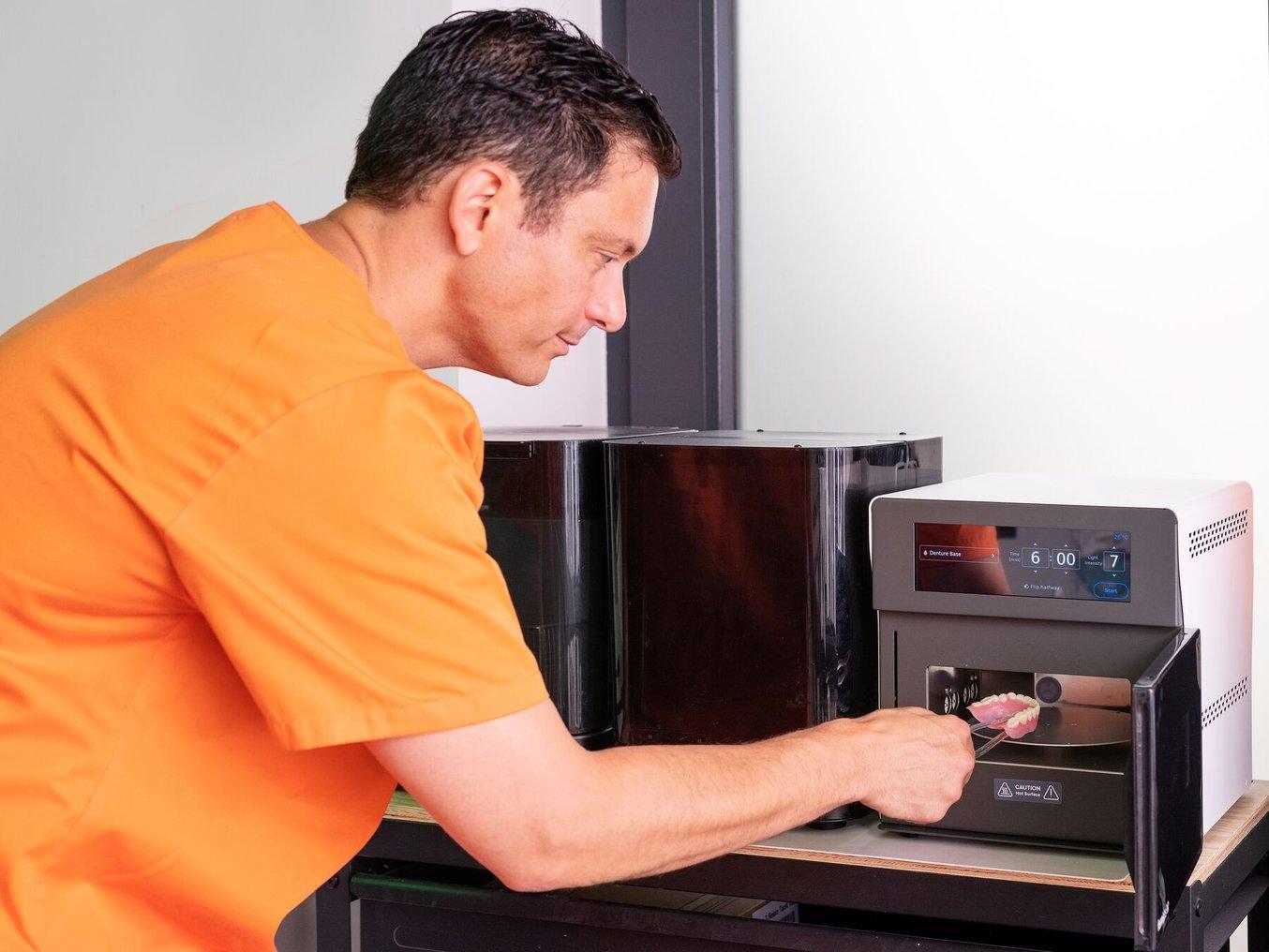
Following the implementation of digital dentistry for model and aligner production, 3D printing is expanding in the field of digital prosthetic dentistry. Today, Formlabs stereolithography (SLA) 3D printers are providing end-to-end solutions for high-quality digital dentures, leading to greater efficiencies and ROI.
German dental lab Zahntechniklabor MVZ Zahnkultur Berlin-Köpenick GmbH has been leveraging Formlabs SLA 3D printers for production. In this interview, dental technician Maximiliano Guendler tells us about the digital production of full dentures and provides more insight into the benefits of digital workflows with Formlabs resins and the Form 3B+ 3D printer compared to traditional manufacturing methods.
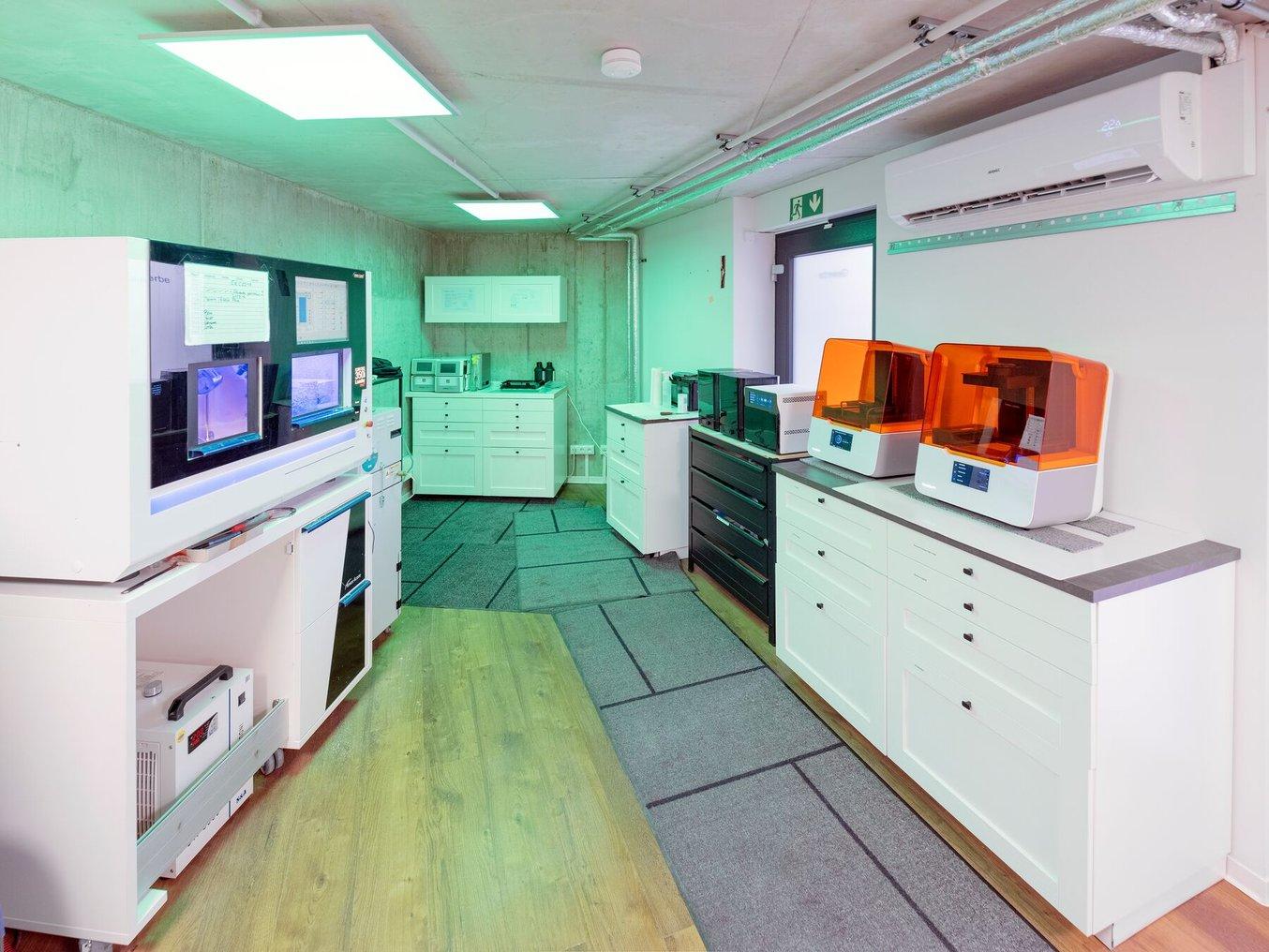
German dental lab Zahntechniklabor MVZ Zahnkultur Berlin-Köpenick GmbH utilizes Form 3B+ SLA 3D printers (right) for producing full dentures and a variety of other dental indications.
