Wie Die Zahnwerkstatt mit digitalem Workflow und 3D-gedruckten Try-Ins eine saubere, effiziente und planungssichere Teleskopprothesen-Produktion erreicht
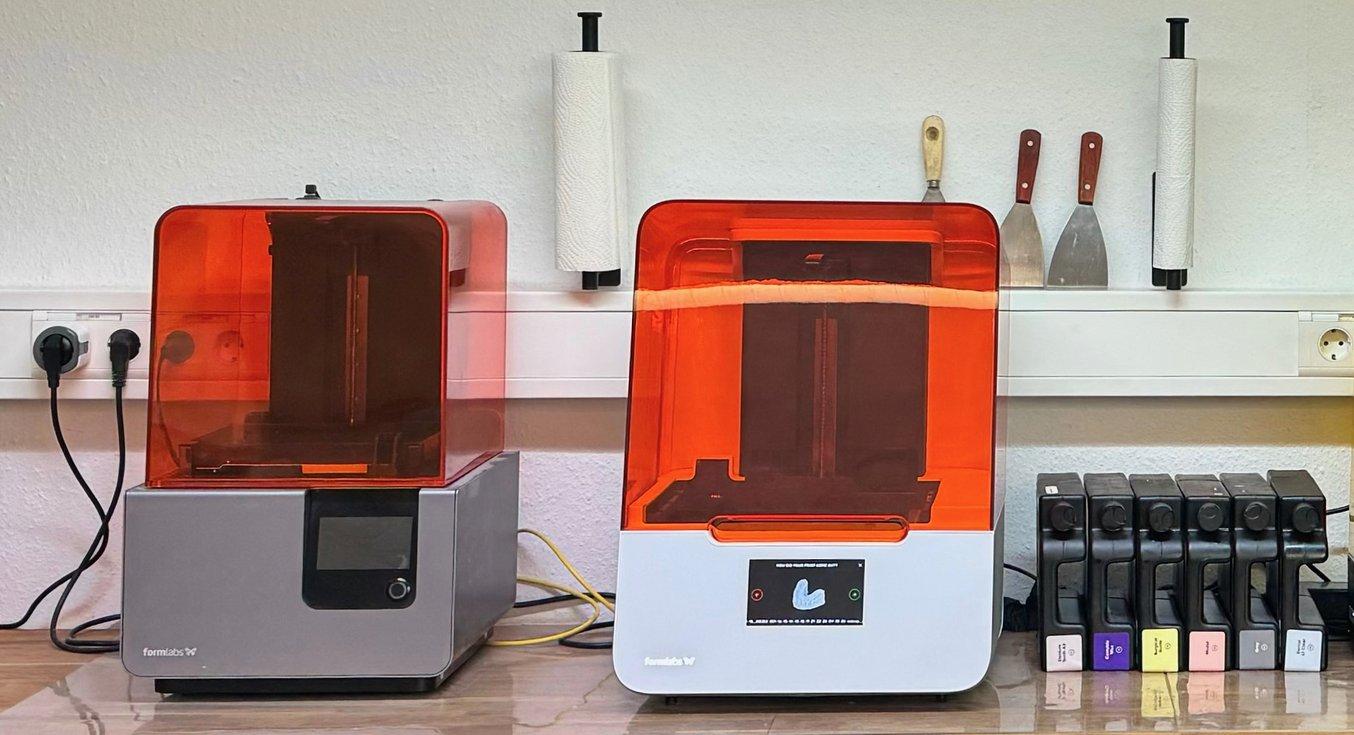
Bereits seit 2011 zaubert Die Zahnwerkstatt aus Weißenhorn Lächeln in Gesichter. Der zahntechnische Meisterbetrieb hat sich mit Hingabe zur Handwerkskunst und höchstem Anspruch an Präzision auf Teleskoparbeiten spezialisiert. Für Andreas Leimbach, Gründer und CEO, sollen am Ende der Behandlung alle Patient*innen ihr Lachen mit der Welt teilen wollen.
Im Mittelpunkt jeder Arbeit stehen daher die ästhetischen Wünsche der Behandelten, die ebenso vielseitig sind wie ihre Gesichter und medizinischen Ausgangssituationen. Die Herstellung von Zahnersatz war daher stets individuelle und manuelle Arbeit, abhängig von den Fähigkeiten der Zahntechniker*innen. Dies macht den Beruf so aufregend, abwechslungsreich und spannend, aber birgt stets die Gefahr menschlicher Fehler. Um diese einzudämmen, Zahnersatz verlässlich sowie in höchster Qualität herzustellen und dabei die Wünsche von Patient*innen durchgängig zu berücksichtigen, damit spätere kostspielige Anpassungen vermieden werden, setzt Andreas Leimbach auf moderne Technologien und Prozesse.
Erfahren Sie im Folgenden, wie Andreas Leimbach Try-Ins für teleskopischen Zahnersatz mit dem Form 3B+ herstellt, um die Zahntechnik vom analogen Staub zu befreien und mit digitaler Arbeitsweise auf das nächste Level zu bringen.
