How a Dental Lab Leverages 3D Printed Try-Ins for Telescopic Prosthesis Production
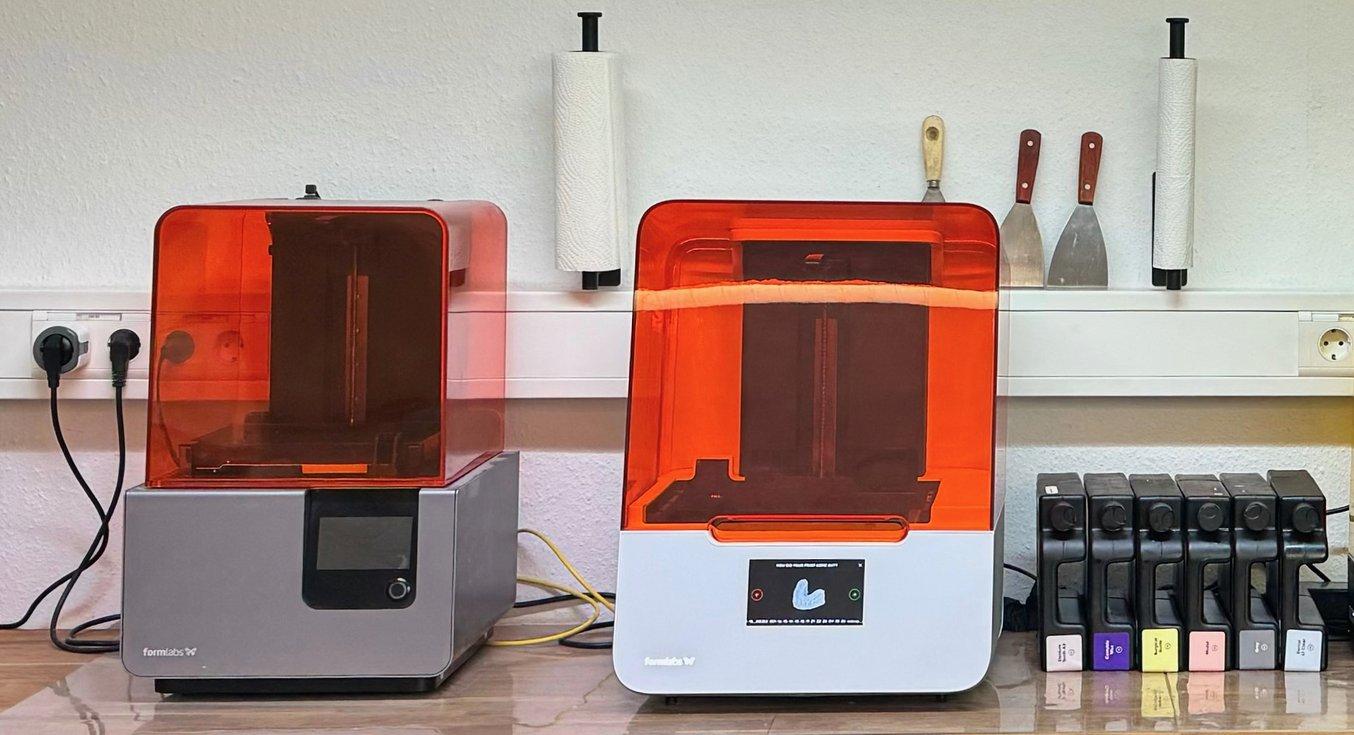
Die Zahnwerkstatt Dental Lab in Weißenhorn, Germany, has been putting smiles on people's faces since 2011. With a passion for craftsmanship and precision, the dental lab specializes in the creation of telescopic prostheses.
For founder and CEO Andreas Leimbach, the goal is to have every patient eager to share their smile with the world at the end of their procedure. This is why the aesthetic requests of patients drive the development of their treatment.
The manufacturing of dentures has always been a case-specific, manual task that relies on an individual dental technician's skill level. While this makes the profession exciting and versatile, it also bears the risk of human error. To reliably produce high-quality customized dentures and restorations, Andreas Leimbach turned to modern technologies and processes.
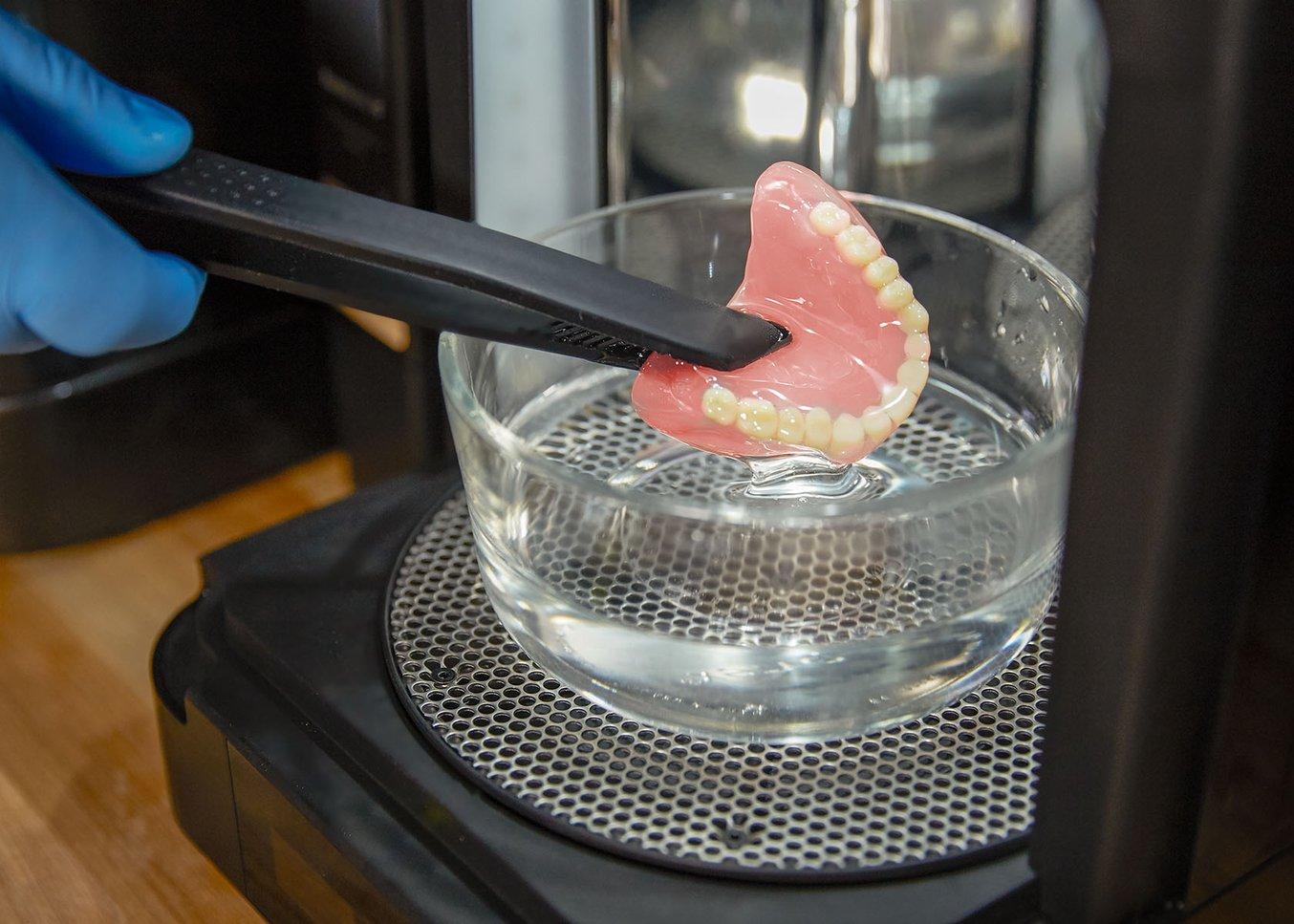
Digital Dentures with Formlabs Dental and VITA
Increase your knowledge of digital full dentures and benefit from the advantages of this innovative technology. In this session, we will also showcase how to characterize printed dentures to achieve perfect aesthetics.
Achieving Aesthetics and Function With Backward Planning
In the past, the design of dental restorations has been focused on function, with aesthetics and patient preferences a secondary consideration at best.