Entering the Future of Dental Technology With the Form 3B+
One Printer, Multiple Applications
Working with 3D printers on a daily basis, Maximiliano Guendler emphasizes the benefits of a digital workflow in contrast to traditional manufacturing techniques.
"The PreForm software is very intuitive and the 3D printer is easy to use."
Maximiliano Guendler, Dental Technician at Zahntechniklabor MVZ Zahnkultur Berlin-Köpenick GmbH
The Form 3B+ 3D printer is ready to print upon arrival and PreForm, Formlabs print preparation software, is designed for easy use. For Guendler, onboarding colleagues to the 3D printing workflow does not require any additional training sessions, saving him even more time and labor.
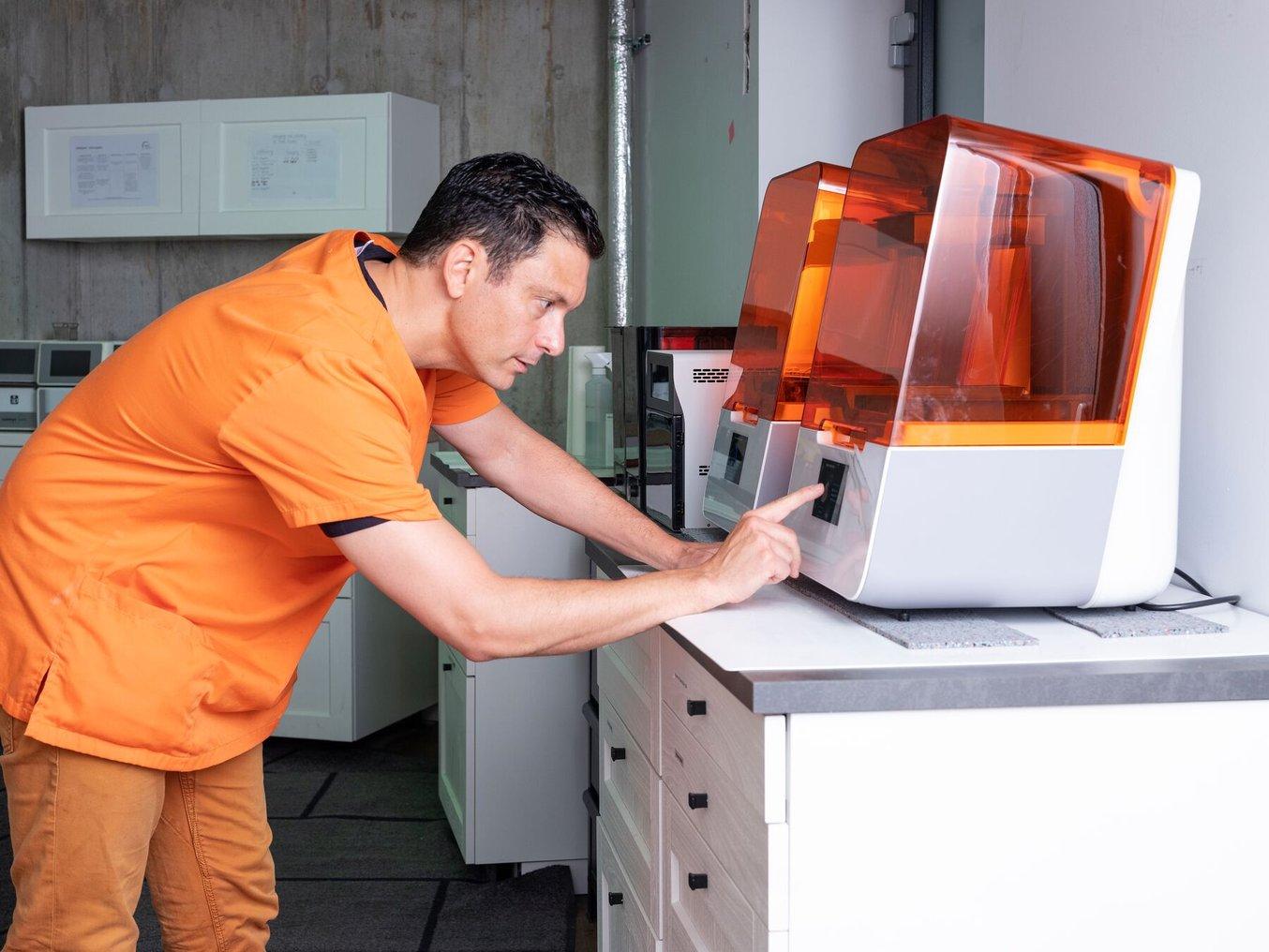
Guendler uses the intuitive touchscreen of the Form 3B+ to initiate printing.
He is especially excited by how quick and easy it is to change materials on the Form 3B+. Simply by swapping resin cartridges and tanks and cleaning the build platform, it’s possible to go from one material to another, and thus from one application to another, in a matter of minutes.
"Even with our constant changes of materials, Formlabs provides me and my colleagues speed and practicality in our everyday operation."
Maximiliano Guendler, Dental Technician at Zahntechniklabor MVZ Zahnkultur Berlin-Köpenick GmbH
The great variety of dental resins plus quick material changeover enables the creation of a wide range of dental applications on the same Form 3B+ printer. MVZ Zahnkultur Berlin-Köpenick GmbH leverages this to print appliances for the following applications, all on one printer.
