Wie digitale Arbeitsabläufe und 3D-Druck Partnerschaften mit mehr als 160 Zahnarztpraxen in Italien möglich machen
Im Jahr 2011 gründete Mimmo Castellana SmileLine Allineatori Invisibili, ein auf unsichtbare Kieferorthopädie spezialisiertes Zahnlabor mit Sitz in Mola di Bari. Dank digitaler Arbeitsabläufe arbeitet SmileLine heute mit mehr als 160 Zahnarztpraxen in ganz Italien zusammen und stellt mit Formlabs-Druckern bis zu 100 Modelle und Aligner pro Tag her.
Im Folgenden erfahren Sie, was Mimmo dazu bewegt hat, die Modelle mittels 3D-Druck betriebsintern zu produzieren, statt auf externe Hersteller zurückzugreifen, wie es in der Branche bisher üblich war.
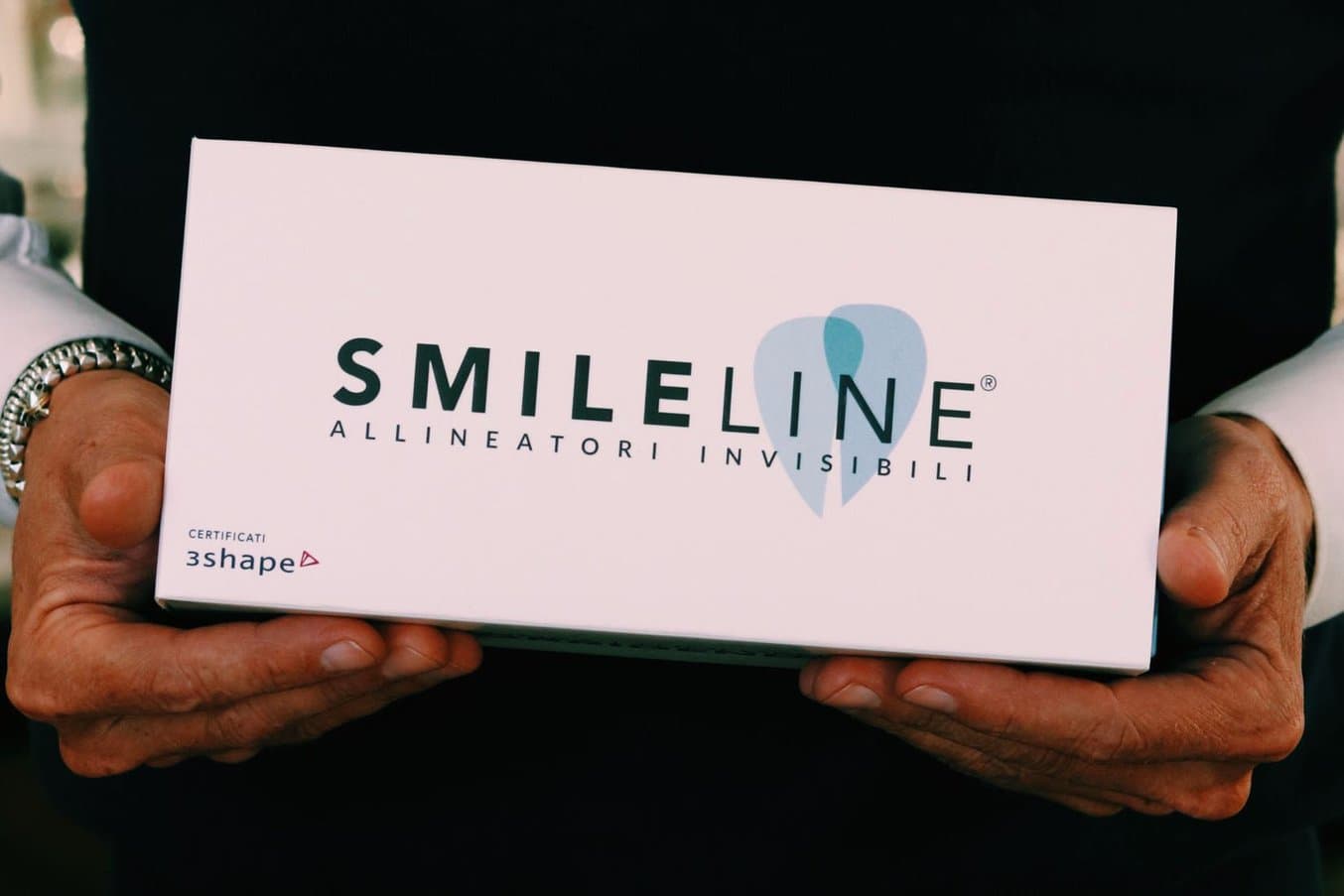
Wechsel zu digitalen Arbeitsabläufen
Die Modelle der verschiedenen Hersteller in Italien und anderen Ländern erreichten nicht die gewünschte makellose Oberflächengüte. Tatsächlich wies die Oberfläche dieser Modelle statt einer polierten Beschaffenheit sogar deutliche Schichtlinien auf. Die darauf thermogeformten Alignern reproduzierten diese Schichtlinien und waren dadurch lichtundurchlässig und anfällig für Plaque. Durch die Ansammlung von Plaquebakterien zwischen den Schichten verfärbten sich die Aligner innerhalb weniger Tage von transparent zu gelb. Hierbei darf man nicht vergessen, dass sich Patienten gezielt für unsichtbare Kieferorthopädie entscheiden, damit ihre kieferorthopädische Behandlung weniger auffällig ist. Es ist also eine begründete Erwartung, dass der Aligner während der gesamten Behandlung transparent und unsichtbar bleibt. Als mit den Ansprüchen von Ärzten und Endverbrauchern auch der Arbeitsaufwand anstieg, erkannte Mimmo den Bedarf an einem Produkt, das eine funktionierende Alternative zur existierenden Lösung bieten könnte.
2015 traf er auf der International Dental Show (IDS) in Köln das Team von Formlabs. Nach der Messe schickte er Formlabs eine Datei zur Fertigung eines kostenlosen Probedrucks zu. Dieselbe Druckdatei schickte er auch einem der Hersteller und verglich anschließend die Ergebnisse. Wie Mimmo uns berichtet, erhielt er zwei völlig unterschiedliche Modelle: Eines wies die bekannten, deutlichen Oberflächenmängel auf, während das andere über eine glatte Oberfläche und präzise Details verfügte. Er beschloss, seinen ersten Formlabs-3D-Drucker zu erwerben. Inzwischen besitzt SmileLine sechs Stück.
