Transferschienen für die Platzierung kieferorthopädischer Brackets, gedruckt auf den SLA-3D-Druckern von Formlabs
Dieser Anwendungsleitfaden ist eine Schritt-für-Schritt-Anleitung des Arbeitsablaufs zur Herstellung von Transferschienen für die Platzierung kieferorthopädischer Brackets mittels Formlabs' IBT Flex Resin und der 3D-Drucker von Formlabs Dental. Ziehen Sie für die unbedingten Anforderungen stets den Fertigungsleitfaden und die Gebrauchsanweisung zurate.
IBT Flex Resin ist ein flexibles biokompatibles Material für die effiziente und präzise Platzierung von kieferorthopädischen Brackets. 3D-gedruckte Transferschienen verringern die Behandlungsdauer und erhöhen den Patientenkomfort, indem alle Brackets oder ganze Quadranten auf einmal platziert werden. IBT Flex Resin ist ein Medizinprodukt der Klasse I und bietet optimierte Reißfestigkeit, Lichtdurchlässigkeit und Flexibilität für dentale Anwendungen, die sich leicht planen, verwenden und lösen lassen.
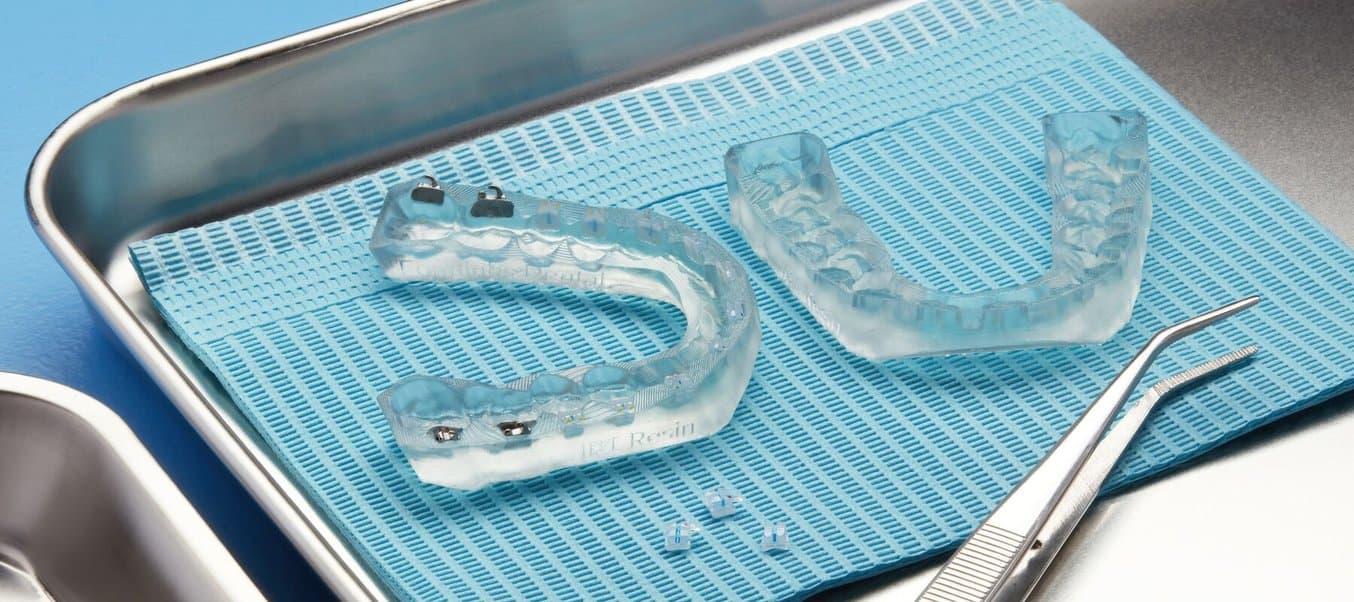
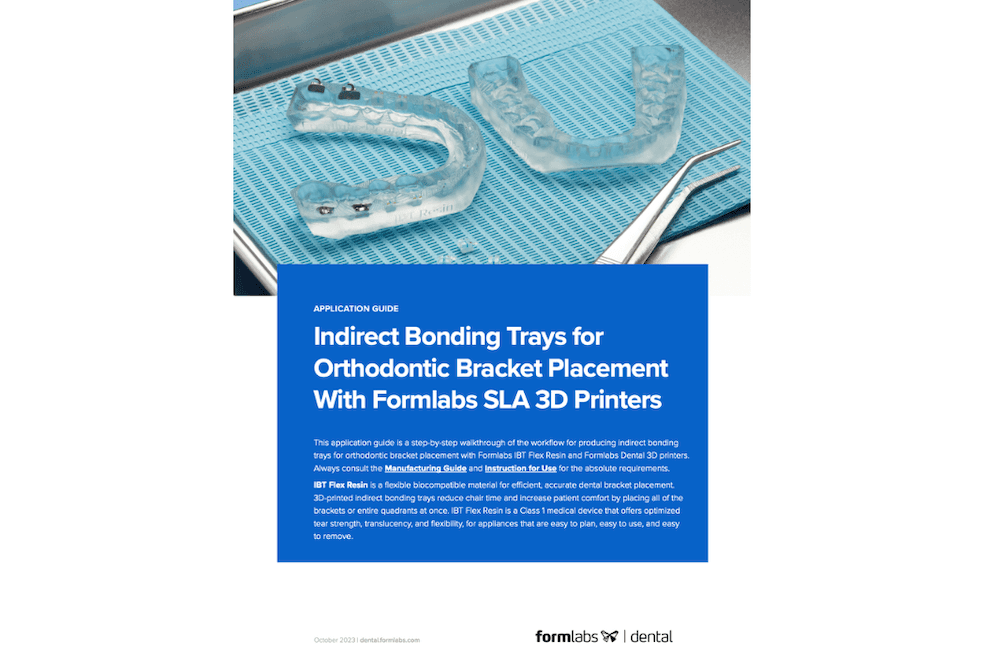
Transferschienen für die Platzierung kieferorthopädischer Brackets, gedruckt auf den SLA-3D-Druckern von Formlabs
Möchten Sie diesen Leitfaden speichern, drucken oder mit anderen teilen? Laden Sie ihn als PDF herunter.
Prozessanforderungen
Von zahnärztlicher Seite benötigt
- Eine physische oder digitale Abformung des Patientengebisses
Benötigte Hardware und Materialien
Von Formlabs:
- SLA-3D-Drucker Form 3B/+ oder SLA-3D-Drucker Form 3BL
- Form 3 Resin Tank oder Form 3L Resin Tank
- Standardmäßige Build Platform, Stainless Steel Build Platform oder Build Platform 2
- IBT Flex Resin
- Form Wash oder Form Wash L
- Von Formlabs validierte Aushärteeinheit: Form Cure, Form Cure L, Fast Cure
- Finish Kit oder zweite Waschstation
Von Drittanbietern:
- Desktop-Scanner (bei Verwendung physischer Abformungen oder Modelle)
- Schneid- und Nachbearbeitungswerkzeuge (bei Druck mit Stützstrukturen)
- Lichtundurchlässige oder orangefarbene Behälter für die Lagerung der dentalen Anwendungen
- DVT-Scanner (optional, je nach CAD-Software)
Benötigte Software
Von Formlabs:
- PreForm Version 3.32 oder höher (kostenlos)
- Firmware 2.2.0 oder höher – Weitere Informationen
Von Drittanbietern:
- Software für das Dentaldesign oder Outsourcing zu einem Dentaldesign-Dienstleister
1. Scan
Die Software für das Dentaldesign erfordert eine digitale Abformung der Patientenanatomie, um eine Transferschiene für die indirekte Verklebung zu entwerfen. Scannen Sie Patient*innen dafür direkt mit einem 3D-Intraoralscanner oder scannen Sie eine physische Abformung oder ein gegossenes Modell mit einem Desktop-3D-Scanner.
DVT-Daten sind zwar optional, doch von einigen Designsoftwarepaketen für Transferschienen werden diese Daten unterstützt, was für Fallplanung und -aufbau äußerst nützlich sein kann.
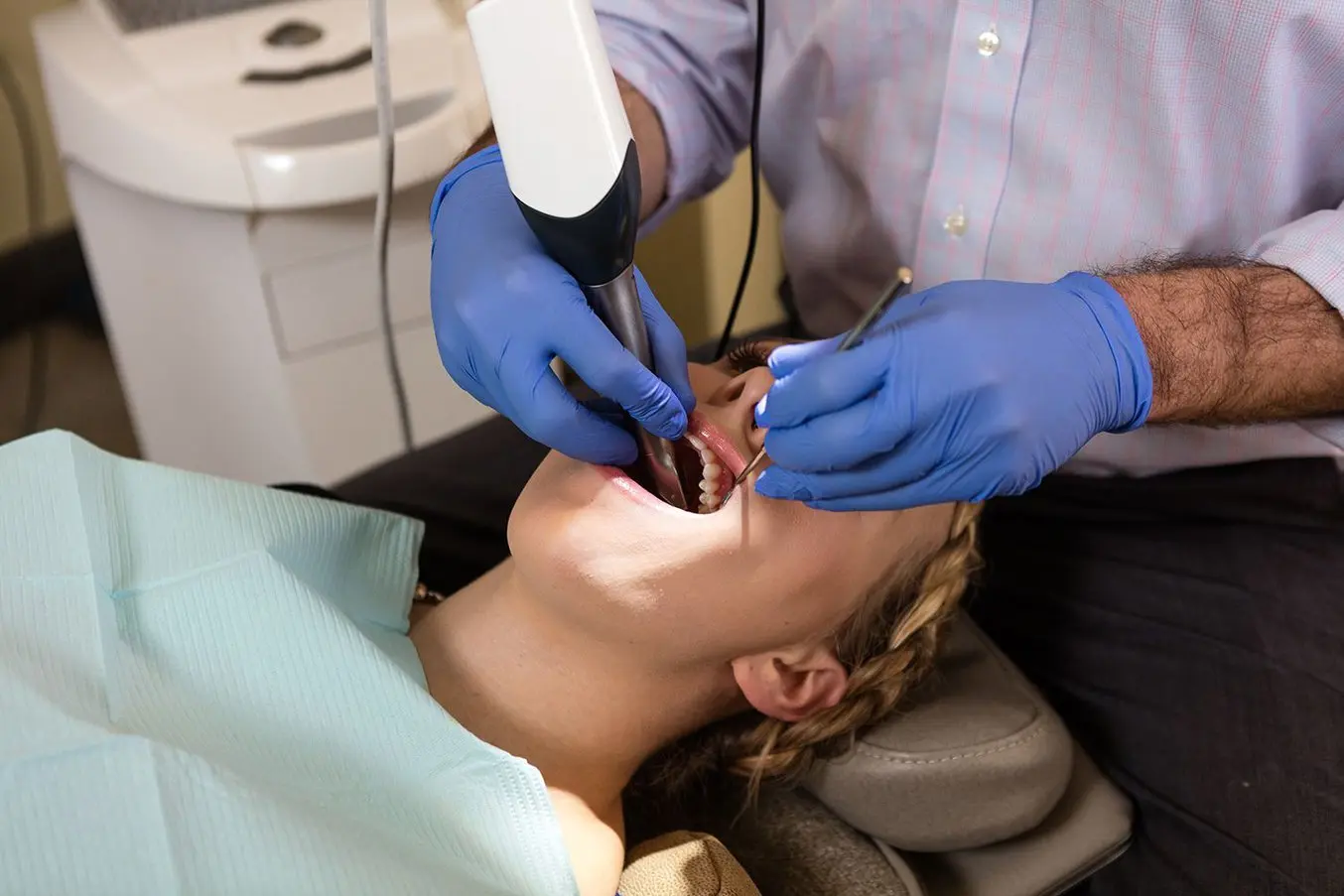
2. Design
2.1 Transferschiene entwerfen
In diesem Abschnitt gehen wir auf die Designparameter und bewährten Praktiken für 3Shape Ortho System ein (Ortho Analyzer und Appliance Designer). Die Grundlagen und Empfehlungen sind auch für andere Behandlungs- und Planungssoftwares wie etwa OnyxCeph hilfreich und sollten daher gelesen werden.
Sie können die digitale Abformung und die Anforderungen auch an einen zahnmedizinischen CAD-Dienstleister senden, wie z. B. ein zahnmedizinisches Designzentrum oder ein spezialisiertes Dentallabor, um die dentale Anwendung und die Fertigungsdatei erstellen zu lassen.
Anmerkung: Bei 3Shape Ortho System empfehlen wir die Verwendung des Typs „Block“ für die dentale Anwendung. Eine ausführliche Anleitung zur Einrichtung und zum Design dieser Anwendungen finden Sie im Anwendungsleitfaden von 3Shape.
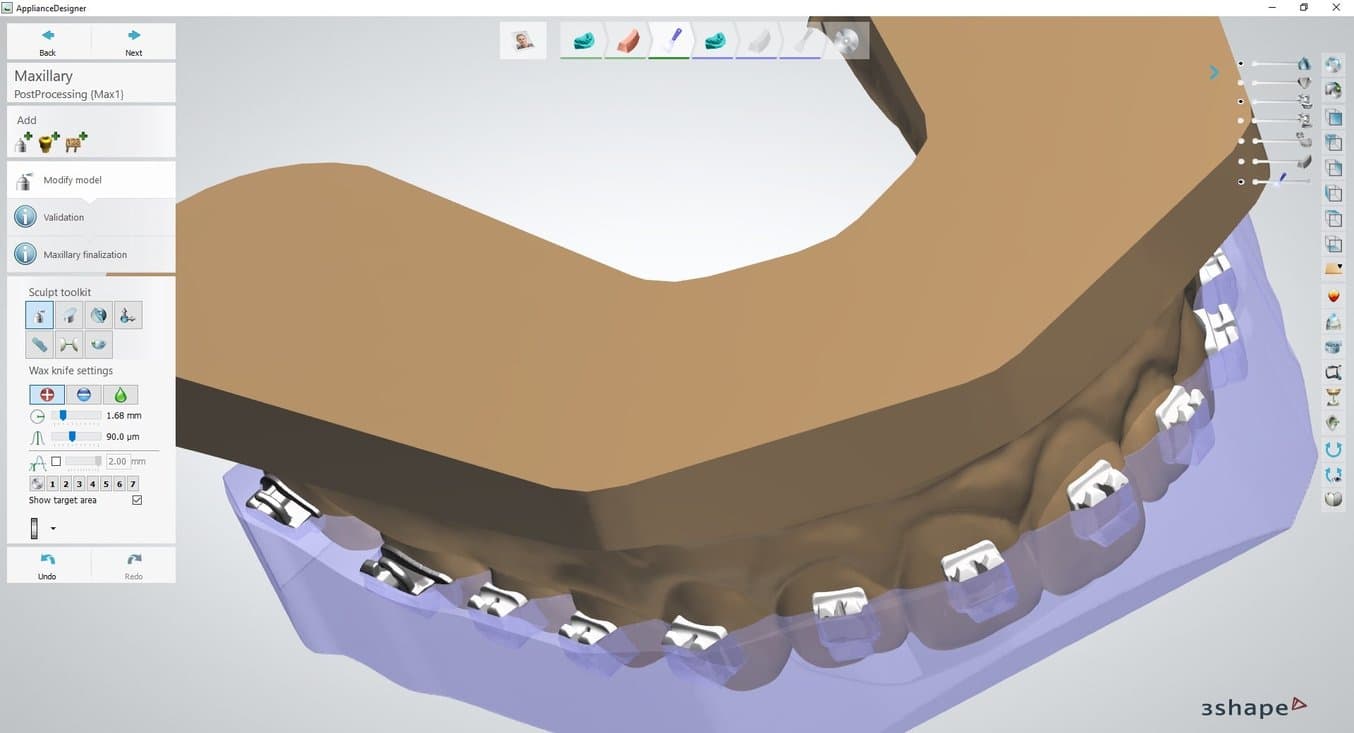
Empfehlungen und Anforderungen für Konstruktion und Versatz der Anwendung
2.1.1 Einsetzrichtung
Achten Sie auf die korrekte Einsetzrichtung. Dies kann den Versatz und die Hinterschneidungen beeinflussen und sich auf die physische Position der endgültigen Anwendung auswirken.

2.1.2 Typ und Konstruktion der dentalen Anwendung
Es gibt typischerweise zwei Möglichkeiten, Transferschienen für die indirekte Klebetechnik einzurichten und zu erstellen:
- Block
- Offset
Mit dem Material IBT Flex Resin bieten wir eine Kompatibilität mit Block- wie auch Offset-Designs.
Block-Designs bieten bei der Verwendung möglicherweise folgende Vorteile:
- Flexibilität im Bereich der Brackets, da die dentale Anwendung in kritischen Bereichen noch dünn ist
- Eine dickere Bodenfläche, die der dentalen Anwendung eine gewisse Steifigkeit verleiht
- Druck direkt auf der Konstruktionsplattform, was Stützstrukturen überflüssig macht
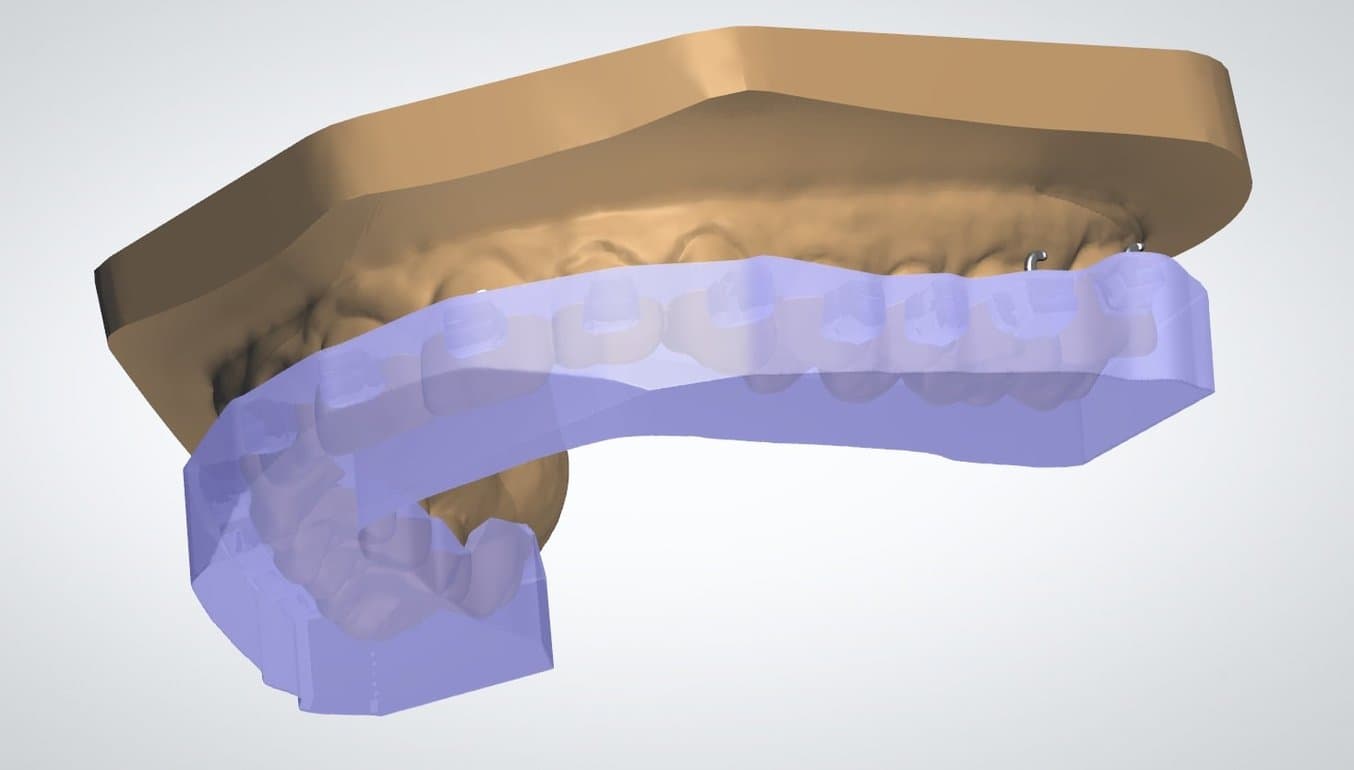
1. Beispiel eines Block-Designs
Hinweis: Block-Designs und Offset-Designs verwenden einen unterschiedlichen CAD-Offset (siehe unten).
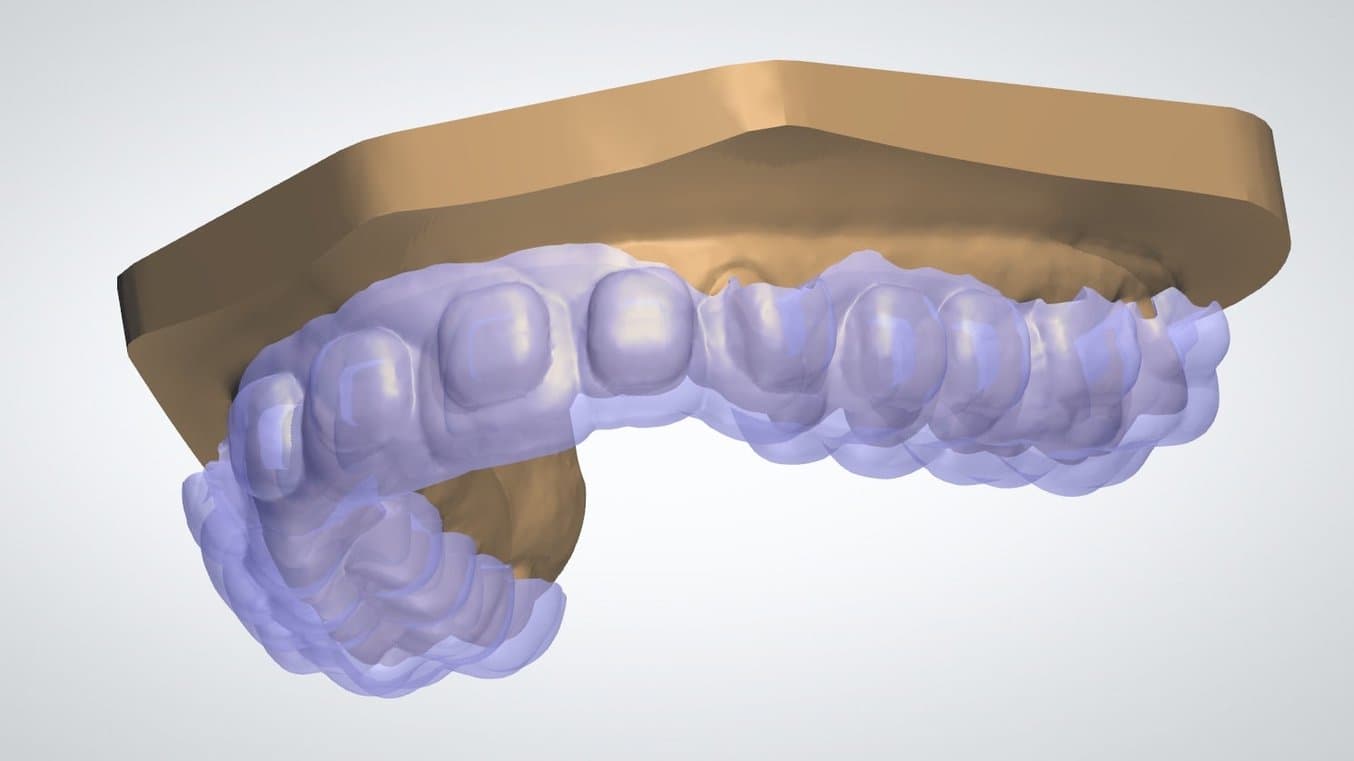
2. Beispiel eines Offset-Designs
2.1.3 Container-Design und -Bedeckung
In unseren Tests haben wir festgestellt, dass sich bei den Aussparungen eine Abdeckung über die Hälfte oder drei Viertel der Brackets am besten für Transferschienen eignet, insbesondere beim Block-Design.