- Full and hybrid dentures printed in Denture Base Resin (available in 4 different shades) and Denture Teeth Resin (available in 6 different shades)
- Temporary and permanent crowns printed in Permanent Crown Resin and Temporary CB Resin
- Custom impression trays printed in Custom Tray Resin
Guendler and his team also frequently use their Formlabs 3D printers to print models. Using Model V3 Resin, the team is able to rapidly print highly accurate resin prints with a smooth surface finish. "It's quite handy to have the option to quickly print a model for a flexible denture or for manufacturing occlusal guards or splints. We've had a lot of positive experiences so far,” says Guendler.
In general, the dental lab switches between six different Formlabs resins regularly on their two Form 3B+ printers – often changing materials daily.
High-Quality Dentures With SLA 3D Printing
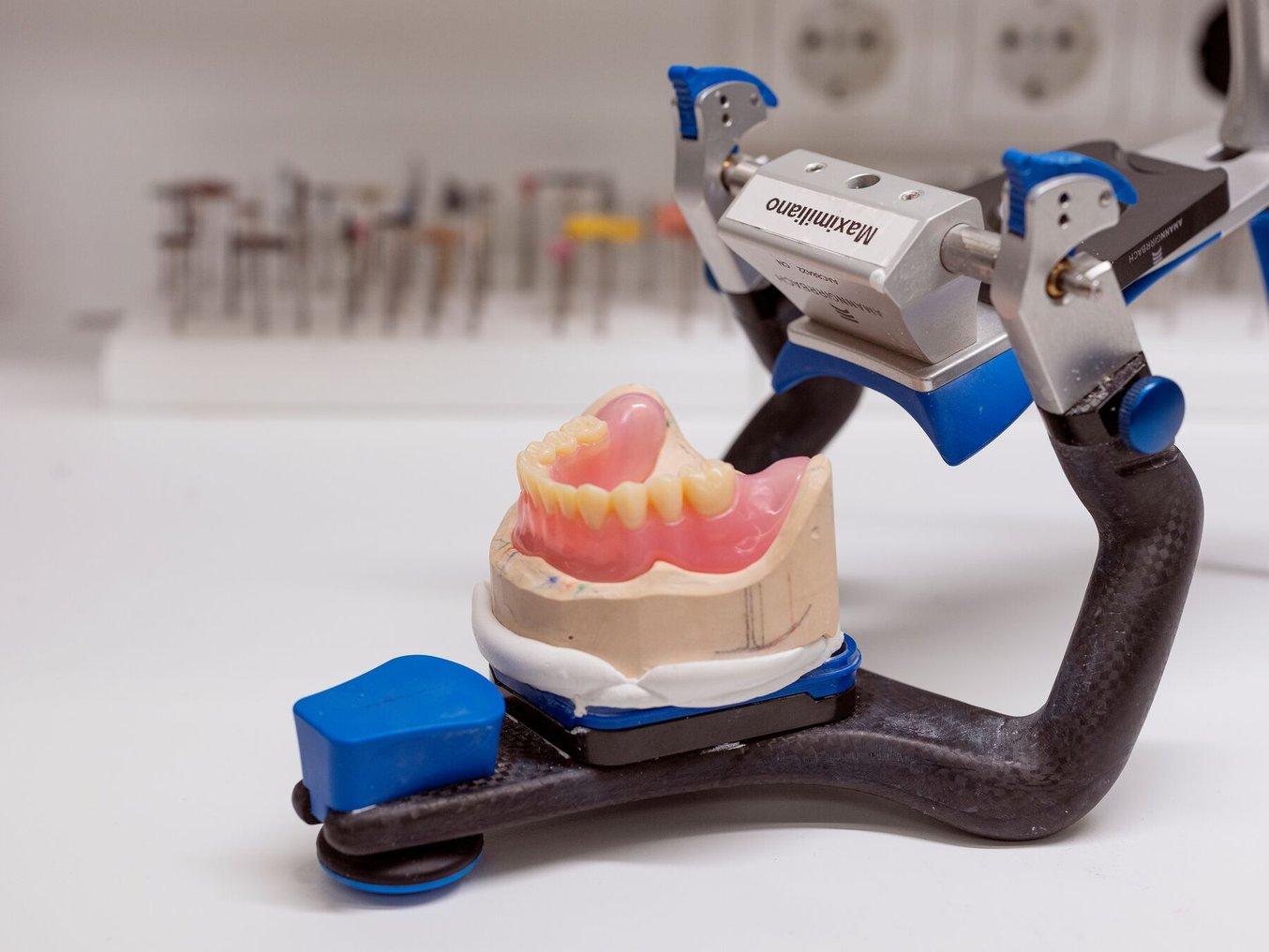
A finished mandibular denture printed in Denture Base Resin and Denture Teeth Resin.
Having already integrated 3D printed models into the lab’s workflow, lab owner and dentist Carsten-Can Öztan saw great potential in the application of digital dentures and realized that customers matched his interest in the technology.
"First, we created a test denture with Formlabs as a sample print, and the result convinced our boss as well as the customers. Afterward, we decided to invest in a Formlabs SLA 3D printer,” says Maximiliano Guendler. Since the beginning of 2022, the roughly 20 dental technicians at MVZ Zahnkultur Berlin-Köpenick GmbH are focused on scaling their production of 3D printed dentures with the help of the Form 3B+.
