Thermoforming Clear Appliances With 3D Printed Models
Producing thermoformed clear aligners and retainers enables practices and labs to provide a valuable service to patients and clients while saving time and costs. This application guide details the clear aligner and retainer workflow using a Formlabs 3D printer, from start to finish.
Table of Contents
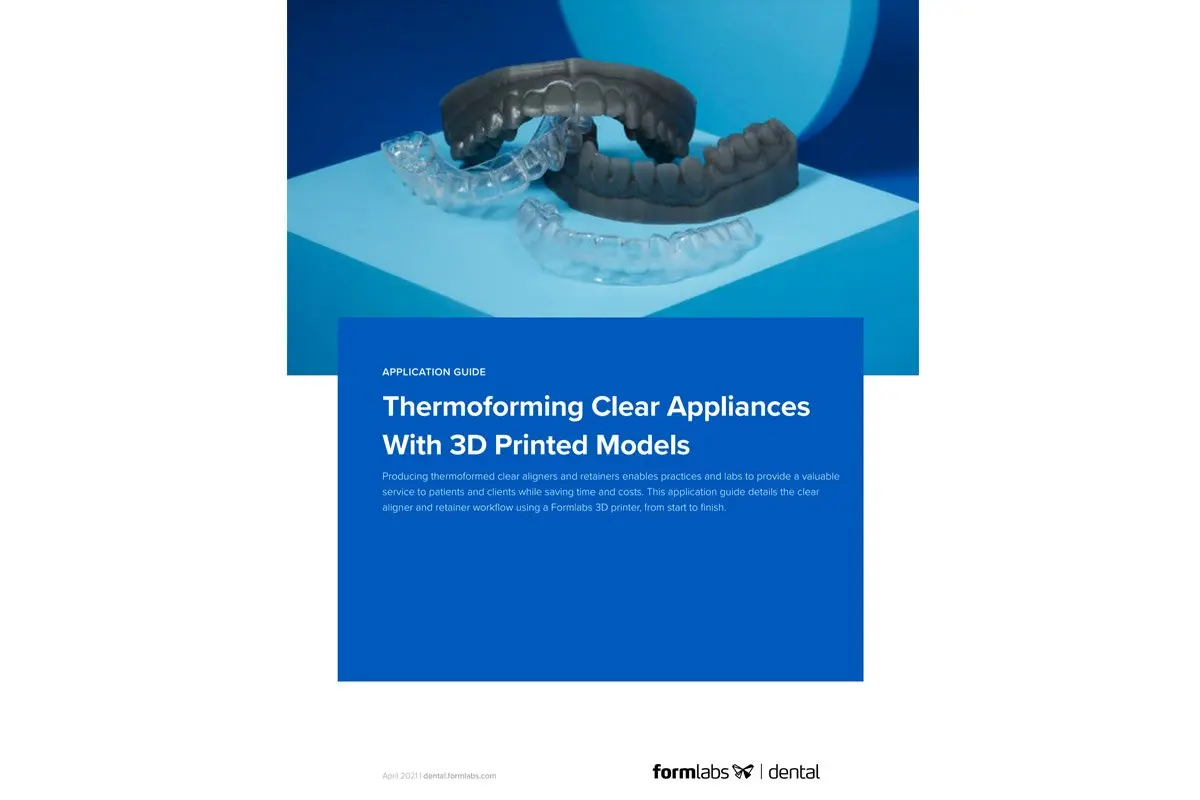
Manufacturing Thermoformed Clear Aligners and Retainers on 3D Printed Models
Would you like to save this guide, print it, or share it with colleagues? Download it as a PDF.
Essentials
Needed From the Orthodontist or Dentist
- A physical or digital impression of the patient's dentition
Required Hardware, Materials, and Software
Made by Formlabs:
- Formlabs SLA 3D printer
- Resin Tank
- Build Platform
- Draft Resin (V2)
- Finish Kit or Form Wash
- Form Cure
- The latest PreForm Software (free) and firmware
Made by Third Parties:
- Thermoforming machine
- Plastic film suitable for machine and appliance
- High or low speed dental lab handpiece
- Double-sided diamond cutting disc
- Scissors
- CAD (computer aided design) software
1. Scan
A digital impression, in .STL format, is required to create the appropriate models in CAD. To acquire this data, scan the patient with a 3D intraoral scanner or scan a physical impression or poured model with a desktop 3D scanner.
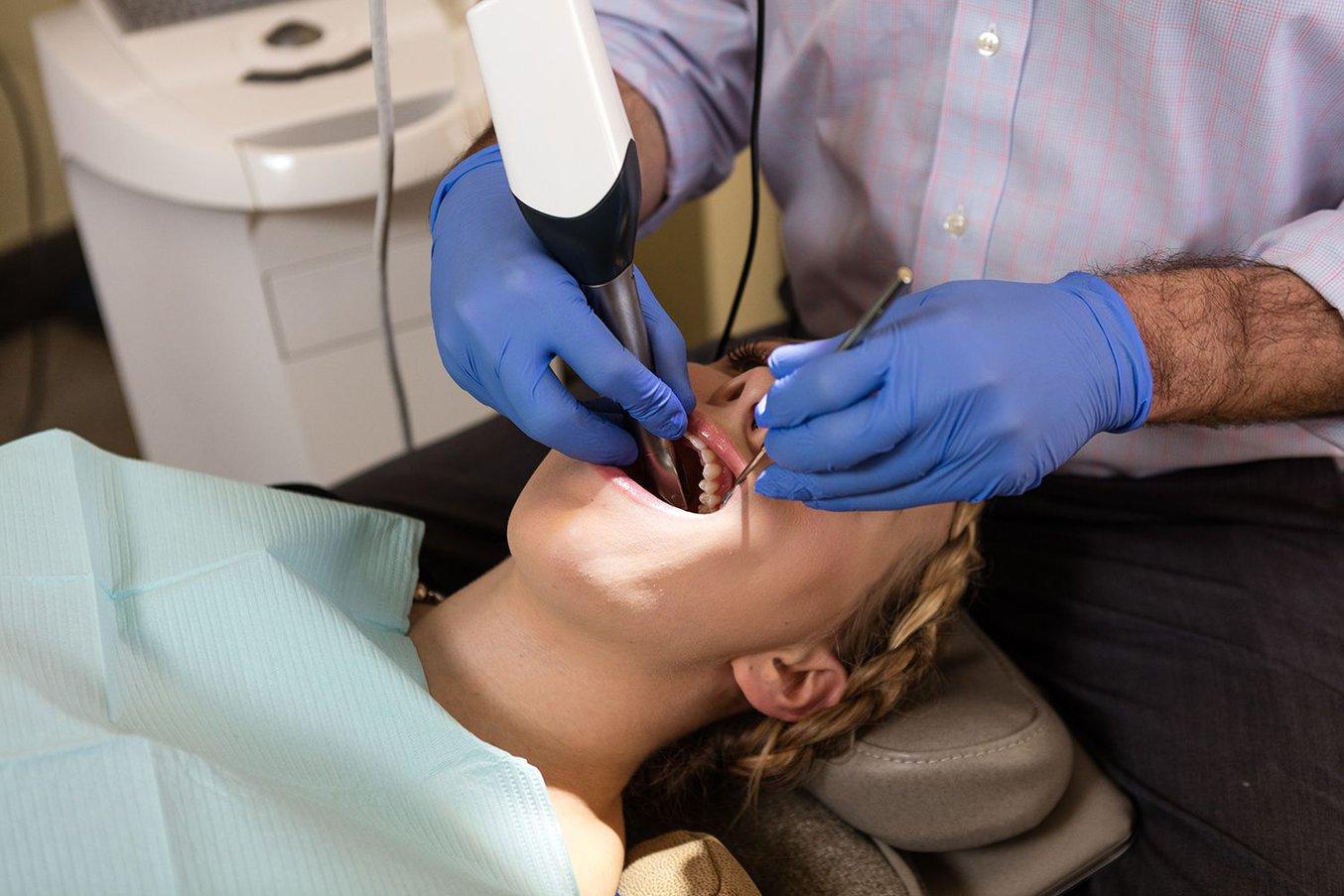
2. Design
Import the digital impression scan files into the appropriate orthodontic or dental computer-aided design (CAD) software. Be sure to select an orthodontic CAD software that offers open .STL file export to ensure compatibility with the Formlabs PreForm software.

Clear aligner treatments require multiple model sets and require specialized orthodontic CAD software.
Treatment planning and setup is done inside the software from the digital impression and sometimes CBCT data. Once complete, each substep is generated into the various stages of the treatment as individual 3D printable (.STL) model files.
Clear retainers require a simple replica or diagnostic model file.
A digital impression is brought into a model building software, which is used to trim, base, and prepare it. The software produces a 3D printable (.STL) model file.
2.1 Design Options
Orthodontic and model software is changing rapidly, and today, there are many options to choose from. We highly recommend doing your own research on the various software options to find what's best for you and your dental laboratory or practice. The following table should be used as a starting point in finding the right CAD software or service provider.
2.2 Design Recommendations
Chamfer or Plane Cut
Chamfering the model base makes removing parts significantly easier.
This can typically be done easily in dental CAD software by using a plane cut tool at the rear of the model (see 1).
Hollow Models
Some dental CAD software produces hollow models.
If hollowing a part, ensure that wall thickness is at least 3 mm thick (see 2).
When designed correctly, hollow models can decrease print time and reduce unit cost.
Note
Formlabs recommends printing non-hollow or solid models to reduce post-processing difficulty and breakage.
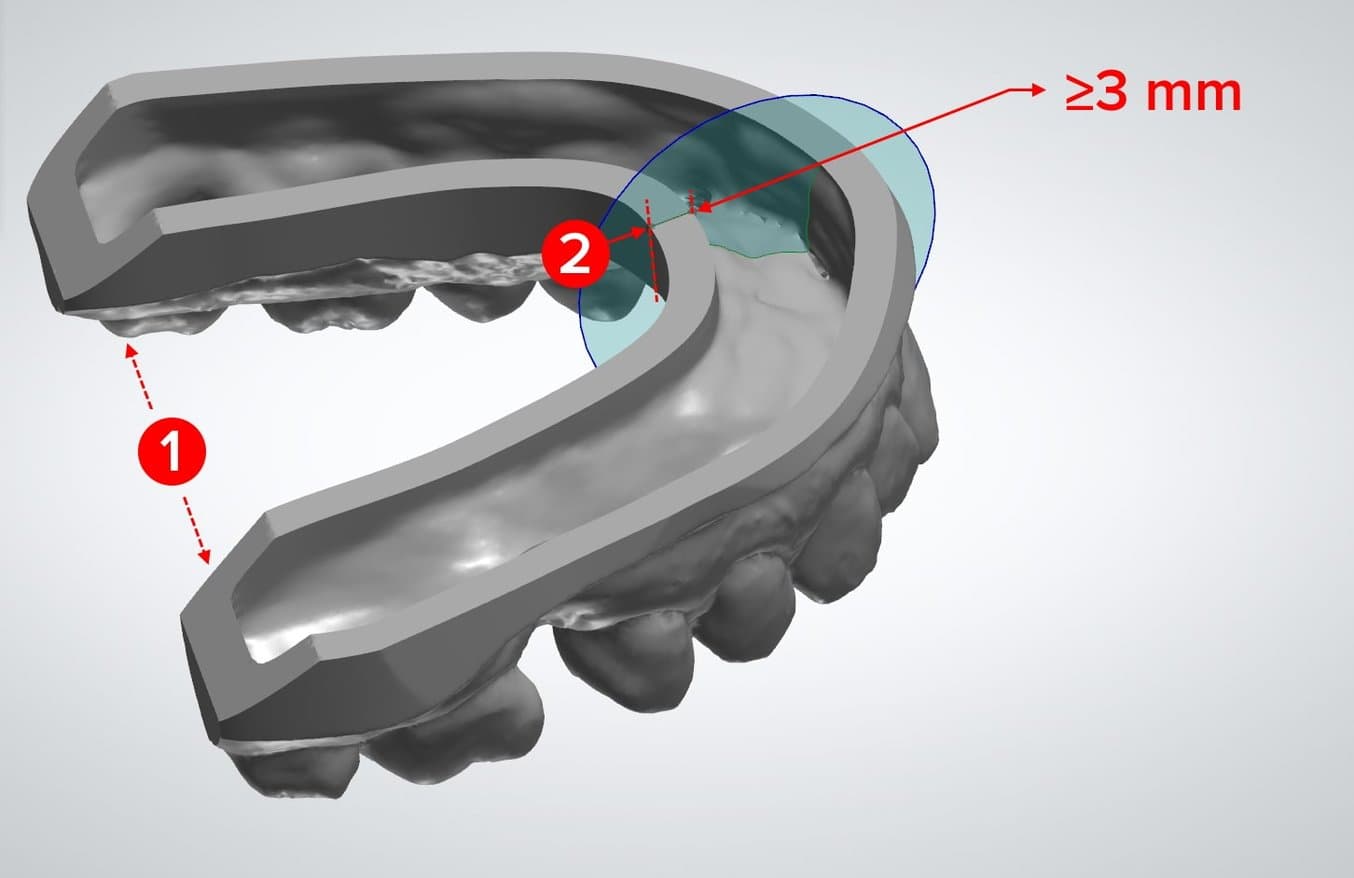
Cupping and Hollow Models
When 3D printing hollow models directly to the build platform it's important to take proper precautions in order to prevent cupping.
Preform will detect and show cupping issues in yellow (see 1).
The easiest way to prevent cupping is to add drain holes or using a cutting plane tool on the back of the model (see 2).
Tip: Scan to Model can modify models built in other CAD softwares. You can use this functionality to prevent cupping, add pry points, and shorten models. Watch this video to learn how.
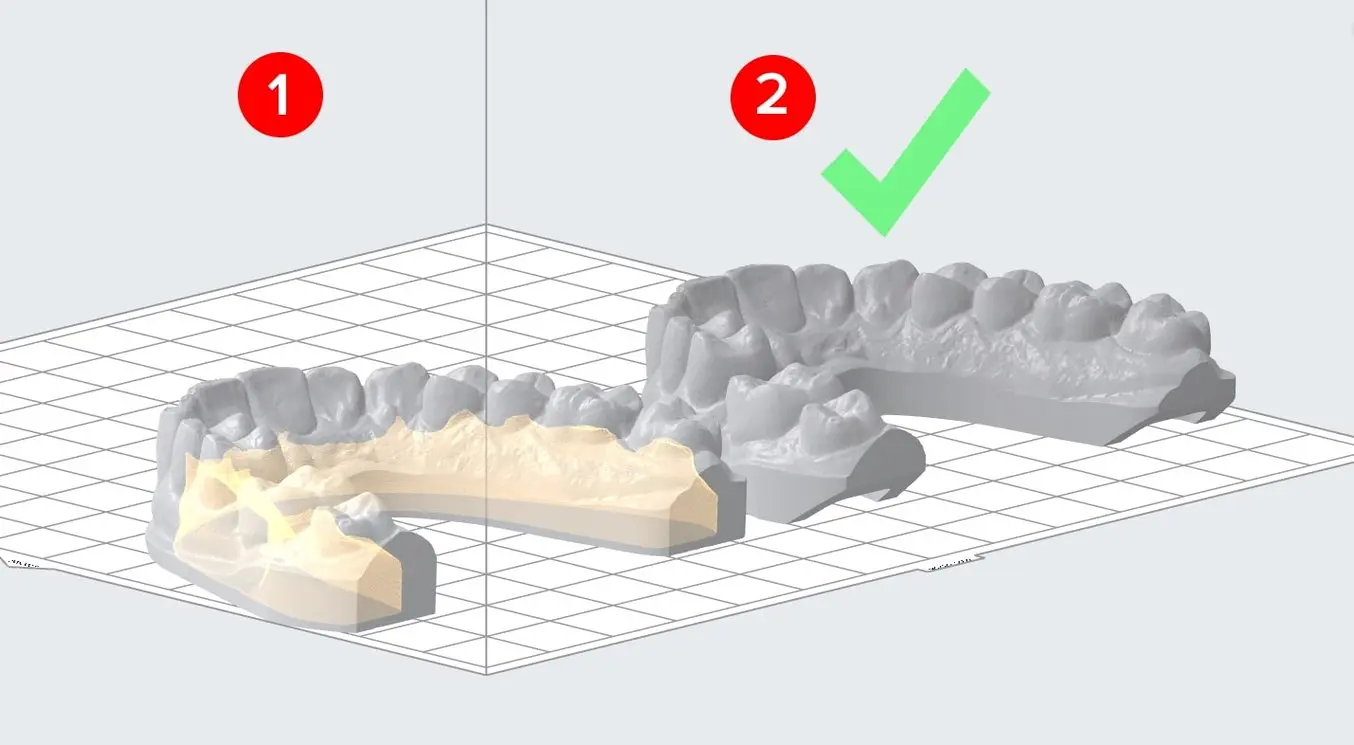
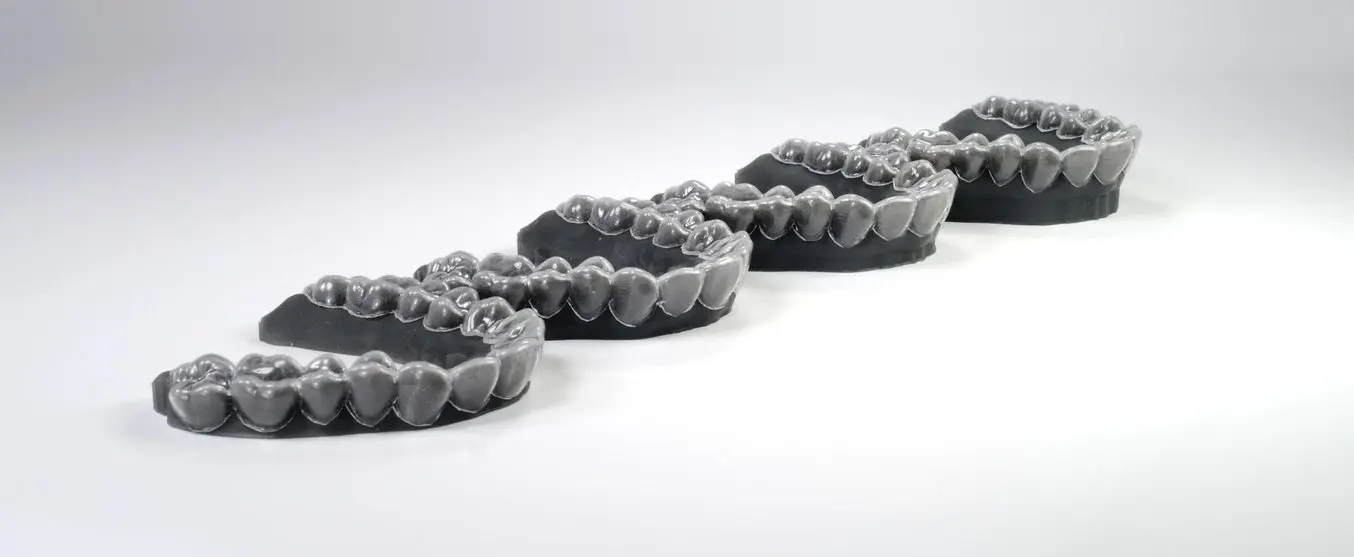
Model Height
The height of the model height will determine how far the thermoforming material will be stretched around the model.
You can add consistency to your appliances by:
-
Building your models to a set height in CAD (we’ve found 15 to 20 mm is best)
-
Use pellets during thermoforming (more information below in the thermoforming section 5.2.3)
2.3 Prepare and Print With Formlabs Scan to Model
Note
If you are producing models for aligners or using third-party dental CAD software this section can be skipped. Proceed to section 3.
Intraoral scanning equipment captures digital impressions of the mouth to form a high-detail 3D scan, but they create open meshes or uneven edges. Scan to Model is a tool within our PreForm print preparation software that can remove some extraneous data from the scan and creates a base. This is ideal for replica diagnostic models for treatment planning and appliances like thermoformed clear retainers.
Note
The Scan to Model tool is only available on printers that have been optimized for dental materials, like the Form 2, 3B, and 3BL. Be sure to have the latest PreForm version installed and a compatible printer selected in Job Setup.
Looking to create models from multiple scans? Watch our Advanced Multiple Files Walkthrough.
You can also use the Scan to Model feature to plane cut models built in another CAD software to avoid cups in printing. Watch our tutorial.
2.3.1 Job Setup
Open the latest version of PreForm on your computer.
Set up the print in the Job Info menu, on the right-hand side. Make sure that you are connected to a Form 2, Form 3B, or Form 3BL printer on your network.
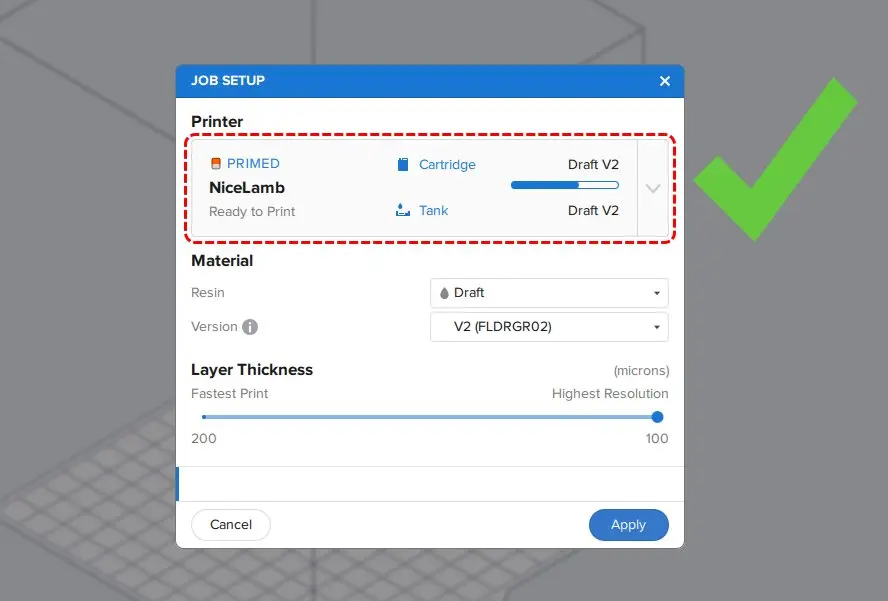
Draft V2 Resin is recommended for creating thermoformed appliances.
For fast printing, use 200 microns.
For moderately fast printing and smooth surfaces, use 100 microns.
Once you have made your selection, click Apply to close the menu.
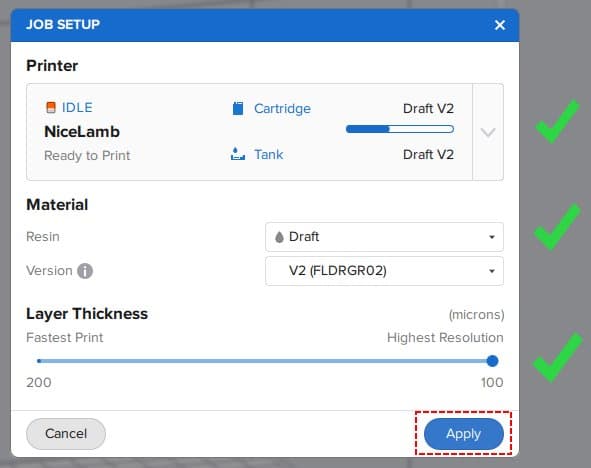
2.3.2 Import Scan
With a Form 3B, Form 3BL, or Form 2 selected in the Job Setup menu, the Scan to Model icon will be present on the left of the screen.
Click the Tooth Icon on the left menu to open Scan to Model.
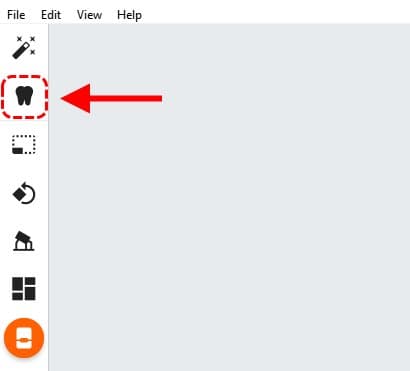
Click the Import button.
Locate the file (STL) on your computer or network.
Click OK.
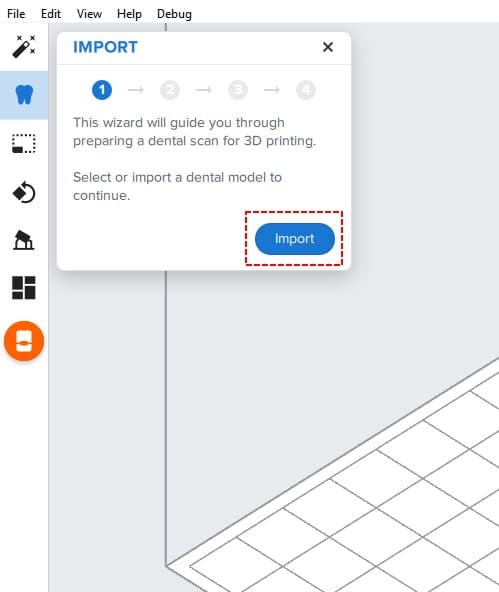
2.3.3 Orient Scan
Use the rotation tools to position the digital impression with the occlusal surface facing away from the build plate.
Click Next.
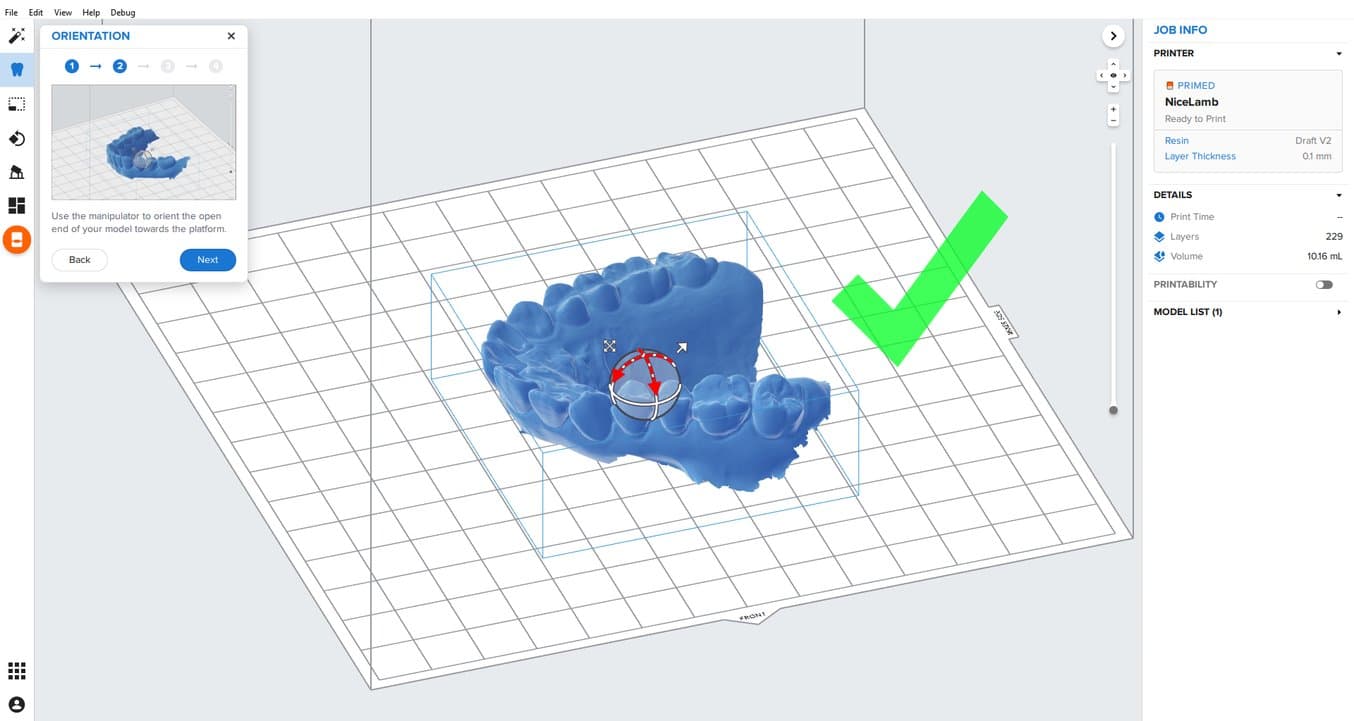
2.3.4 Trim Unneeded Data
Remove excess scan data using the Trim tool. Move the Trim Plane Position Slider tool to move the trimming plane. It starts at zero; leave it there to keep all scan data.