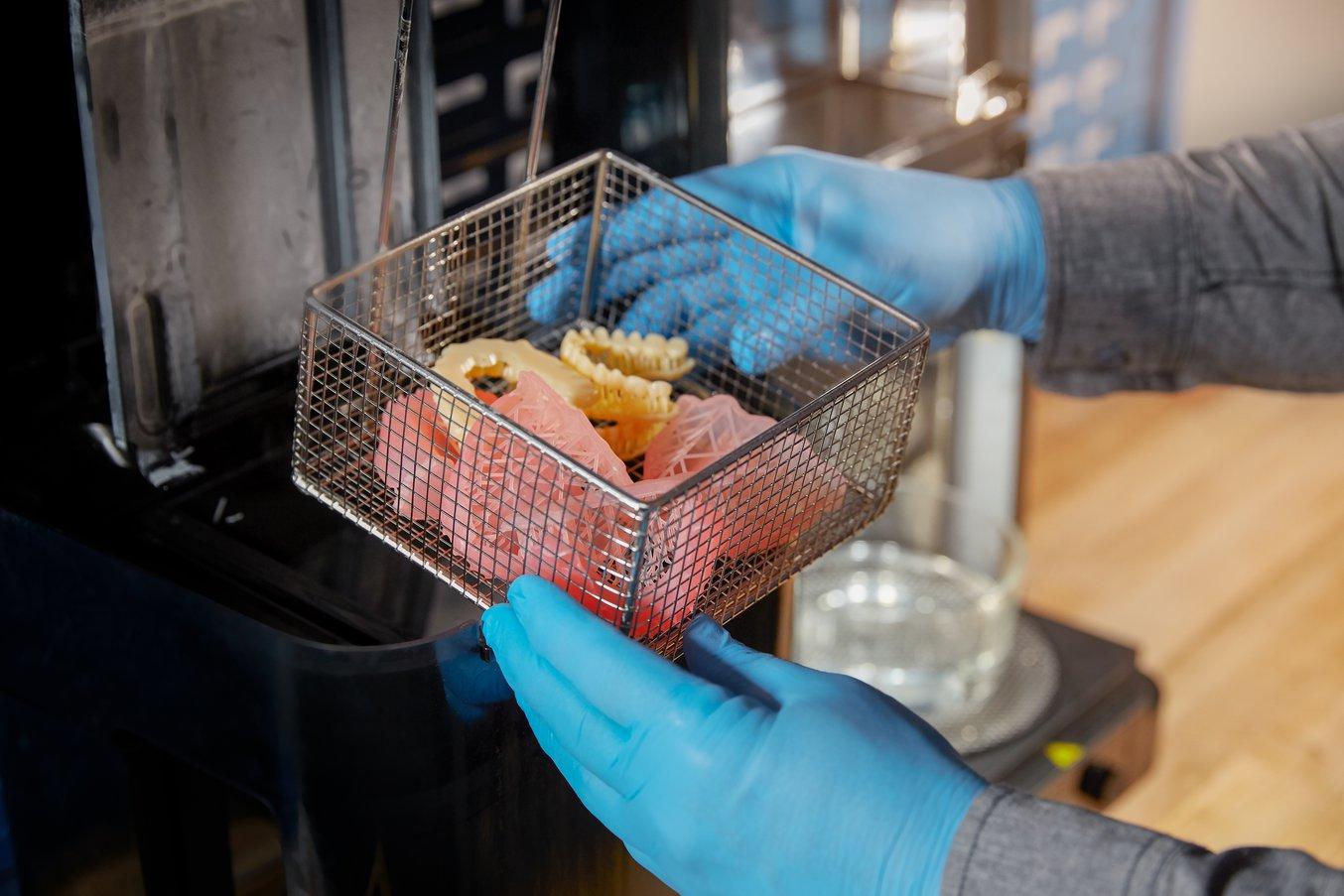
Vollprothesen kostengünstig herstellen mit Formlabs & Vita
In diesem Webinar geben die Referenten Jürgen Sander, ZT und Kursleiter der VITA Zahnfabrik, sowie Bernhard von Oppeln, ZTM und Dental Application Engineer bei Formlabs, einen umfassenden Überblick zum Arbeitsablauf bei der additiven Herstellung von Prothesen sowie zu den möglichen Varianten in Kombination mit traditionellen Methoden.
Von der Ästhetik zur Funktion – Unnötige Arbeit vermeiden mit Backward-Planning
In der Vergangenheit wurde Zahnersatz in Form von Prothesen oder Implantaten primär vom funktionalen Kern aus entwickelt und die ästhetische Erscheinung im Sinne der Patient*innen erst zum Abschluss berücksichtigt. Die erste Rückmeldung, ob der Zahnersatz funktioniert, so Leimbach, erhielten Zahntechniker mit der Planungs- und Zahnaufstellung. Allerdings gingen dieser bereits mehrere Schritte und aufwendige Arbeiten voraus – von der Fertigung der Primärteile, Einprobe, Bissnahme bis zur Gerüstfertigung. „Wenn der Punkt erreicht war, dass der Zahnarzt anruft und sagt‚ das sieht wirklich schrecklich aus', hieß es wieder zurück an den Anfang. Da habe ich aber schon viele Arbeitsschritte gemacht”, erinnert sich Leimbach.
Für Leimbach gehört der traditionelle Prozess, der zu seinem Unmut noch weitläufige Anwendung in der Zahntechnik findet, aus den Lehrbüchern und in die Geschichtsbücher verbannt. Immer wieder frustrierte ihn, wenn aufwendige Arbeiten sich als obsolet herausstellten. Daher begann er seine Produktion stets auf dem zu erzielenden Endergebnis zu basieren. Diese konsequente Planung des Therapiewegs anhand des Behandlungsziels wird in der Zahntechnik auch als Backward-Planning bezeichnet. Behandelnde Ärzt*innen und ihre Patientenschaft erhalten durch provisorischen Zahnersatz wie Mock-Ups, Wax-Ups und Try-Ins frühzeitig Eindruck vom finalen Zahnersatz und ihre Rückmeldungen werden in die weitere Planung einbezogen.
Leimbach beginnt stets mit einem Try-In als Prototyp des Zahnersatzes, der bei Einproben auf phonetische Funktionalität und Ästhetik geprüft wird. Erst bei positiver Rückmeldung zum Zahnersatz fährt er mit der Entwicklung der Primärteile fort. So kann er bösen Überraschungen, Rückläufern, kostspieligen Anpassungen, enttäuschten Patient*innen und unnötiger Arbeitszeit – samt Frustration – vorbeugen. „Ab der ersten Sekunde möchte ich in meinem Labor auf etwas Sinnvolles hinarbeiten, und das geht nur, wenn der Patient ab dem ersten Moment weiß, wie seine neuen Zähne aussehen. Das heißt, ich erstelle gleich zu Beginn Try-Ins und hole mir das Feedback ab”, erklärt Leimbach.