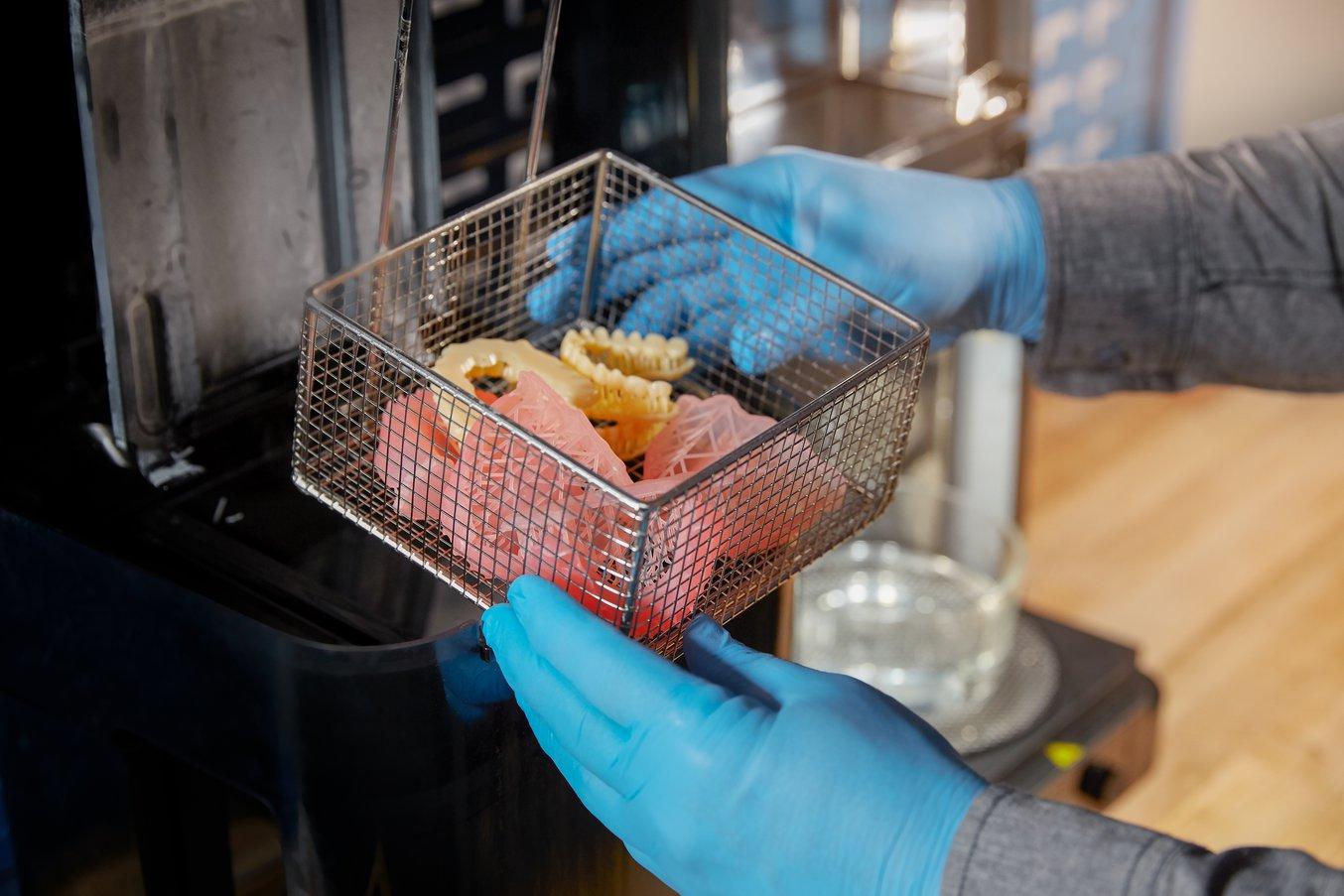
Digital Denture Masterclass
Hear from exocad America and Formlabs Dental about the latest in 3D technology, learn best practices for producing digital dentures, and see for yourself what the new industry standard will be.
Non-Stop Operation With the Form 3B+
For the Form 3B+, Guendler focuses on manufacturing hybrid dentures. This means that denture teeth are 3D printed while denture bases are produced via traditional machining and then assembled with the 3D printed teeth using cold-curing acrylic.
"We are convinced that teeth printed in Denture Teeth Resin present a high-quality solution for restorations."
Maximiliano Guendler, Dental Technician at Zahntechniklabor MVZ Zahnkultur Berlin-Köpenick GmbH
Every week, technicians in the lab produce between ten and twelve sets of hybrid dentures to be sent out to customers. If duplicate or travel dentures are needed, they often manufacture them completely through 3D printing. In such cases, both the denture bases and the denture teeth are 3D printed and precisely assembled during post-processing.

Assembly of denture base and denture teeth during post-processing using Denture Base Resin.
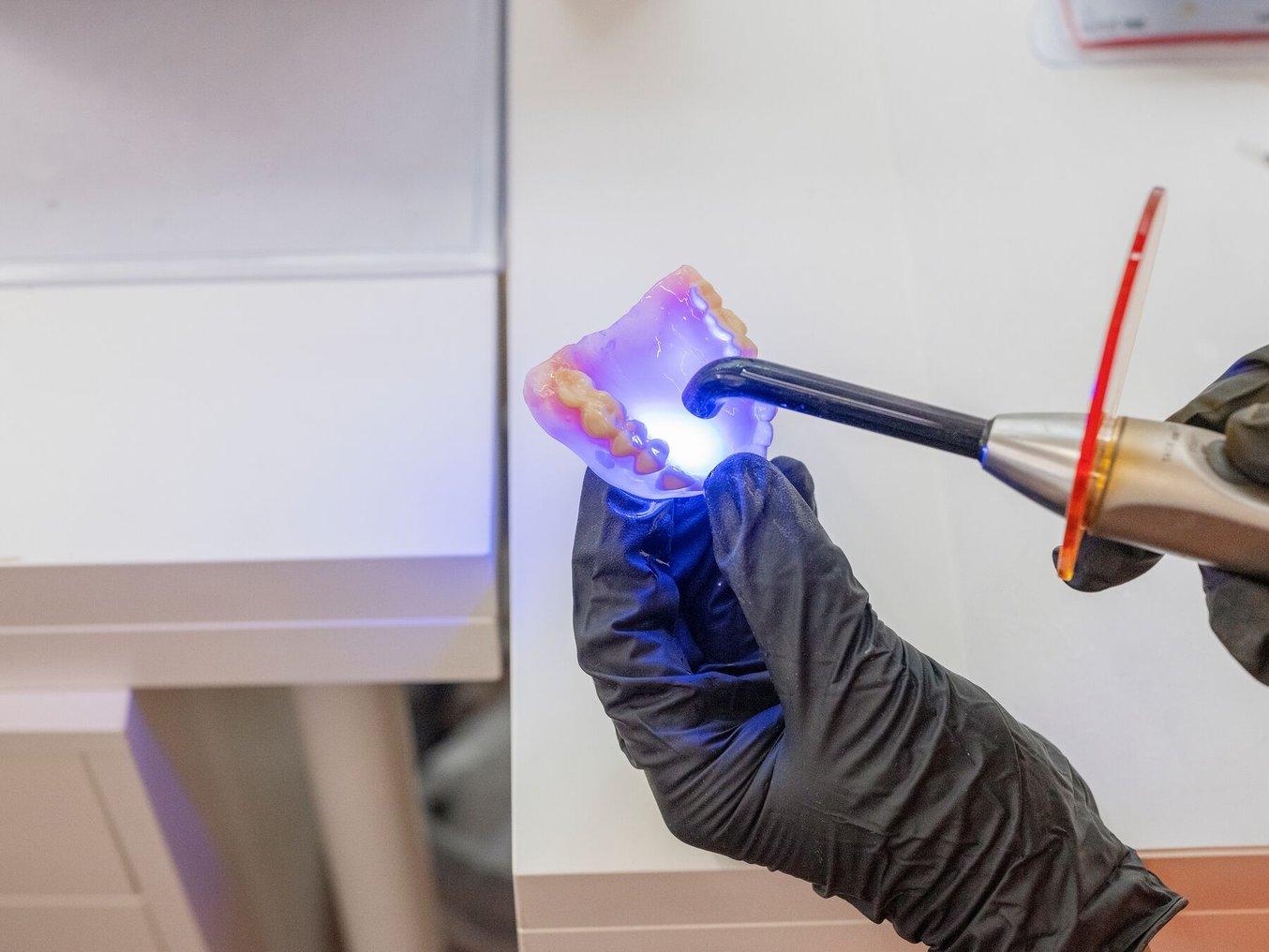
Denture assembly using dental adhesive and a polymerization lamp.