„Bevor ich mich für Formlabs entschied, habe ich mich auf dem Markt umgesehen, doch zu meinen Ansprüchen passte Formlabs genau. Ich musste durchgängig drucken können, und in dieser Hinsicht stießen andere Drucker leider an ihre Grenzen. Bei anderen Druckermodellen hätten wir das Kunstharz zum Beispiel manuell einfüllen müssen. Das hätte uns riesige Umstände bereitet. Ich brauchte die Option, Drucke auch nachts starten zu können, damit meine Arbeit am nächsten Morgen bereit für die Aligner ist.“
Mimmo Castellana, Gründer von SmileLine Allineatori Invisibili
Druck und Bearbeitung der Modelle
Mimmo und sein Team halten die Drucker dauerhaft in Betrieb, Tag und Nacht, und zwar mit durchgehend hervorragenden Ergebnissen. Dadurch läuft die Arbeit des gesamten Teams reibungslos ab. Die Drucker arbeiten nach betriebsinternen Prozessen, die für das SmileLine-Team eine hoch schematische, saubere und fehlerlose Arbeitsumgebung schaffen.
Durch Tests mit vertikalen und horizontalen Drucken stellte Mimmo fest, dass die thermogeformten Aligner wie angegossen auf das Gipsmodell passten, wenn die Zahnmodelle horizontal gedruckt werden. Nachdem die Modelle fertig gedruckt sind, werden sie in der Spülstation Form Wash behandelt, gründlich überprüft und schließlich in den Form Cure übertragen, der die Nachhärtung abschließt. Ist auch die Nachhärtung beendet, wird das Modell in hochpräzise Thermoformmaschinen eingesetzt und der Vorgang wird fertiggestellt. Um durchgehend optimale Druckergebnisse zu gewährleisten, werden die Modelle nicht hohl, sondern massiv gedruckt. Wird hohl gedruckt, besteht die Gefahr, dass durch den hohen Druck der professionellen Thermoformmaschinen (6 bar), dem die Aligner ihre Passgenauigkeit verdanken, Teile des dünnen Modells verformt werden. Durch Druck massiver Modelle werden derartige Probleme vermieden.