Vorteile digitaler und additiver Fertigung
Die analoge Herstellung von Prototypen ohne 3D-Druck ist für Leimbach heute kaum noch vorstellbar, weshalb er alle Konstruktionen digitalisiert hat. Für Planungen arbeitet er mit CAD-Software von 3Shape, Exocad oder Zirkonzahn.
Für die Umsetzung setzt Leimbach auf additive Fertigung mit dem Stereolithografie-Drucker (SLA) Form 3B+. Subtraktive Fertigung beschränkt er auf das Fräsen von Zirkon-Material mit einer kleinen VHF-Fräse. Größere CNC-Fräsen, beispielsweise für die Verarbeitung von Stahl, waren aufgrund der hohen Anschaffungskosten, hohen Materialverbrauchs und aufwendiger Instandhaltung nie attraktiv für ihn.
Diese subtraktive Technik passt nicht in meine Welt. Ich finde 3D-Druck großartig, weil es additiv ist, weil es Material spart, weil es Kosten spart, weil es effizient ist, weil es schnell geht.
Andreas Leimbach, ZTM & CEO von Die Zahnwerkstatt
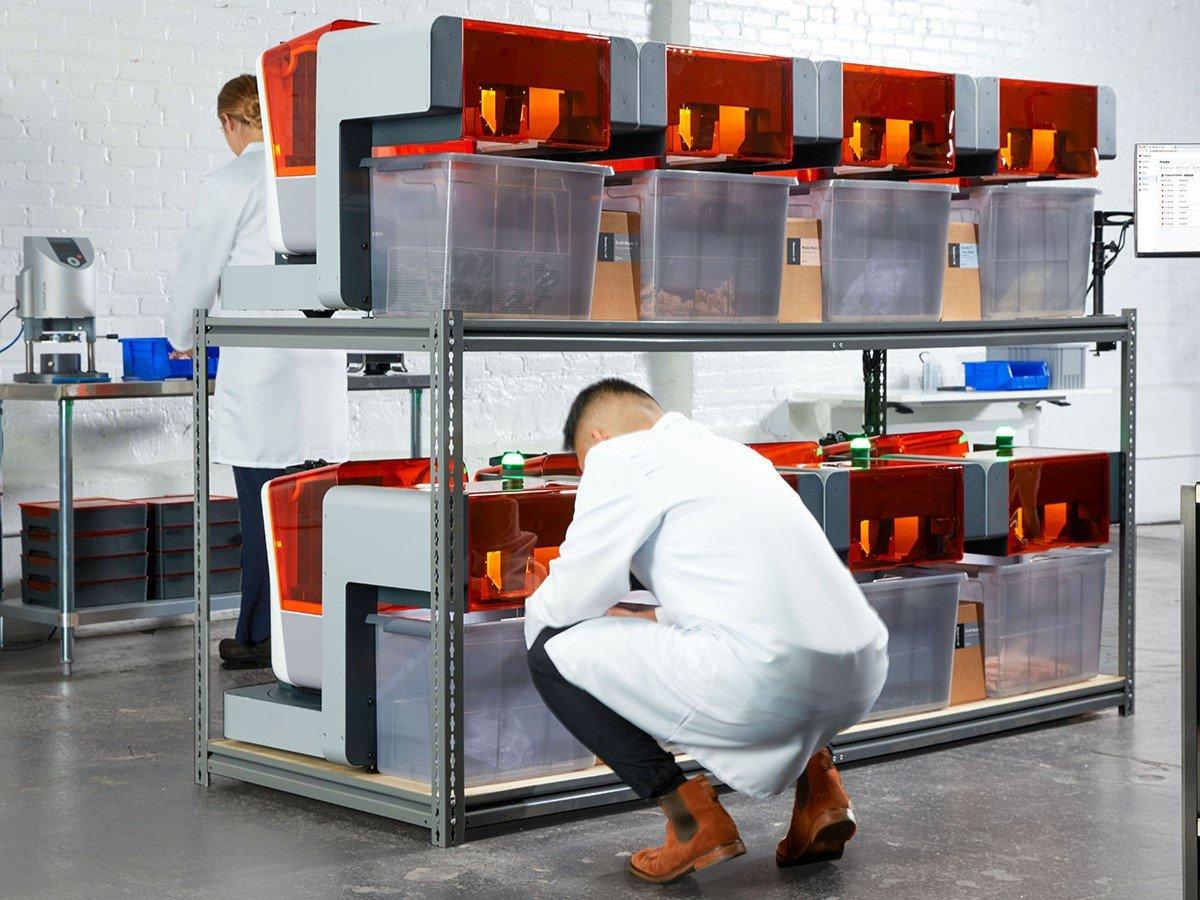
Einführung in das neue automatisierte Ecosystem
Im Webinar erfahren Sie, wie Sie mit dem automatisierten Ecosystem von Formlabs den Durchsatz sowie die Produktivität Ihres Dentallabors steigern, und Ihre vollautomatisierte 3D-Druckerflotte dank Fleet Control, Form Auto und dem Resin Pumping System mit Ihrer Nachfrage skalieren.
Work-Life-Balance – Wie 3D-Druck Effizienz steigert und den Feierabend rettet
Dermaßen von der additiven Fertigung überzeugt, hat Leimbach den Tag, an dem der erste SLA-3D-Drucker von Formlabs sein Labor erreichte, noch in lebhafter Erinnerung. Mit noch zwei zu erstellenden Try-Ins auf der täglichen Aufgabenliste, erschien es ihm immer unwahrscheinlicher, den lange feststehenden Termin mit seiner Frau und seinen vier Kindern am Abend pünktlich wahrnehmen zu können.
