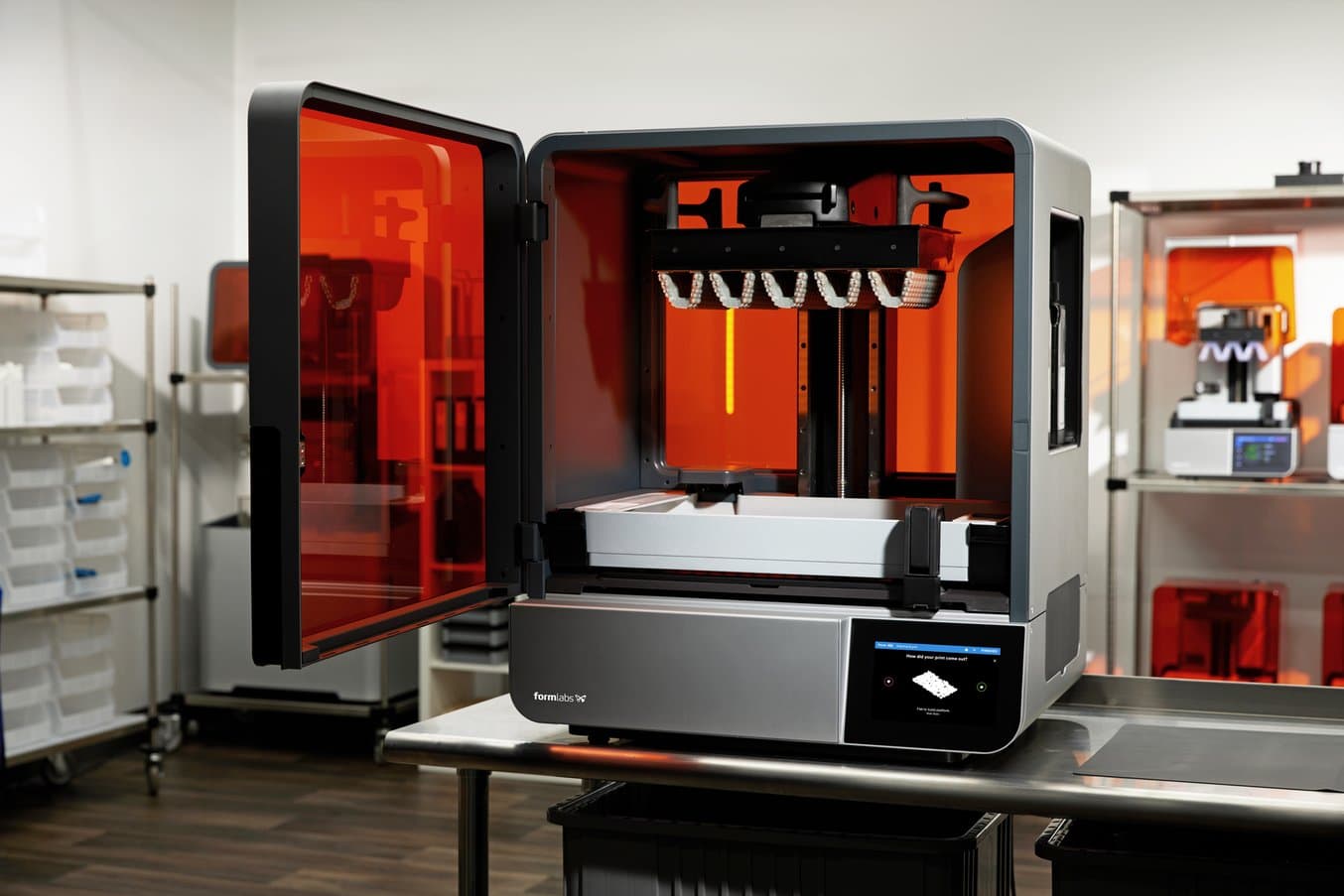
Form 4BL has a 2.7x larger build surface than Form 4B, unlocking the ability to print more than 120 orthodontic models per hour with Fast Model Resin at 160 μm.
Adding Automation
Automating 3D printing is becoming an increasingly attractive option for dental labs, as well as for dental practices that want the ability to print multiple batches of prints without interacting with the printer. With the slower print speeds of some dental 3D printers, the addition of automation, such as the Formlabs Automation Ecosystem, enables 24/7 production, as hardware removes prints from the Build Platform 2 and starts the next print. However, the high-throughput and blazing speeds of Form 4BL enable even more production volume in a single work day than printing for 24 hours.
When comparing a printer to an automated solution, it’s important to look at the number of prints in both a 24-hour period and when printing 24/7, all while factoring in the labor required to print on a printer without automation.
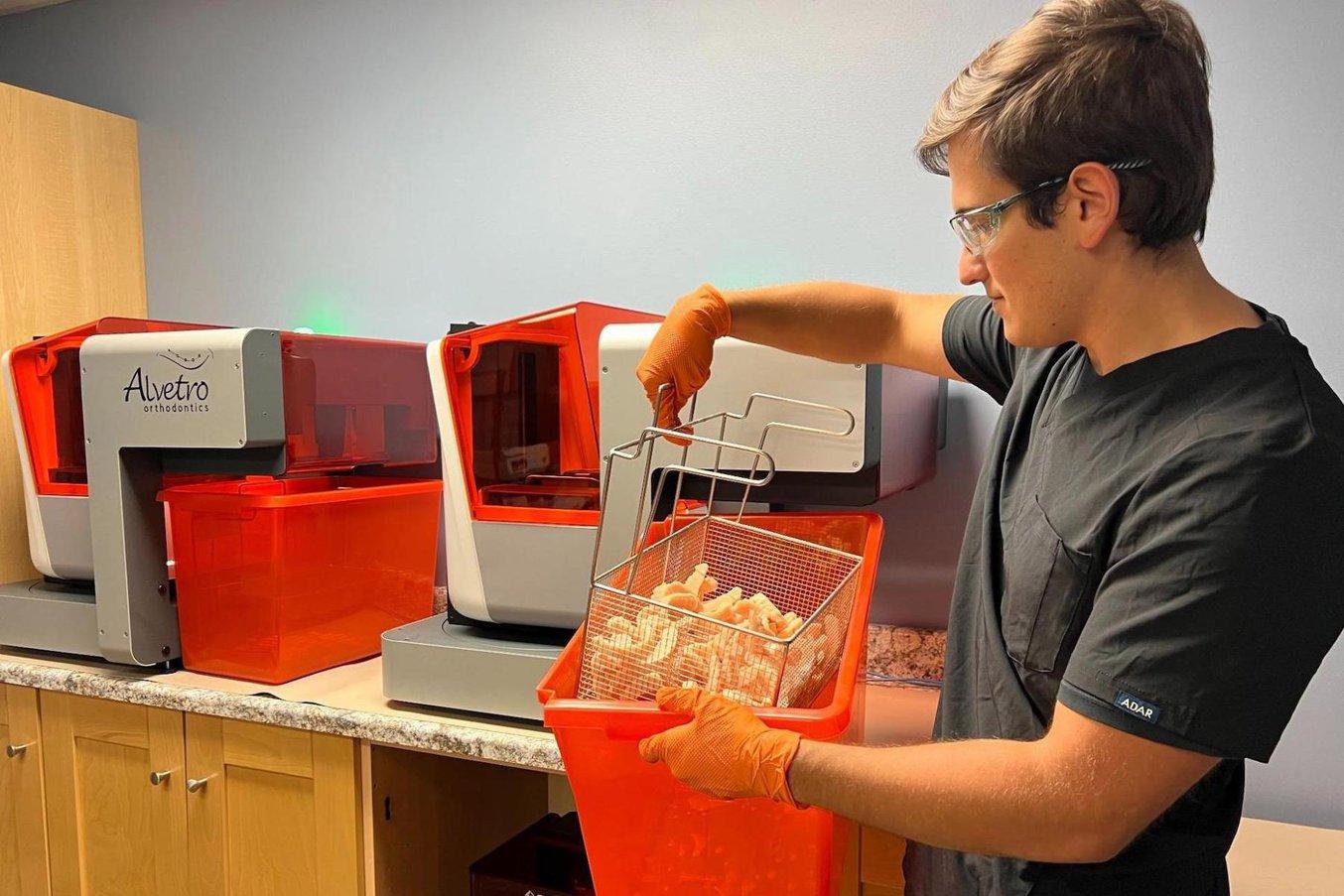
Alvetro Orthodontics leverages the Form Auto for in-house production, saving costs and improving efficiency.