Nachdem Mimmo und das Team von SmileLine mehrere Modelle mit verschiedenen Formlabs-Kunstharzen getestet hatten, kamen sie zu dem Schluss, dass Grey Resin für ihre Aligner und kieferorthopädischen Geräte die ideale Wahl darstellt. Für die Herstellung von Lehrmodellen verwendet das Dentallabor von SmileLine allerdings auch White Resin und Model Resin, sowie Draft Resin zur schnellen Produktion von Bleichschablonen und Retainern. Bei vollem Betrieb von Montag bis Freitag druckt SmileLine bis zu 100 Modelle pro Tag auf sechs Druckern von Formlabs, unter anderem dem Form 2, Form 3 und Form 3B. Zusätzlich dazu hat Mimmo sich vor Kurzem die Build Platform 2 bestellt, die seiner Meinung nach eine große Bereicherung für sein Team darstellen wird. Da das Team von SmileLine horizontal, ohne Stützstrukturen druckt, erfordert das Entfernen der Modelle von der Konstruktionsplattform besondere Umsicht, damit keine Brüche entstehen.
Ausdehnung auf neue zahnmedizinische Anwendungen
SmileLine nutzt seine Formlabs-Drucker neben der Herstellung von Alignern auch für traditionelle kieferorthopädische Modelle. Es gibt eine große Palette möglicher Anwendungen, zum Beispiel Dehnplatten, Gaumennahterweiterungen, Palatinalbögen, funktionelle Zahnspangen und sonstige traditionelle und digitale kieferorthopädische Anwendungen jeder Art.
Mimmo erzählte uns von seinem Traum, in naher Zukunft leistungsstarke digitale Okklusionsschienen herstellen zu können, mithilfe neuer Produkte, die den bisher verfügbaren möglichst nahe kommen. Vorerst stellt SmileLine diese Schienen noch auf der Werkbank her, nach einem eigenen Protokoll. Er berichtete uns außerdem, dass er dringend nach elastischen Produkten suche, mit denen statt orthopädischer auch kieferorthopädische Erweiterungen möglich wären, indem ausschließlich die Zähne bewegt würden, um Platz zu schaffen.
„Ich glaube, Wissenschaft und Unternehmen, die sich mit Forschung und Entwicklung beschäftigen, suchen ständig nach Produkten zur Vereinfachung der täglichen Arbeit, die für die Bedürfnisse aller Patienten geeignet sind, auch solcher mit Allergien. So etwas machen biokompatible Produkte möglich, die verträglicher sind als die bisher verfügbaren Metalle und Metalllegierungen. Das wäre wirklich ein Wundermittel.“