Since the dental lab is using their 3D printers daily for different applications, they rely on organized workflows to leverage the full capacity of the lab's two Form 3B+ printers. More and more denture bases are being printed overnight after Guendler creates the CAD design during the day. That leaves the 3D printers available to print denture teeth and crowns during the day, as well as appliances for the preparation of procedures, such as custom impression trays and models. "If I need to print denture teeth, for example, I do that during the day, as they are done within one and a half or maximum two hours, allowing me to continue my work,” says Guendler.
Workflow for Digital Dentures
The digital denture workflow begins with capturing an intraoral scan. "Our dentists are doing a lot of intraoral scanning. About 80% of impressions are sent to us digitally," Guendler reports. Based on these scans, custom impression trays are digitally designed and then 3D printed. The custom trays can then be used to take a further, traditional impression of the patient's dentition, as full dentures usually require an additional mucodynamic impression. This way, muscle attachments can be taken into consideration when printing the denture base. The new impression is then digitalized.
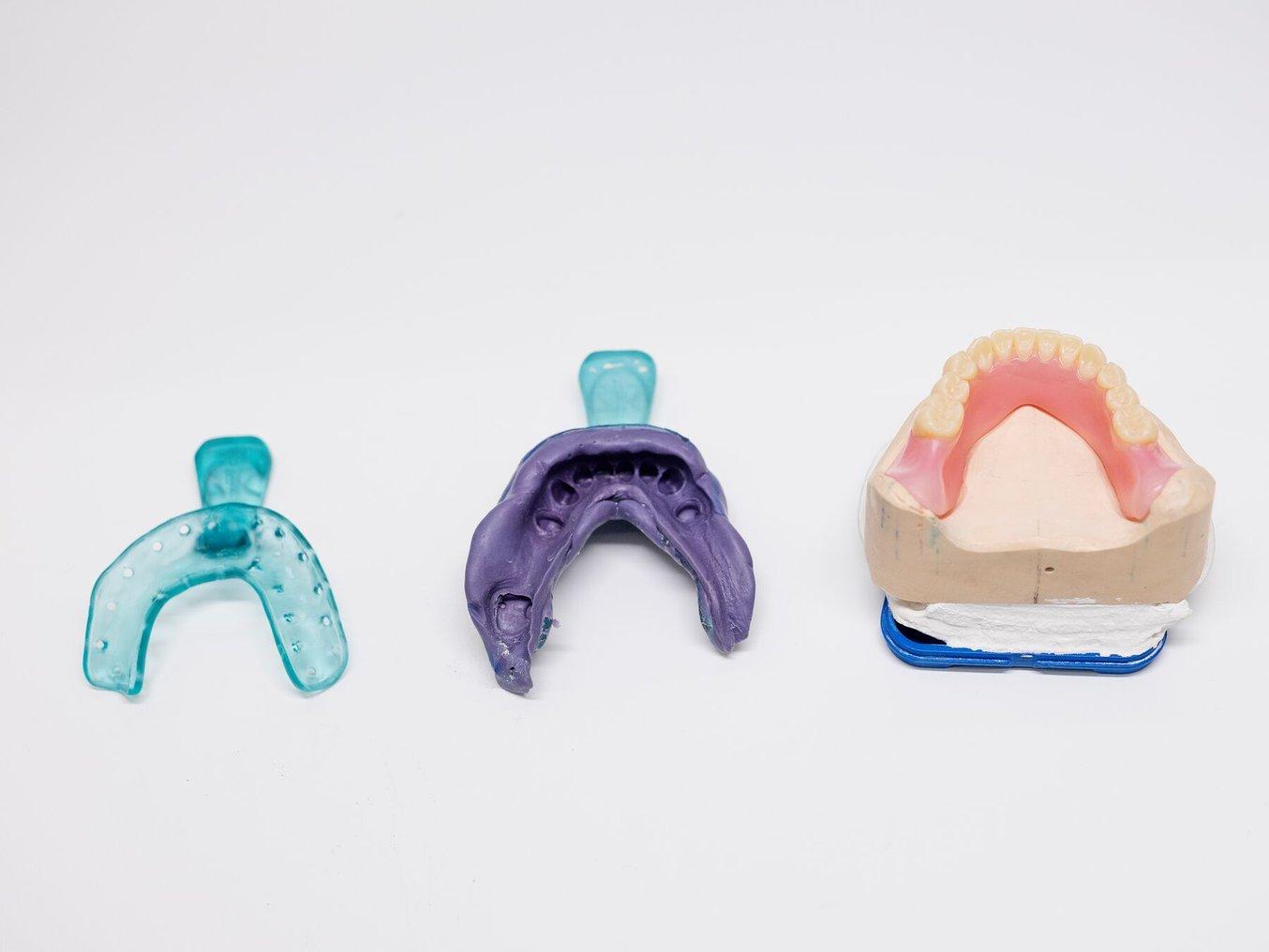
The workflow for producing digital dentures, from custom impression trays printed in Custom Tray Resin for taking traditional impressions, to a finished mandibular denture.
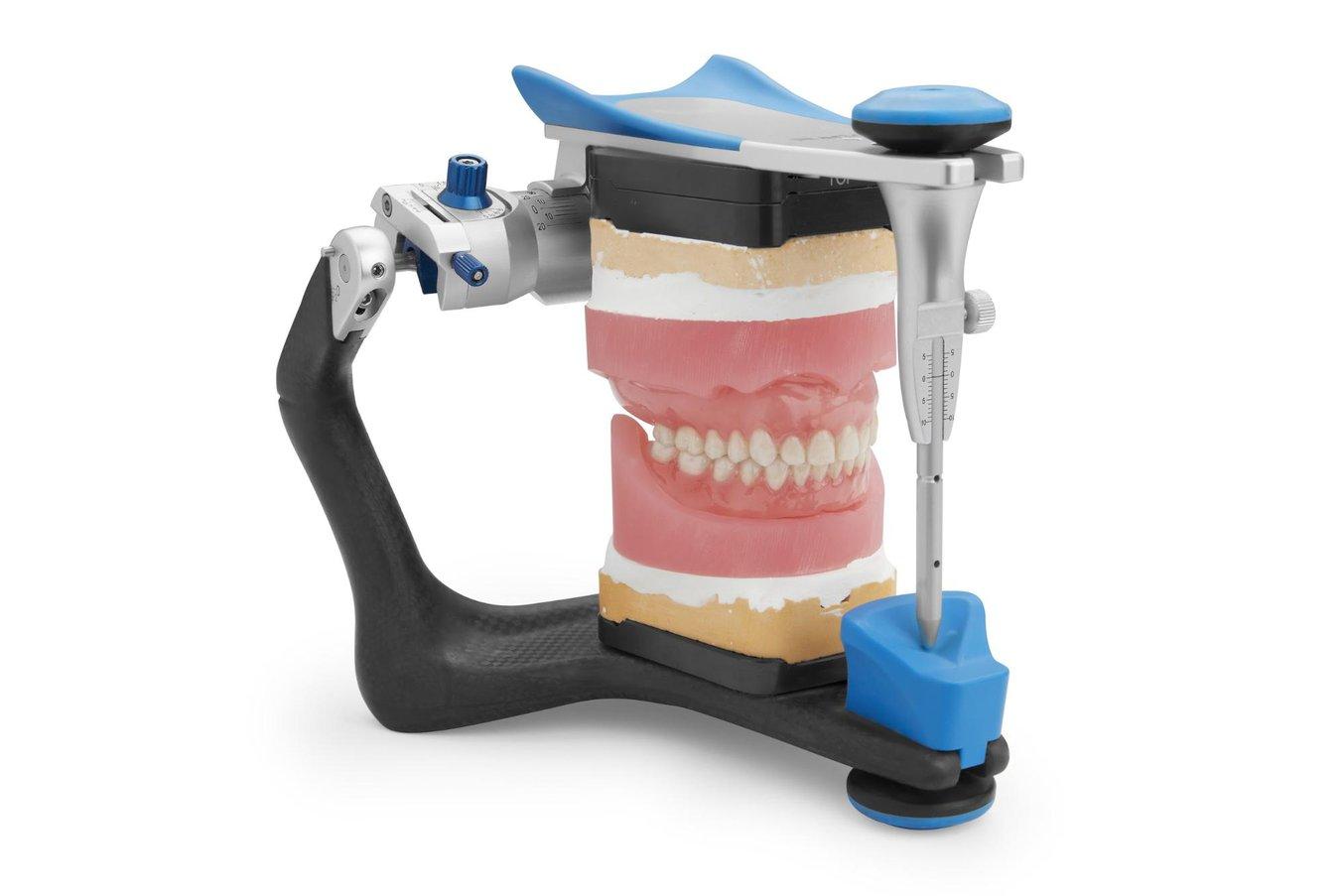
3D Printing Full Dentures with Formlabs 3D Printers
Formlabs Digital Dentures allow dental laboratories to grow or expand production with an efficient, cost-effective 3D printed denture solution.