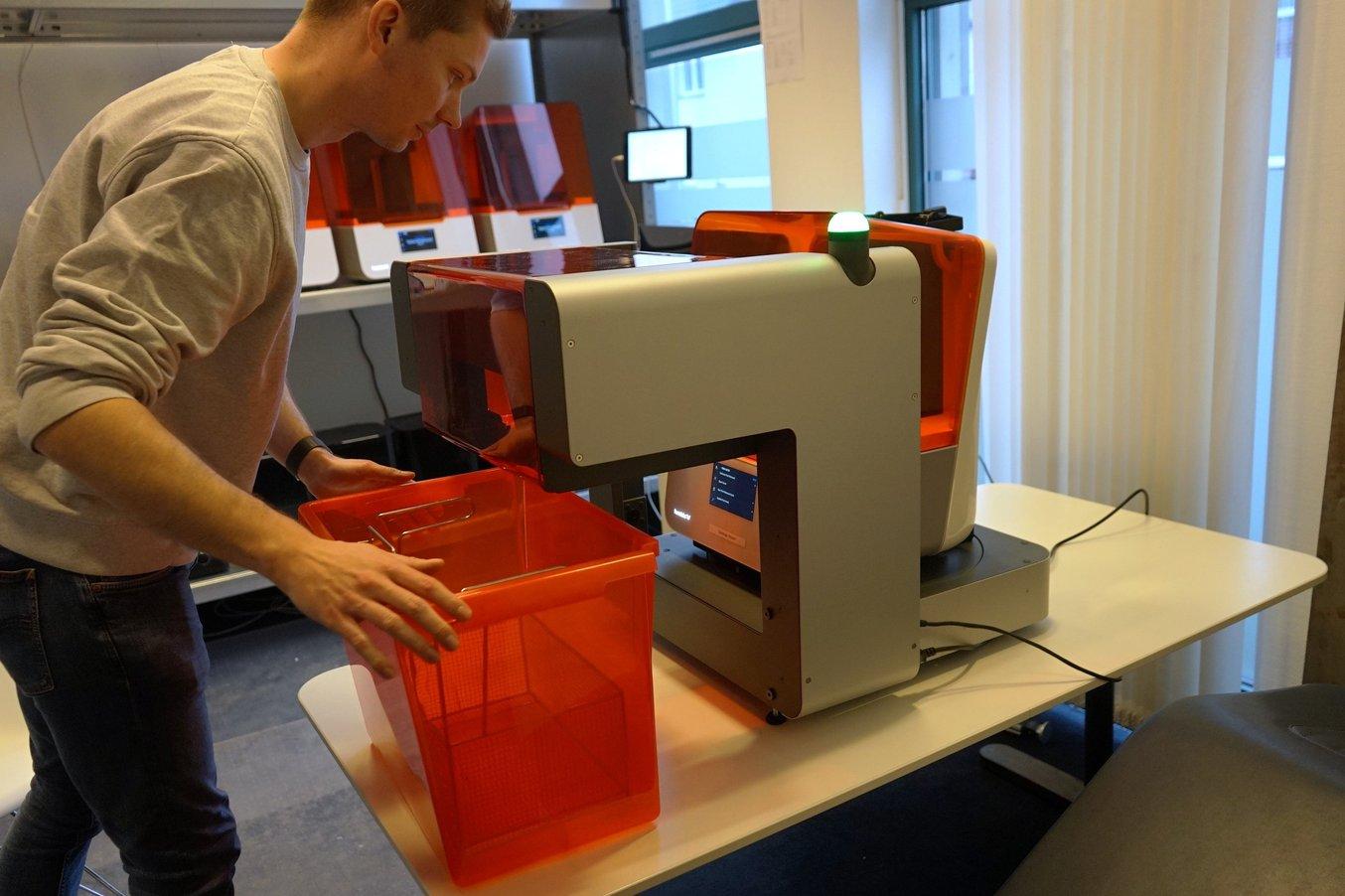
Master dental technician Stephan Kreimer of Kreimer Dentallabor GmbH & Co. KG, tripled dental model production at his dental lab by adding automation.
For example, a printer with automation hardware can print for an entire weekend without needing worker interactions. By contrast, printing 11 dental models in nine minutes on a faster printer would require a worker to remove parts from a build platform and replace the platform before the next print begins. Depending upon your unique business requirements, automation may be the most efficient solution.