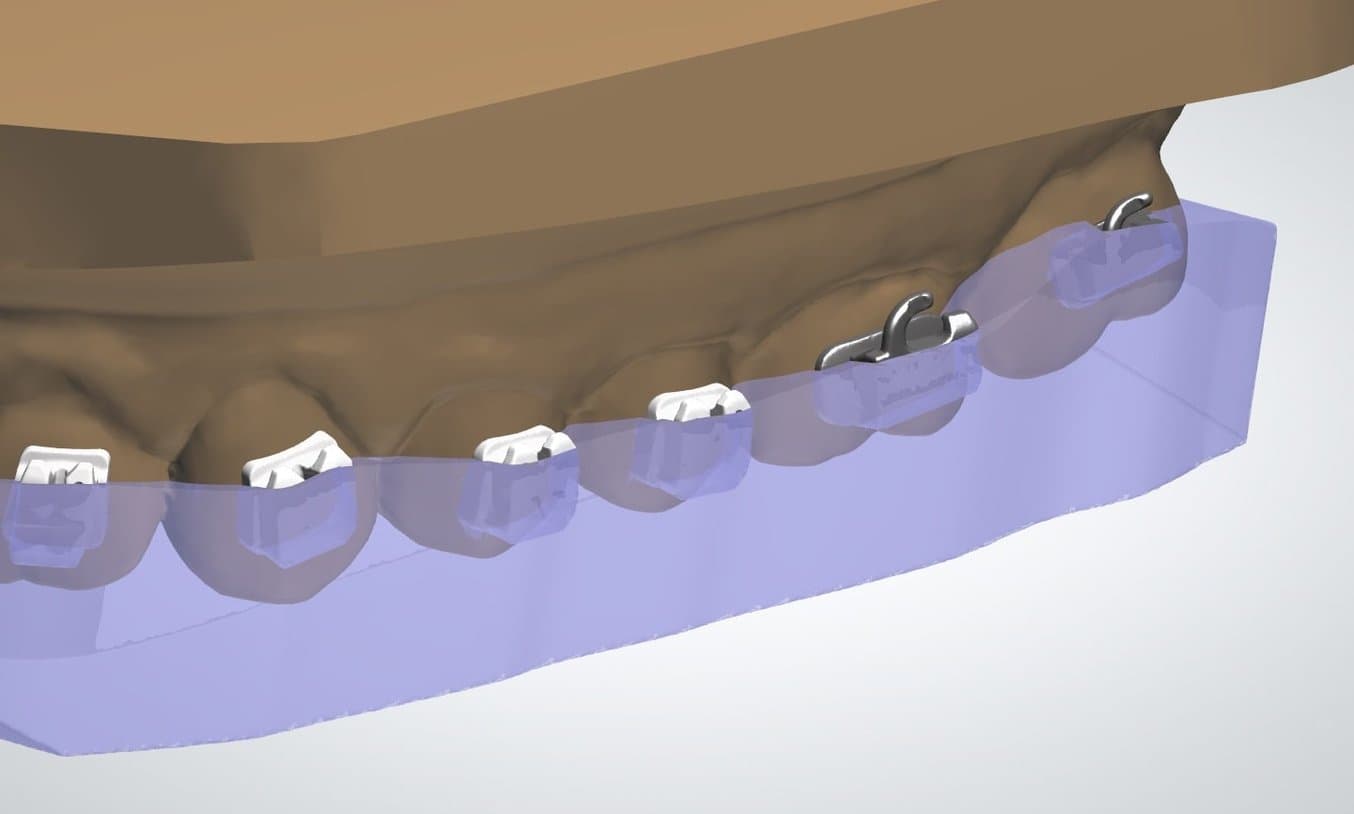
Beispiel für einen Halb- oder Dreiviertelbehälter bzw. -bedeckung
Da Anwendungen vom Typ Offset dünner (und damit flexibler) sind, profitieren bestimmte Brackets von Vollbedeckungsbehältern.
Brackets mit Haken sollten nicht vollständig abgedeckt werden. Die Bracket-Haken können sich beim Ablösen in der dentalen Anwendung verfangen.
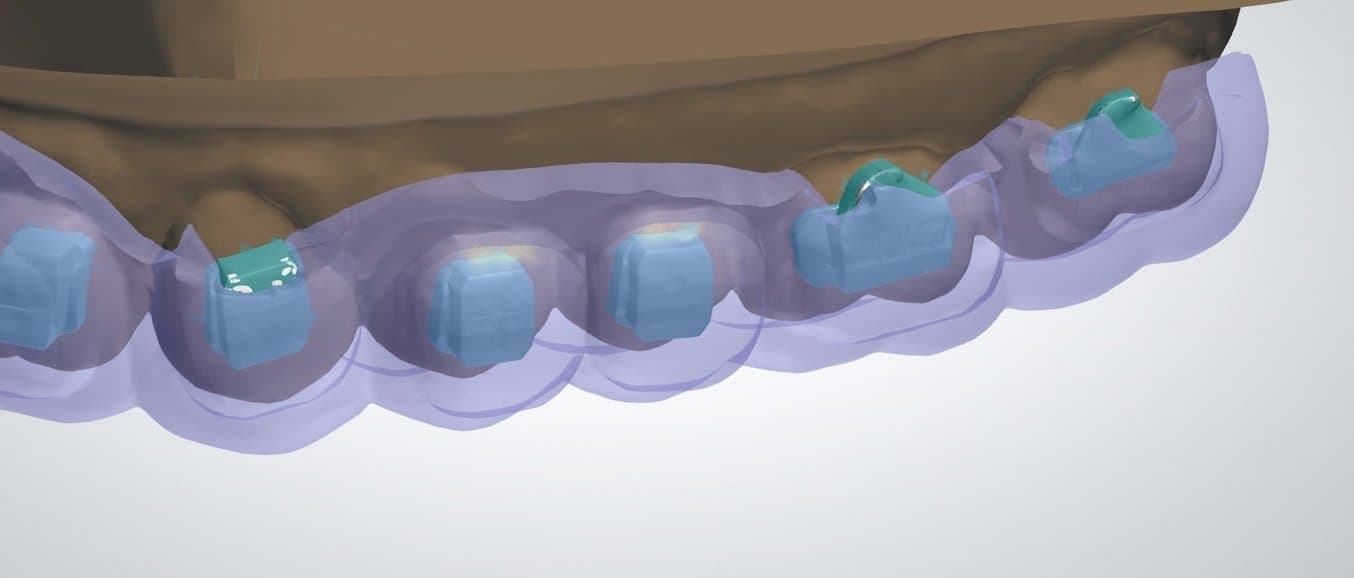
Beispiel für einen Dreiviertel- und Vollbehälter bzw. -bedeckung
Einstellungen und Versatz beim Block-Design
Mindeststärke der dentalen Anwendung: 2,0 mm
2.1.4 Aussparungen
Innenflächenversatz | 0 min |
Blockwinkel | 0° |
Retentionsmaß | 0 min |
Verlängerung | 1 mm |
Bracket-Positionierungskerbe | Überprüft |
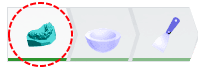
2.1.5 Fertigstellung
Nicht modifizieren | Deaktiviert |
Subtrahiertes Modell | Überprüft |
Versatz für Innenfläche verwenden | Deaktiviert |
Hinterschneidungen entfernen | Deaktiviert |
Extra kombinieren mit Modell | Deaktiviert |
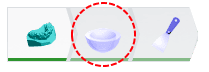
2.1.6 Modell modifizieren
Im letzten Schritt haben Sie die Möglichkeit, das Modell zu modifizieren (siehe 1). Im Arbeitsablauf des Block-Designs ist es wichtig, in diesem Schritt überschüssiges Material zu entfernen.
Hier ist ein Beispiel für ein fertiges Block-Design, das einige Änderungen erfordert.
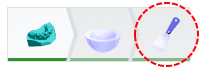
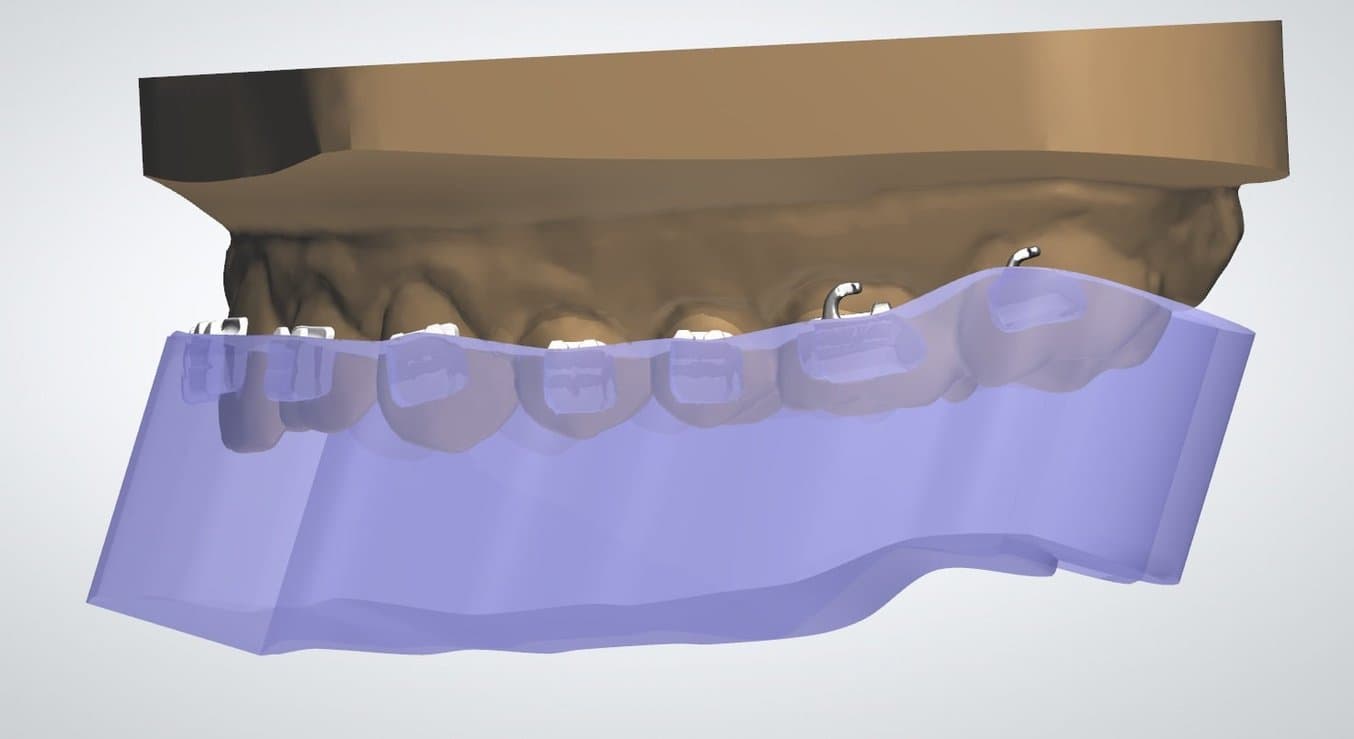
Richten Sie das Modell zunächst so aus, dass die Okklusionsfläche senkrecht zum Betrachtungswinkel steht. Dadurch wird sichergestellt, dass bei ebenen Schnitten eine gleichmäßige Materialmenge von der Unterseite der dentalen Anwendung bis zur Intagliofläche verbleibt.
Klicken Sie auf das Ebenenschnitt-Werkzeug (siehe 2) und ziehen Sie den Mauszeiger, um überschüssige Geometrie abzuschneiden.
Sie können den Abstand zum Anatomiemodell überprüfen und bearbeiten, indem Sie den Versatzwert (siehe 3) prüfen oder ändern.
Hinweis: Die minimale Materialstärke beträgt 1,0 mm.
Achten Sie nach dem Zeichnen der Schnittebene darauf, dass der grüne Pfeil in Richtung der Seite zeigt, die abgeschnitten werden soll. Klicken Sie auf Schnittrichtung wechseln, um die zu entfernende Seite zu wechseln (siehe 4).
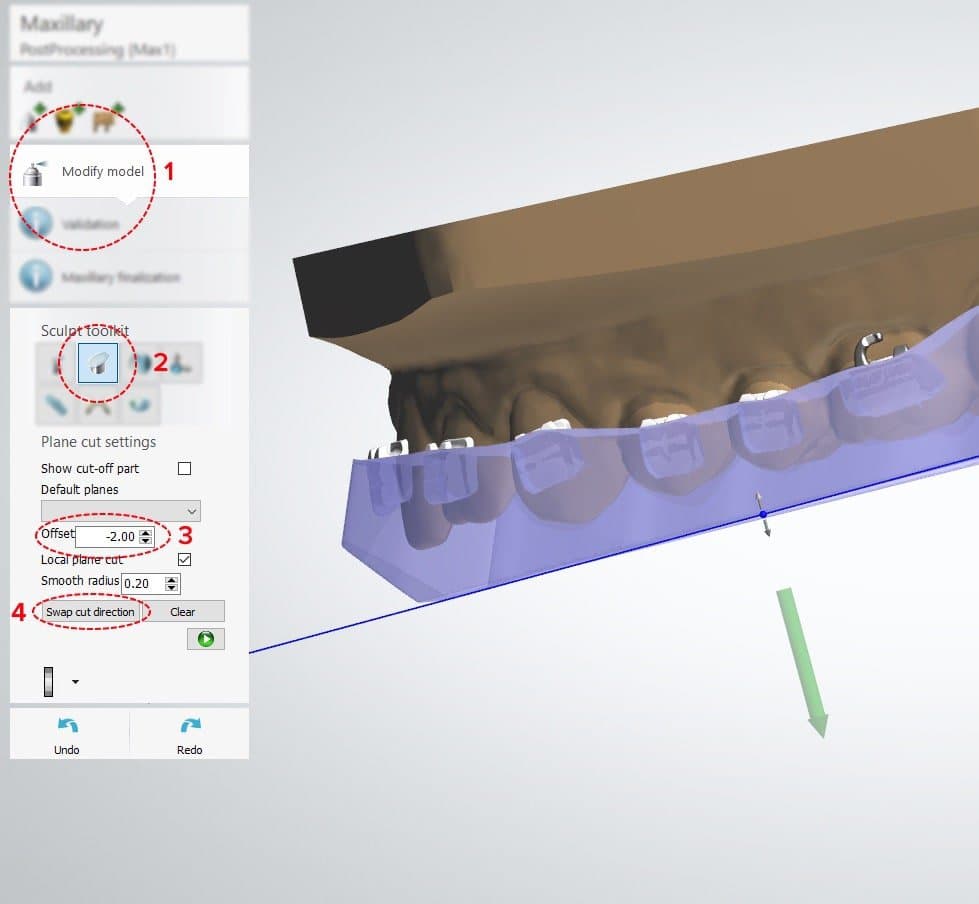
Ebenenschnitt 1 ist optional, bietet aber einen Hebelpunkt am Druckteil.
Ebenenschnitt 2 wird parallel zur Okklusalebene gezeichnet und erzeugt eine ebene Fläche, um das Teil effizient zu drucken.
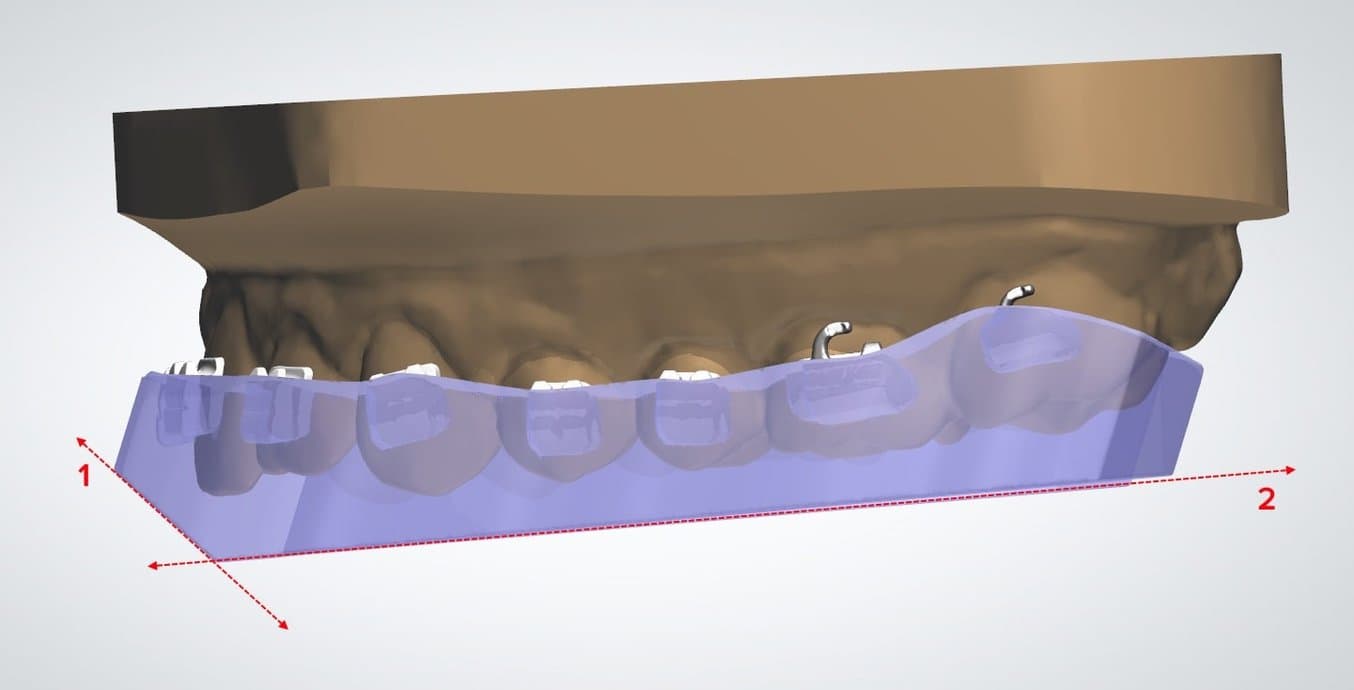
Designeinstellungen und Versatz
2.1.7 Einstellungen
Stärke | 2 mm |
Hinterschneidungen entfernen | Deaktiviert |
Versatz für Innenfläche verwenden | Deaktiviert |
Kanten glätten | Keine |
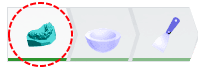
2.1.8 Aussparungen
Innenflächenversatz | 0 min |
Blockwinkel | 0° |
Retentionsmaß | 0 min |
Verlängerung | 1 mm |
Bracket-Positionierungskerbe | Überprüft |
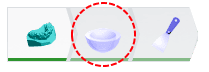
2.2 Export der STL-Datei
Sobald das Design spezifikationsgemäß abgeschlossen ist, kann die Fertigung beginnen. Die meisten zahnmedizinischen Designprogramme erstellen die Fertigungsdateien im STL-Format. Ziehen Sie die Datei in die Druckvorbereitungssoftware PreForm.
3. Druck
Anmerkung
Verwenden Sie Version 3.23 oder höher von PreForm und die Firmware-Version 2.2.0 oder höher.
3.1 Import der Datei(en)
Importieren oder öffnen Sie die Designdatei(en), indem Sie sie in das PreForm-Fenster ziehen. Oder wählen Sie die Datei(en) über das Menü File (Datei) auf Ihrem Computer oder in Ihrem Netzwerk aus.
