Indirect Bonding Trays For Orthodontic Bracket Placement With Formlabs SLA 3D Printers
This application guide is a step-by-step walkthrough of the workflow for producing indirect bonding trays for orthodontic bracket placement with Formlabs IBT Flex Resin and Formlabs Dental 3D printers. Always consult the Manufacturing Guide and Instructions For Use for the absolute requirements.
IBT Flex Resin is a flexible biocompatible material for efficient, accurate dental bracket placement. 3D printed indirect bonding trays reduce chair time and increase patient comfort by placing all of the brackets or entire quadrants at once. IBT Flex Resin is a Class 1 medical device that offers optimized tear strength, translucency, and flexibility, for appliances that are easy to plan, easy to use, and easy to remove.
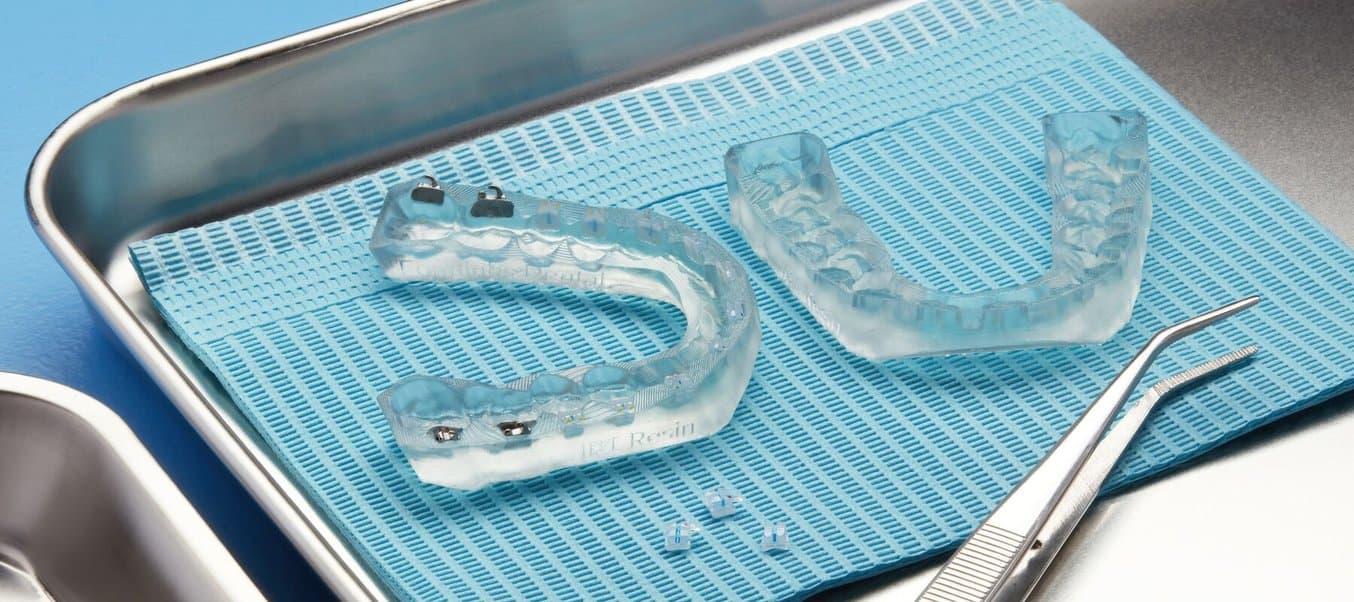
Table of Contents
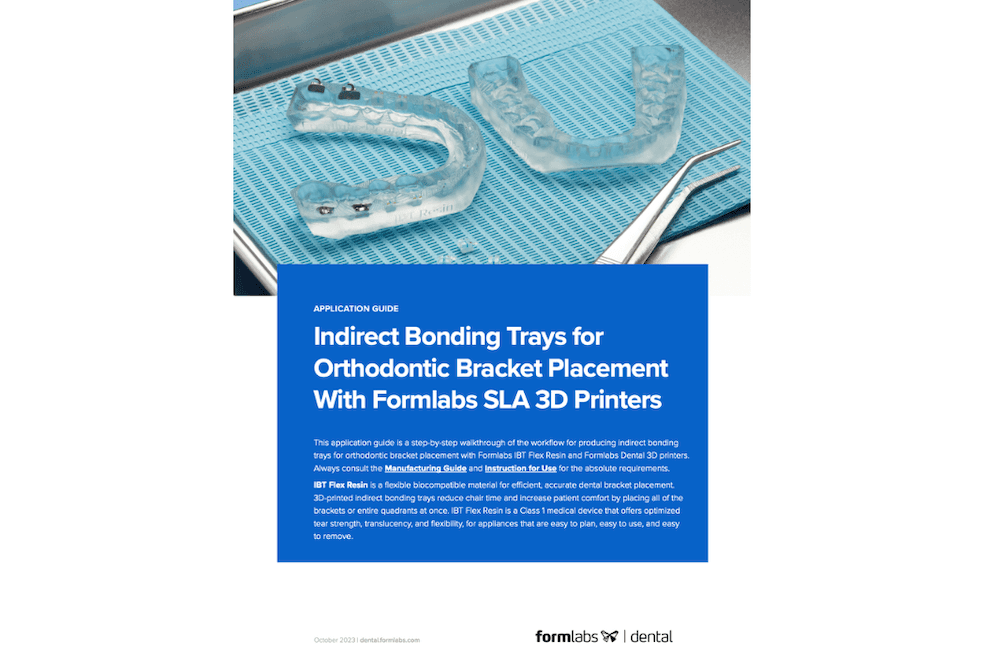
Indirect Bonding Trays for Orthodontic Bracket Placement With Formlabs SLA 3D Printers
Would you like to save this guide, print it, or share it with colleagues? Download it as a PDF.
Workflow Requirements
Needed From the Dentist
- A physical or digital impression of the patient's dentition
Required Hardware and Materials
Made by Formlabs:
- Form 3B/+ SLA 3D Printer or Form 3BL SLA 3D Printer
- Form 3 Resin Tank or Form 3L Resin Tank
- Standard Build Platform, Stainless Steel Build Platform, or Build Platform 2
- IBT Flex Resin
- Form Wash or Form Wash L
- Formlabs validated curing unit: Form Cure, Form Cure L, or Fast Cure
- Finishing kit or secondary wash station
Made by Third Parties:
- Desktop scanner (if physical impression or model is used)
- Cutting and finishing tools (if printing on supports)
- Opaque or amber containers for appliance storage
- CBCT scanner (optional, depending on CAD software)
Required Software
Made by Formlabs:
- PreForm Software (free) 3.32 or higher
- Firmware 2.2.0 or higher - Learn more
Made by Third Parties:
- Dental design software or outsourcing to a dental design provider
1. Scan
Dental design software requires a digital impression of the patient’s anatomy in order to design the indirect bonding tray. To acquire this data, scan the patient directly with a 3D intraoral scanner or scan a physical impression or poured model with a desktop 3D scanner.
While CBCT data is optional, some IBT design software supports this data, which can be extremely useful for case planning and setup.
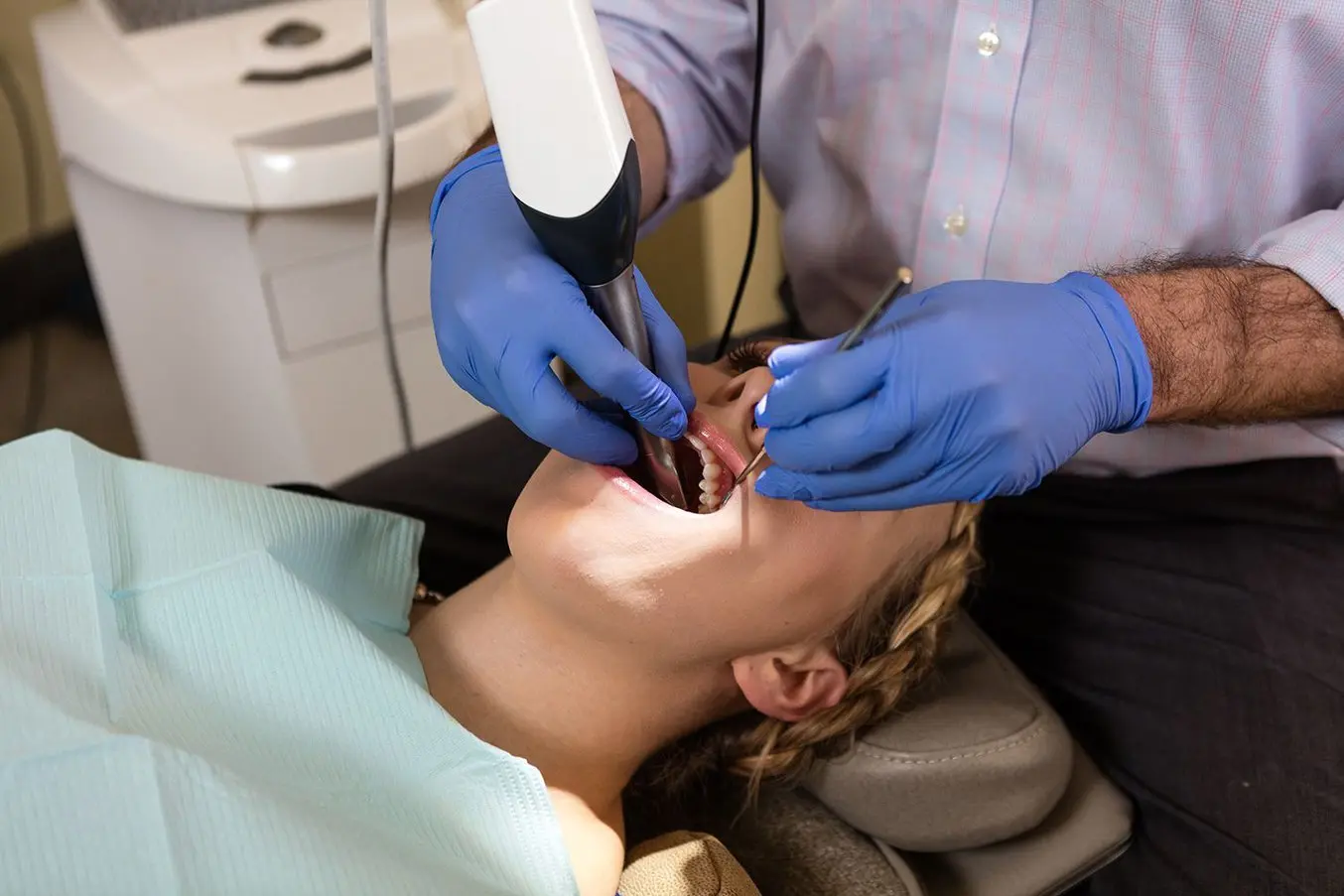
2. Design
2.1 Design the Indirect Bonding Tray
In this section we will outline design parameters and best practices for 3Shape Ortho System (Ortho Analyzer and Appliance Designer). The fundamentals and recommendations can still be helpful for other treatment and planning softwares such as OnyxCeph and should be reviewed.
You can also send the digital impression and requirements to a dental CAD outsourcing provider, like a dental design center or specialized dental laboratory, to create the appliance and manufacturing file.
Note: Using 3Shape Ortho System, we recommend using “Bar” type appliances. For more detailed guidance on how to set up and design these appliances, refer to 3Shape’s application guide.
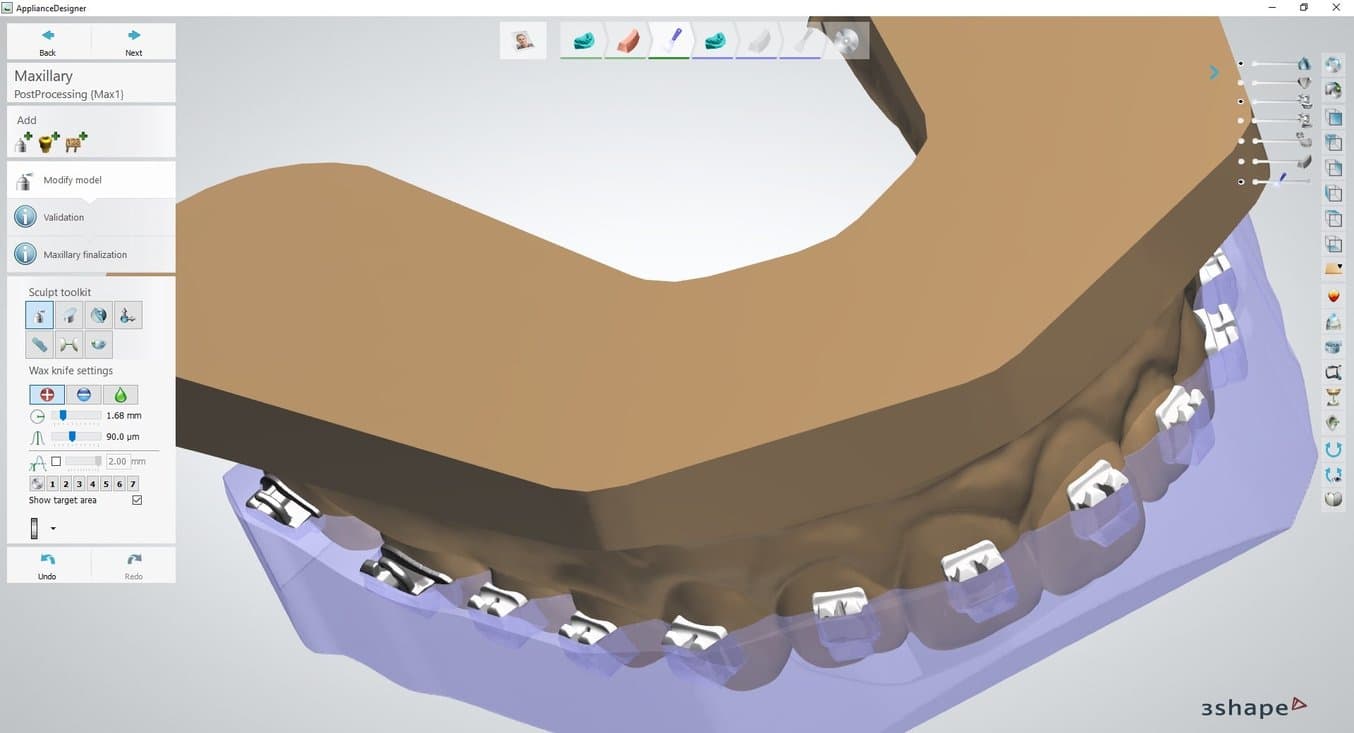
Construction and Appliance Offset Recommendations and Requirements
2.1.1 Insertion Direction
Ensure the correct insertion direction. This can influence how offsets and undercuts are applied and impact physical insertion of the final appliance.

2.1.2 Appliance Construction and Type
There are typically two ways to set up and create indirect bonding trays:
- Bar
- Offset
With the IBT Flex material, we offer compatibility with both bar and offset designs.
The bar design may offer the following advantages during use:
- Flexibility around brackets since the appliance is still thin in critical areas
- Thicker bottom surface providing some useful rigidity to the appliance
- Ability to print directly on the build platform, removing the need for support structures
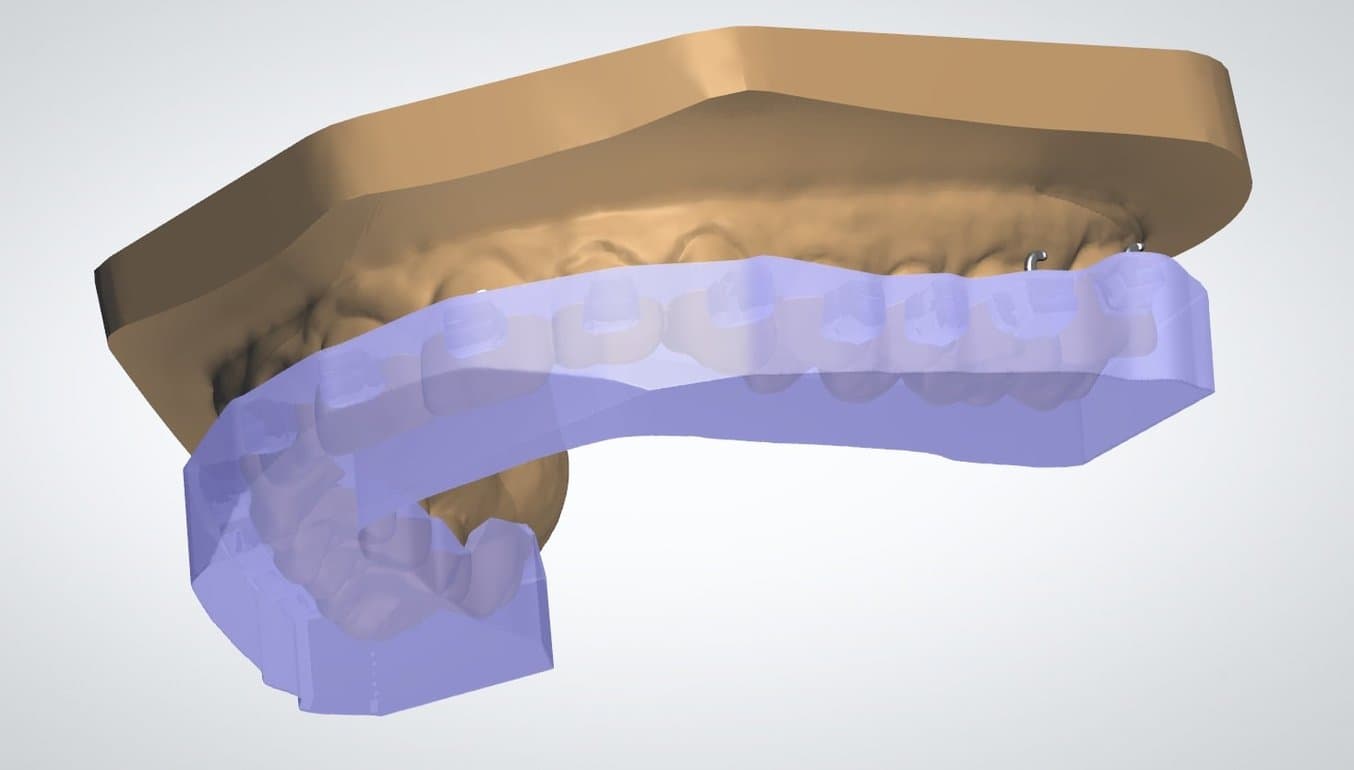
1. Bar type design example
Note: There are different CAD offsets for bar designs and offset designs, see details below.
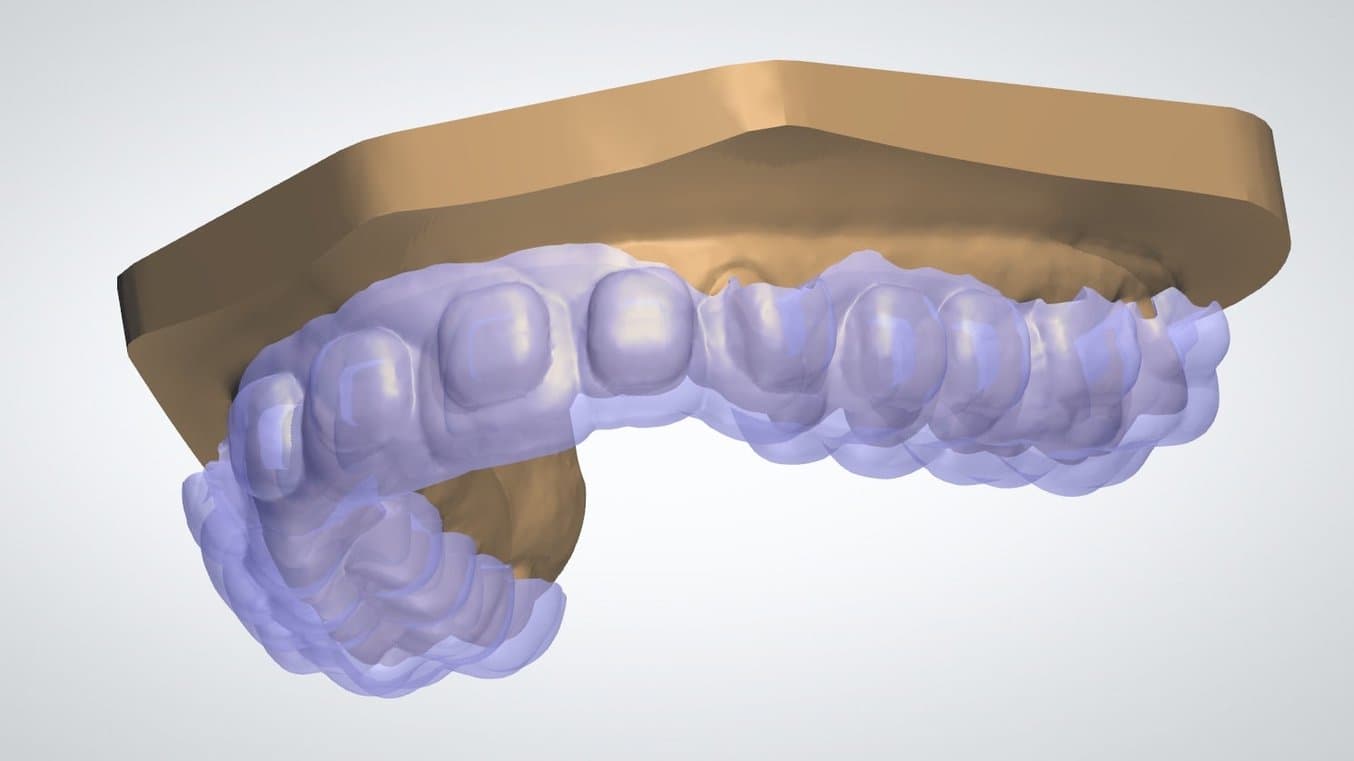
2. Offset type design example
2.1.3 Container Design and Coverage
In our testing, we found half- or three-quarter container coverage the best way to design IBT appliances, especially using the bar type design.