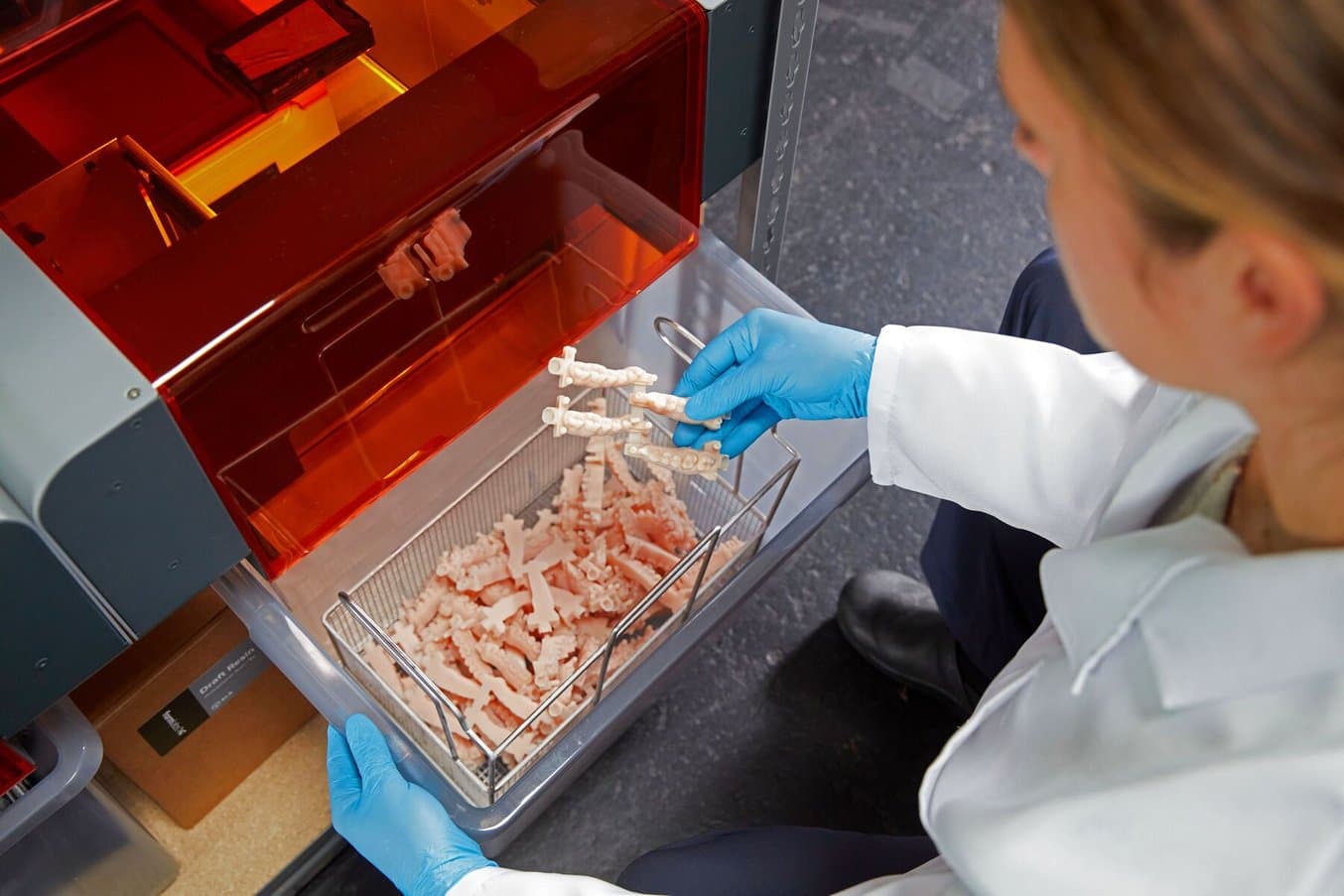
Calculating ROI for the Formlabs Automation Ecosystem
In this whitepaper, we’ll walk through three manufacturing scenarios to explain cost per part and return on investment (ROI) calculations.
Accuracy and Precision
Guaranteeing high-quality, accurate, final parts is the most important concern for any dental practice, orthodontist, or lab. Unfortunately, not all 3D printers marketed for dentistry or orthodontic applications can deliver the quality, precision, and accuracy needed. Additionally, comparing different dental 3D printers goes beyond looking at technical spec sheets.
Some manufacturers may try to confuse prospective customers with misleading statements and technical specifications. Most commonly, they indicate layer height, laser spot size, or pixel size as “accuracy,” even though these specifications do not have a direct impact on the accuracy of final parts. While most companies refer to a single number for accuracy (i.e. 50 μm or 75 μm), these are typically marketing gimmicks, and most commonly represent the limit of resolution of the printer.
Fundamentally, accuracy and precision depend on many different factors: the quality of the 3D printer, the 3D printing technology, materials, software settings, post-processing, and how well-calibrated all of these systems are, so a 3D printer can only be judged on its final dental parts.
Always evaluate accuracy studies with real scan data of printed parts. Even better, ask for a sample part, or a custom sample of your own design, to check the fit or measure against the original design.
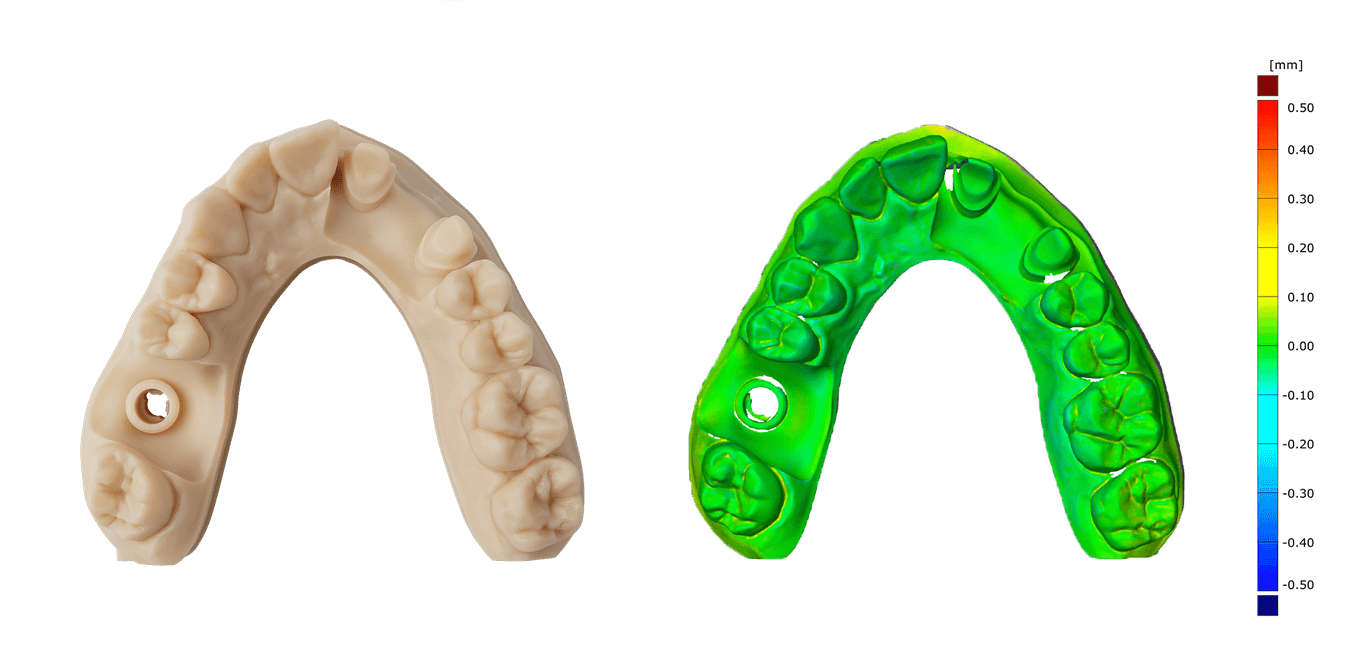
Form 4 Series printers print highly accurate parts anywhere on the Build Platform.
