How Dr. Lanoiselée’s Digital Practice Adopted IBT Flex Resin for Direct Composite Restoration Guides
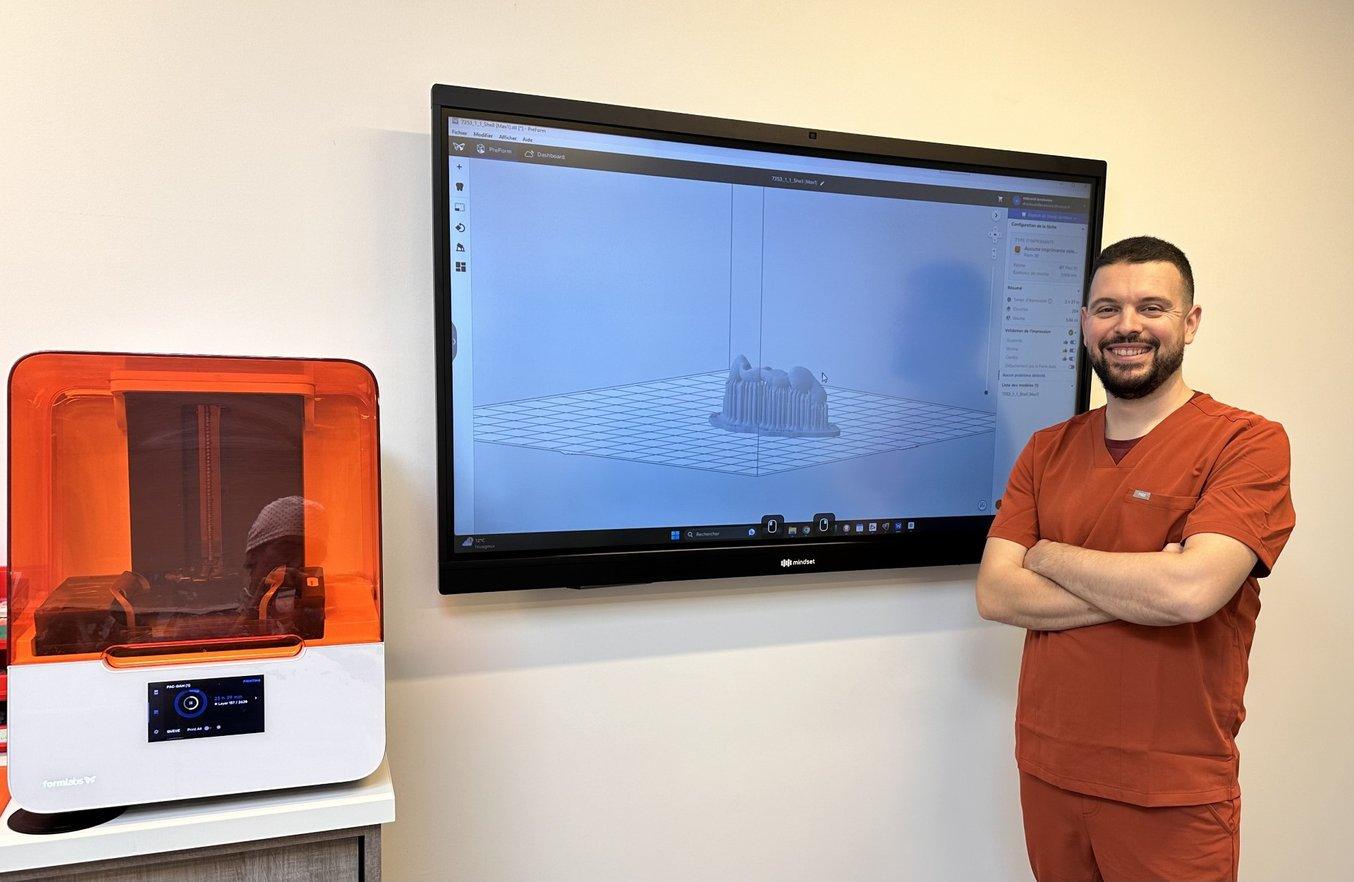
For Dr. Édouard Lanoiselée, digital dentistry is an essential part of providing top-notch patient care, advancing the art and science of dentistry, and running an efficient business.
Dr. Édouard Lanoiselée realized early in his career that digital workflows offered substantial benefits for his practice such as saving time and reducing costs while improving clinical outcomes. His Nozay, France dental practice was a pioneer in adopting digital technologies such as intraoral scanning and 3D printing.
“Having digital technologies inside the office makes workflows easier, earns time for me and my patients, and saves costs,” explains Dr. Lanoiselée. “The workflows are very easy and reassuring for us. My staff and I are excited when we can adopt a new digital workflow.”
With Formlabs’ new IBT Flex Resin, dentists can print guides for direct composite restorations for the first time ever. For Dr. Lanoiselée, this new capability opens up exciting opportunities.
“It’s a very interesting resin with a different way of working,” says Dr. Lanoiselée. “When you can jump directly from a digital scan to the composite guide, you earn a lot of time and save costs. You don’t consume a lot of the IBT Flex Resin when you print direct composite restoration guides.”
IBT Flex Resin Opens New Horizons
In late summer 2023, Dr. Lanoiselée took part in beta testing for a new material, IBT Flex Resin. One of its indications - direct composite restoration guides - did not yet exist for any 3D printing workflow. When Dr. Lanoiselée tried it, he immediately saw its potential - just as he’d seen the potential for many other technologies and workflows over the years.
“When I compared the 3D printing process to the traditional way of working, using IBT Flex Resin was clearly easier and more cost-effective.”
Dr. Édouard Lanoiselée, DDS, Cabinet dentaire de Nozay
Dr. Lanoiselée tested a wide variety of printed trays for different clinical situations. These included printing trays for injectable composite technique, partial and full mouth mock-ups with bis-acryl resin, and palatal indexes for a Class IV incisal edge reconstruction case.