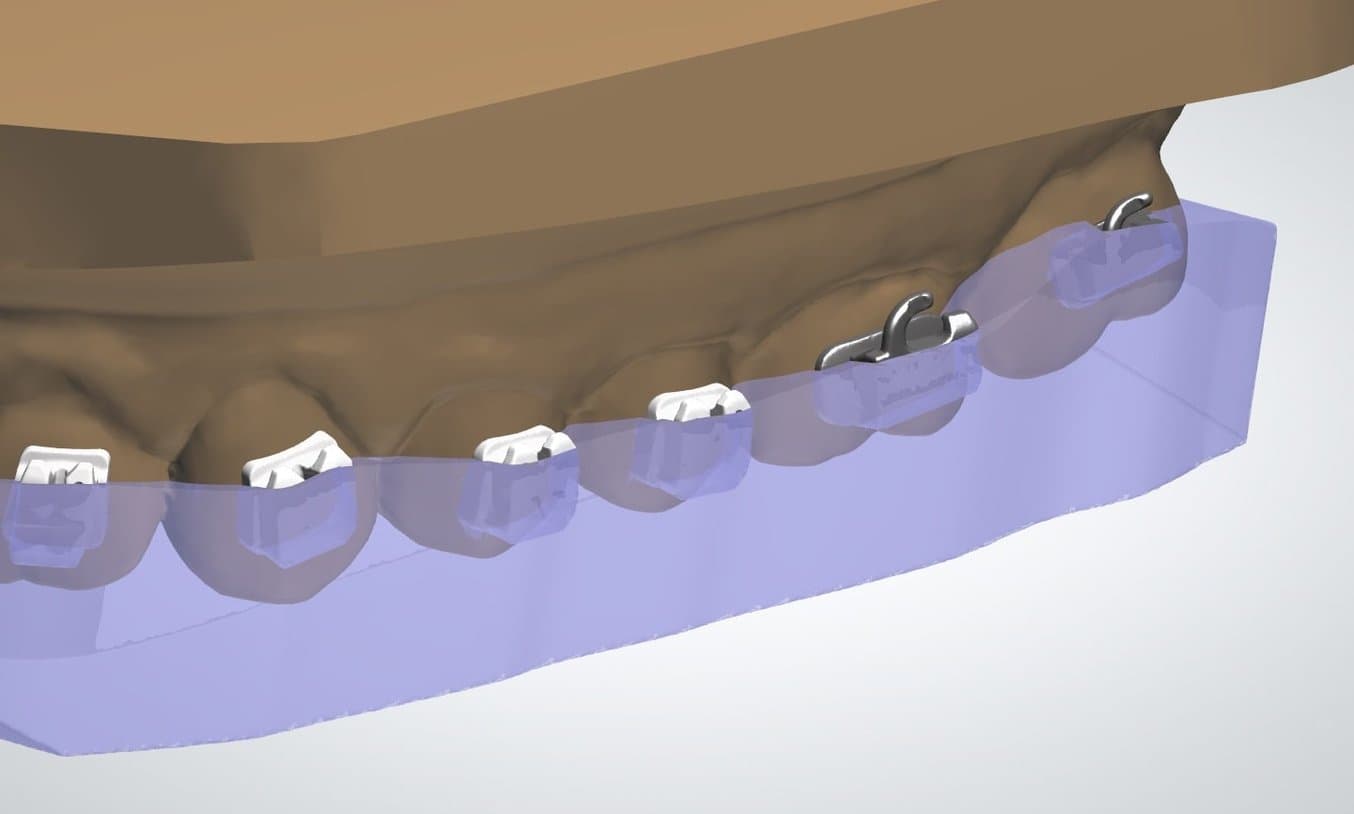
Example of a half- or three-quarter container or bracket coverage
Since the offset appliance design type is a thinner (thus more flexible) appliance, certain brackets may benefit from full coverage containers.
Full coverage should not be used on brackets with hooks. The bracket hooks can be caught in the appliance during removal.
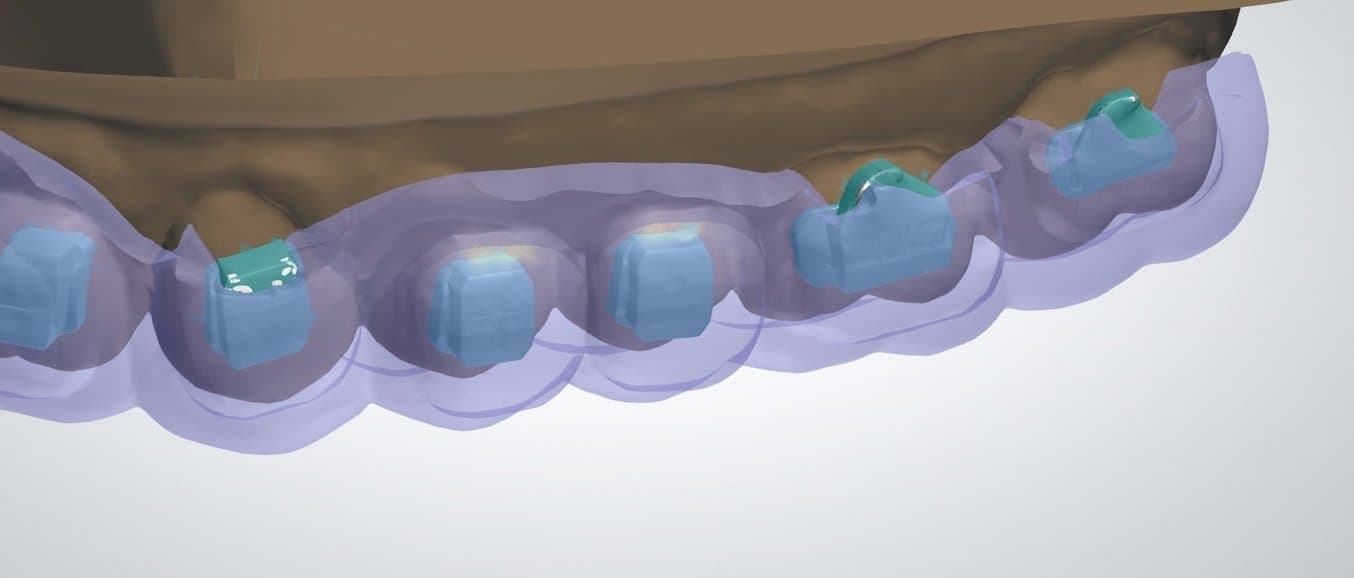
Example of a three-quarter and full container or bracket coverage
Bar Design Settings and Offsets
Appliance Minimum Thickness: 2.0 mm
2.1.4 Containers
Inner surface offset | 0 mm |
Block-out angle | 0° |
Retention amount | 0 mm |
Prolongation length | 1 mm |
Brack slot block-out | Checked |
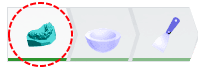
2.1.5 Finalization
Do not modify | Unchecked |
Subtracted model | Checked |
Use offset for inside surface | Unchecked |
Remove undercuts | Unchecked |
Extra combine with model | Unchecked |
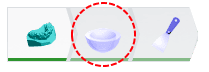
2.1.6 Modify Model
In the final step, you have the ability to Modify model (see 1). In the Bar Design workflow, it is critical to remove excess material in this stage.
This is an example of a completed bar design that requires some modification.
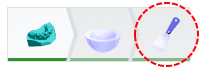
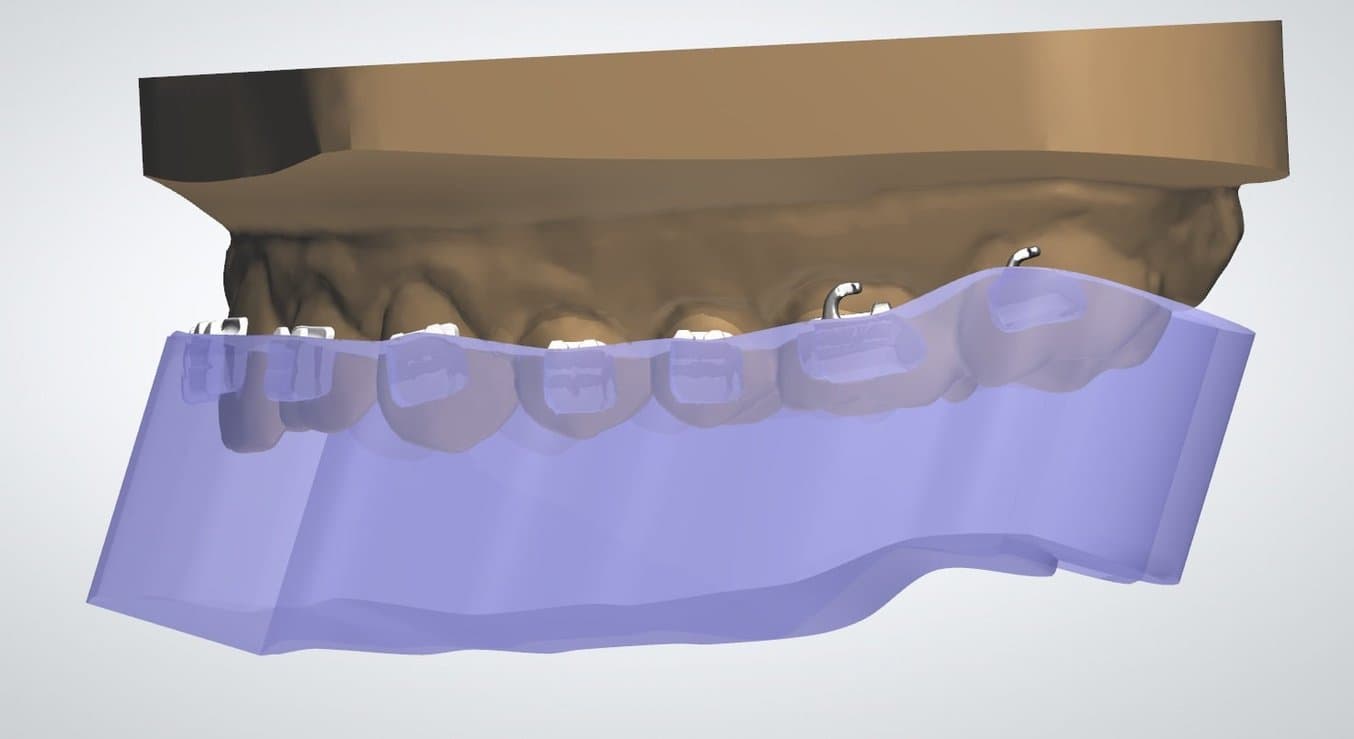
To start, orient the model so the occlusal surface is perpendicular to the viewing angle. This ensures that any plane cuts will leave an equal amount of material from the bottom surface of the appliance to the intaglio surface.
Click the Plane cut tool (see 2) and drag the mouse to cut any excess geometry.
You can check and edit the distance to the anatomy model by referencing or changing the Offset (see 3) value.
Note: Minimum material thickness is 1.0 mm.
After drawing the cut plane, be sure the green arrow is facing the side that needs to be cut away. Click Swap cut direction to change which side is removed (see 4).
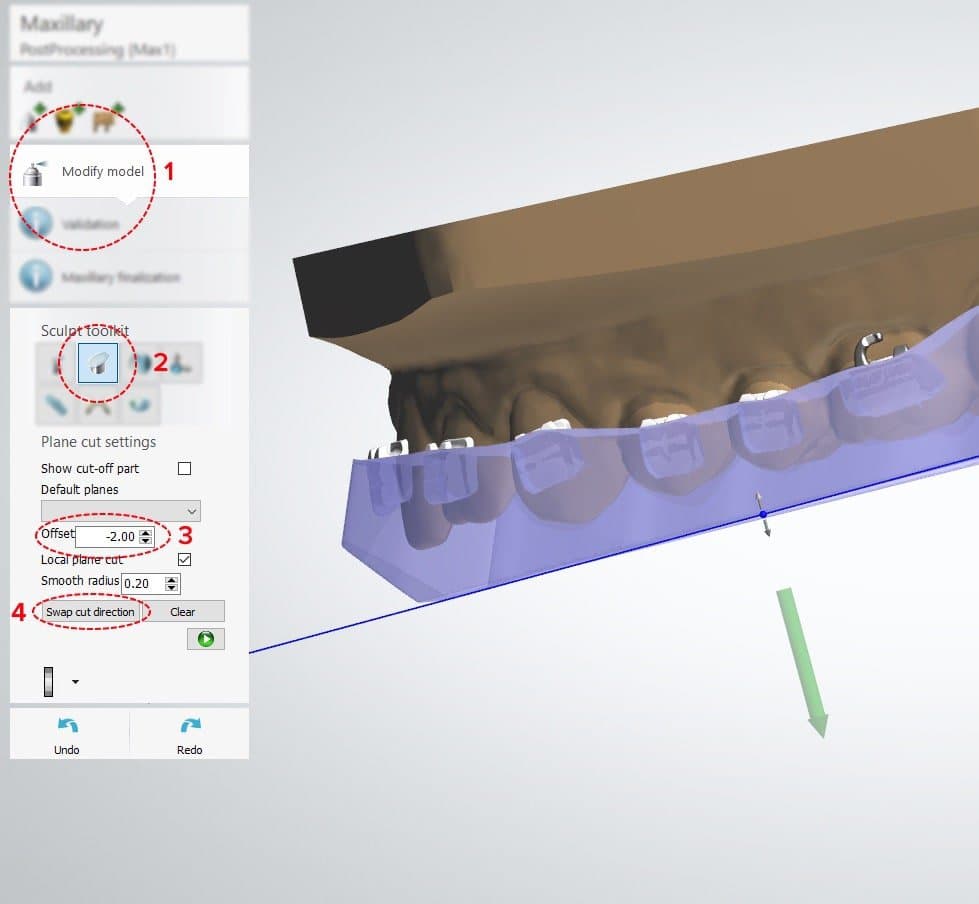
Plane cut 1 is optional, but provides a pry point once the part is printed.
Plane cut 2 is drawn parallel to the occlusal plane and creates a flat surface to 3D print the part efficiently.
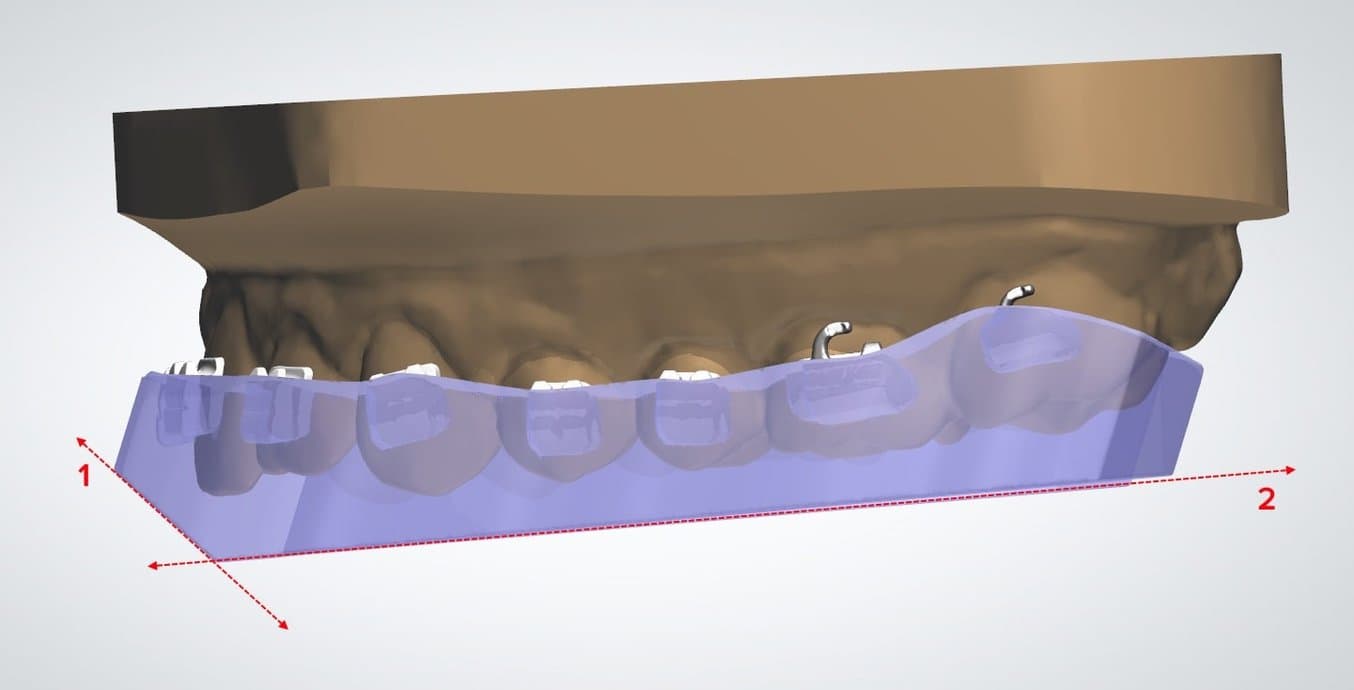
Design Settings and Offsets
2.1.7 Settings
Thickness | 2 mm |
Remove undercuts | Unchecked |
Use offset for inside surface | Unchecked |
Edges smoothing | None |
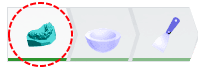
2.1.8 Containers
Inner surface offset | 0 mm |
Block-out angle | 0° |
Retention amount | 0 mm |
Prolongation length | 1 mm |
Brack slot block-out | Checked |
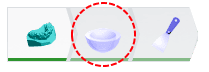
2.2 Export the STL File
Once the case has been designed to specification, manufacturing can begin. The majority of dental design software generates a manufacturing file in STL format. Locate the file and move it into the print preparation software, PreForm.
3. Print
Note
Use PreForm version 3.23 or higher and firmware 2.2.0 or higher.
3.1 Import the File(s)
Import or open the design file(s) by dragging them into PreForm, or use the File menu to locate them on your computer or network.
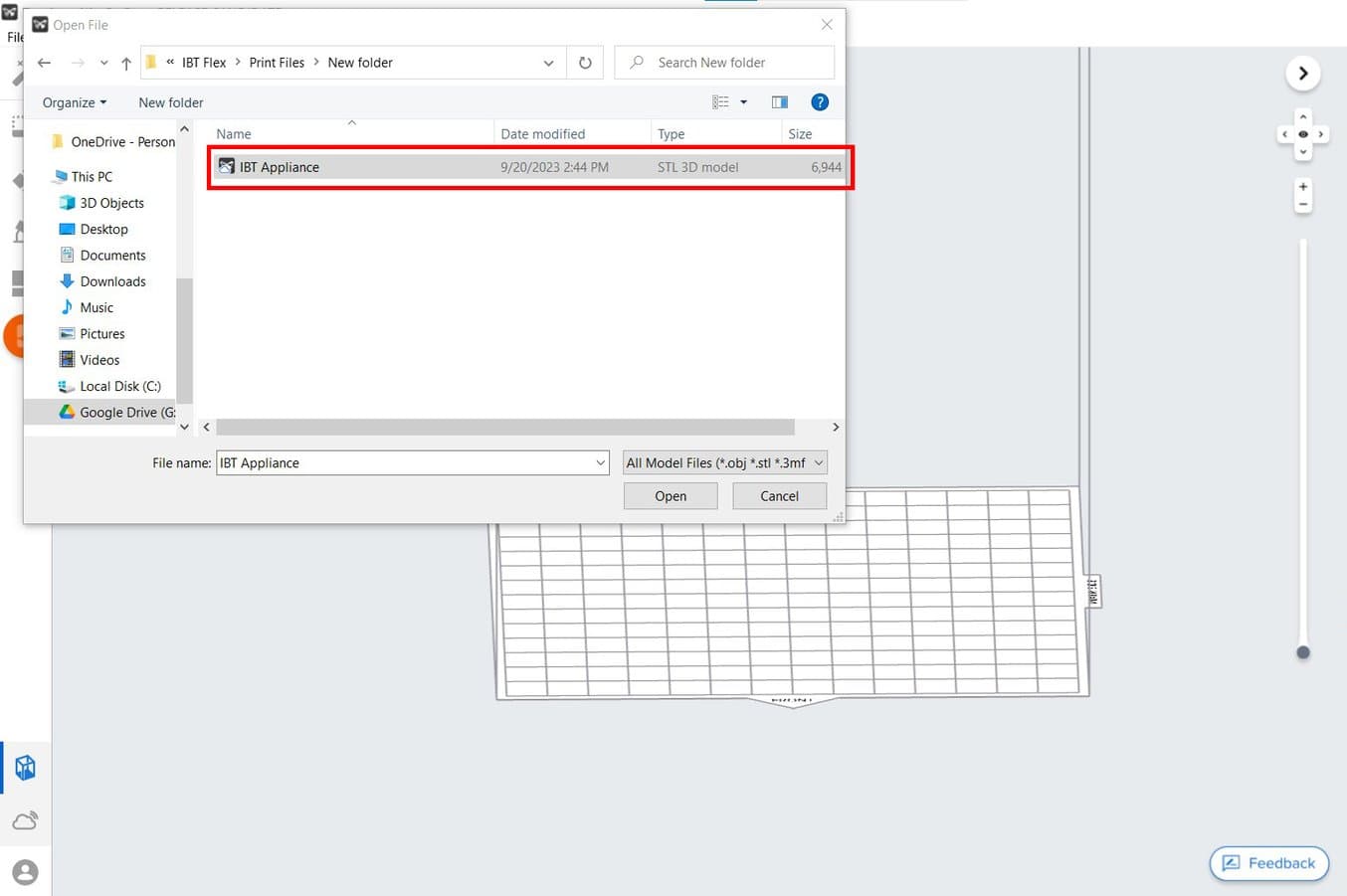
3.2 Material and Layer Height Selection
Select the material for printing by clicking the printer box in the Job Setup menu on the right hand side.