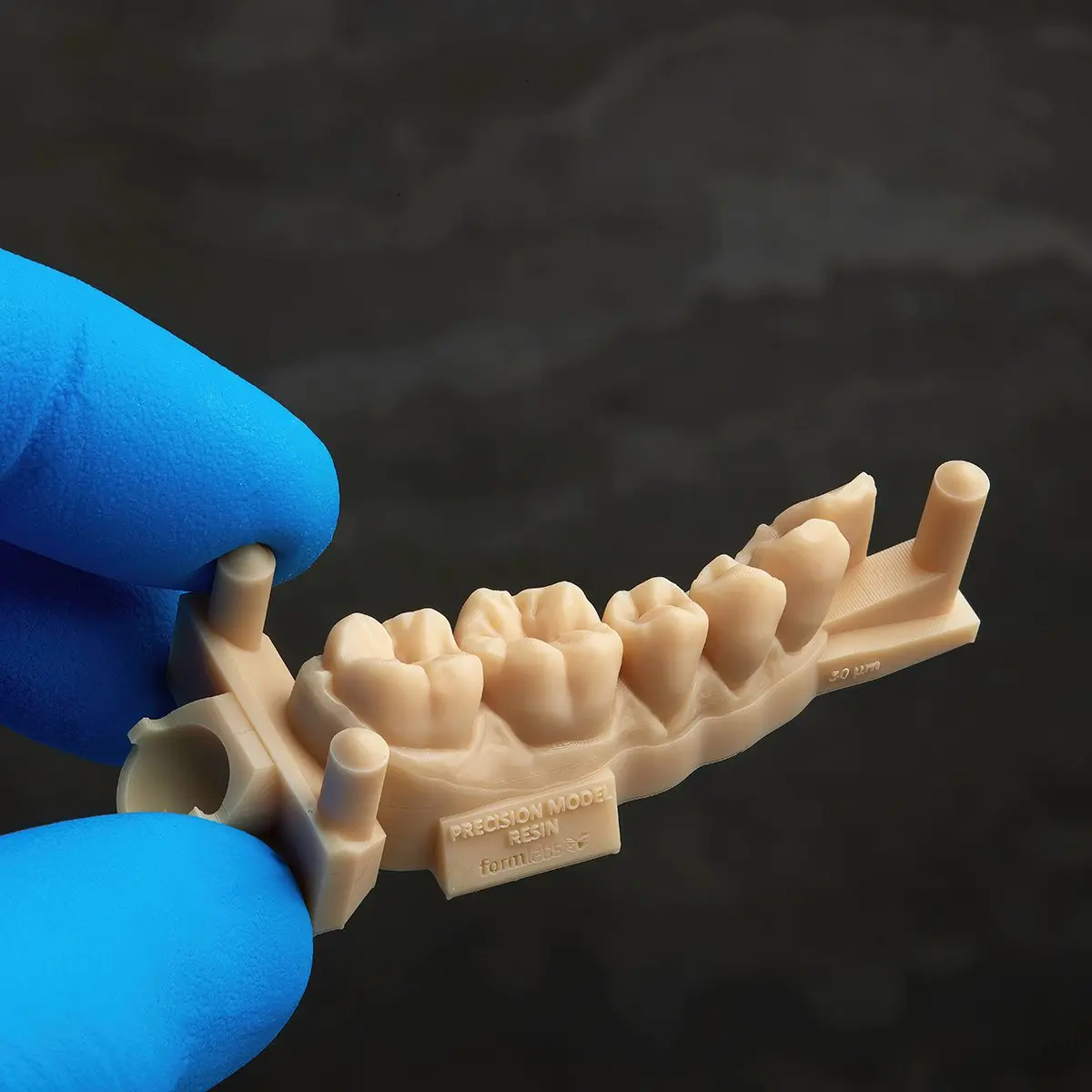
Request a Free 3D Printed Sample Dental Part
Curious to see the quality firsthand? Pick a material and we'll ship you a free sample part 3D printed on the Form 4B to evaluate.
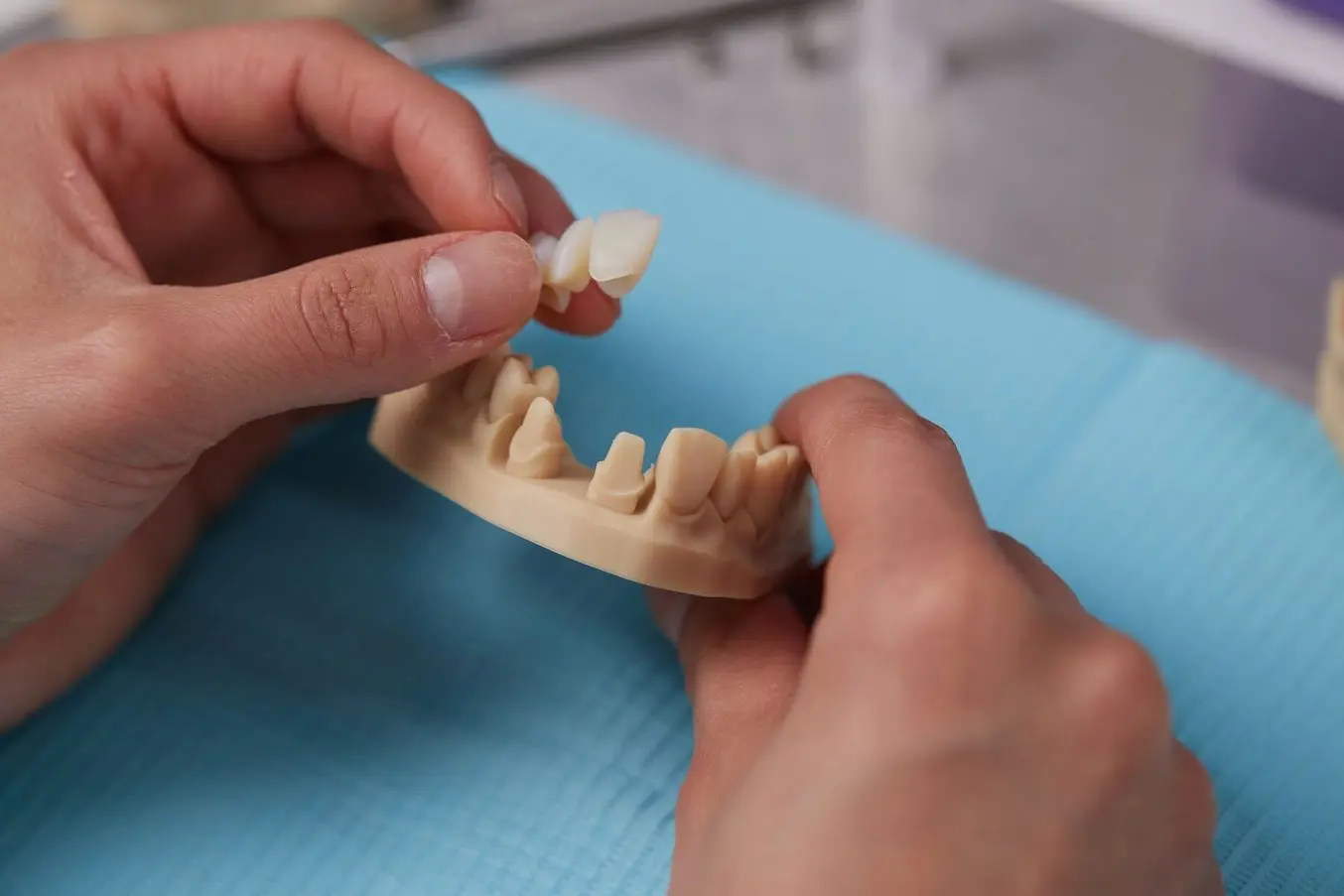
Precision Model Resin and Form 4B: Guide to Making the Most Accurate Restorative Dental Models
The Formlabs Form 4B Masked Stereolithography (MLSA) 3D printer is a game-changer for printing restorative dental models. It features fast printing speeds, reliability, and consistently precise outputs. This article is a guide on how to easily make functional and accurate restorative dental models on Form 4B with Precision Model Resin.