Bis dahin musste er für Prototypen wie diesen jeden Zahn individuell anpassen und einzeln aufstellen, wofür er bis zu vier Stunden benötigte. An diesem Tag musste es jedoch schneller funktionieren, um dem sonst vorprogrammierten Familienkrach zu entgehen. „Als ich den Form 2 geliefert bekam, habe ich gedacht: ‚Okay, bevor ich mich jetzt hier hinsetze und vier Stunden lang diese Zähne aufstelle und Stress mit meiner Frau bekomme, konstruiere ich das einfach virtuell.' Das habe ich in der Vergangenheit schon öfter mal gemacht. Einfach weil ich Lust hatte neue Prozesse auszuprobieren. So habe ich es dann gemacht und diese 28 Zähne innerhalb von einer halben Stunde aufgestellt”, sagt Leimbach.
Während der 3D-Drucker die nächtlichen Überstunden übernahm, konnte Andreas Leimbach seinen Feierabend genießen. Am nächsten Morgen war er von der Qualität der Drucke begeistert, entfernte die Stützstrukturen, löste verbliebene Reste in der automatisierten Nachbearbeitungsstation Form Wash und prüfte das Modell im Artikulator. Den Umstieg auf additive Fertigung hätte er sich nicht einfacher vorstellen können. Beeindruckt von der einfachen Bedienung des 3D-Druckers sowie der Effizienz und Sauberkeit des Vorgangs, war ihm klar, dass er Try-Ins nie wieder analog in Wachs aufstellen würde.
"Das war einfach Plug-and-Play und ab dem ersten Versuch bekam ich genau das Ergebnis, das ich wollte. So habe ich 28 Zähne, ganz viel Dreck und vor allem Zeit gespart, denn mit Druck und Nachbearbeitung war meine relative Arbeitszeit vielleicht eine Stunde. Das steht in keinem Vergleich zu der analogen Geschichte, mit vier Stunden für das Aufstellen und die Reinigung im Anschluss", erklärt Leimbach.
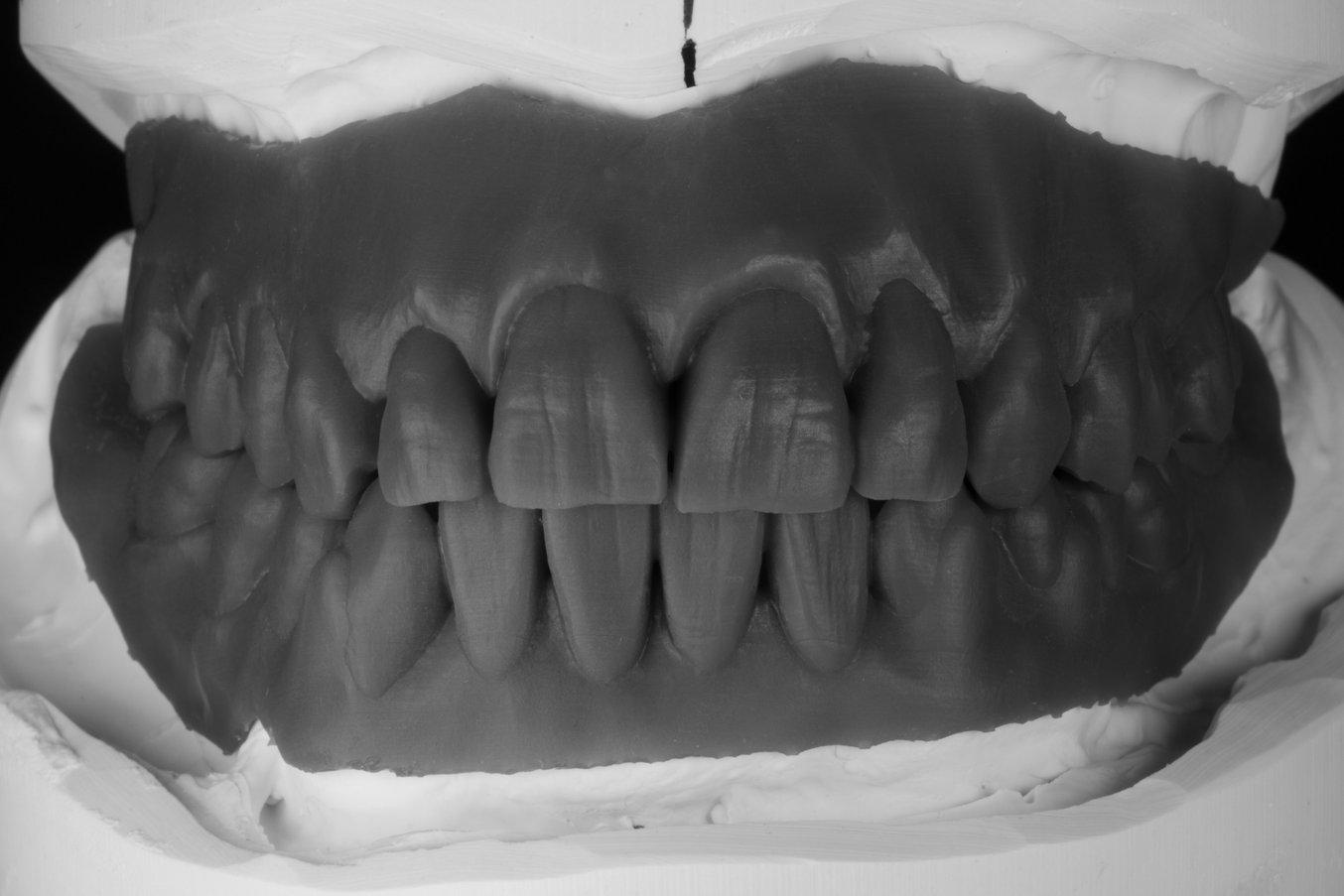
Mit 3D-gedruckten Prototypen aus Draft Resin kann die Funktion und Ästhetik des geplanten Zahnersatzes frühzeitig und kostengünstig im Artikulator validiert werden
Weiches Wachs, hartes Harz – hygienische und stabile Try-Ins aus dem 3D-Drucker
Neben der Verringerung von Arbeitszeit und manuellen Arbeitsschritten verbesserte die additive Fertigung die Try-In Produktion für Leimbach auch hinsichtlich der erreichten Qualität. Aufgrund der verwendeten Kunstharze und der Herstellungsweise sind die Prototypen formstabiler als früher angefertigte Modelle auf Wachsbasis und damit resistenter gegenüber Verformungen während des Transports und der Einprobe. „Die Praxisaufstellungen, die ich früher gemacht habe, das war eine Basisplatte plus Wachs, plus 28 Zähne, die ja nicht verbunden waren. Wenn du da drauf beißt und das alles warm wird im Mund, verschiebt sich das wieder. Das war nie so eine sichere Geschichte. Zumindest nicht nach einer Viertelstunde im Mund”, erklärt Leimbach.