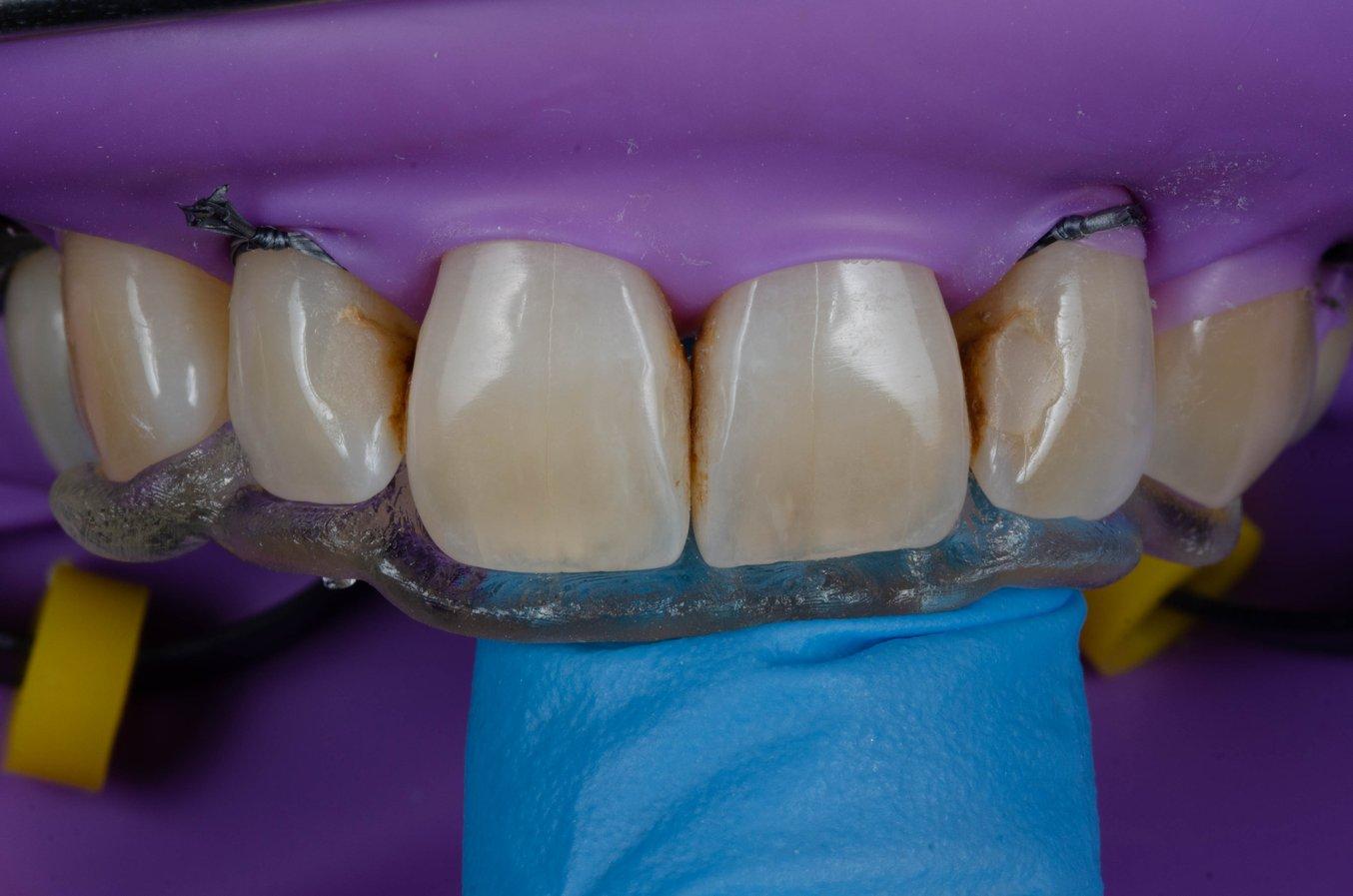
Fitment check and usage of a printed palatal index for Class III restorations in lateral incisors.
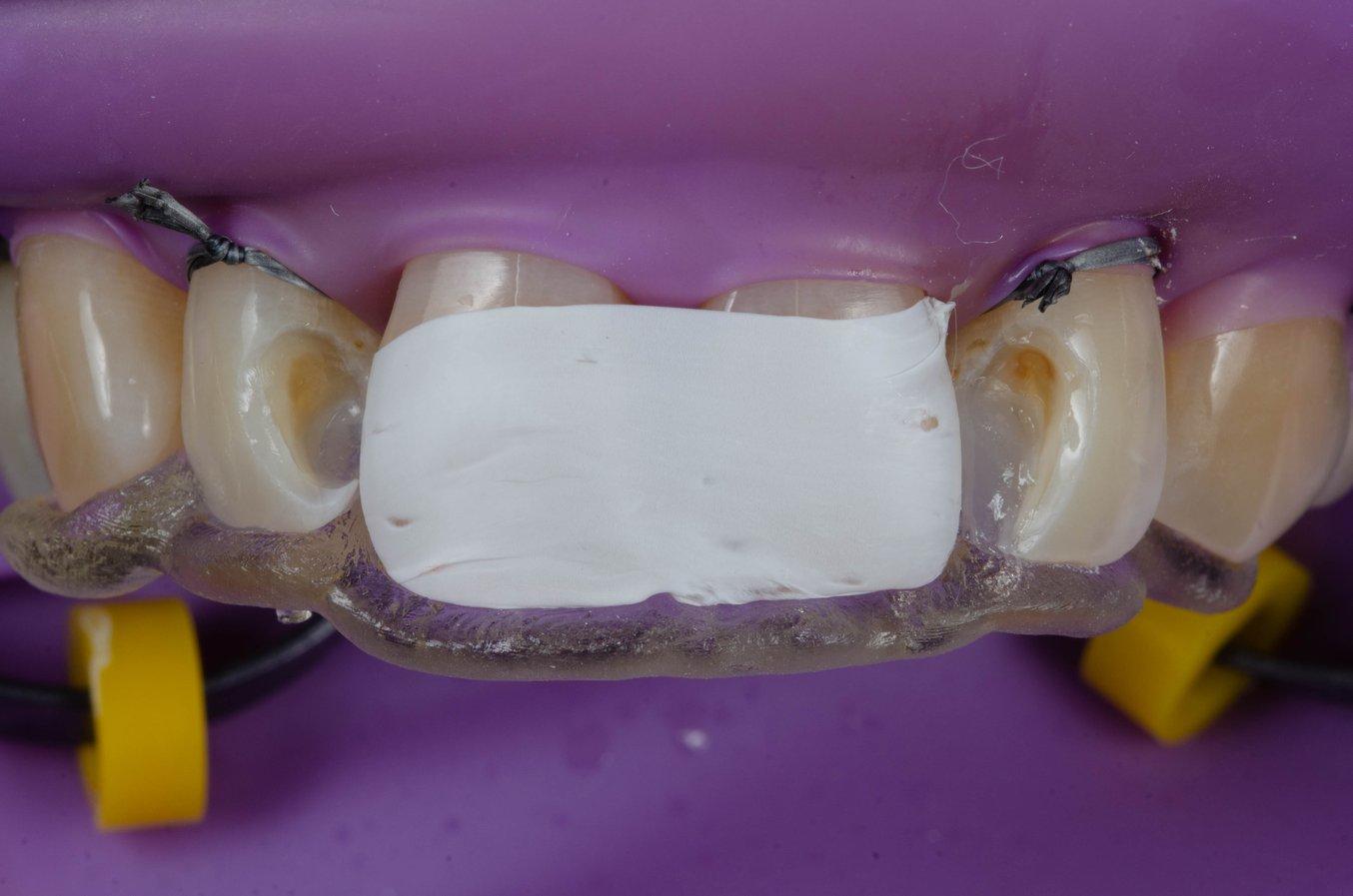
Printed palatal index used for Class III restorations of lateral incisors.