Ease of Use
Ease of use is key not just for onboarding and training, but for daily operations and delegation. After all, you and your team are going to have to learn how to use the equipment and incorporate it into daily work. Try to get a sense of the learning curve that will come with a new 3D printer by watching tutorials, visiting a trade show, contacting sales teams, or asking colleagues about their experience.
The availability of educational resources and guides makes learning new workflows and indications easier. Many companies offer free guides, tutorials, webinars, and even courses to help you get up to speed with the latest, clinically-approved applications.
Some printers come with custom software to prepare 3D models for printing, such as PreForm Dental for Formlabs 3D printers, while other manufacturers offer off-the-shelf solutions less optimized for dentistry. Features differ by software tool. For example, PreForm Dental offers a one-click print setup, where automatic algorithms set up your model’s layout, orientation, and supports based on customizable presets for each indication, so anyone in your office can print successfully without extensive training. With Scan to Model, intraoral scans can be converted into solid printable dental models in less than ten seconds. Plus, advanced users can create custom presets with preferred material, layer height, orientation, and support settings.
Consider the types of everyday interactions as well as regular maintenance the printer will need once it is up and running. For example, some printers require you to manually refill resin, whereas others are automated. Form 4B and Form 4BL include intelligent maintenance modes to keep the printer running smoothly. Additionally, six onboard control systems precisely measure and maintain the temperature, resin level, print forces, and print status inside the printer, shortening the pre-print process and freeing up you or your technicians for higher-value tasks.
Once a part is printed, it must be removed from the build platform. Removing printed parts can result in scratches, broken models, or part defects. Form 4B Flex Build Platform and Form 4L Flex Build Platform features Quick Release Technology, which allows you to remove parts without the use of tools just by moving the stainless steel side handles.
Build Platform Flex with Quick Release technology allows for the removal of parts without the use of tools.
Resin 3D prints require post-processing after printing, so workflow and space requirements as well as labor needs should be considered.
First, the parts need to be washed in a solvent to remove excess resin. Automated washing solutions, such as Form Wash and Form Wash L, can significatly reduce hands-on time and increase efficiency.
Biocompatible dental parts also require post-curing. Formlabs offers high-speed, desktop, and large-format solutions to automate these steps as well, saving time and effort, and making a big difference in keeping a clean, low-maintenance production environment.
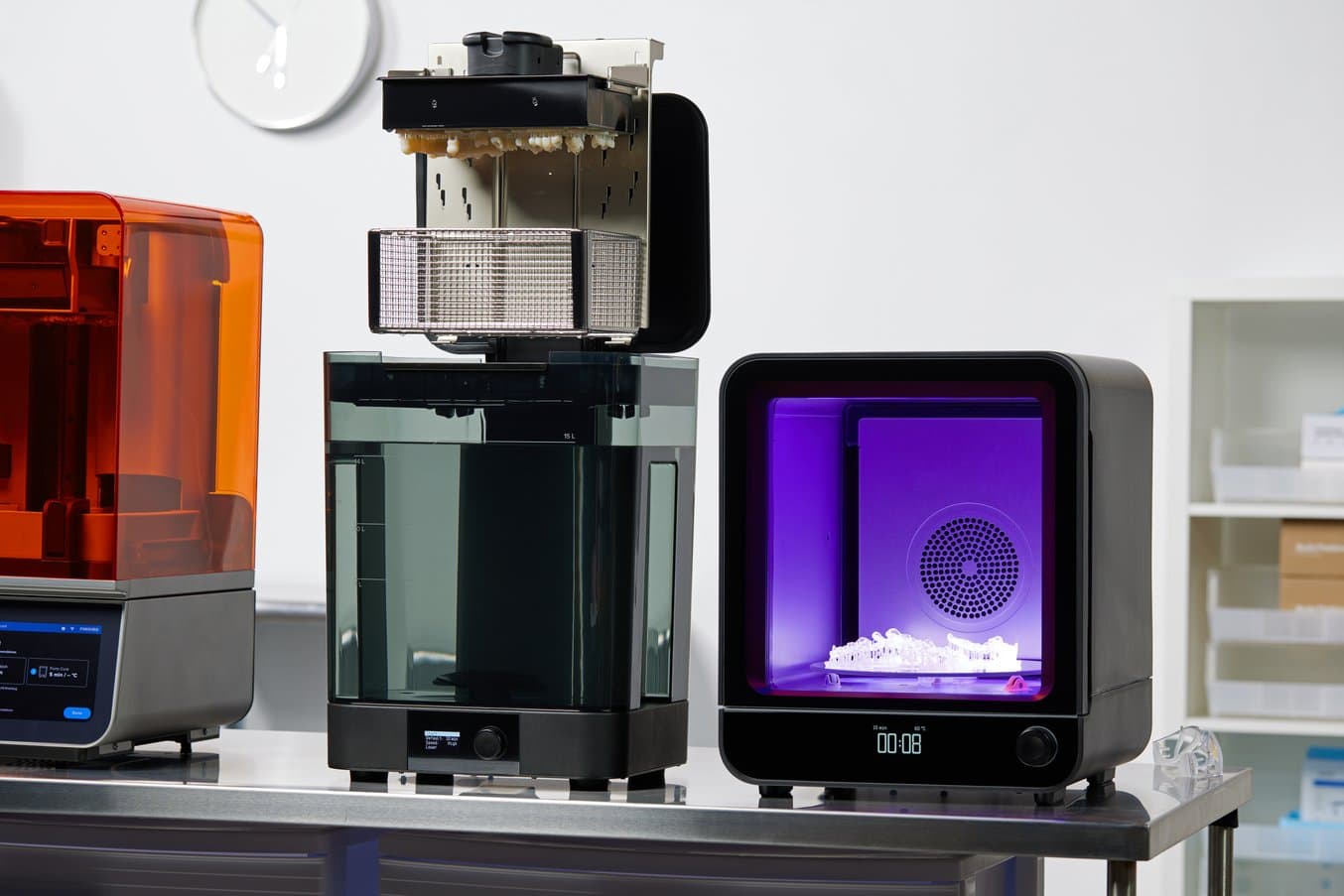
Form Wash and Form Cure automate post-processing, saving time and effort.
Lastly, depending on the design, some parts need to be cleared of support structures. To simplify this step, Formlabs’ resin printers offer light touch supports that greatly reduce both the need for finishing and costly labor. Plus, with the Build Platform Flex, some parts can be printed directly on the build platform — without supports.
Early 3D printers had an infamous reputation for spending half of their lives in service, with many failed prints even when they were online. Fortunately, more recent generations of printers deliver greatly improved reliability. Dig deep into published reliability information, and make sure that a manufacturer has appropriate warranties and service offerings to ensure you’ll be taken care of if service is needed.