Dental technicians receive the first feedback on a restoration during the planning and tooth setup phase. However, this phase is preceded by several workflow steps and cumbersome tasks including manufacturing the primary components, try-on sessions and impressions, and the creation of the frame. "If we reached the point where a dentist called and said: 'This looks really terrible,' we had to go back to square one. But by then, a lot of workflow steps had already been done,“ Leimbach recalls.
Frustrated over this waste of time and materials, Leimbach started utilizing backward planning. This involves basing production on the desired end result. With backward planning, dental professionals and patients utilize temporary restorations like mock-ups, wax-ups, and try-ins early in the process, so that feedback can be implemented in the treatment plan.
Leimbach always begins by prototyping the restoration in the form of a try-in that can be tested for phonetic functionality and aesthetics. Only once he receives positive feedback on the restoration does he continue to develop the primary components. That way he avoids surprises, redesigns, costly modifications, disappointed patients, and unnecessary labor – as well as the frustration that comes with it.
"Starting from the first second, I want to be working towards something useful in my lab, and that's only possible if the patient knows from the beginning what his new teeth will look like. That's why I create try-ins right at the start and get their feedback,“ Leimbach explains.
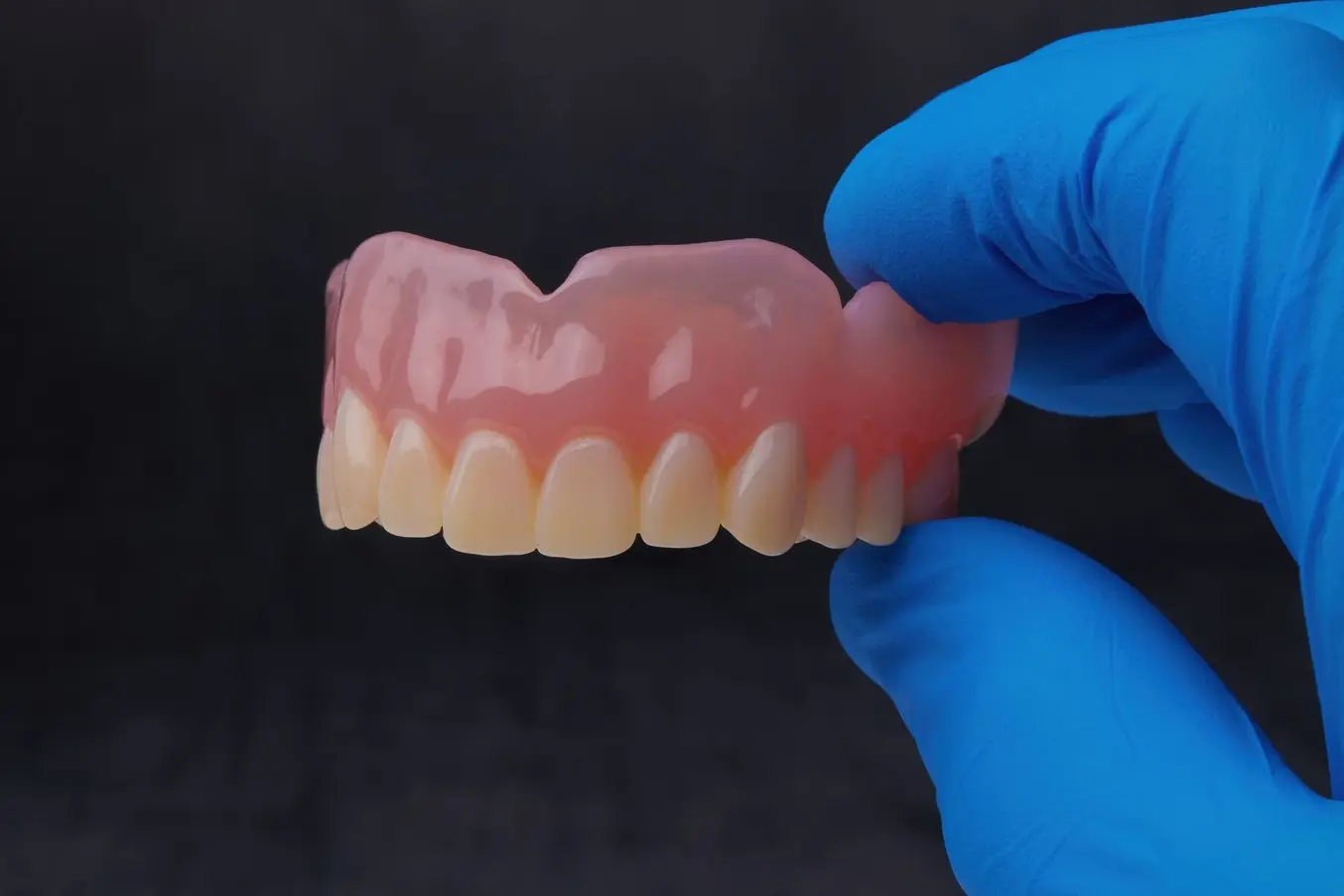
Longevity of Appliances Made With Premium Teeth Resin: In-Vitro Evaluation
Longevity is a critical factor in selecting a material for producing teeth for patients. In this paper, we present findings from a series of in-vitro studies conducted on Premium Teeth Resin to demonstrate the longevity and predict its clinical performance.
The Additive Advantage
Today, Leimbach has shifted to a wholly digital process. For denture planning, he uses CAD software by 3Shape, exocad, or Zirkonzahn, printing the designs on the Form 3B+ stereolithography (SLA) 3D printer. This process is purely additive. Any subtractive manufacturing Leimbach’s lab uses is limited to milling zirconium material with a small vhf milling machine. Larger CNC machines, like the ones used to machine steel, have never tempted him due to their high upfront cost, high material usage, and laborious maintenance.
"That type of subtractive technique does not fit into my world. I think 3D printing is great, because it's additive, it saves material, it saves costs, it's efficient, it's fast.”
Andreas Leimbach, Master Dental Technician and CEO, Die Zahnwerkstatt
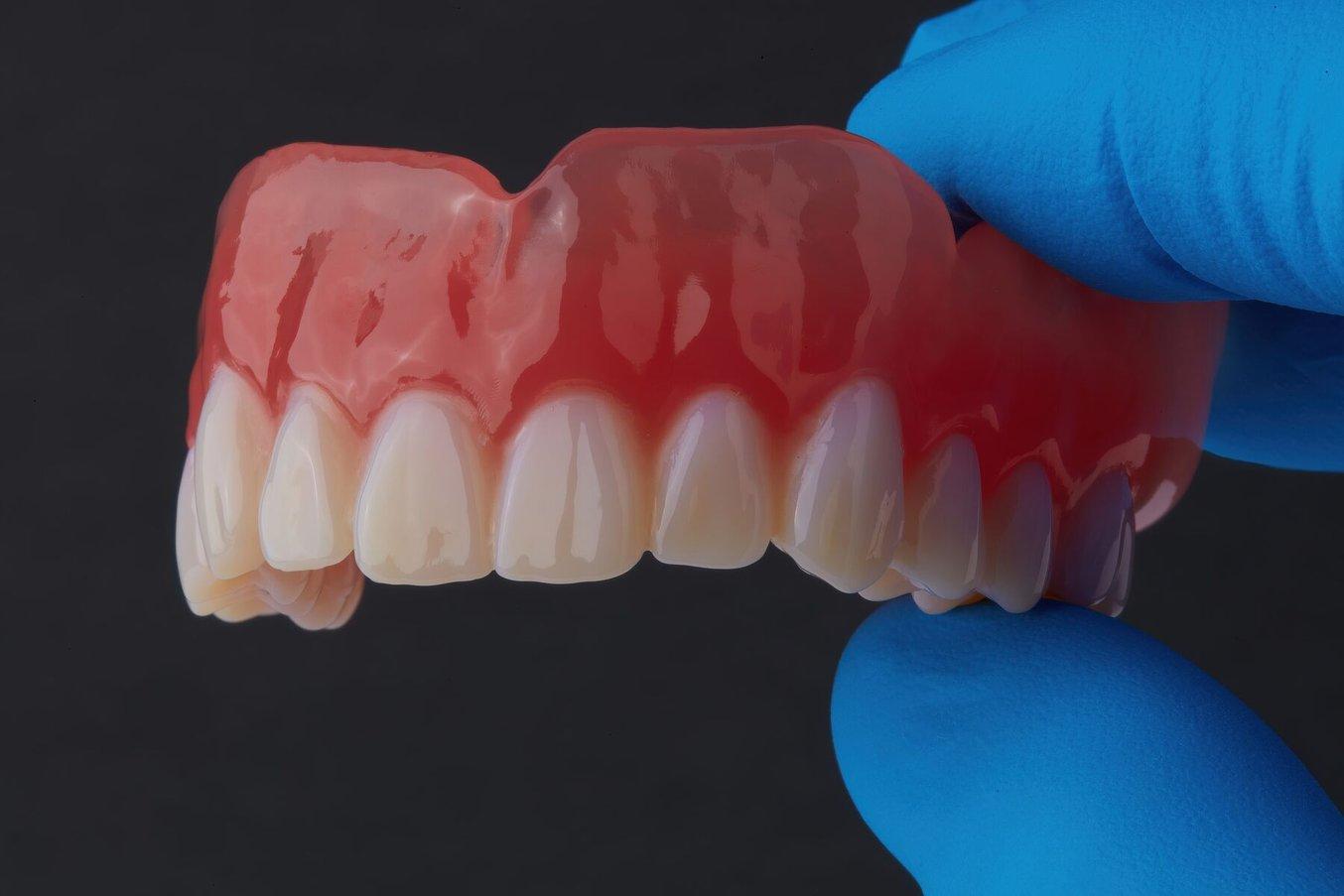
Techniques for Aesthetic Digital Dentures: 3D Printing Workflow and Characterization
Learn the digital workflow for printing and producing dentures together with a step-by-step characterization technique demonstration for optimal results.