Locate and select IBT Flex in the material selector.
IBT Flex can be printed with default printing in 100 micron layer height. If you are using IBT Flex for restorative purposes it can also be printed in 50 microns. Printing indirect bonding trays in 50 microns may extend print time.
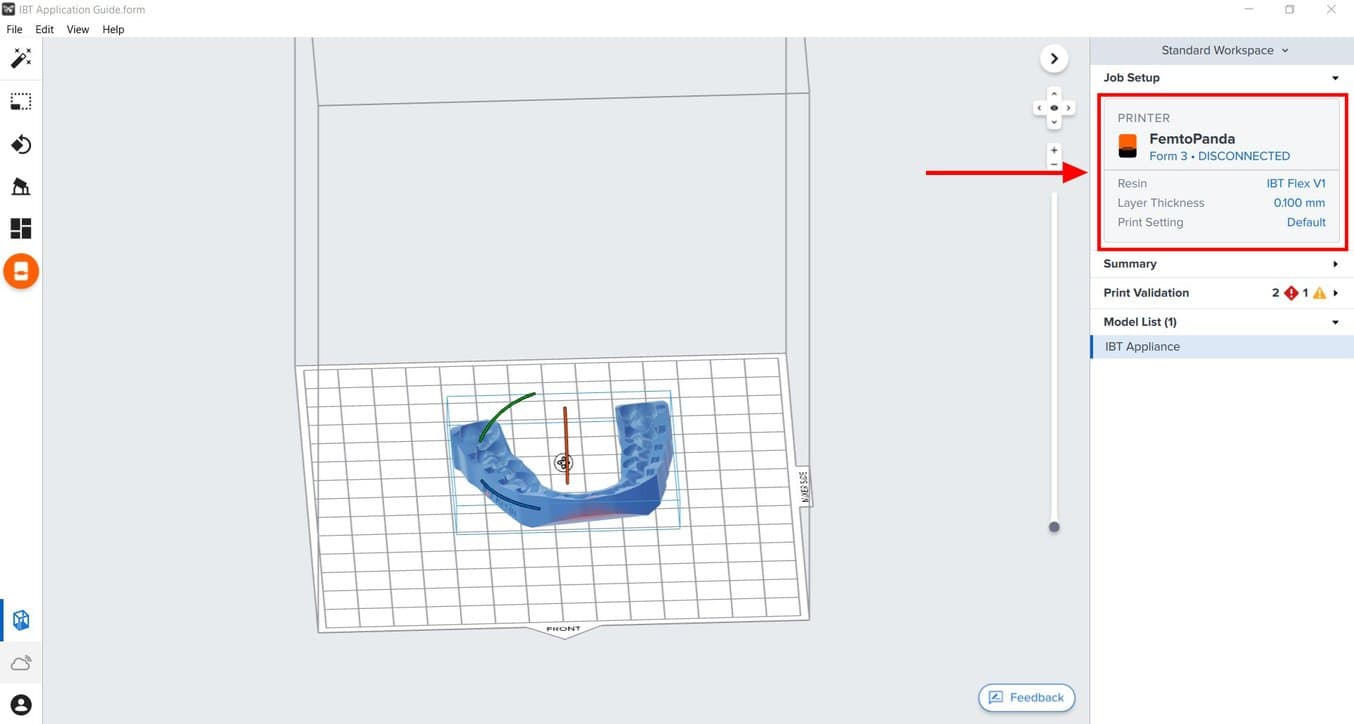
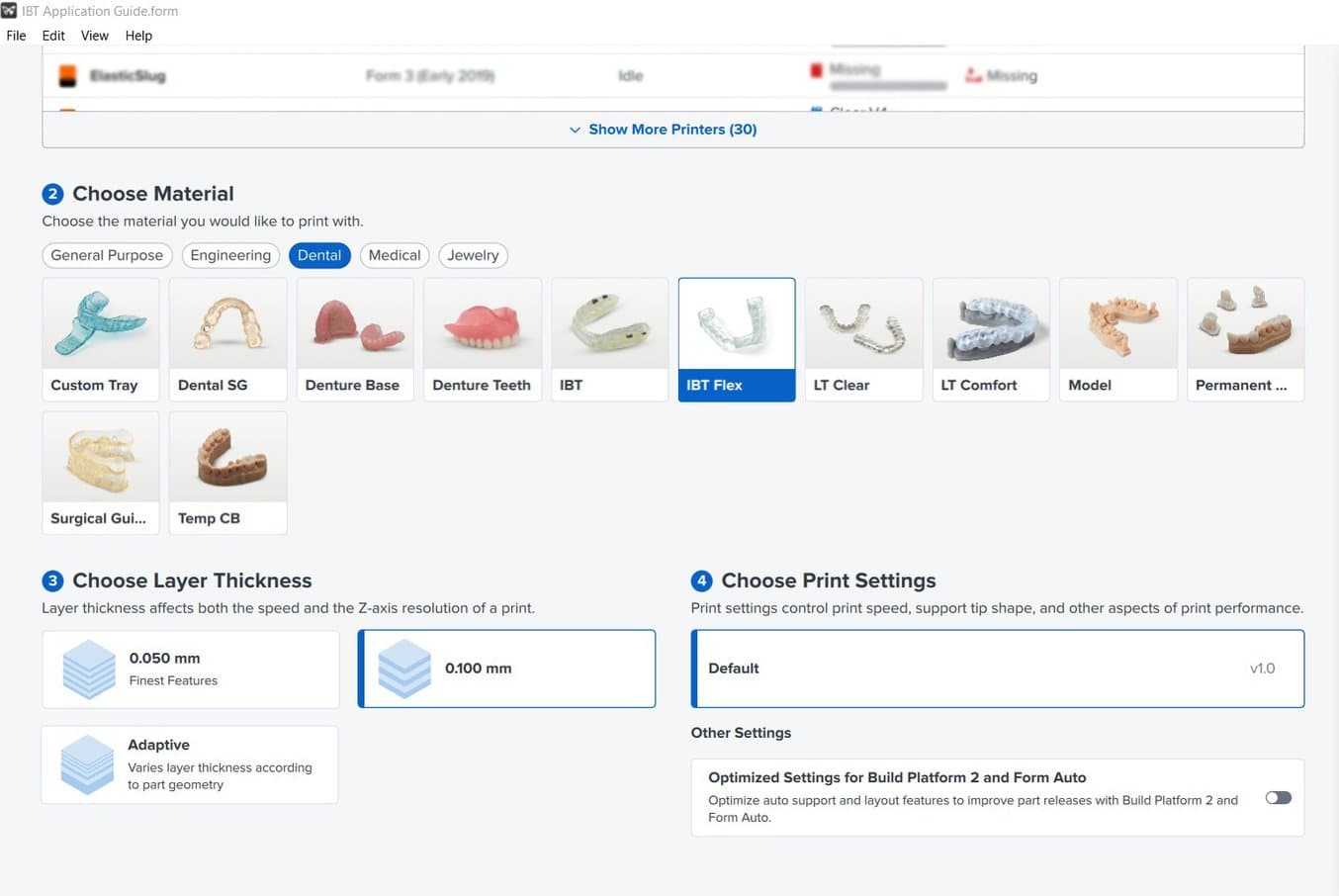
3.3 Orientation
3.3.1 Positioning Bar Type Appliances
If you designed the appliance using the bar technique, you can adhere the bottom surface directly to the build platform.
Open the Orientation tool (see 1) and click the Select Base... (see 2) button.
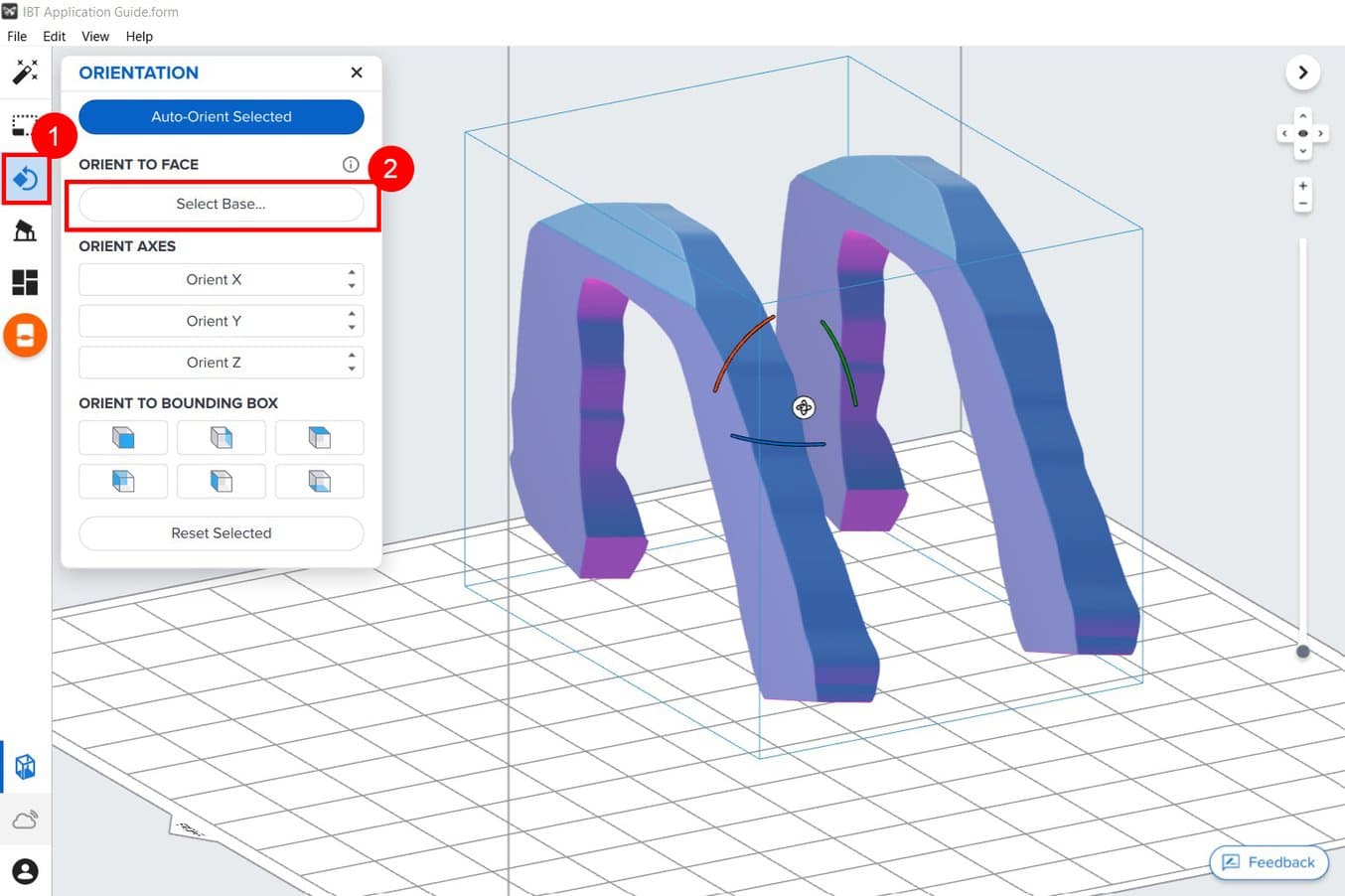
Next, click the bottom surface of the part to adhere it to the build platform.
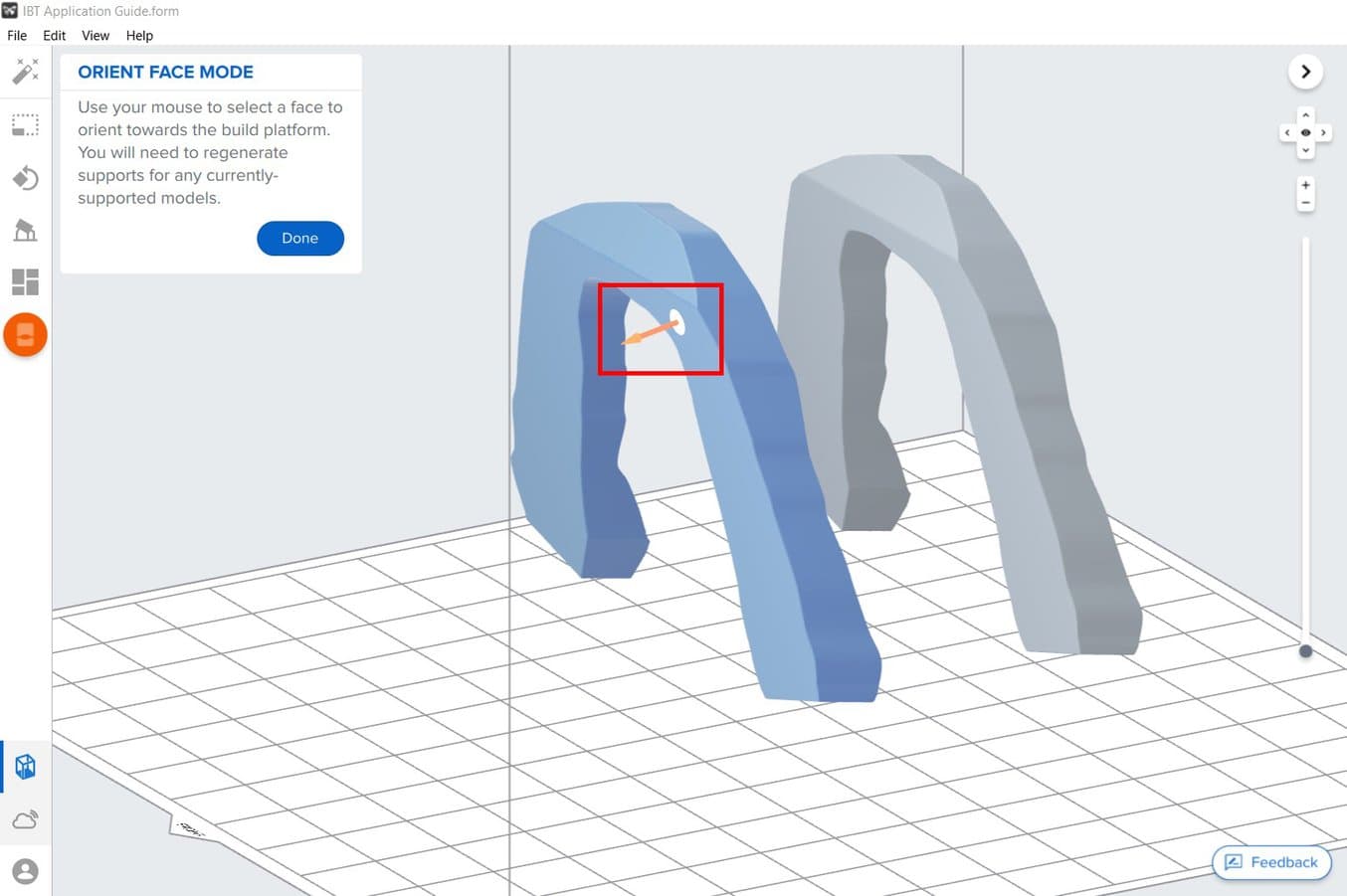
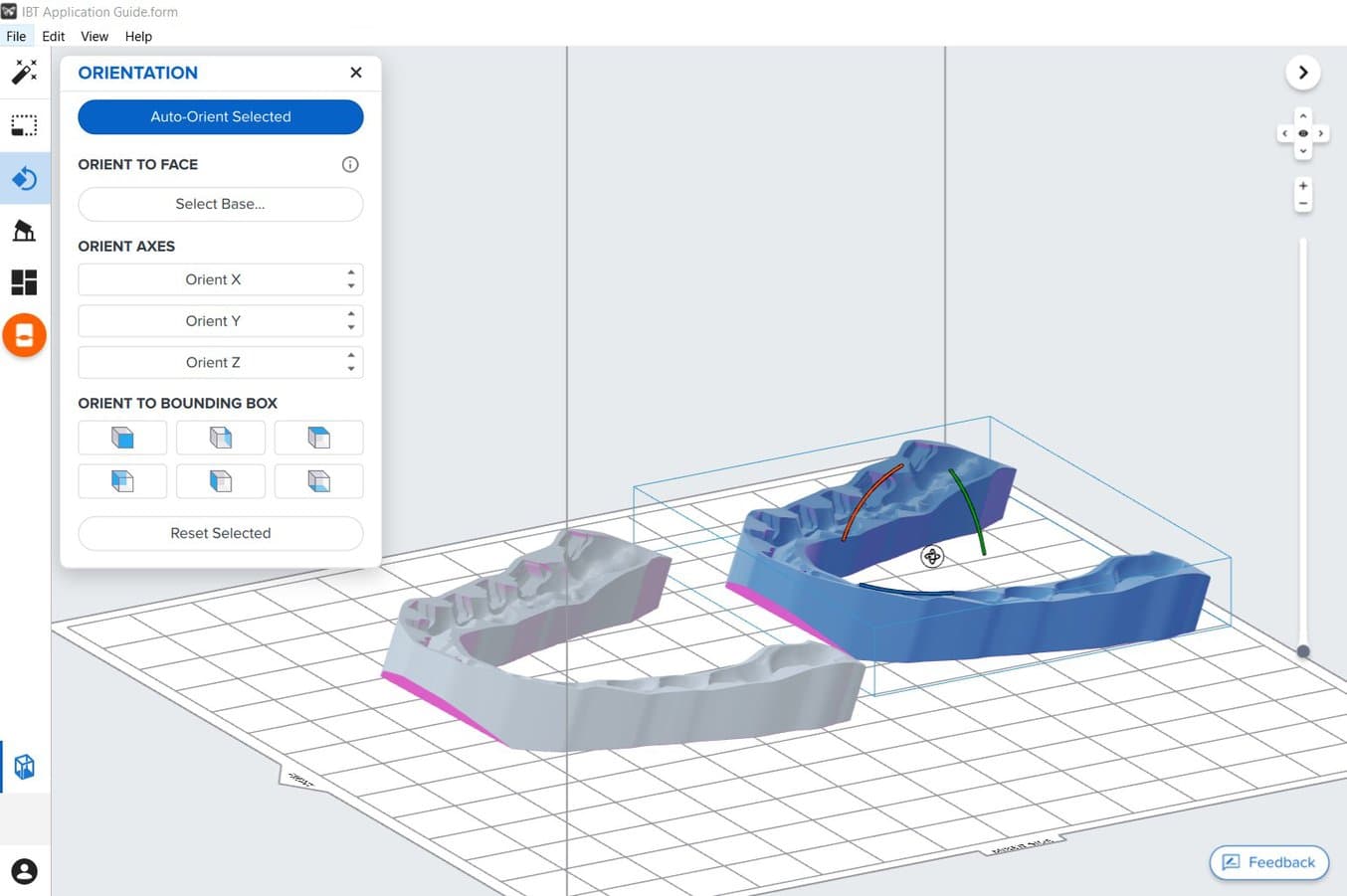
3.3.2 Positioning Offset Type Appliances
To rotate a part into the correct position, with the part selected, click and drag the sphere manipulator.