Mimmo Castellana, Gründer von SmileLine Allineatori Invisibili
Traditionelle und digitale Methoden im Vergleich
Das Labor von SmileLine ist von 3Shape zertifiziert, da es das gesamte System des Entwicklers integriert hat, vom Scanner bis zur Verarbeitungssoftware. So kann SmileLine nicht nur Scan-Dateien von jeglichen heute erhältlichen Intraoralscannern empfangen, sondern ist über die Software Communicate auch in der Lage, mit den 3Shape-Scans von Partnerpraxen zu kommunizieren. Der digitale Abdruck von 3Shape erkennt den Intraoralscan und sendet dem Labor – in diesem Fall SmileLine – die STL-Datei direkt durch die patentierte Software zu, ohne E-Mail, Dropbox oder sonstige Kommunikationskanäle zu nutzen.
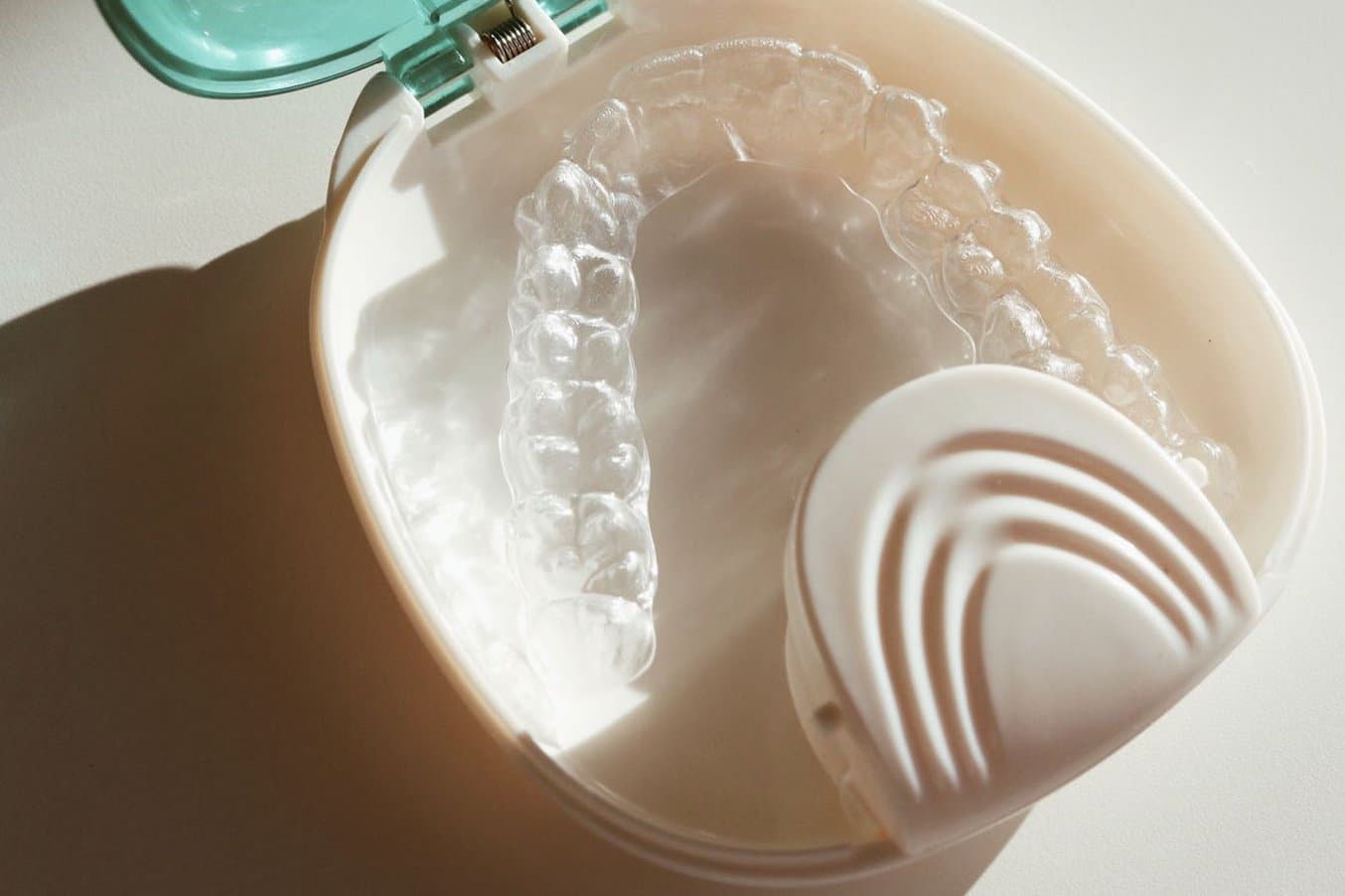
Um sicherzustellen, dass der gesamte Prozess vom Scan zum Labor und wieder zurück perfekt verläuft, führt SmileLine regelmäßig Tests durch, die dank kontinuierlicher Forschung und Entwicklung möglich sind. So wurden zum Beispiel eine Scan-Datei, die intern verarbeitete Datei sowie das mit einem Formlabs-Drucker gedruckte Modell ermittelt. Das Modell wurde gescannt und anschließend wurden alle drei Dateien – also die Scan-Datei, die intern kreierte Datei und die anhand des 3D-Drucks erstellte Datei – miteinander verglichen. Das Ergebnis war überwältigend. Alle drei Dateien waren vollkommen deckungsgleich. Die per Scan erstellte Datei wurde schließlich detailgetreu von den Druckern wiedergegeben. Dieses Ergebnis ist in jeder Hinsicht hervorragend, denn alle Zahnhöcker und jedes Detail des Zahnbogens deckten sich vollkommen mit der ursprünglichen, aus dem digitalen Abdruck erstellten Datei. Das bedeutet, dass die mit Formlabs-Druckern erzielten Ergebnisse mit den durch Intraoralabdrücke oder traditionelle Abdrücke erreichbaren Ergebnissen absolut vergleichbar sind.
Kapitalrendite und Zeitersparnis
In der Vergangenheit musste SmileLine seine Produktionszentren nach Stückzahl bezahlen und außerdem auch die Lieferkosten übernehmen. Dank Formlabs konnte Mimmo diese Kosten deutlich senken.