We recommend trimming models for the fastest print time and least material use.
For a full palate model, it is best to leave the trimming plane at zero.
Review the results by rotating the view around the part to ensure important anatomy isn’t being removed.
Click Next.
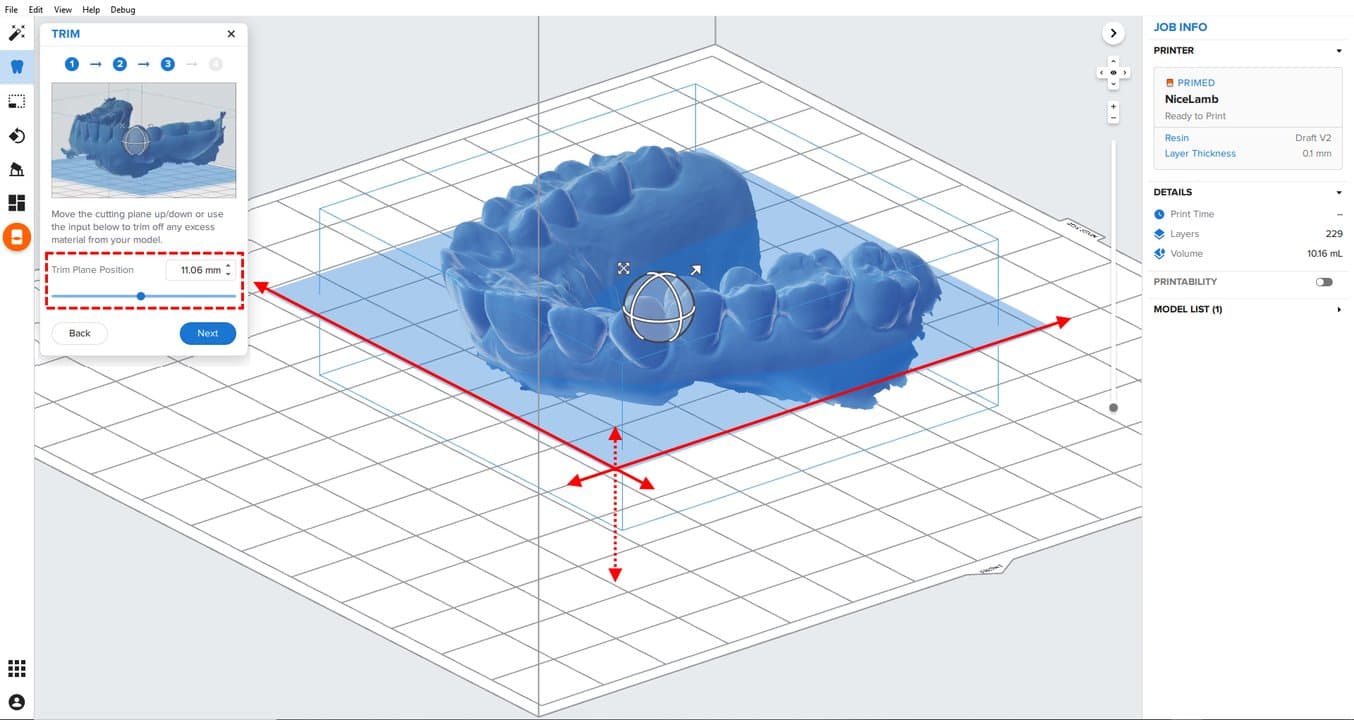
2.3.5 Create Base
Changing the base height adds a base to the digital impressions trimming position, which is particularly important for palatal models.
Move the Base Height Slider or type how many millimeters should be added from the lowest point (trimming plane).
Click Create and the model will be generated.
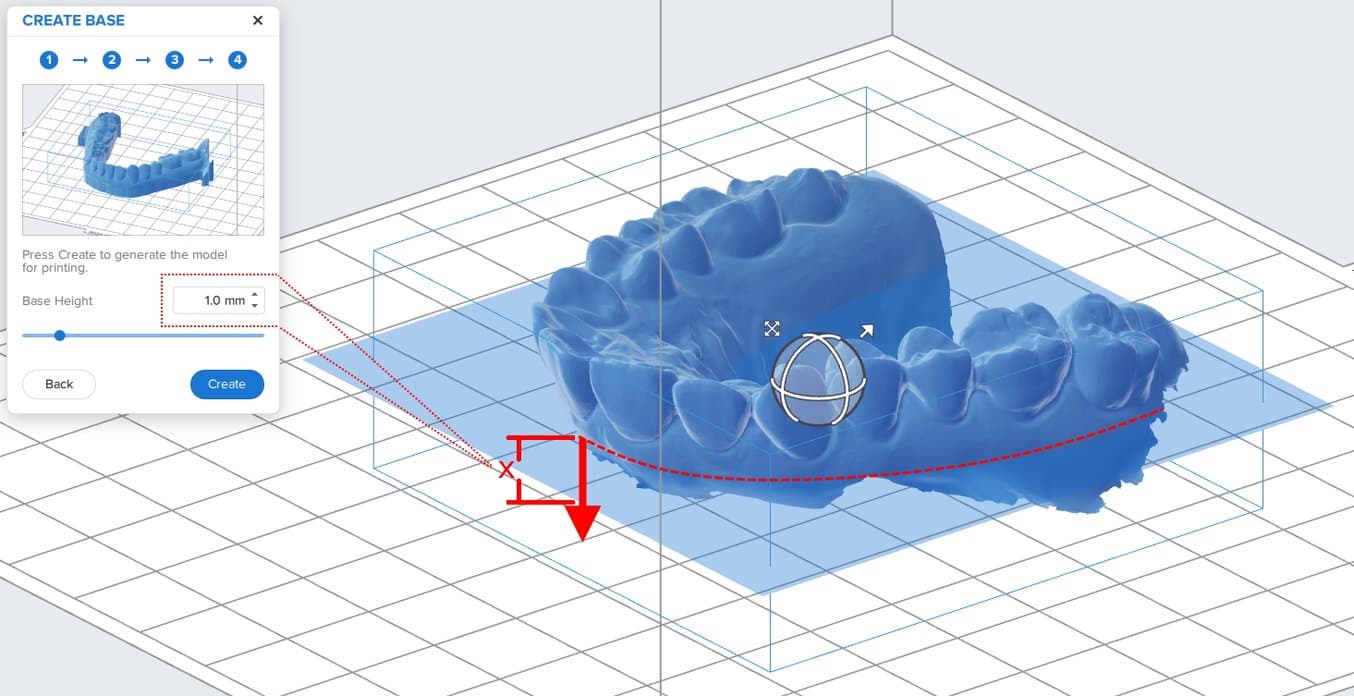
Note
Using Scan to Model allows you to skip many of the next sections in “Print”. For information on setting up models vertically go to section 3.4 and for setting up models directly on the build platform (recommended) go to section 3.6.
3. Print
3.1 Import File(s)
Import or open the model file(s) by dragging the STLs into PreForm, or use the File menu to locate them on your computer or network.
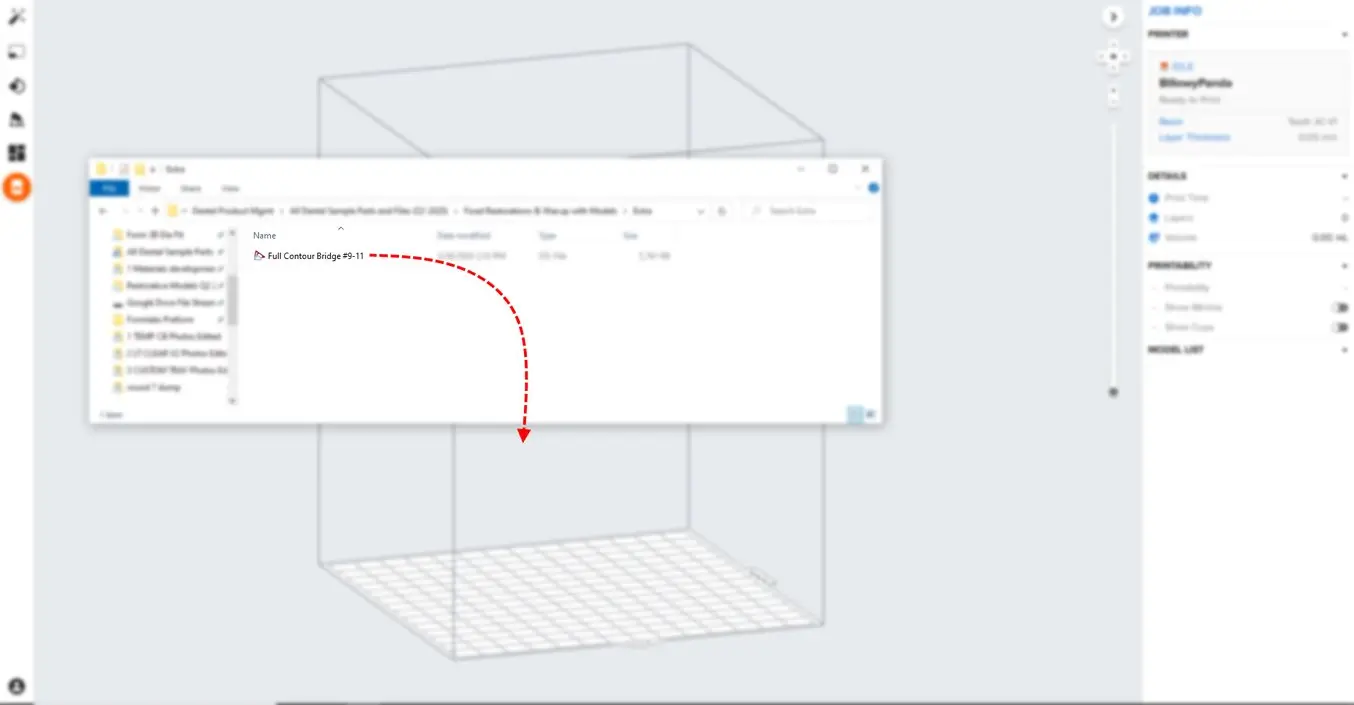
3.2 Material Selection
Select the material for printing by clicking the printer box in the Job Info menu on the right hand side.
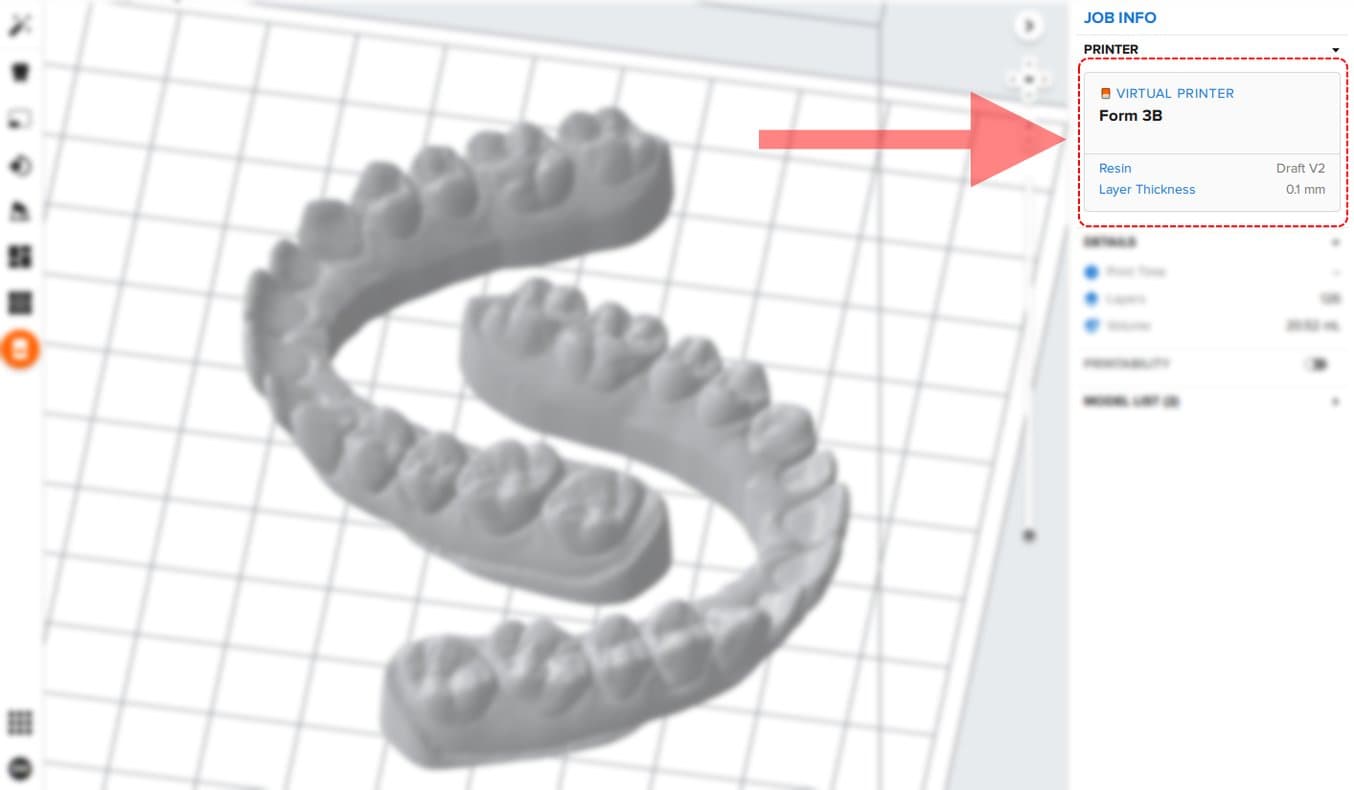
Locate Draft in the material dropdown.
Note: Be sure to use Draft V2, we no longer recommend Draft V1.
For models needing to be printed as fast as possible use 200 micron settings and print them directly on the build platform.
For high resolution models, printed directly to the build platform and vertically printed models, use 100 micron settings.
Note
For the best facial anatomy we do not recommend printing vertical models using 200 micron settings.
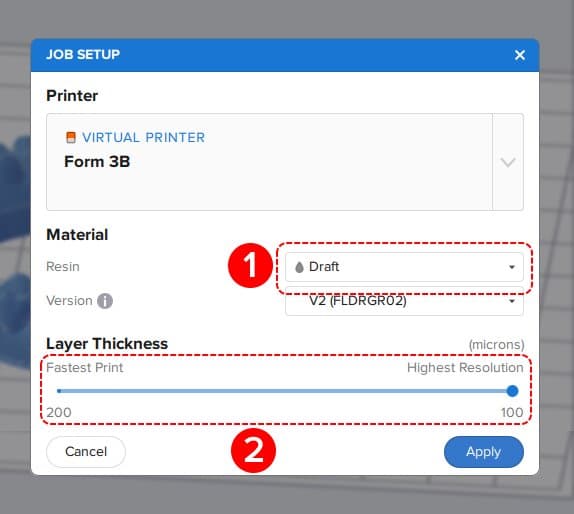
3.3 Print Job Set-Up
The two ways we recommend printing orthodontic models:
-
Directly on the build platform (see 1, for highest accuracy and speed)
-
Near vertical (see 2, for the most parts per print)
When printing vertically we recommend a model angle between 65 and 75 degrees (see 2), see the instructions in the following sections to make this process easy.
Note
If you prefer printing on supports, but not vertically, the best accuracy is achieved when the model is horizontal to the build platform (see 1) without any angulation.
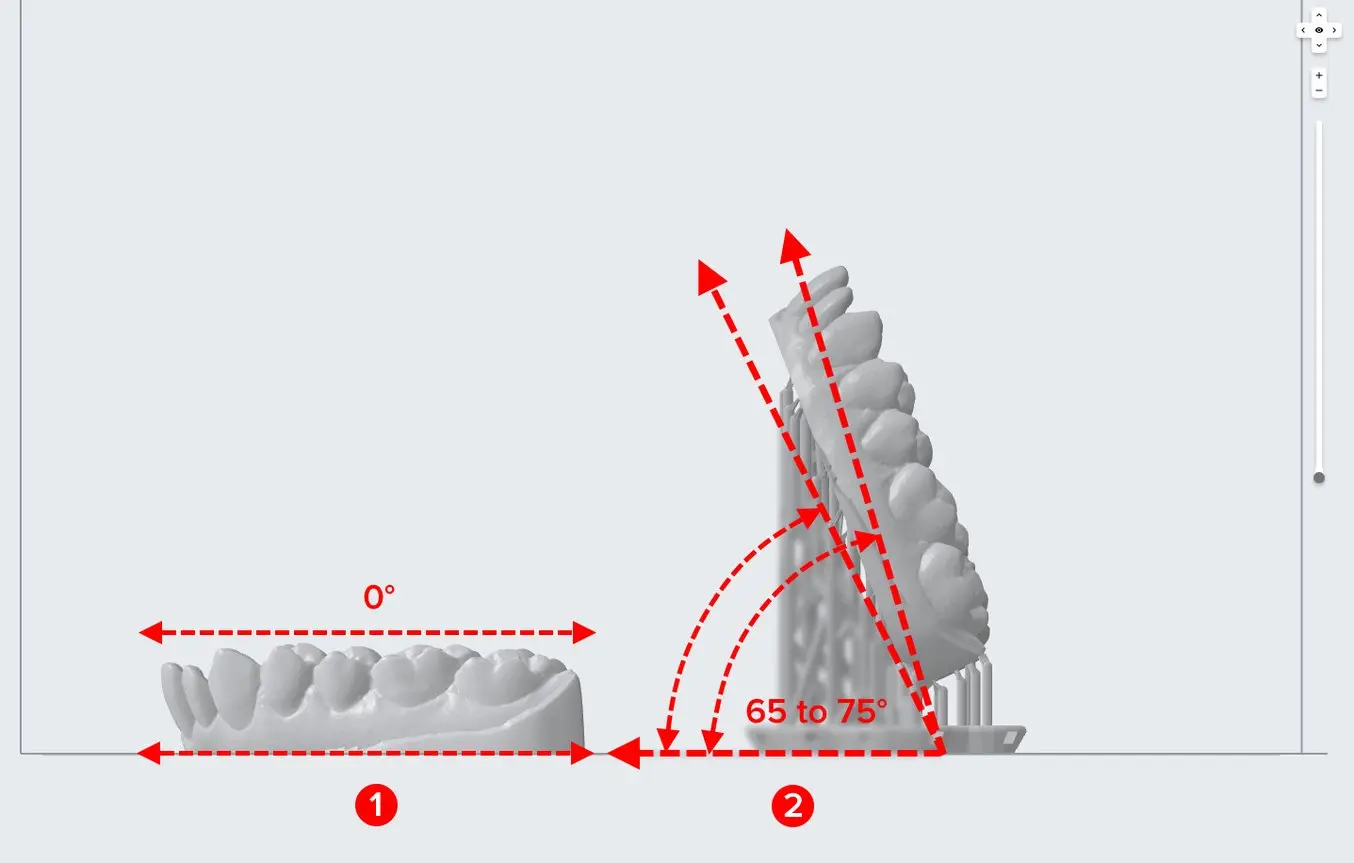
3.4 Starting Orientation
Regardless of final orientation, always start by snapping the models down to the build platform.
Click the “Orientation” button on the left menu (see 1).
Once open, click the button “Select Base…” (see 2).
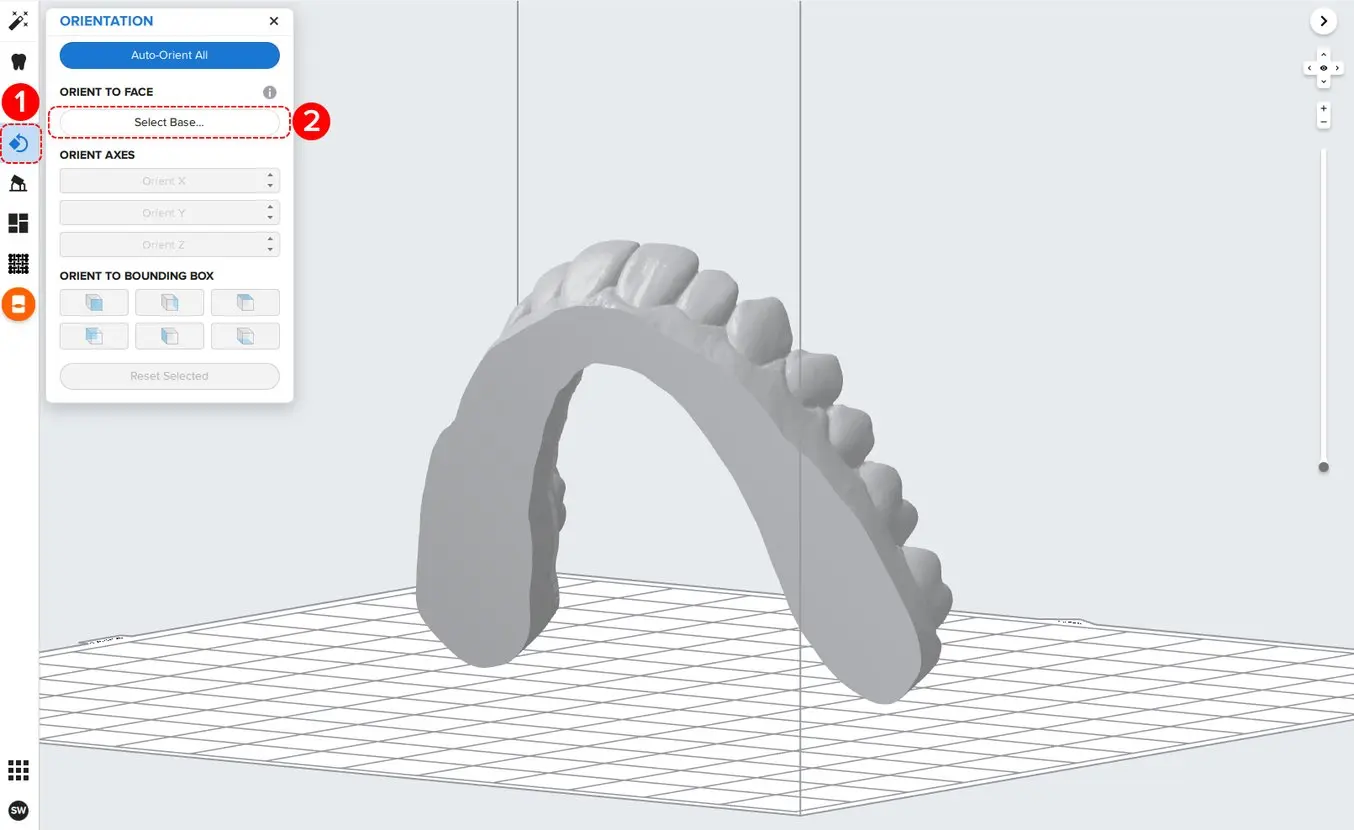
Move your mouse cursor to the bottom surface of the model, you should see an orange arrow, and click.
This should snap your model flush to the build platform.
If you are printing models directly to the build platform you can skip to the second to last section “Printing Layout”.
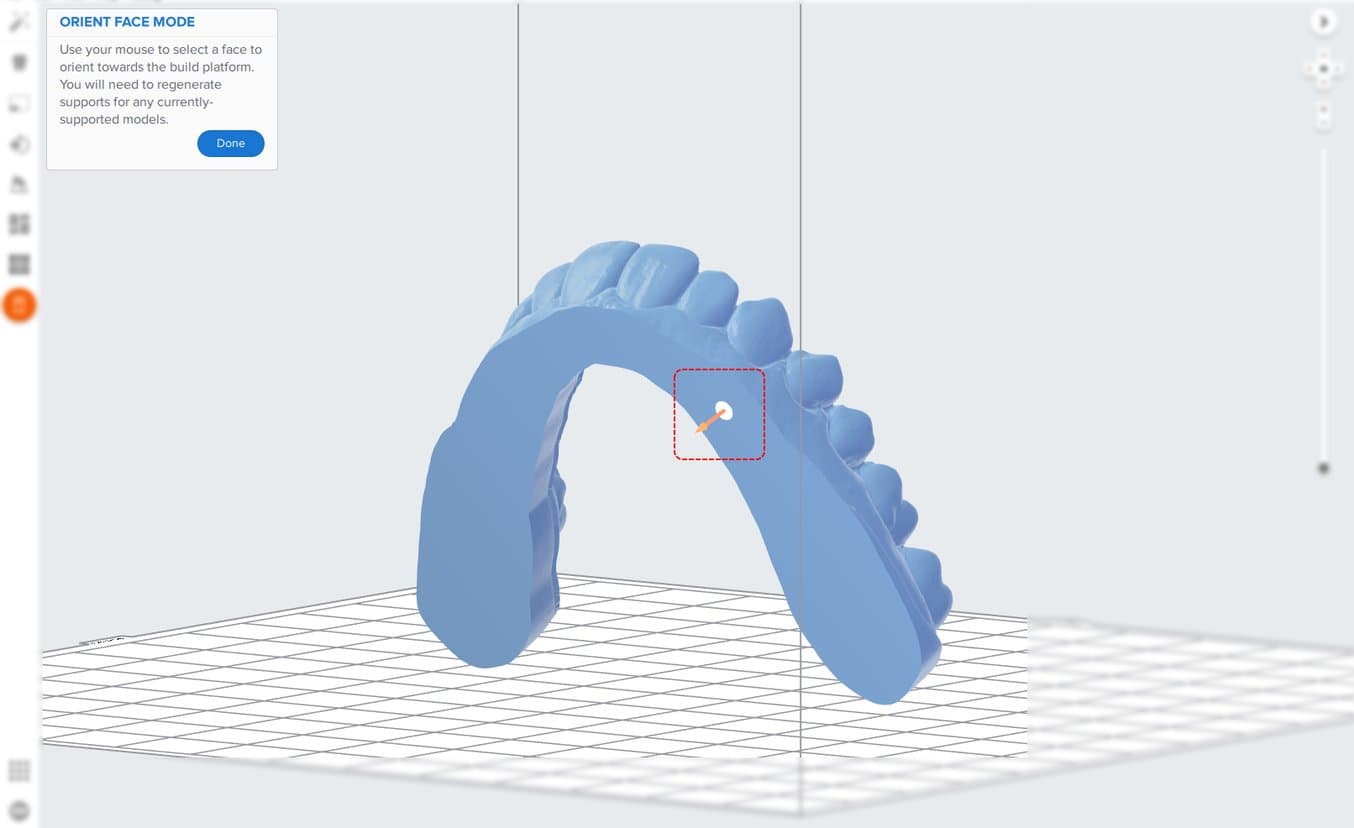
Typically, models printed directly to the platform do not require any support structures or additional steps.
When printing parts directly on the build platform, you might see a printability warning. If the part is snapped down to the build platform as outlined in the above section, it is okay to ignore this error.