Achieving a Work-Life Balance
The day Leimbach received his first Formlabs resin printer, he had the manufacturing of two try-ins still due. With evening plans approaching, it seemed unlikely he’d finish the try-ins in time, meaning he’d have to stay late, disappointing his wife and four kids.
With previous workflows, he had to customize and set up each individual tooth for prototypes like these, taking hours of his time. On this day, however, he had to work faster in order to avoid a family dispute.
When the printer was delivered, Leimbach says he thought, “Okay, rather than sitting here, setting up these teeth for four hours and getting a telling-off from my wife, I'm going to construct this virtually. I had done it that way a few times before, just because I was curious to try out new processes. So that's how I did it, and I set up the 28 teeth within half an hour.”
Andreas Leimbach hit print and left to enjoy his evening. The next morning, he marveled at the quality of the prints as he worked on post-processing: washing in the Form Wash, curing in the Form Cure, removing the supports, and testing the model in an articulator. Impressed by the intuitive printer operation and the efficient and clean post-processing workflow, he knew he would never again create try-ins the analog way.
"It was simply plug-and-play, and already on my first try, I got exactly the result that I wanted. I received 28 teeth and saved myself from a lot of mess and labor time, since both printing and post-processing only took me around one hour. The analog method is just no match, with four hours for the setup and the subsequent clean-up."
Andreas Leimbach, Master Dental Technician and CEO, Die Zahnwerkstatt
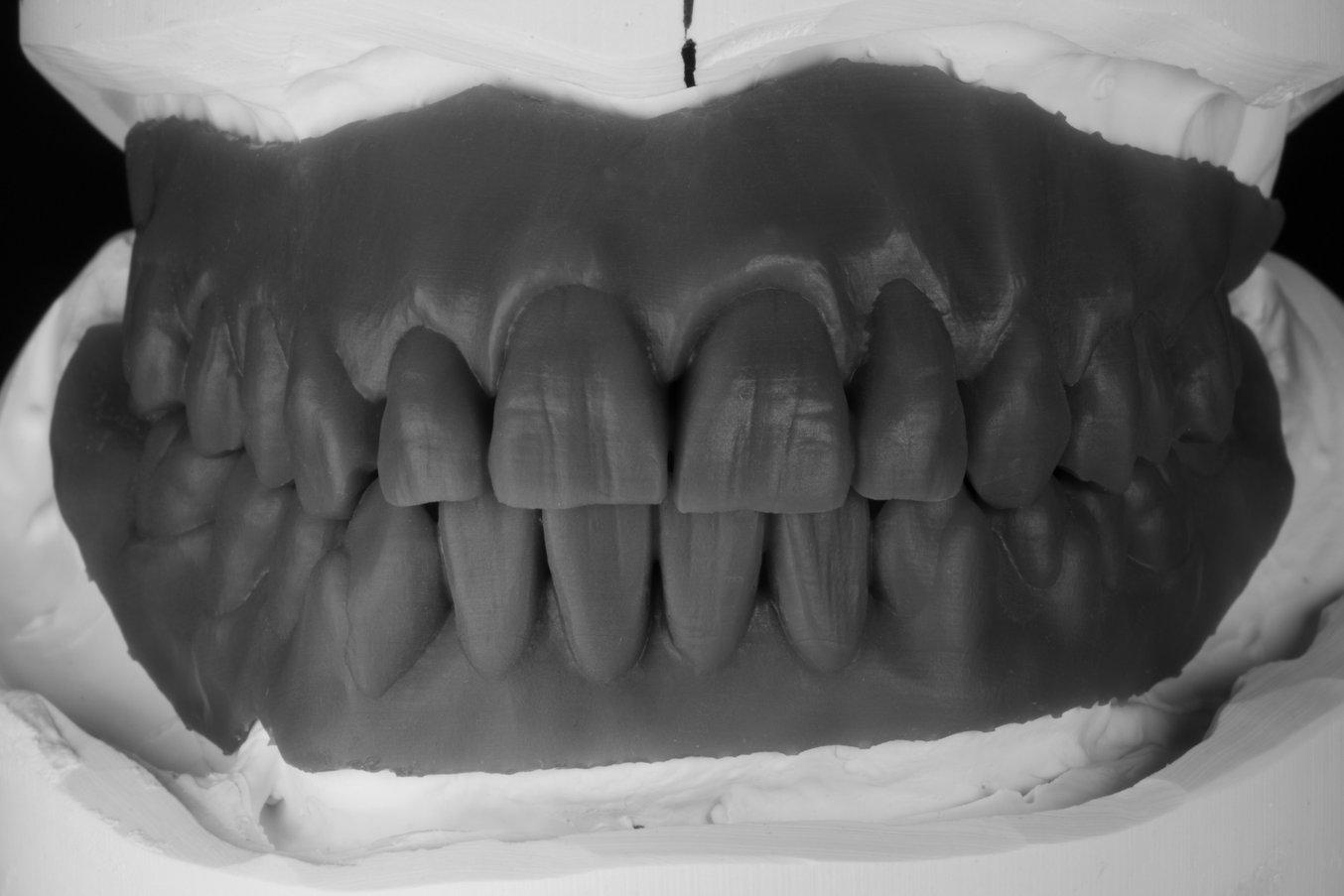
3D printing prototypes in Draft Resin allows dental technicians to validate the functionality and aesthetic of the planned denture in an articulator early on and at a low cost.