Die 3D-gedruckten Zähne sind hingegen aus einem Stück geformt und stabil mit der extra dafür gefertigten Basisplatte verklebt. Durch die Stabilität des Modells werden Fehlerquellen in der Planung reduziert. Für Patient*innen ist die Einprobe der dentalen Druckmaterialien darüber hinaus angenehmer, sauberer und hygienischer im Vergleich zu den Materialien, die Leimbach noch von seiner Arbeit in anderen zahntechnischen Werkstätten erinnert. „Rein hygienetechnisch sind wir hier auf einem ganz neuen Niveau. Vor zehn Jahren haben wir noch so eine klebrige, schleimige Basisplatte aus lichthärtendem Kunststoff gemacht. Die hat schon ausgesehen, als ob du davon sterben musst, wenn du das anfassen musst, verarbeiten musst, riechen musst", erinnert sich Leimbach.
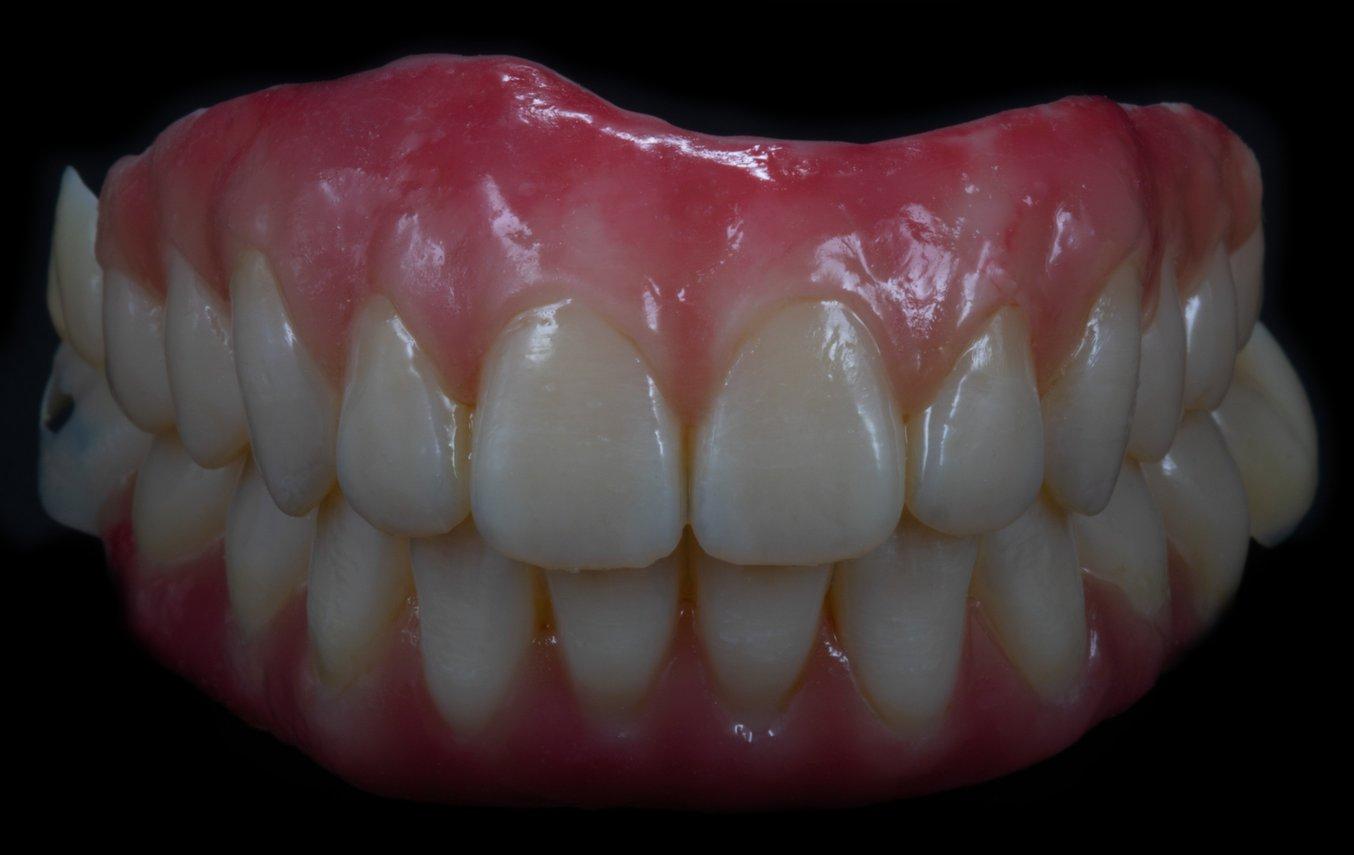
Backward-Planning und 3D-gedruckte Visualisierungen reduzieren Herstellungszeit und -kosten für hochqualitativen Zahnersatz
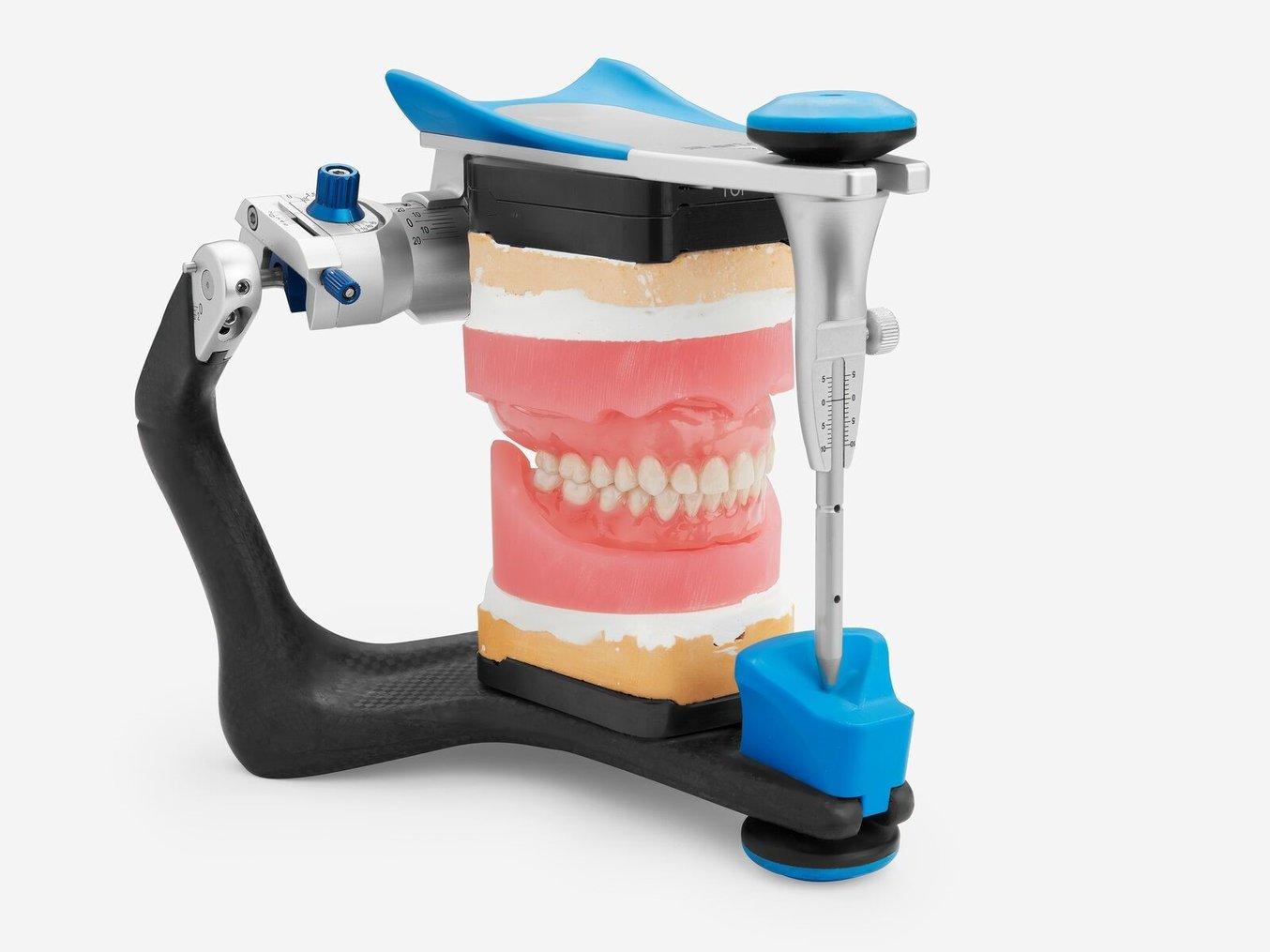
3D-Druck vollständiger Zahnprothesen mit Formlabs 3D-Druckern
Sie lernen in diesem Anwendungsleitfaden die wichtigen Faktoren und Schritte kennen, mit denen Sie von einem digitalisierten Patientenmodell zu 3D-gedruckten Zahnprothesen kommen, um die Effizienz Ihres Labors zu steigern.
Zusammenarbeit mit Arztpraxen