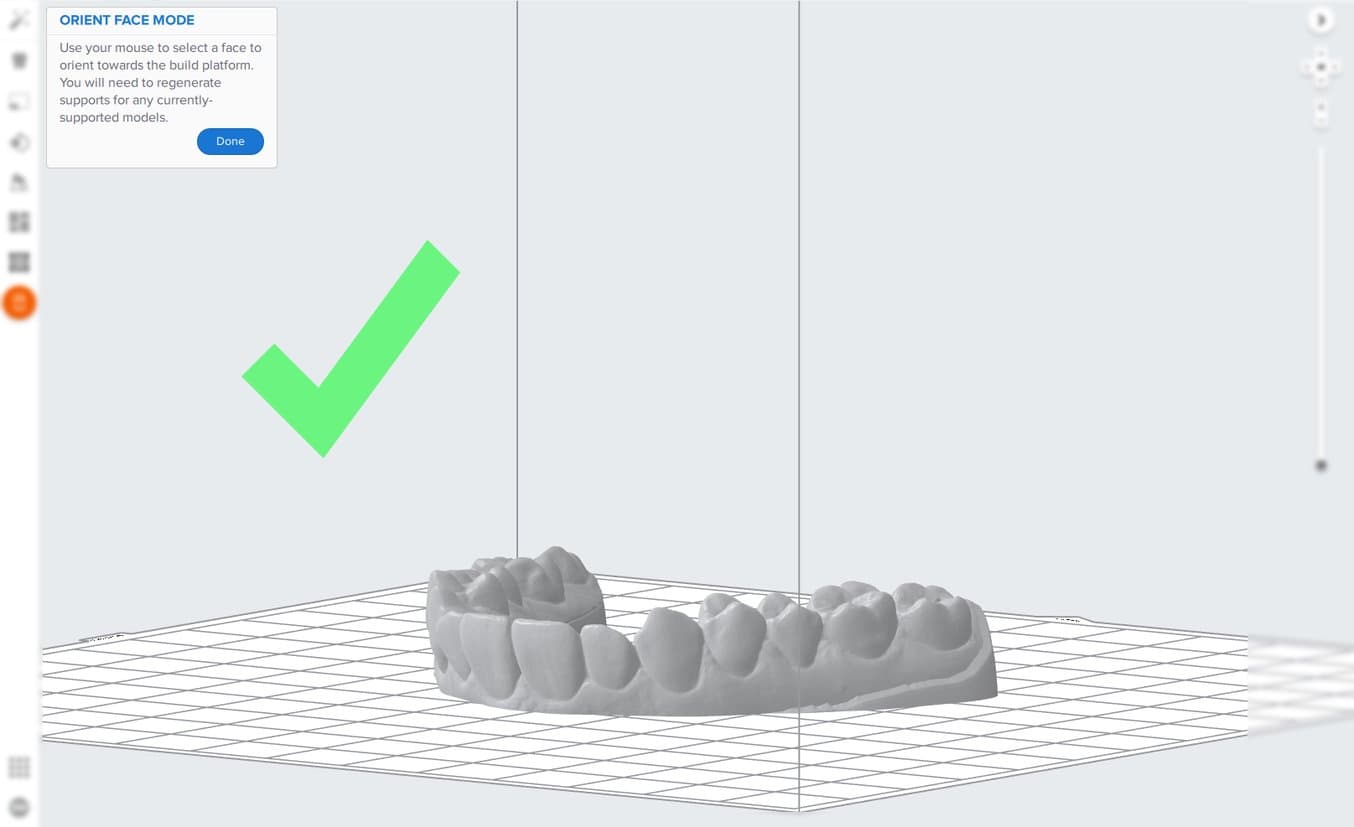
3.5 Vertical Models and Support Structures
Tip: Click here to watch a video tutorial of setting up models vertically.
When setting up your models for vertical printing, rotate and drag the models so the rear-most molars are in similar alignments
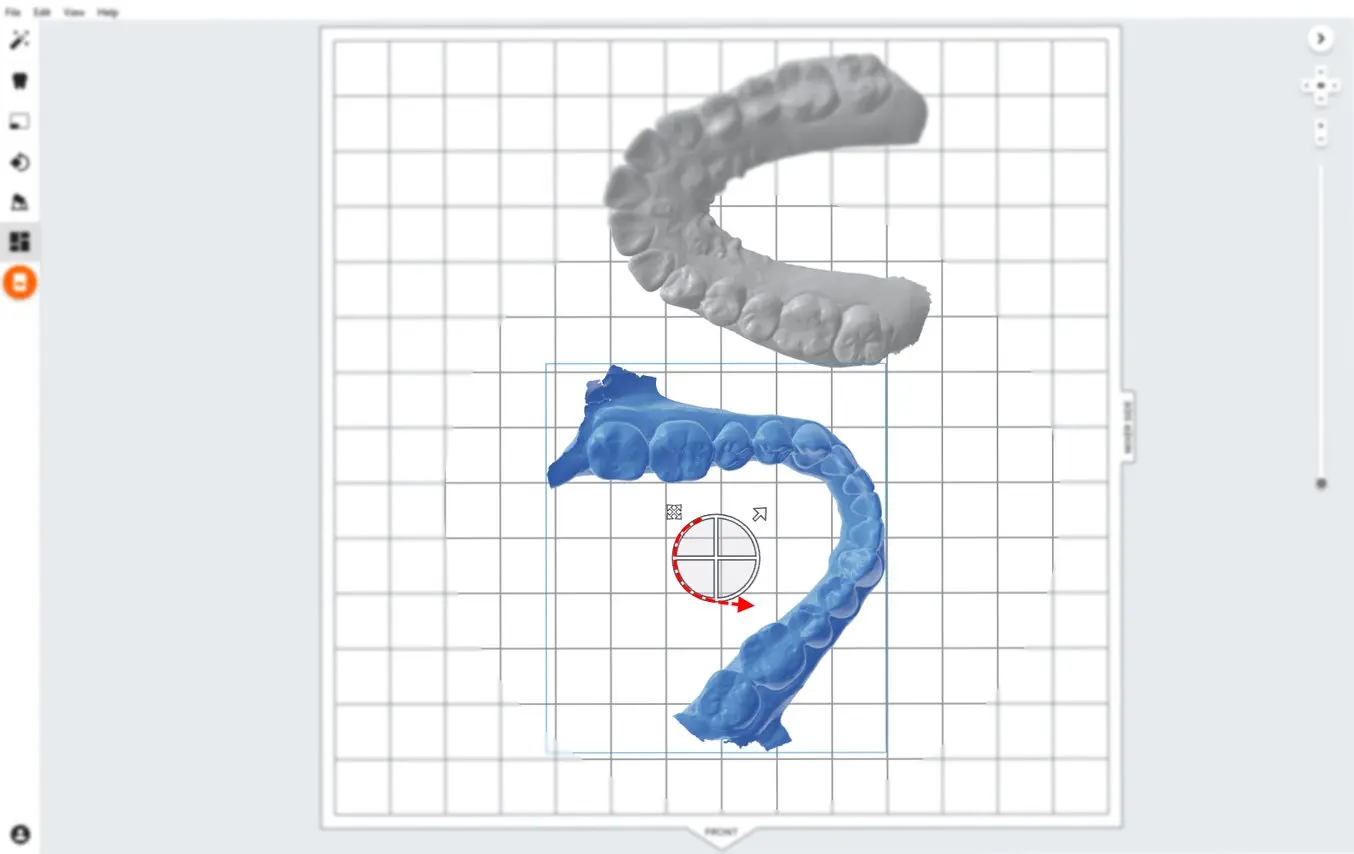
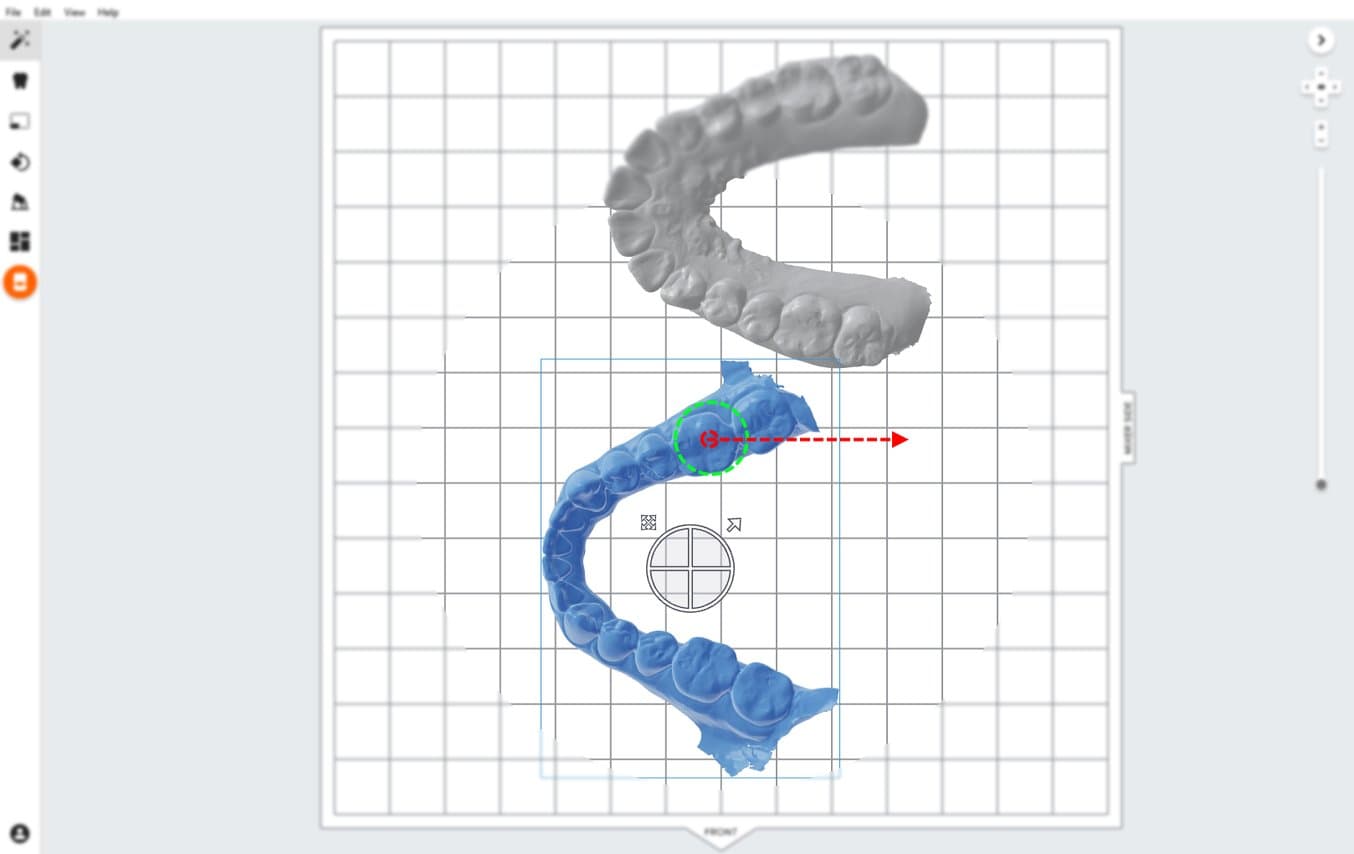
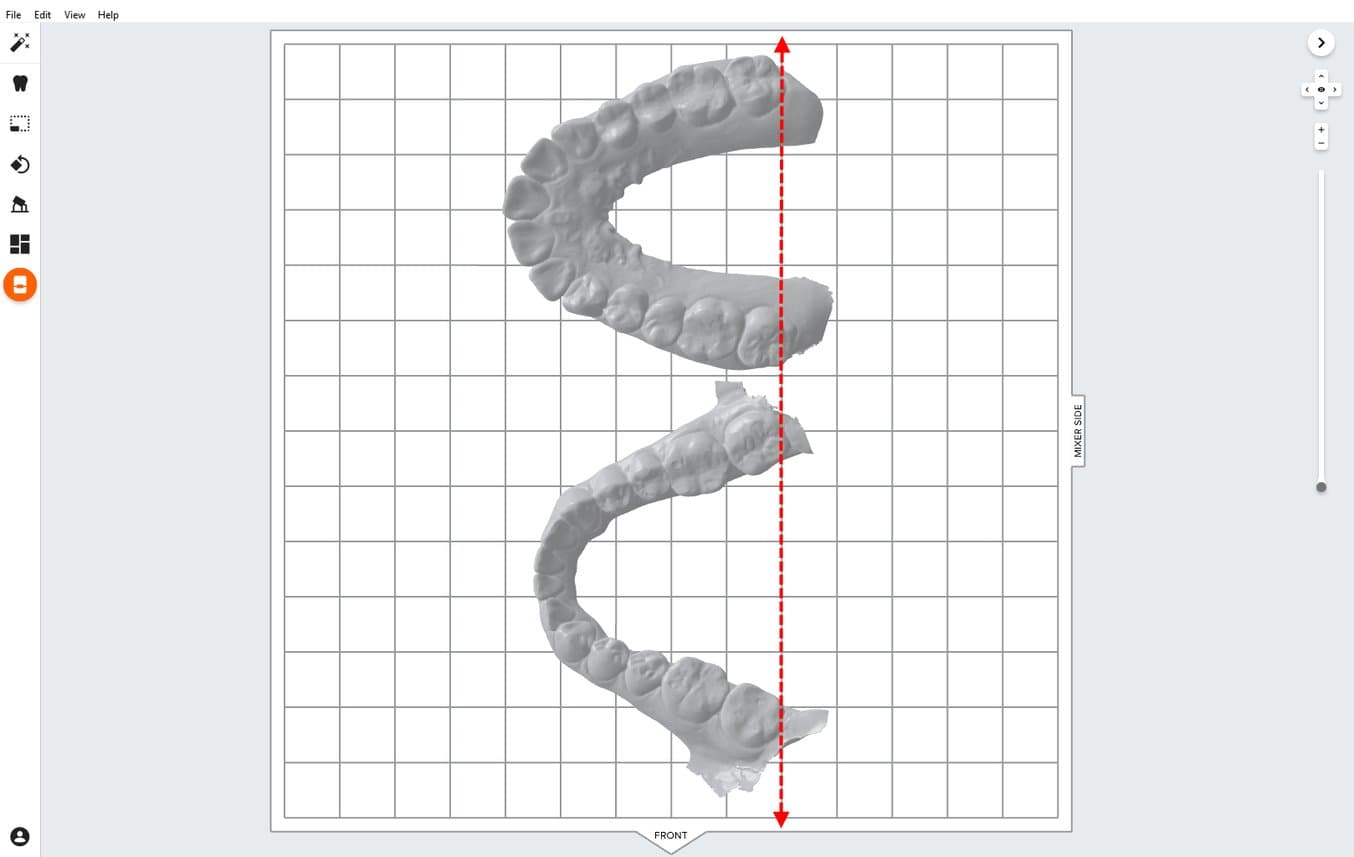
Tip: When setting up multiple models you can quickly get them into position by rotating and overlapping the parts. The corner or edge of the build platform can be helpful as a stop.
This technique also works great when using Scan to Model.
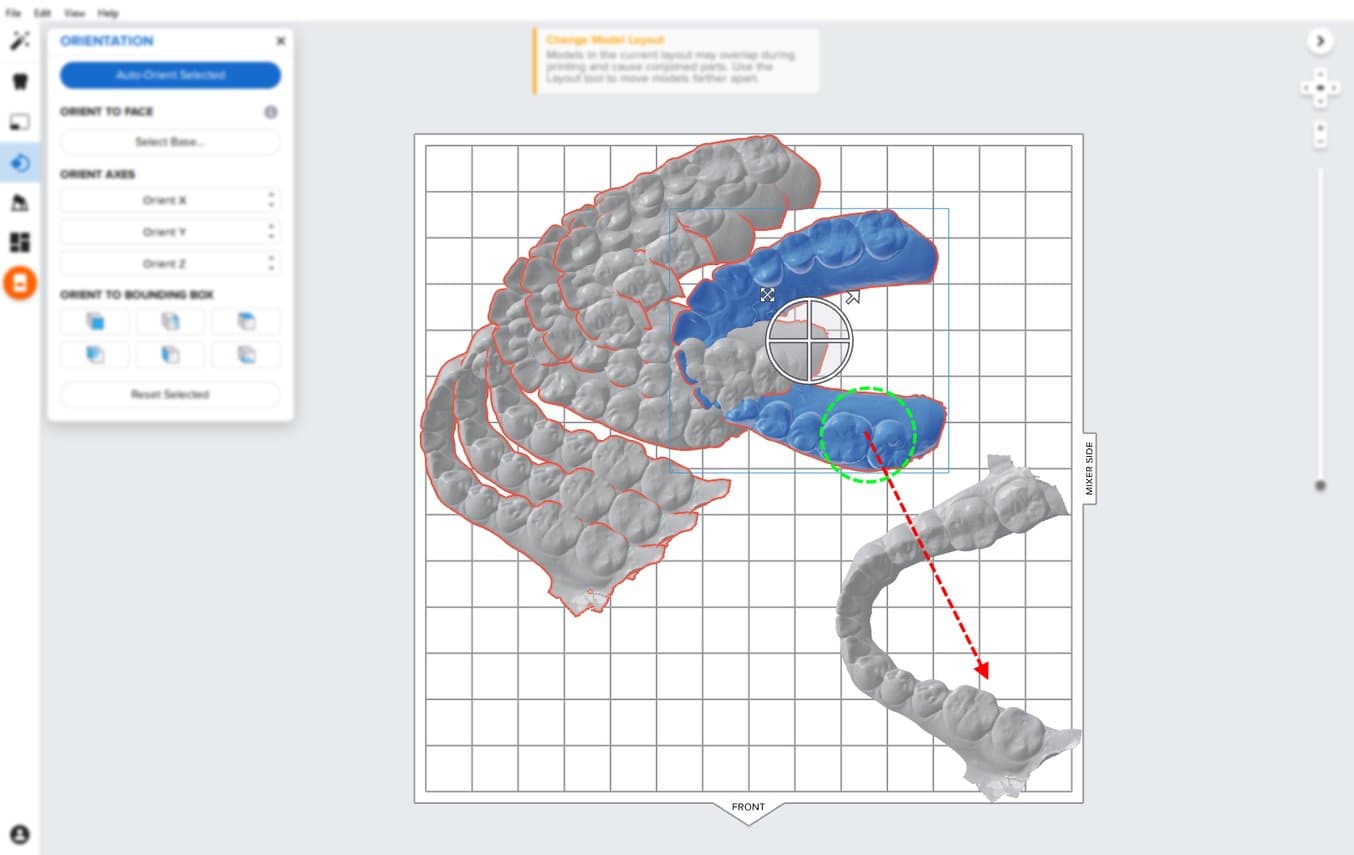
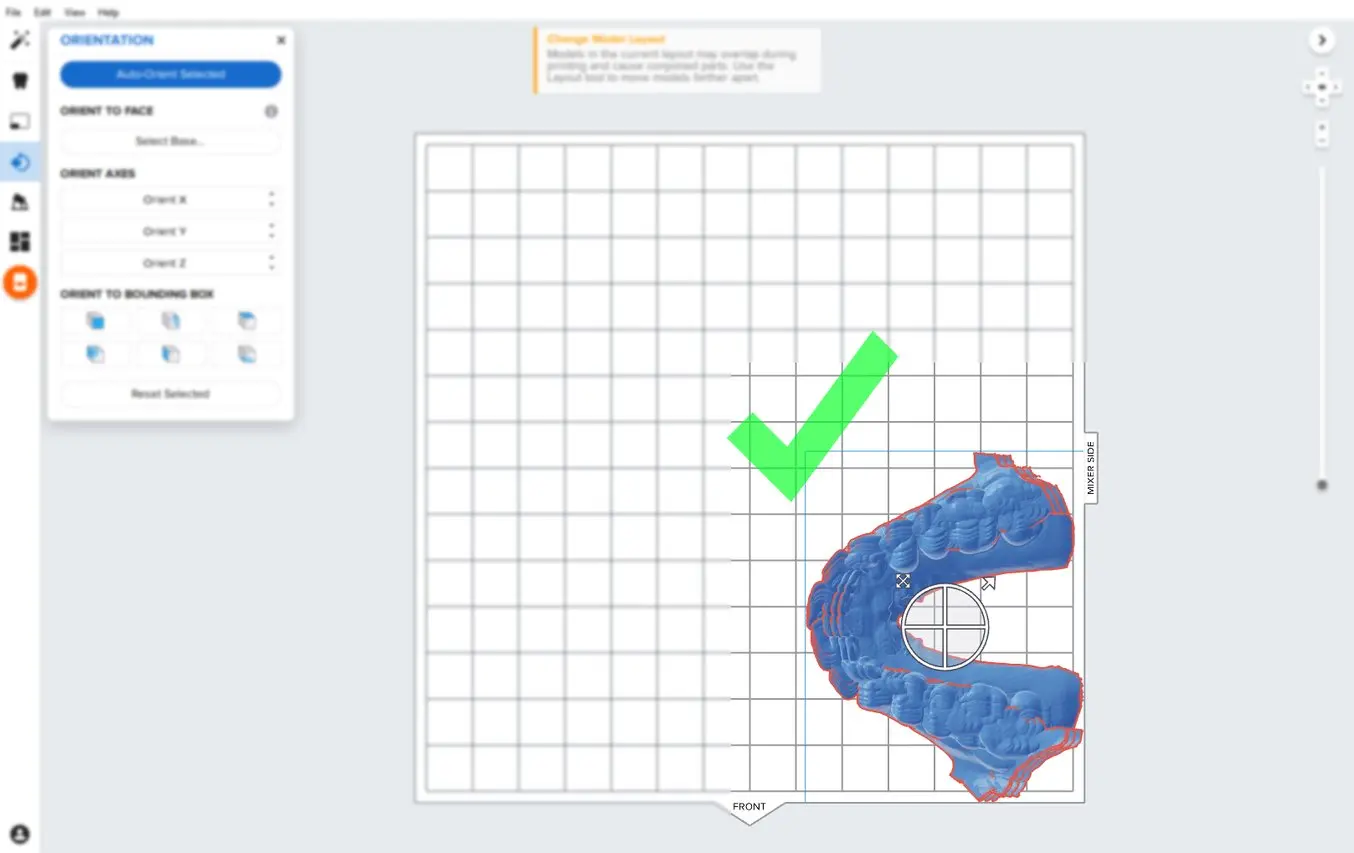
Once the models are positioned, view the build from the side. Use the view tools on the top right of PreForm as shown.
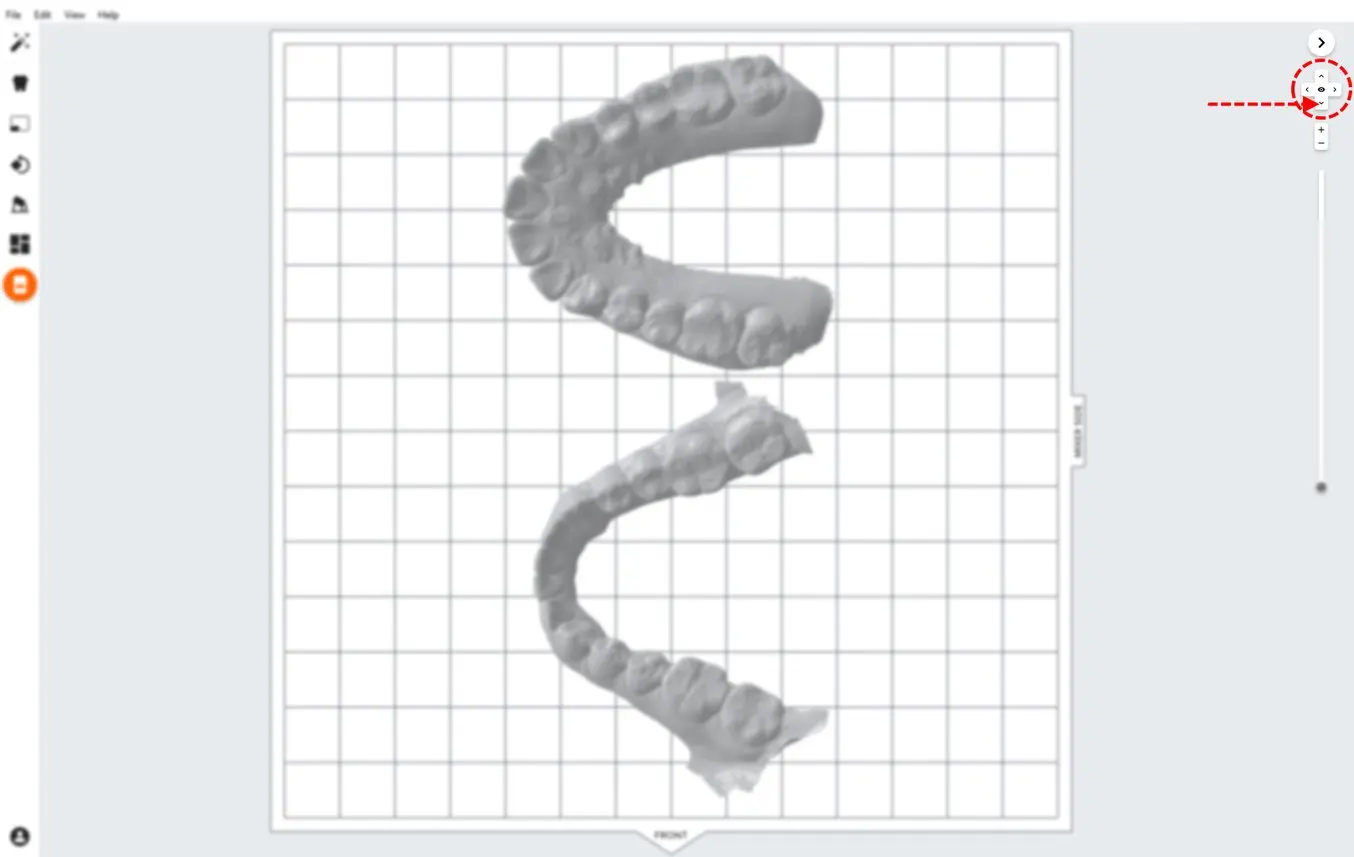
Select all the models by clicking and dragging over all the models.