Guendler designs new dentures using the software exocad. If a duplicate is needed, he simply scans the existing denture or retrieves the file from the database, edits it in the software 3Shape, and directly prints it in Denture Base Resin and Denture Teeth Resin.
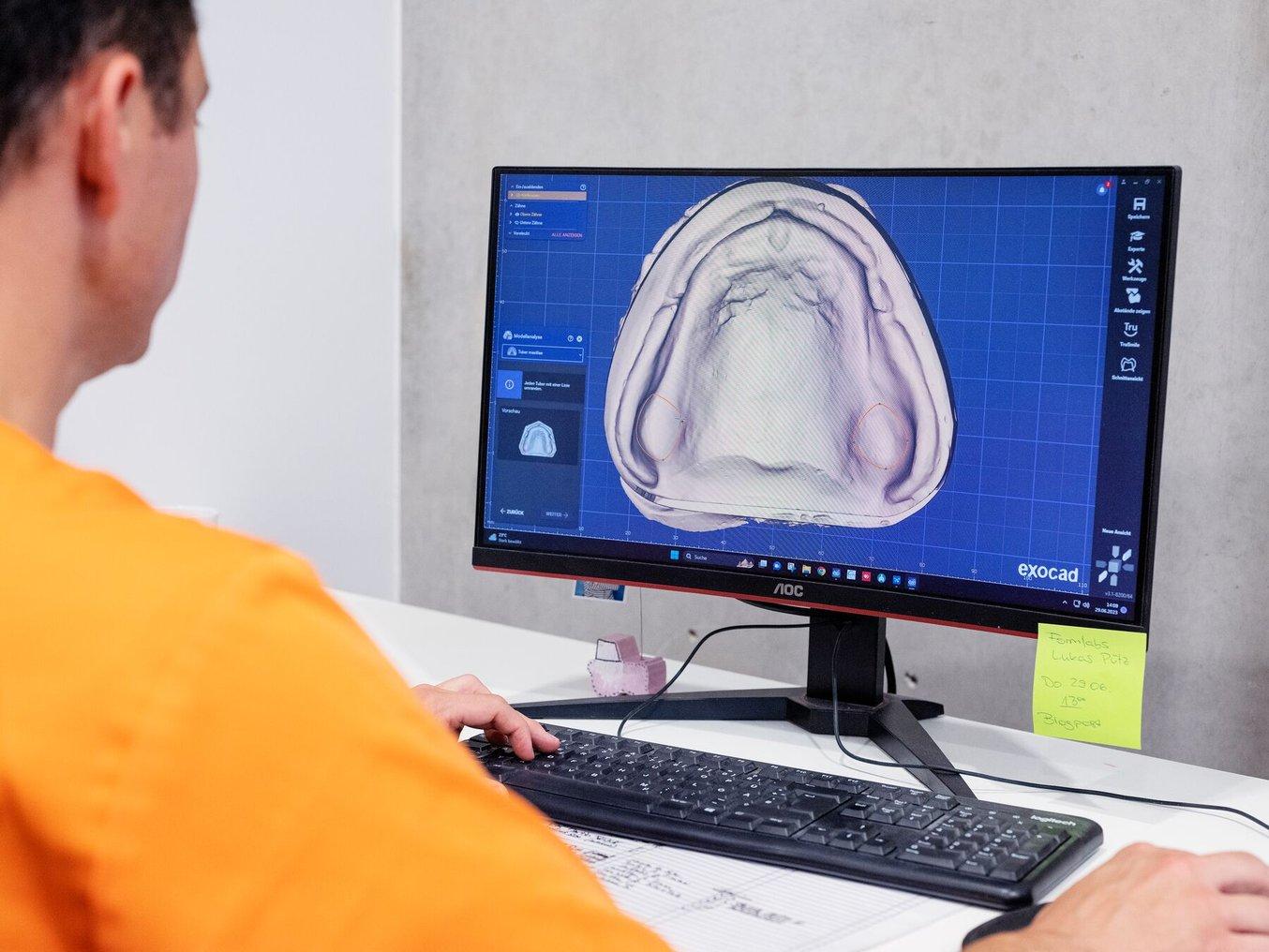
Digitized impression of a dentition used to design a denture in the software exocad.
Advantages of Digital Dentures Over Traditional Workflows
The transition from conventional methods to digital manufacturing of dentures offers dental labs like MVZ Zahnkultur Berlin Köpenick GmbH significant benefits. One of the obvious advantages is the economic benefit of digital dentures for labs as well as patients. This is particularly evident in the cost of materials. For a full denture that is 100% 3D printed in Formlabs resins, material cost comes to around $30. In comparison, a set of denture teeth alone produced with traditional methods costs $150, excluding the costly and labor-intensive denture base which can vary in price.