Der typische Ablauf der Herstellung von teleskopierenden Prothesen startet für Andreas Leimbach in 80 Prozent der Fälle mit traditionellen Abformungen, die ihm von Ärzt*innen zugesandt werden. Mithilfe eines Labor-Scanners digitalisiert er diese und fährt mit seiner Planung virtuell fort.
Die Zusammenarbeit mit Ärzt*innen, welche die Vorteile digitaler Prozesse ebenso erkannt haben, ist für ihn noch leichter. In diesen Fällen erhält er direkt digitale Abbilder des Mundraums, die mittels Intraoralscan erfasst wurden, und nimmt die Zahnaufstellung virtuell in Exocad oder 3Shape vor. Mit immer mehr Praxen arbeitet er darüber hinaus bereits direkt in cloud-basierter Planungssoftware zusammen. Für regional ansässige Zahnpraxen druckt er die Try-Ins und versendet diese postalisch. Durch digitale und additive Prozesse konnte er seine Kundschaft zusätzlich überregional erweitern. Einem Arzt aus Schweden sendet er schlicht die virtuellen Modelle als 3D-Dateien zu, welche dieser dann in der Praxis mit einem Form 3B+ druckt. Auch Kunden ohne eigene 3D-Drucker – bis in die USA – profitieren von der Perfektion aus der bayerischen Zahnwerkstatt. In diesen Fällen übermittelt Leimbach seine Modelle an nahegelegene Kollegen, welche die Prototypen drucken und versenden.