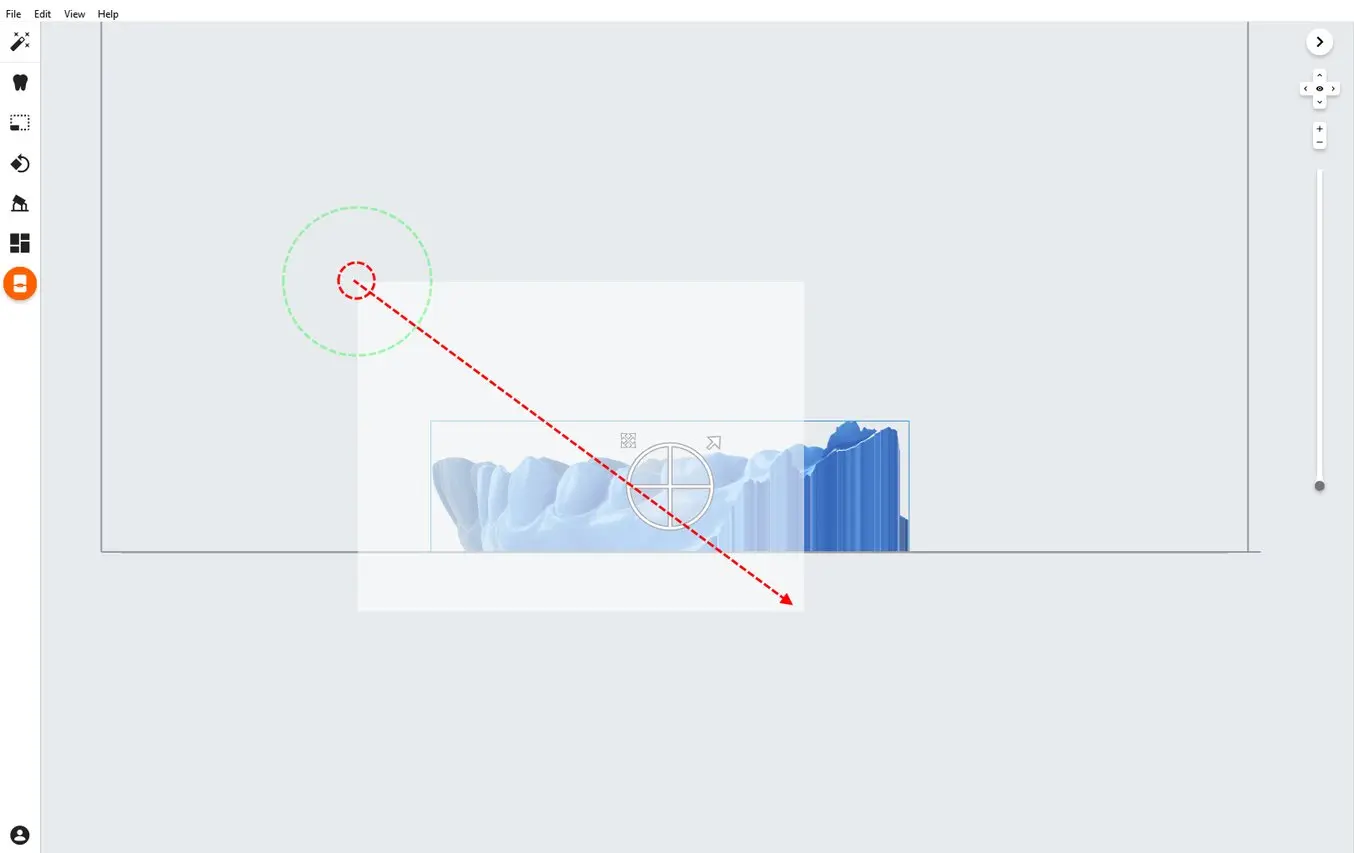
Once selected, rotate the models to near vertical orientation.
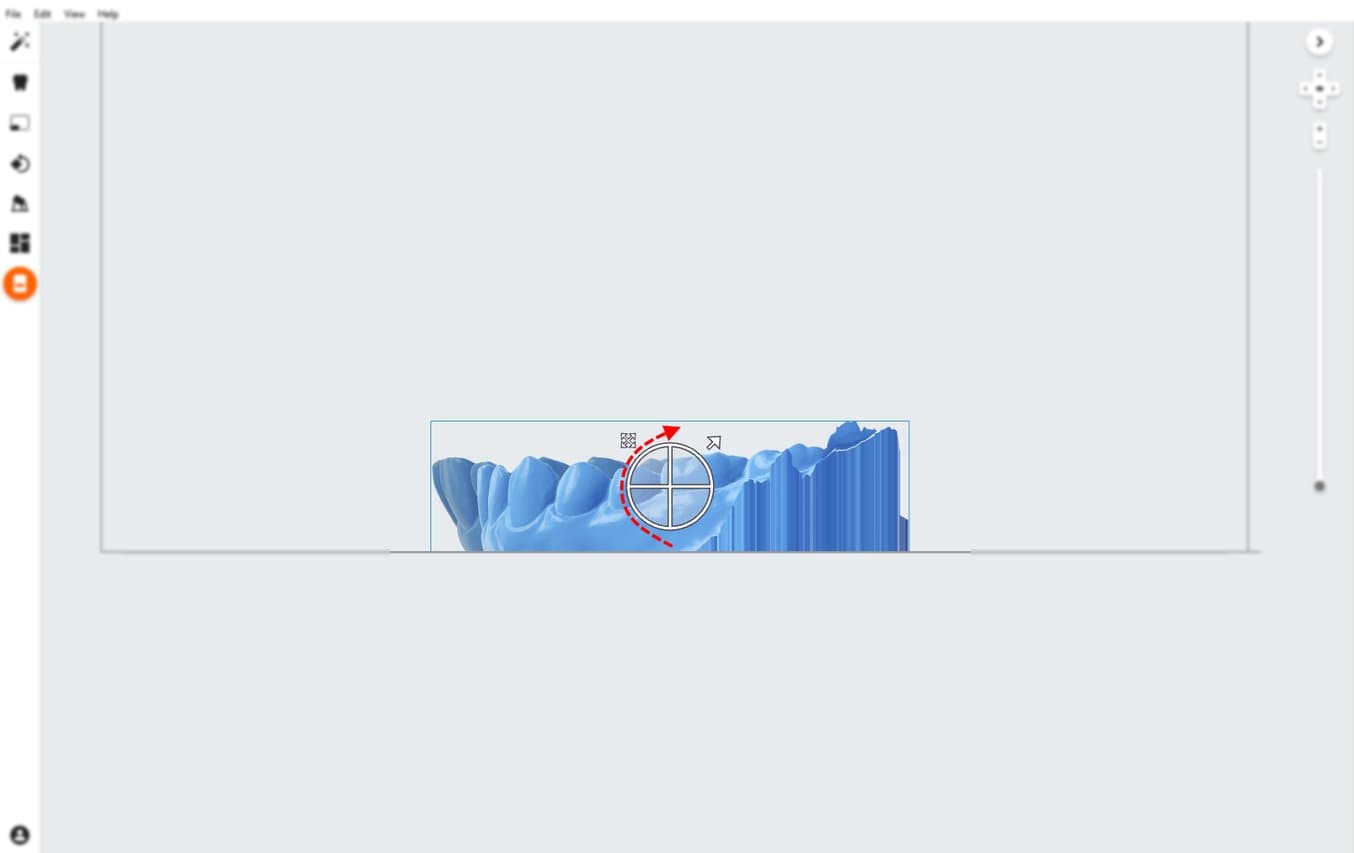
Once the models are in their desired orientation, add supports.
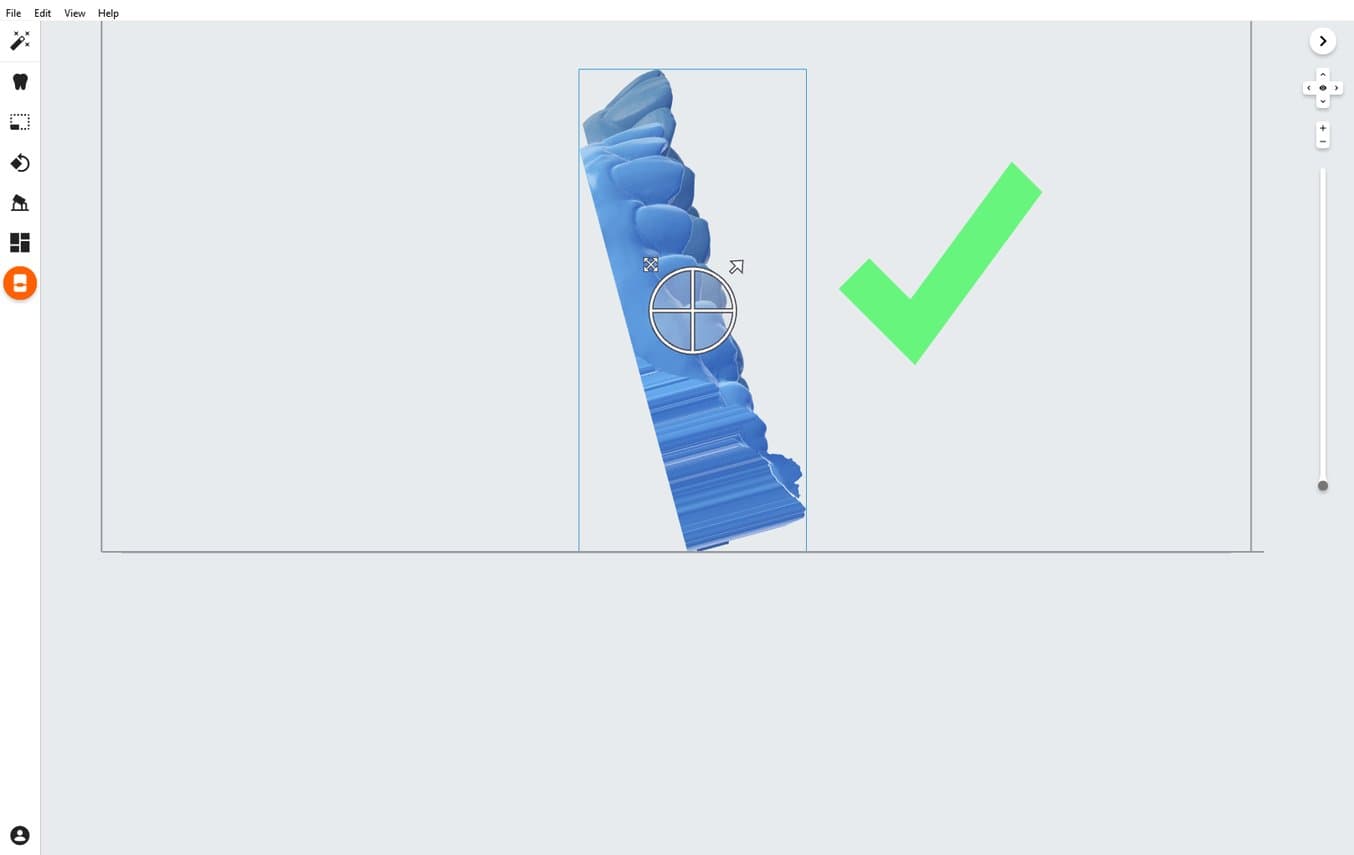
3.6 Generate Support Structures
3.6.1 Automatic Support Generation
For jobs where supports are needed, like vertical models, open the Supports tool (see 1) on the left side of PreForm and click the Auto-Generate Selected or Auto-Generate All button (see 2).
Always review, and where needed, edit supports touch points after generation to ensure none are on critical anatomy.
Note: Uncheck the Internal Supports button (see 3) to prevent the generation of some unnecessary support structures.
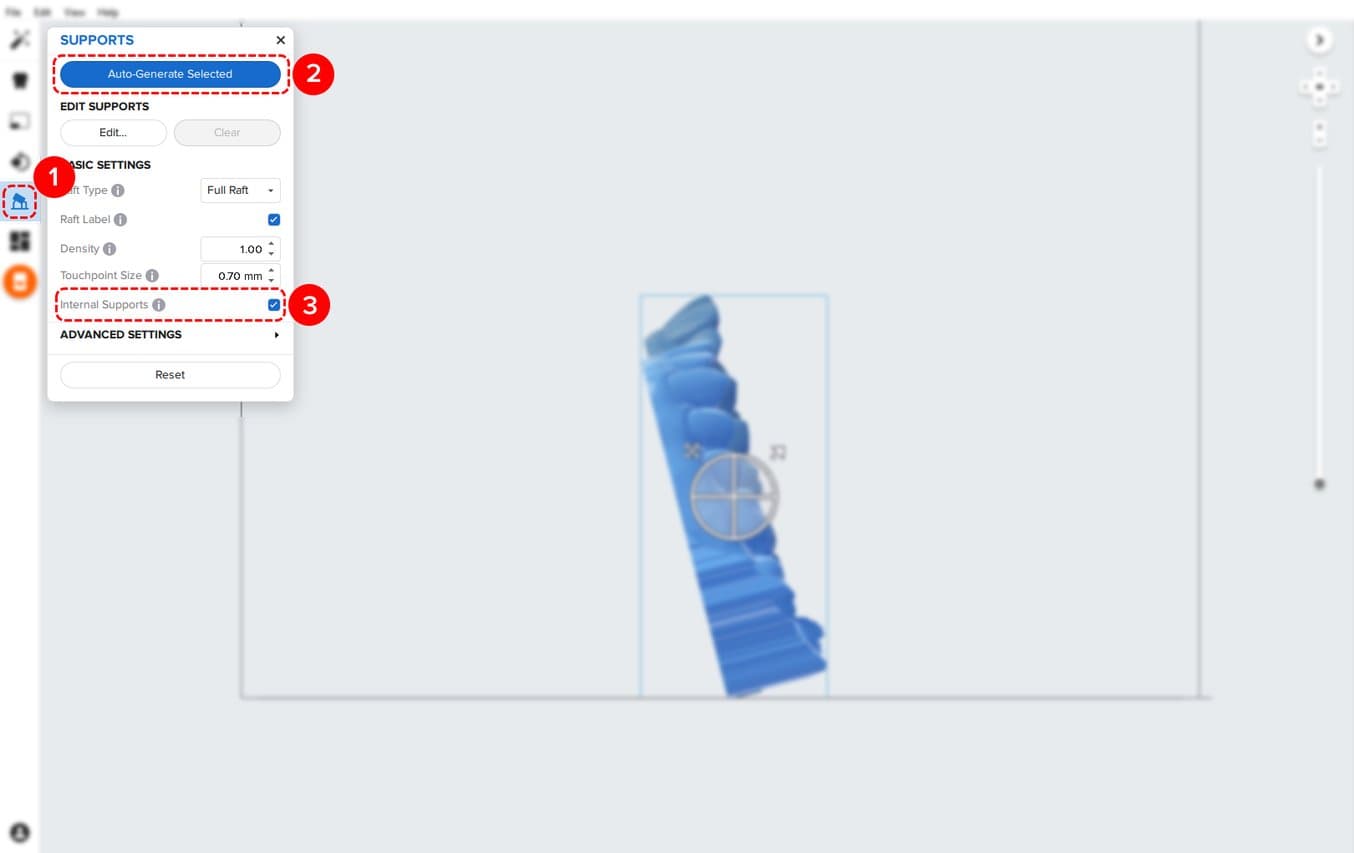
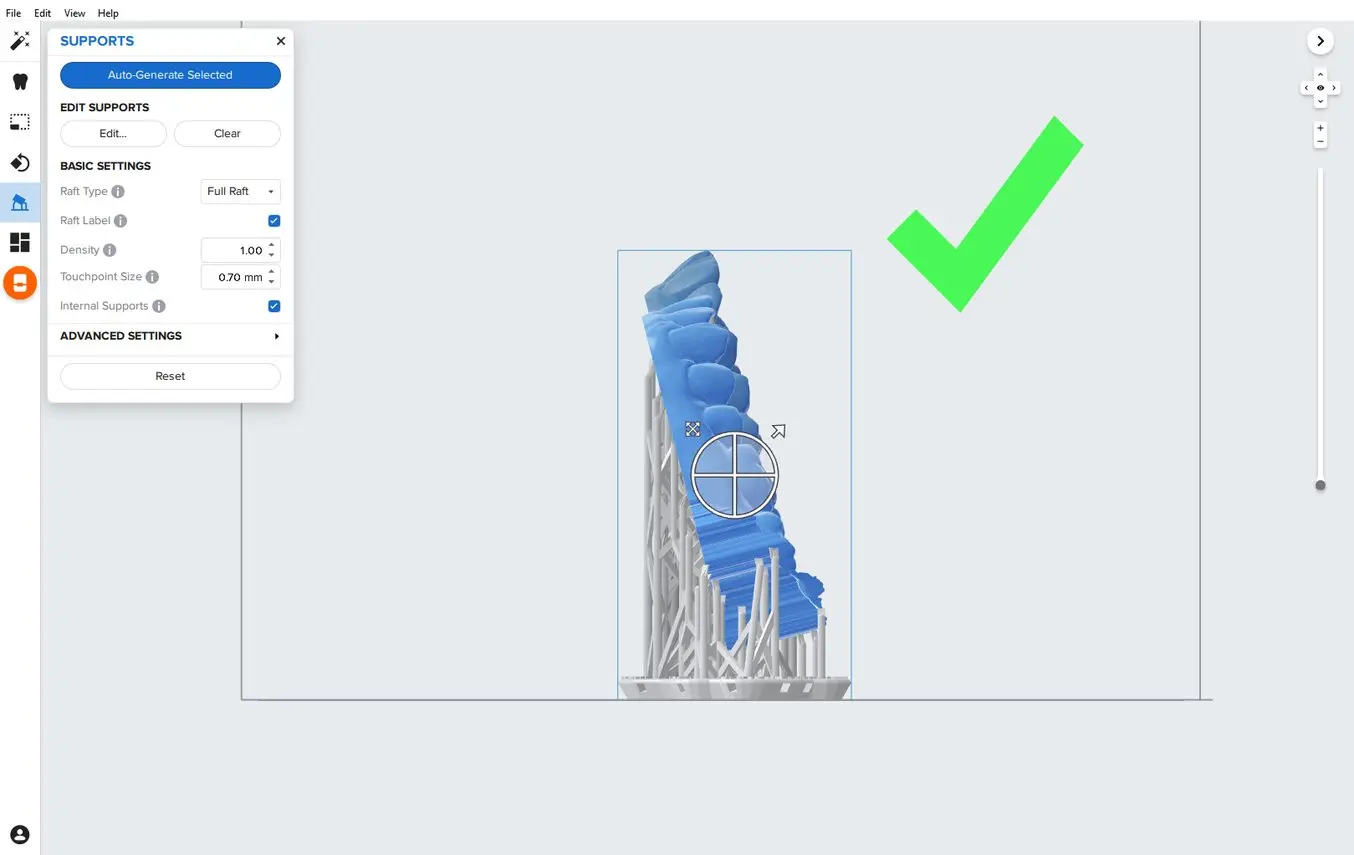
3.6.2 Manual Support Editing
If a support point is not in an ideal location, you can edit their position.
To edit supports click the “Edit…” button.
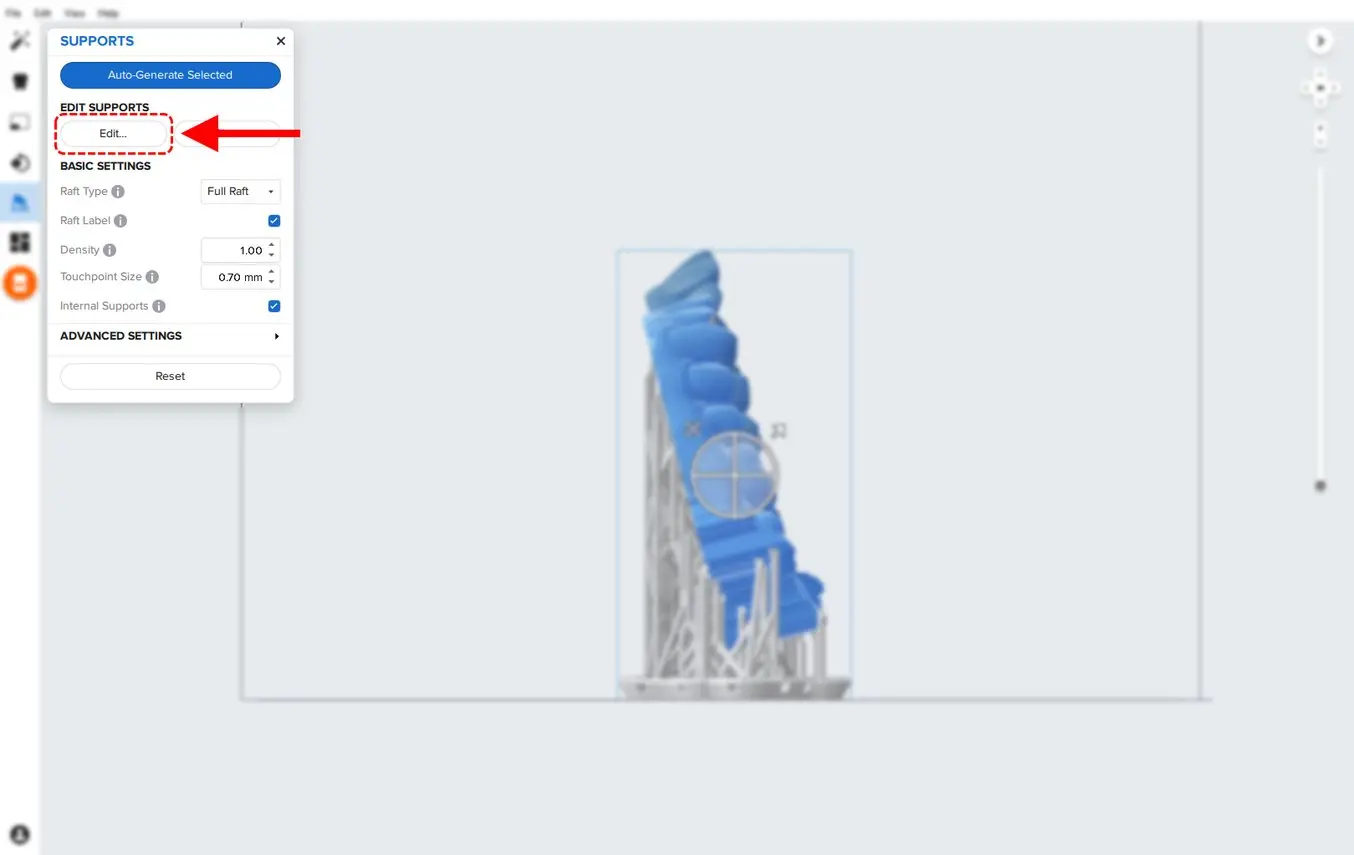
Once in edit mode click on a support touchpoint sphere to remove it and click on areas without supports to add touchpoints, if additional are needed.
PreForm will indicate in red which areas might require additional support.
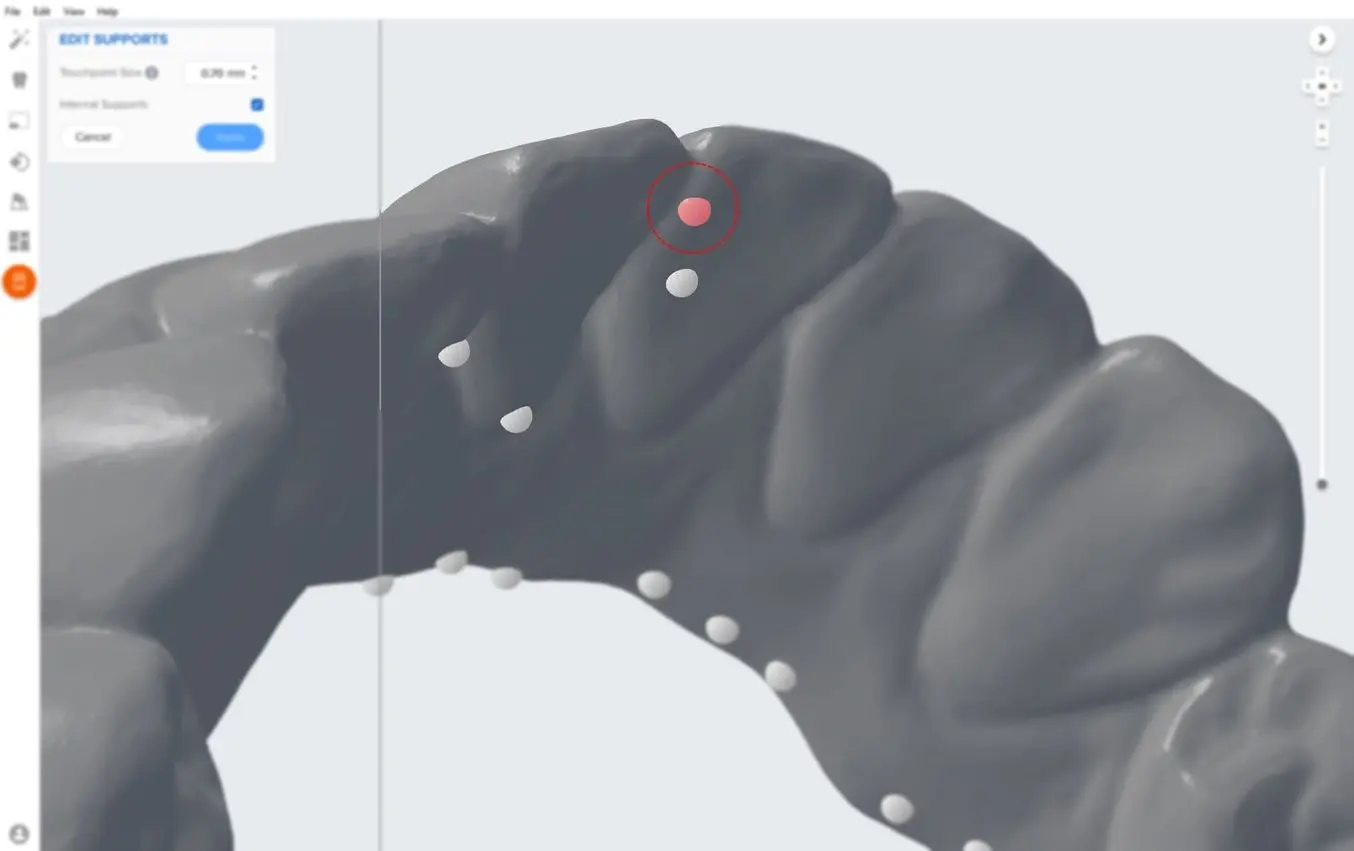
Tip: To quickly remove multiple support points from anatomy click and drag and release across the points you want to remove and hit the delete key on your keyboard.

One of the advantages of orienting models not completely vertical is that support points on critical anatomy are normally not needed.
Supports might still be generated in those areas. If they are, they can be removed.
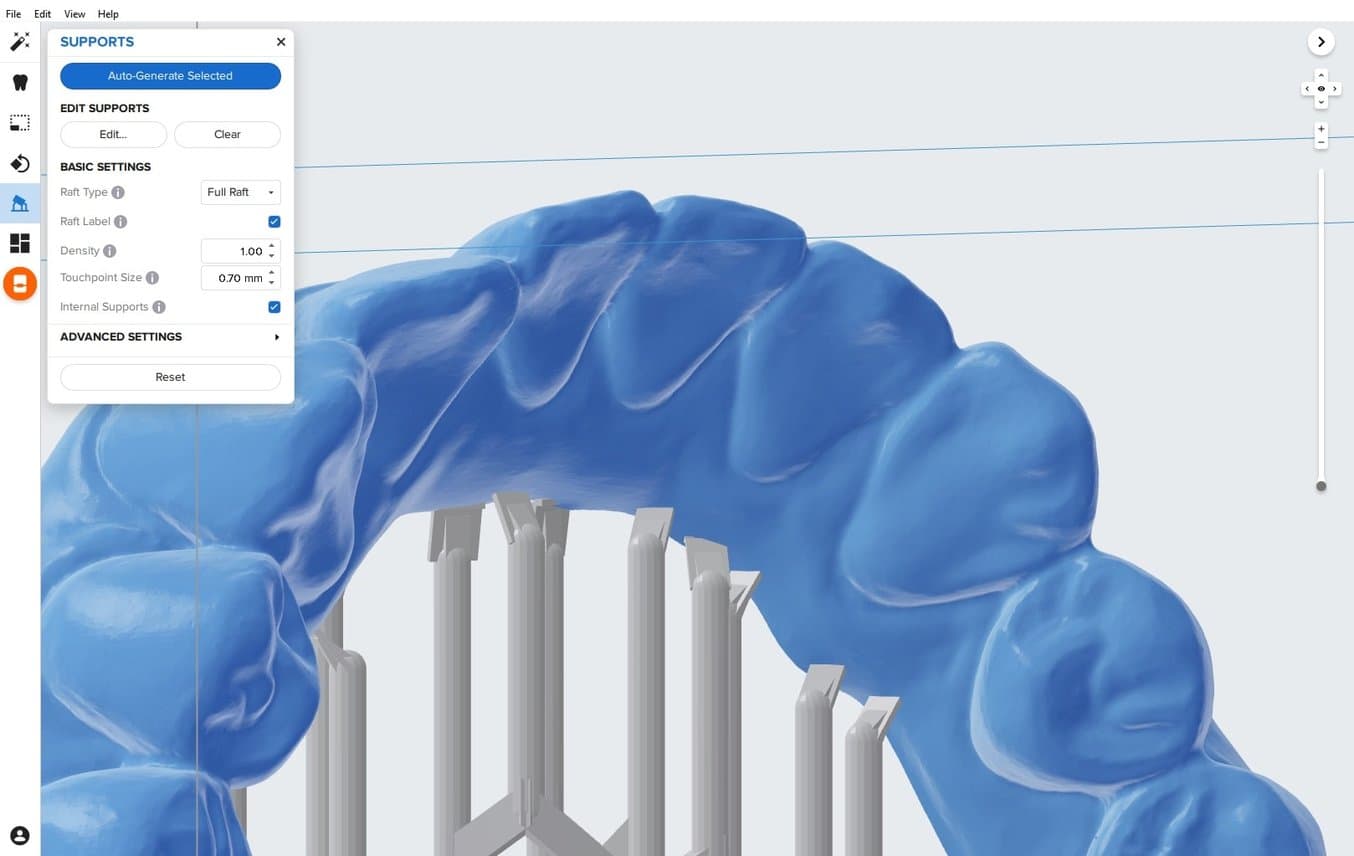
Confirm under the Job Info menu bar on the right side of the screen that Printability shows a green thumbs up.