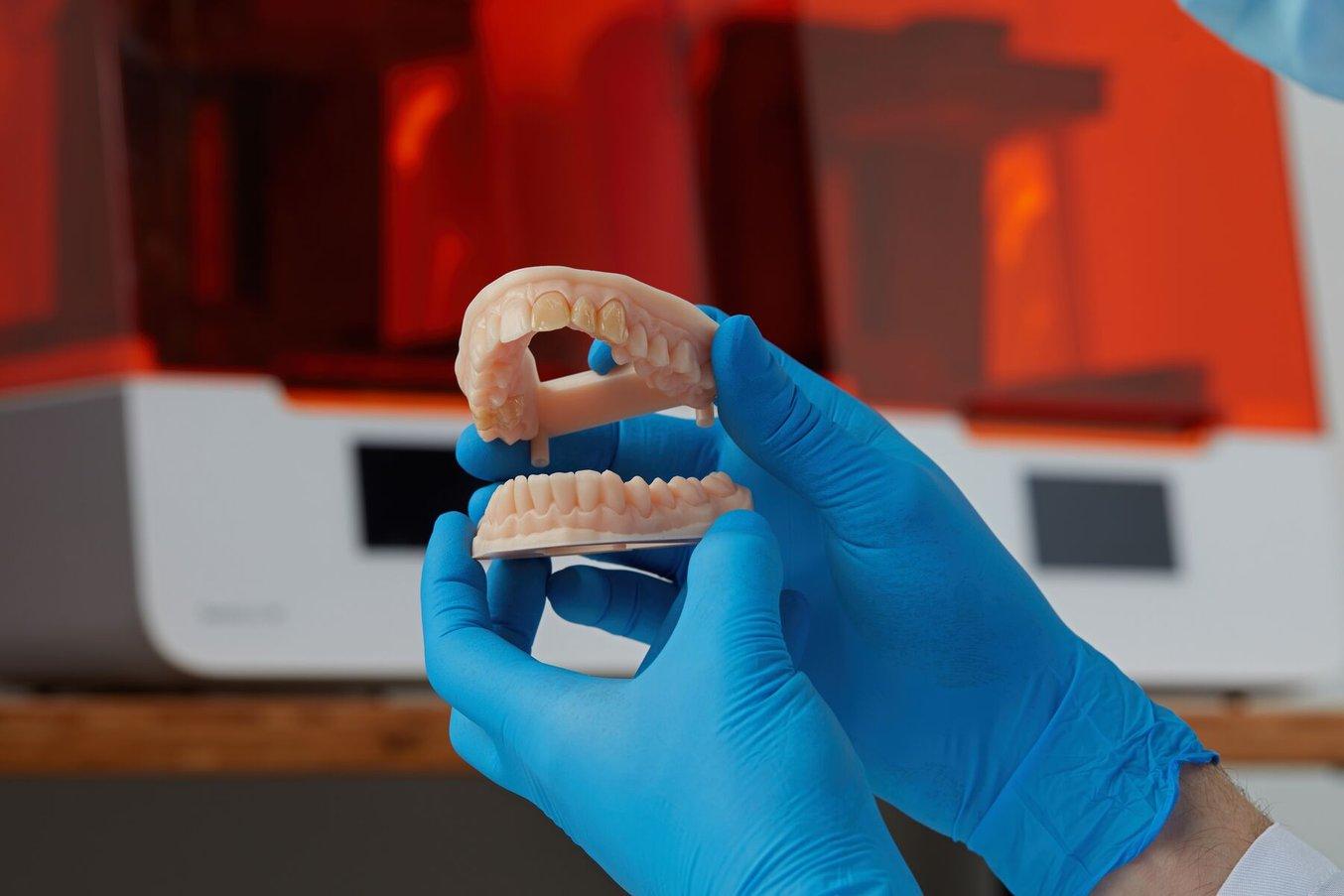
3D Printing Diagnostic Models With Formlabs SLA 3D Printers
Simple diagnostic models can be used for visualizing patient anatomy, case planning, presentation, and more. With PreForm’s Scan to Model feature, you can turn digital impressions directly into diagnostic models for printing on Formlabs 3D printers.
Robust 3D Printed Try-Ins
In addition to cutting down on labor time and manual tasks, additive manufacturing improved the quality of Leimbach's final product. SLA printing with resin creates prototypes that are more dimensionally stable than analog, wax-based models, ensuring better resistance against deformation during transport and patient trials.
"The practical setups that I used to create consisted of a base plate and wax, plus 28 teeth that weren't interconnected. If you bite on that and it warms up in the mouth, it's all going to shift again. It was never a sure thing - at least not after leaving it in the mouth for 15 minutes," says Leimbach.
3D printed teeth, on the other hand, are formed in one piece and securely glued to the specially manufactured base plate; the model's stability reduces the risk of error during planning. Additionally, trying on a model made from dental 3D printing materials is more comfortable for patients. "Ten years ago, we used to make this sticky, slimy base plate from light-curable plastic," Leimbach says. By contrast, Formlabs biocompatible resins are easy to use. After fully curing, post-processed parts are stable and can be cleaned, disinfected, and safely used for try-in.