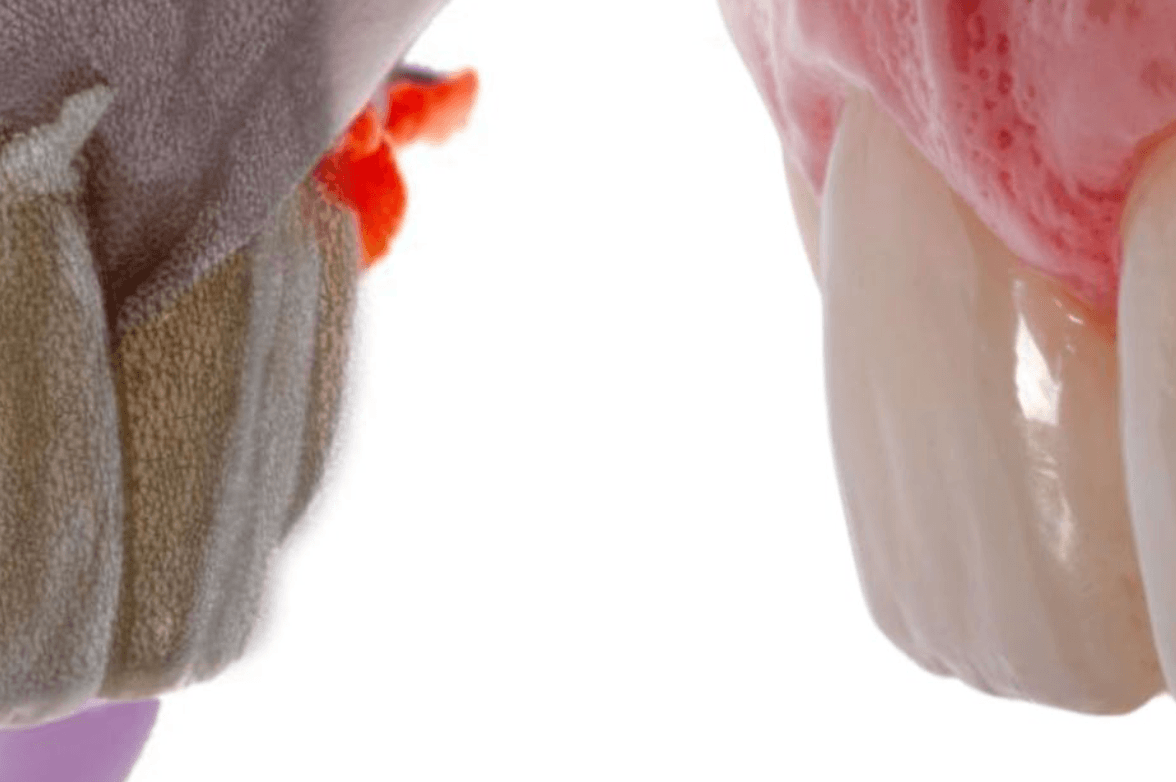
Aesthetic Direct Composite Restoration Using a 3D Printed Palatal Key
In this clinical case study, Dr. Édouard Lanoiselée gives a step-by-step overview of how he uses a palatal key 3D printed with IBT Flex Resin to perform a direct composite restoration in the anterior sector.
Certifications and Compliance
Formlabs’ new IBT Flex Resin is the first and only 3D printing material indicated for direct composite restoration guides. Biocompatible, FDA-listed, and CE Marked according to the EU MDR, IBT Flex Resin is manufactured in the United States at Formlabs’ ISO 13485 certified facility for dental and medical materials development and manufacturing. IBT Flex Resin can be used in Formlabs Form 3B/+, and Form 3BL stereolithography (SLA) 3D printers.
When it comes to 3D printing, certification and compliance are of the utmost importance to Dr. Lanoiselée. “We only use biocompatible and certified systems because we want to be ready for regulations.”
Dr. Lanoiselée’s controlled ecosystem helps him make sure that he stays compliant with Annex I of the EU’s Medical Device Regulation (MDR). “With a certified workflow we can ensure the quality of our printings,” he says. “Plus, biocompatibility testing ensures that we are prioritizing patient safety.”
“IBT Flex Resin was designed and validated for use as direct composite restoration guides in compliance with the requirements of US FDA and EU MDR regulations for medical devices. Performance and safety testing of IBT Flex Resin has been performed and is documented in the device technical file to support FDA listing and EU MDR certification.”