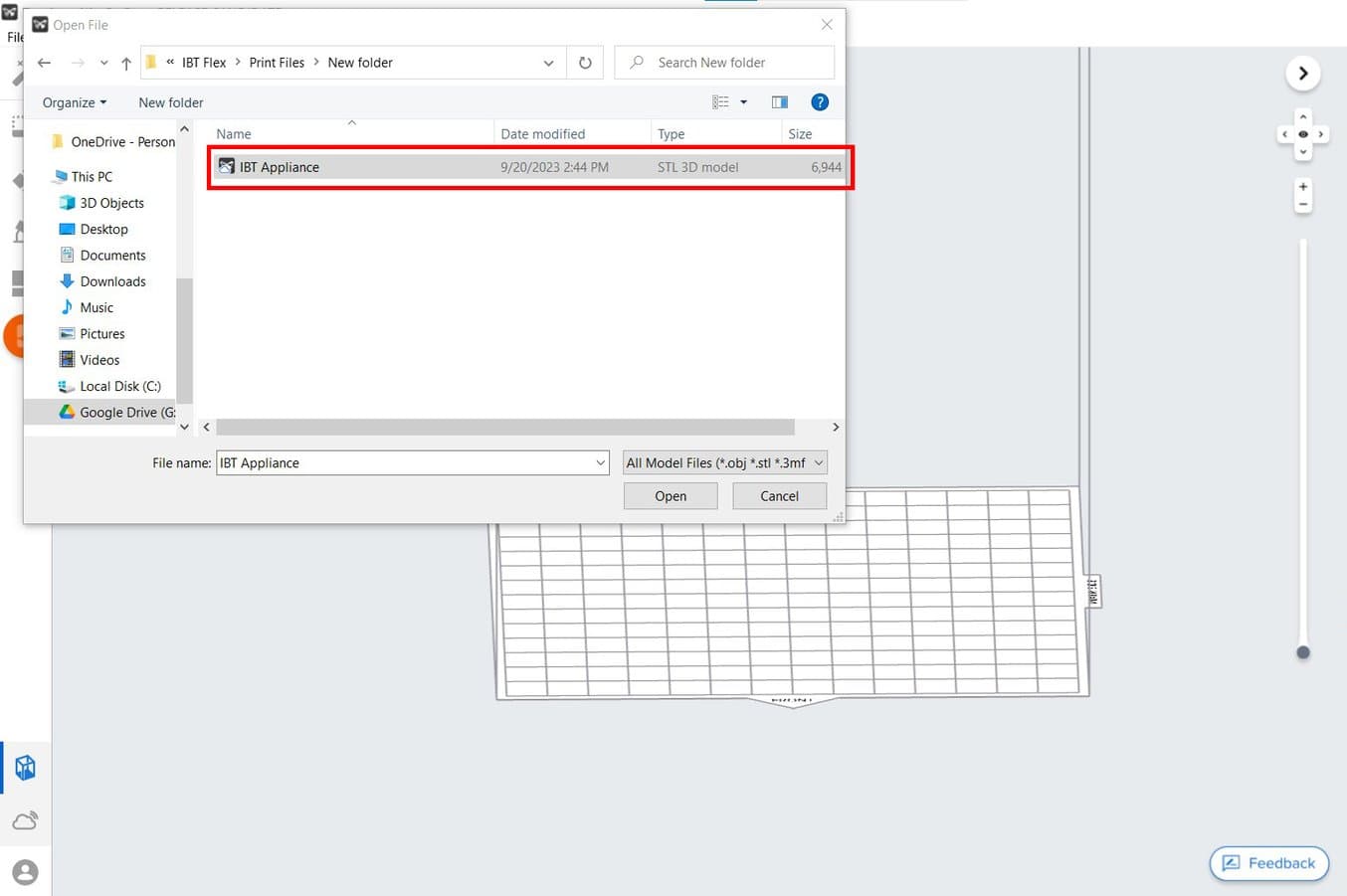
3.2 Auswahl von Material und Schichthöhe
Wählen Sie das zu druckende Material rechts in der Leiste Job Setup (Druckeinrichtung) aus.
Wählen Sie IBT Flex aus der Materialauswahl aus.
IBT Flex Resin kann mit Standard-Druckeinstellungen und 100 Mikrometern Schichthöhe gedruckt werden. Wenn Sie IBT Flex Resin für restaurative Zwecke verwenden, kann es auch mit 50 Mikrometern Schichthöhe gedruckt werden. Der Druck von Transferschienen bei einer Schichthöhe von 50 Mikrometern kann die Druckzeit verlängern.
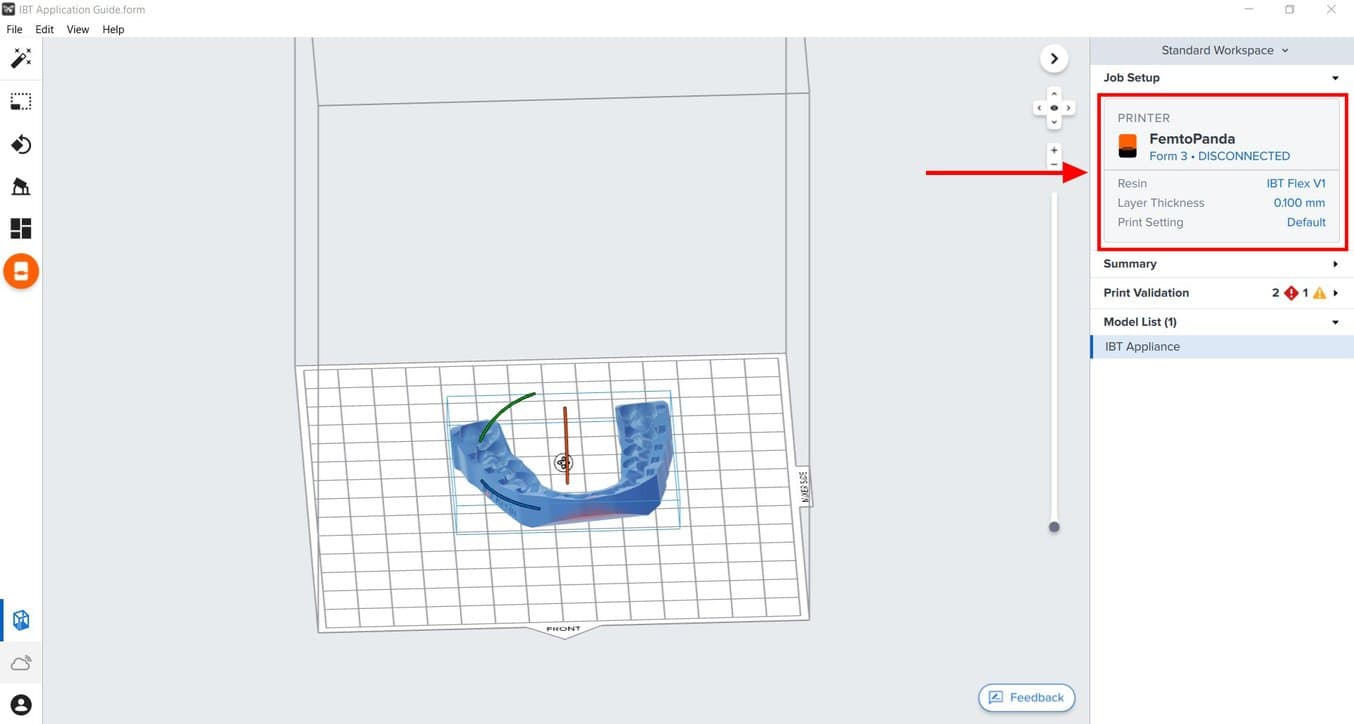
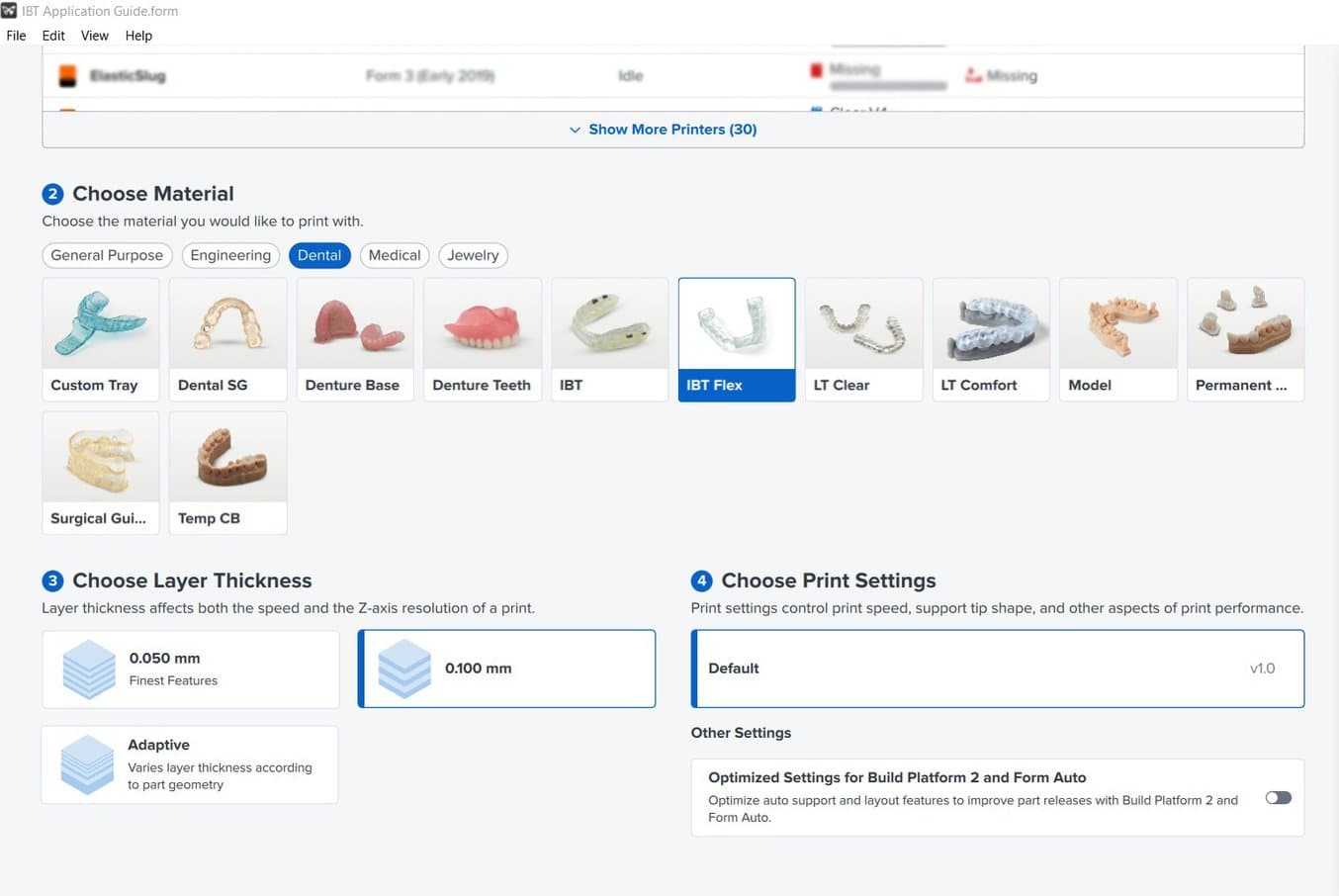
3.3 Ausrichtung
3.3.1 Positionierung dentaler Anwendungen des Typs Block
Wenn Sie die Transferschiene mit der Block-Technik konstruiert haben, können Sie die Bodenfläche direkt auf der Konstruktionsplattform positionieren.
Öffnen Sie das Ausrichtungswerkzeug (siehe 1) und klicken Sie auf die Schaltfläche Select Base... (Basis auswählen...) (siehe 2).
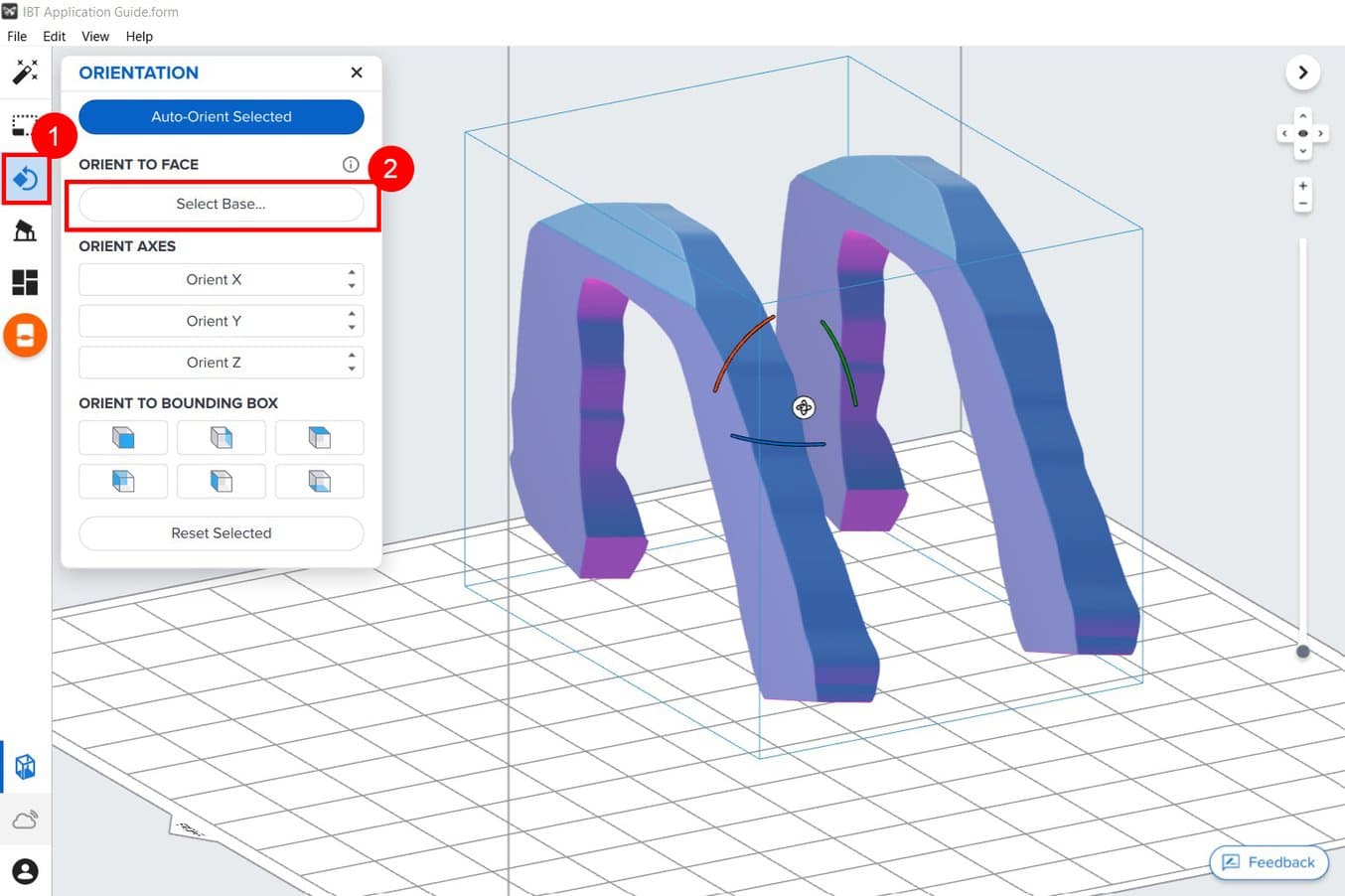
Klicken Sie anschließend auf die Unterseite des Teils, um sie auf der Konstruktionsplattform zu positionieren.
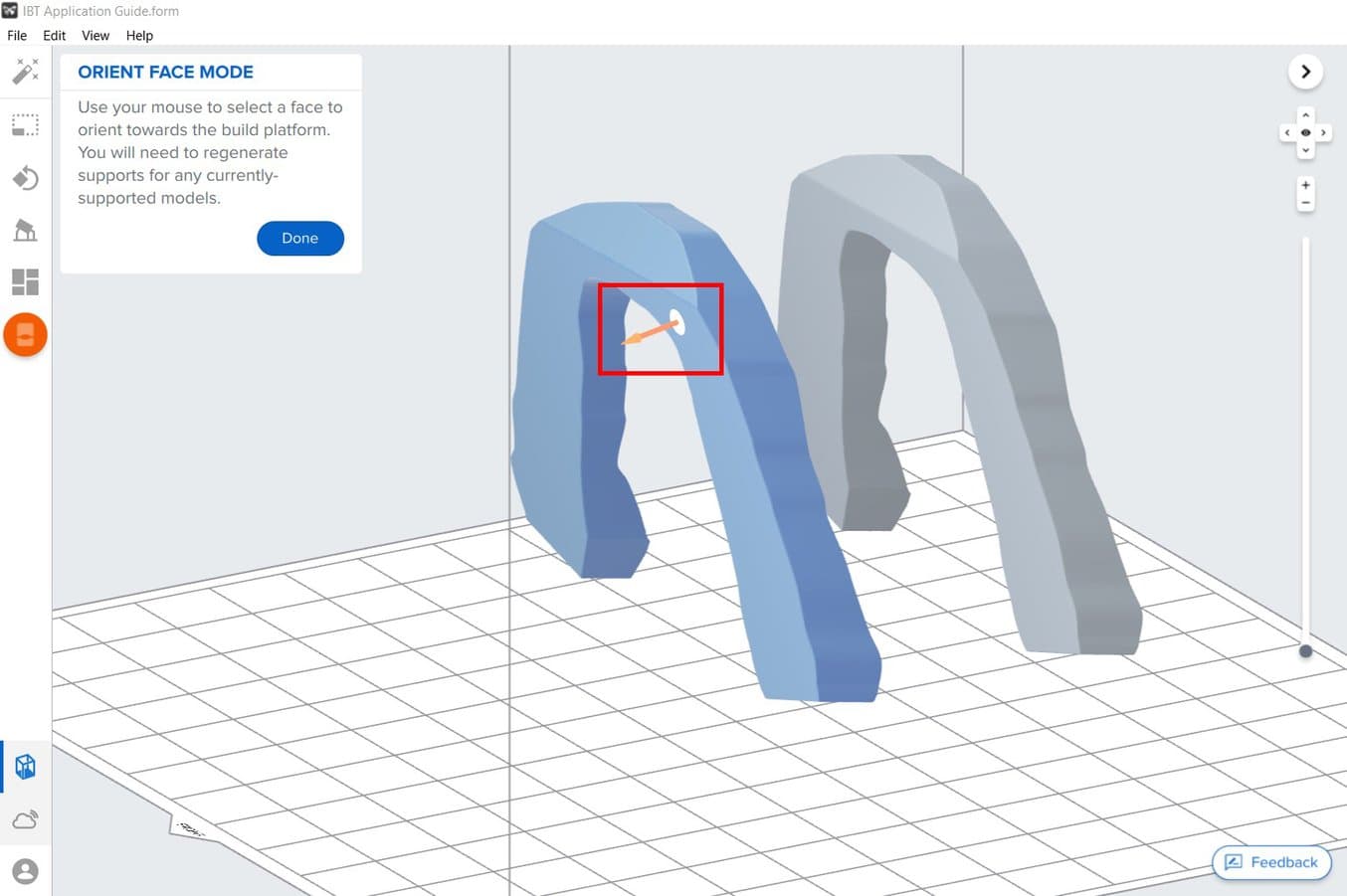
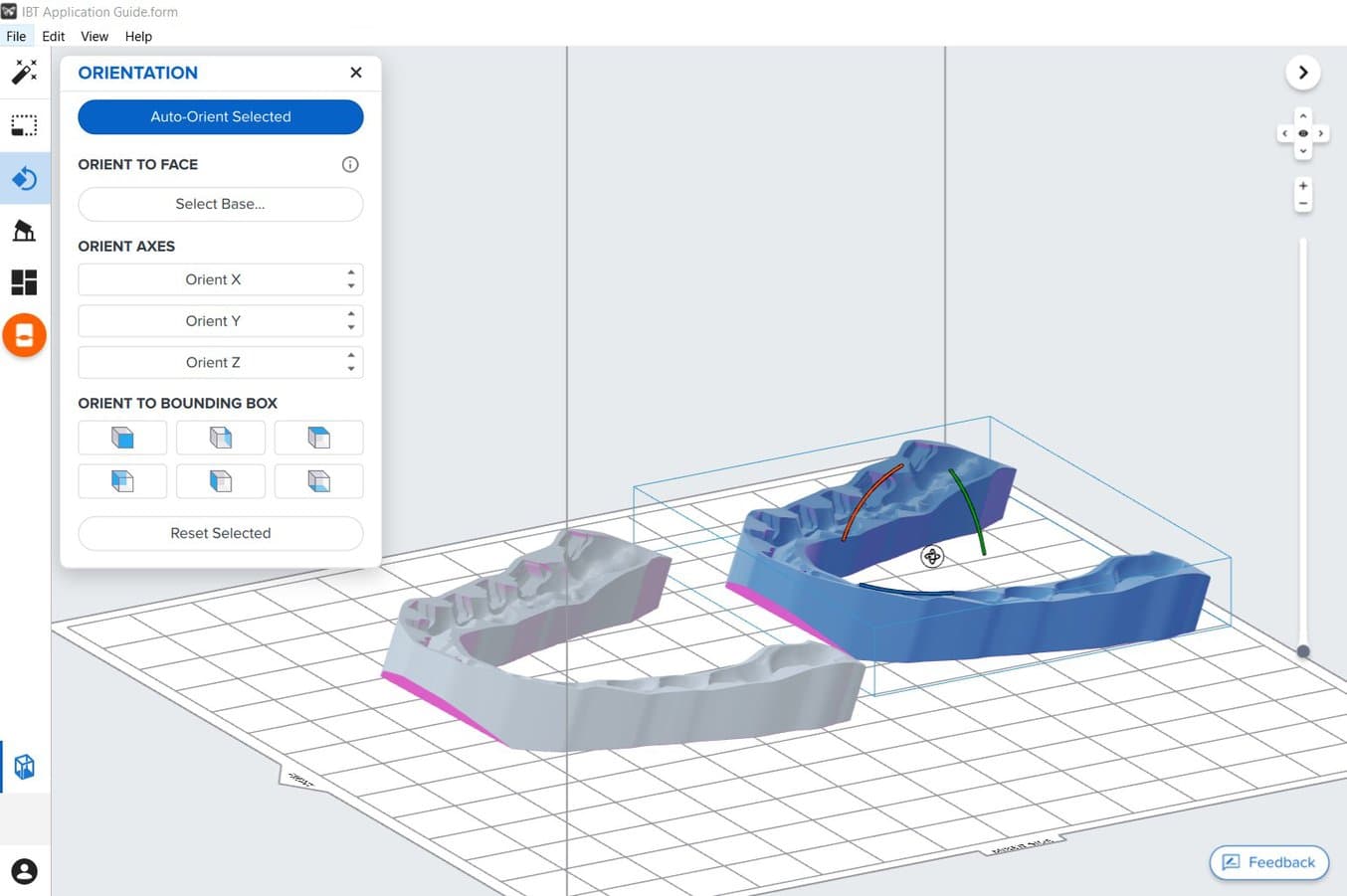
3.3.2 Positionierung dentaler Anwendungen des Typs Offset
Um ein Teil in die richtige Position zu drehen, wählen Sie das Teil aus und drehen Sie es mit der Manipulationskugel.