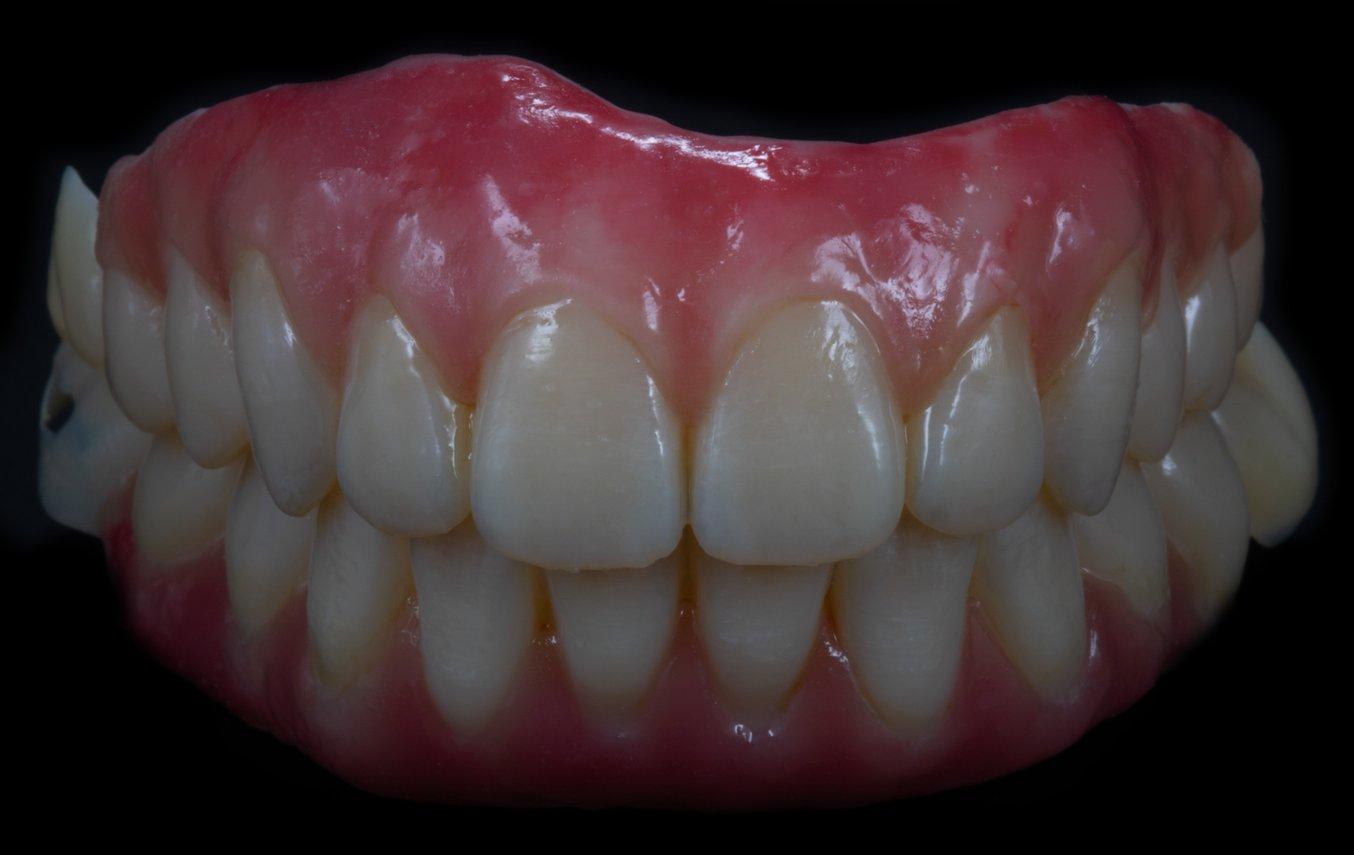
Backward planning and 3D printed try-ins reduce the production time and cost of high-quality dentures.
Empowering Dental Practices
In 80 percent of Leimbach’s cases, the process of producing telescopic dentures begins with a traditional impression sent to Die Zahnwerkstatt by dentists. Using a lab scanner, he digitizes them and continues the treatment planning virtually.
Working with dentists who have also realized the advantages of digital processes makes it even easier for Leimbach. In these cases, he receives digital images of the mouth that have been captured via intraoral scan, and can proceed with the virtual teeth setup in exocad or 3Shape right away.
More and more practices are working with cloud-based planning software. For practices based in Leimbach’s region, he prints out the try-ins and mails them. However, digital processes and the desktop printing capabilities of the Form 3B+ have allowed him to expand his customer base beyond his region.
Leimbach sends a dentist in Sweden 3D files that the dentist can then print in-house on his own Form 3B+. But even customers without their own printer can benefit from Leimbach’s try-ins - including in the US. In such cases, Leimbach sends files to colleagues with a printer. They then print the files and mail them to the receiving dental practice.
The dentists can then try the denture, get feedback from the patient, and document the situation via photos and intraoral scans. Leimbach uses this data to perform aesthetic modifications on the completed dentures, or to design a new try-in if there are functionality issues. Thanks to the continuous virtual exchange, Leimbach is able to implement requests for improvements before beginning to construct the primary components, frames, and the final setup.
"The system works perfectly. All of the dentists I partner with adapted immediately, too. Because of this, my return quota today is one percent at most."
Andreas Leimbach, Master Dental Technician and CEO, Die Zahnwerkstatt
Through consistent backward planning and the use of additive manufacturing techniques, Leimbach has decreased his return quota to below one percent. With the Form 3B+ and the expanding Formlabs library of dental 3D printing materials, Leimbach has been able to further enhance the quality of his try-ins, taking his processes "to a new level – in terms of repeatability, labor time, [and] aesthetics."