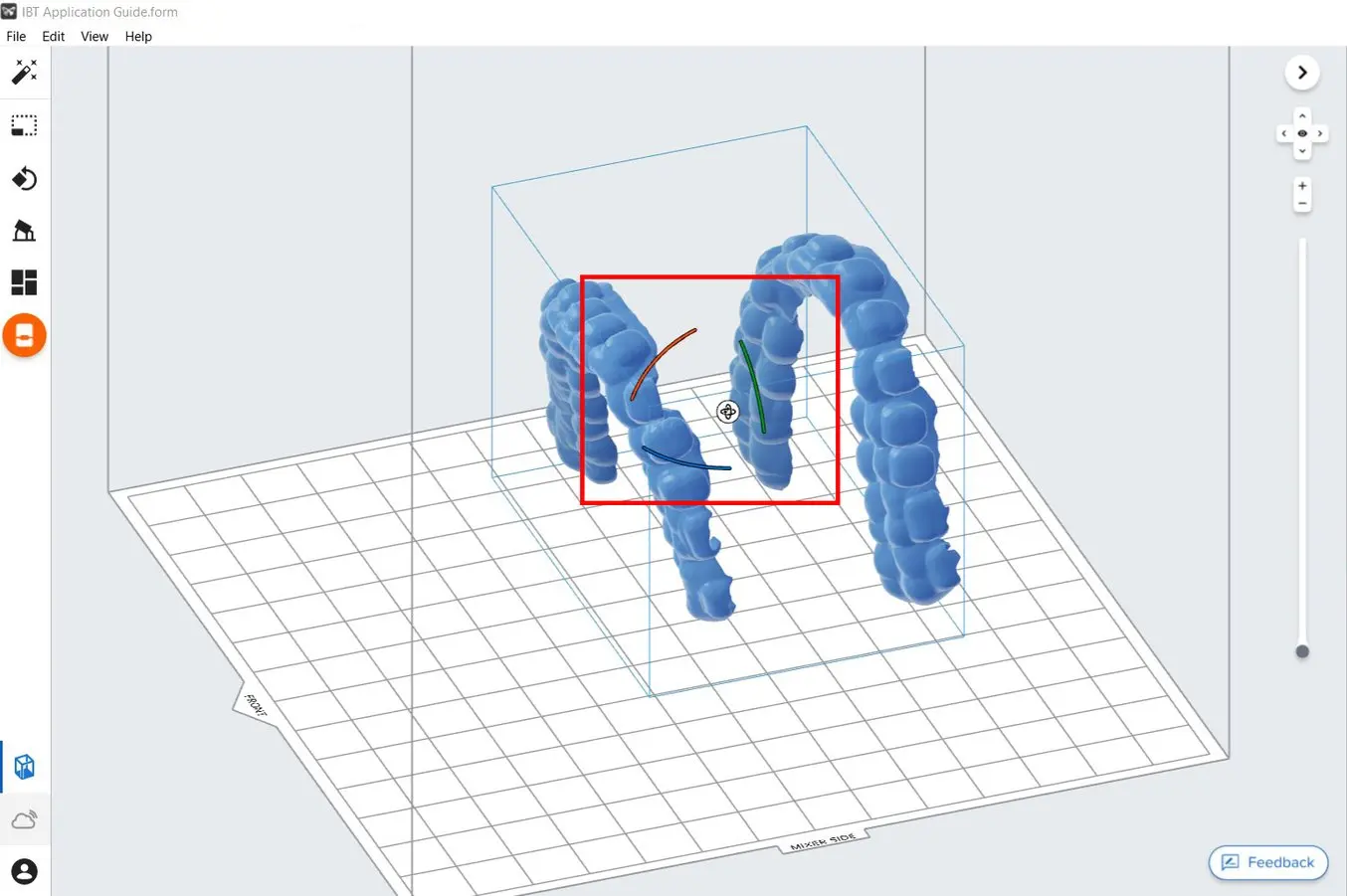
Another option is to open the Orientation tool (see 1) and hover over the surface icons under the Orient To Bounding Box (see 2) section to find the bottom or occlusal surface of the part.
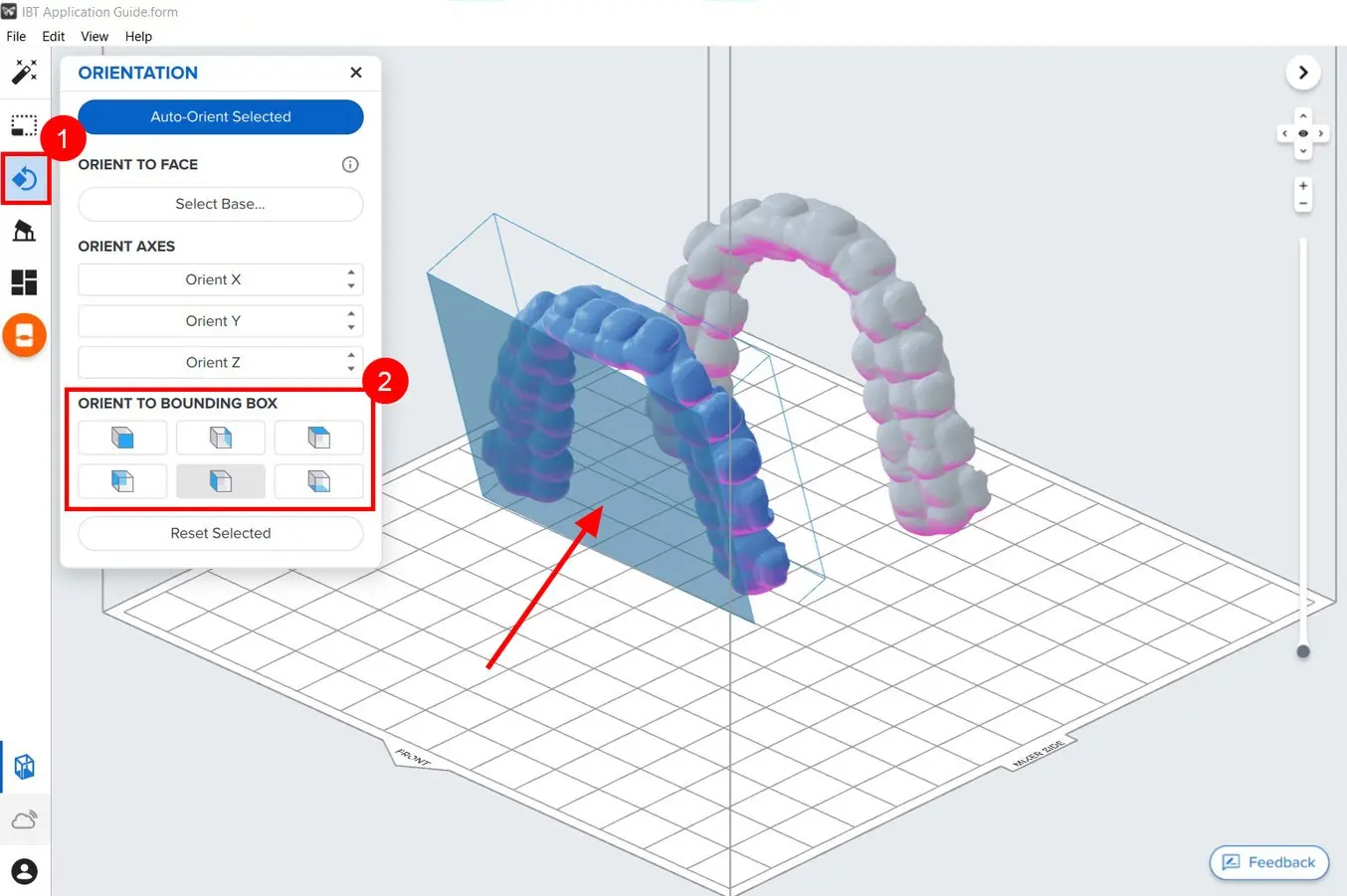
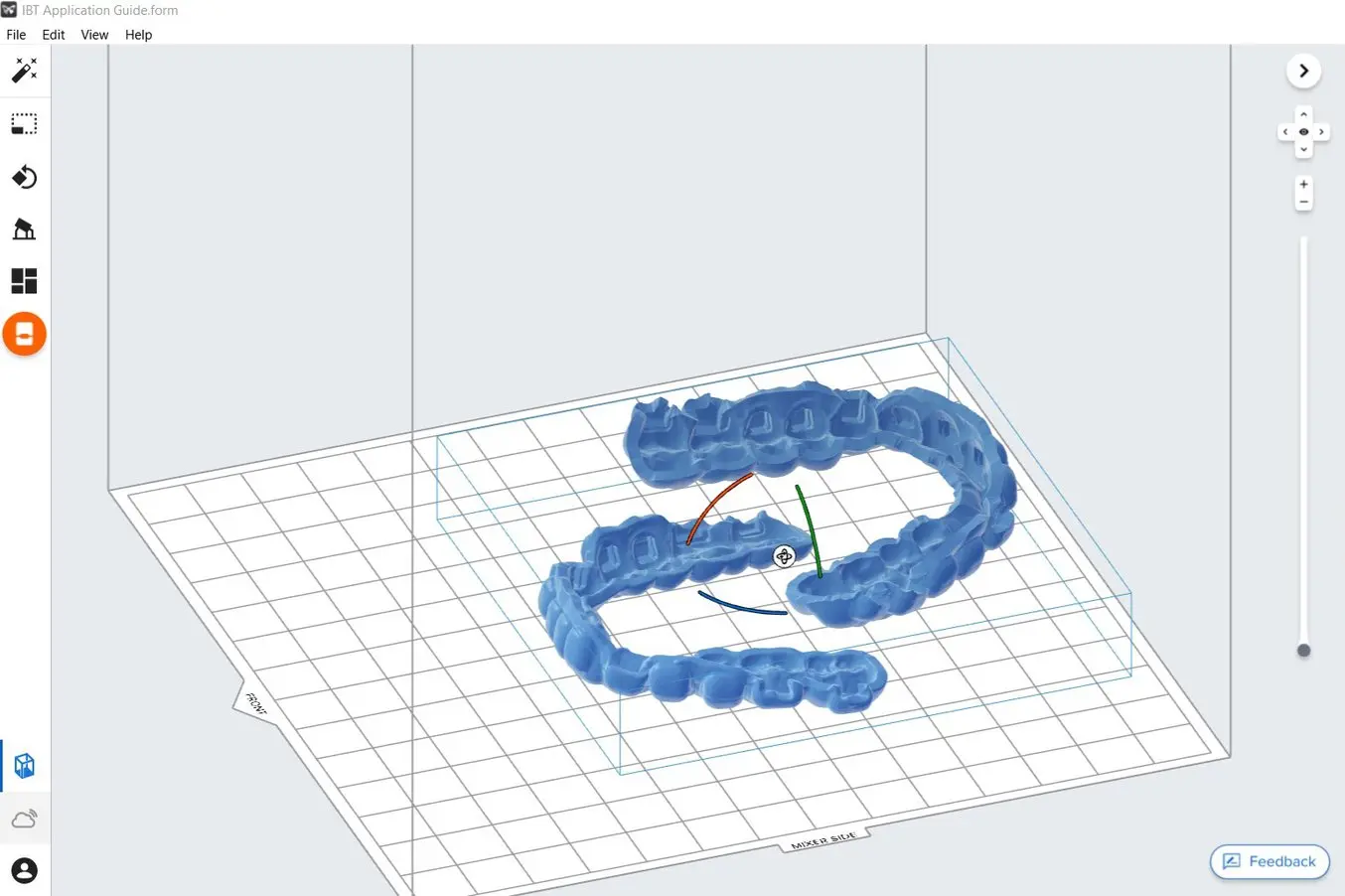
3.3.3 Angulation
Proper part orientation ensures part accuracy and fitment.
Always position the appliance with the intaglio surface facing away from the build platform. The part should be parallel to the build platform or, at most, a 40-degree angle, with the anterior section toward the build platform.
Note: Printing times vary depending on object orientation and job setup.
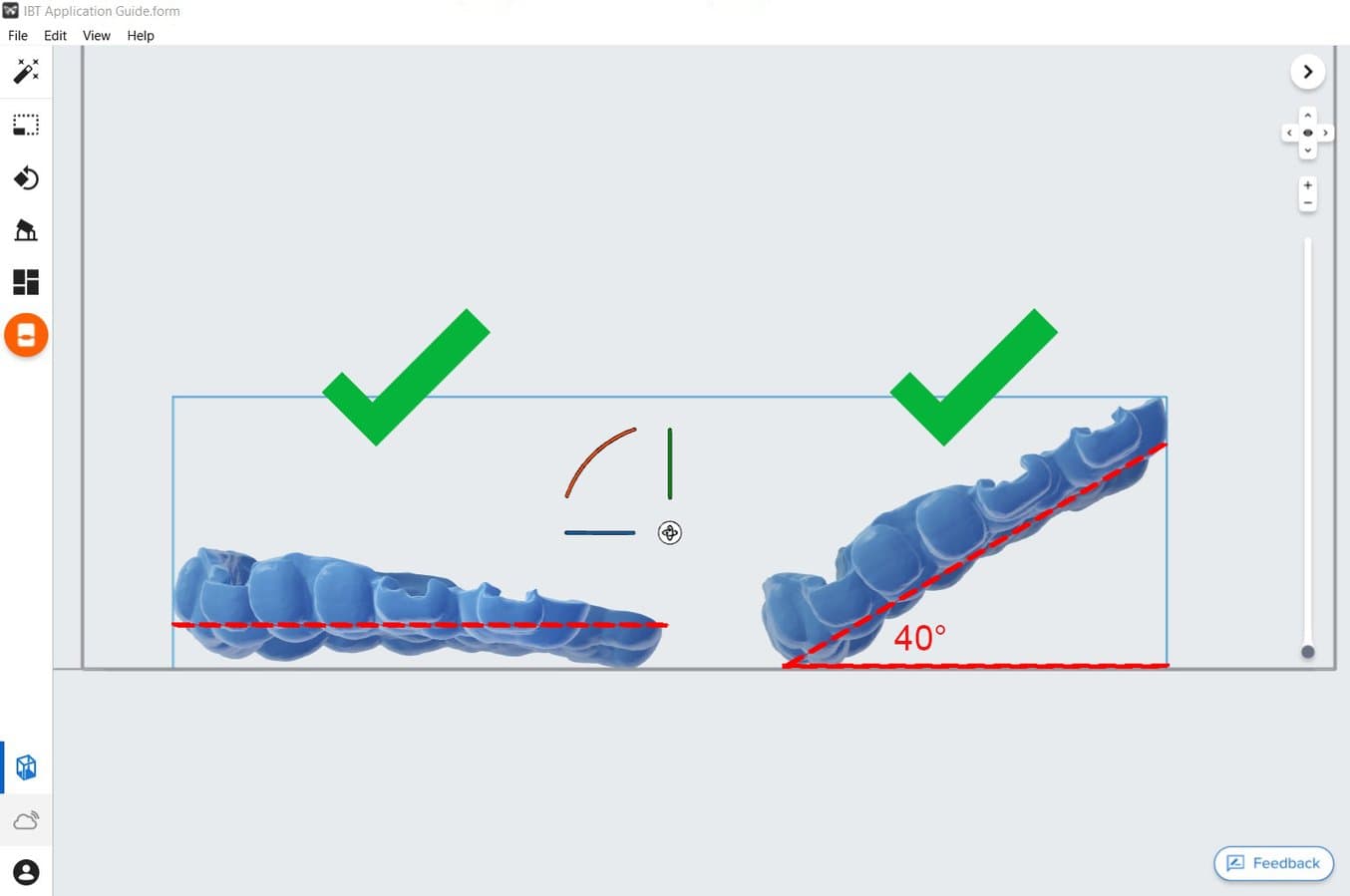
3.4 Generate Support Structures
Depending on the overhanging surfaces, it is possible to print bar type appliances that are adhered to the build platform without any support structures.
3.4.1 Automatic Support Generation
For cases where supports are needed, open the Supports tool on the left side of PreForm and click the Auto-Generate Selected or Auto-Generate All button.
If adding supports to a bar type design that should be printed directly to the build platform, change the Raft Type to None in the Supports tool.
Note: Uncheck the Internal Supports button to prevent generation of unnecessary support structures.
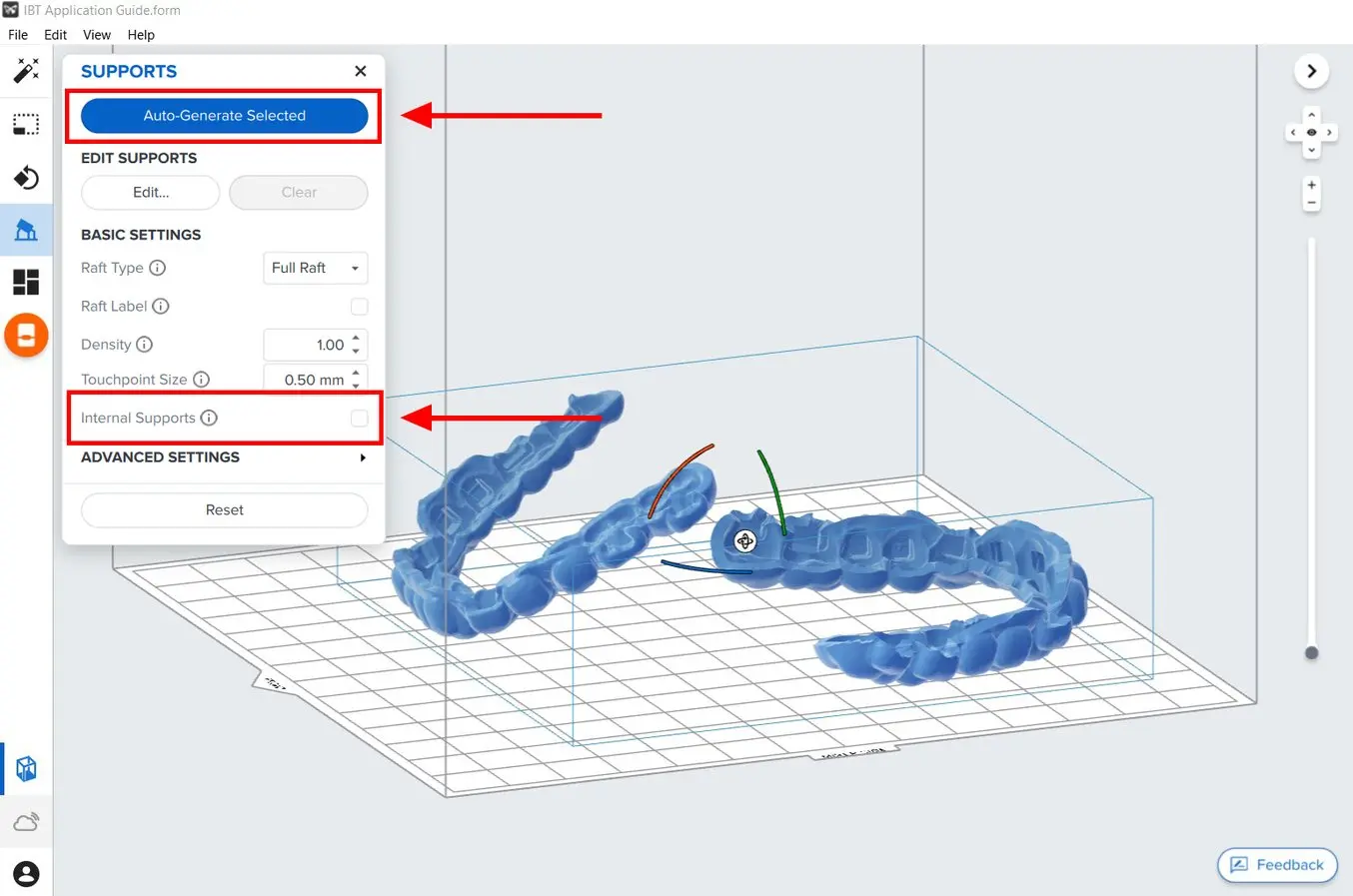
3.4.2 Manual Support Editing
Once supports are generated, verify their locations. If a support point is not in an ideal location, you can edit their location by clicking the Edit… button in the Supports menu.
Note: With internal supports turned off and correct orientation, there is typically no need to edit supports.
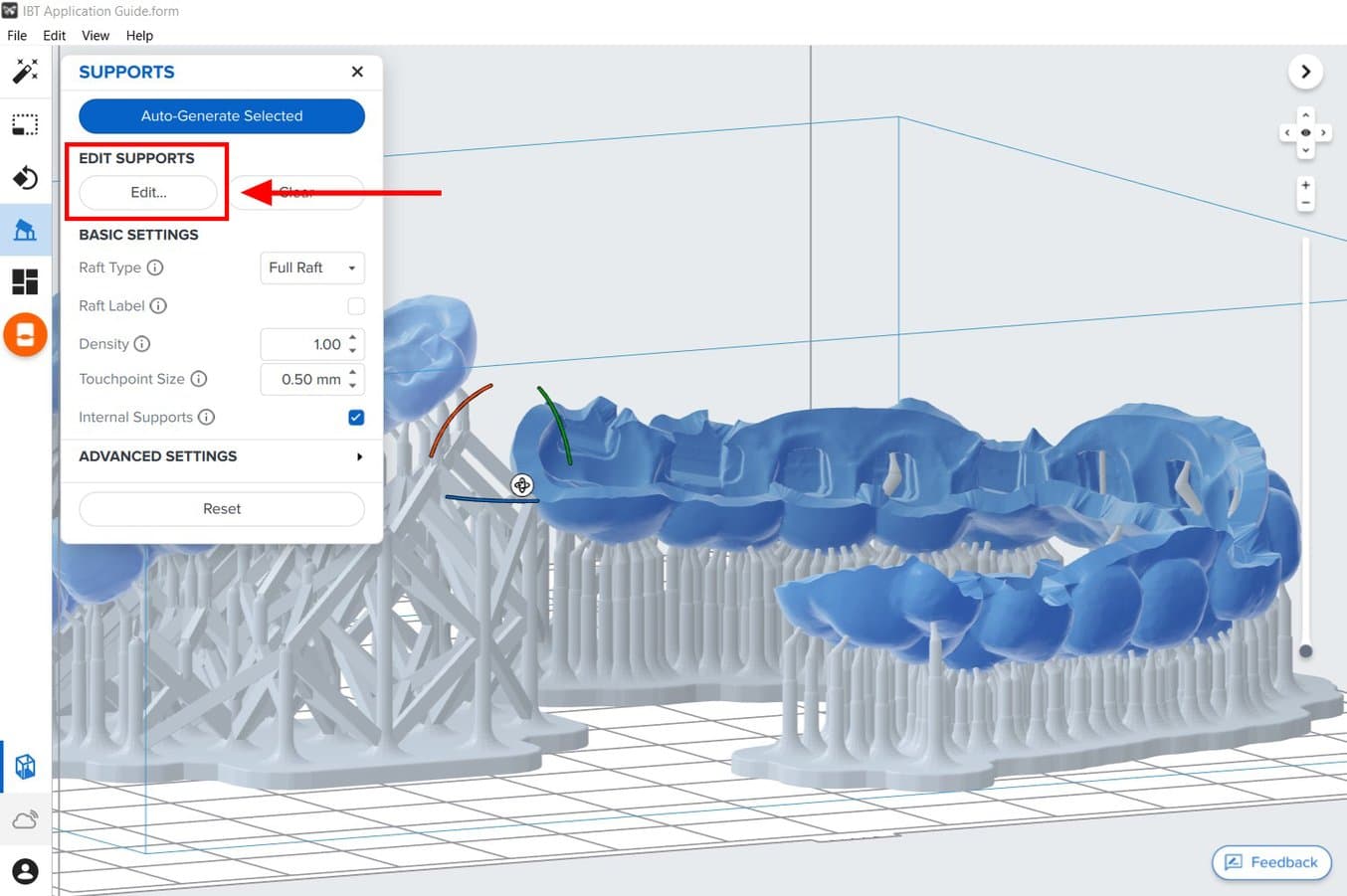
Click on a support touchpoint sphere to remove it and click on areas without supports to add touchpoints.