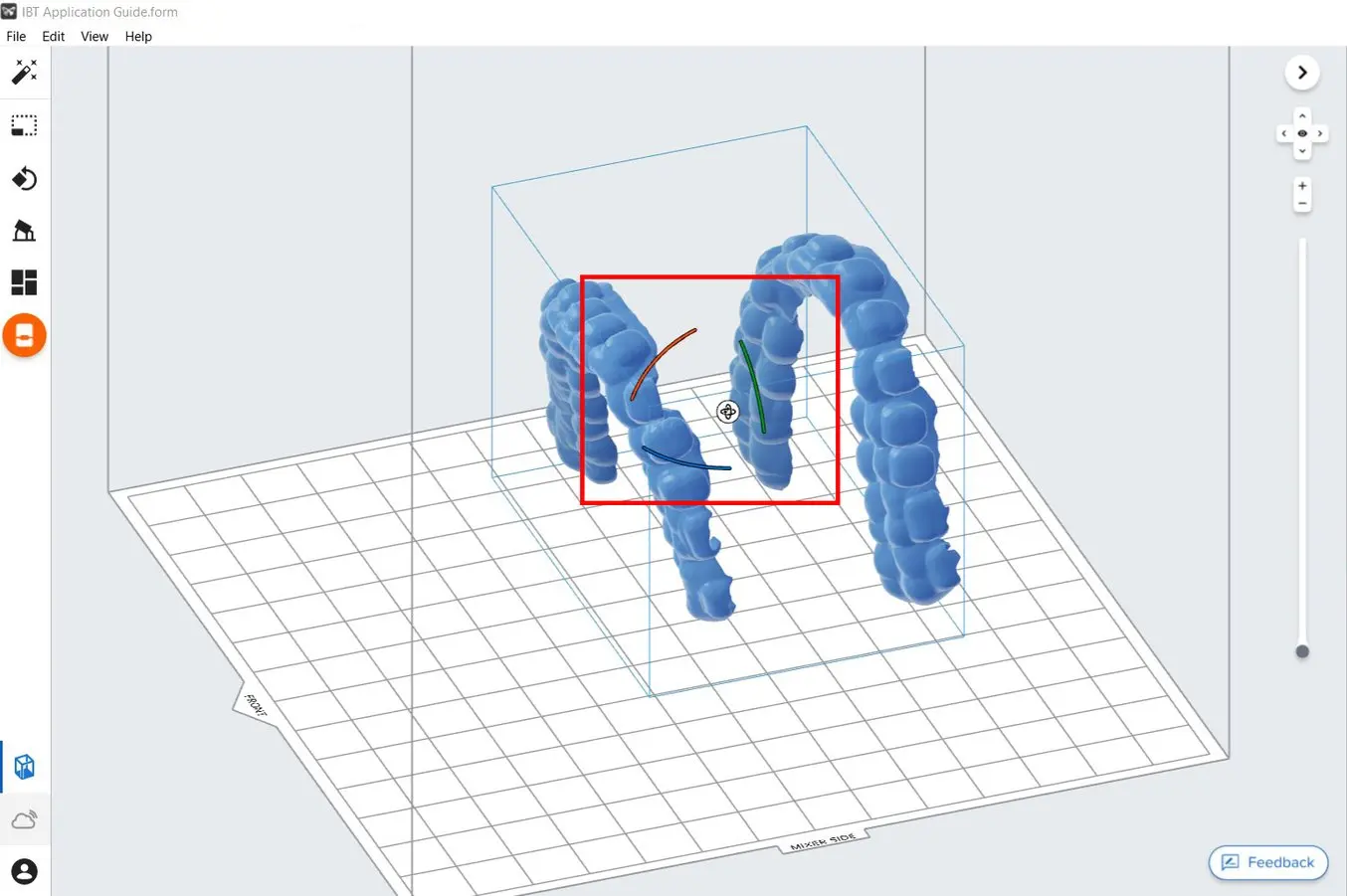
Eine weitere Möglichkeit besteht darin, das Ausrichtungswerkzeug (siehe 1) zu öffnen und mit dem Mauszeiger über die Oberflächensymbole unter Orient To Bounding Box (An Begrenzungsrahmen ausrichten) zu gehen (siehe 2), um die Boden- oder Okklusionsfläche des Teils zu finden.
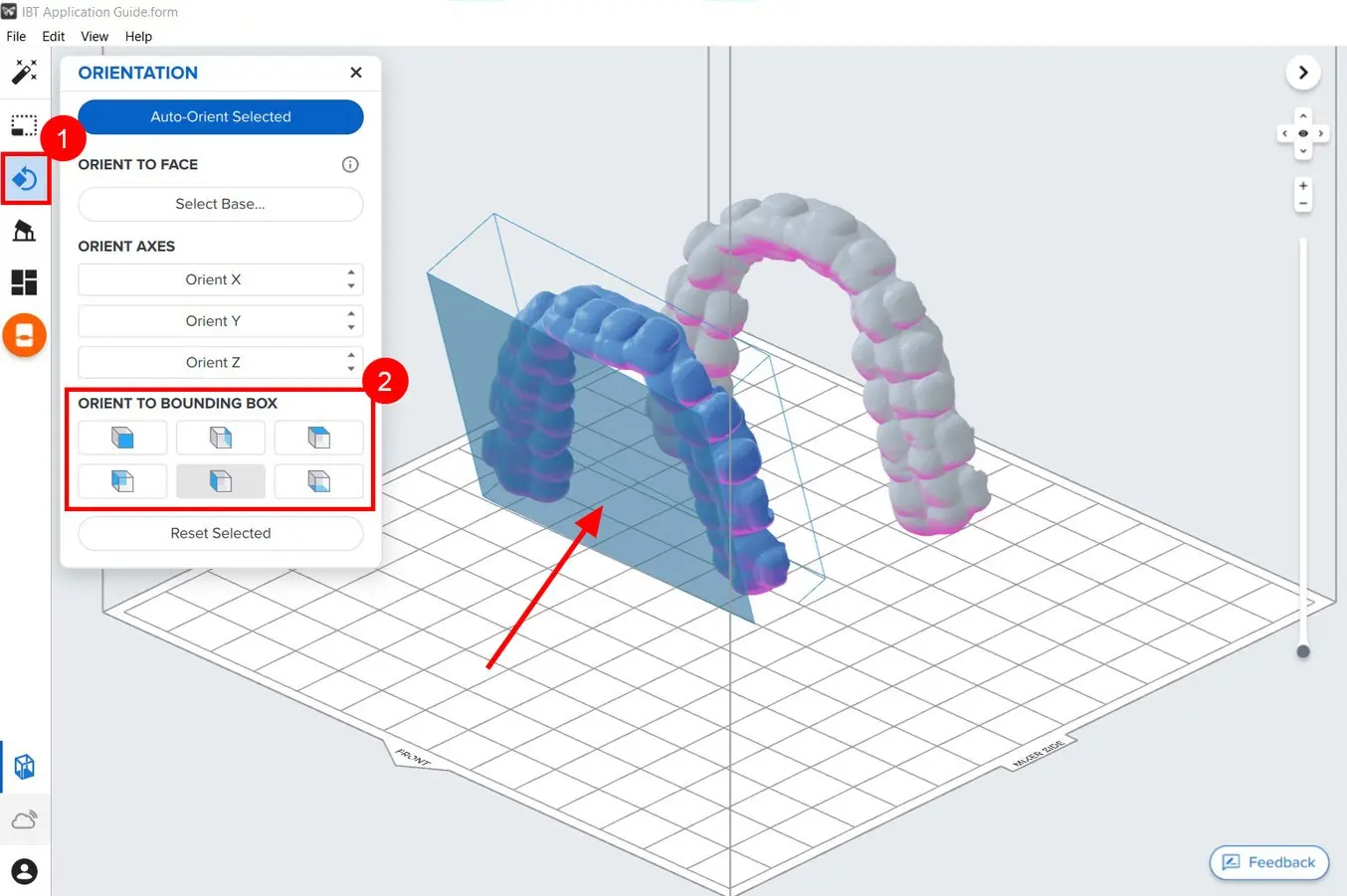
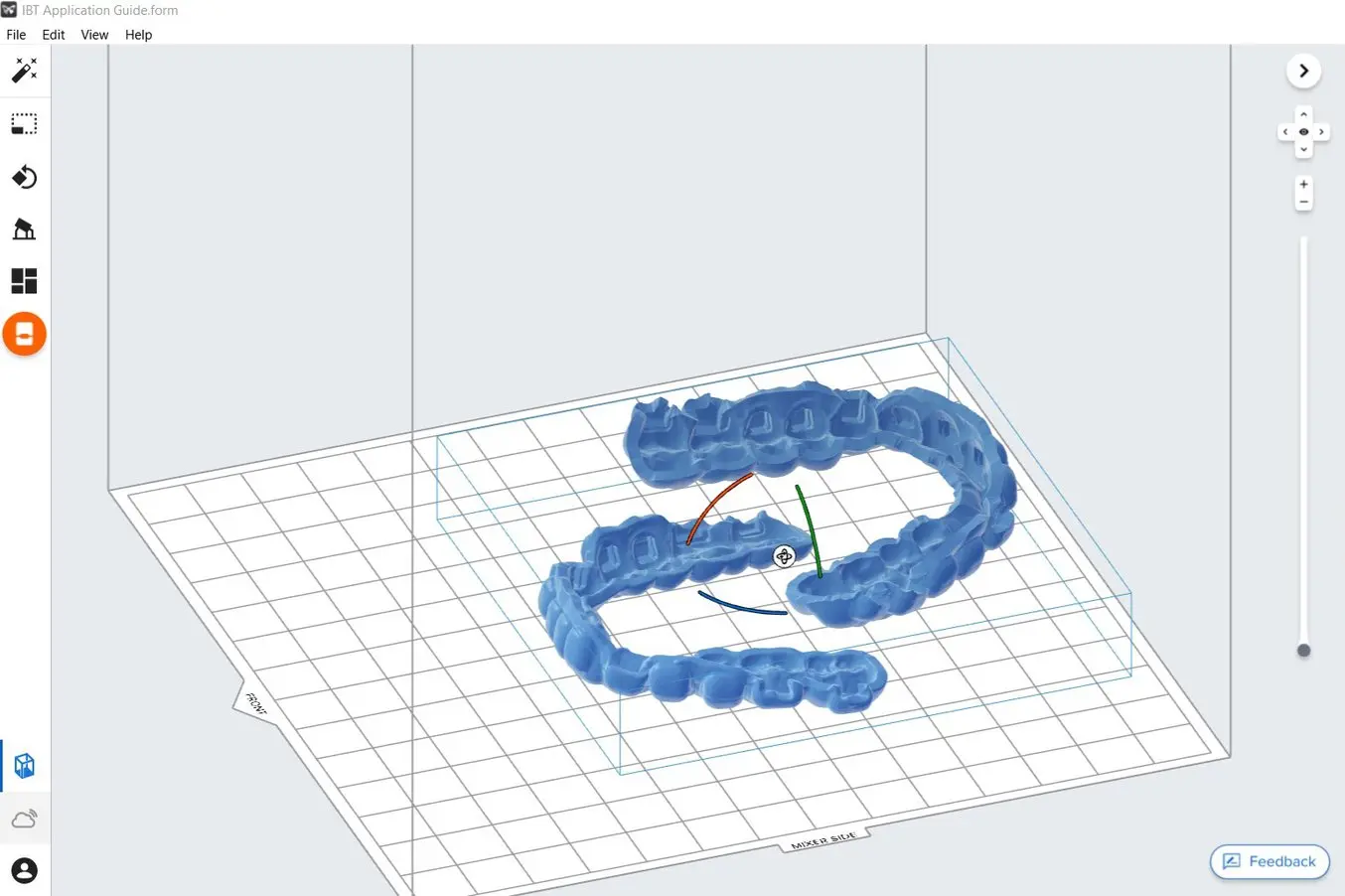
3.3.3 Winkel
Die richtige Modellausrichtung stellt die Teilegenauigkeit und Passung sicher.
Richten Sie die dentale Anwendung immer so aus, dass die Intagliofläche von der Konstruktionsplattform abgewandt ist. Das Teil sollte parallel zur Konstruktionsplattform oder in einem Winkel von höchstens 40 Grad ausgerichtet sein, wobei der anteriore Bereich zur Konstruktionsplattform zeigt.
Hinweis: Die Druckzeiten variieren je nach Objektausrichtung und Druckeinrichtung.
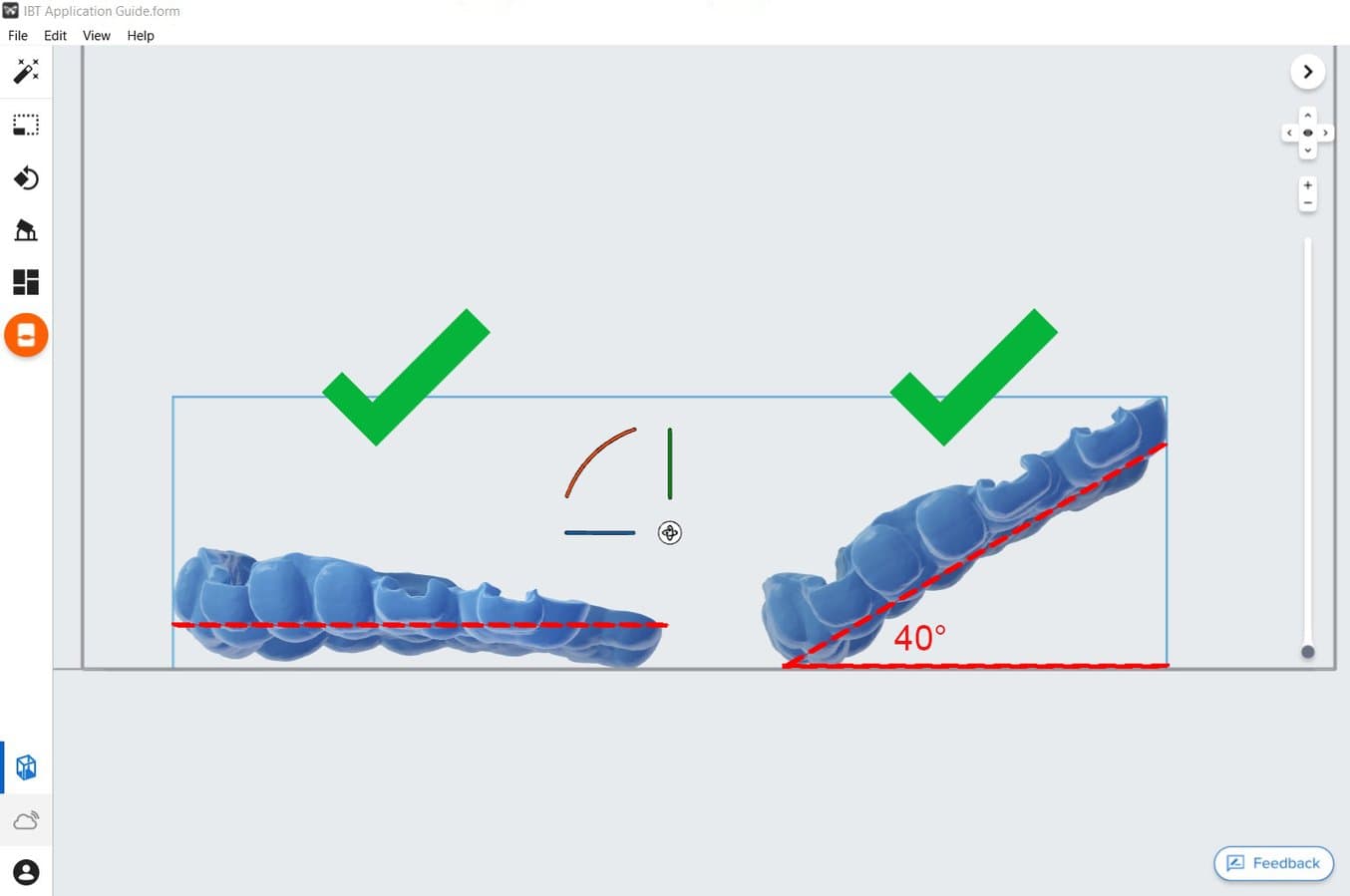
3.4 Stützstrukturen generieren
Abhängig von den überhängenden Flächen können Transferschienen des Typs Block, die direkt auf der Konstruktionsplattform positioniert sind, ganz ohne Stützstrukturen gedruckt werden.
3.4.1 Automatische Stützstrukturerstellung
Falls Stützstrukturen notwendig sind, öffnen Sie in der linksseitigen Navigation in PreForm das Stützstrukturenwerkzeug und klicken Sie anschließend auf die Schaltfläche Auto Generate Selected (Auswahl automatisch generieren) oder Auto Generate All (Alle automatisch generieren).
Falls Sie Stützstrukturen zu einem Block-Design hinzufügen, das direkt auf der Konstruktionsplattform gedruckt werden sollte, ändern Sie den Raft-Typ im Stützstrukturenwerkzeug auf None (Kein Raft).
Hinweis: Deaktivieren Sie das Kontrollkästchen Internal Supports (Interne Stützstrukturen), um die Erstellung unnötiger Stützstrukturen zu vermeiden.
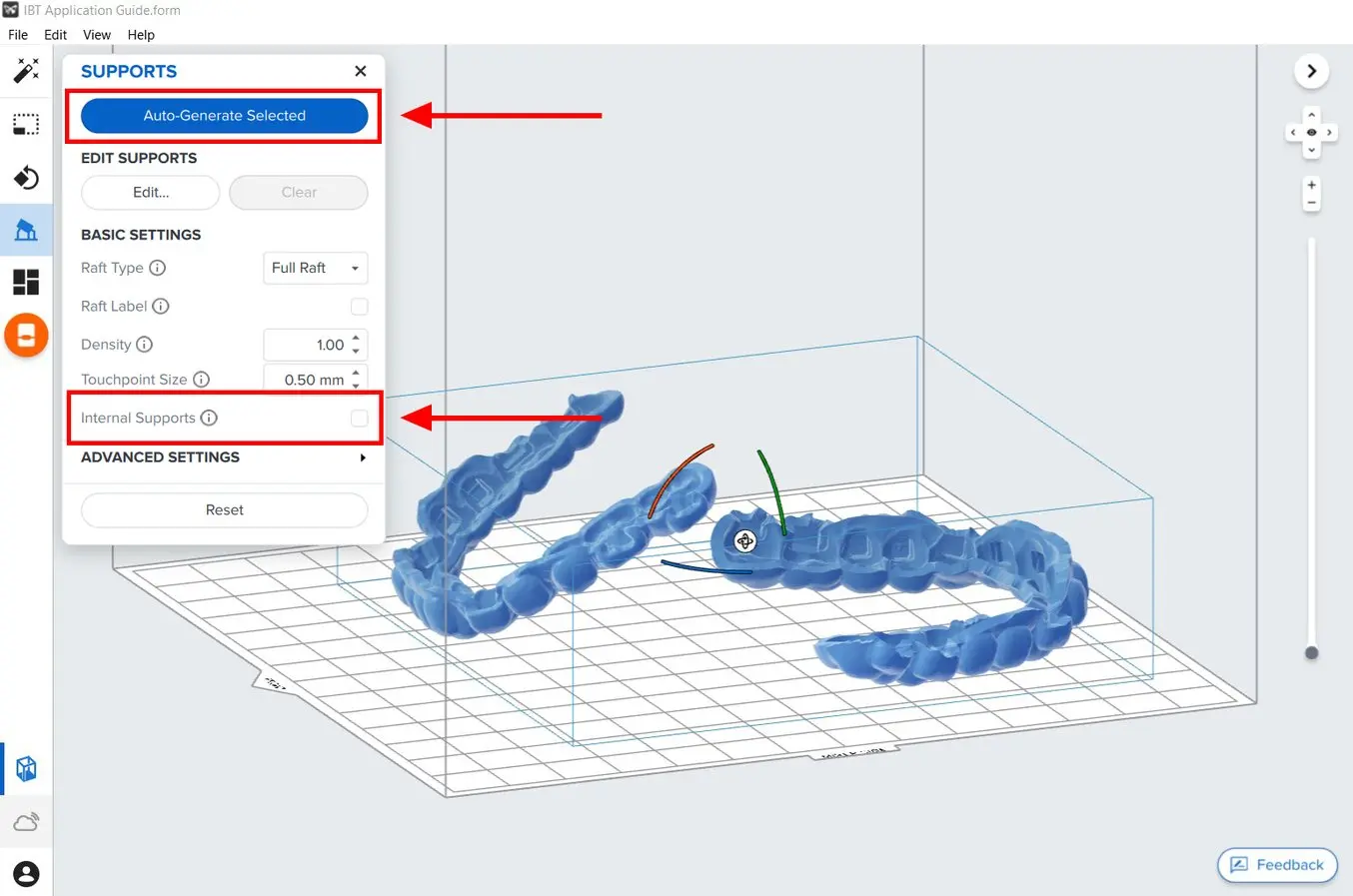
3.4.2 Manuelle Bearbeitung der Stützstrukturen
Sobald die Stützstrukturen erzeugt sind, überprüfen Sie deren Position. Falls sich eine Stütze nicht am besten Ort befindet, kann sie umpositioniert werden, indem Sie die Schaltfläche Edit... (Bearbeiten...) im Stützstrukturmenü anklicken.
Hinweis: Sind interne Stützstrukturen deaktiviert und das Modell korrekt ausgerichtet, ist eine Bearbeitung der Stützstrukturen normalerweise nicht erforderlich.
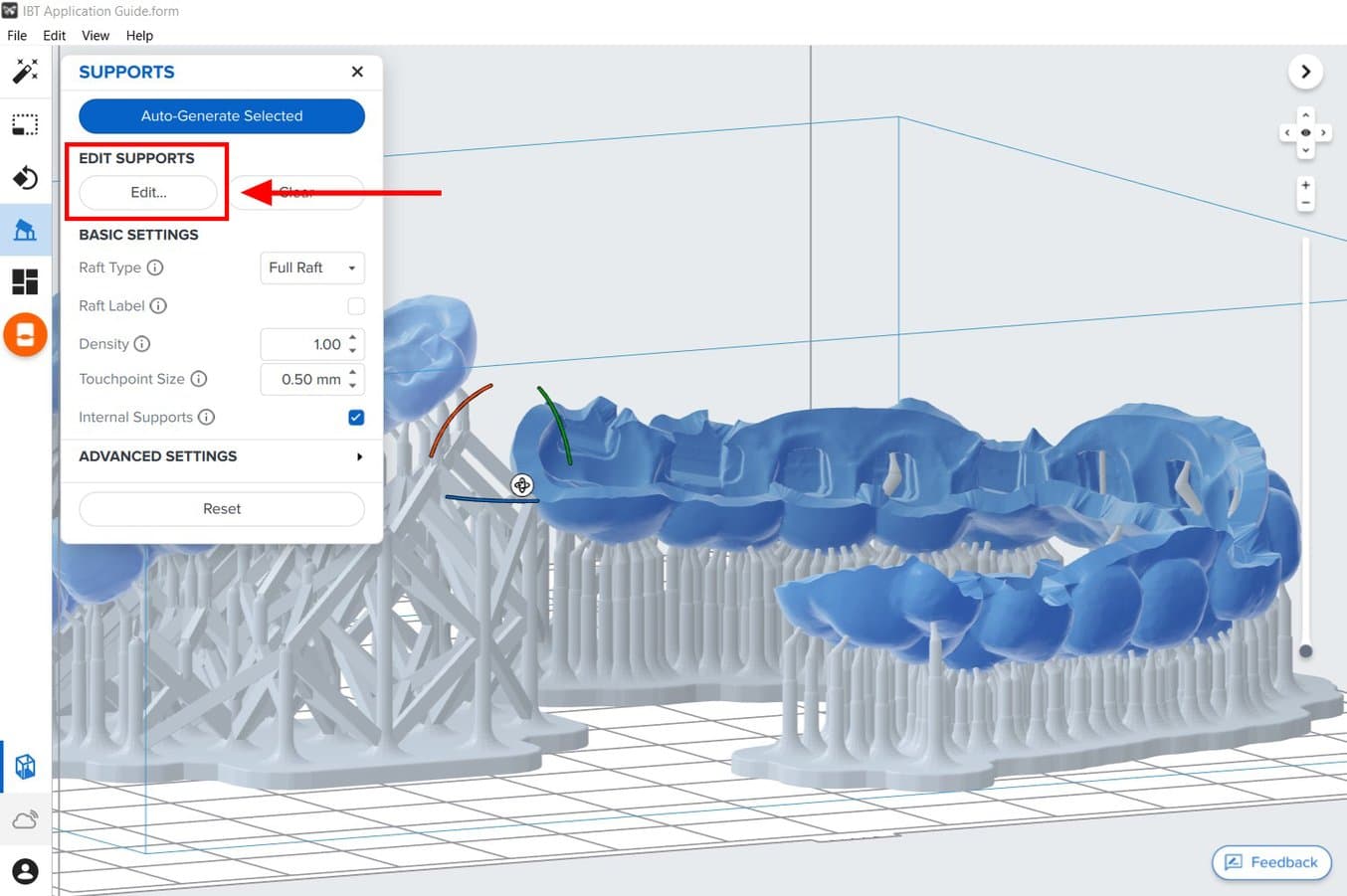
Klicken Sie auf eine Stützberührungspunktkugel, um die Stütze zu entfernen. Klicken Sie auf Bereiche ohne Stützstrukturen, um Berührungspunkte hinzuzufügen.