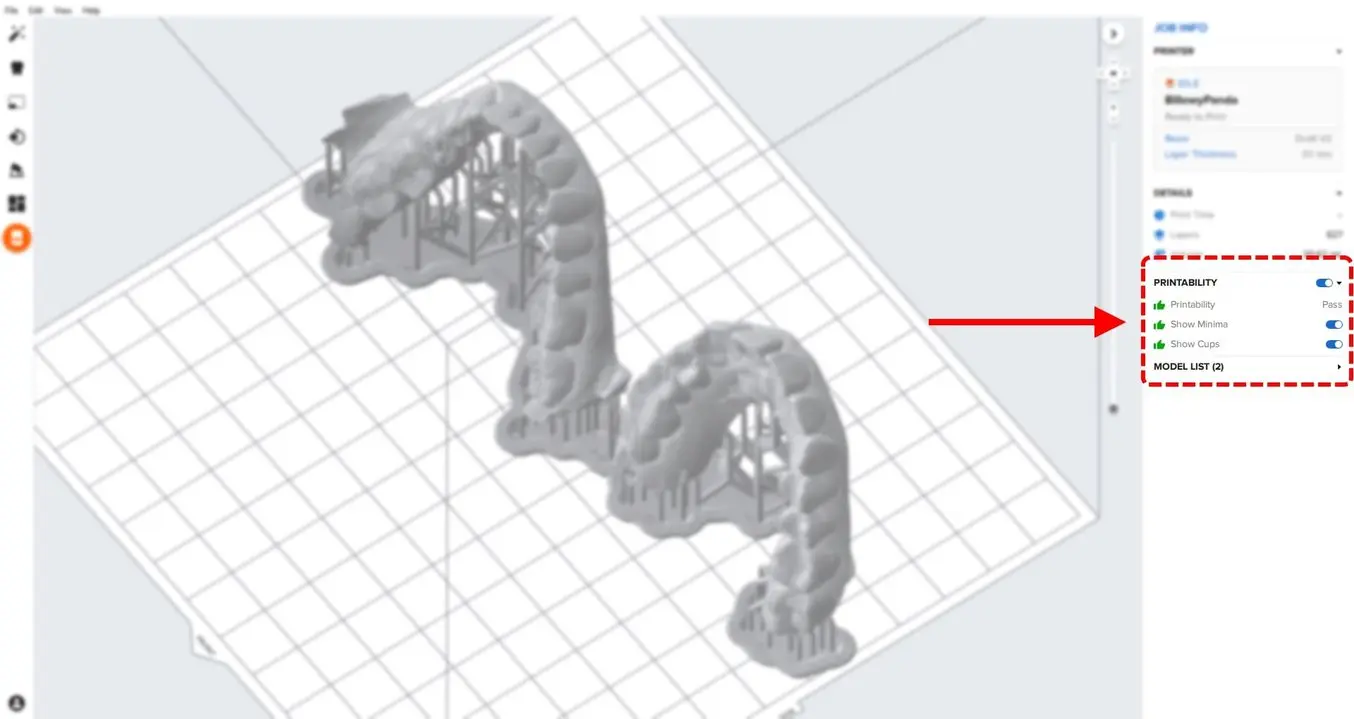
3.7 Printing Layout
Whether you are printing on support structures or directly on the build platform, position the parts so they are not overlapping each other. Overlapping parts will be outlined in red.
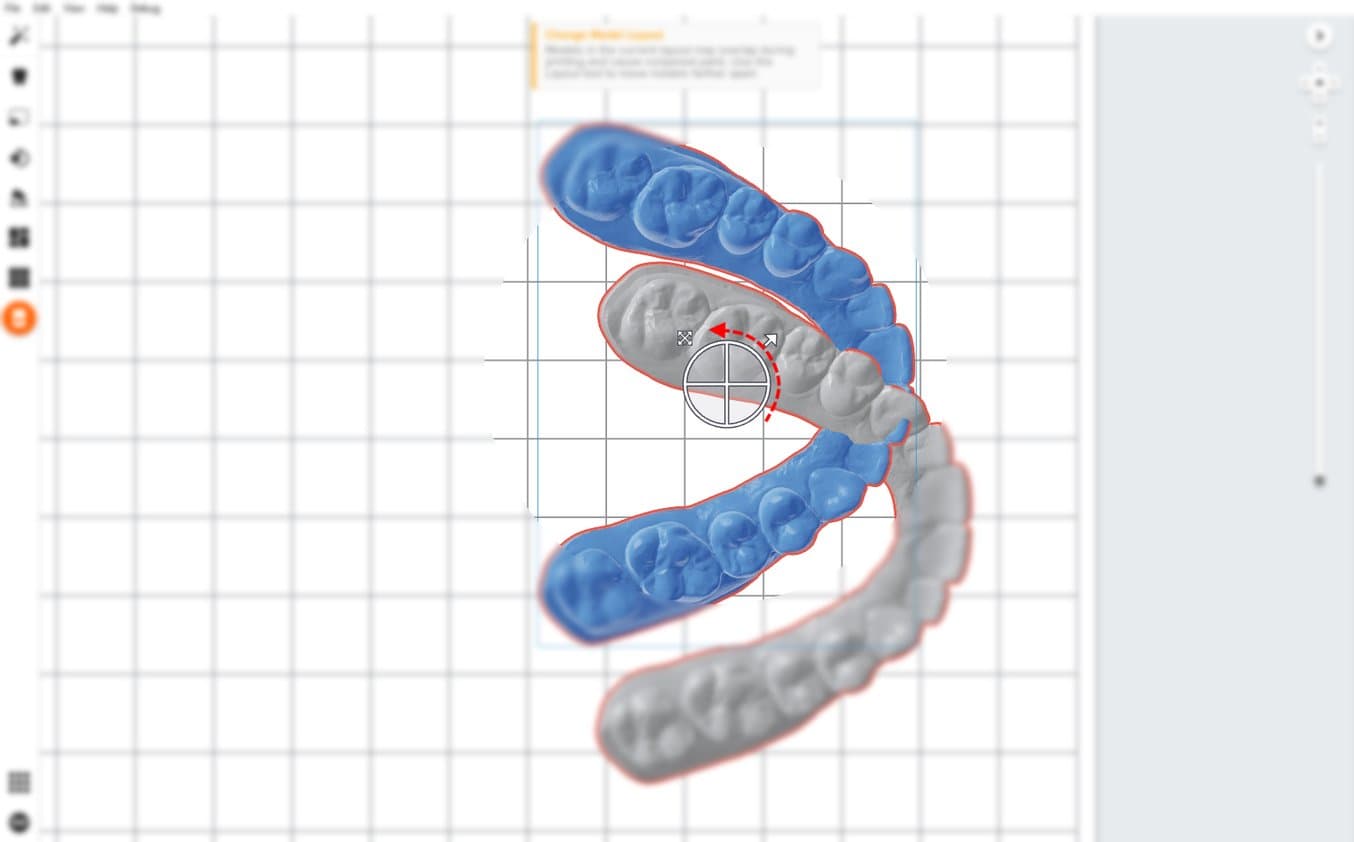
To rotate the part while it is selected, click-and-drag the outer edge of the orientation sphere.
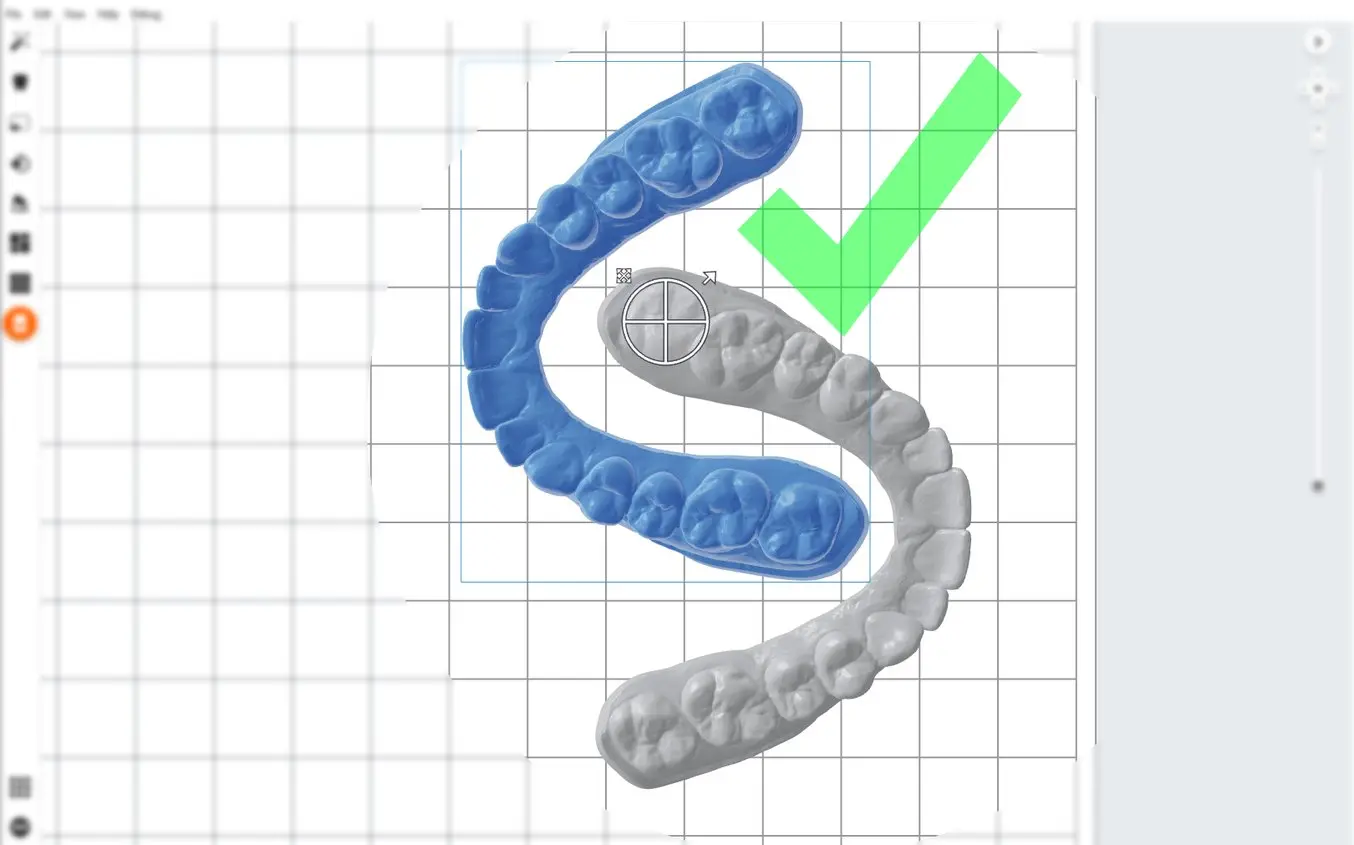
To move the part, click-and-drag anywhere on the part.

Note: Overlapping the support raft is recommended.
When maximizing the amount of parts on a build move the models as close to each other as possible.
Always make sure support structures from one model are not touching parts of another model.
To check for issues. rotate the view and make move models when needed.
Once layout is complete, the job is ready to send to the printer.
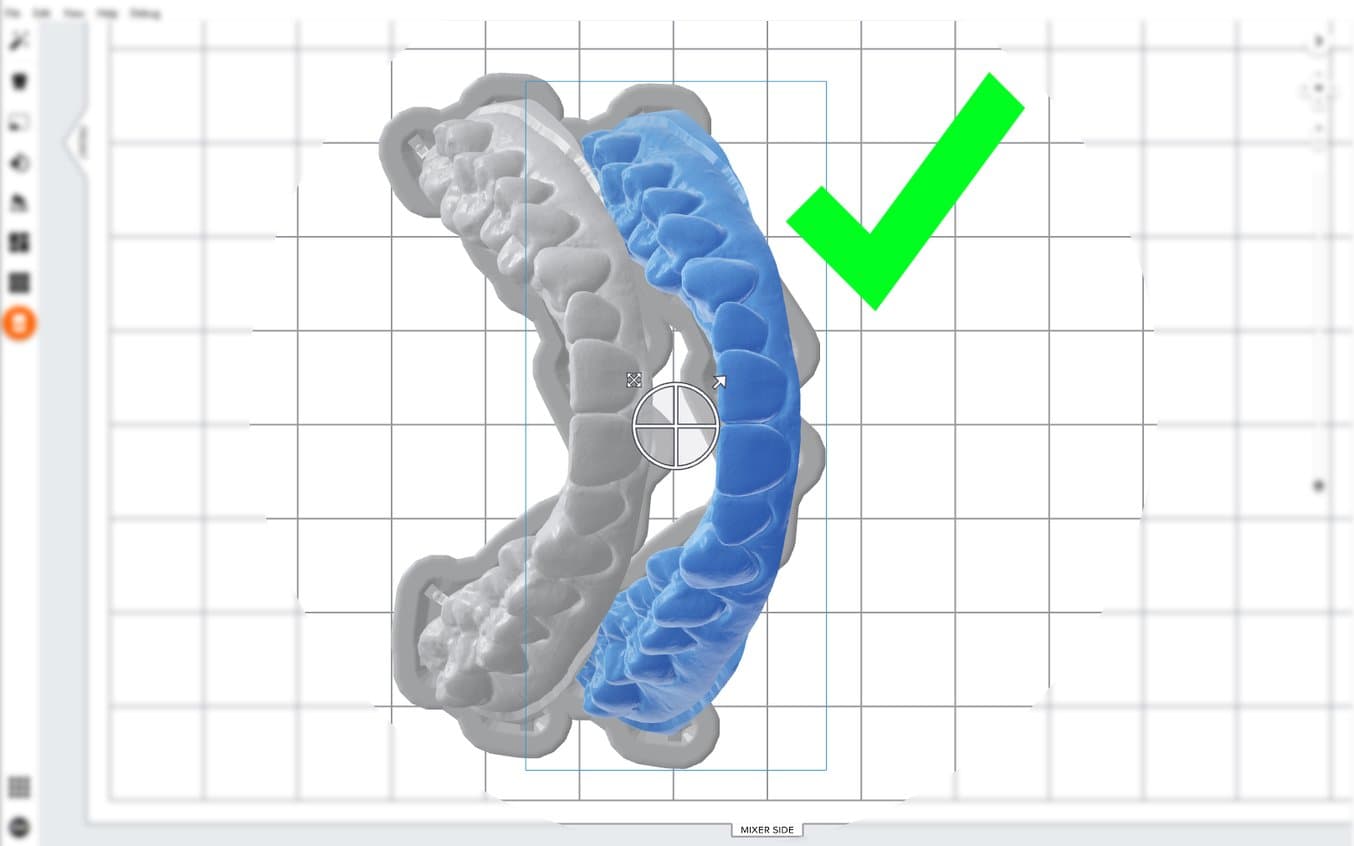
Tip: For parts printed directly on the build platform, when positioning models so that the pry point is facing toward the outside of the build platform. This will simplify part removal once printed.
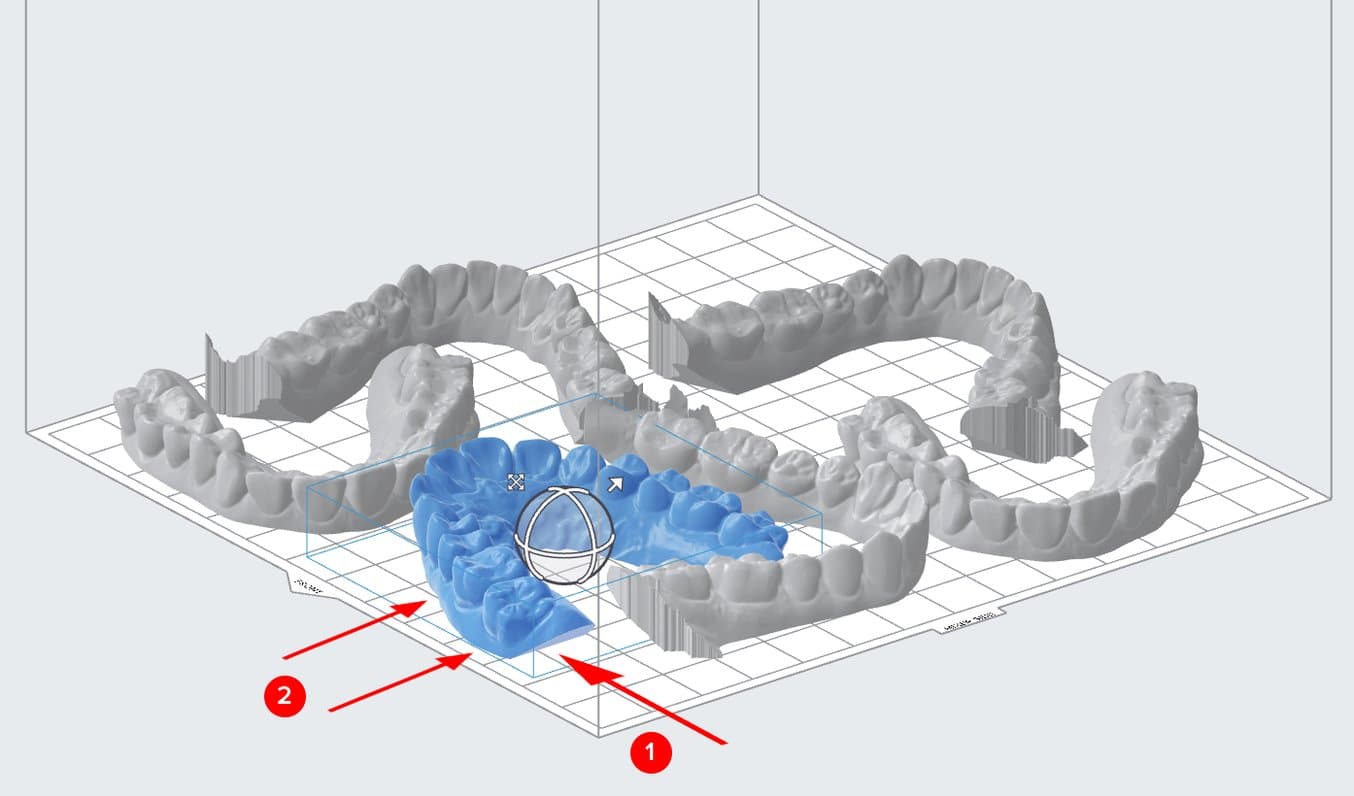
3.8 Transfer the Job to the Printer
Send the job to the printer by clicking the orange printer icon on the left side of the screen.
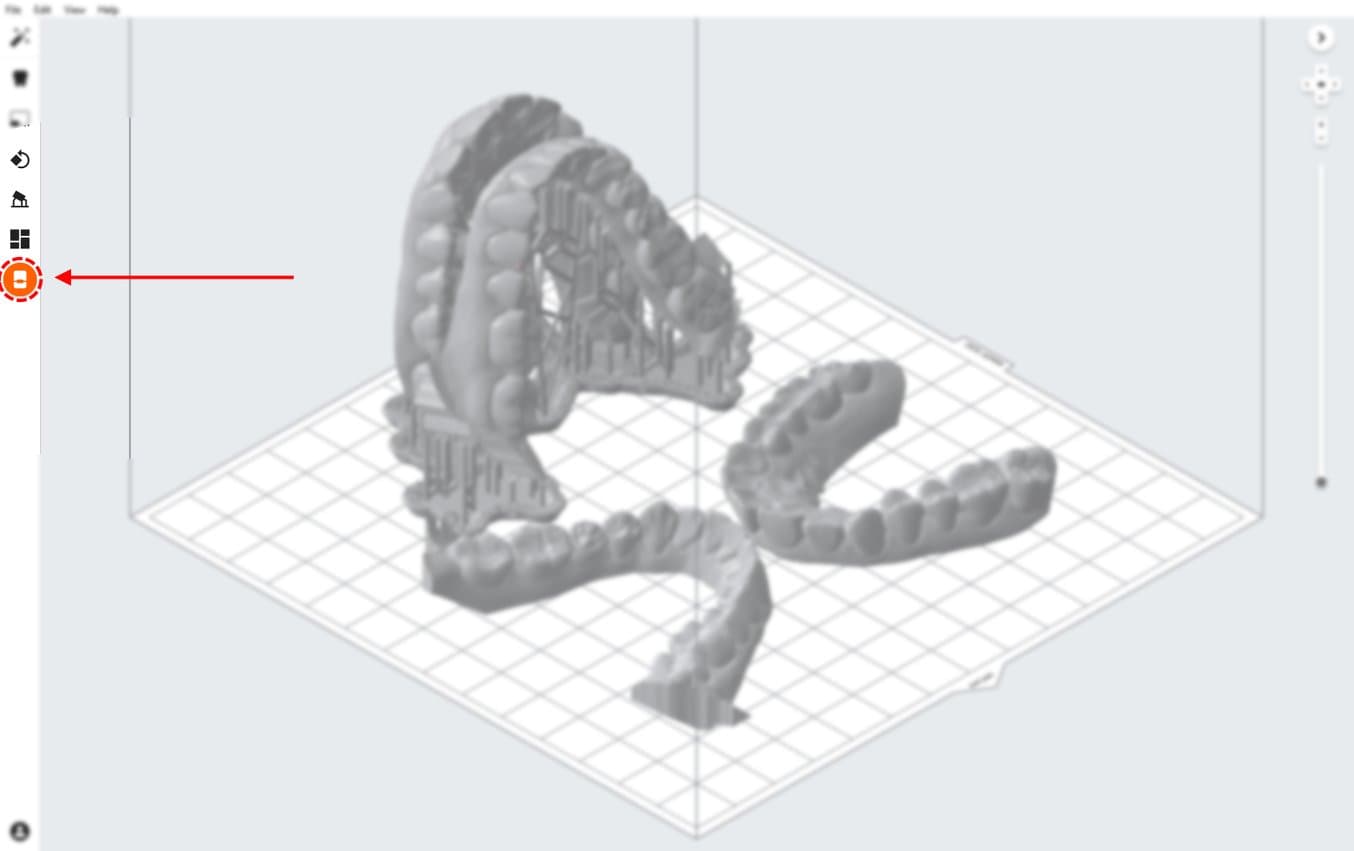
The Print dialog box will open, here you can change the printer the job is being sent to (see 1), rename the job (optional, will take use name of file if saved), and send the job to the printer using the Upload Job (see 2) button.
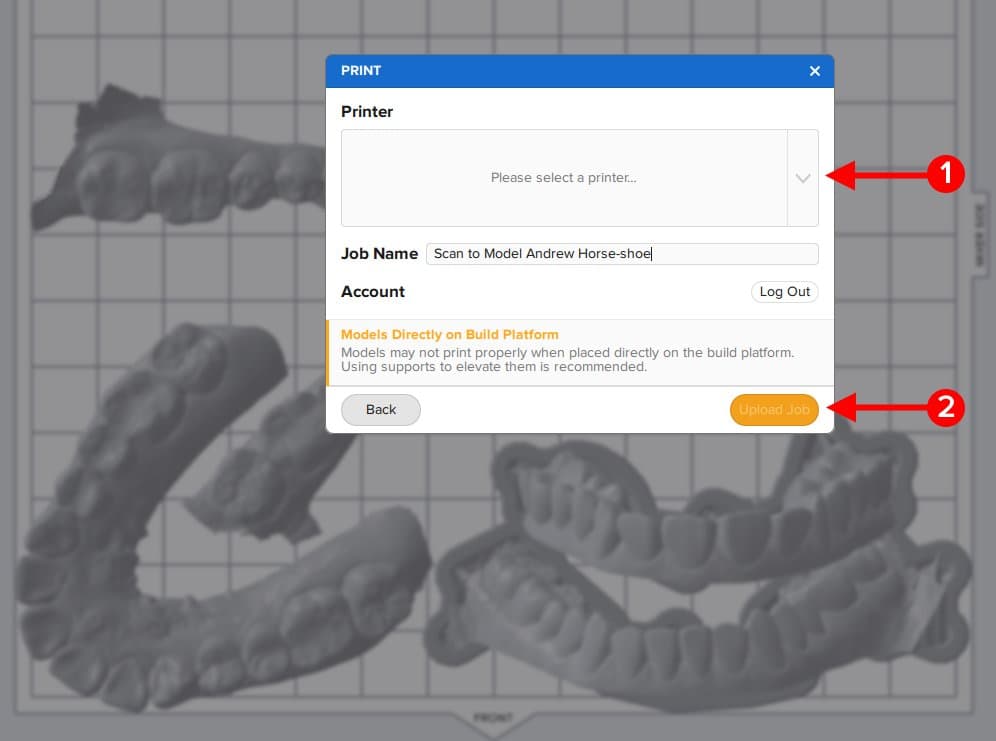
3.9 Start Print
Shake the resin cartridge and then insert the cartridge, a build platform, and a compatible resin tank into the Formlabs 3D printer.
-
Begin printing by selecting the print job from the printer’s touchscreen.
-
Follow any prompts or dialogs shown on the printer screen.
-
The printer will automatically complete the print.
Note: Please verify printer and resin compatibility on the Formlabs support site before printing.
4. Prepare
4.1 Part Removal
Remove printed parts from the build platform by wedging the part removal or scraping tool under the printed model (or support raft) and rotating the tool.
Caution
Always use nitrile gloves when handling uncured resin.
4.1.1 Models Printed Directly on the Build Platform
When removing models printed directly to the build platform it's important to use the correct technique.
Caution
Never apply force to the scraping tool toward your hand or body.