PreForm will indicate in red which areas might require additional support.
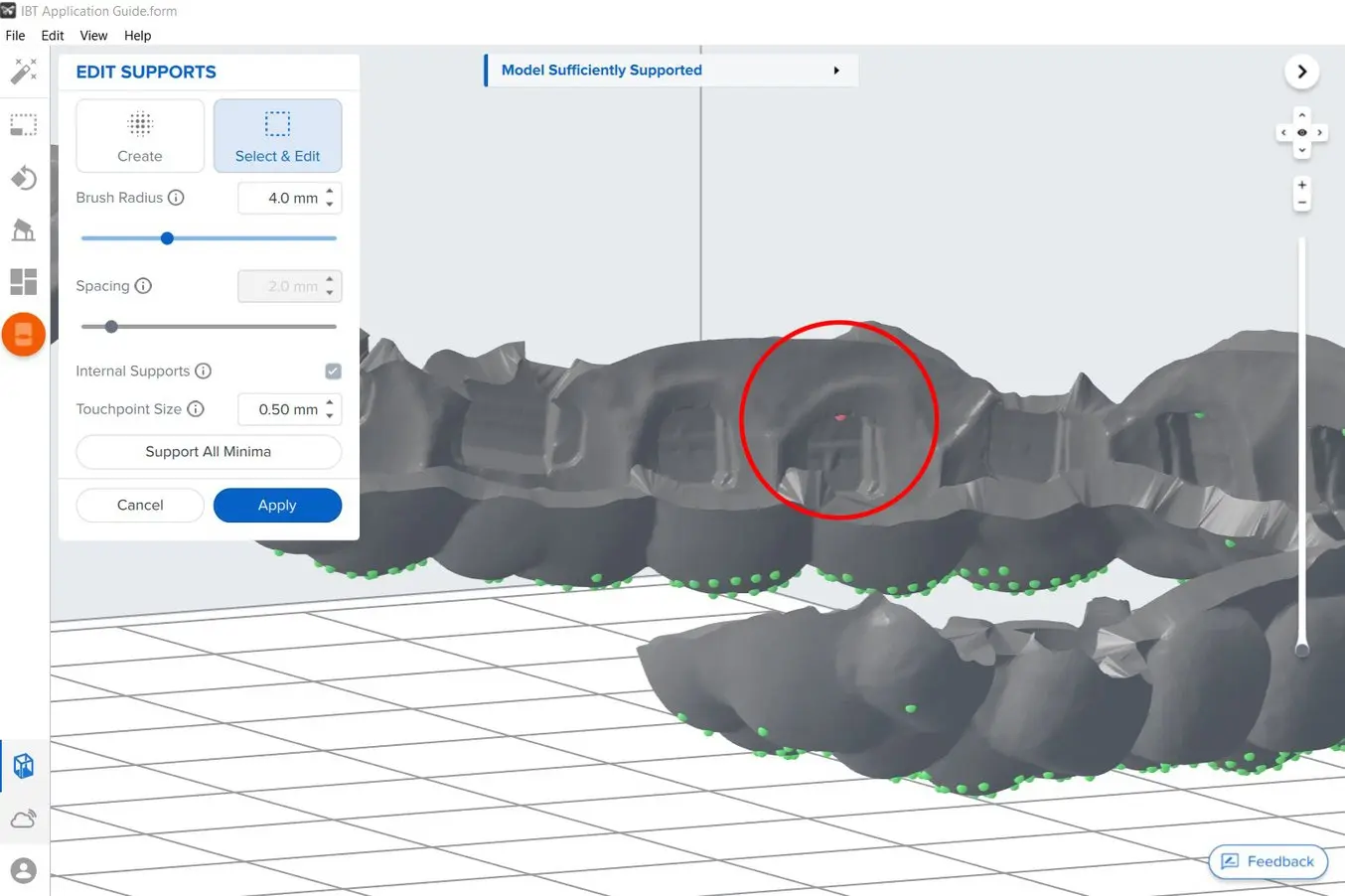
Confirm under the Job Setup menu bar on the right side of the screen that Print Validation shows a green thumbs-up.
When printing parts directly on the build platform, you will see a printability warning. If the part is snapped down to the build platform as outlined in the above section, it is okay to ignore this error.
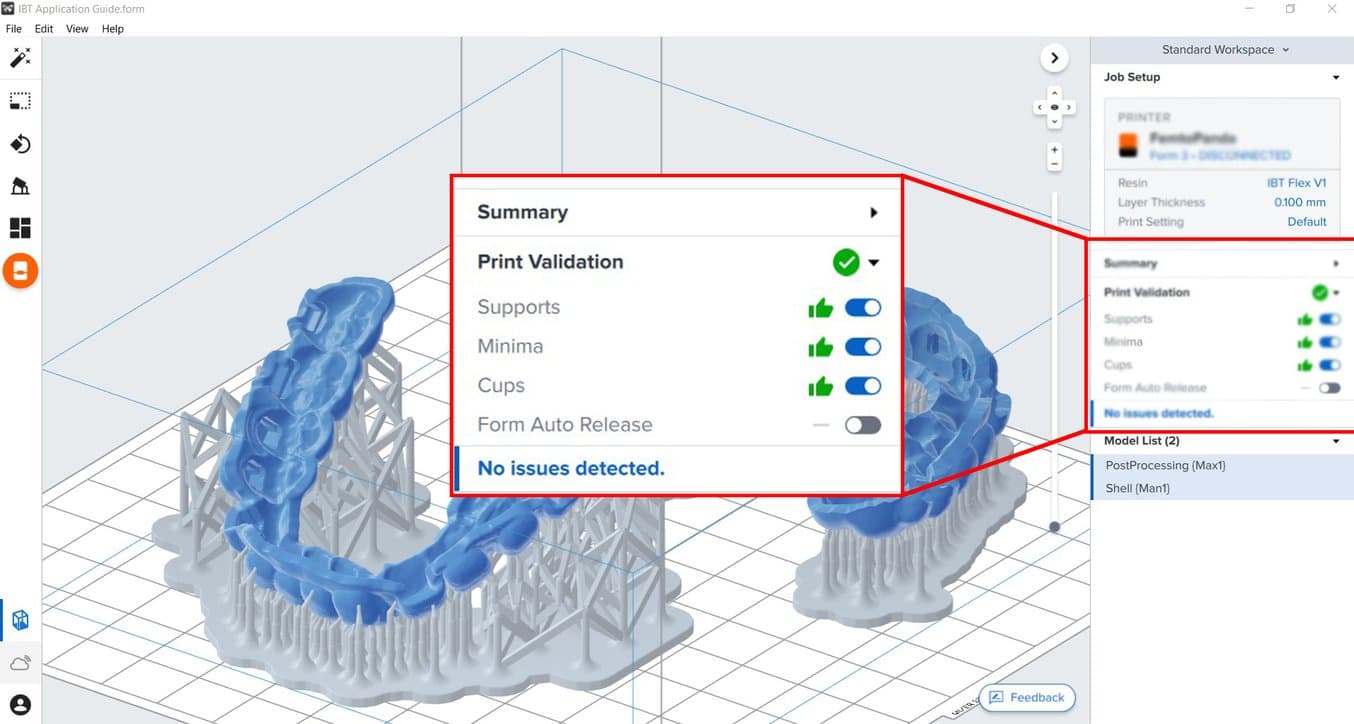
3.5 Printing Layout
Whether you are printing on support structures or directly on the build platform, position the parts so they are not overlapping each other. Overlapping parts will be outlined in red.
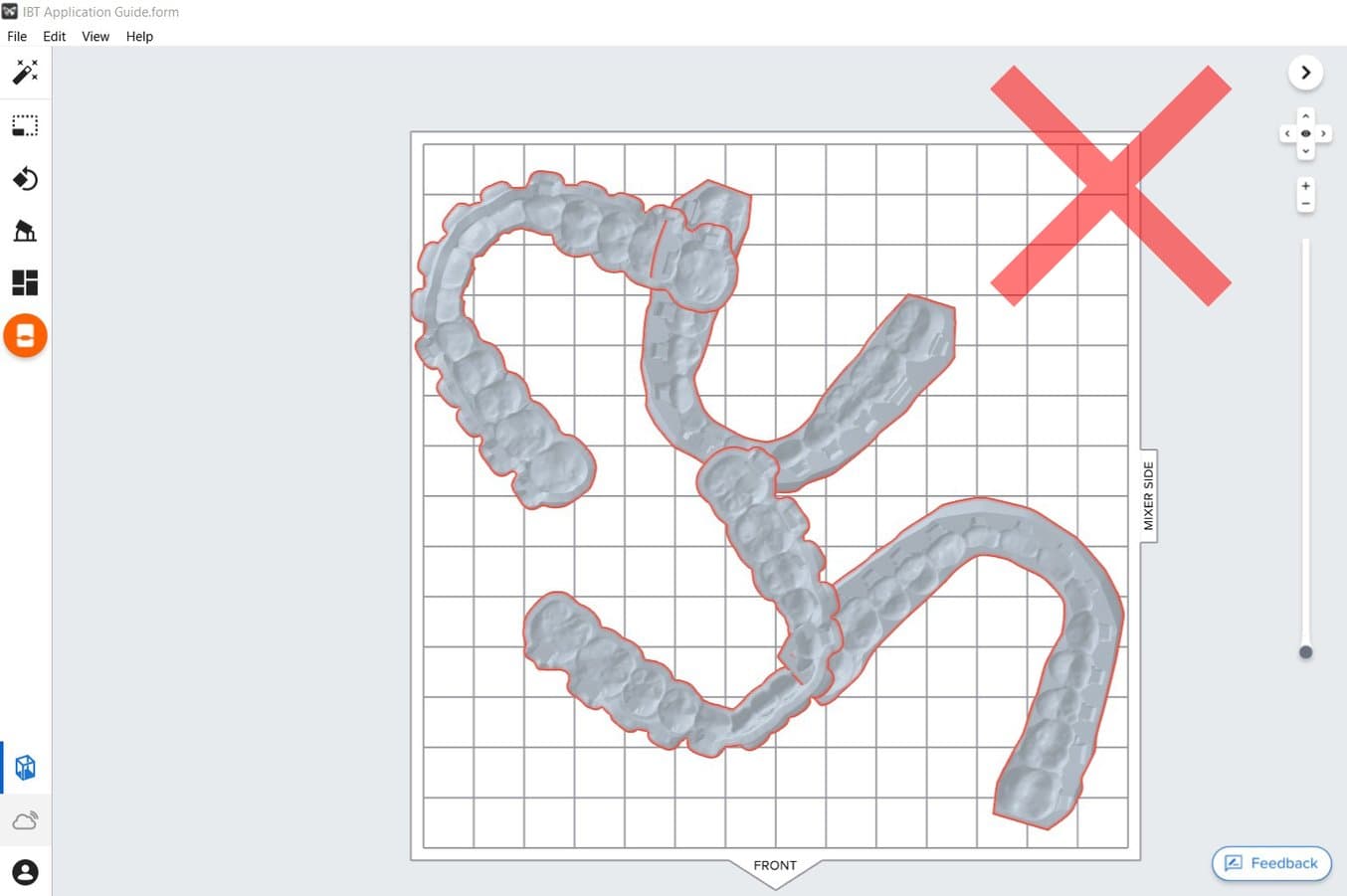
To rotate the part while it is selected, click-and-drag the outer edge of the orientation sphere.
To move the part, click-and-drag anywhere on the part.
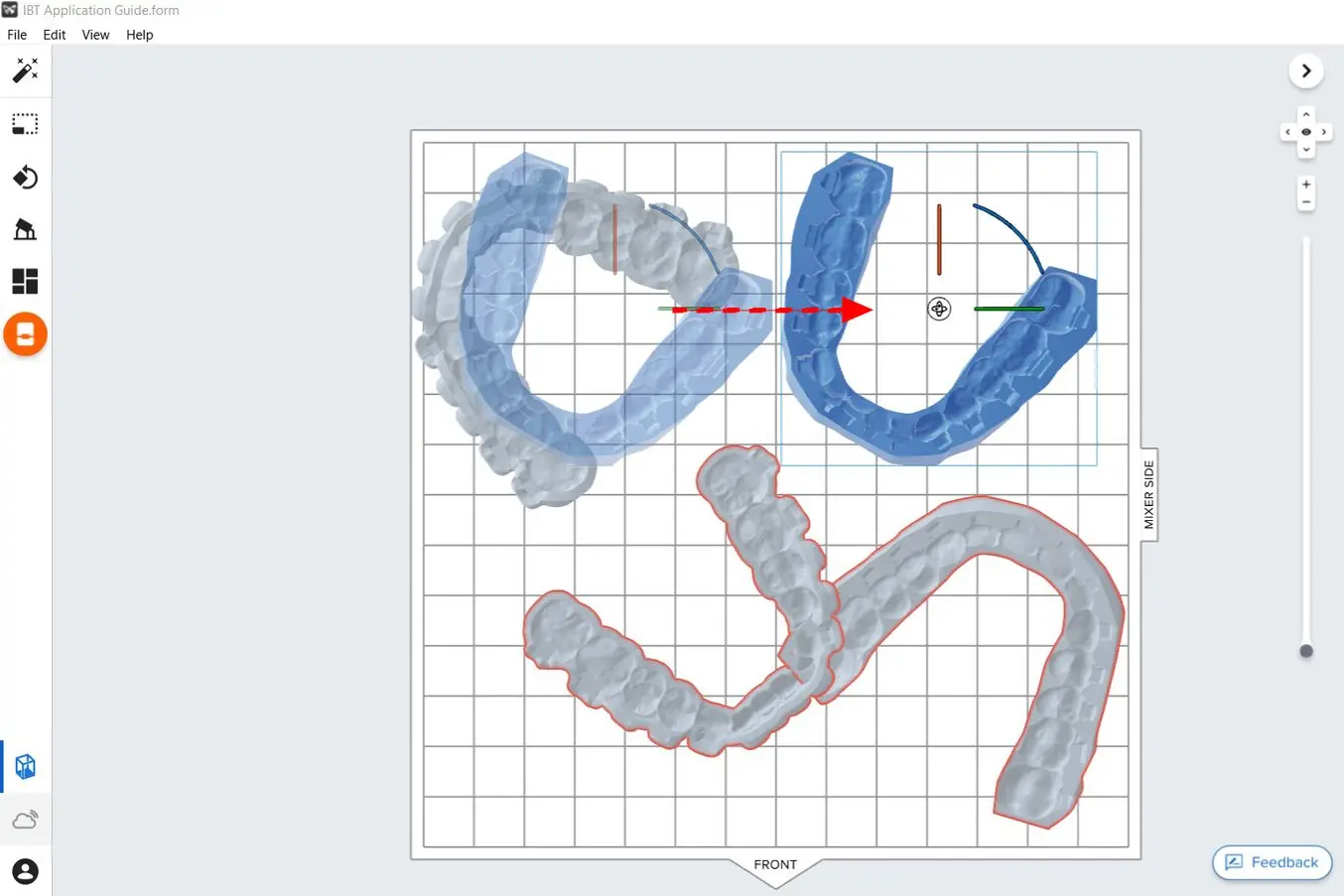
Another option is to use the Auto-Layout tool. Select all parts on the Build Platform and select Layout All.
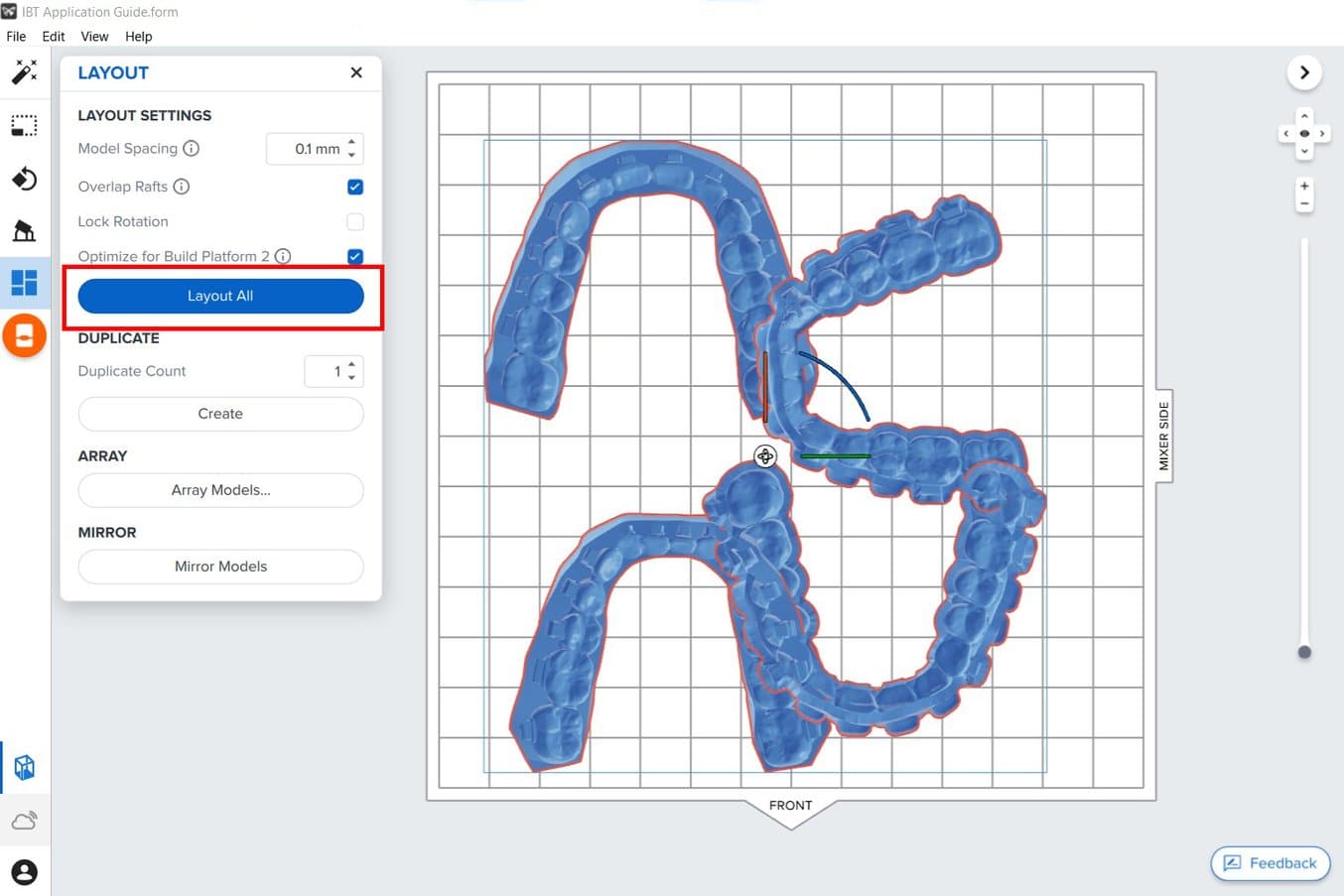
Note: Overlapping the support raft is okay.
Once the layout is complete, the job is ready to send to the printer.