PreForm färbt Stellen rot ein, die eventuell mehr Stützstrukturen benötigen.
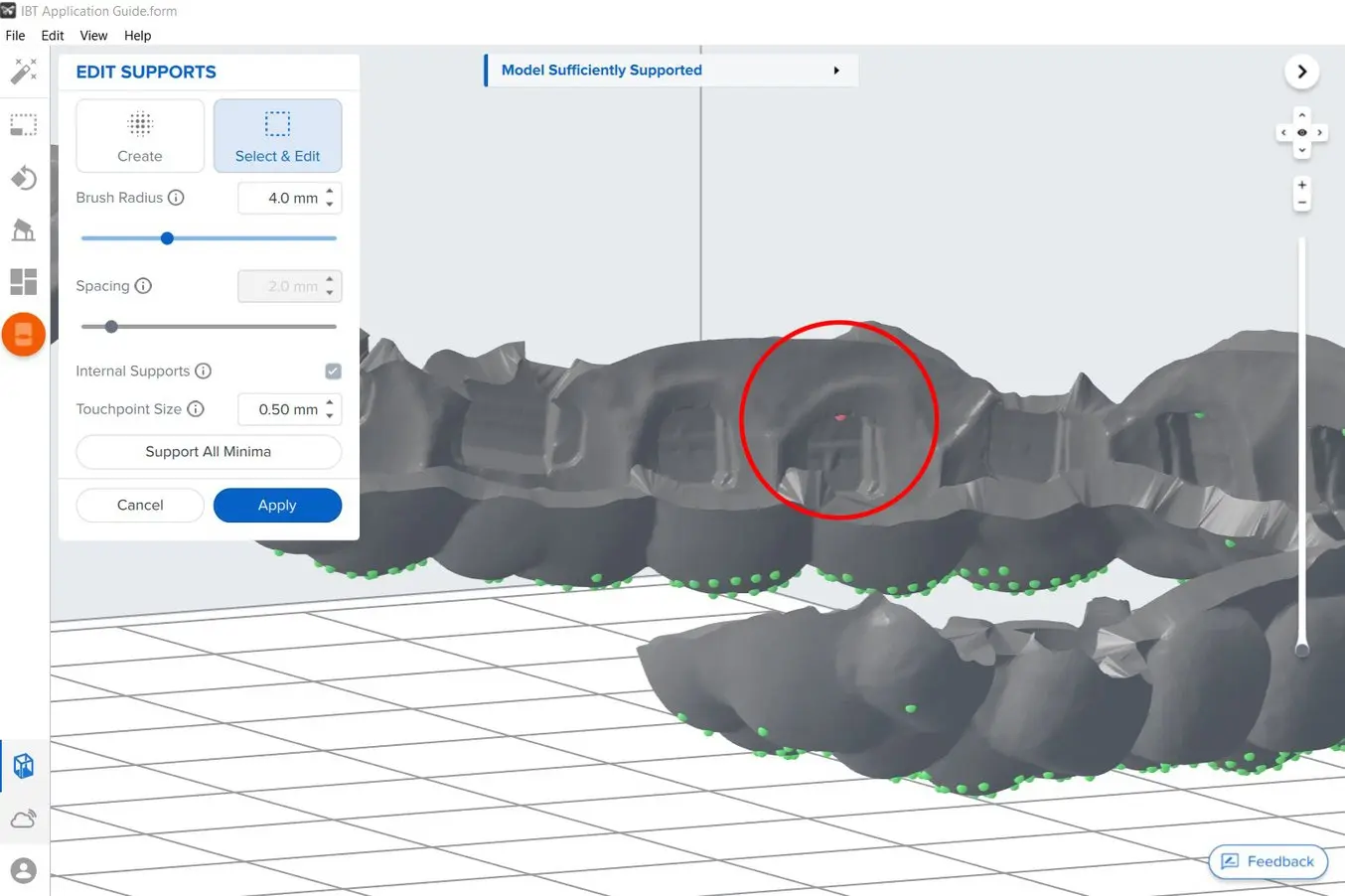
Gehen Sie sicher, dass rechts in der Menüleiste Job Setup (Druckeinrichtung) bei Print Validation (Druckvalidierung) ein grüner Daumen angezeigt ist.
Wenn Sie Teile direkt auf der Konstruktionsplattform drucken, wird eine Druckbarkeitswarnung angezeigt. Wenn das Teil – wie im obigen Abschnitt beschrieben – auf der Konstruktionsplattform eingerastet ist, können Sie diesen Fehler ignorieren.
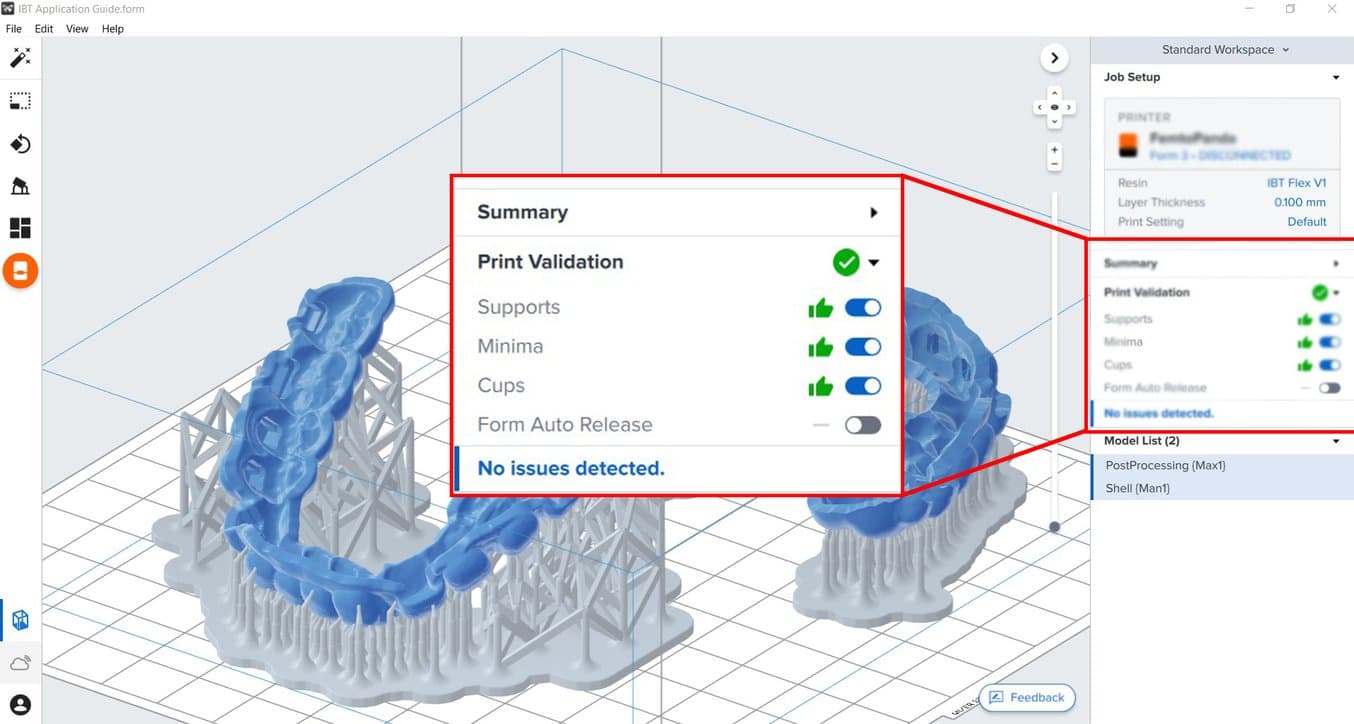
3.5 Drucklayout
Unabhängig davon, ob Sie mit Stützstrukturen oder direkt auf der Konstruktionsplattform drucken, positionieren Sie die Teile so, dass sie sich nicht gegenseitig überlappen. Einander überlappende Teile werden rot hervorgehoben.
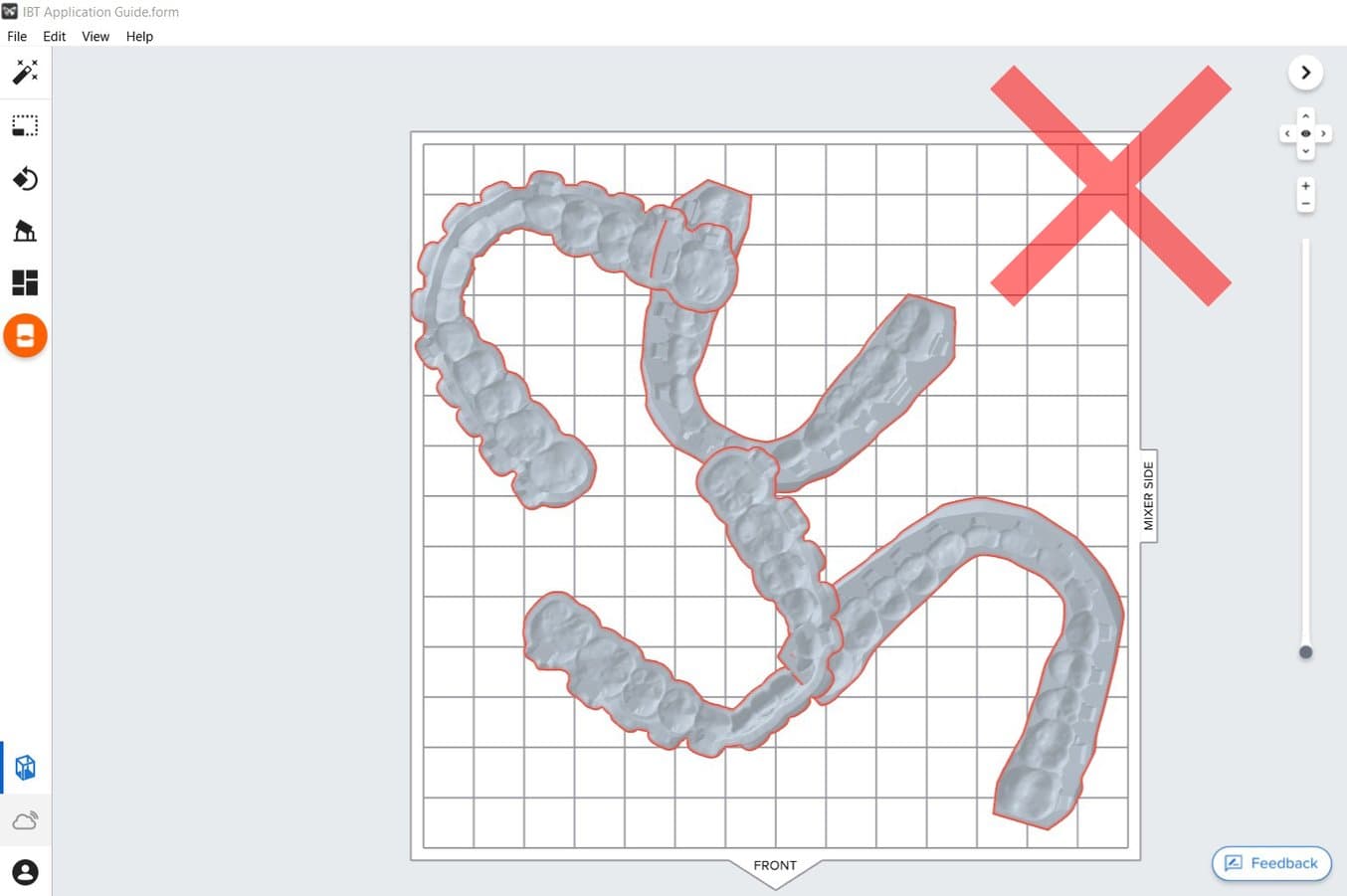
Um das ausgewählte Teil zu drehen, klicken und ziehen Sie den äußeren Rand der Ausrichtungskugel.
Um das Teil zu verschieben, klicken und ziehen Sie an einer beliebigen Stelle des Teils.
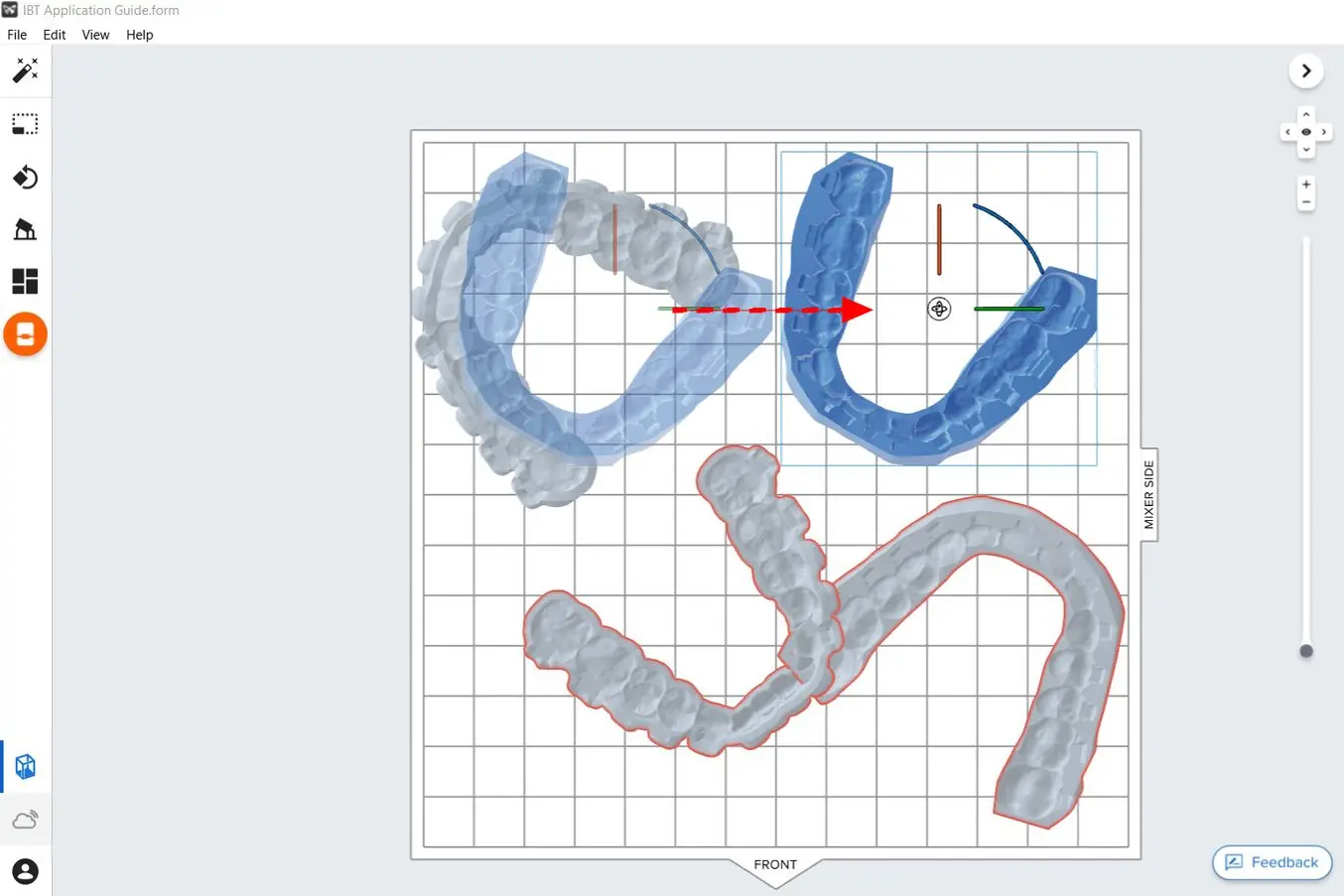
Eine andere Option ist das automatische Layout-Tool. Wählen Sie alle auf der Konstruktionsplattform befindlichen Teile aus und klicken Sie auf Layout All (Alle positionieren).
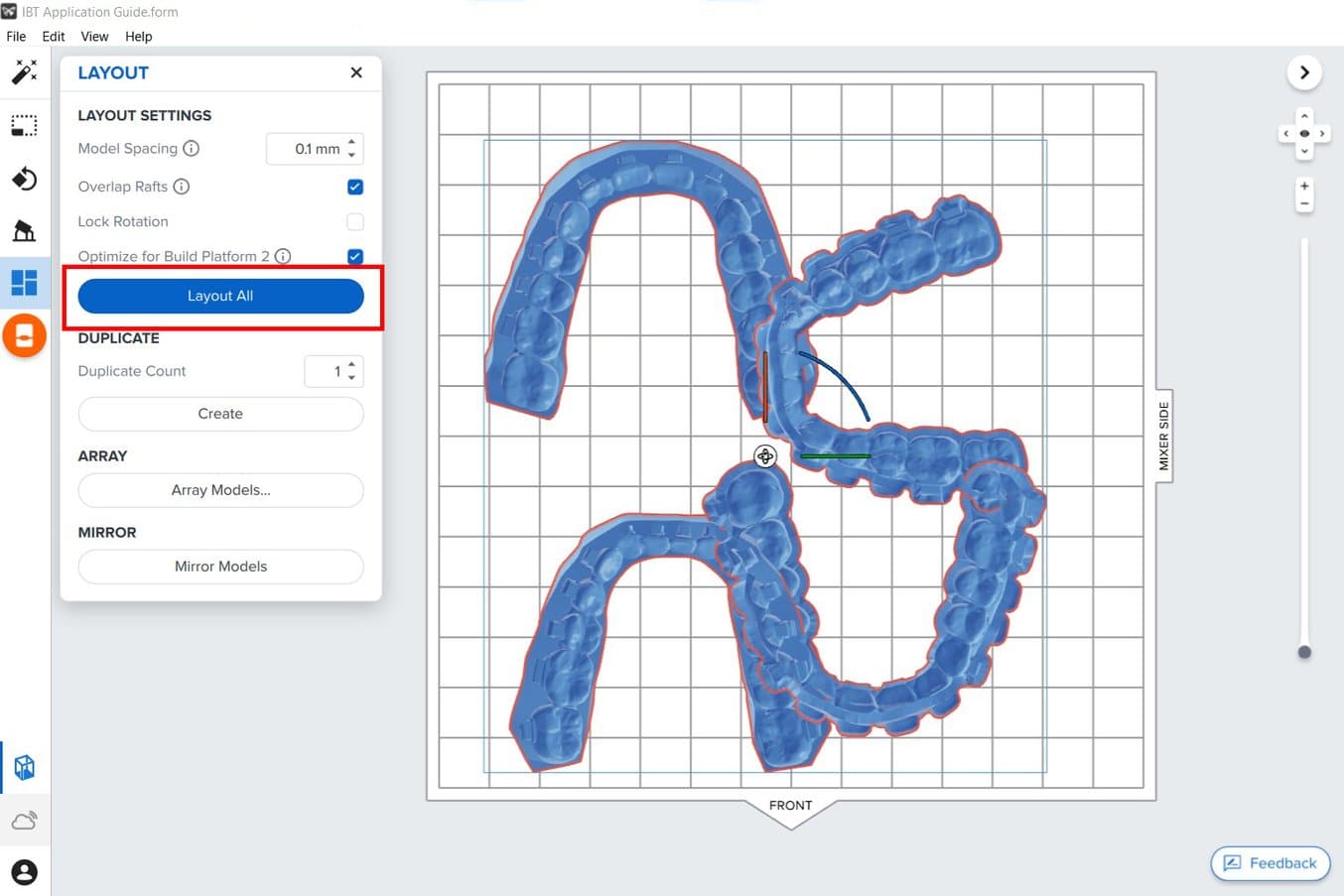
Anmerkung: Ein Überlappen der Rafts ist kein Problem.
Nach der Finalisierung des Layouts kann der Druckauftrag an den Drucker gesendet werden.