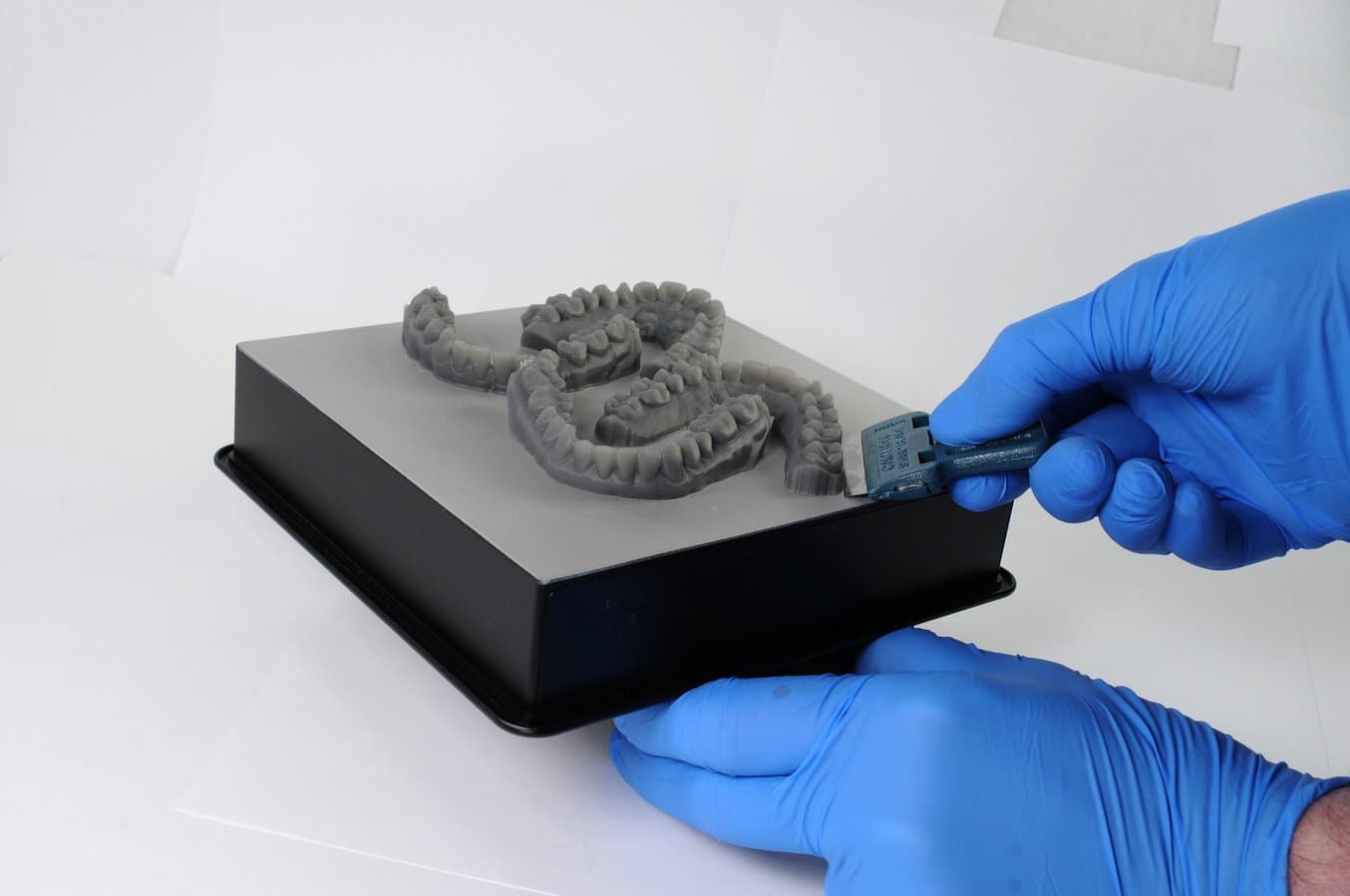
Use a razor blade or sharp scraping tool to work around and under the model. Apply light but constant force on multiple parts of the model's edge.
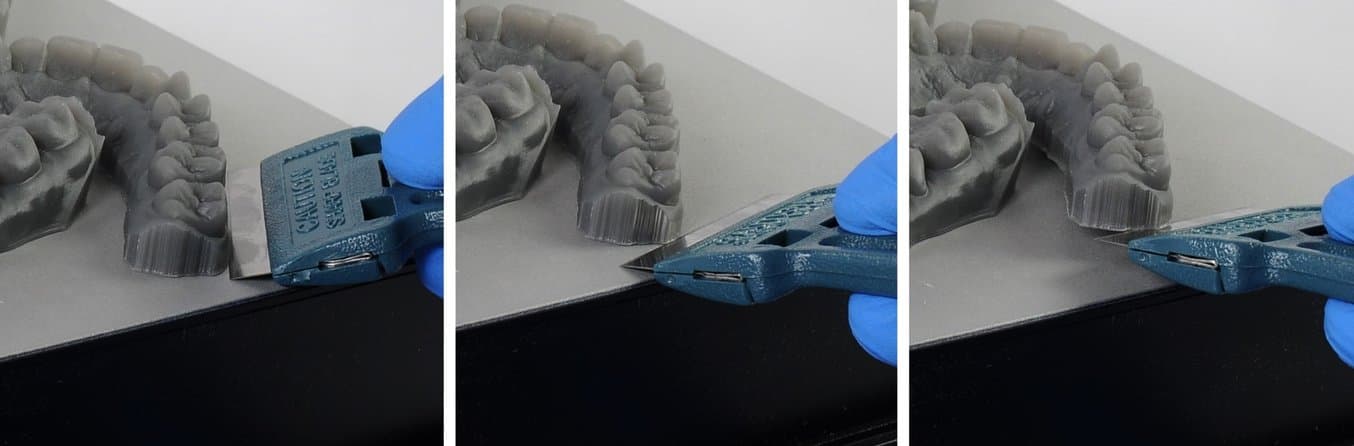
Tip: When safely used, razor blade scrapers can be extremely effective in removing models from the build platform.
Replacement blades are perfectly sharp and very affordable. Much less force is needed with a sharp blade to easily get between the model and build platform.

Be sure to have the blade or scraping tool flush to the build platform.
If the process is too difficult or if the blade or part gets damaged:
-
The blade is not completely under the model
-
The blade should be replaced or sharpened
-
Too much force is being applied in one area of the model, work around the perimeter
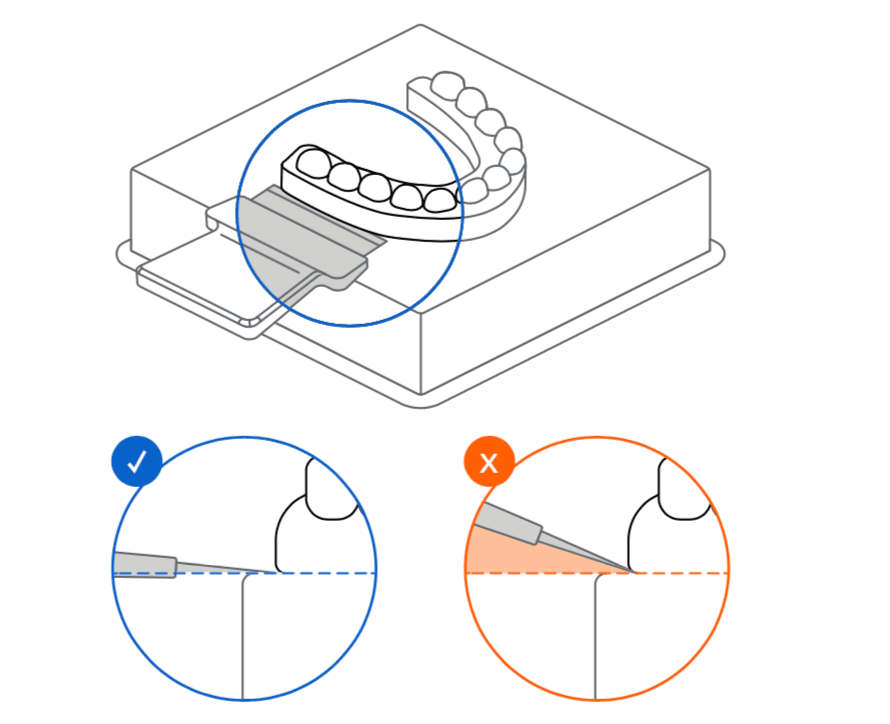
4.1.2 Models Printed on Supports
For models on supports, insert the scraping tool under the edge of the support raft, apply an even and constant force, and gently twist to pop the part off of the build plate.
Applying this technique in multiple locations around the raft may be needed.
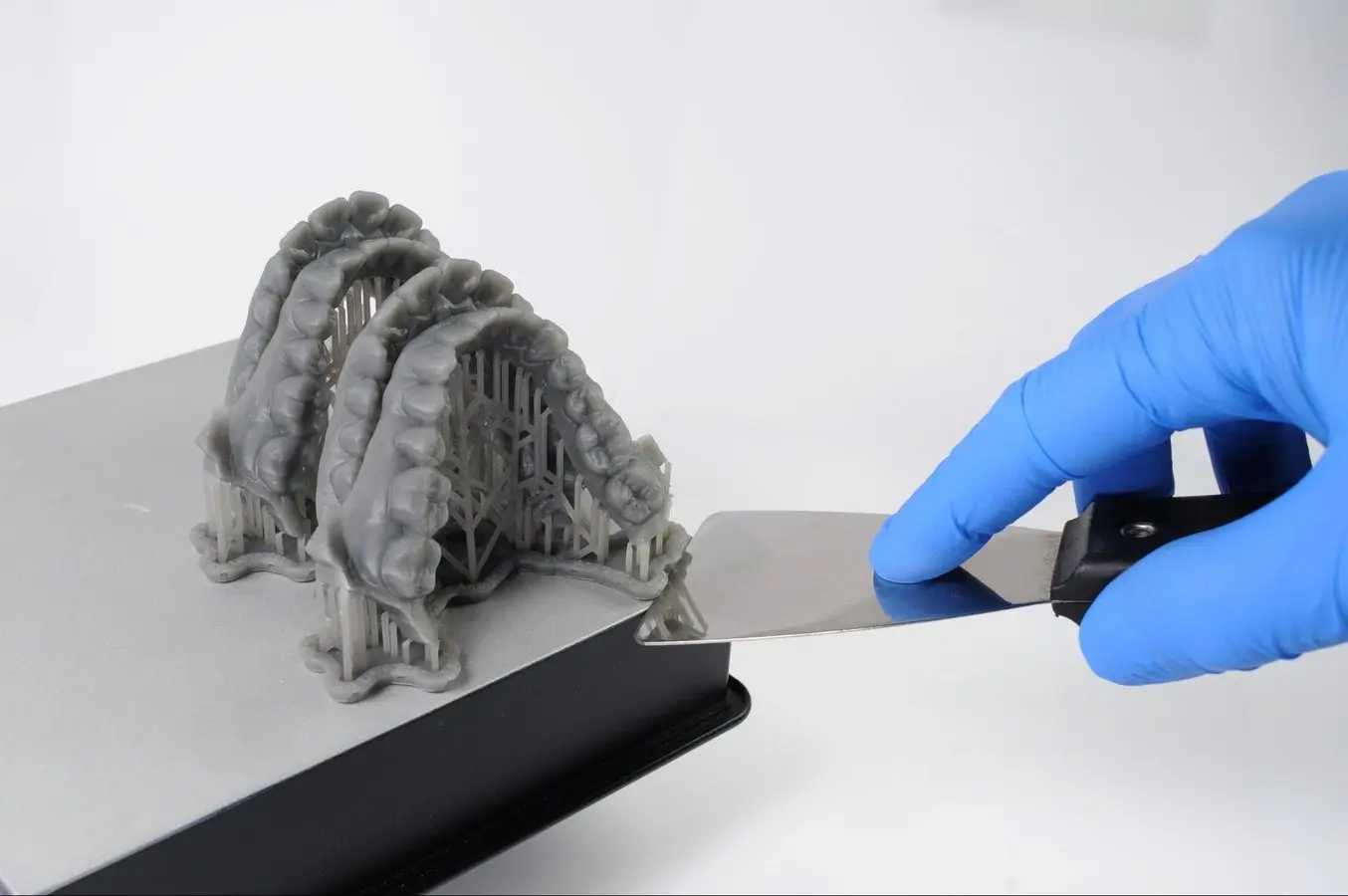
4.2 Wash
Caution
When washing the printed part with solvent, ensure a properly ventilated environment with proper protective masks and gloves. Expired or unused resin shall be disposed of in accordance with local regulations.
Place the model in a Form Wash filled with isopropyl alcohol (IPA, ≥96%) and wash for 10 minutes.
Make sure all parts are fully submerged in IPA when washing.
Greatly exceeding wash duration may affect dimensional accuracy and performance of printed parts over time.
Using the Standard Finish Kit
Formlabs recommends using Form Wash for optimal resin removal and surface finish. If using the Finish Kit, remove parts first from the build platform with the part removal tool. Rinse the parts in two buckets of isopropyl alcohol (IPA), 96% or higher for an initial bath for 10 minutes, and a second bath for 5 minutes.
4.3 Dry and Inspection
Remove parts from IPA and leave to air dry at room temperature in a well-ventilated area for about 10 minutes.

Tip: Compressed air can be used to help dry parts, remove trapped resin from small spaces, and allow for rapid inspection of unwashed resin.
Still, allow for a few minutes of bench drying if using compressed air.
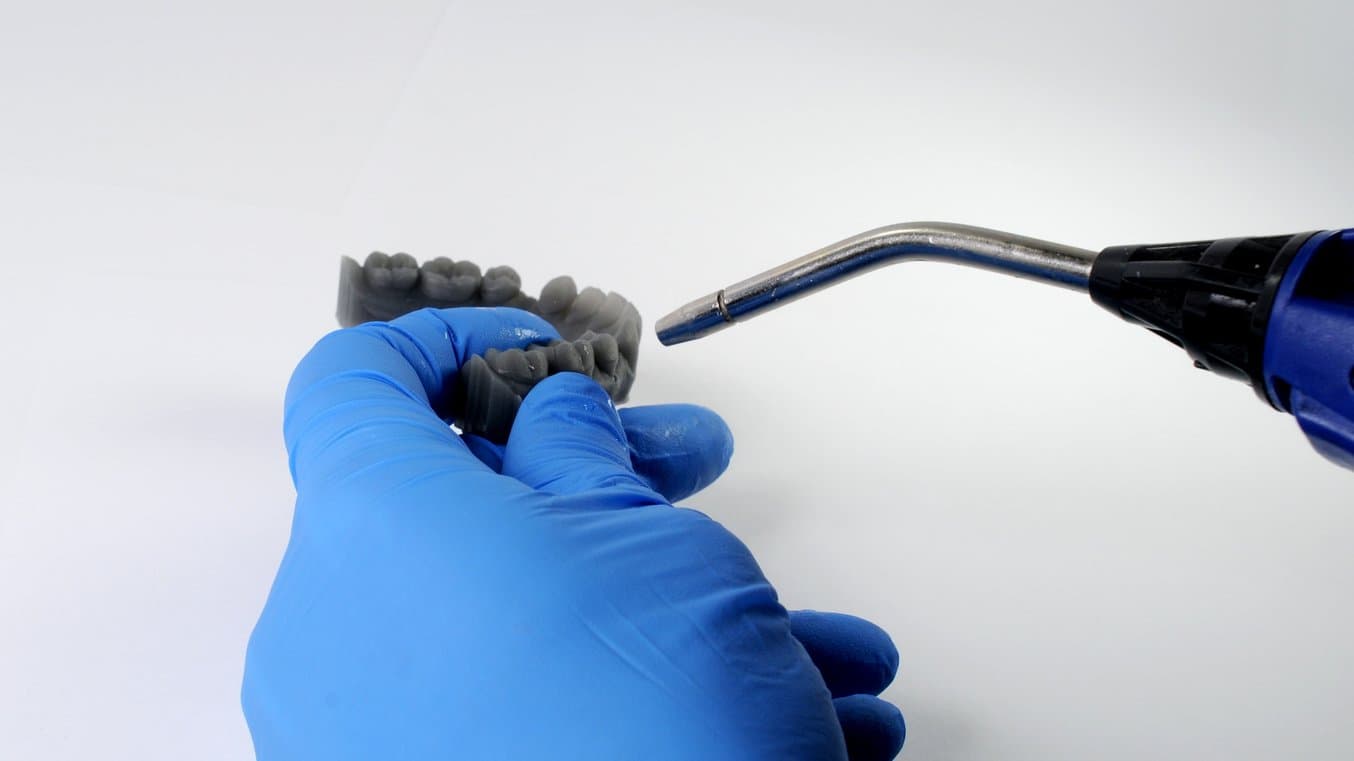
Inspect printed parts to ensure that parts are clean and dry.
Ensure no residual alcohol, excess liquid resin, or residue particles must remain on the surface before proceeding to subsequent steps.
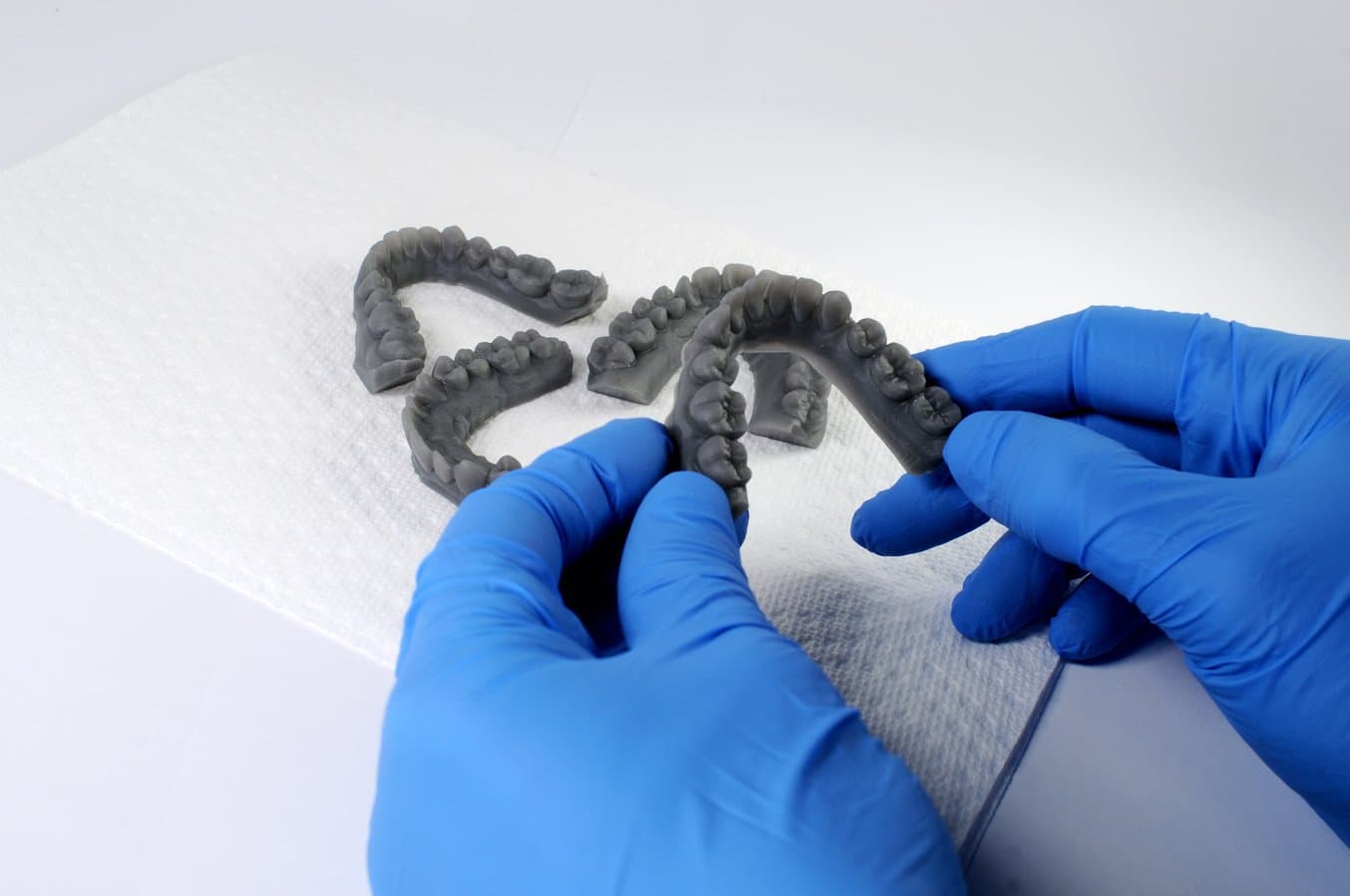
If any wet, uncured resin is still present after drying, use a squeeze bottle or submerge the part in clean IPA for about a minute, then air dry the parts again.
Again, use of compressed air allows for rapid inspection.
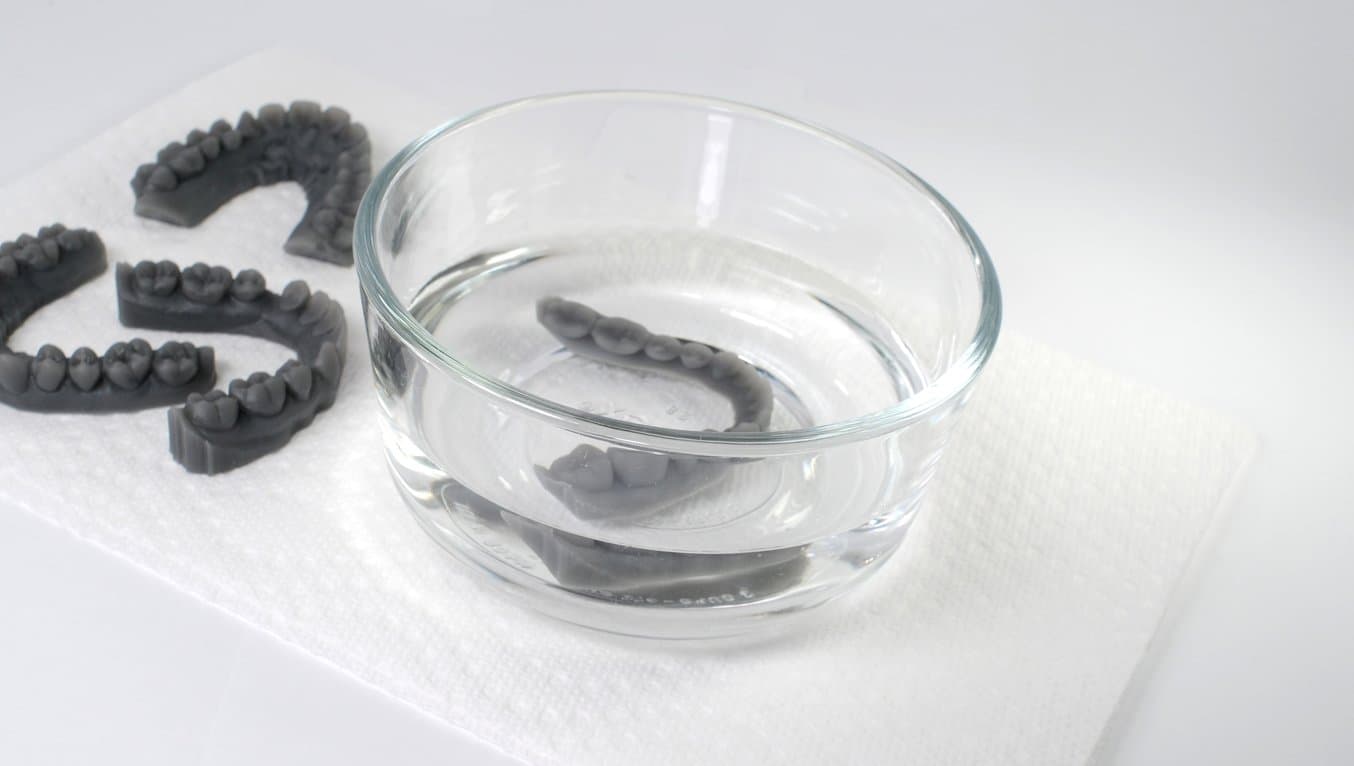
4.4 Post Cure
Place the washed and dried models into the Form Cure, set the proper curing time, and temperature.
Draft V2 Resin - 5 minutes at 0 °C
Tip: For even stronger Draft V2 models you can set the temperature to 60 °C. Models 3D printed in Draft V2 Resin were fully tested and validated in making dental appliances with or without temperature during post-curing.
4.5 Support Removal (optional)
If supports were used, remove the supports using the clippers provided in the Formlabs Finish Kit, scissors, or other trimming tools.
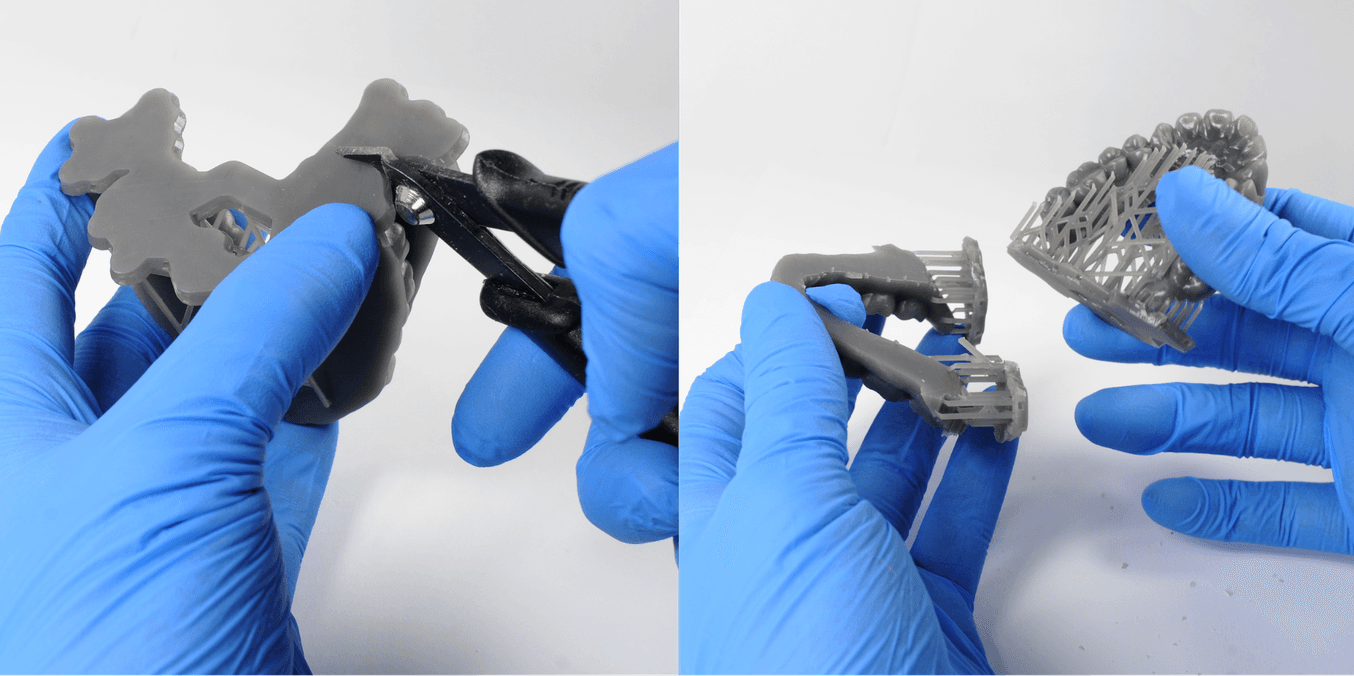
Tip: While ripping the supports from the part might be quicker, it can leave divots in the part or damage the model. We recommend cutting the supports where connected to critical anatomy off individually.