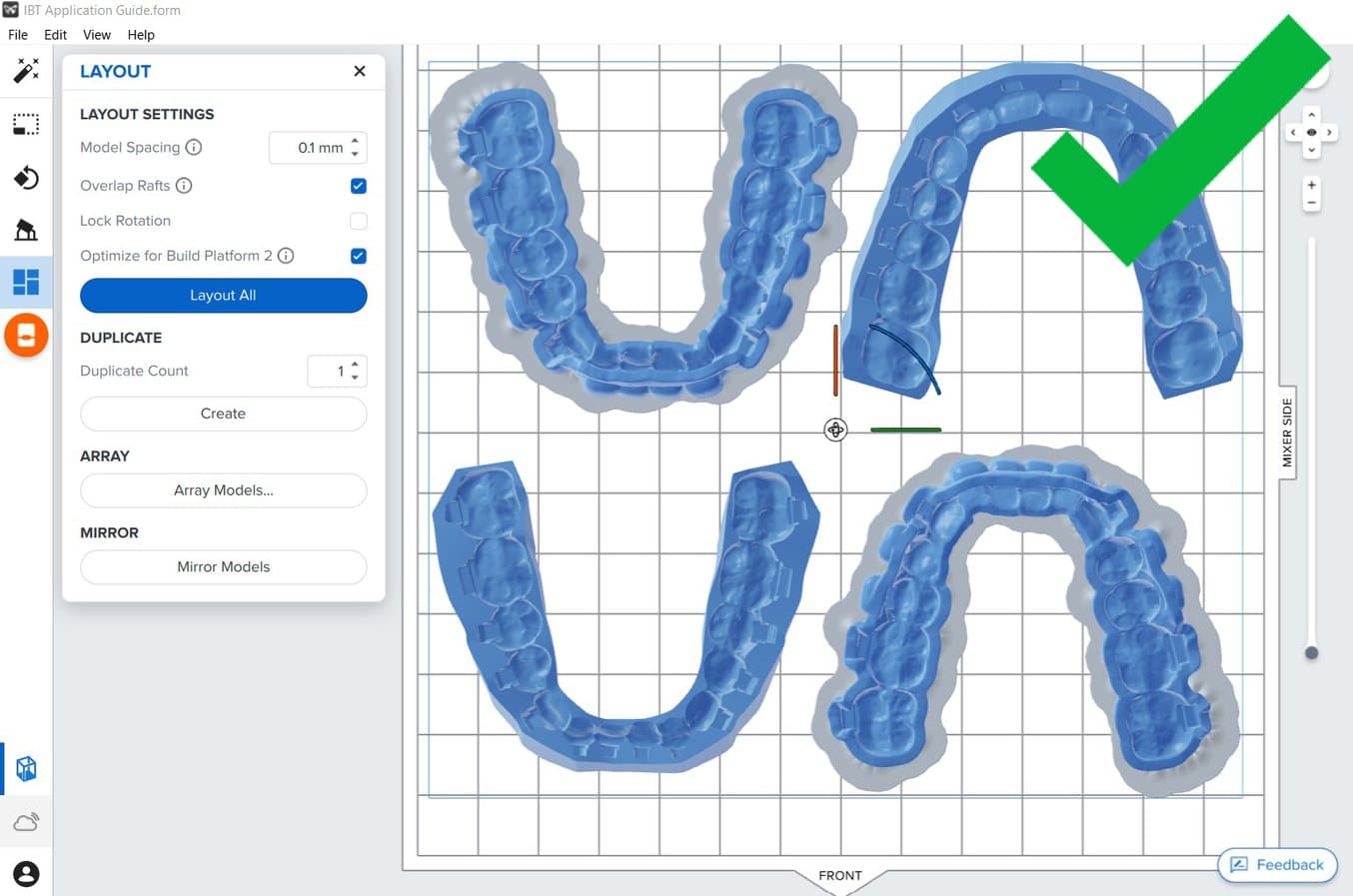
3.6 Transferring Job to the Printer
Send the job to the printer by clicking the orange printer icon on the left side of the screen.
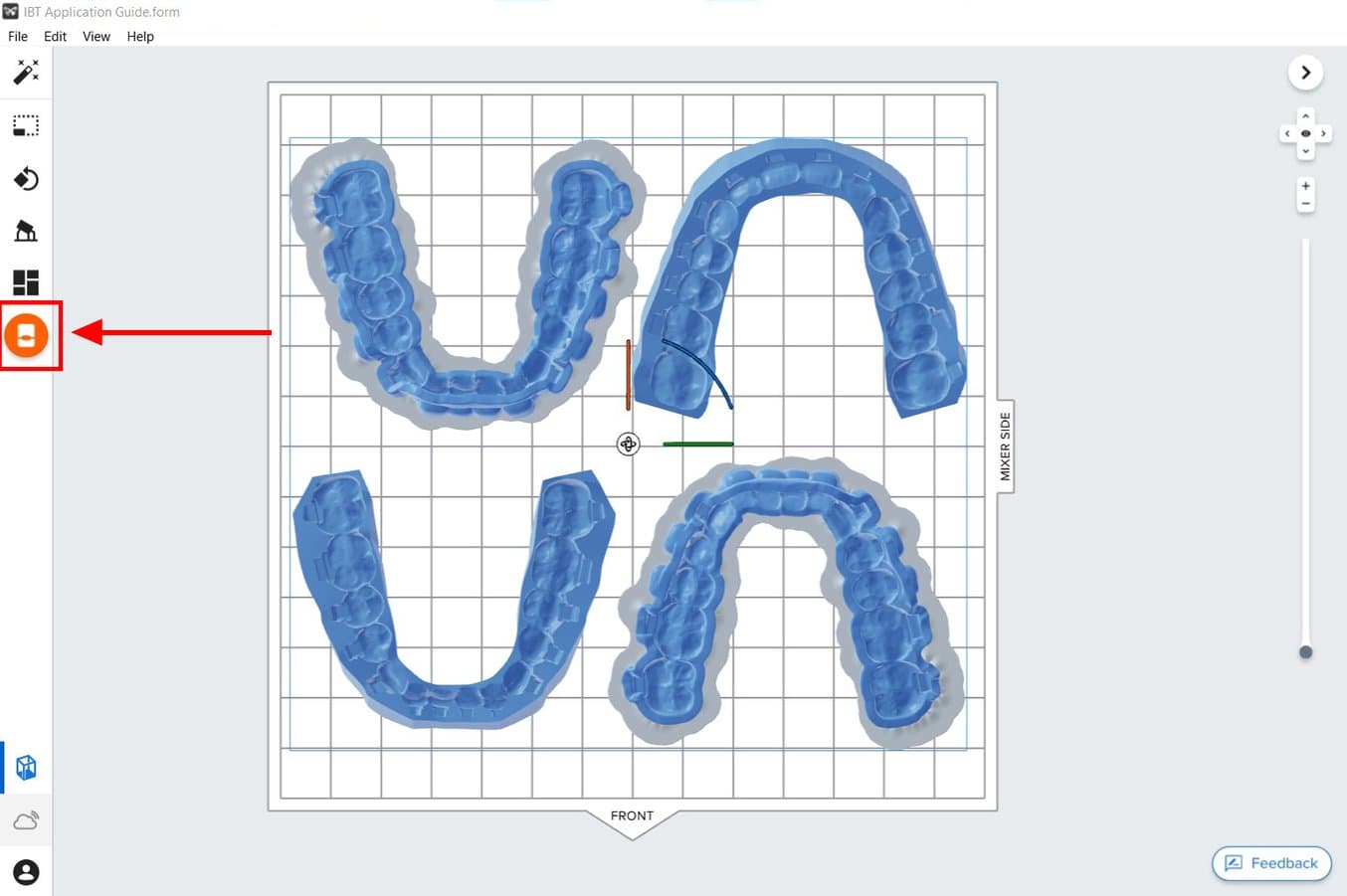
The Print dialog box will open. Here you can change the Printer the job is being sent to, rename the job, and send the job to the printer using the Upload Job button.
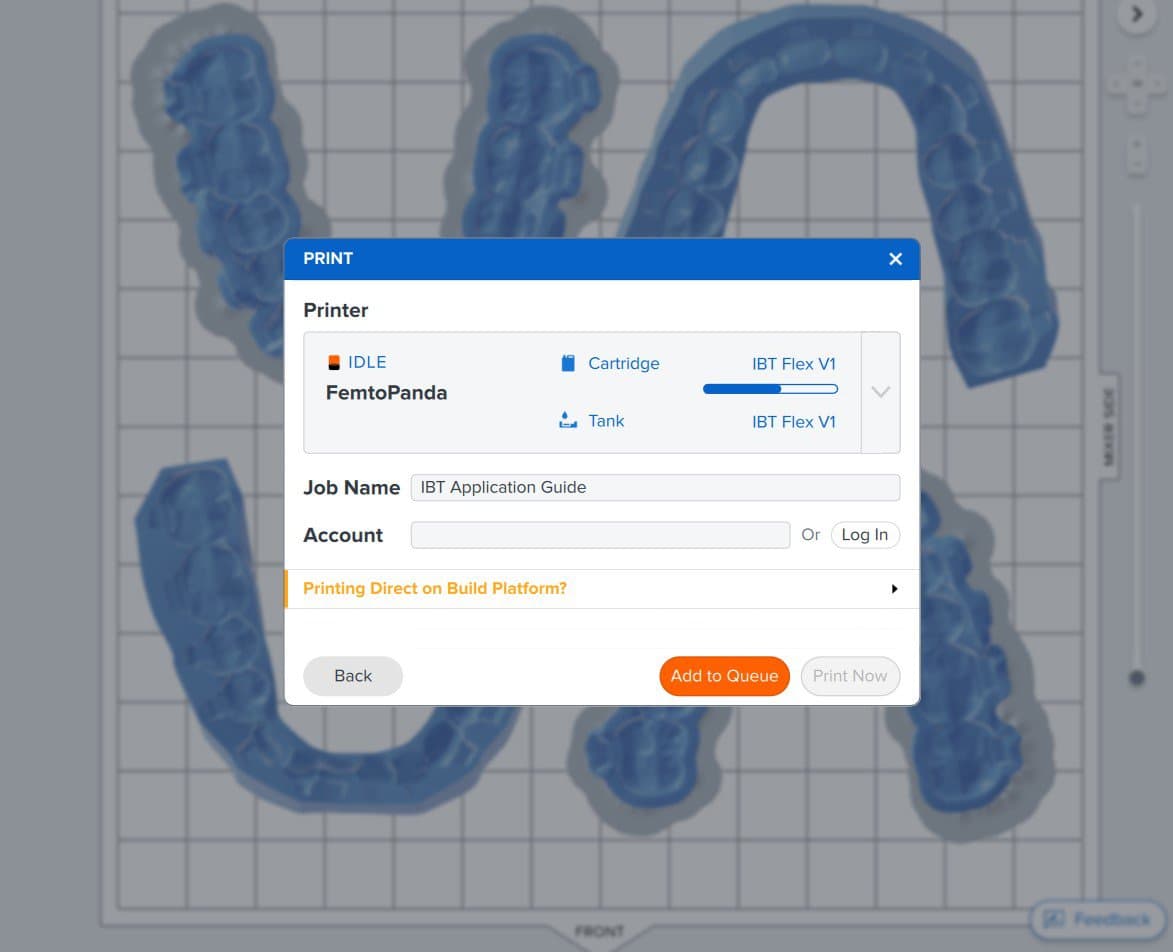
3.7 Set up the Printer
Shake the IBT Flex Resin cartridge and then insert the cartridge, a build platform, and a compatible resin tank into the Formlabs 3D printer.
- Begin printing by selecting the print job from the printer’s touchscreen.
- Follow any prompts or dialogs shown on the printer screen.
- The printer will automatically complete the print.
If starting with an empty resin tank, save time by manually pre-filling the tank by pouring in resin directly from the cartridge.
Note: Please verify printer and resin compatibility on the Formlabs support site before printing.
Note
For full compliance and biocompatibility, IBT Flex Resin requires a dedicated resin tank, build platform, Form Wash, and Finish Kit, which should not be mixed with any other resins.
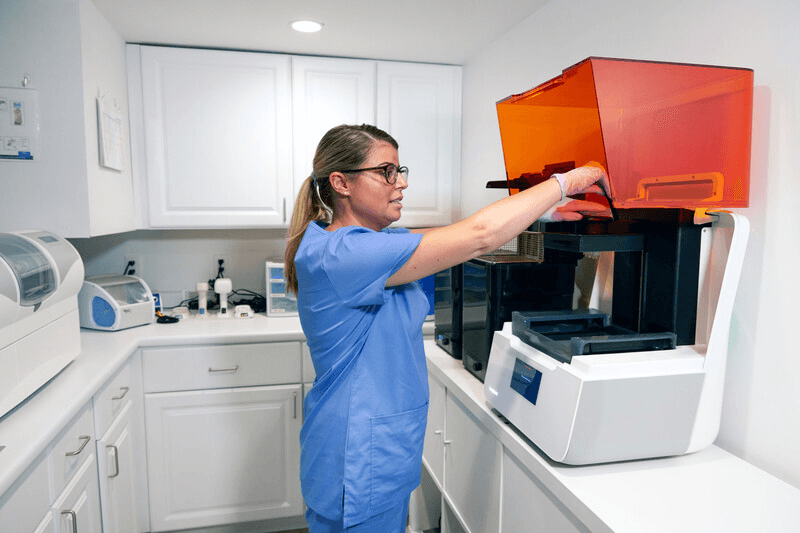
4. Post-Processing
Always use gloves when handling uncured resin and parts.
4.1 Part Removal
Remove printed parts from the build platform by wedging the part removal or scraping tool under the part raft and rotating the tool.
Note: Due to the flexibility of parts printed with IBT Flex Resin, they might not be released as easily as other more rigid materials when using the Build Platform 2.
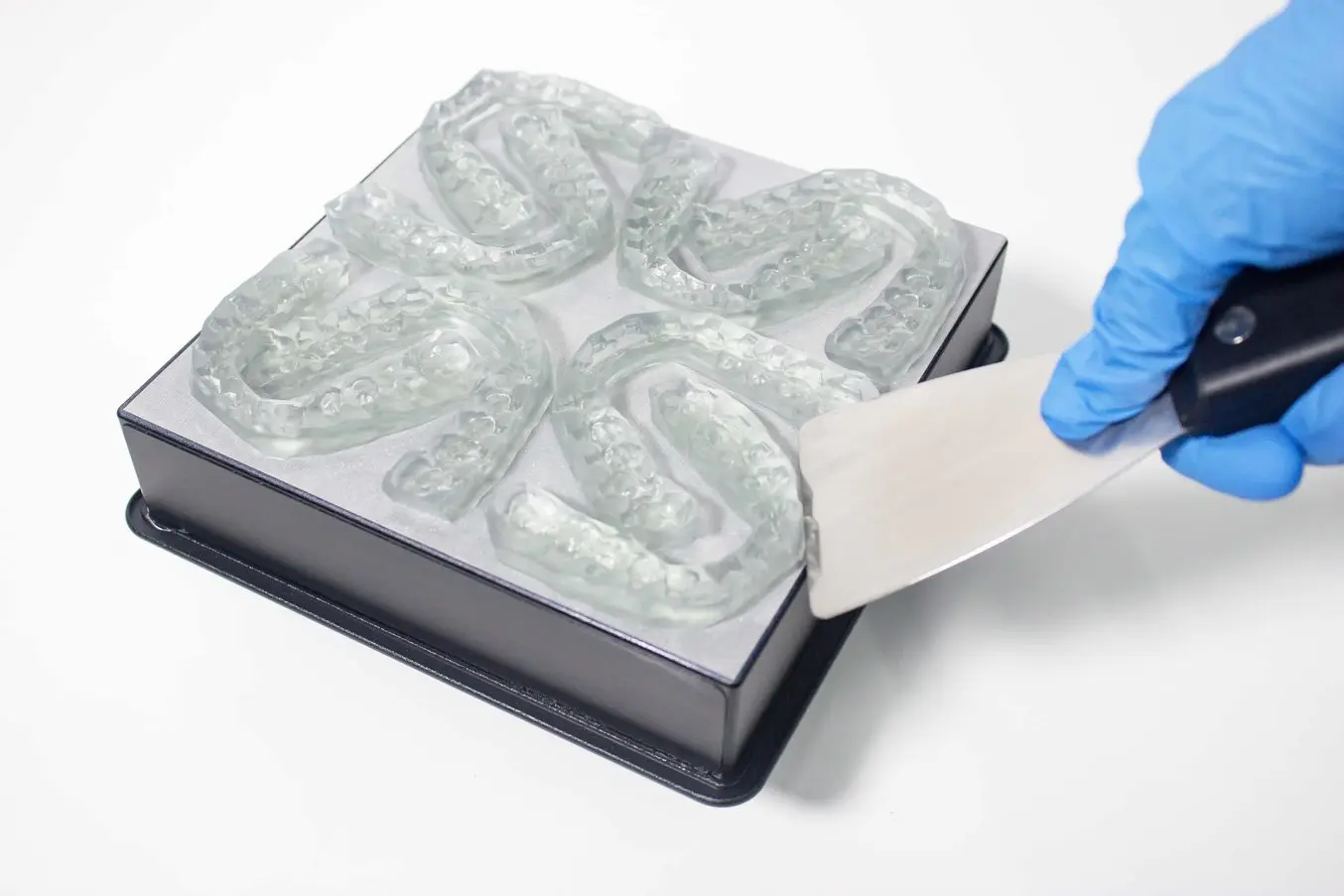
4.2 Washing
Precautions
- When washing the printed part with solvent, ensure a properly ventilated environment with proper protective masks and gloves.
- Expired or unused IBT Flex Resin shall be disposed of in accordance with local regulations.
Place printed parts in a Form Wash or Form Wash L filled with isopropyl alcohol (IPA, ≥99%) and wash them for the time established in the Manufacturing Guide.
Make sure the parts are fully submerged in IPA when washing.
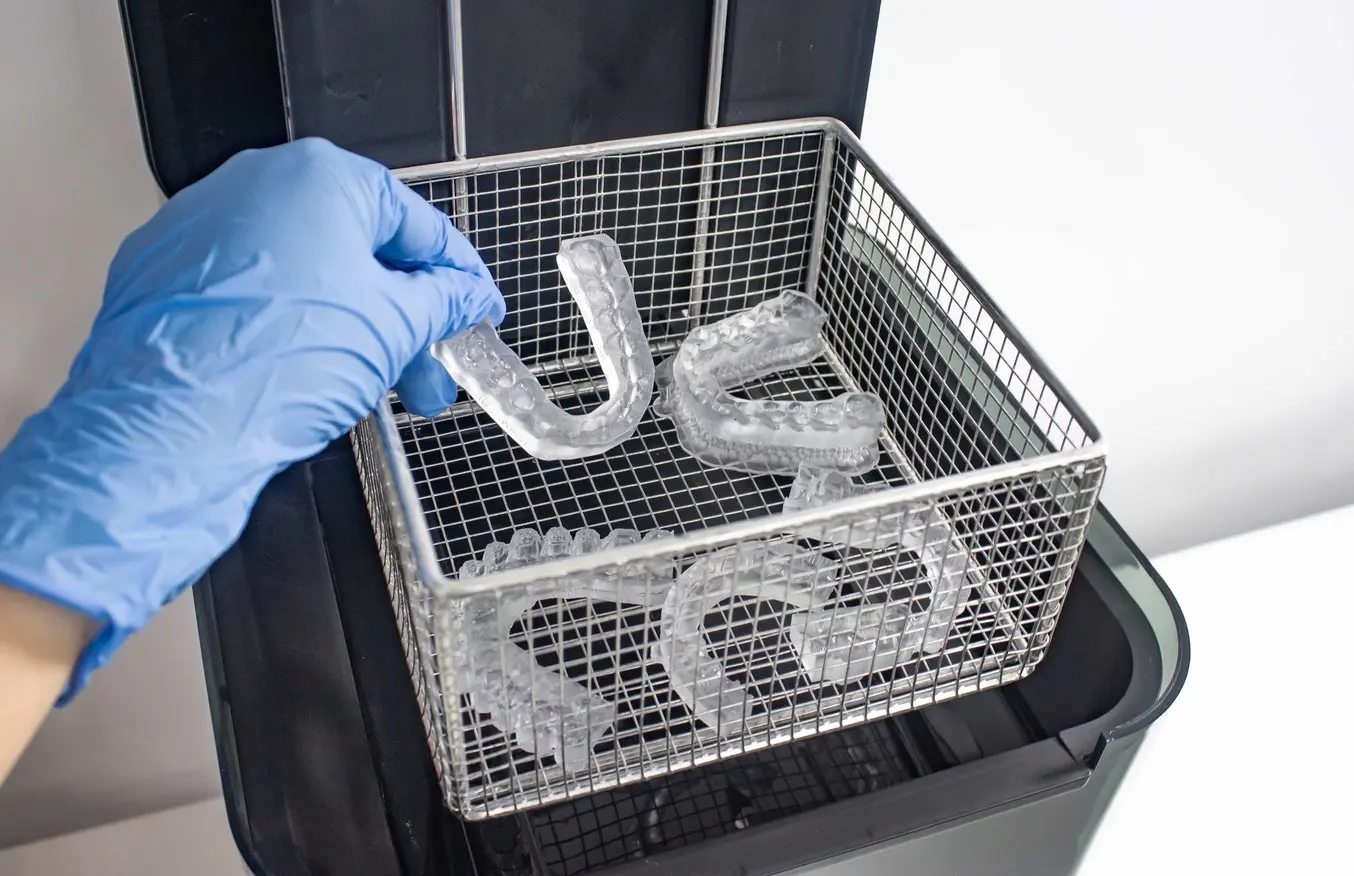
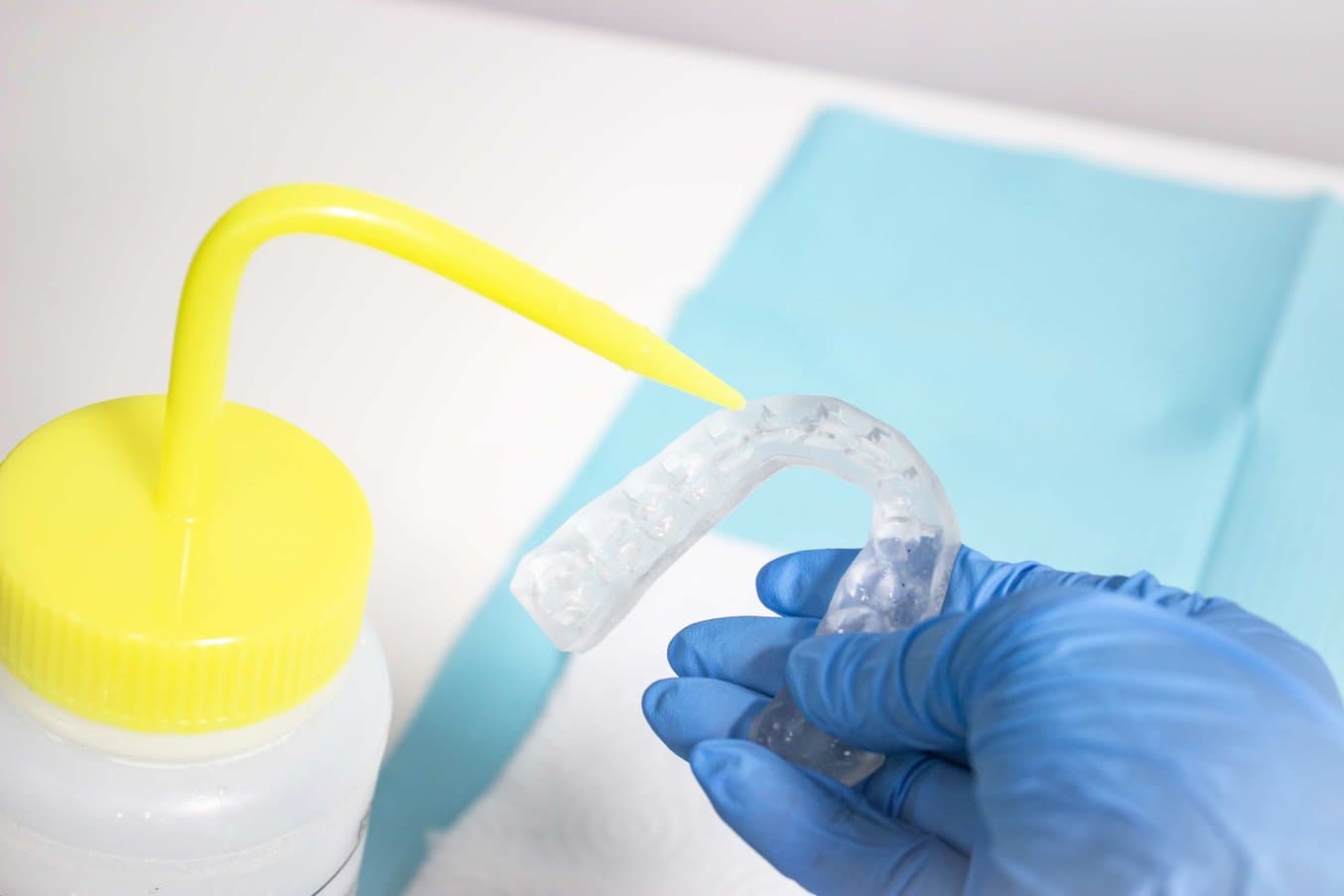
If your part geometry traps residual resin, it may be beneficial to lightly swish a paintbrush back and forth along the bracket pockets midway through the wash cycle.