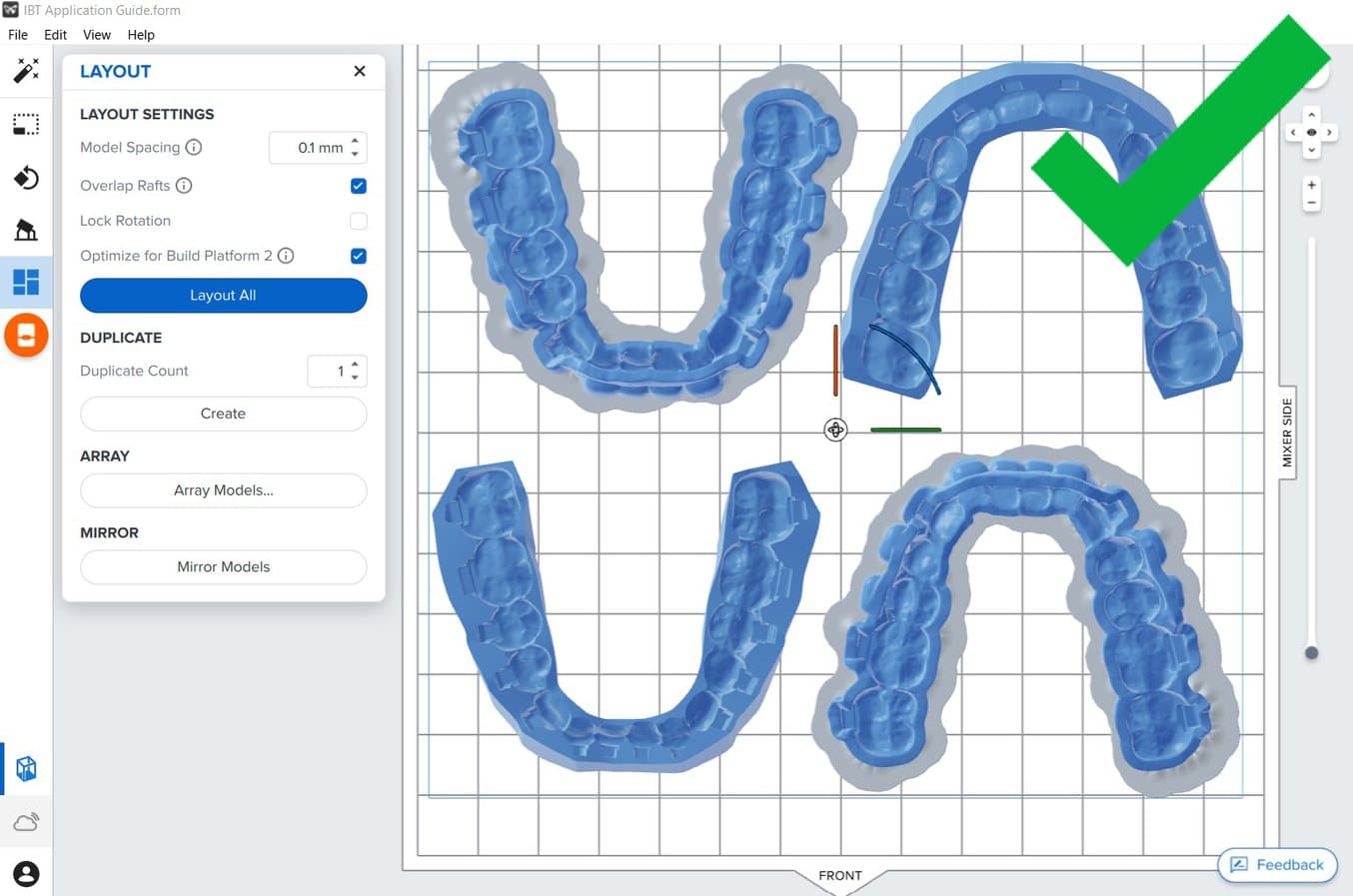
3.6 Senden des Druckauftrags an den Drucker
Senden Sie den Druckauftrag an den Drucker, indem Sie auf das orangefarbene Druckersymbol auf der linken Bildschirmseite klicken.
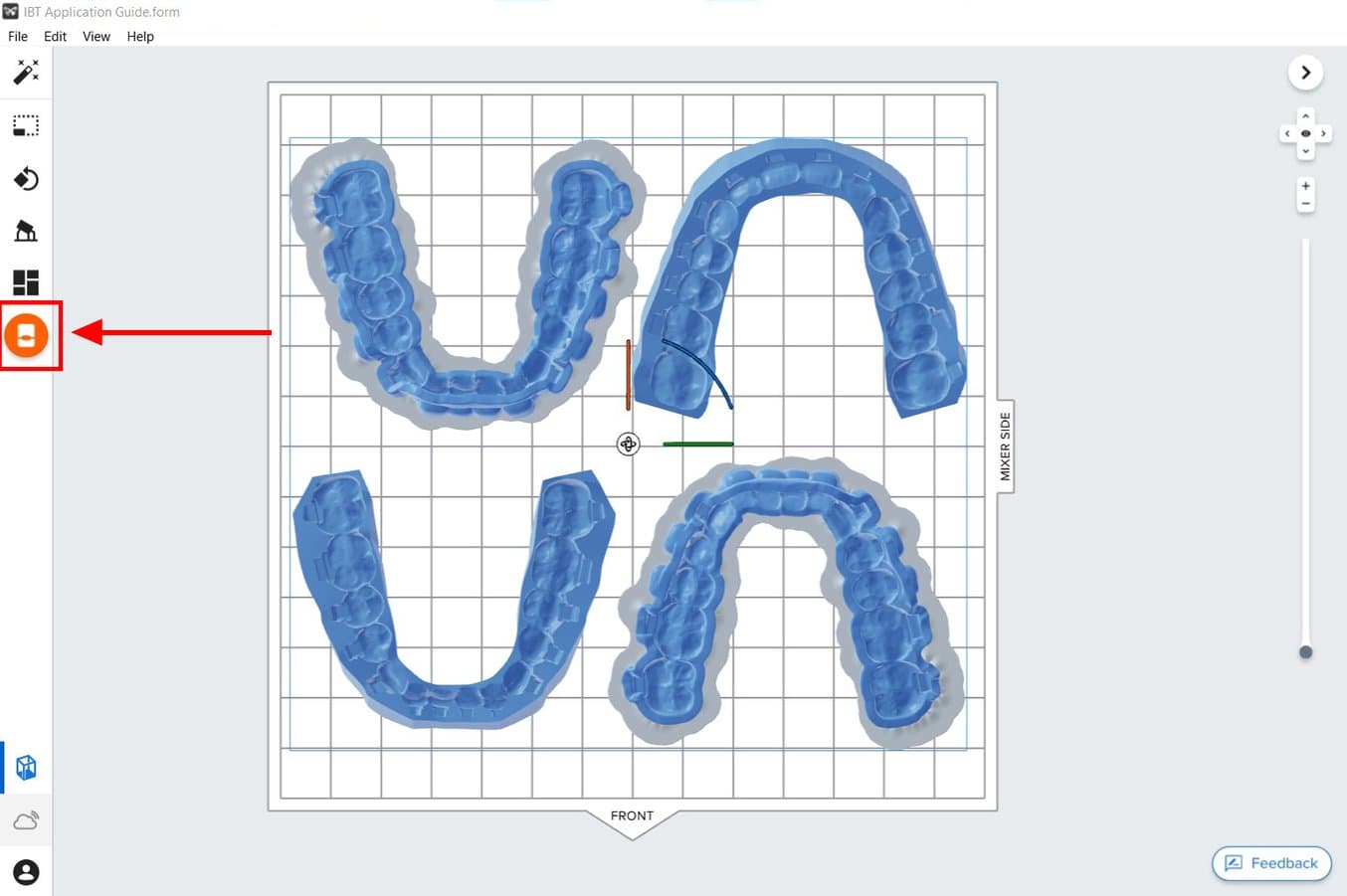
Das Dialogfeld Print (Drucken) wird geöffnet.Hier können Sie den Drucker ändern, an den der Auftrag gesendet wird, den Auftrag umbenennen und den Auftrag mit der Schaltfläche Print Now (Jetzt drucken) an den Drucker senden.
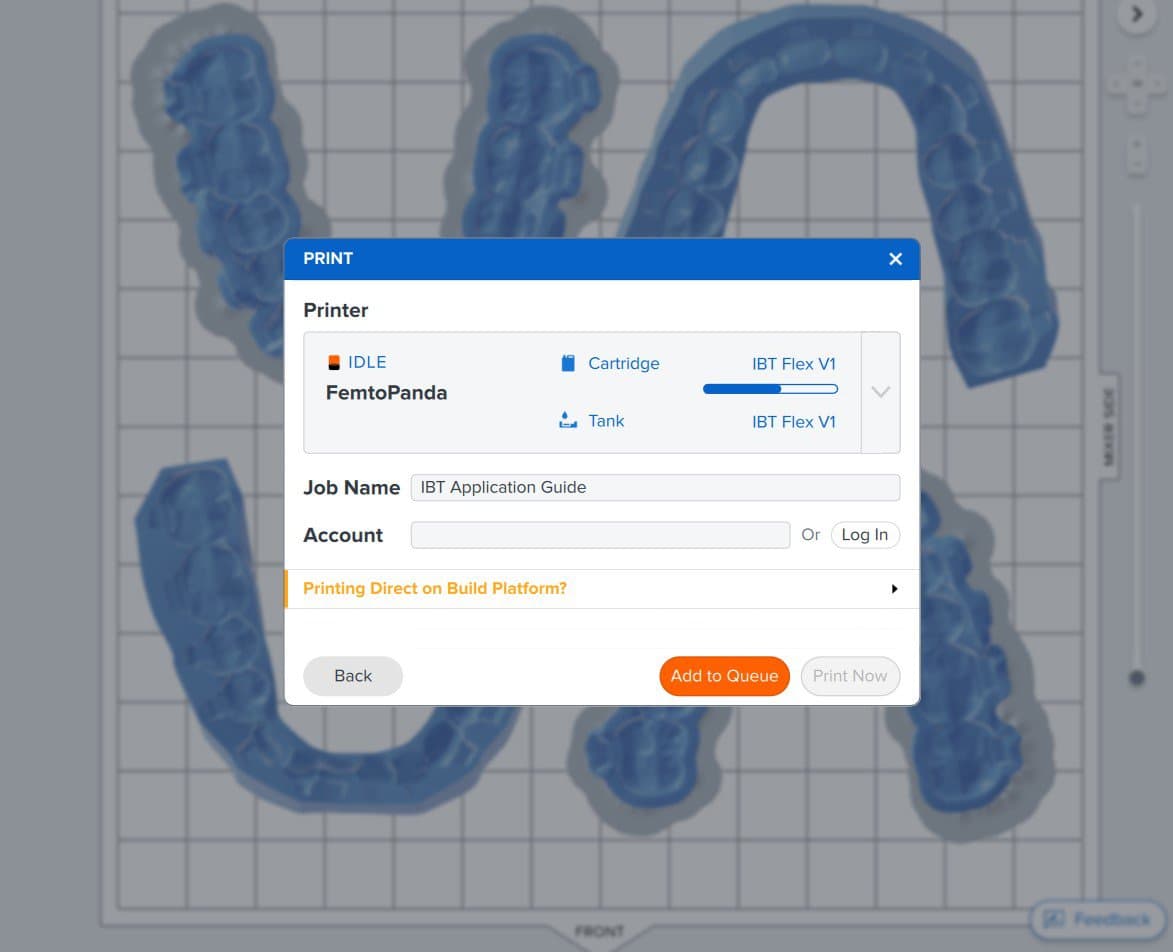
3.7 Einrichten des Druckers
Schütteln Sie die Kartusche mit IBT Flex Resin und setzen Sie sie anschließend in den Formlabs-3D-Drucker ein, zusammen mit einer Konstruktionsplattform und einem kompatiblen Harztank.
- Starten Sie den Druckauftrag durch Auswahl am Touchscreen des Druckers.
- Befolgen Sie alle Anweisungen oder Dialoge, die auf dem Druckerbildschirm angezeigt werden.
- Der Drucker schließt den Druckvorgang automatisch ab.
Wenn Sie mit einem leeren Harztank beginnen, sparen Sie Zeit, indem Sie den Tank manuell direkt aus der Kartusche mit Kunstharz vorfüllen.
Hinweis: Prüfen Sie auf der Formlabs-Supportseite, ob Ihr Drucker und das von Ihnen verwendete Kunstharz miteinander kompatibel sind, bevor Sie einen Druck starten.
Anmerkung
Zur vollen Gewährleistung der Konformität und Biokompatibilität erfordert IBT Flex Resin einen eigenen Harztank, eine eigene Konstruktionsplattform, einen eigenen Form Wash und ein eigenes Finish Kit, die nicht mit anderen Kunstharzen verwendet werden dürfen.
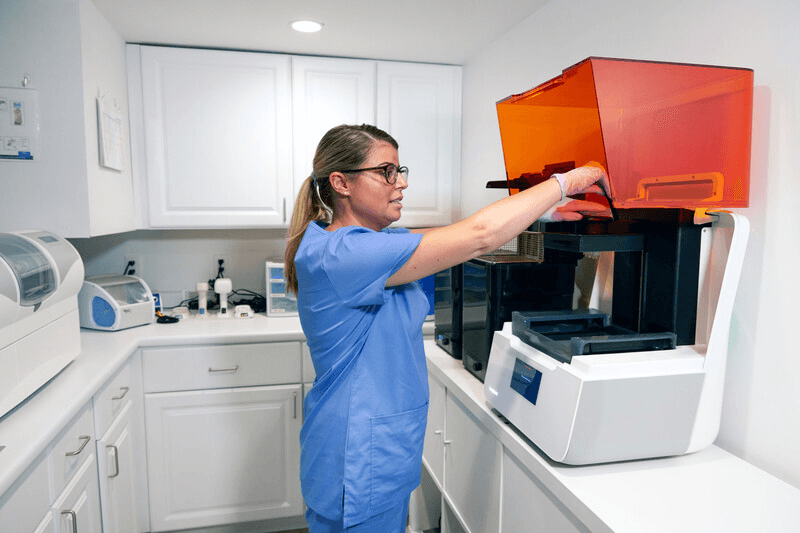
4. Nachbearbeitung
Tragen Sie bei der Handhabung ungehärteter Kunstharze und Teile immer Handschuhe.
4.1 Entfernen von Teilen
Um Druckteile von der Konstruktionsplattform zu entfernen, schieben Sie das Ablösewerkzeug unter das Raft des Teils und drehen Sie es.
Hinweis: Aufgrund der Flexibilität von Teilen aus IBT Flex Resin lassen diese sich bei Verwendung der Build Platform 2 womöglich weniger leicht lösen als steifere Materialien.
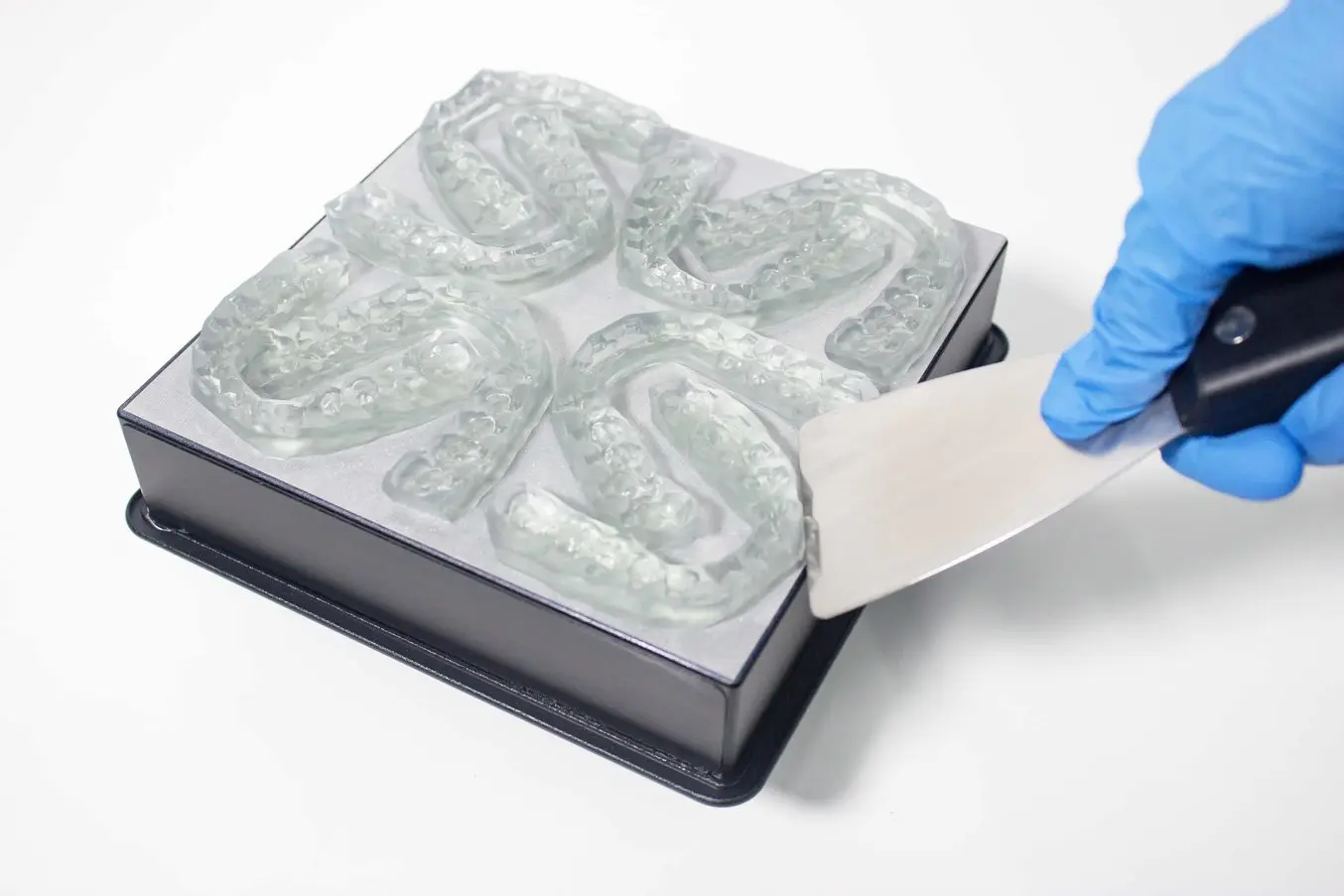
4.2 Waschen
Vorsichtsmaßnahmen
- Das Waschen des Druckteils mit Lösungsmitteln muss in einer gut belüfteten Umgebung erfolgen sowie mit geeigneten Schutzmasken und -handschuhen.
- Abgelaufenes oder unverbrauchtes IBT Flex Resin muss gemäß den örtlichen Vorschriften entsorgt werden.
Platzieren Sie die Druckteile in einem mit Isopropylalkohol (IPA, ≥99 %) gefüllten Form Wash oder Form Wash L und lassen Sie sie für die im Fertigungsleitfaden angegebene Zeit waschen.
Beim Waschvorgang müssen die Teile vollständig mit IPA bedeckt sein.
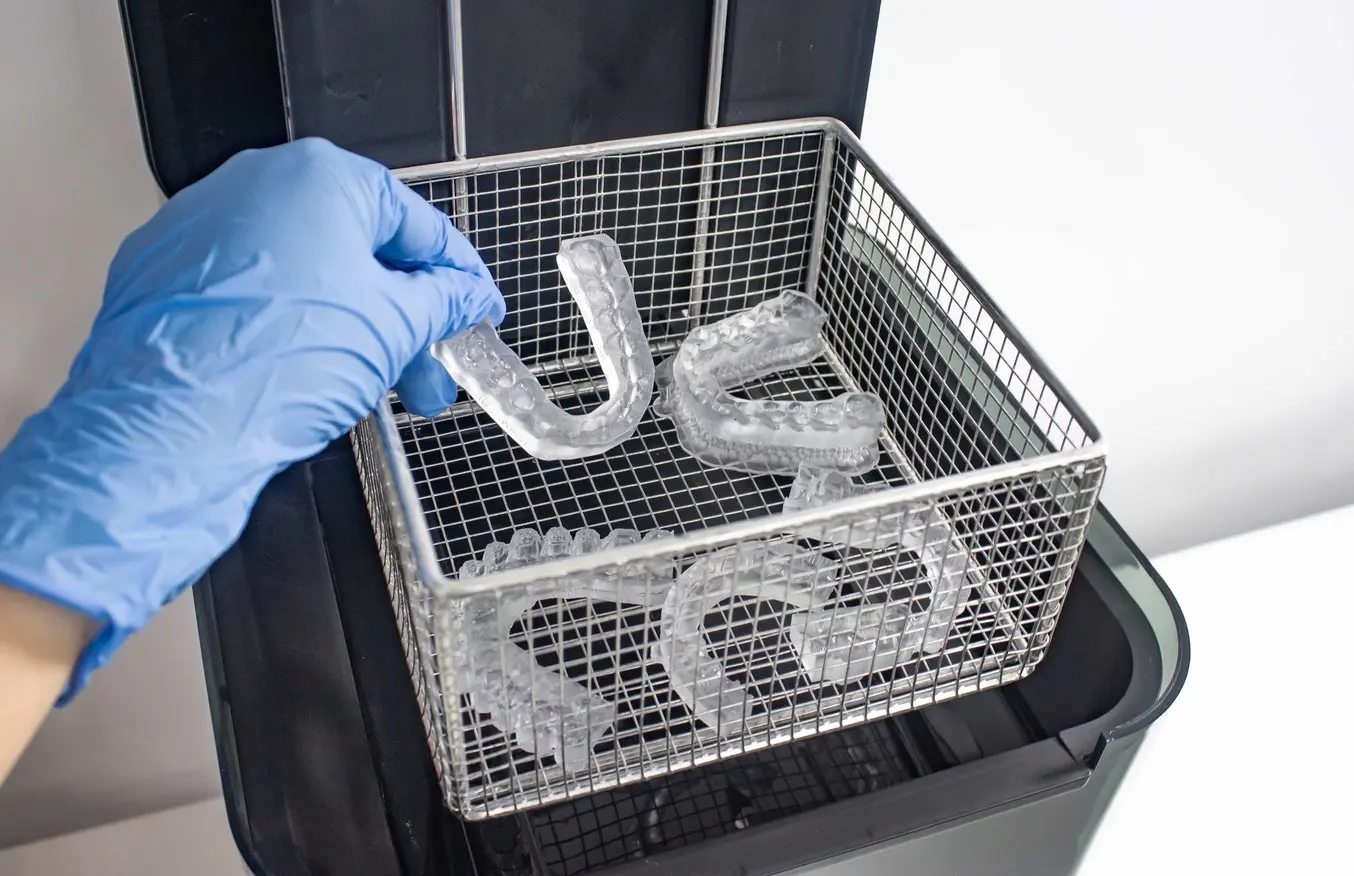
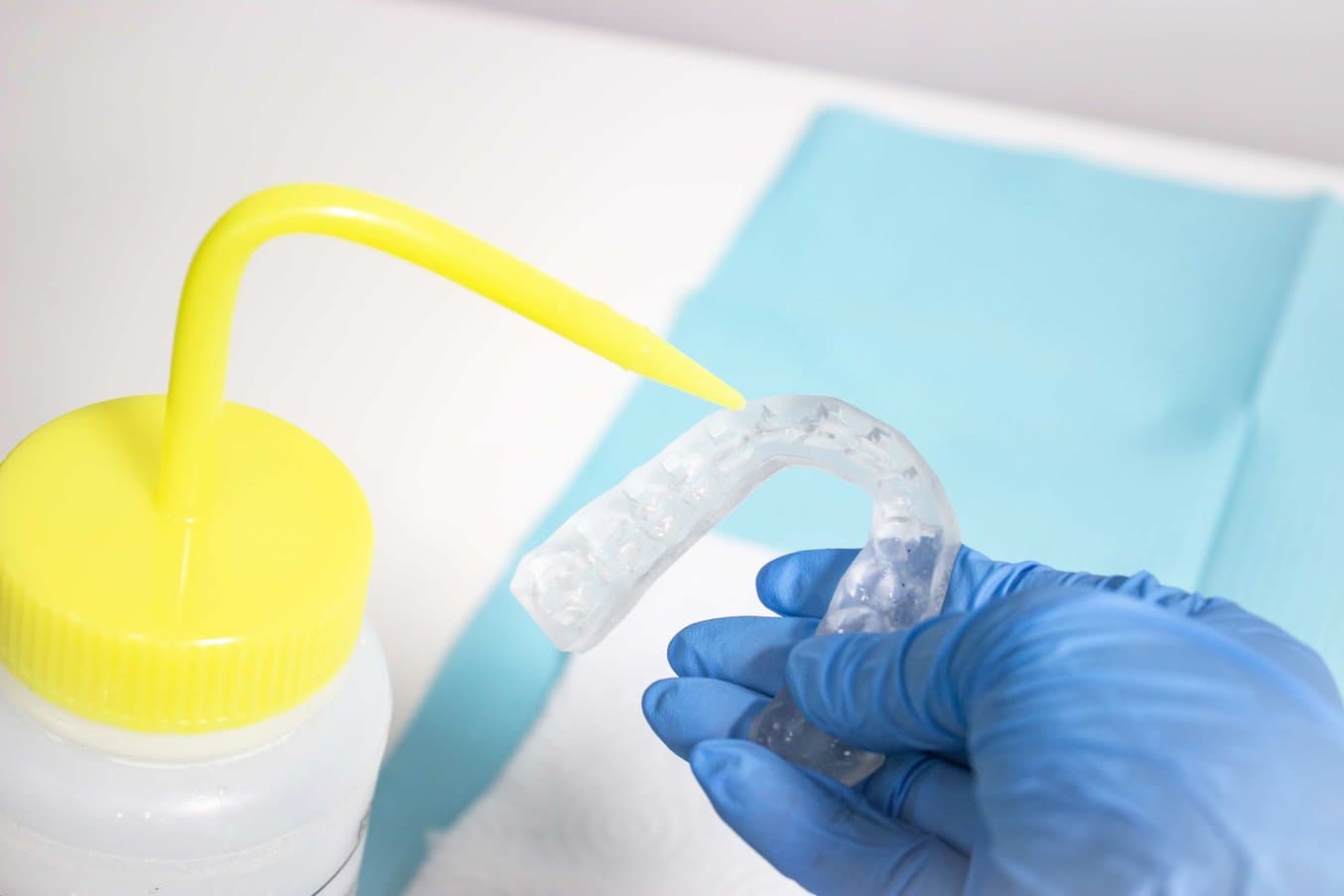
Falls durch die Geometrie Ihres Druckteils Kunstharzreste eingeschlossen werden, kann es helfen, nach der Hälfte des Waschzyklus leicht mit einem Pinsel über den Bracket-Aussparungen entlangzustreichen.