Nathan Alt, Director, Regulatory Affairs and Quality Assurance, Formlabs
Direct Composite Restorations: A New Application for Digital Dentistry
A direct composite restoration, which involves the bonding of composite resins to teeth in order to restore tooth defects, is one of the most common dental procedures performed globally.1 According to the ADA, in the United States alone over 76 million posterior composite restorations are placed each year.2 Additionally, in 2014, the Academy of Operative Dentistry European Section (AODES) declared that it views adhesively bonded resin composites with appropriate composition and properties as the preferred material for direct minimal intervention approaches in restoring posterior teeth.3
In traditional production, clear polyvinyl siloxane (PVS) and a stone or 3D printed model are used to create an index. Traditional silicone indexes can require the application of a separating agent to prevent the composite from adhering to it during clinical use. The procedure is highly manual, which means it can take extra time and leave room for error.
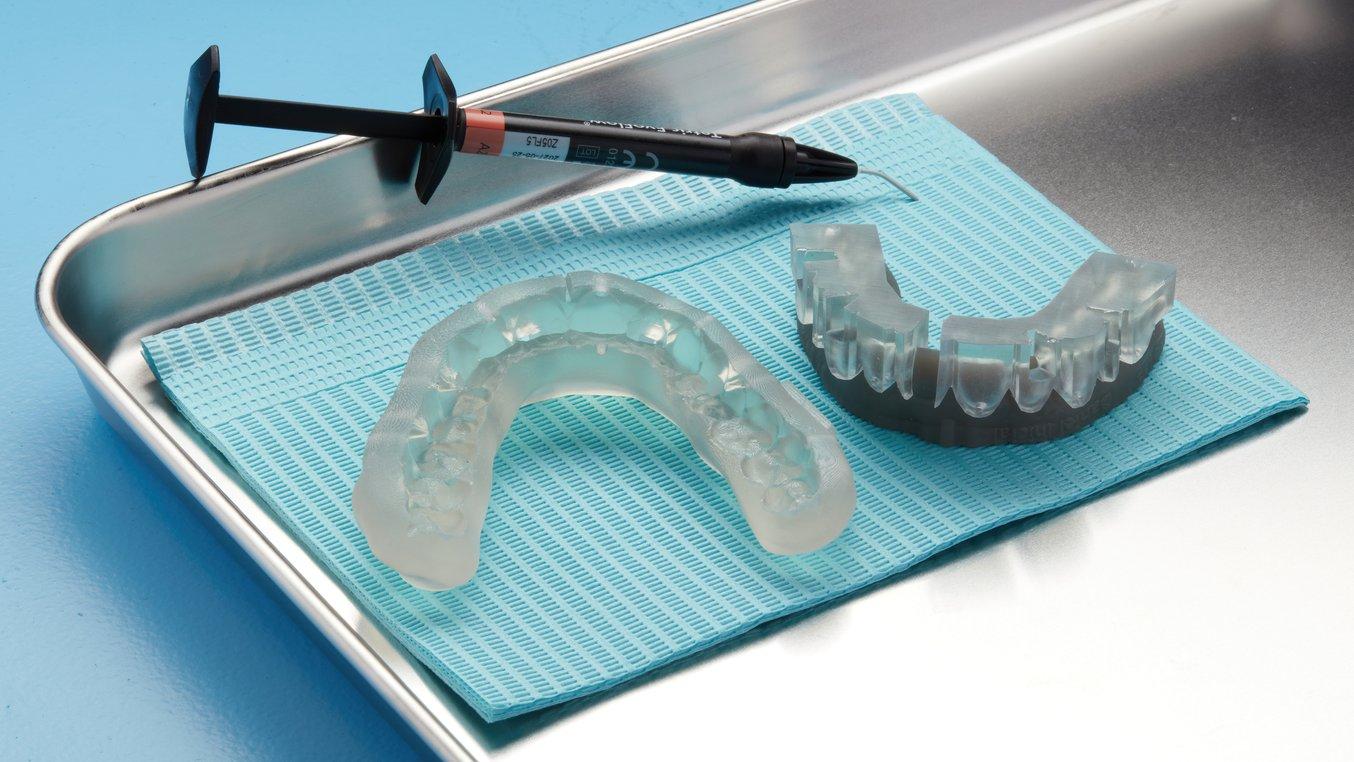
Unlock the Potential of 3D Printed Direct Composite Restoration Guides
In this webinar, Dr. Luken de Arbeloa, Education Content & KOL Manager at Digital Smile Design and Dr. Elisa Praderi, Senior Clinical Protocols & KOL Manager at Formlabs Dental will walk you through the workflow for 3D printing high quality direct composite restoration guides with IBT Flex Resin.
Faster, Easier, and More Cost-Effective
In addition to the advantages of the IBT Flex Resin’s material properties, leveraging a digital workflow for direct composite restoration guides means that Dr. Lanoiselée is able to pass savings onto his patients and improve their experience. As with other digital workflows, the ability to keep a digital record of the patient’s intraoral anatomy and designed appliances creates quicker visits and provides better results.