Exceeding wash duration may affect dimensional accuracy and performance of printed parts over time.
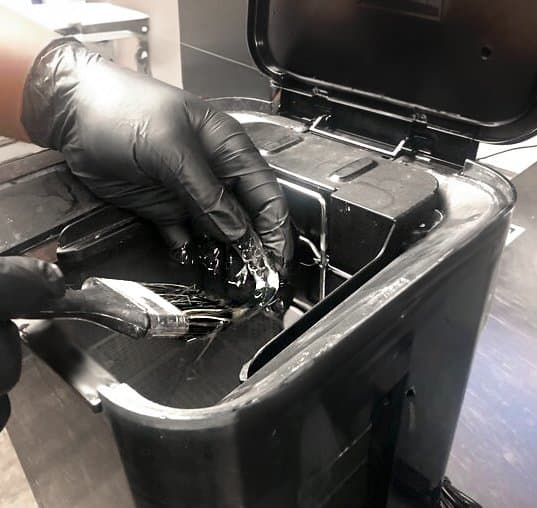
4.3 Drying
Remove parts from IPA and leave to air dry at room temperature for at least 30 minutes in a well-ventilated area.
Compressed air can be used to help dry parts and allow for rapid inspection of unwashed resin. Still allow for sufficient bench drying if using compressed air.
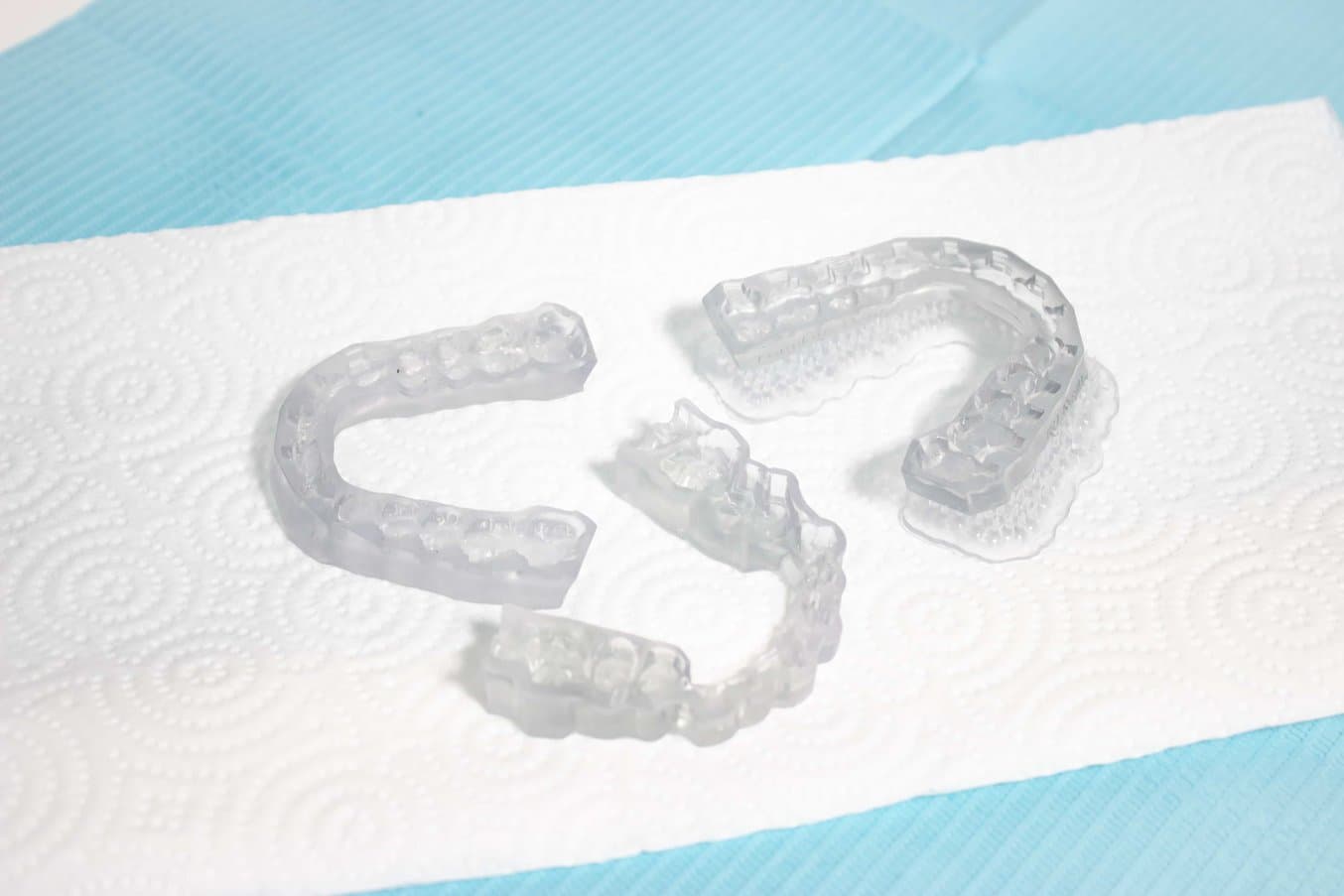
Inspect printed parts to ensure that parts are clean and dry. No residual alcohol, excess liquid resin, or residue particles must remain on the surface before proceeding to subsequent steps.
If any wet, uncured resin is still present after drying, use a squeeze bottle with fresh IPA to remove the uncured resin. Lightly swishing a paintbrush back and forth along the bracket pockets may also help with the removal of uncured resin. After removal, dry the parts again. The use of compressed air allows for rapid inspection.
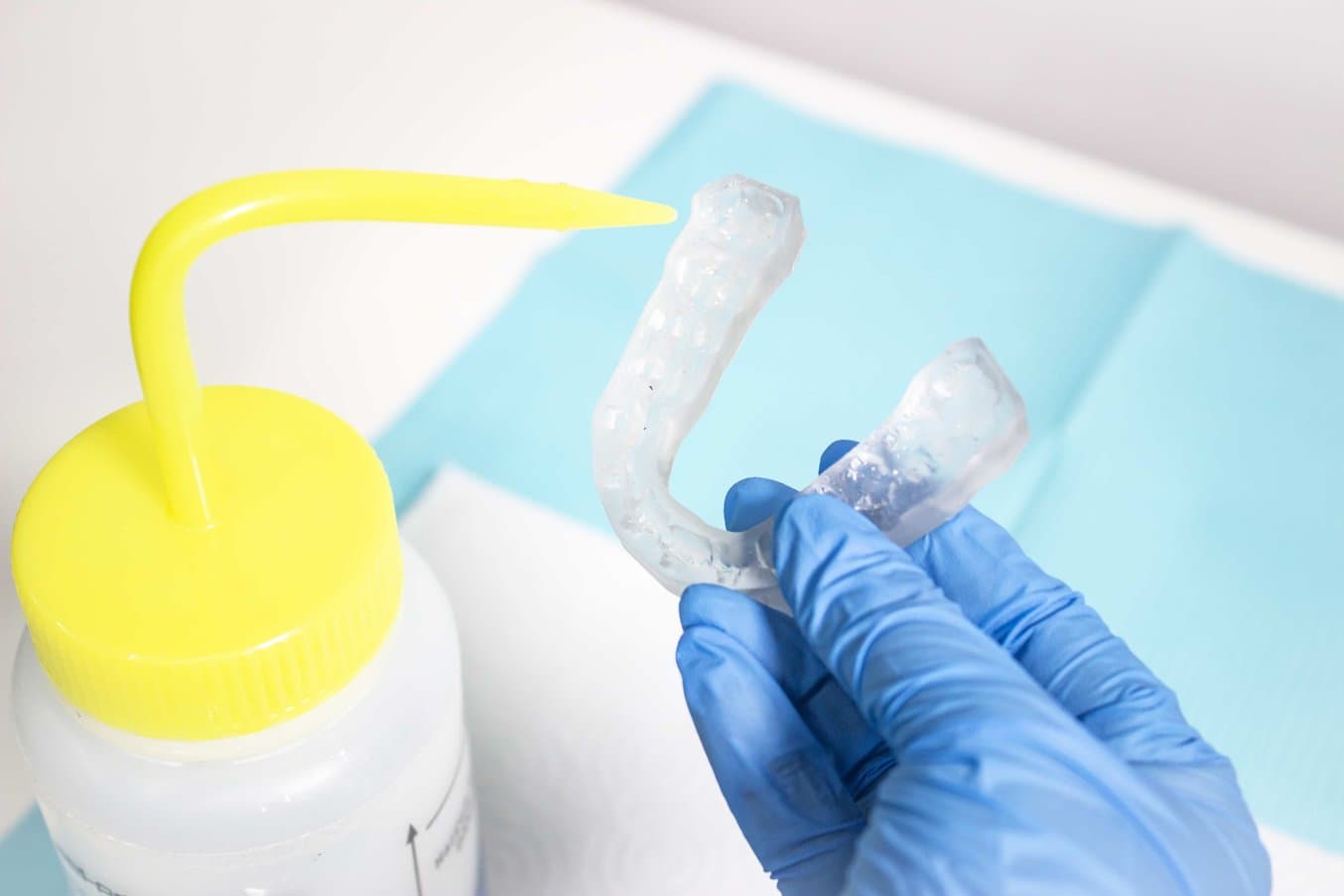
4.4 Post-Curing
To maintain dimensional accuracy and biocompatibility, specific post-curing instructions must be followed.
Printed parts should be cured while submerged in a transparent, water-filled container inside a Formlabs validated curing unit (Form Cure, Form Cure L, or Fast Cure).
If indirect bonding trays are printed with rafts and supports, place printed parts in the curing unit with the raft side down. If the trays are printed directly on the build platform without supporting structures, place the part in the curing unit with the intaglio surface of the appliance facing up.
Post-cure the parts in a Form Cure, Form Cure L, or Fast Cure using settings established in the Manufacturing Guide.
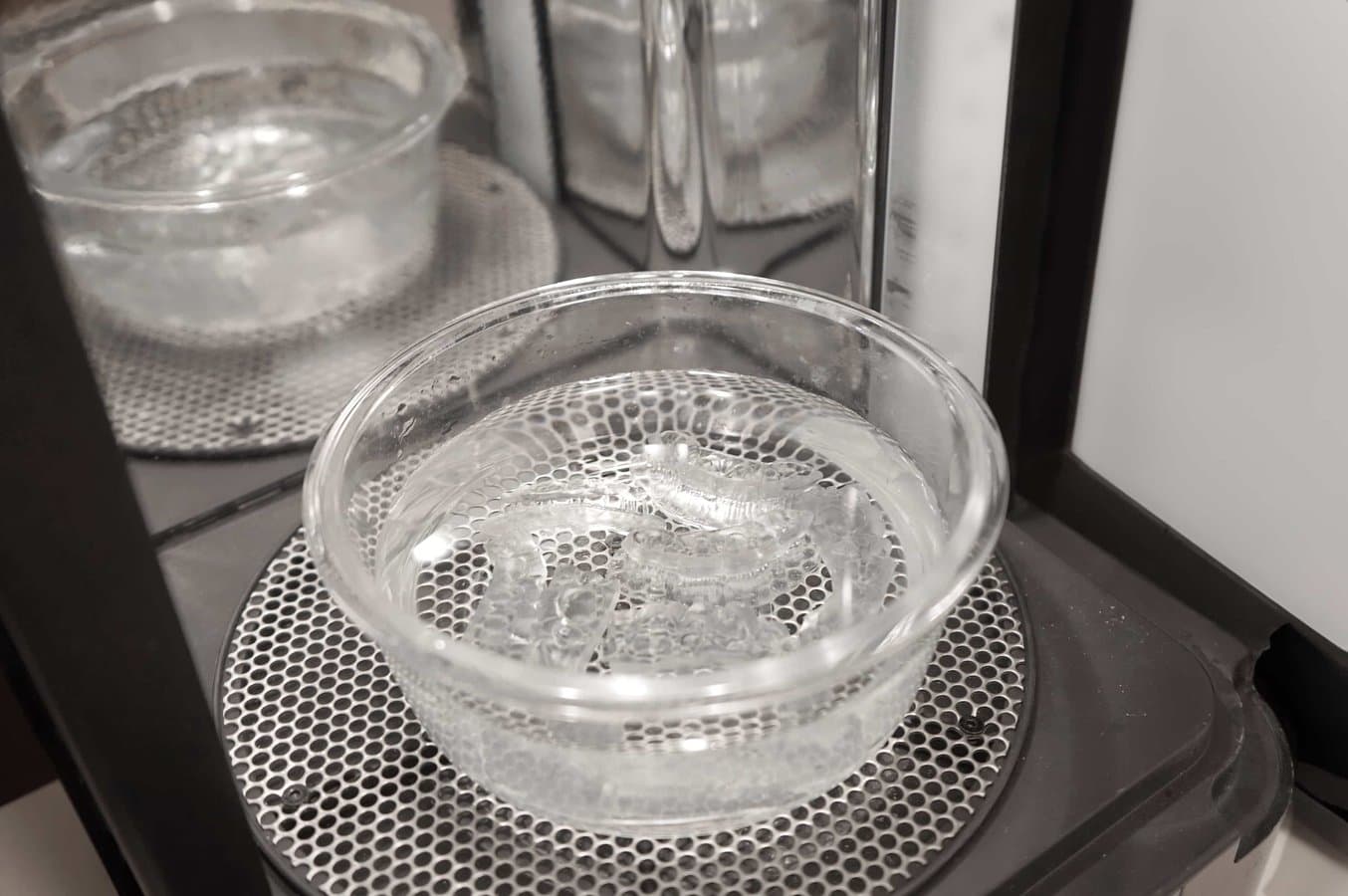
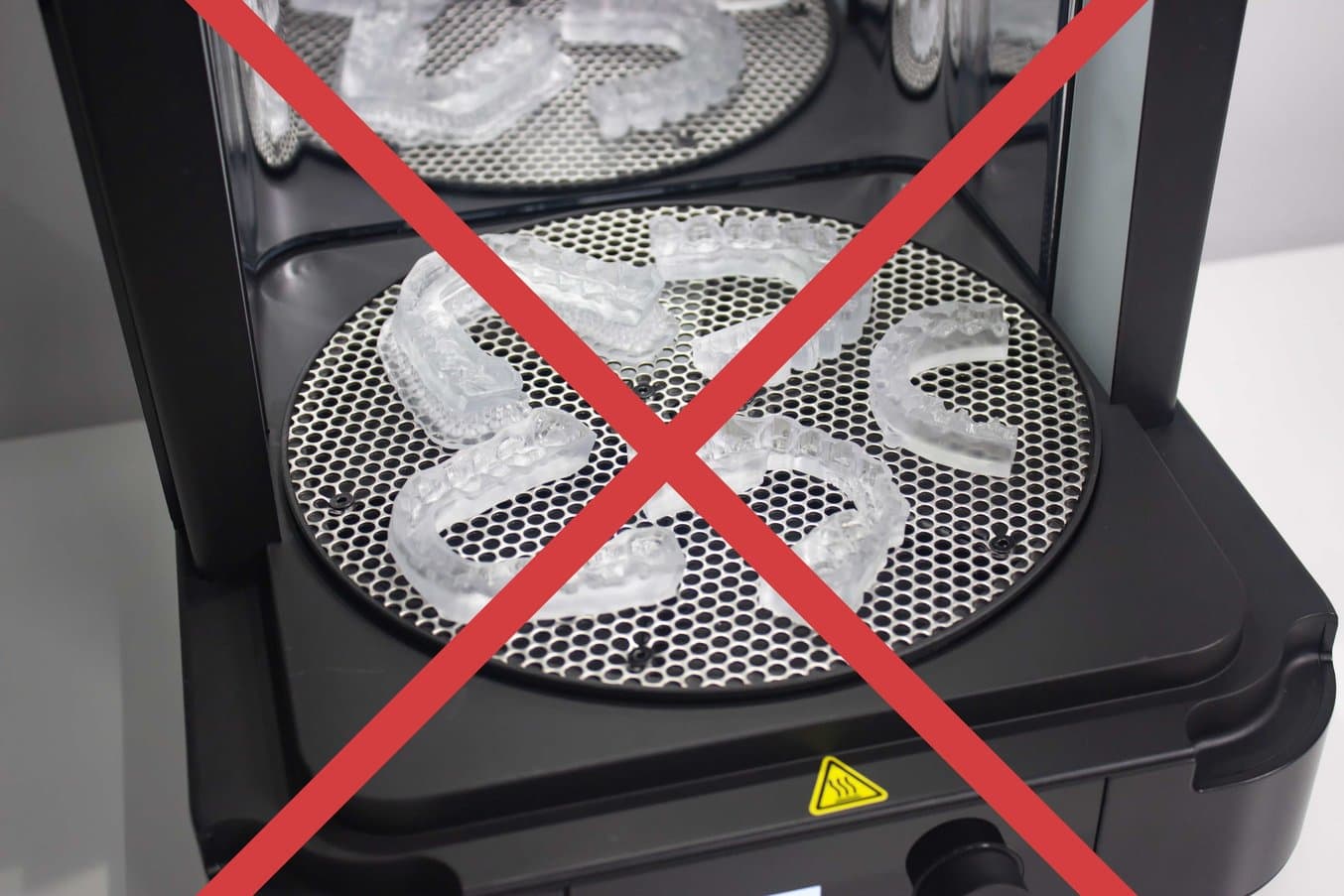
4.5 Support Removal
If supports were used, remove the supports using the clippers provided in the Formlabs Finish Kit or scissors as needed.