Die Ärzt*innen nehmen dann die Einprobe vor, holen Patientenfeedback ein und dokumentieren die Situation durch Fotos oder intraorale Scans. Diese Rückmeldungen verwendet Leimbach für ästhetische Anpassungen der fertigen Prothesen oder bei funktionalen Problemen zur Erstellung eines weiteren Try-Ins. Durch den permanenten Austausch kann Leimbach Verbesserungswünsche sofort einarbeiten, bevor er mit der Konstruktion von Primärteilen, Gerüsten und endgültigen Aufstellungen beginnt.
Das System funktioniert perfekt. Das hat auch jeder Zahnarzt von mir direkt so übernommen. Ich habe mich auch auf nichts anderes mehr eingelassen. Dadurch habe ich heute eine Rücklaufquote von maximal einem Prozent.
Andreas Leimbach, ZTM & CEO von Die Zahnwerkstatt
Durch konsequentes Backward-Planning und den Einsatz additiver Fertigung konnte Leimbach seine Rücklaufquote auf unter ein Prozent senken. Obwohl er schon von seinem ersten Druck mit dem Form 2 begeistert war, konnte er seine Qualität mit dem Form 3B+ und dessen zahnmedizinischen Druckmaterialien weiter steigern, die seine Arbeitsprozesse auf „ein neues Niveau gehoben haben – in Bezug auf Reproduzierbarkeit, Arbeitszeit, Ästhetik”.
Die Zukunft der Zahntechnik – digital und additiv
Was für Andreas Leimbach mittlerweile zum unumgänglichen Standard wurde, klingt für viele Zahntechniker*Innen noch wie Zukunftsmusik. Zu häufig lassen Dentallabore die Vorteile digitaler Planung und additiver Fertigung ungenutzt, findet Leimbach, und versucht mit seinen Online-Kursen Aufklärung zu betreiben. „Die interessante Frage ist ja, wie viel Prozent der Zahntechniker weltweit nutzen Try-Ins, 3D-Druck oder digitale Planung? Denn aus meiner Erfahrung raus, und das habe ich gelernt bei unseren Kursen, sind ganz viele noch total analog unterwegs und können sich gar nicht vorstellen, was man alles machen kann”, sagt Leimbach.
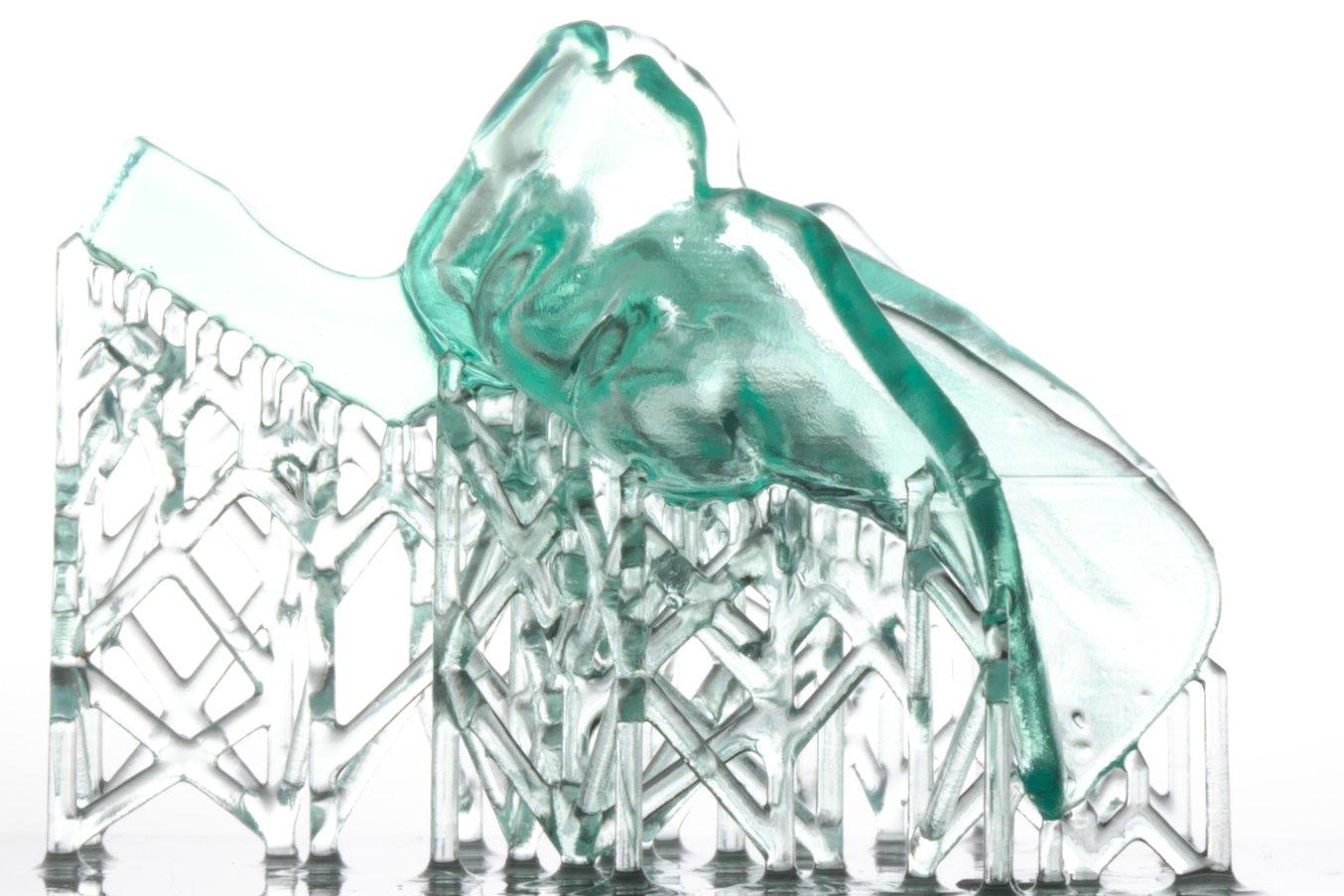
Additive Fertigung ermöglicht eine Vielzahl verschiedener Anwendungen, beispielsweise den 3D-Druck individualisierter Abdrucklöffel mit Custom Tray Resin
Durch einfach zugängliche 3D-Drucker wie den Form 3B+, der spezifisch für zahnmedizinische Anwendungen entwickelt wurde, so erwartet Leimbach, wird der Prozess vollständig digitaler Planung und frühzeitiger Vorstellung der Modelle durch Try-Ins zum neuen Standard der Zahntechnik.