Traditional dentures | 3D printed dentures | |
---|---|---|
Material cost | $150 | $30 |
Labor time | 4.5 h | 3 h |
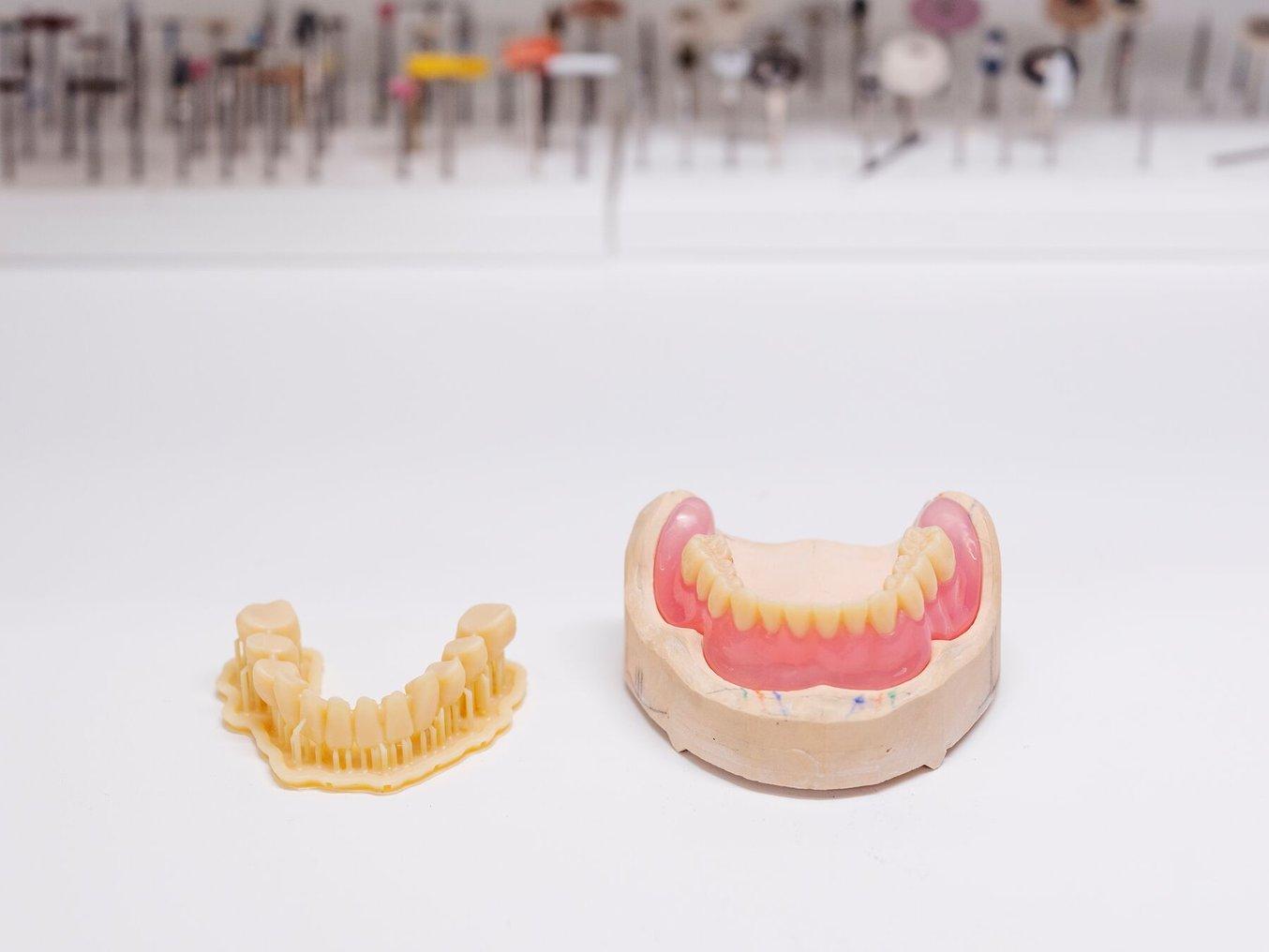
Left: 3D printed denture teeth made from Denture Teeth Resin. Right: 3D printed full mandibular denture made from Denture Base Resin and Denture Teeth Resin.
Guendler also details how the digital workflow helps him organize his time at work more efficiently. "For instance, I will design four to five dentures in the morning, and then prepare everything else in PreForm and on the 3D printers, so the dentures can be printed in the evening. The following day, I allocate time for post-processing and finishing and can deliver all orders of the week almost at the same time,” he explains.
According to his estimates, based on years of experience with both workflows, producing a full denture using the digital workflow is up to 30% faster than with traditional processes. Additionally, conventional methods are often less streamlined, since you can only ever work on one denture at a time. Meanwhile, a 3D printer can print up to six denture bases simultaneously once they have been designed in CAD software.
From the patient's perspective, 3D printed dentures offer the advantage of higher comfort. As Guendler explains, "Compared to a plastic denture, the full dentures printed with Formlabs materials are lighter and thus more comfortable to wear for our patients, especially on the upper jaw." Patients can also benefit from the database of labs; in case a denture gets lost or damaged, a replacement can be quickly reprinted.
"This is definitely a big advantage of going digital. All models and dentures are scanned and saved and can be retrieved and reprinted at any time. This way, cumbersome visits in the dental clinic to have a new impression taken or a new denture adjusted will become a thing of the past."
Maximiliano Guendler, Dental Technician at Zahntechniklabor MVZ Zahnkultur Berlin-Köpenick GmbH
Guendler also highlights the health benefits that he experiences with digital workflows compared to his years of using traditional manufacturing methods. "The digital manufacturing of dentures I think has the big advantage that us dental technicians hardly come into contact with the material. I used to have skin contact with various harmful plastics, monomers, and polymers on a daily basis and was breathing in their hazardous fumes." Having to work with wax and fire are further unpleasant elements of traditional workflows. By designing dentures on the computer and 3D printing, comparatively minimal post-processing is required, meaning dental technicians can benefit from a cleaner, safer, and more pleasant workflow.