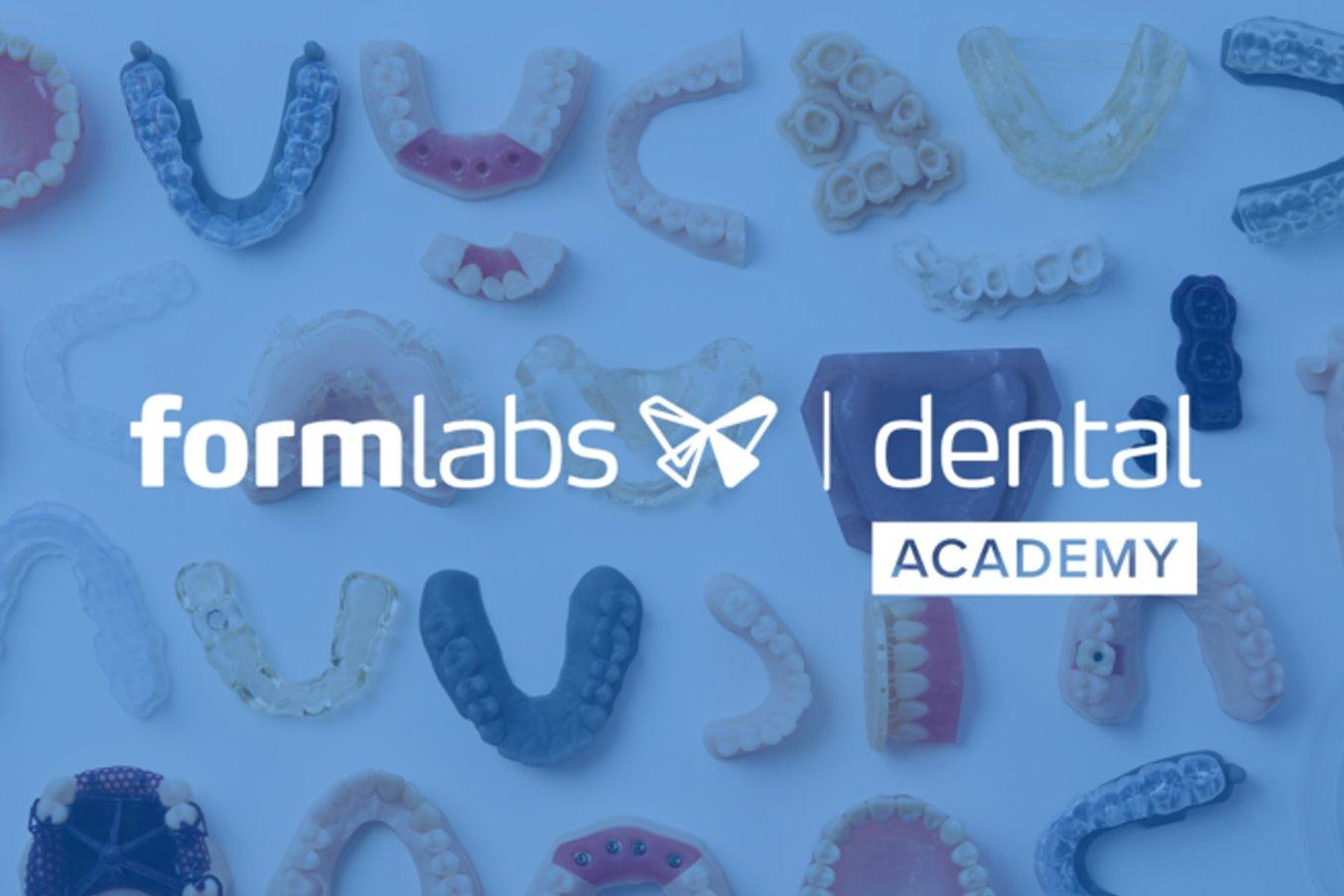
Formlabs Dental Academy
Master digital dentistry workflows, acquire new skills, or go from beginner to dental 3D printing expert with our guided learning sessions and courses.
Cost and Return on Investment
When you consider adopting a new technology, it needs to make sense for your business. Dental 3D printer prices have dropped significantly since the early days and the systems on the market today offer the lowest costs for many applications.
For example, a practice or lab printing surgical guides or dental models to produce thermoformed aligners in-house can often reduce costs by 75-95% for each part compared to outsourcing to labs or service providers — enough to pay for a 3D printer in a few weeks and save many times its price tag over the years.
When you compare dental 3D printers, remember to consider:
- Upfront costs, including not just the machine cost, but also training, setup, and potentially software.
- Running costs, best estimated with per-unit material costs.
- Servicing and maintenance costs, which can be expensive without a service plan.
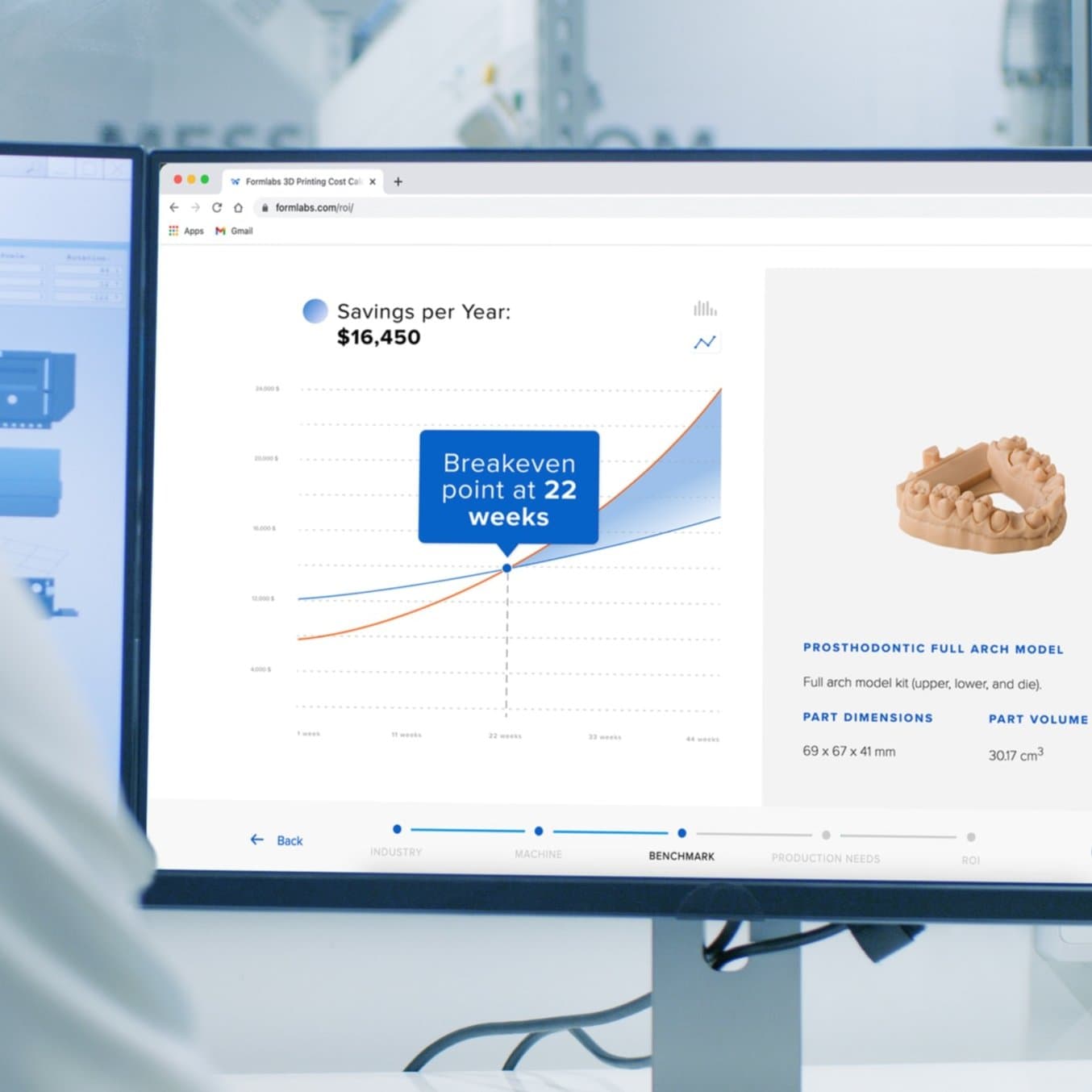
Calculate Your Time and Cost Savings
Try our interactive ROI tool to see how much time and cost you can save when 3D printing on Formlabs dental 3D printers.