Eine zu lange Waschdauer kann die Maßgenauigkeit und Eigenschaften von Druckteilen mit der Zeit beeinträchtigen.
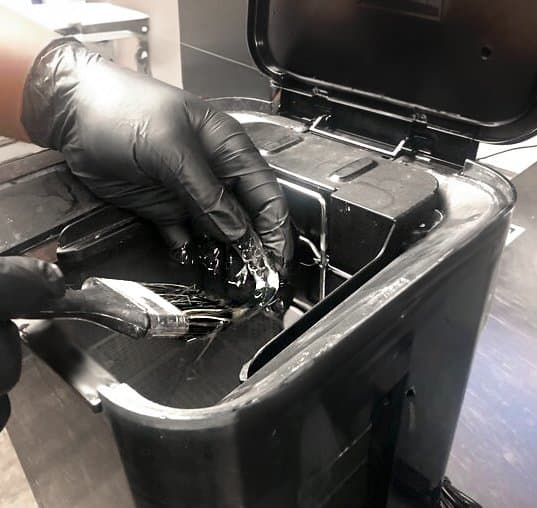
4.3 Trocknen
Nehmen Sie die Teile aus dem IPA und lassen Sie sie mindestens 30 Minuten bei Raumtemperatur an der Luft trocknen, in einem gut belüfteten Bereich.
Mit Druckluft lassen sich Teile schnell trocknen und auf verbleibendes flüssiges Kunstharz untersuchen. Auch beim Einsatz von Druckluft sollten Sie für genug Ruhetrocknung sorgen.
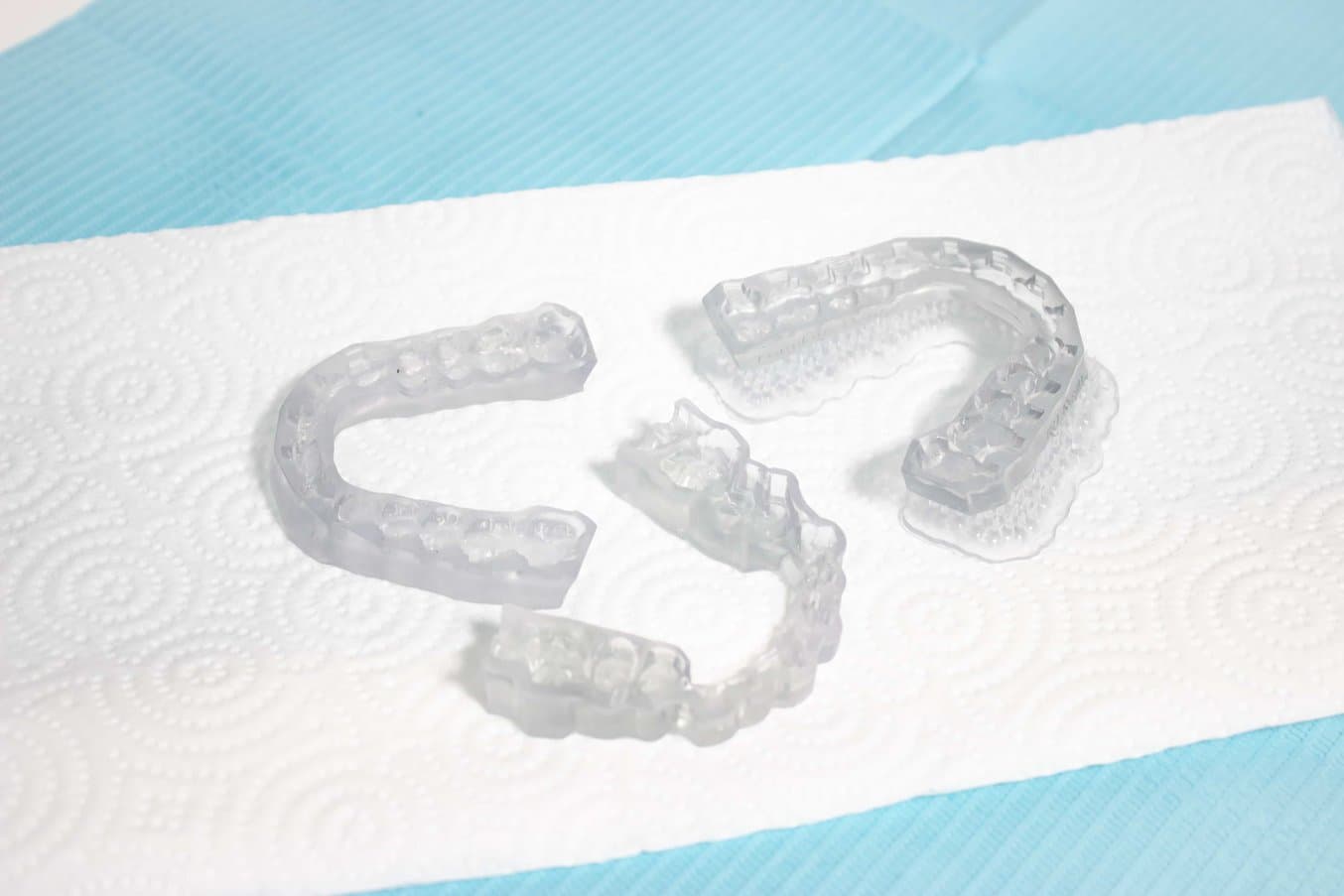
Untersuchen Sie die Druckteile und stellen Sie sicher, dass sie sauber und trocken sind. Vor den nächsten Schritten dürfen sich kein Restalkohol, kein überschüssiges flüssiges Kunstharz und keine Rückstände auf den Oberflächen befinden.
Sollte nach dem Trocknen noch feuchtes, ungehärtetes Harz verbleiben, verwenden Sie eine Druckflasche mit frischem IPA, um dieses zu entfernen. Zum Entfernen ungehärteten Harzes kann es auch helfen, mit einem Pinsel leicht über den Bracket-Aussparungen entlangzustreichen. Trocknen Sie die Teile erneut, nachdem das flüssige Harz entfernt ist. Auch hier ermöglicht Druckluft eine schnelle Inspektion.
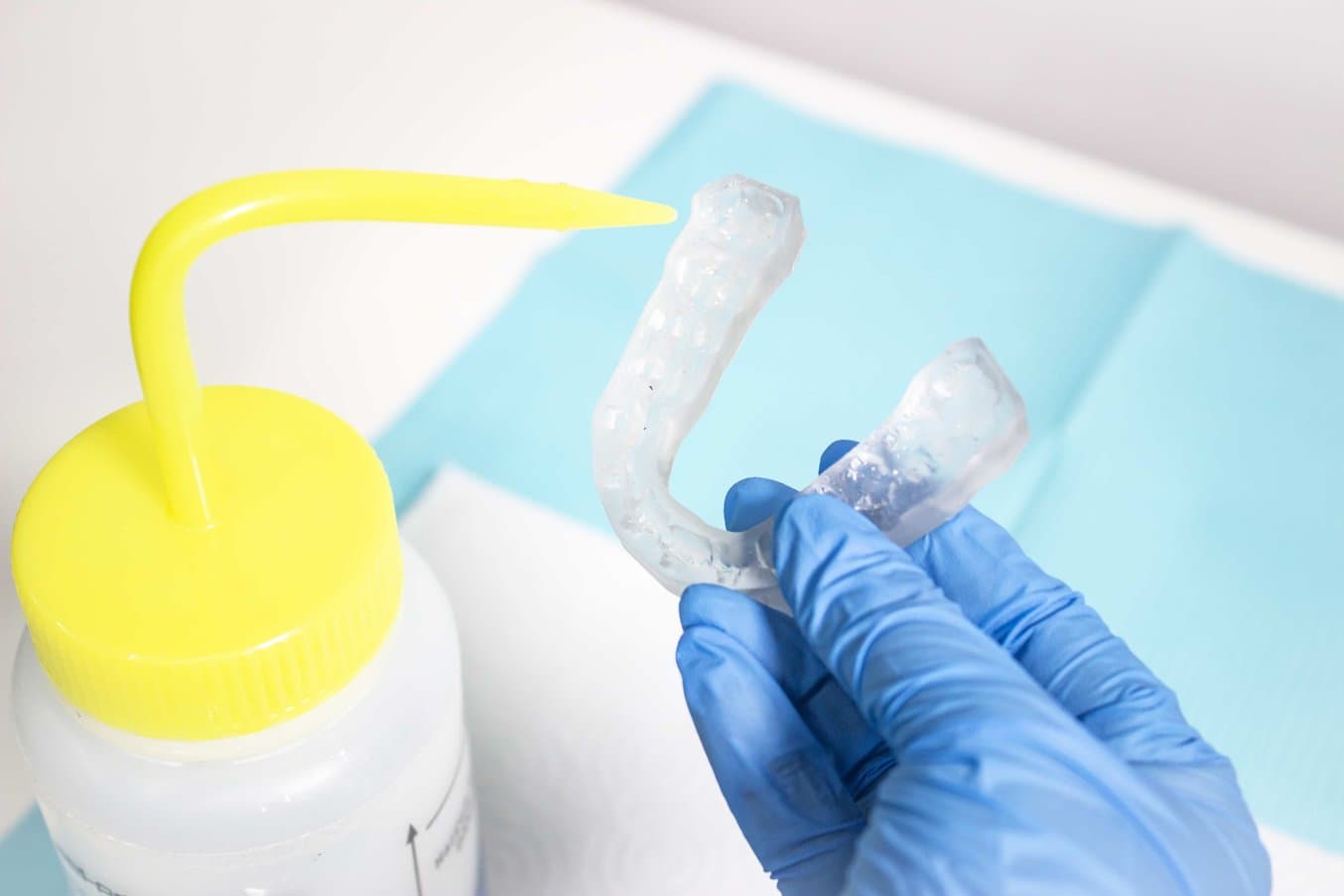
4.4 Nachhärtung
Zur Erhaltung der Maßgenauigkeit und Biokompatibilität müssen beim Nachhärten bestimmte Anweisungen befolgt werden.
Die Druckteile sollten sich während der Nachhärtung in einer von Formlabs validierten Nachhärtestation (Form Cure, Form Cure L oder Fast Cure) in einem transparenten Behälter befinden und mit Wasser bedeckt sein.
Wurden die Transferschienen mit Raft und Stützstrukturen gedruckt, platzieren Sie die Druckteile so in der Nachhärtestation, dass die Raftseite unten liegt. Wurden die Transferschienen ohne Stützstrukturen direkt auf der Konstruktionsplattform gedruckt, platzieren Sie sie mit den Intaglioflächen nach oben in der Nachhärtestation.
Härten Sie die Teile in einem Form Cure, Form Cure L oder Fast Cure mit den im Fertigungsleitfaden angegebenen Einstellungen nach.
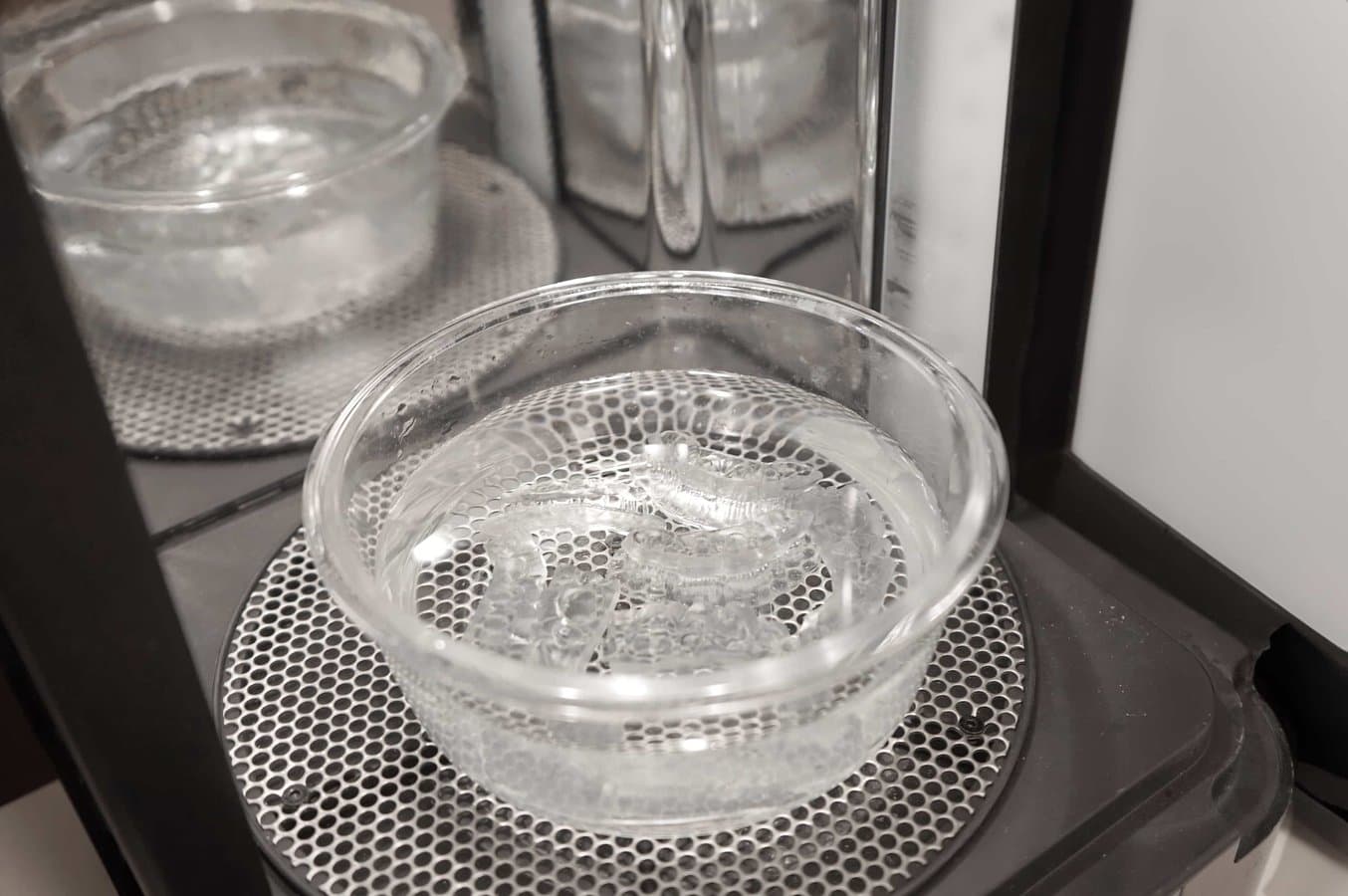
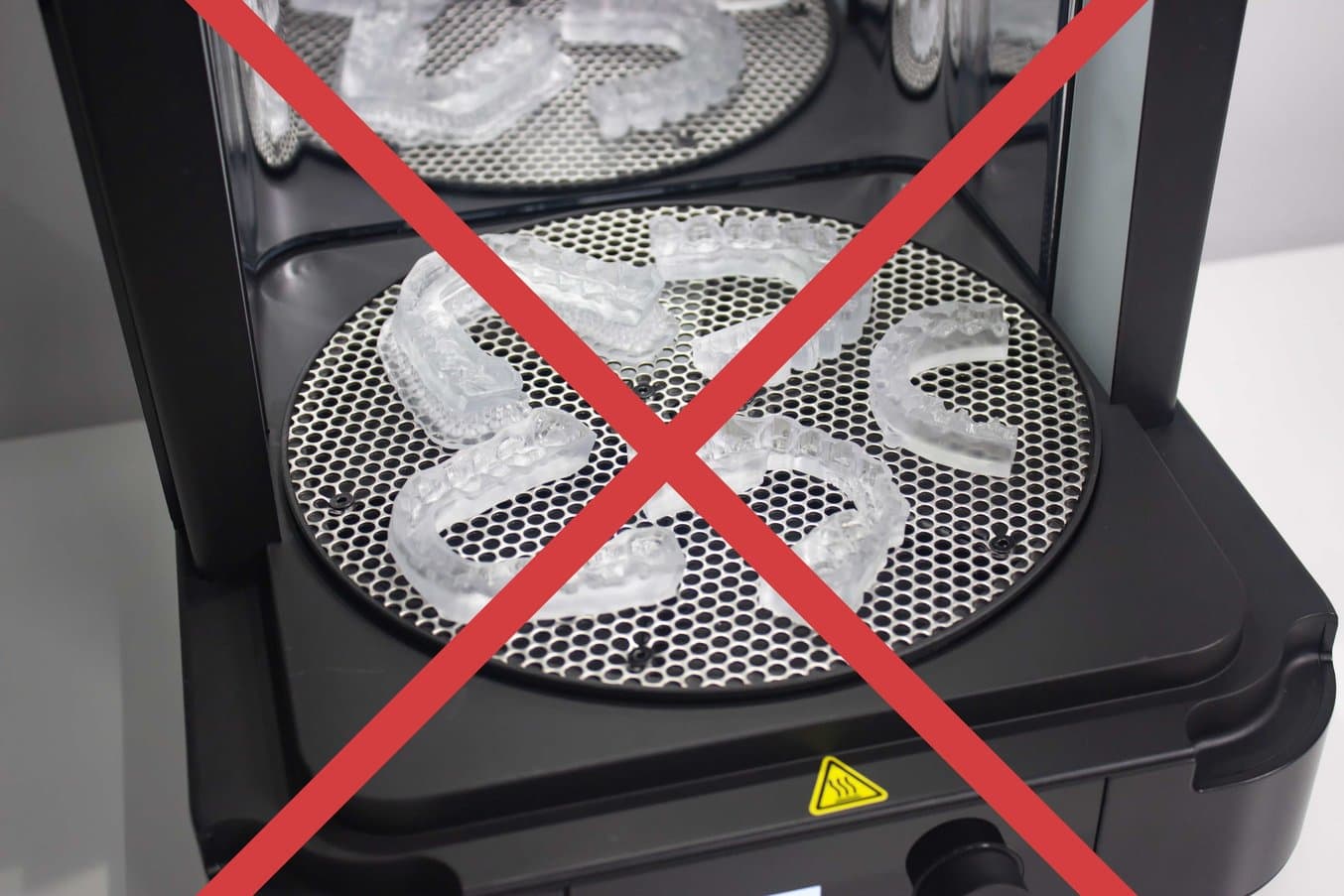
4.5 Entfernen der Stützstrukturen
Entfernen Sie Stützstrukturen, falls vorhanden, mit dem im Formlabs Finish Kit enthaltenen Seitenschneider oder einer Schere.