Ich finde das Thema Try-In für die Zukunft extrem wertvoll, weil es uns einfach Zeit sichert und sicherere Arbeitsabläufe generiert. Und ich glaube, das ist noch nicht in allen Köpfen angekommen in der Zahntechnik.
Andreas Leimbach, ZTM & CEO von Die Zahnwerkstatt
Die Implementierung von 3D-Druckern lohnt sich, denn die Anwendungsfelder in der Zahnmedizin sind vielfältig. Neben prototypischen Try-Ins nutzt Leimbach seinen Formlabs-Drucker für die Herstellung individualisierter Abdrucklöffel. Auch für die Fertigstellung des herausnehmbaren Zahnersatzes nutzt er additive Fertigung. So nutzt er das ausbrennbare Material Castable Wax Resin zur Herstellung von Gussformen für Primär- und Sekundärkonstruktionen.
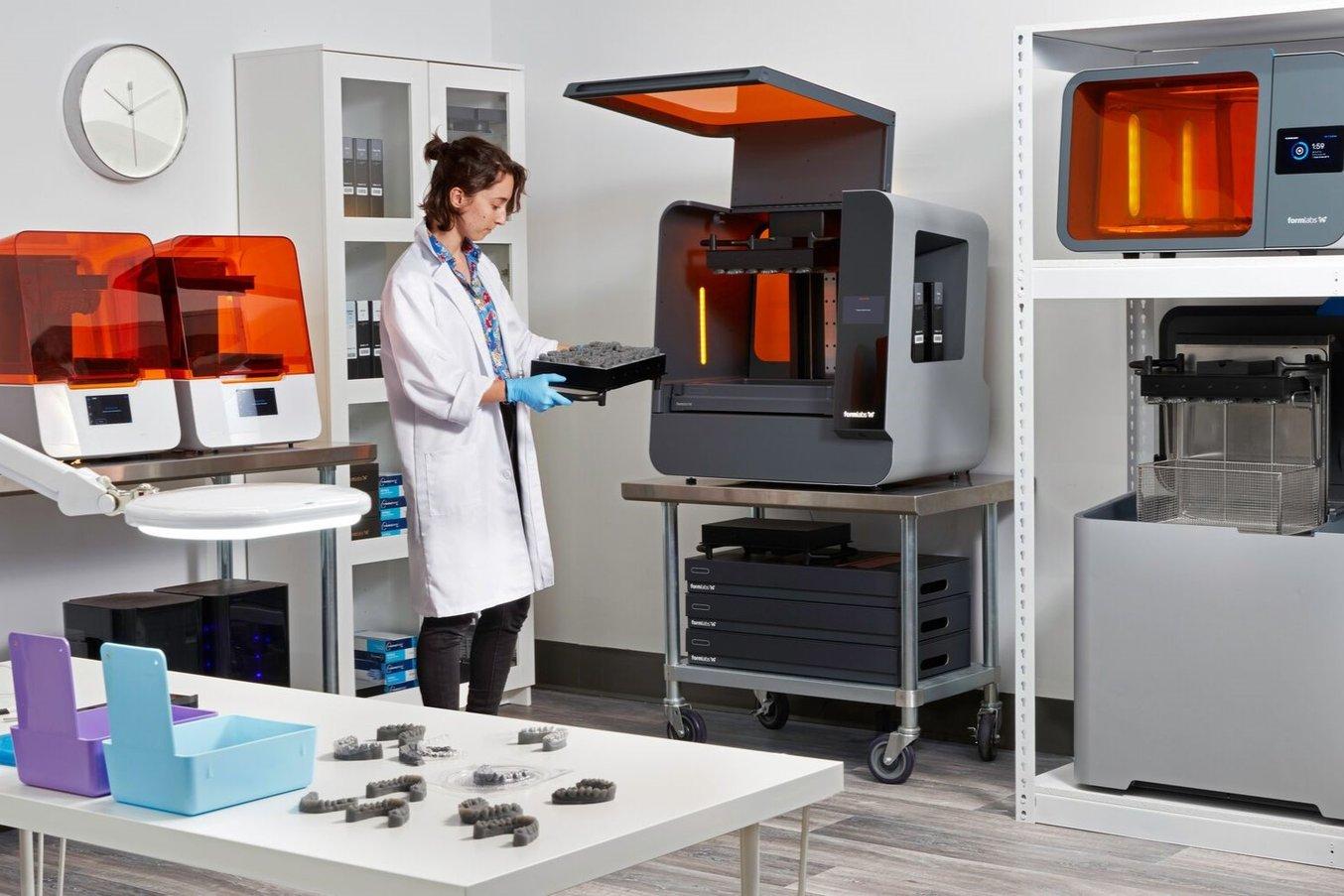
Profi-Tipps von ZTM Stephan Kreimer: wie Sie den Arbeitsablauf in Ihrem Dentallabor optimieren können
Im Webinar erfahren Sie, wie Stephan Kreimer, ZTM und Inhaber des Kreimer Dentallabors, den 3D-Druck in seinem Labor eingeführt hat und wie sein digitaler Arbeitsablauf durch unseren optimierten Desktop 3D-Drucker, den Form 3B+, die Build Platform 2 und unser neuestes Model Resin optimiert wurde.