Materials and Applications
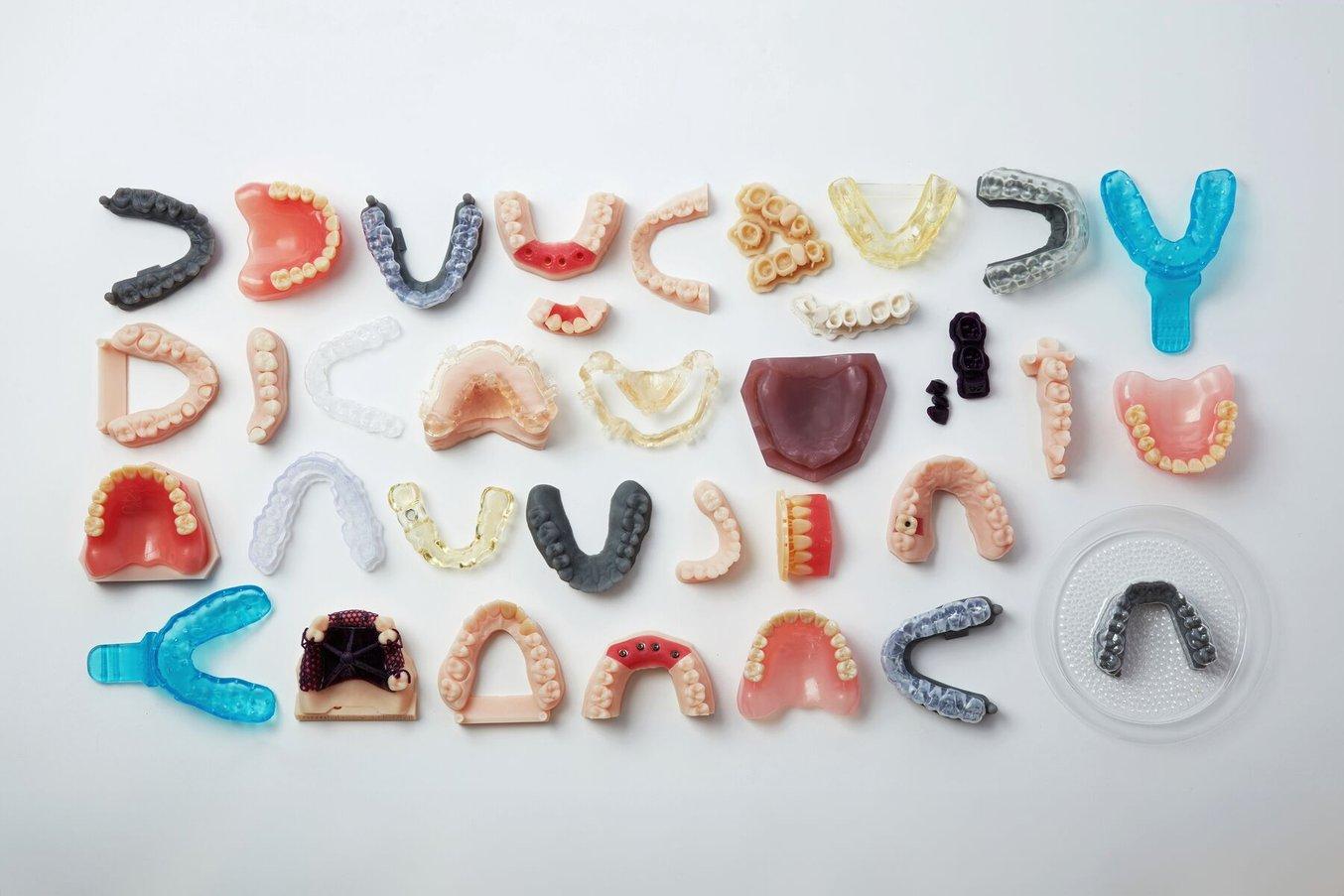
Formlabs offers 17+ dental resins, including biocompatible resins produced at our FDA-registered facility in Ohio.
Professional 3D printers are some of the most versatile tools found today in dental and orthodontic practices and labs, and the key to their versatility is dedicated materials.
Material selection varies by printer brand and model. Some basic 3D printers can only produce a few indications like diagnostic models, while more advanced systems such as Form 4B/BL can manufacture appliances for orthodontic or restorative applications including:
- Diagnostic models
- Clear aligner models
- Orthodontic models for wire retainers
- Restorative models
- Surgical guides
- Splints, mouthguards, and occlusal guards
- Full dentures
- Temporary All-on-X appliances
- Temporary restorations
- Permanent restorations
- Custom impression trays
- Patterns for casting and pressing
- Indirect bonding trays
- Direct composite restoration guides
Some 3D printers work only with proprietary materials, which means your options are limited to the offerings of the printer manufacturer. Others have an open system, meaning that they can use materials made by third-party manufacturers.
However, when using third-party materials, it’s important to make sure that the results achieve clinically acceptable quality and accuracy. Furthermore, using biocompatible materials on non-validated 3D printers that claim to be “open” breaks the usage requirements and will produce non-biocompatible appliances. Be careful that you know what risks your business takes by using non-validated 3D printers and materials.
It’s important to check the available materials for a given 3D printer against the list of appliances you’re looking to print. However, the industry is innovating incredibly fast, so most manufacturers regularly release new materials and updated formulations, and there’s a good chance that the printer you buy today will become capable of creating an increasing variety of dental products in the near future.
Form 4B can print 17+ dental-specific Formlabs resins including biocompatible resins developed and validated under a stringent QMS and produced in an ISO 13485-certified facility. For even more freedom, open materials and print settings are also available.