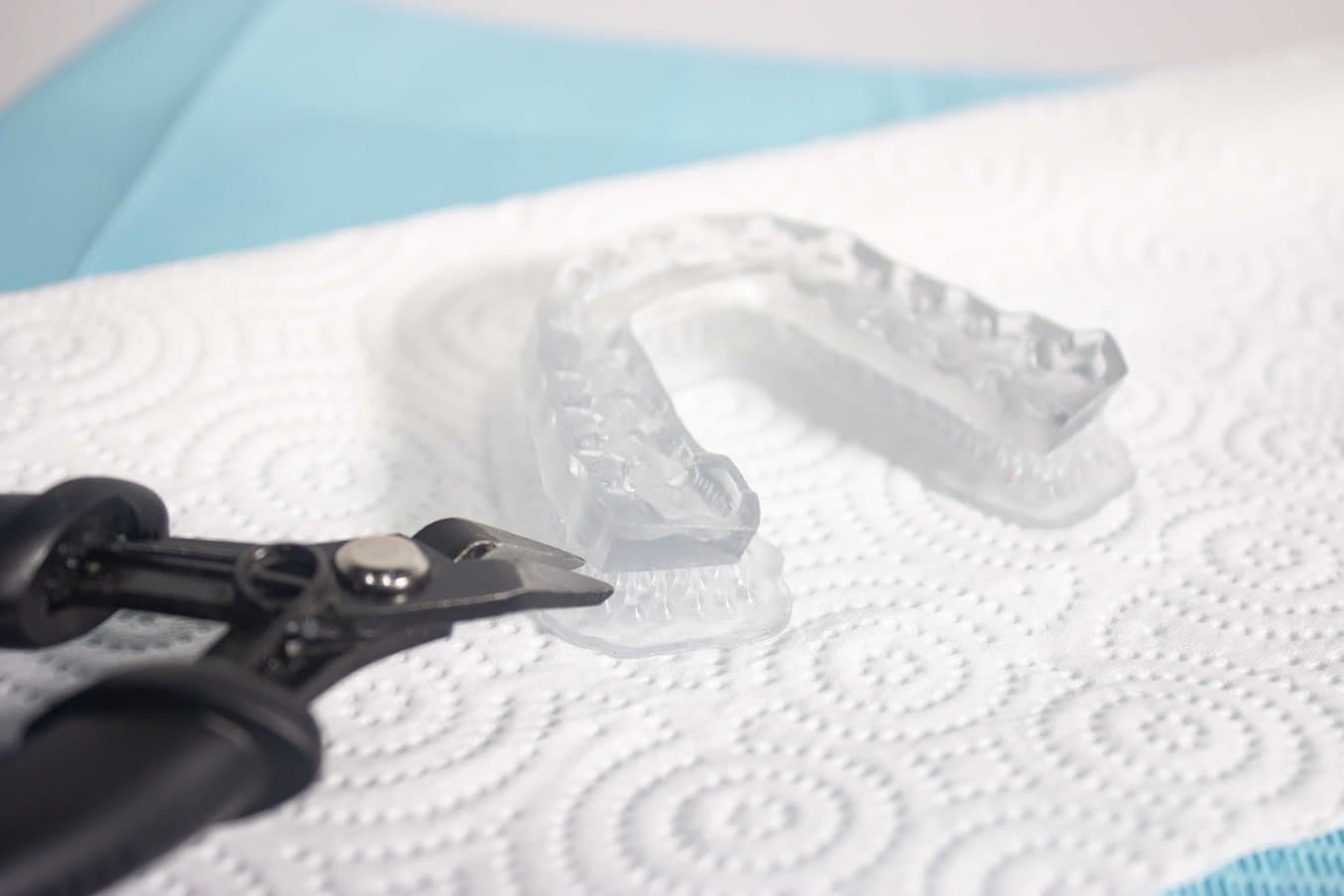
4.6 Fertigstellung
Falls nach dem Entfernen der Stützstrukturen noch Überreste auf der Oberfläche der 3D-gedruckten Transferschiene verbleiben, können Sie diese mit einer scharfen Irisschere entfernen.
Untersuchen Sie die dentale Anwendung. Entsorgen Sie das Teil und drucken Sie es erneut, falls Sie Beschädigungen oder Risse entdecken.
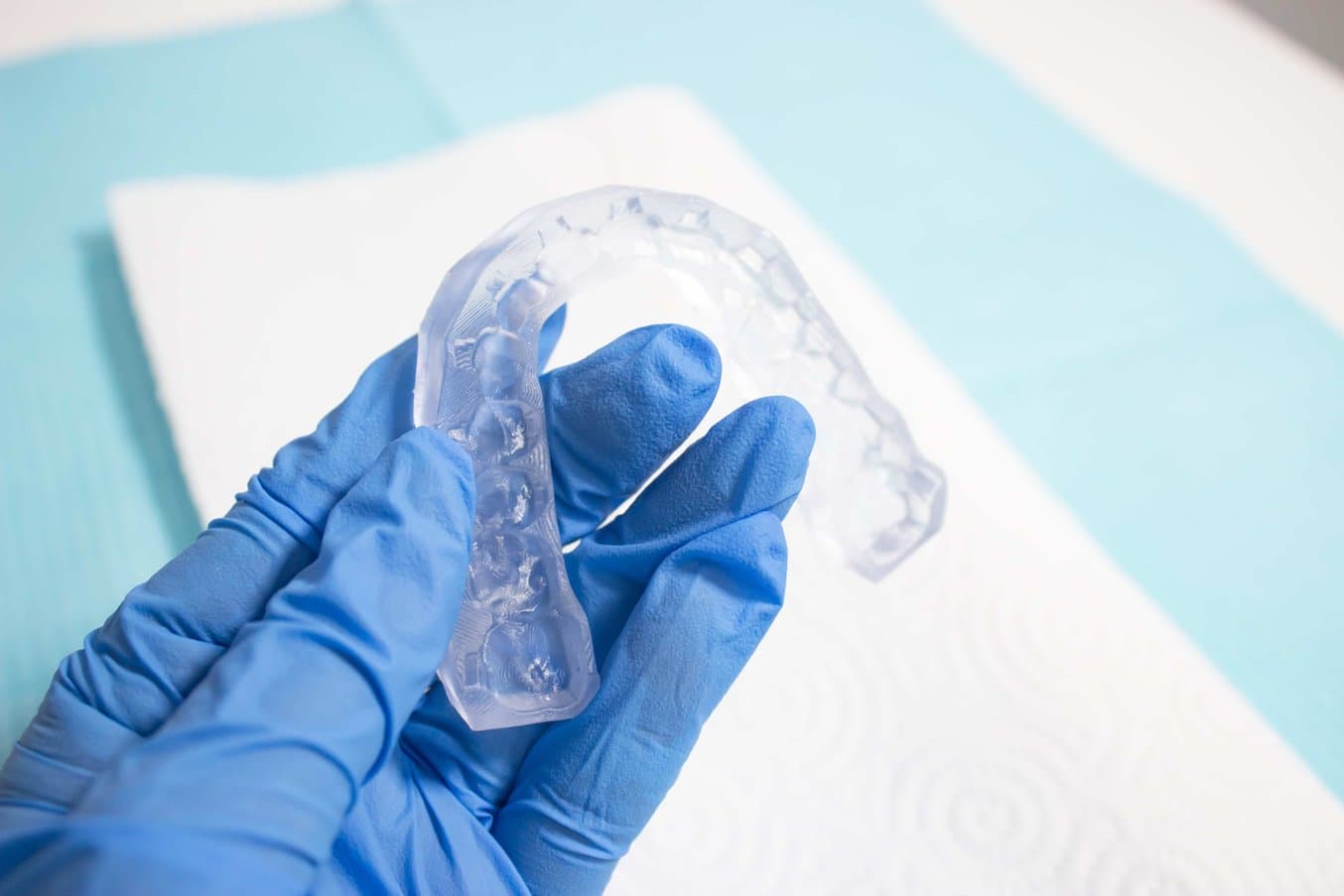
5. Pflege und Verwendung der dentalen Anwendung
Empfehlung zur Polymerisationslampe
Bei unserer Zusammenarbeit mit Kieferorthopäd*innen haben wir festgestellt, dass die richtige Polymerisationslampe die Haftung der Brackets über die Transferschienen erheblich verbessert. Wir empfehlen die recht erschwingliche und leistungsstarke Lampe Ledex WL-090+ Curing Light.
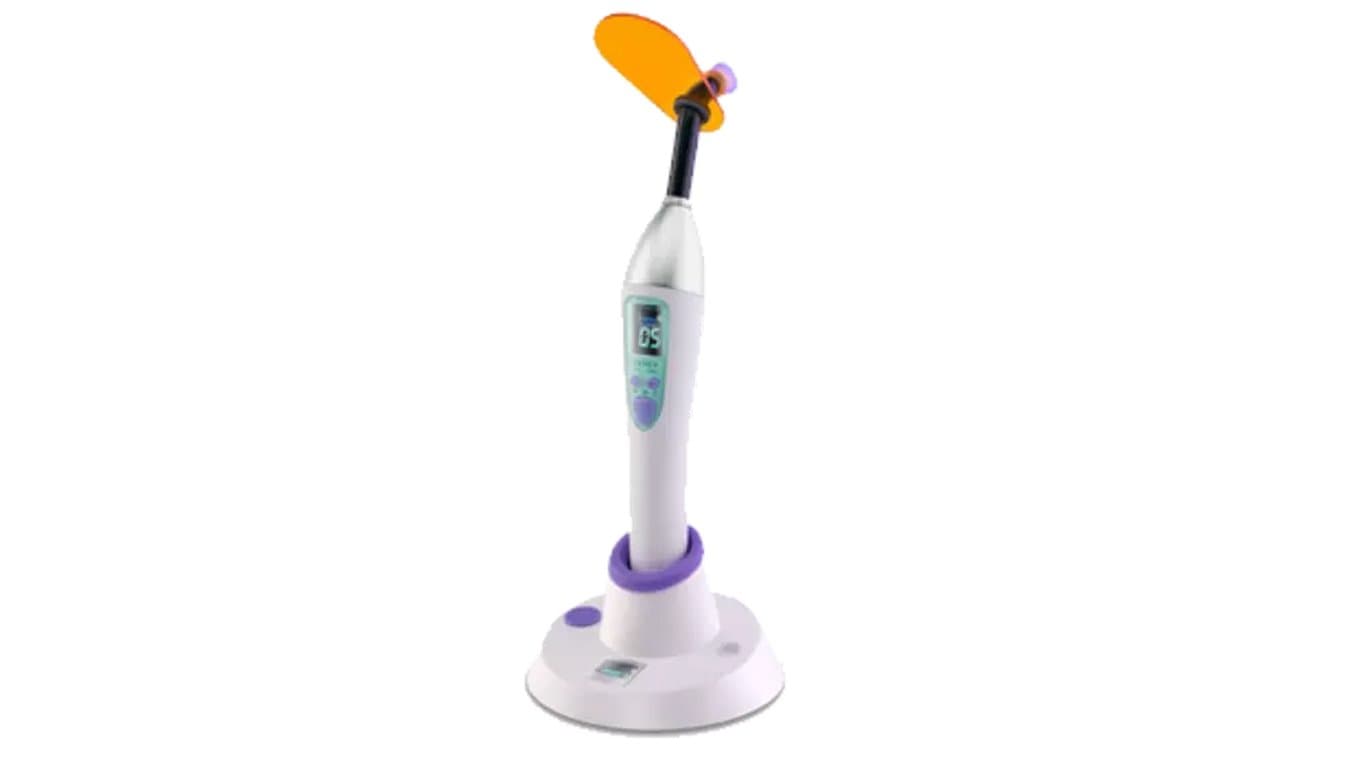
5.1 Reinigung
Vollständig nachbearbeitete Teile können mit neutraler Seife und zimmertemperiertem Wasser gereinigt werden.
Untersuchen Sie die Teile nach dem Reinigen immer auf Risse. Entsorgen Sie die Teile, falls Sie Beschädigungen oder Risse feststellen.
5.2 Desinfektion
Die Transferschiene für die indirekte Verklebung kann gemäß den betriebsinternen Anweisungen gereinigt und desinfiziert werden.
Die von uns getestete Desinfektionsmethode umfasst das Eintauchen der fertigen Teile in frischen 70%igen IPA für 5 Minuten.
Hinweis: Lassen Sie das Teil nicht länger als fünf Minuten in der Alkohollösung.
Untersuchen Sie das Teil nach der Desinfektion auf Risse, um die Integrität der Transferschiene zu gewährleisten.
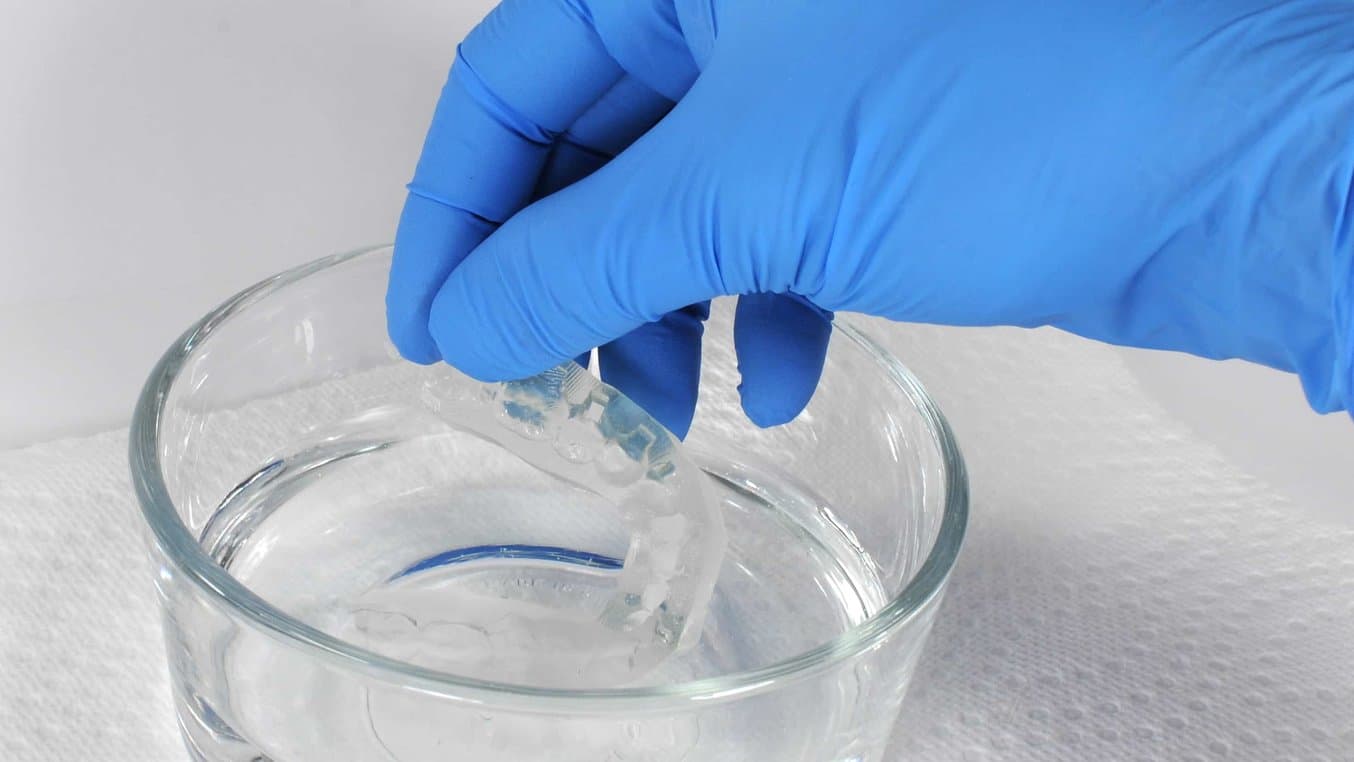
5.3 Lagerung
Wenn sie nicht verwendet werden, sind die Druckteile in geschlossenen, lichtundurchlässigen oder orangefarbenen Behältern aufzubewahren.
Lagern Sie die Teile an einem kühlen, trockenen Ort ohne direkte Sonneneinstrahlung. Übermäßige Lichteinwirkung kann im Laufe der Zeit die Farbe und Leistung der Druckteile beeinträchtigen.
Lagern Sie Kartuschen bei 10 - 25 °C. Bei der Lagerung dürfen 25 °C niemals überschritten werden. Von Zündquellen fernhalten.
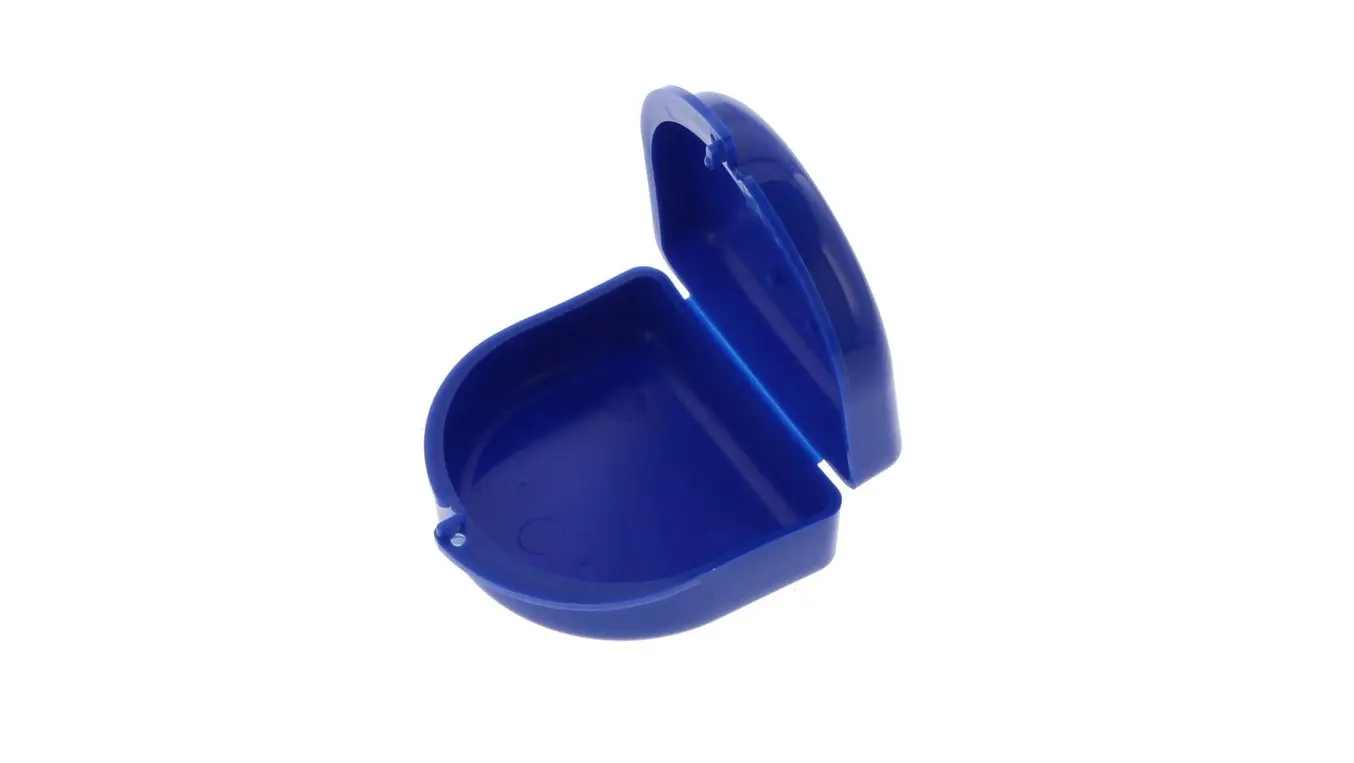
5.4 Entsorgung
1. Ausgehärtetes Kunstharz ist ungefährlich und kann als normaler Hausmüll entsorgt werden.
-
Befolgen Sie die betrieblichen Vorschriften für Abfälle, die als biogefährdend gelten könnten.
2. Flüssiges Kunstharz sollte gemäß den gesetzlichen Bestimmungen (auf kommunaler, regionaler oder nationaler Ebene) entsorgt werden.
- Wenden Sie sich an einen zugelassenen Entsorgungsfachbetrieb, um flüssiges Kunstharz zu entsorgen.
- Der Abfall darf nicht in das Entwässerungssystem bzw. die Abwasserkanalisation gelangen.
- Freisetzung in die Umwelt vermeiden.
- Verunreinigte Verpackungen wie unbenutzte Produkte entsorgen.
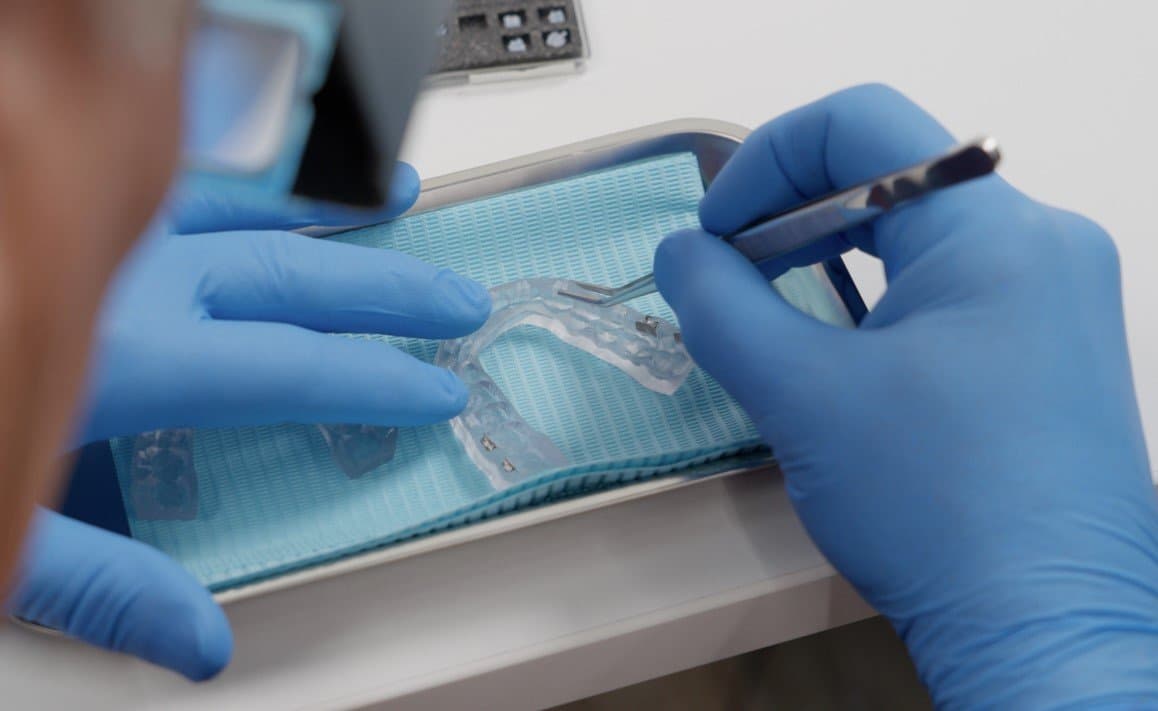
Weitere Ressourcen
Lernen Sie die zahnmedizinischen Ressourcen von Formlabs kennen und entdecken Sie detaillierte Leitfäden, Schritt-für-Schritt-Anleitungen, Whitepapers, Webinare und vieles mehr.