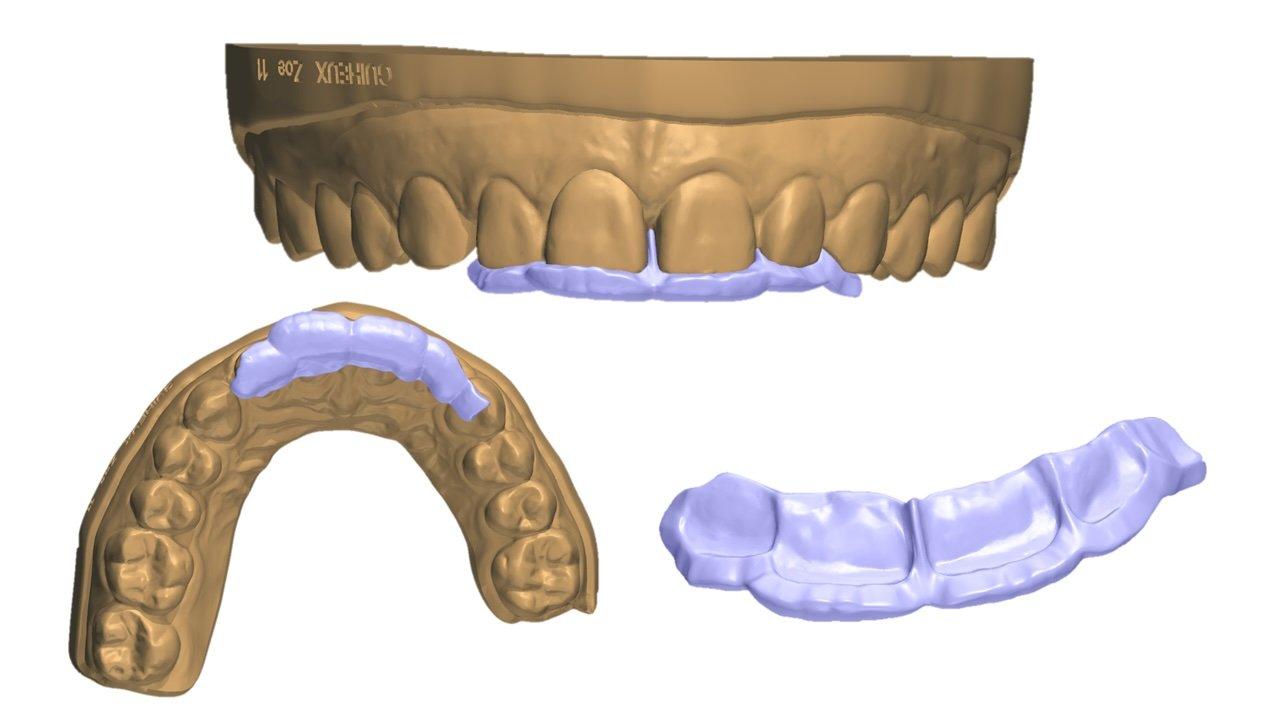
Intraoral scan transformed into a printable model and CAD design of the direct composite guide ready to be imported into PreForm Dental.
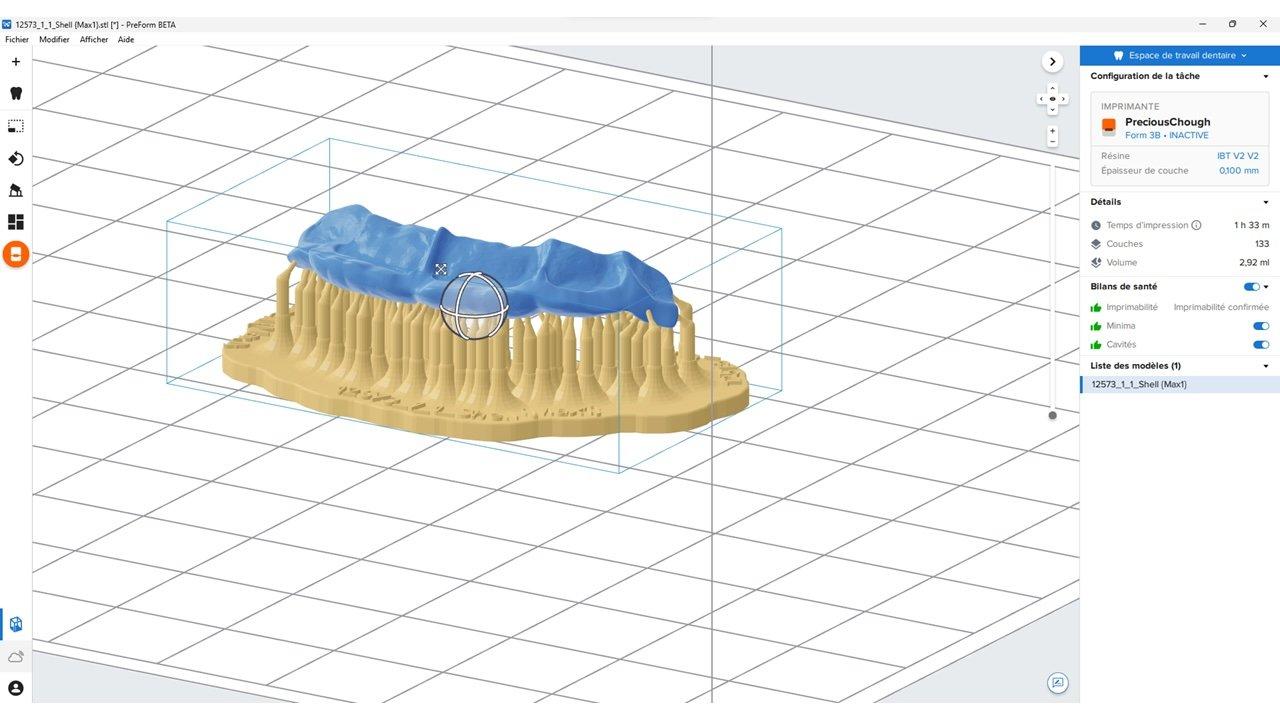
Formlabs PreForm Dental software enables print preparation and remote printer control with a few clicks.
“It’s very affordable for us and our patients. I don’t have to bill them big amounts,” says Dr. Lanoiselée. “And all the data is in my computer, so if I have to see a patient in an emergency because he broke another tooth, all I have to do is print another guide.”
Method | Cost per unit | |
---|---|---|
PVS tray | Denture teeth, All-on-X | $10-20 |
Direct composite restoration guides | IBT Flex Resin printed on a Form 3B+ | $2-5 |
By using IBT Flex Resin, Dr. Lanoiselée is able to skip costly and time-consuming steps such as printing out models, preparing them, purchasing different types of silicone, and trimming the indexes. For him, that makes 3D printing direct composite restoration guides a no-brainer.