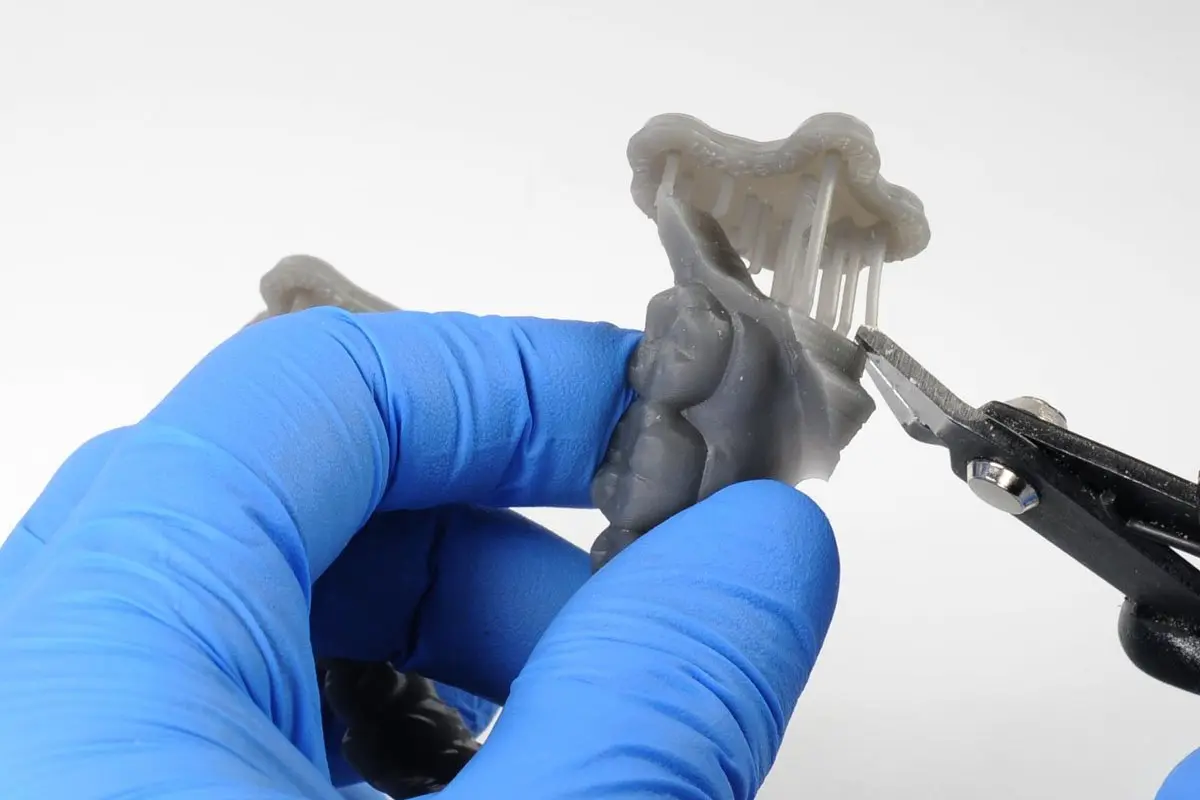
Disposal
1. Any cured resin is non-hazardous and may be disposed of as regular waste
-
Follow facility protocols for waste that may be considered biohazardous.
2. Liquid resin should be disposed of in accordance with government regulations (community, regional, national).
- Contact a licensed professional waste disposal service to dispose of liquid resin.
- Do not allow waste to enter storm or sewer drainage systems.
- Avoid release into the environment.
- Contaminated packaging: Dispose of as unused product.
5. Thermoform
Use a dental thermoformer machine on the printed model to make the appliance. Always start by using the recommended settings for the equipment and material being used.
5.1 Vacuum vs. Pressure Formers
Vacuum formers pull the material over the model with negative pressure.
Pros
-
Affordable
-
No compressed air needed
-
Simple machine
Cons
-
Device quality can be unreliable
-
Pressure forming is superior
-
Depending on unit, 3D printed models can be a challenge compared to gypsum models
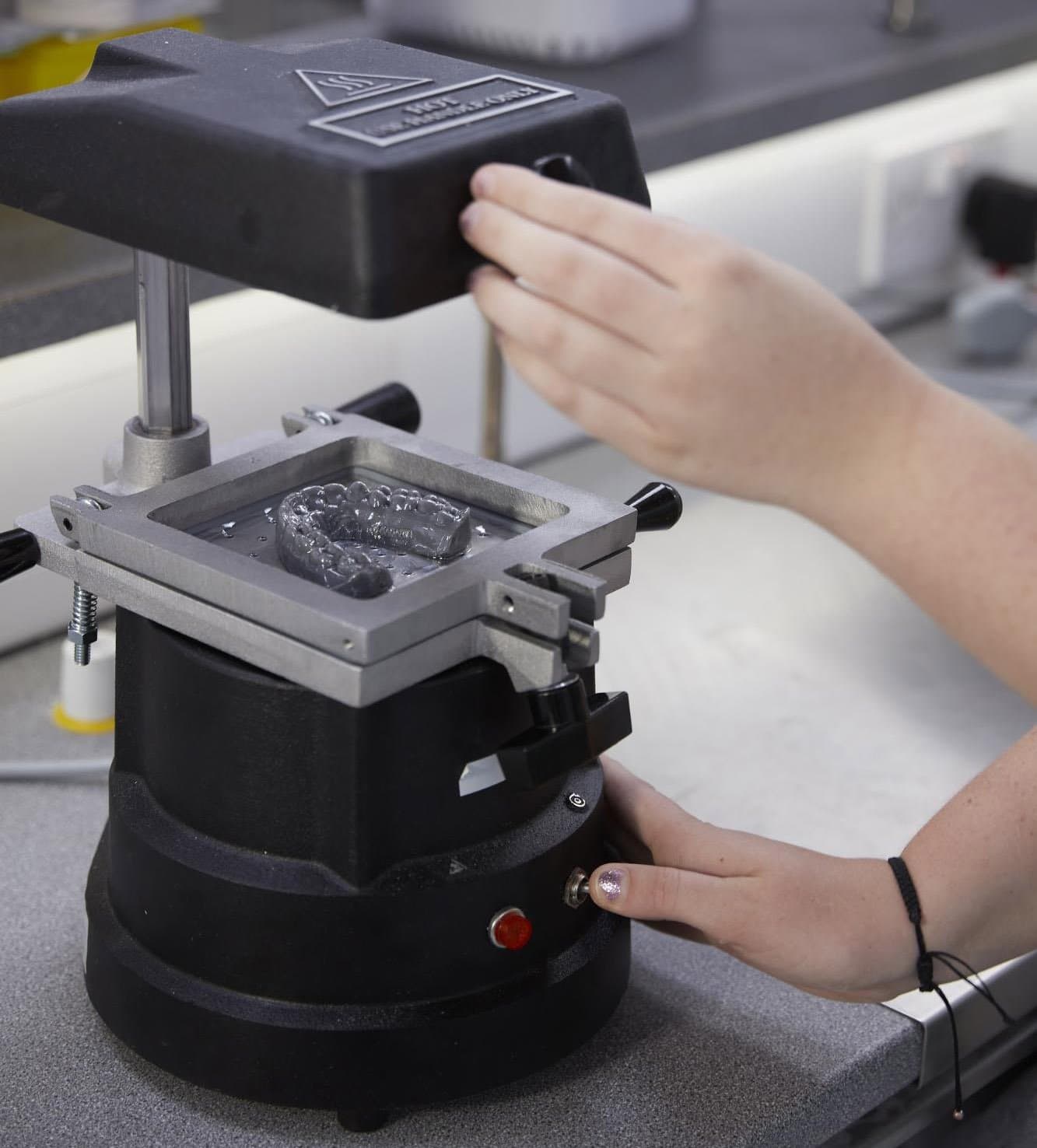
Pressure formers push the material over the model with positive pressure.
Pros
-
Excellent fitment around models
-
High quality machines
-
Some units have automated control; preset programs and pressure release
Cons
-
Expensive
-
Requires clean, dry, compressed air (up to 90 psi or 6.2 bar)
Tip: Formlabs recommends a pressure former for most orthodontic appliance production. Some pressure formers to consider are Dentsply Drufomat, Great Lakes MiniSTAR, and Erkodent.
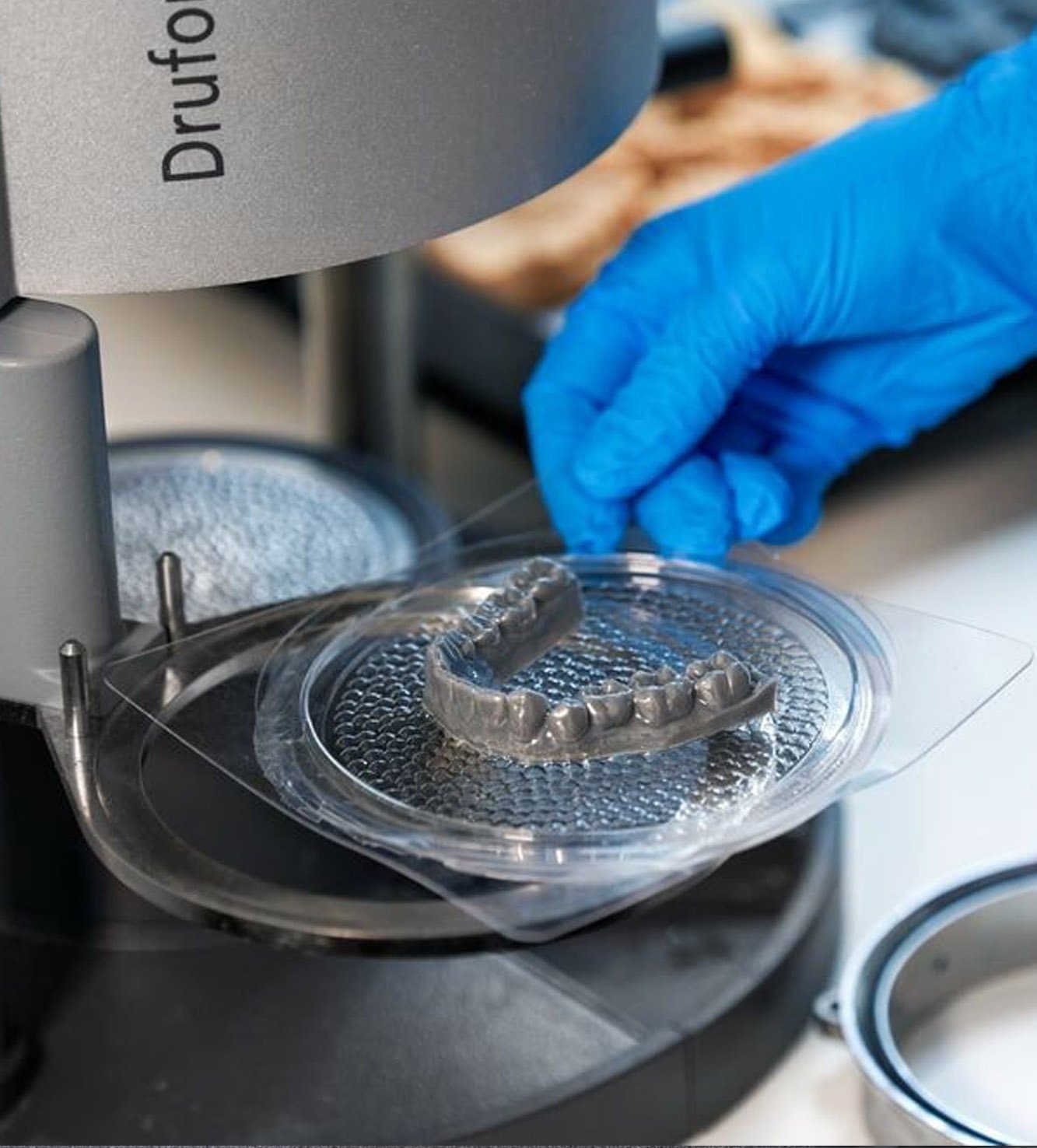
5.2 Thermoforming Best Practices
5.2.1 Preventing Adhesion
Inspect models before thermoforming.
Models that are not completely washed and UV cured can adhere to the thermoforming material.
Unwashed resin will be shiny in appearance and tacky to the touch.
Resin is more difficult to wash from divots and negative features like engraving.
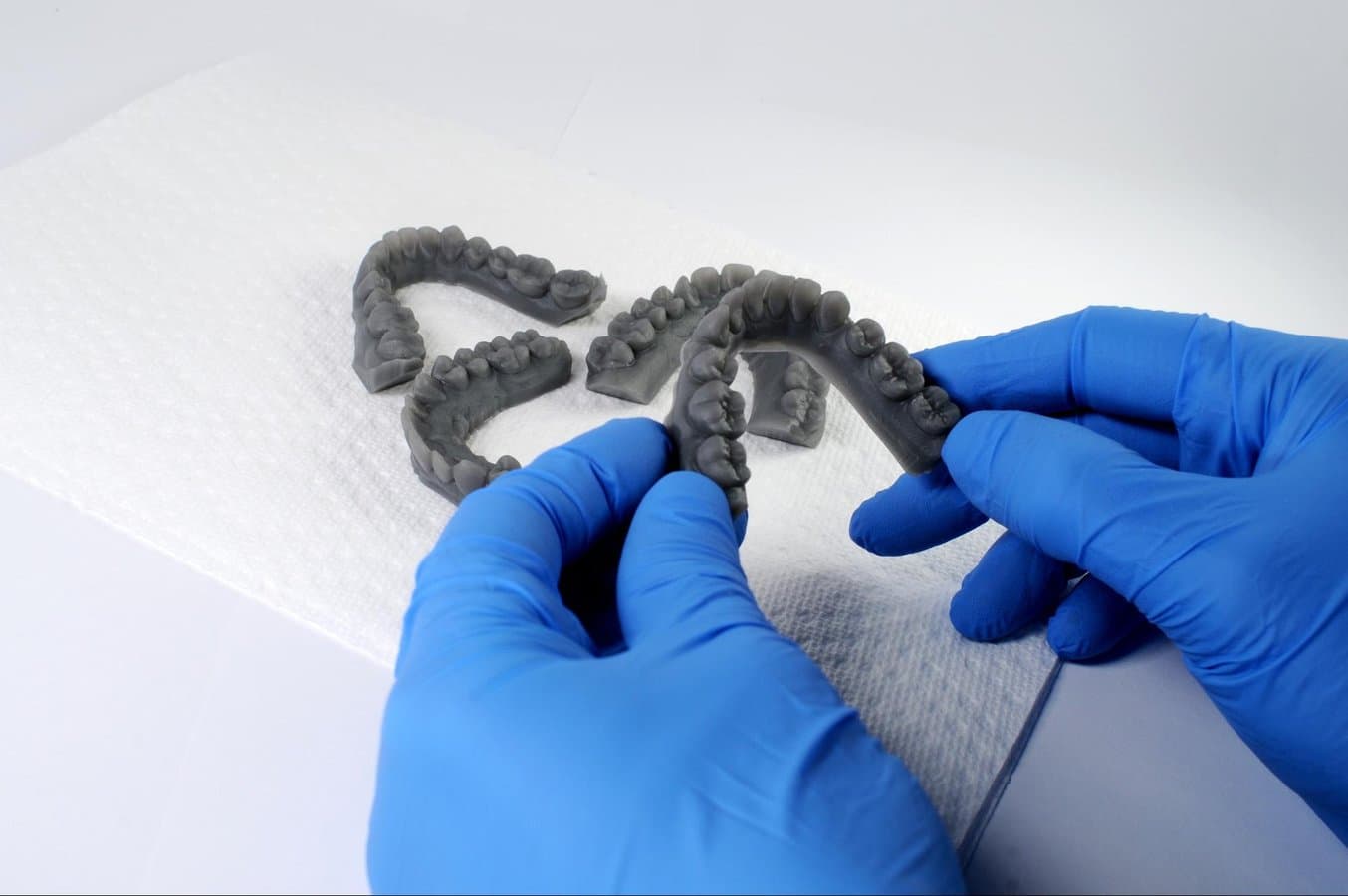
5.2.2 Warm-up Cycles
Thermoformers warm up as they are used and can change heating times. Running a handful of warm up cycles before thermoforming will add consistency to the process.
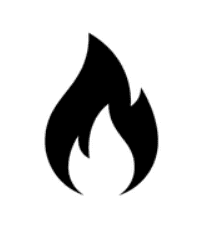
5.2.3 Model Height in Thermoforming
Depending on the heating cycle, thickness and brand of the material results may vary.
In testing we found after pressure forming materials 1 mm in thickness resulted in an appliance of ~0.7 mm (see 2).
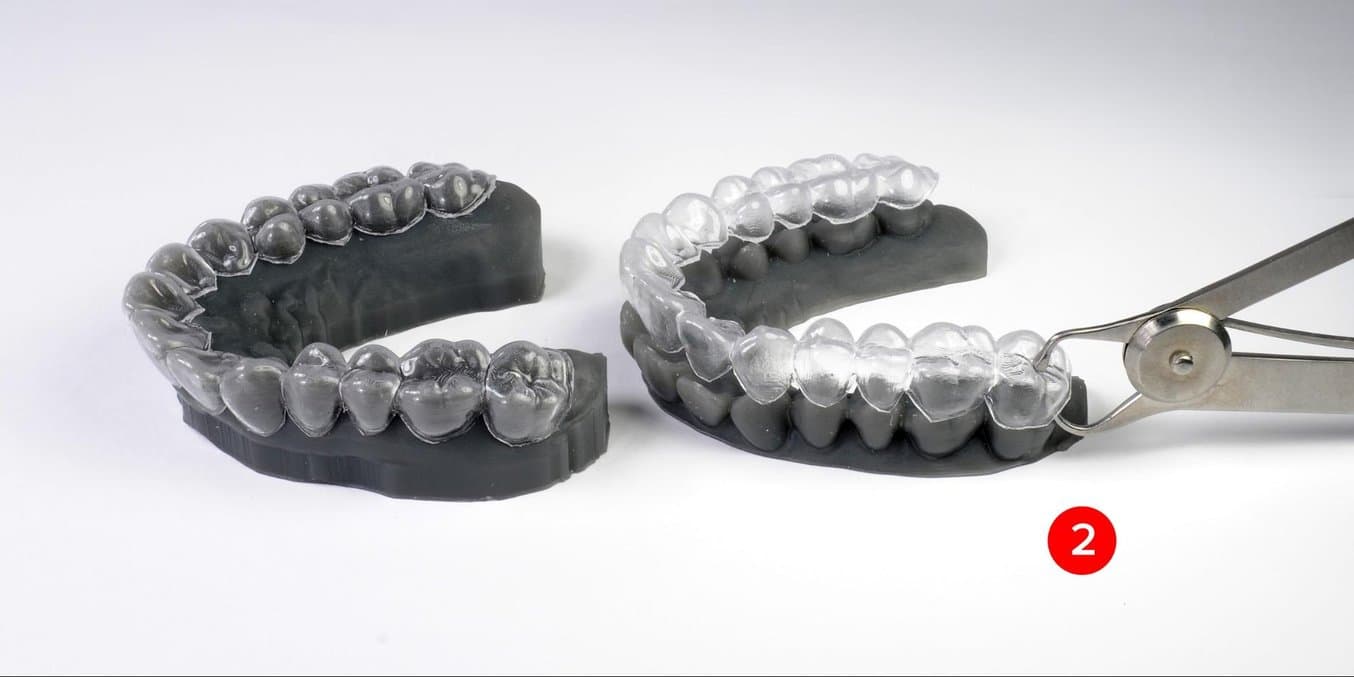
We also noticed appliance thickness variation in thermoforming models of different heights. In testing models 20 mm tall produced ~0.100 mm thinner appliances when compared to a 13 mm model (see 1).
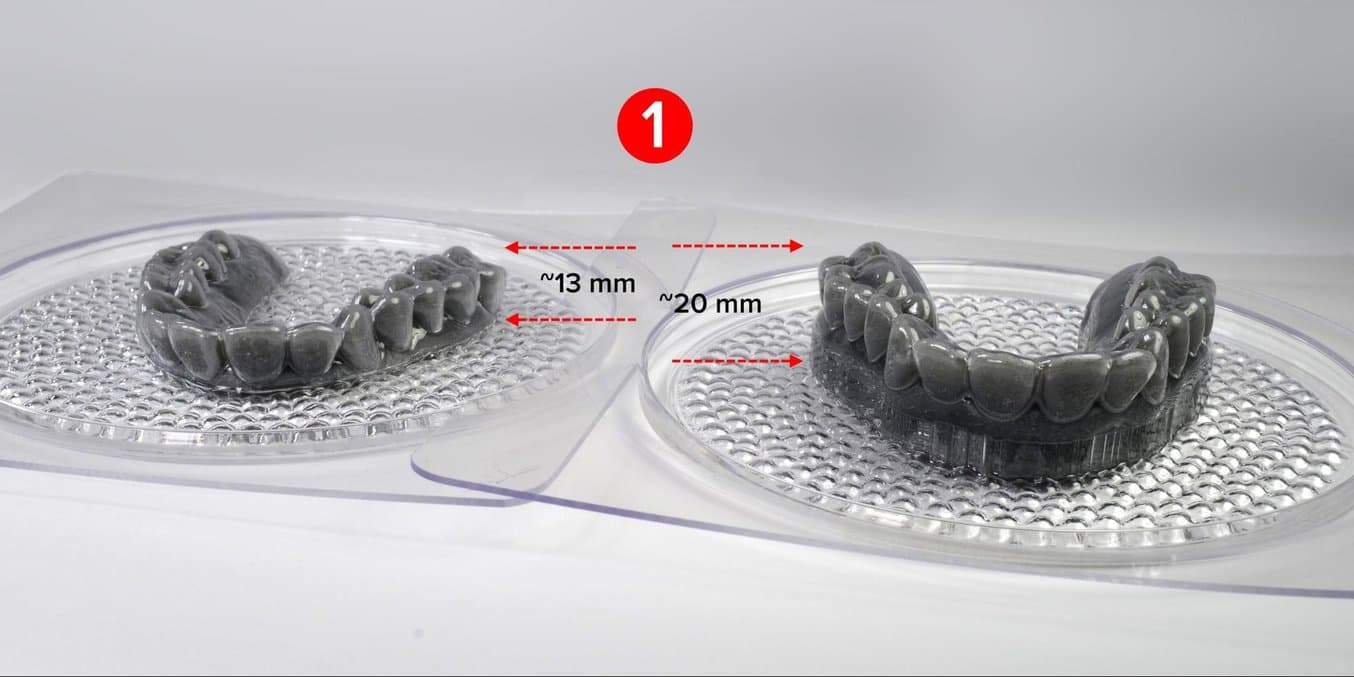
Having controlled CAD outputs can help keep thermoforming consistent; another option is to use pellets or beads to approximate equal heights during thermoforming.
The dental pressure formers recommended in the above section have this capability.
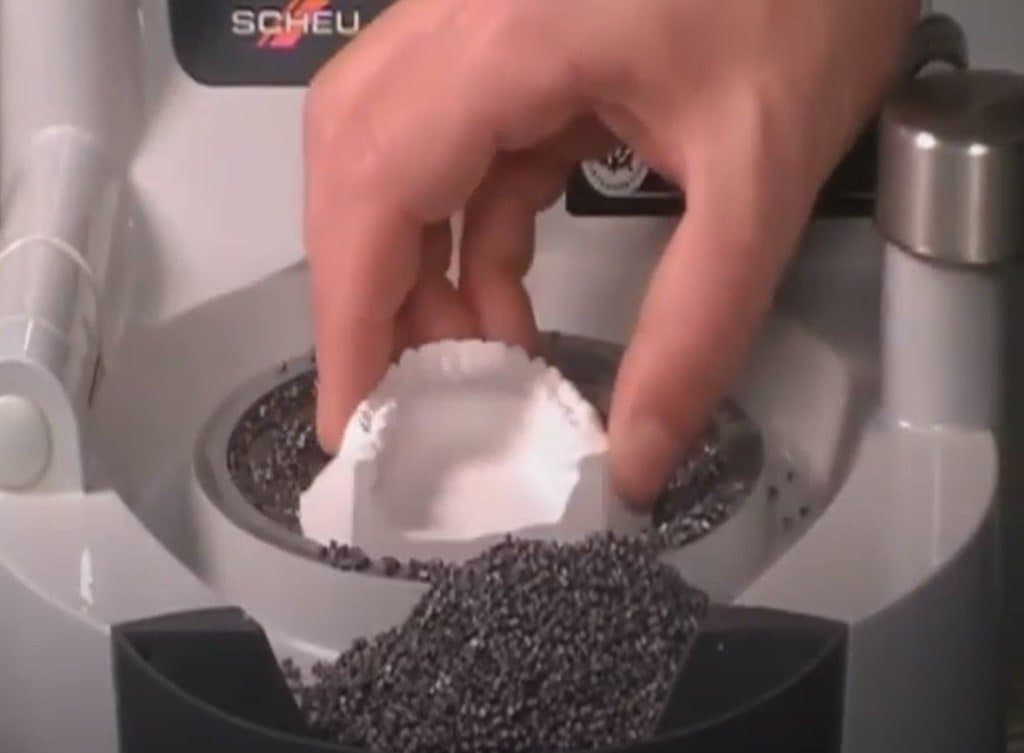
6. Cutting and Finishing
Depending on thickness of the material used and preferred method a variety of techniques can be used for cutting out and finishing the appliance. Experiment and find what works best for you and whoever else is doing the work.
The goals are to be quick, have clean edges, and produce appliances that meet your expectations.
Tip: Thermoforming materials by nature are very susceptible to heat. When using rotary instruments, heat can build and start melting the cutting area, which adds finishing steps.
6.1 Removing Appliance
Start by removing the model from the sheet of plastic.
Make the initial rough cut by using durable scissors or shears (see 1).
Cut around the bottom of the model (see 2), freeing the outer plastic from the part.
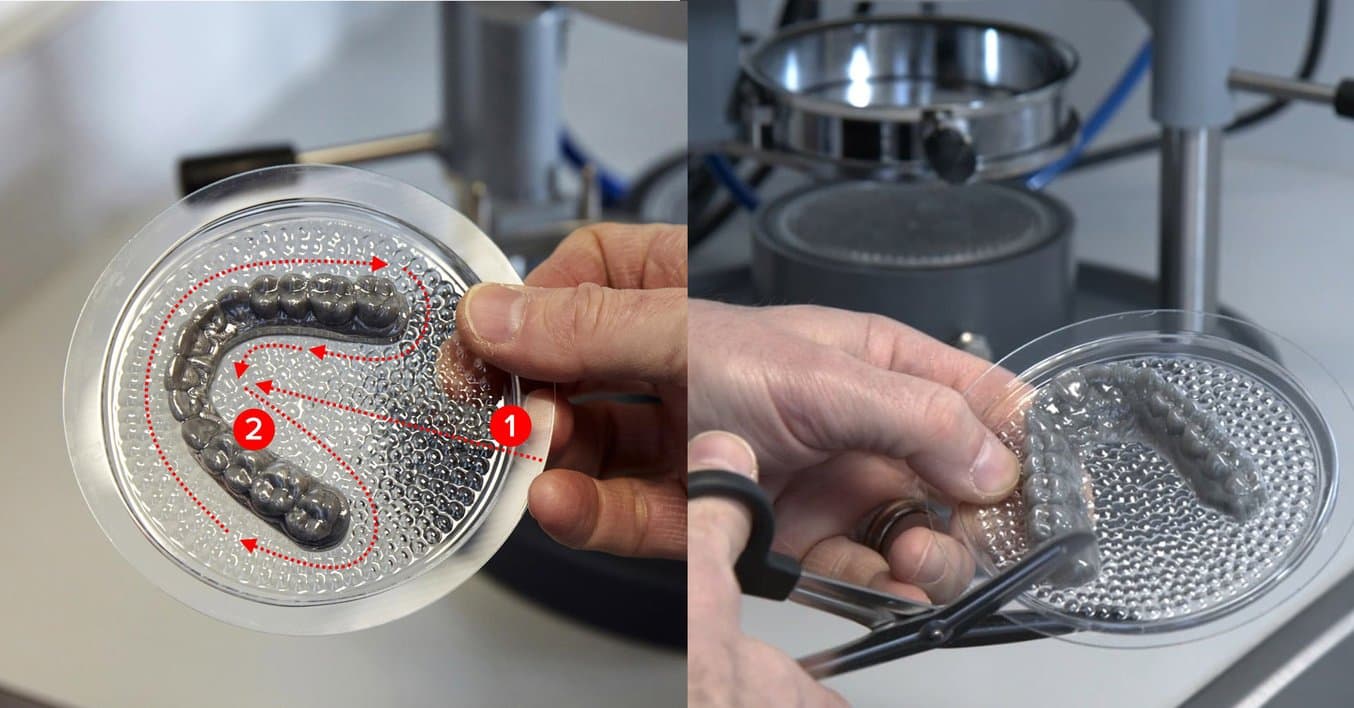
Use a dental low speed cutting disc or wheel to cut the back corner of the plastic away (see 3).