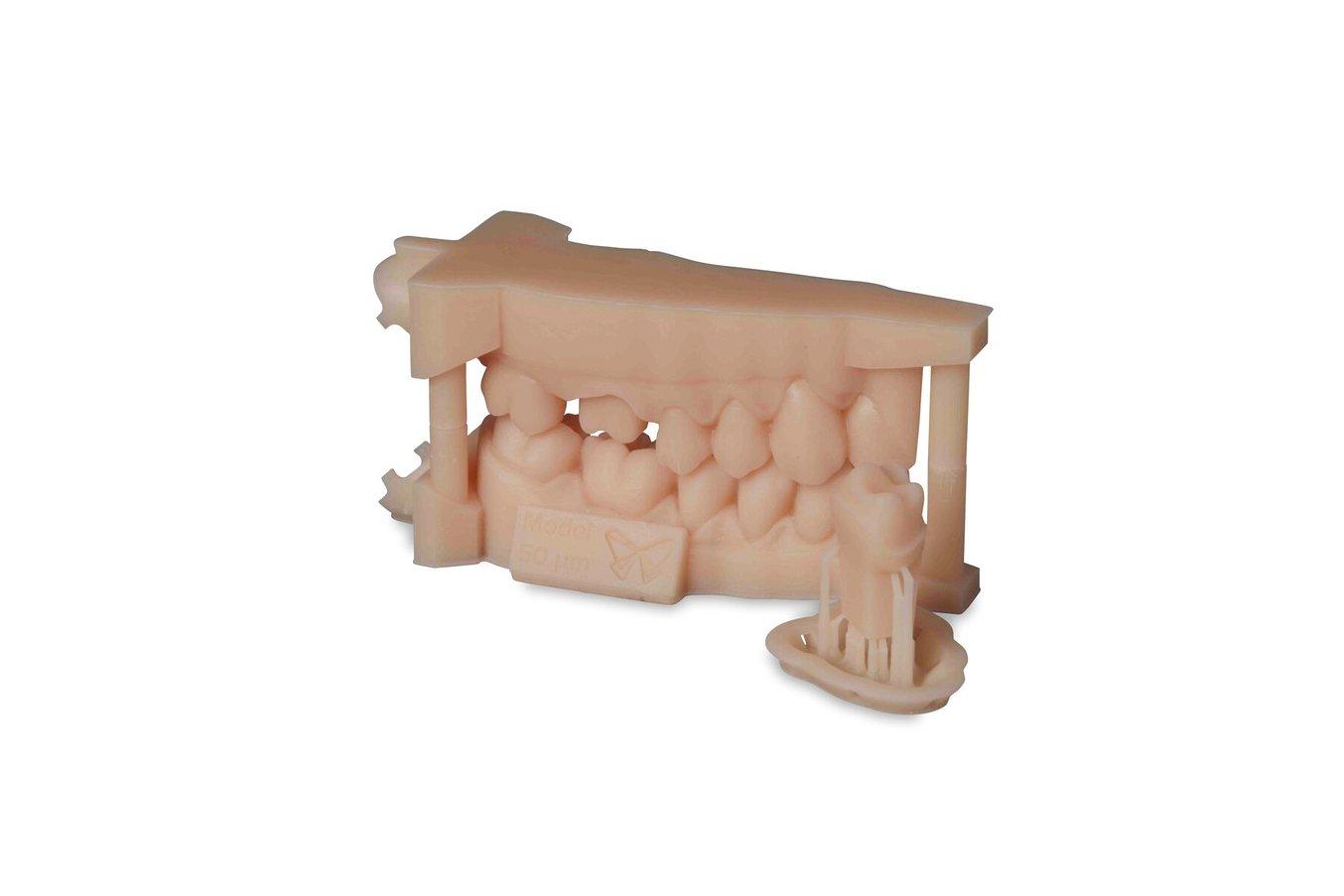
3D Printing Diagnostic Models With Formlabs SLA 3D Printers
Curious to see the quality firsthand? Pick a material and we'll ship you a free sample part 3D printed on the Form 3B to evaluate.
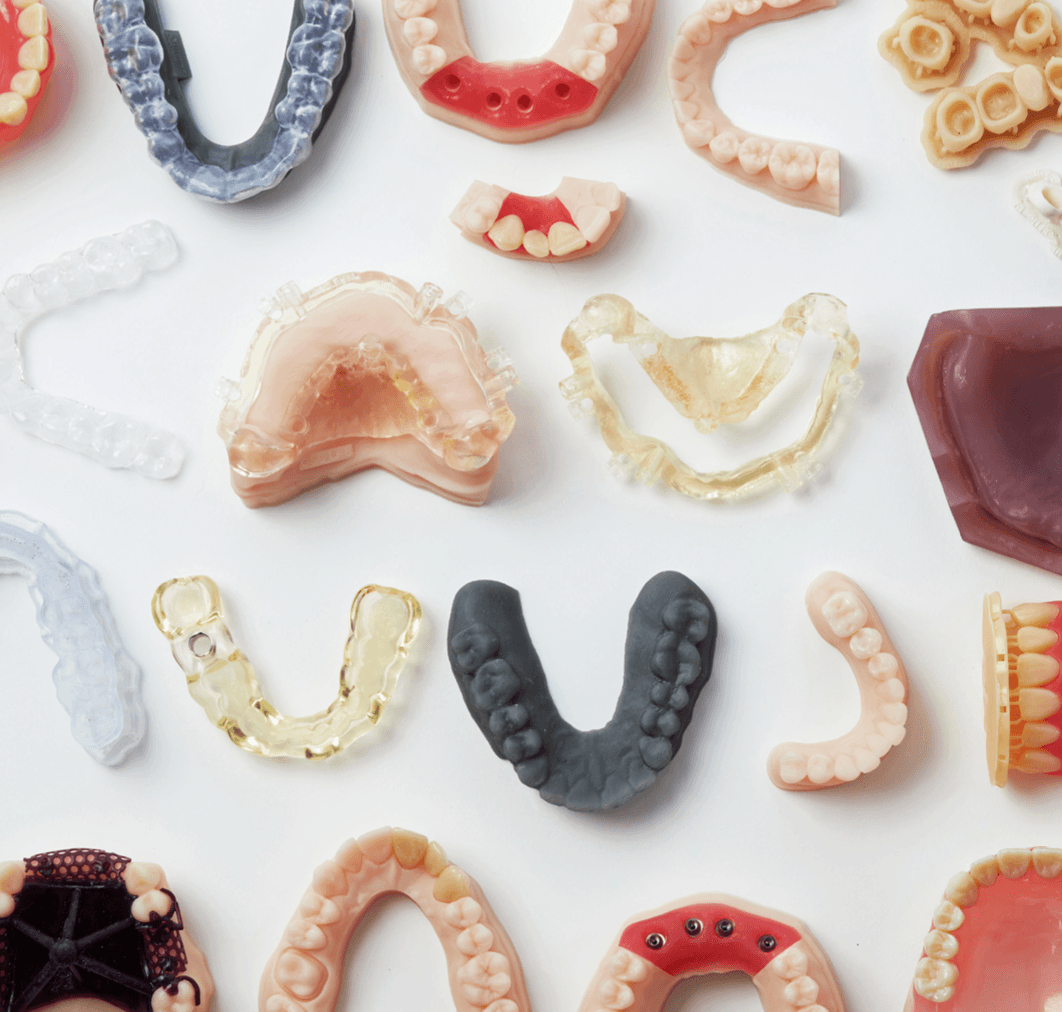
An Introduction to Regulatory Compliance in Dental 3D Printing
Implementing 3D printing workflows in your lab or practice can be a game changer for your business. Understanding the basics of regulatory compliance can help inform your decisions and what is best for your business. Regulation depends on geography; in this paper, we examine regulations in the United States of America and the European Union.