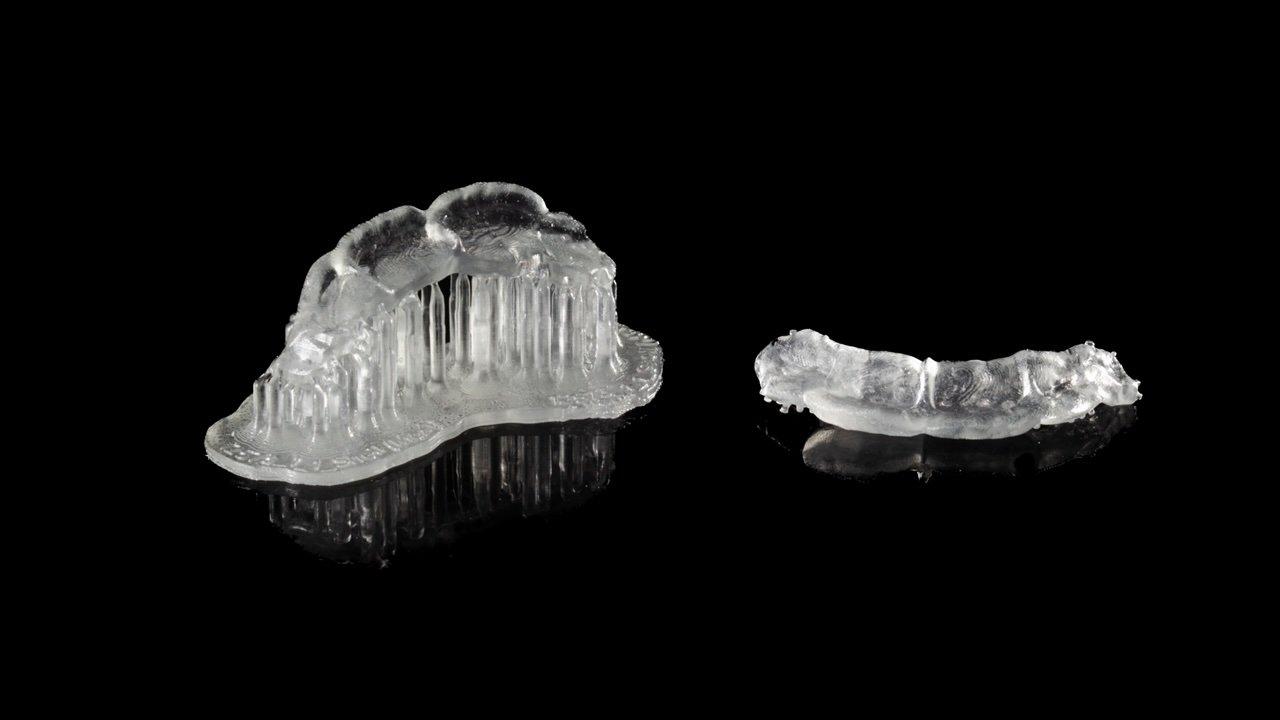
IBT Flex Resin direct composite restoration guides (palatal index) printed on a Form 3B+ 3D printer.
“We can do many restoration cases using this workflow and it helps me with my patients,” says Dr. Lanoiselée. “The traditional workflow is quite long and complicated and not cheap.”
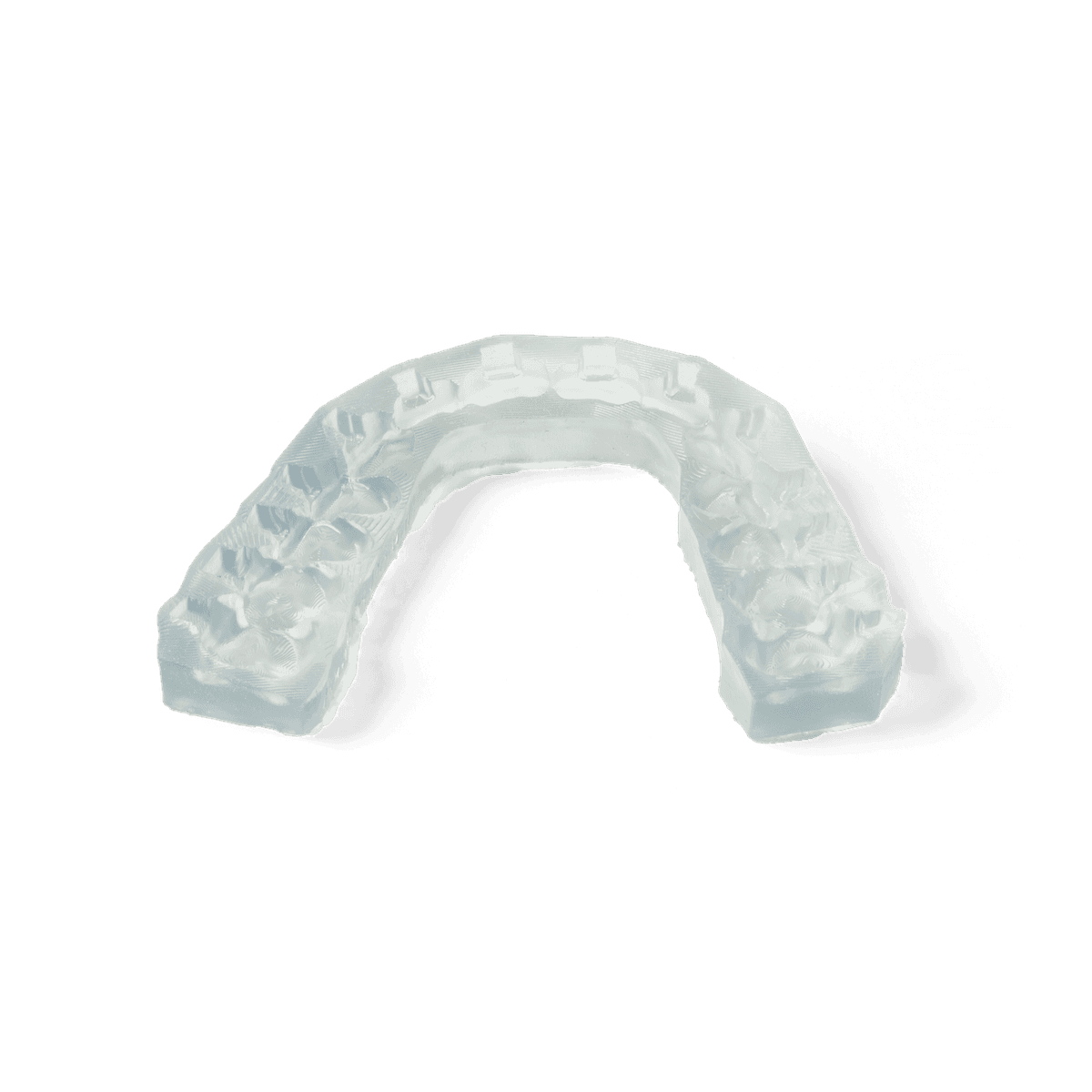
Request a Free Sample Part
See and feel Formlabs quality firsthand. We’ll ship a free IBT Flex Resin 3D printed sample part to your office.