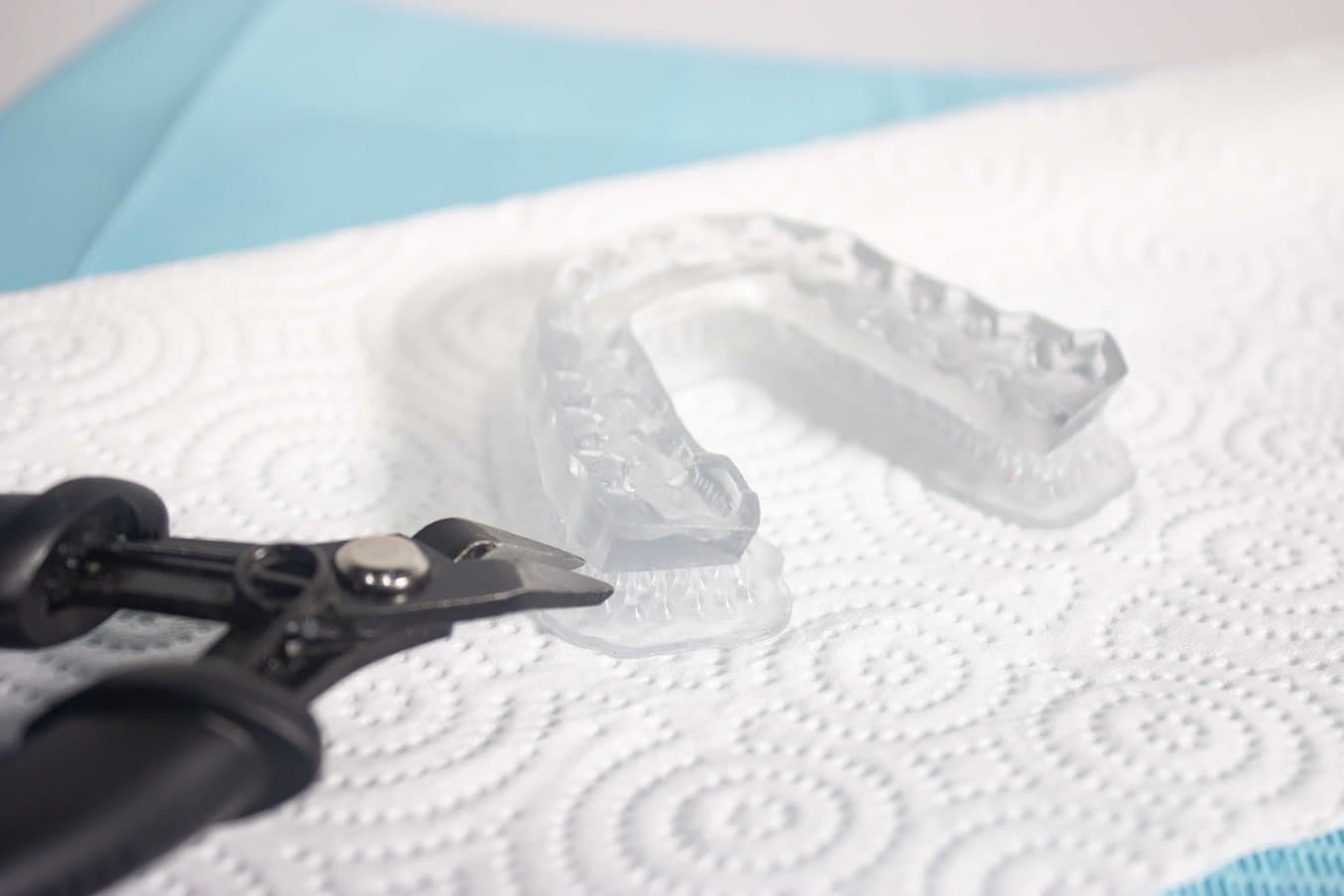
4.6 Finishing
After support removal, if any support structures are left on the surface of the 3D printed indirect bonding tray, you can remove them with a set of sharp iris scissors.
Inspect the appliance. Discard and reprint it if any damage or cracks are detected.
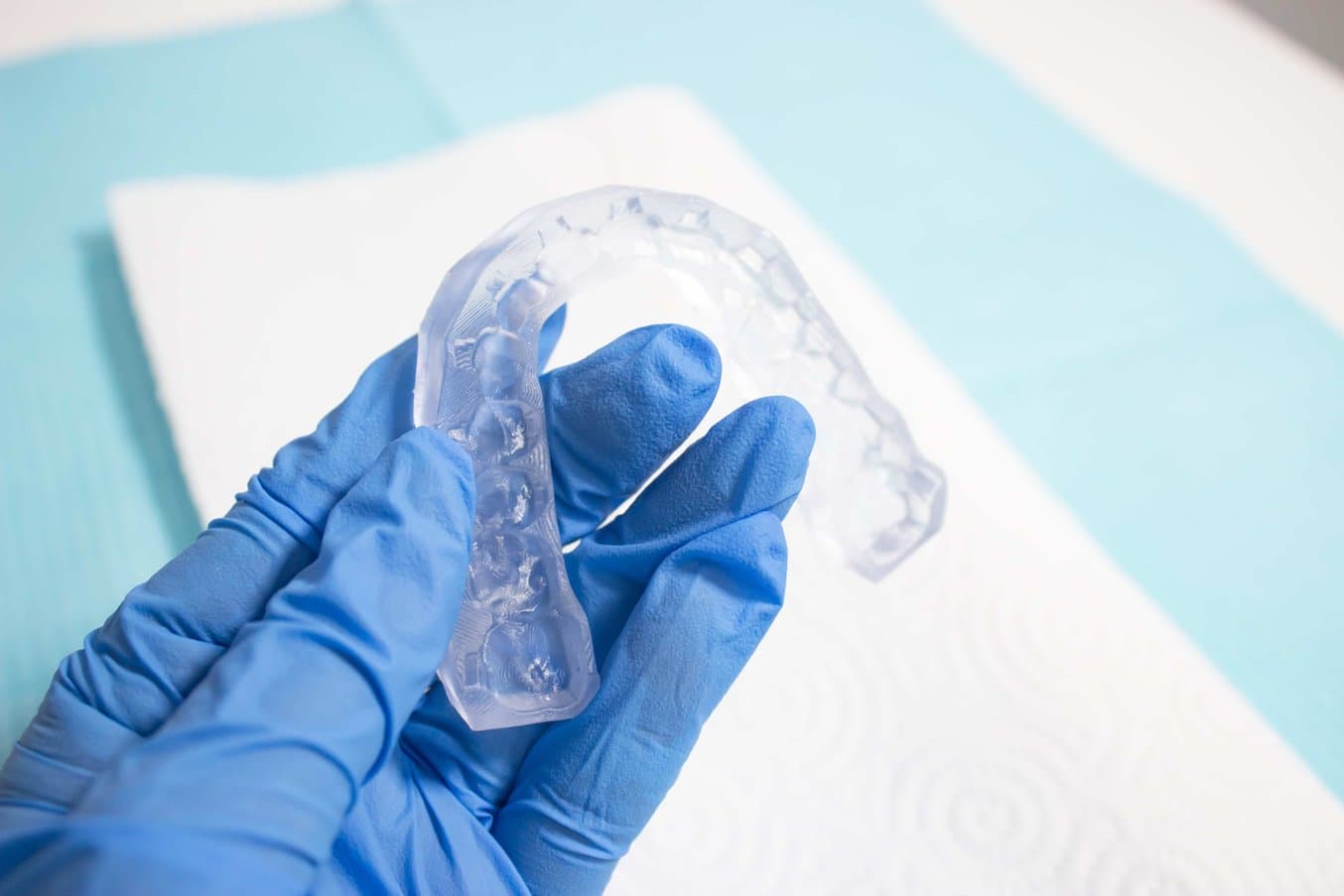
5. Appliance Care and Use
UV Cure Light Recommendation
While working with orthodontists, we found having the right UV curing light greatly improves the adhesion of the brackets through the indirect bonding tray. A fairly affordable, high-powered light we recommend is the Ledex WL-090+ Curing Light.
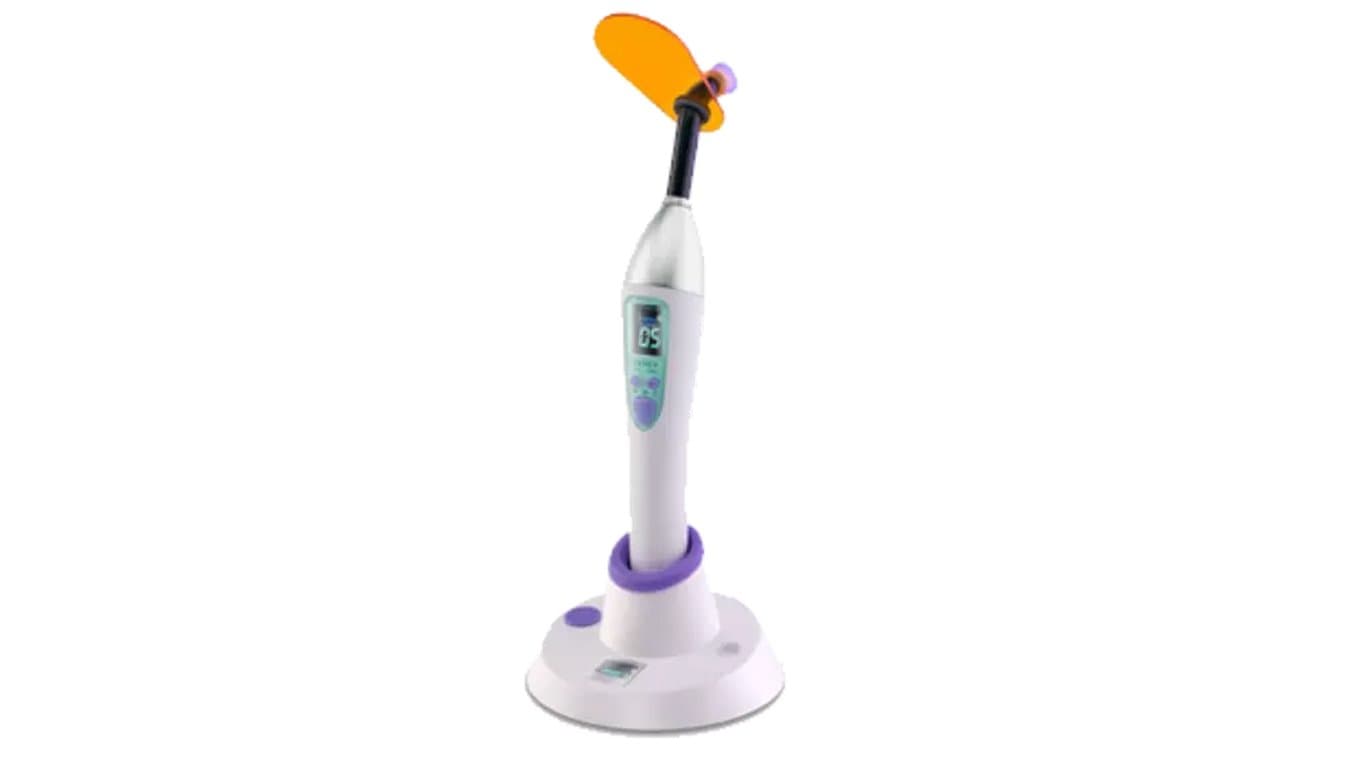
5.1 Cleaning
Fully post-processed parts can be cleaned using neutral soap and room temperature water.
After cleaning, always inspect parts for any cracks. Discard if any damage or cracks are detected.
5.2 Disinfection
The indirect bonding tray may be cleaned and disinfected according to facility protocols.
Our tested method of disinfection involves soaking the finished indirect bonding tray in fresh 70% IPA for 5 minutes.
Note: Do not leave the part in the alcohol solution for longer than 5 minutes.
After disinfection, inspect the part for cracks to ensure the integrity of the indirect bonding tray.
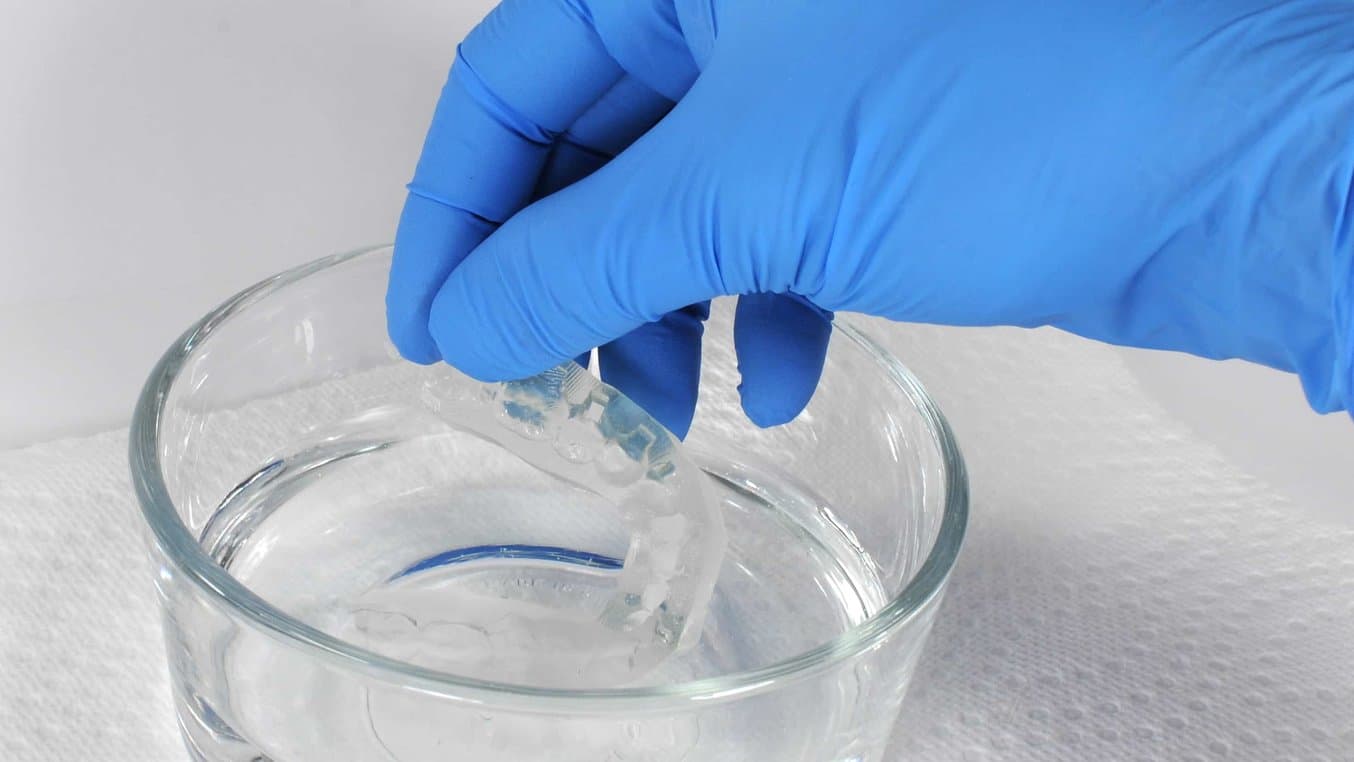
5.3 Storage
When not in use, place printed parts in closed, opaque or amber containers.
Store in a cool, dry place out of direct sunlight. Excess light exposure overtime may affect the color and performance of printed parts.
Store the cartridges at 10 °C–25 °C (50 °F–77 °F). Do not exceed 25 °C (77 °F) when in storage. Keep away from ignition sources.
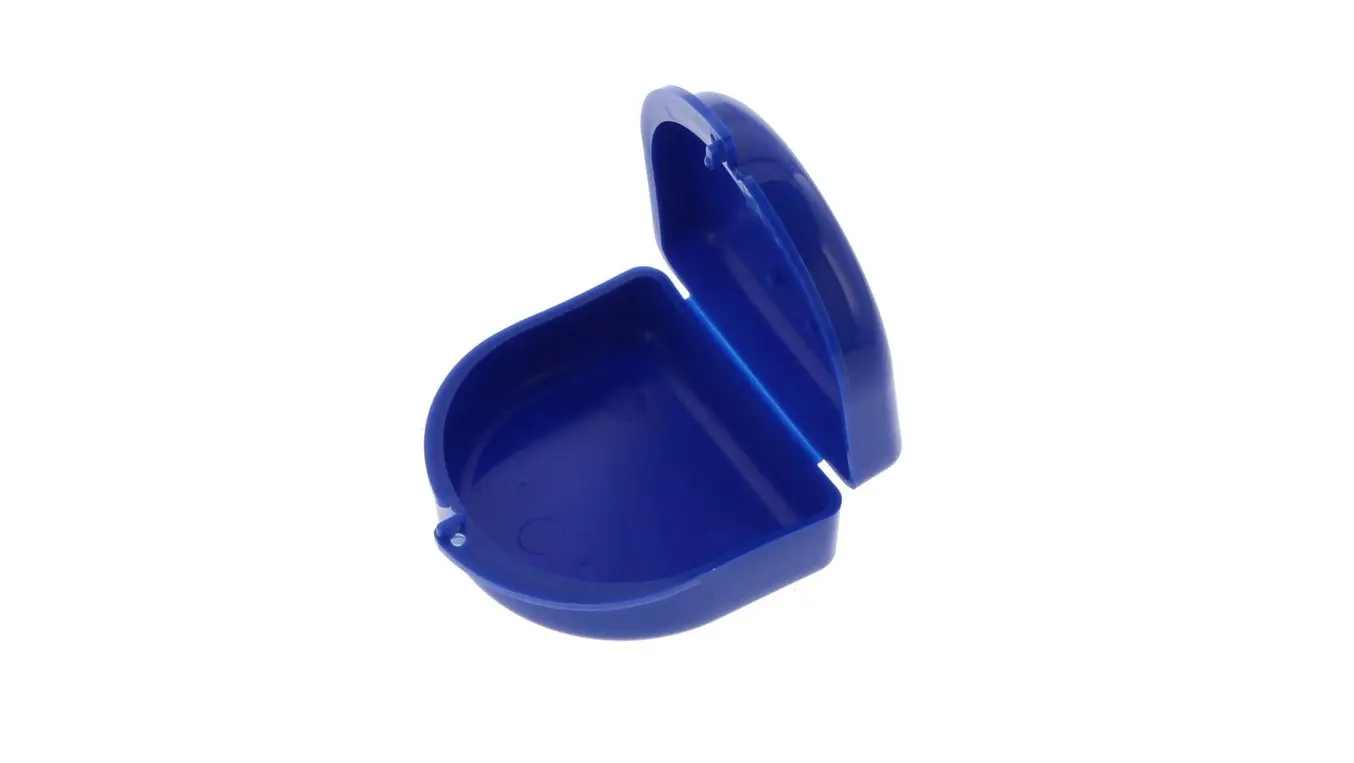
5.4 Disposal
1. Any cured resin is non-hazardous and may be disposed of as regular waste.
-
Follow facility protocols for waste that may be considered biohazardous.
2. Liquid resin should be disposed of in accordance with government regulations (community, regional, national).
- Contact a licensed professional waste disposal service to dispose of liquid resin.
- Do not allow waste to enter storm or sewer drainage systems.
- Avoid release into the environment.
- Dispose of contaminated packaging as unused product.
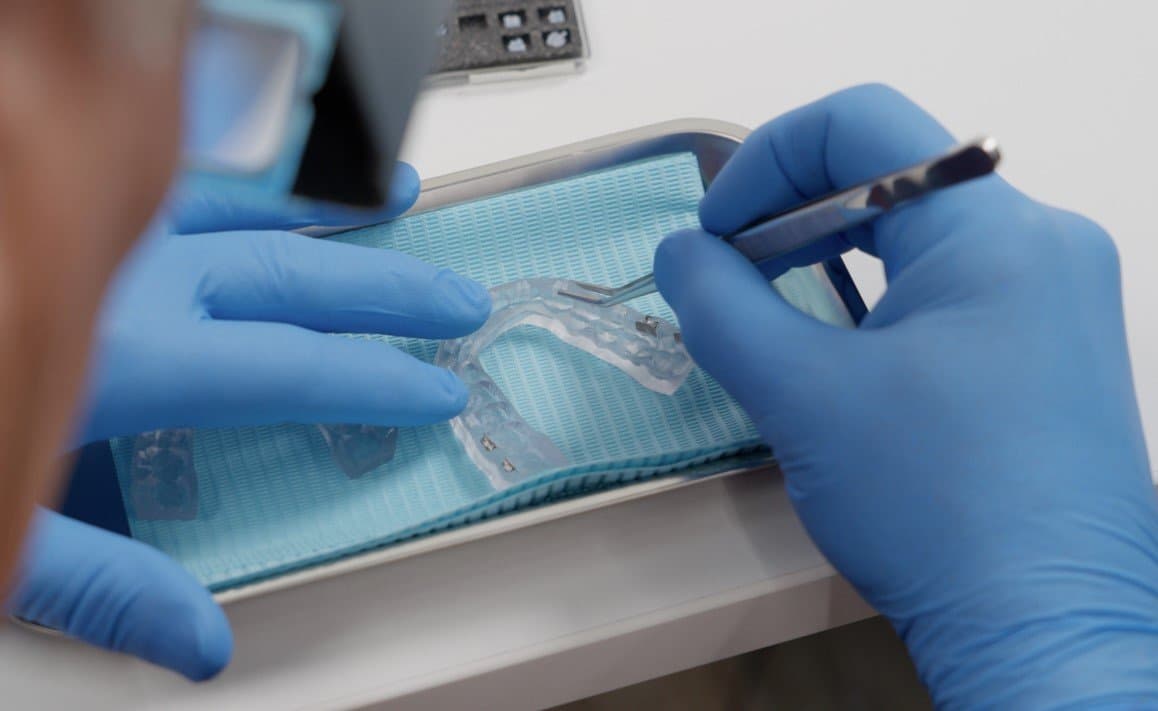
Additional Resources
Explore Formlabs dental resources for in-depth guides. step-by-step tutorials, white papers, webinars, and more.