„Das Beste an Formlabs ist aber, dass es mir hilft, keine Zeit zu verschwenden. Dank der digitalen Scans kommt die Datei sofort im Labor an und schon am nächsten Tag können wir den Retainer verschicken. Bei Retainern ist es entscheidend, dass sie schnell versandt werden, da das Risiko eines Rezidivs und des Verschiebens der Zähne hoch ist. Ginge der Druck nicht so schnell, müssten wir das Modell bearbeiten, es zum Designzentrum schicken und zwei, drei oder sogar vier Tage warten. Stattdessen können wir dem Empfänger heute alles am selben Tag bereitstellen. Das ist einerseits eine große Zeitersparnis, aber auch eine Verbesserung des Service an sich.“
Mimmo Castellana, Gründer von SmileLine Allineatori Invisibili
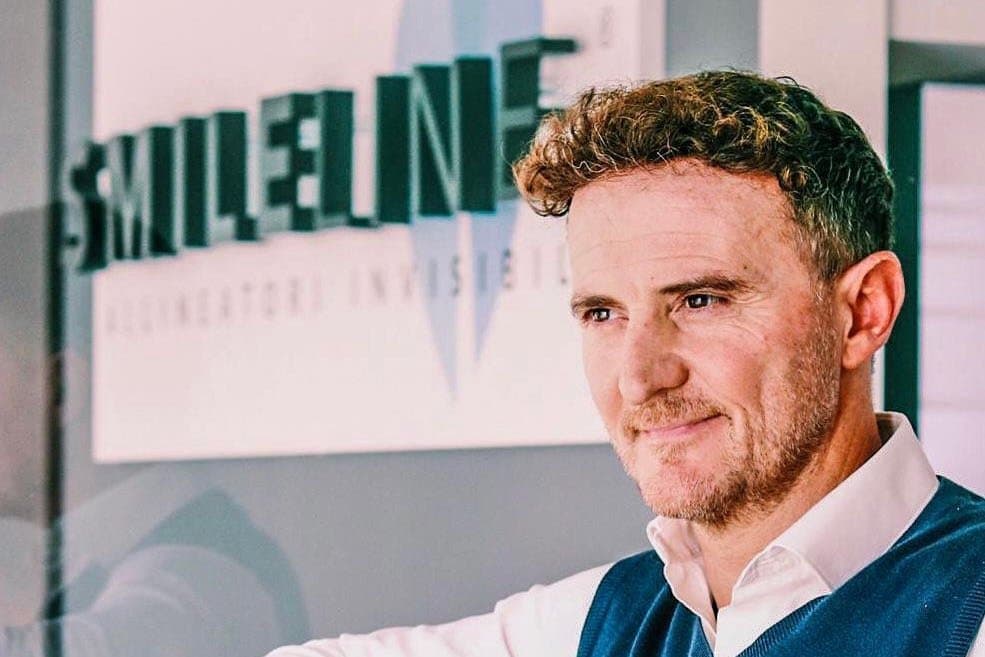
Die Zukunft der digitalen Zahntechnik
„Wenn ich zurückblicke“, so Mimmo, „dann wird mir bewusst, dass wir heute, verglichen mit vor zwei oder drei Jahren, Dinge vollbringen, die vorher unvorstellbar waren.“ Mimmo ist überzeugt, dass 3D-Druck noch viel mehr Möglichkeiten bereithält. Den Großteil seiner Zeit verbringt er heute am Computer, mit der Arbeit an seinen Druckern, und nicht an der Werkbank. „Die Zukunft des 3D-Drucks hängt aber von den Unternehmen ab, und in meiner Branche auch davon, wie viele biokompatible Produkte kreiert werden. Ich denke außerdem, dass additiv gefertigte Produkte qualitativ deutlich hochwertiger sind als subtraktiv gefertigte. Hersteller von festsitzendem Zahnersatz hoffen so bald wie möglich auf ein Material, dass es auch Ihnen ermöglicht, 3D-Druck zu nutzen.“
Fazit
SmileLine verwendet ausschließlich Drucker von Formlabs, da das Labor damit vollkommen äquivalente Ergebnisse erzielt, trotz eines geringfügigen Zeitunterschieds zwischen Form 2 und Form 3. „Meine Drucker leisten harte Arbeit. Ich bin von ihnen beeindruckt, denn ich nutze sie ständig, sie werden fortwährend beansprucht“, berichtet uns Mimmo und erklärt: „Mein Team entfernt die Konstruktionsplattform, löst die Modelle ab, setzt die Plattform wieder ein und dann startet der Drucker auch schon von Neuem. Es ist ein kontinuierlicher und beständiger Arbeitszyklus. Sobald einer meiner Drucker den Geist aufgibt, werde ich ihn guten Gewissens ruhen lassen, denn er hat seinen Beitrag mehr als zufriedenstellend geleistet. Wenn auch der letzte Form 2 sich verabschiedet hat, werde ich ihn ersetzen müssen, vielleicht durch einen neuen Form 3B+.“