No Need For Separating Agents
For Dr. Lanoiselée, one advantage of 3D printed direct composite restoration guides stands out above the rest: based on his experience with IBT Flex Resin printed on a Form 3B+, he does not have to use a separating agent between the printed guide and the restoration material.
Dr. Lanoiselée tests IBT Flex Resin with bisacryl resin and finds it does not adhere.
“I have used five kinds of acrylic resin and three types of composite resin, and none of them bonded to the printed material,” says Dr. Lanoiselée.
Unwanted bonding, which can occur in the traditional workflow when the resin intended for the restoration adheres to the silicone tray, has the potential to derail a direct composite restoration procedure.
“We can’t afford to have complicated protocols for the preparation of our guides,” says Dr. Lanoiselée, “because if I need to use many different materials to prevent bonding, it reduces my confidence in the outcome. The best way to ensure a good result is to have material that doesn’t bond to the resins.”
Dr. Lanoiselée’s tests allow him to create innovative workflows. We recommend that users test their own composite solutions with IBT Flex Resin to ensure a separating agent is not needed.
“The material is translucent, so you can always check if your flowable composite is correctly being injected and cured. It's flexible — it's not a rigid material — so you can also move it for the patient if necessary. It's comfortable and you can adjust it. You don't have problems with undercuts with that kind of material because you can jump around them. In my experience, it doesn't bond to resins, so you can inject and remove it with no problems.”
Dr. Édouard Lanoiselée, DDS, Cabinet dentaire de Nozay
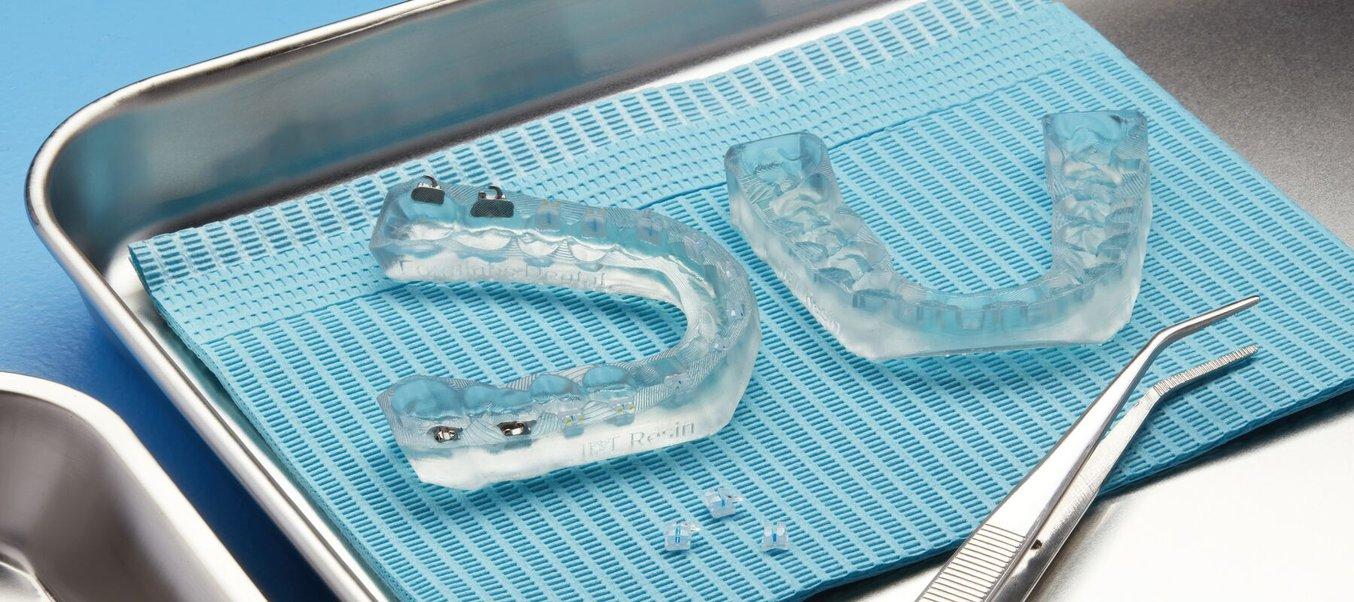
Indirect Bonding Trays for Orthodontic Bracket Placement With Formlabs SLA 3D Printers
This application guide is a step-by-step walkthrough of the workflow for producing indirect bonding trays for orthodontic bracket placement with Formlabs IBT Flex Resin and Formlabs Dental 3D printers.
Building the Digital Practice: Success With Stereolithography
Dr. Lanoiselée has been practicing for 15 years and leveraging the digital workflow for 13 years. Though the workflow wasn’t as seamless back then as it is today, he could already tell that digital dentistry would become a major part of the dental practice of the future. There was serious potential for improving patient outcomes and saving money and time.
“I worked with some digital labs who told me about 3D printing, and I started learning with them,” says Dr. Lanoiselée. “It was obvious that 3D printing was the next step for us.”
“Sometimes you need quick answers for your patients. My printer is in my office so they can see it working. Sometimes it helps them to understand what we are doing now in dentistry because it's quite different from the past. And also it's a new way to communicate with them and to explain why we work and how technology improves the quality of their treatment.”
Dr. Édouard Lanoiselée, DDS, Cabinet dentaire de Nozay
Initially, he tested FDM machines in order to get a feel for the technology. He soon realized that a professional stereolithography (SLA) 3D printer was required to support a digital dental practice.