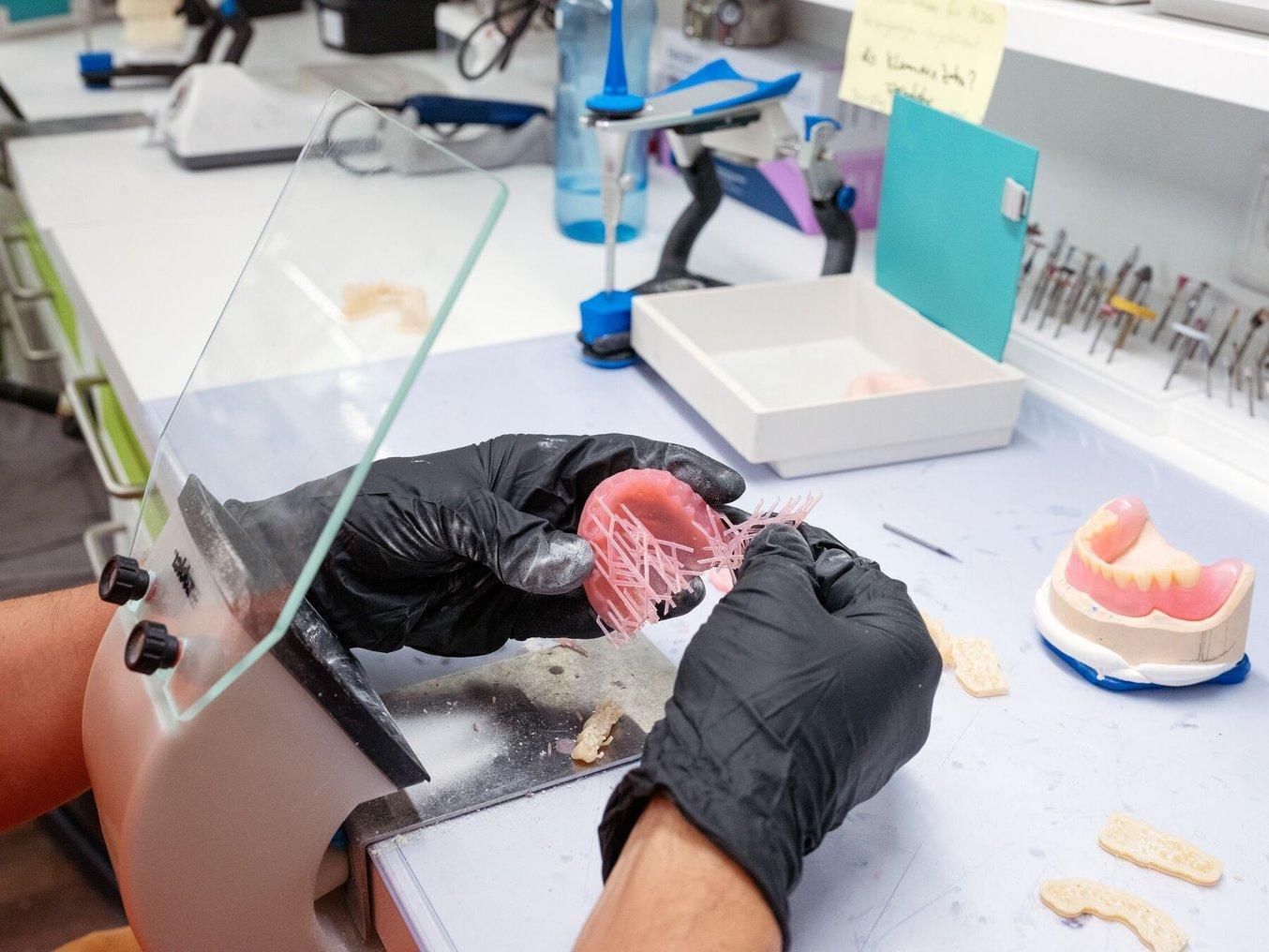
Easy removal of support structures from a denture base printed in Denture Base Resin.
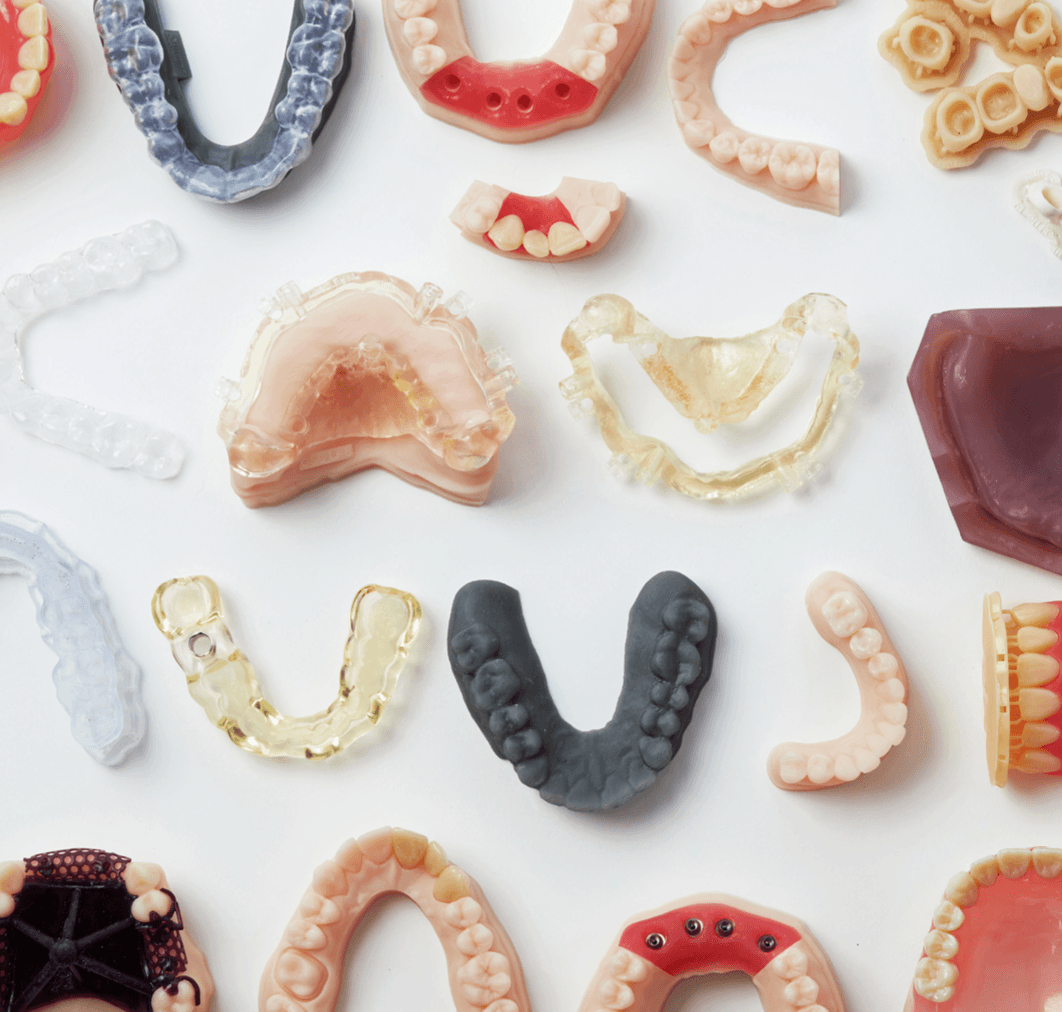
An Introduction to Regulatory Compliance in Dental 3D Printing
Implementing 3D printing workflows in your lab or practice can be a game changer for your business. Understanding the basics of regulatory compliance can help inform your decisions and what is best for your business. Regulation depends on geography; in this paper, we examine regulations in the United States of America and the European Union.
Scaling Production
Looking into the future, Maximiliano Guendler and his team see a lot of potential in digital dentistry. Guendler predicts the demand for 3D printed restorations will continue to grow, and considers scaling up the lab's fleet of 3D printers and adding dental resins a likely scenario.
Adding printers enables production to scale, as does the addition of the Formlabs Automation Ecosystem. Comprised of software and hardware, Form Auto enables round-the-clock remote printing, so dental labs can print on nights and weekends without the need for extra labor.
Whether you’re just entering digital dentistry or looking to scale up, Formlabs Dental experts can help you find the solution that fits your goals.