A Digital Future
"The interesting question is, what percentage of dental technicians around the world use try-ins, 3D printing, or digital planning? Because in my experience, and from what I've learned in our courses, many are still relying on analog workflows and cannot even imagine the things that are possible,“ says Leimbach.
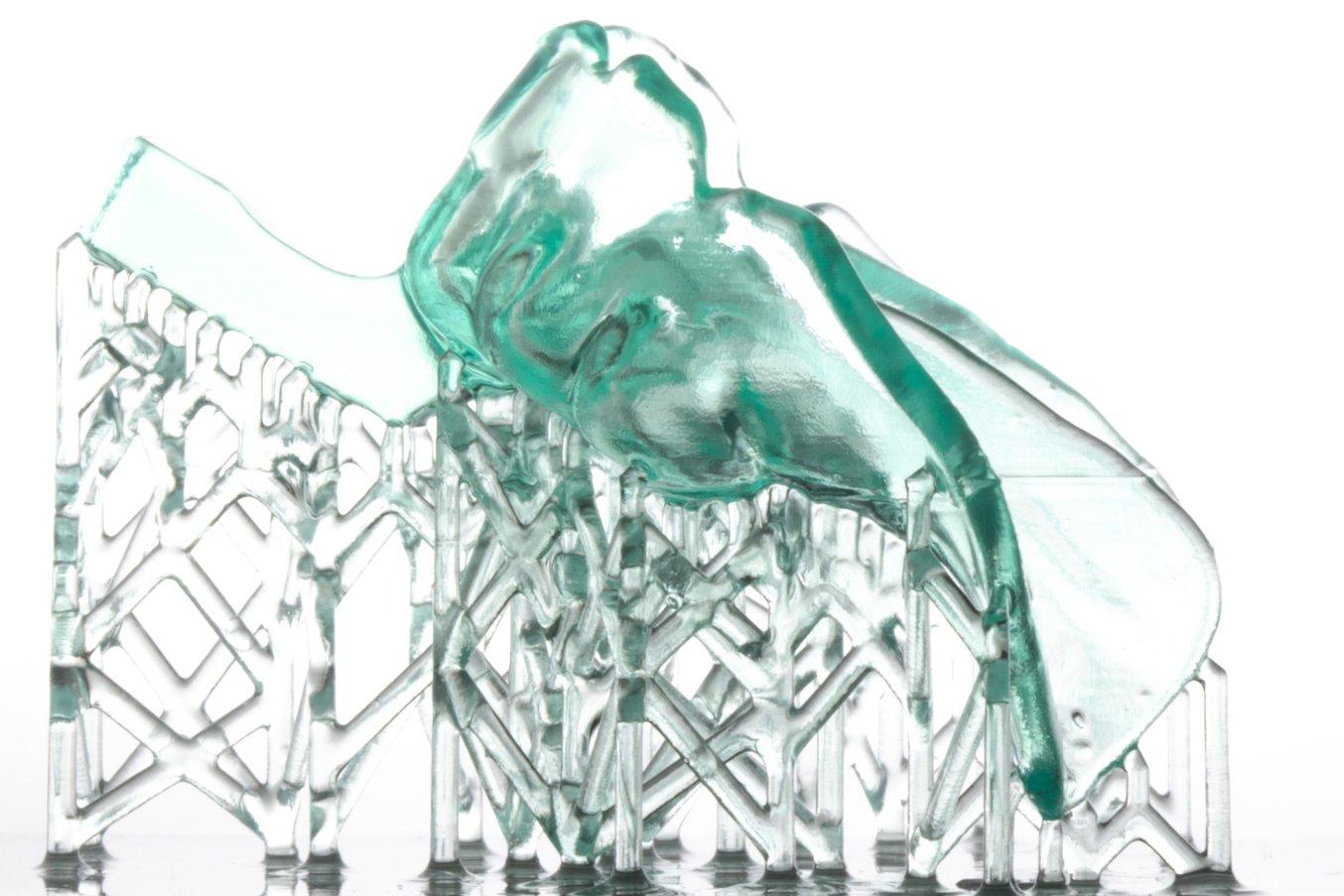
3D printing is efficient for a range of applications, including custom impression trays in Custom Tray Resin.
The versatility of the Form 3B+ has empowered Leimbach to broaden the applications he prints. In addition to prototyping try-ins, Leimbach prints custom impression trays, and molds for primary and secondary crowns in Castable Wax Resin.
Intuitive 3D printers like the Form 3B+ make the digital workflows adopted by Leimbach increasingly accessible. Leimbach says that “the concept of try-ins is extremely valuable for the future, since it saves us time and ensures more secure workflows. And I think that hasn't sunk in for everybody working in dentistry yet."
Explore our dental resources to learn how to create 3D printed dentures, or contact a Formlabs dental expert to learn how digital dentistry can maximize your efficiency.