After years of using intraoral scanners, Dr. Lanoiselée began using Formlabs 3D printers in 2020. At first, he printed models for bleaching trays as well as to help explain procedures to patients. Immediately, he began to see the advantages created by bringing production in-house.
“Working with a lab can cost you time and money,” says Dr. Lanoiselée. “This way, I can design and produce in my office directly.”
He soon added applications to his in-house manufacturing capabilities. Using a digital workflow that consisted of 3Shape intraoral scanners, the 3Shape Dental System and Appliance Designer, and Formlabs 3D printers, he saw serious time and cost savings, as well as increased control over his workflow.
Dr. Lanoiselée uses Formlabs 3D printers and dental materials to print models, direct composite restoration guides, surgical guides, provisional crowns, long-lasting temporary restorations such as bridges, permanent restorations for inlays, temporary and permanent dentures, and splints.
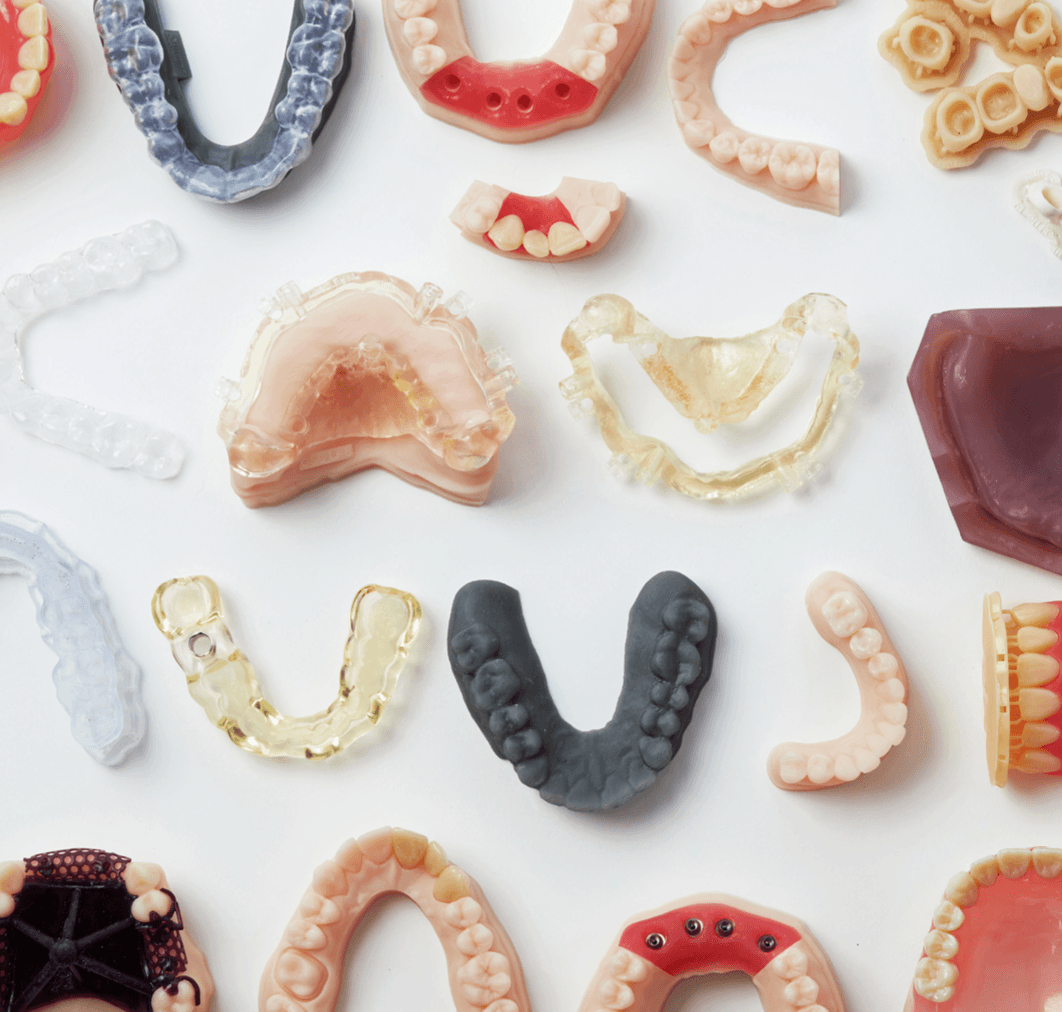
An Introduction to Regulatory Compliance in Dental 3D Printing
Implementing 3D printing workflows in your lab or practice can be a game changer for your business. Understanding the basics of regulatory compliance can help inform your decisions and what is best for your business. Regulation depends on geography; in this paper, we examine regulations in the United States of America and the European Union.
Driving Innovation in Digital Dentistry
In addition to increased efficiency and control, Dr. Lanoiselée’s partnership with Formlabs has helped him push the cutting edge of dentistry, using technology to deliver better results for patients. Dr. Lanoiselée believes his collaboration with Formlabs is a symbiotic relationship that allows him to improve his practice while providing feedback that drives 3D printing innovation.
“Formlabs makes new materials that are compatible with our workflow,” says Dr. Lanoiselée. “They work with us and they learn what we need.”
IBT Flex Resin reinforces the Formlabs Dental promise of making dentistry easier. Learn more about IBT Flex Resin and how dentists are integrating it into their workflows, or request a sample for yourself.
Reference
1. Society Of Cariology And Endodontology C. S. (2015). Guidelines for Direct Adhesive Composite Restoration. The Chinese journal of dental research, 18(4), 217–220. https://doi.org/10.3290/j.cjdr.a35145
2. ADA Report on Dental Services Rendered
3. Lynch, C. D., Opdam, N. J., Hickel, R., Brunton, P. A., Gurgan, S., Kakaboura, A., Shearer, A. C., Vanherle, G., Wilson, N. H., & Academy of Operative Dentistry European Section (2014). Guidance on posterior resin composites: Academy of Operative Dentistry - European Section. Journal of dentistry, 42(4), 377–383. https://doi.org/10.1016/j.jdent.2014.01.009