Be sure to leave enough material around the rearmost molar to meet specifications.
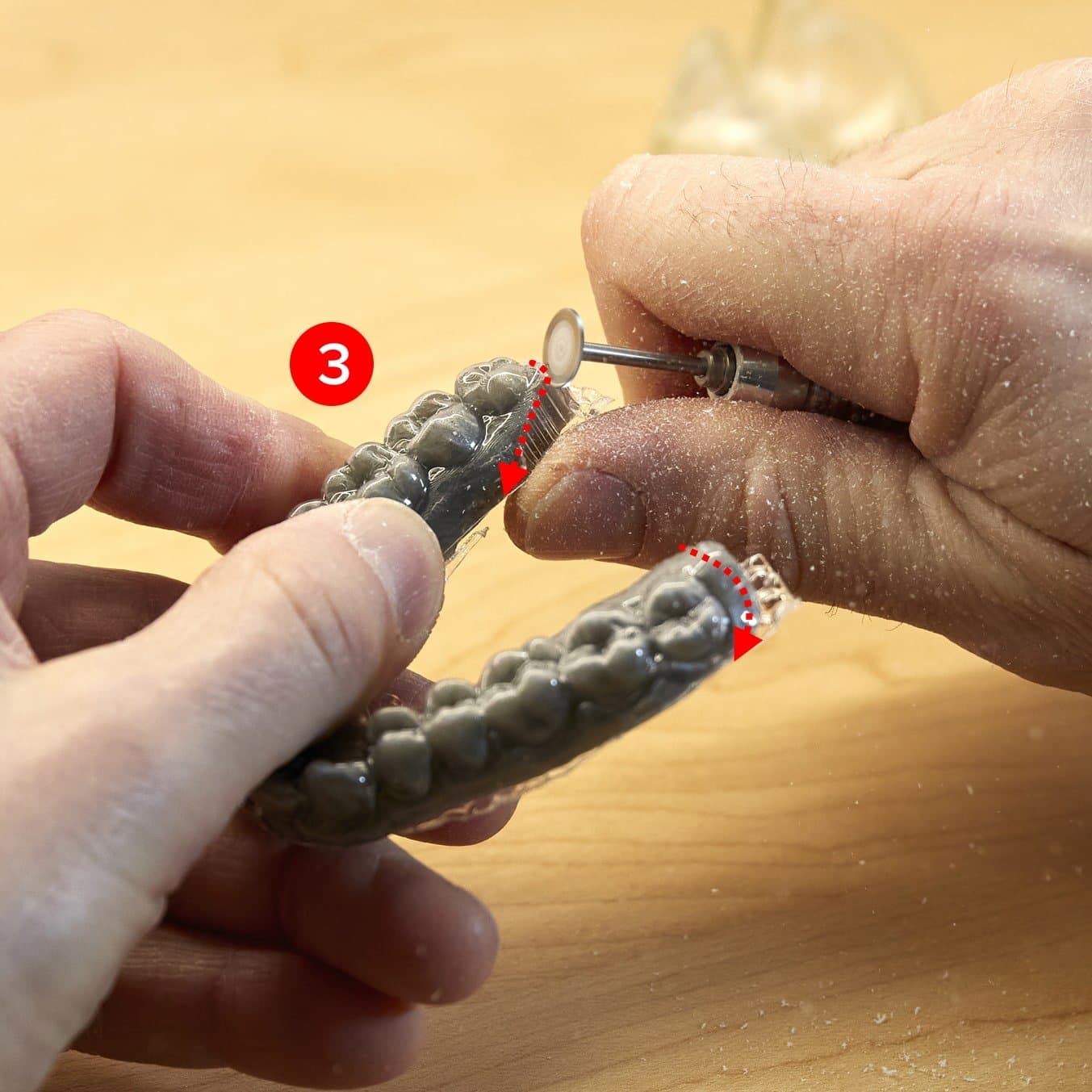
Using a pry tool, work under and between the model and thermoformed sheet (see 4).
Work and lift towards the anterior of the arch.
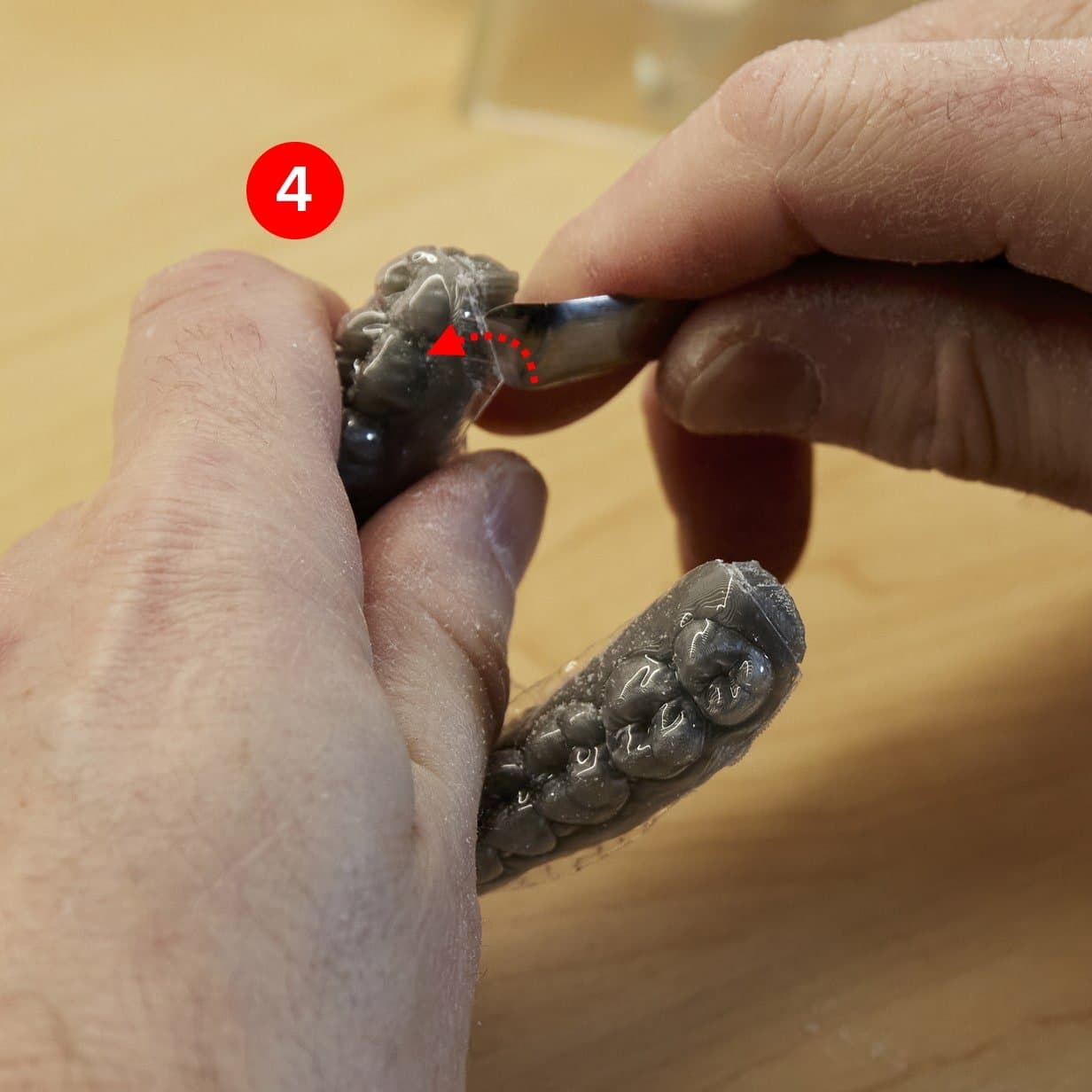
6.2 Trimming
Using sharp, high quality iris scissors trim the appliance to the desired cervical distance.
Working slowly and carefully in this stage can produce the finished appliance.
Tip: Curved scissors can help on the lingual side of the appliance.
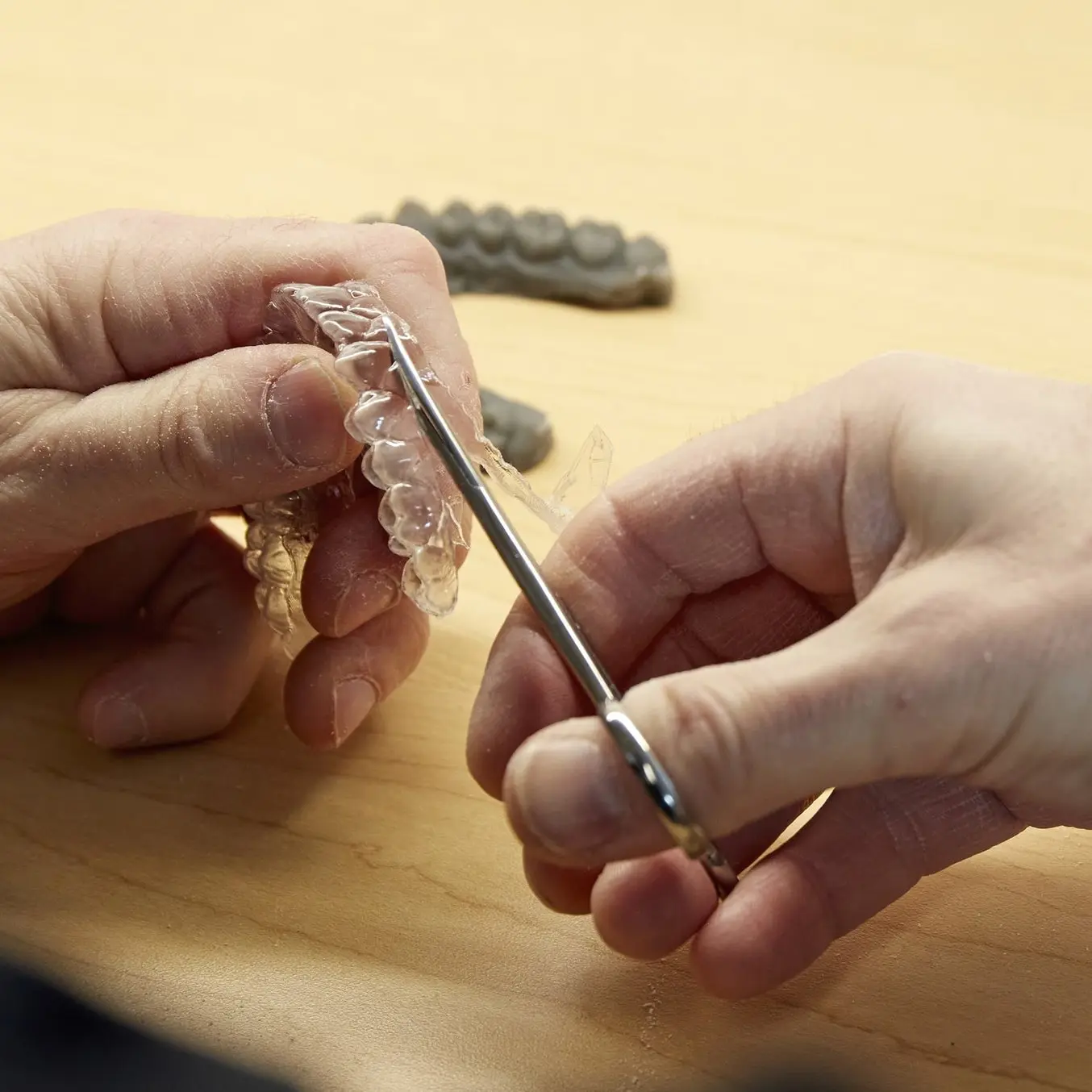
6.3 Finishing and QC
Perform a quality control check to confirm the appliance is complete.
Tip: There are many ways to finish thermoformed retainers and aligners. Thermoforming materials can cut and finish differently by brand and thickness. Choose what technique works best for the material and you.
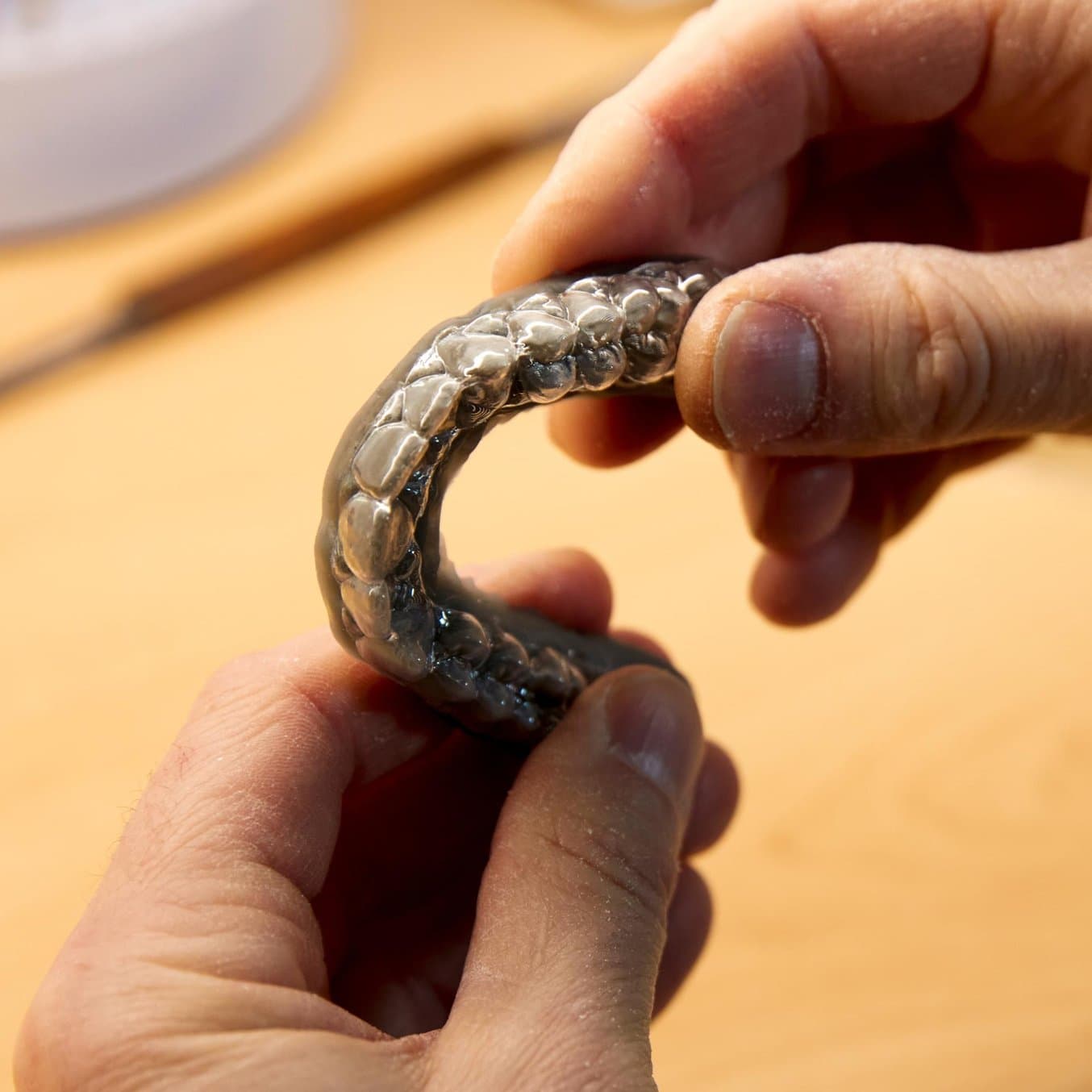
6.4 Alternate Appliance Removal
Rough cut the appliance with a cutting disc directly on the model using a low speed rotary wheel.
While this process can be quicker than others it becomes a messier process and requires bench suction and/or use of a respirator to be safe.
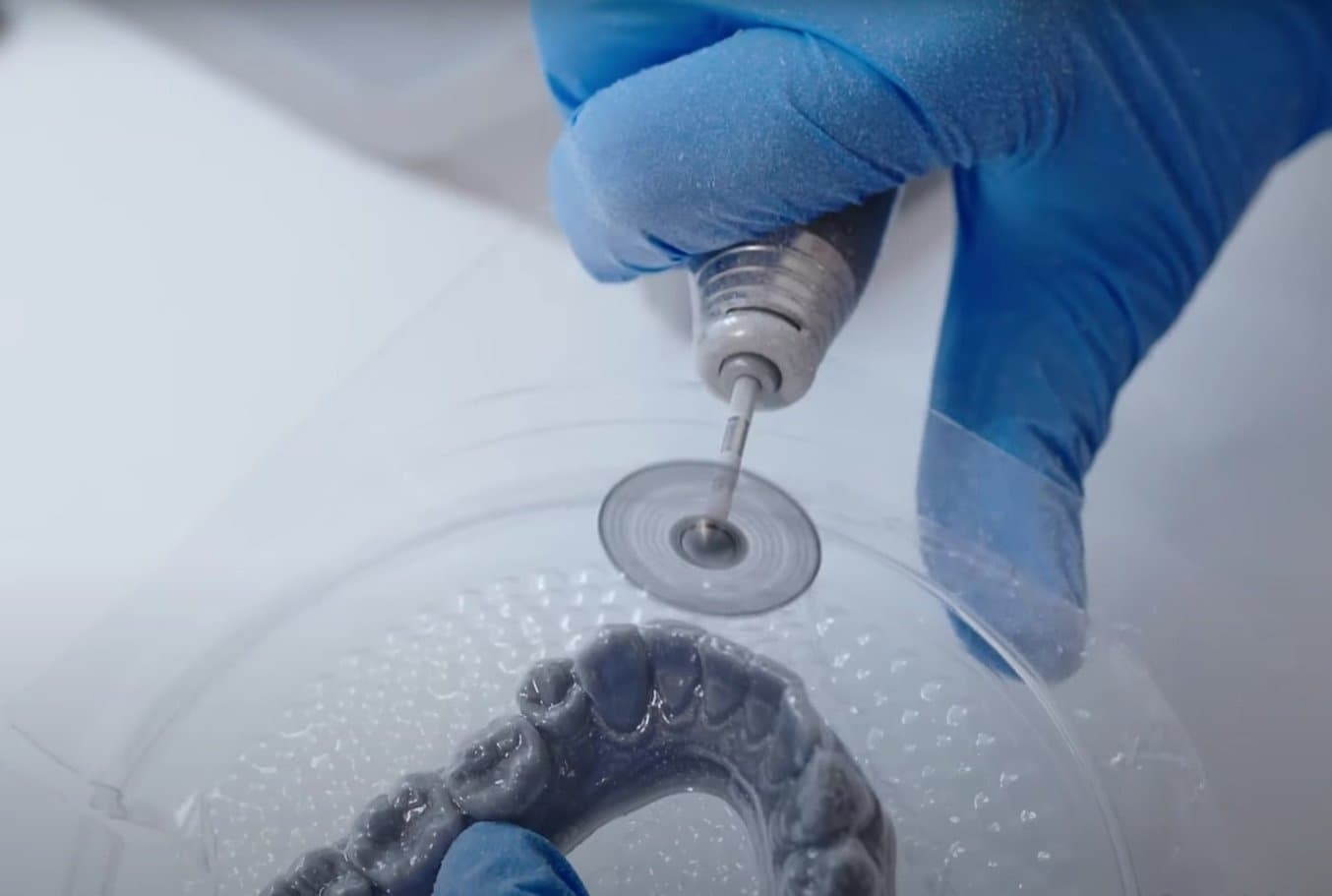
6.5 Alternate Trimming Method
A fluted cone or barrel shaped rotary can help finish down tight corners and rough edges.
This can be helpful if producing appliances that meet the cervical margin and papila.
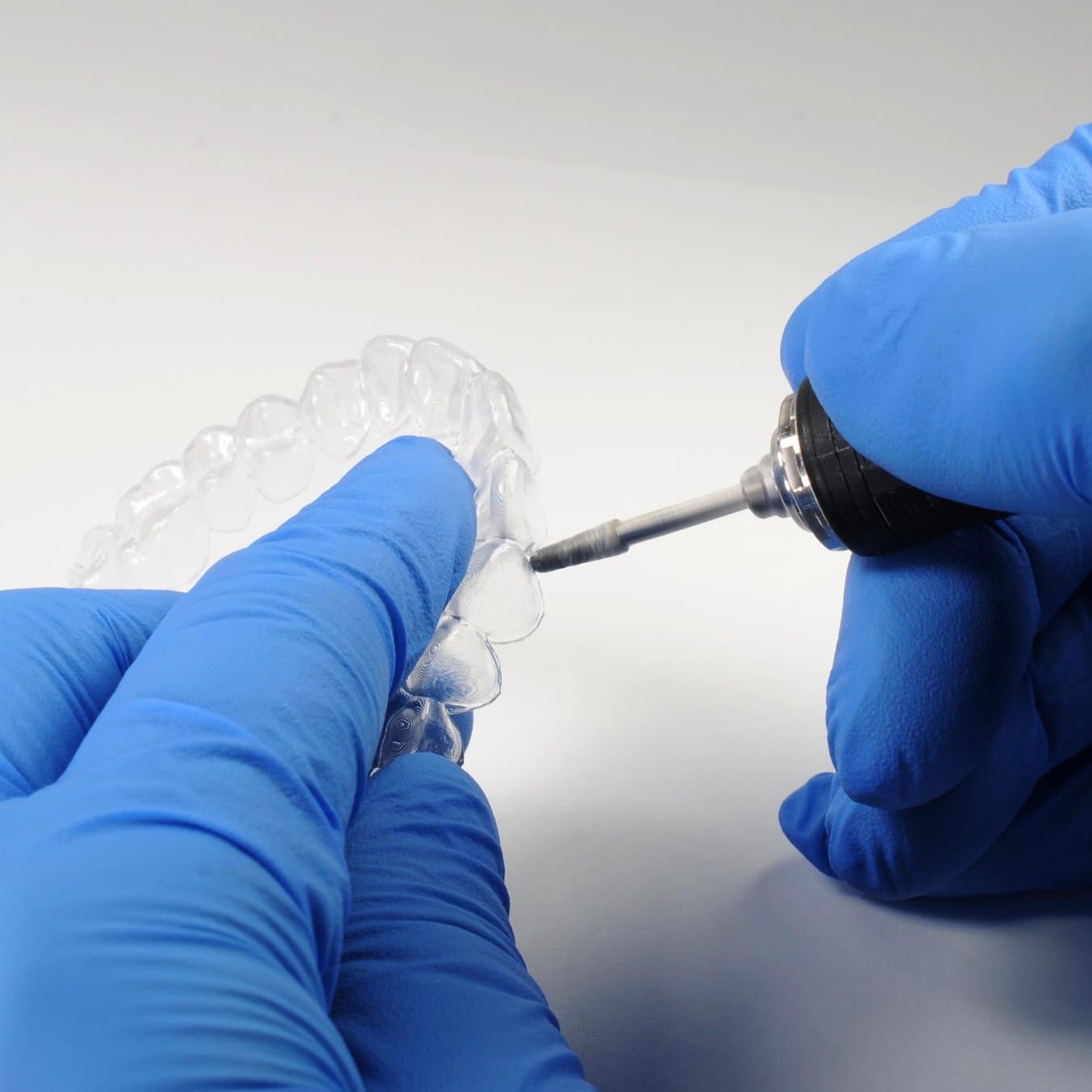
6.6 Alternate Finishing Method
When cutting or trimming with a dental handpiece it can create flashing and rough edges.
A “deburring” wheel or rotary can be used to finish the edges of the appliance.
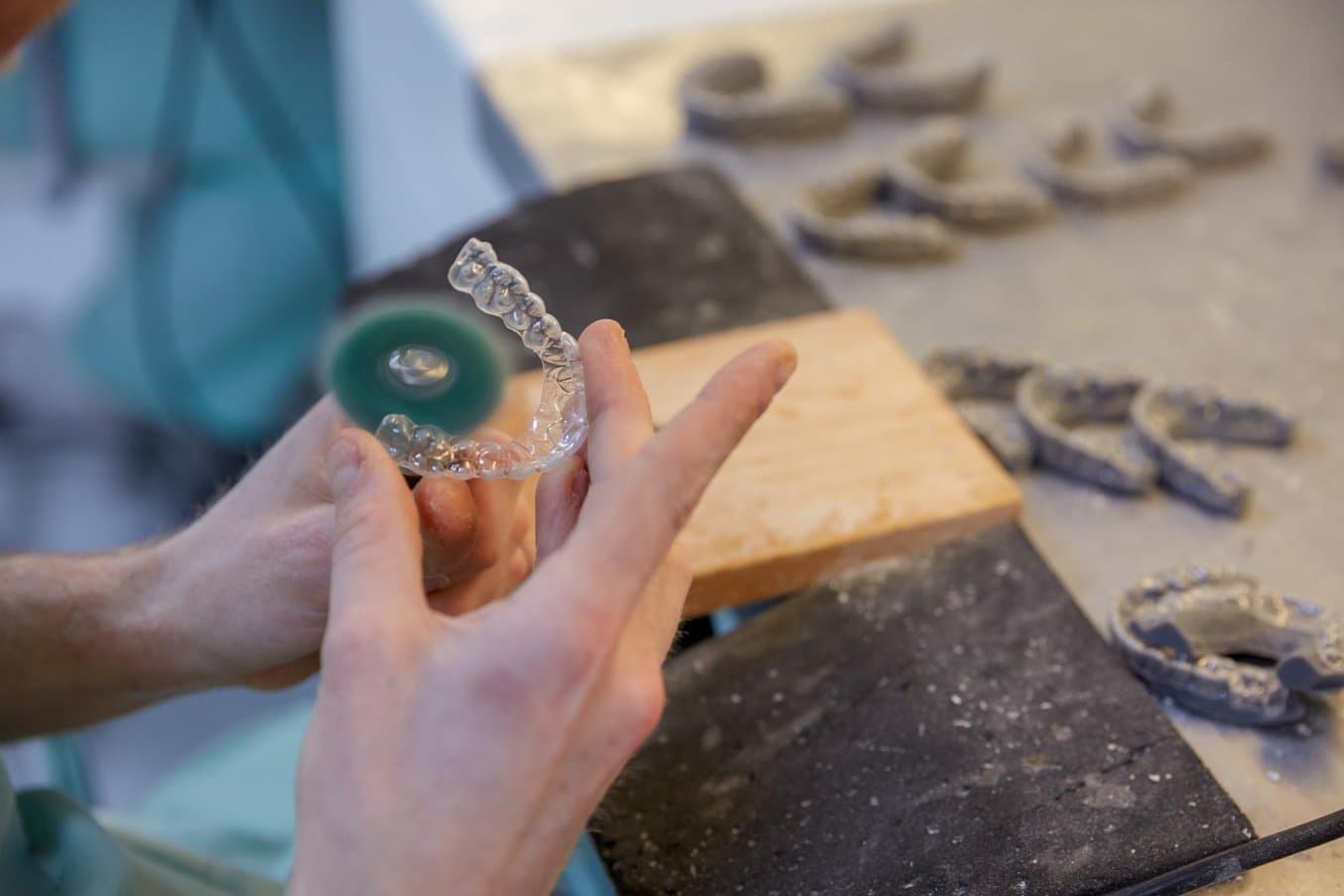