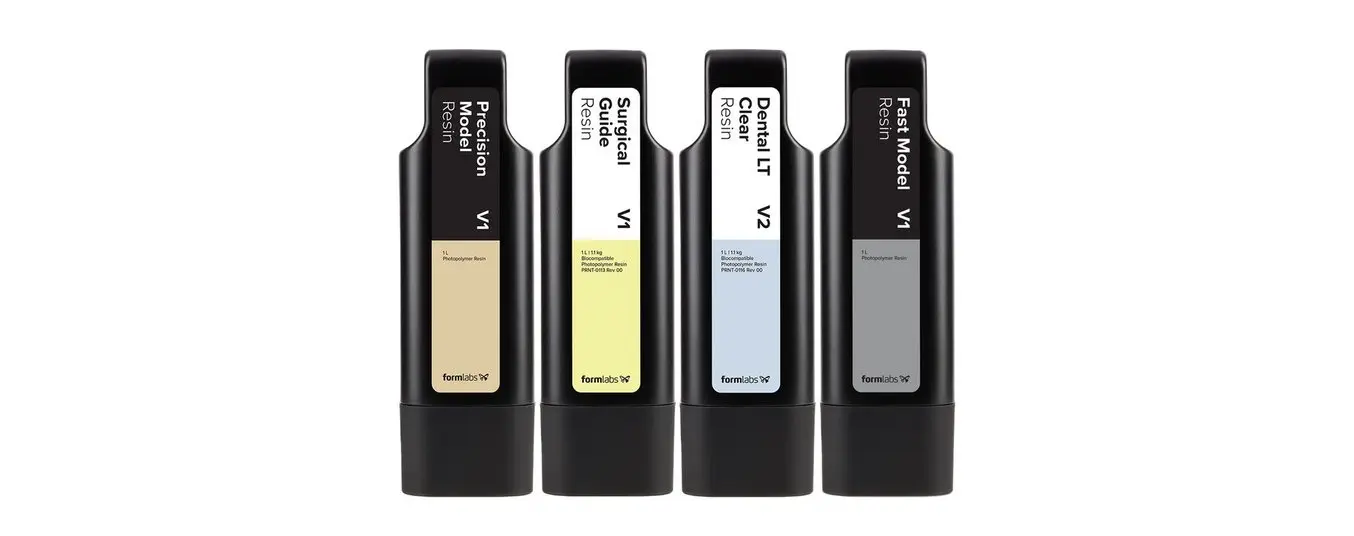
Formlabs Dental Materials Overview: Discover What You Can Print With the Form 4B
This webinar will guide you through the various benefits and applications enabled by Form 4B, including its existing biocompatible materials and newly developed formulations for model production such as Fast Model Resin and Precision Model Resin.
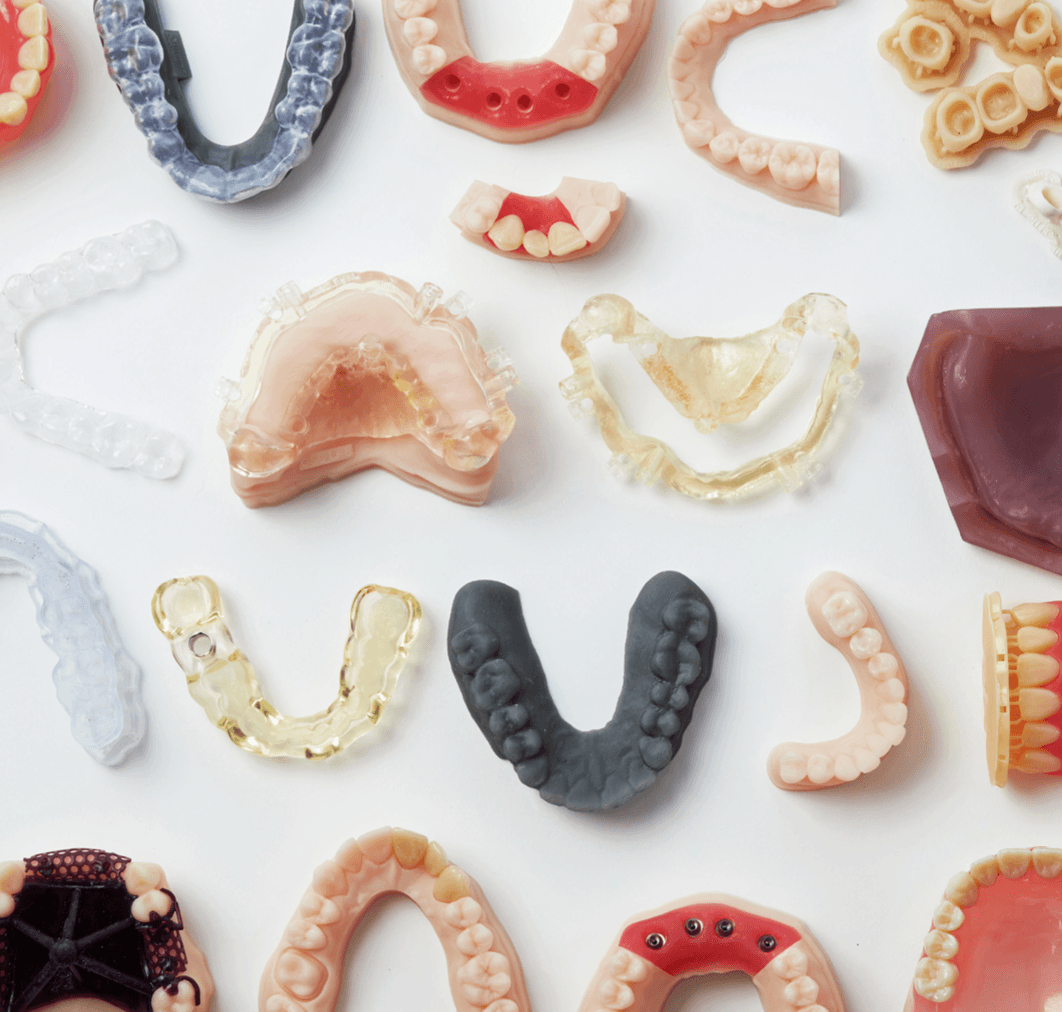
An Introduction to Regulatory Compliance in Dental 3D Printing
Implementing 3D printing workflows in your lab or practice can be a game changer for your business. Understanding the basics of regulatory compliance can help inform your decisions and what is best for your business. Regulation depends on geography; in this paper, we examine regulations in the United States of America and the European Union.
Get Started With Digital Dentistry and 3D Printing
3D printers have become important tools for dental and orthodontic practices as well as labs, streamlining workflows, minimizing turnaround times, and improving patient care.
When selecting a 3D printer, it’s important to weigh speed, throughput, accuracy, precision, ease of use, return on investment, support, and materials. Consider the factors discussed above and the needs of your unique business. Make sure to do your research, evaluate actual parts, and avoid paying a hefty premium.
Get in touch with one of our dental 3D printing experts or explore the Formlabs Dental Academy and our resources library for free guides, step-by-step tutorials, white papers, webinars, and courses to learn how you can integrate 3D printing into your lab or practice.
Curious to see the quality firsthand? Request a free sample part 3D printed on Form 4B to evaluate.